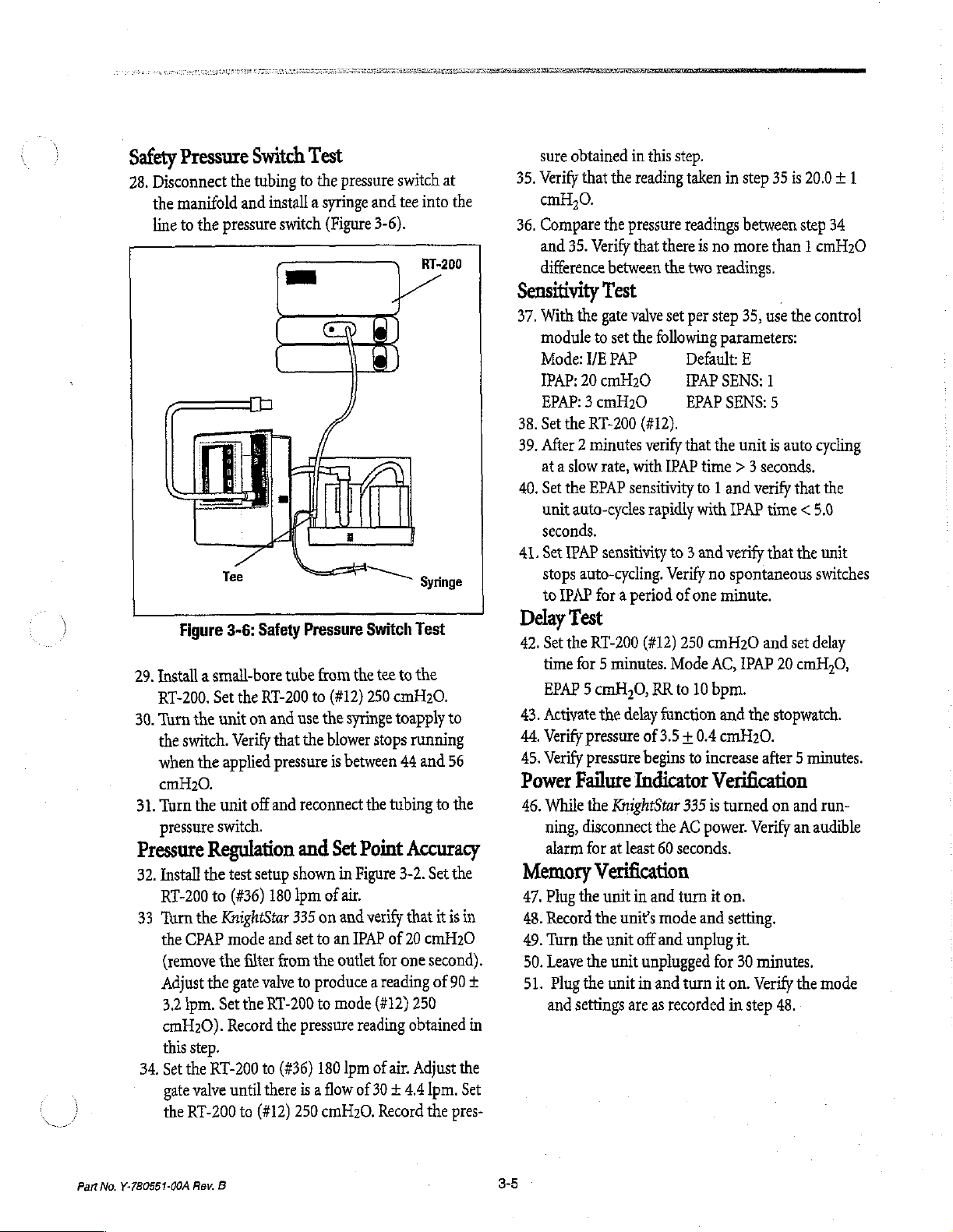
Safety
28.
Pressure
Disconnect
the
manifold
line
to
the
pressure
the
29.
Install a small-bore
RT-200.
30.
Turn
the
when
cmH20.
31.
Turn
pressure
Pressure
32.
Install
RT-200
33
Turn
the
(remove
Adjust
3.2
cmH20).
this
34,
Set
gate
the
Tee
Figure
3-6:
Set
the
unit
switch.
the
applied
the
unit
switch.
Verify
Regulation
the
test
to
(#36)
the
KnightStar
CPAP
mode
the
the
gate
Ipm.
Set
Record
step.
the
RT-200
valve
until
RT-200
Switch
tubing
and
Safety
the
on
off
Test
to
the
install a syringe
switch
Pressure
tube
from
RT-200
to
and
use the
that
the
pressure
and
reconnect
and
setup
shown
180
lpm
335
on
and
set
to
filter
from
the
valve
to
produce a reading
the
to
there
to
(#12)
RT-200
to
the
pressure
(#36)
is a flow
250
180
pressure
and
(Figure
blower
of
Switch
the
(#12)
250
syringe
is
between
the
Set
Point
in
Figure
air.
and
verify
an
IPAP
outlet
mode
reading
lpm
3-6).
stops
(#12)
of
of 30 + 4.4
cmH20.
switch
tee
into
RT-200
Syringe
Test
tee
to
the
cmH20.
toapply
running
44
and
tubing
Accuracy
3-2.
Set the
that
of
20
cmH20
for
one
second).
250
obtained
air.
Adjust
Ipm.
Record
the
at
the
to
56
to
the
it
is
of
90
pres-
in
+
in
the
Set
sure
35,
Verify
cmH,0.
36.
Compare
and
difference
Sensitivity
37,
With
module
Mode:
IPAP:
EPAP: 3 cmH20
38.
Set
39.
After 2 minutes
at a slow
40.
Set
unit
seconds.
41. Set
stops
to
IPAP
Delay
42,
Set
time
EPAP 5 cmH,0,
43,
Activate
44.
Verify
45.
Verify
Power
46.
While
ning,
alarm
Memory
47.
Plug
48.
Record
49.
Turn
50.
Leave
51.
Plug
and
obtained
that
35.
in
the
reading
the
pressure
Verify
that
this
there
between
Test
the gate
20
the
the
auto-cycles
IPAP
auto-cycling.
valve
to
set
the
following
I/E
PAP
cmH20
RT-200
EPAP
(#12).
verify
rate,
with
sensitivity
rapidly
sensitivity
for a period
Test
the
RT-200
for 5 minutes.
(#12)
RR
the
delay
function
pressure
pressure
Failure
the
disconnect
for
of
3.5 + 0.4
begins
Indicator
KnightStar
the
at
least
60
Verification
the
unit
in
and
the
units
mode
the
unit
off
and
the
unit
unplugged
the
unit
in
and
settings
are
as
step.
taken
in
readings
is
no
the
two
readings.
set
per
step
parameters:
Default:
IPAP
SENS:
EPAP
SENS:
that
the
IPAP
time > 3
to 1 and
with
IPAP
to 3 and
Verify
of
Mode
to
one
250
10
verify
no
spontaneous
minute.
cmH20
AC,
bpm.
and
cmH20.
to
increase
Verification
335
is
turned
AC
power.
seconds.
turn
it
on.
and
setting.
unplug
for
turn
it
on.
recorded
in
step
35
is
20.0 + 1
between
more
35,
E
unit
IPAP
the
Verify
step
than 1 cmH20
use
the
1
5
is
auto cycling
seconds.
verify
that
time
< 5,0
that
the
and
set
delay
20
cmH,0,
stopwatch.
after 5 minutes.
on
and
an
audible
it.
30
minutes.
Verify
the
step
48.
34
control
the
unit
switches
run-
mode
Part
No.
Y-780551-00A
Rev.
B
3-5
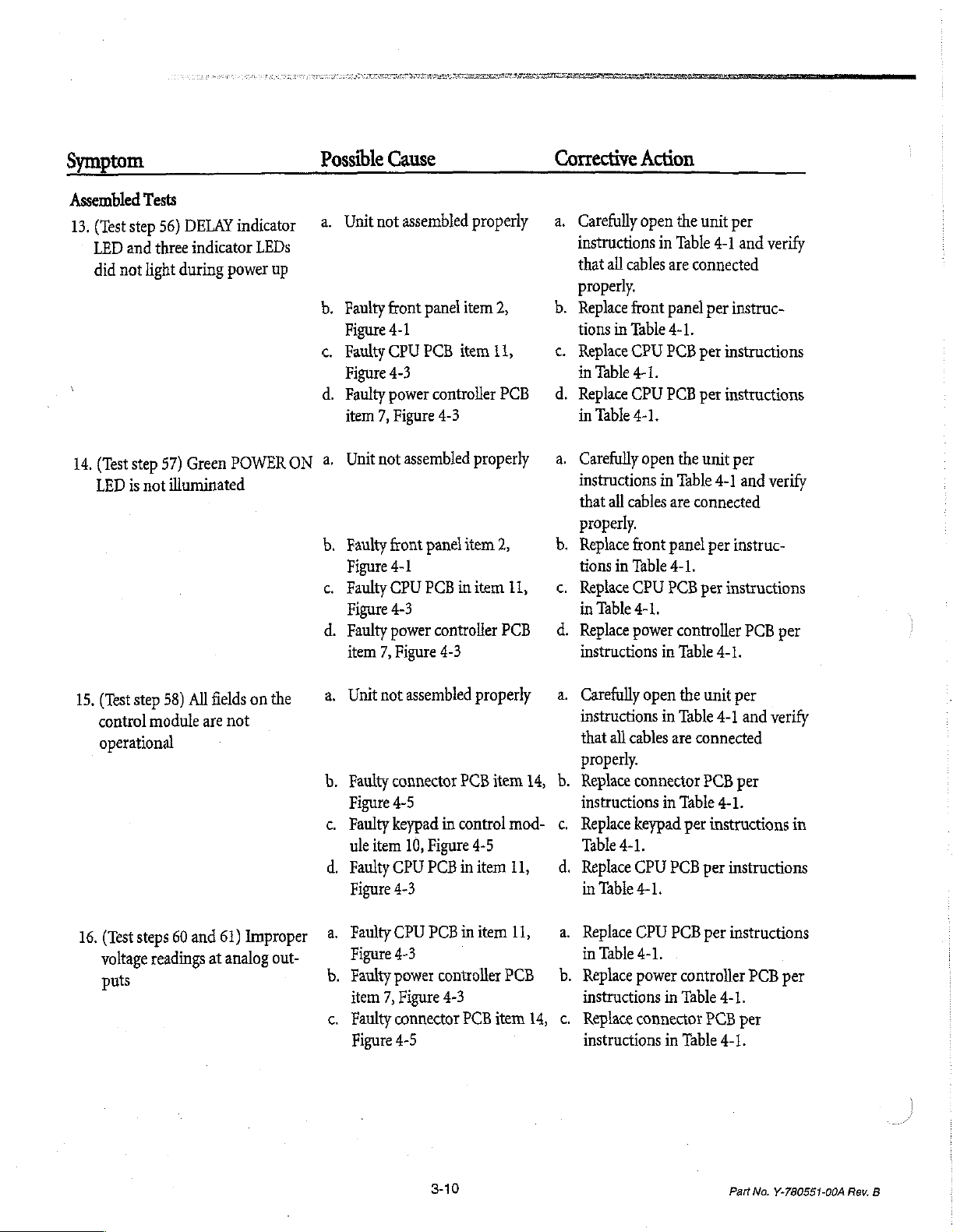
Symptom
Possible
Cause
Corrective
Action
Assembled
13.
(Test
step
LED
and
did
not
14,
(Test
step
LED
is
Tests
56)
DELAY
three
indicator
light
during
57)
Green
not
illuminated
indicator
LEDs
power
up
POWER
ON
a.
b.
c.
d.
a.
b.
с.
d.
Unit
Faulty
Figure
Faulty
Figure
Faulty
item
Unit
Faulty
Faulty
not
front
4-1
CPU
4-3
power
7,
Figure
not
front
Figure
4-1
CPU
Figure
4-3
Faulty
power
item
7,
Figure
assembled
panel
PCB
assembled
PCBinitemil,
properly
item
item
controller
4-3
properly
panel
item
controller
4-3
2,
11,
PCB
2,
РСВ
a.
Carefully
instructions
that
all
cables
properly.
b.
Replace
tions
<.
Replace
in
4.
Replace
in
κ.
Carefully
instructions
that
properly.
b.
Replace
tions
<
Replace
in
4.
Replace
instructions
front
in
Table
CPU
Table
4-1.
CPU
Table
4-1.
all
cables
front
in
Table
CPU
Table
power
4-1.
open
the
in
Table
are
panel
4-1.
PCB
PCB
open
the
in
Table
are
panel
4-1.
PCB
controller
in
Table
unit
per
4-1
and
verify
connected
per
instruc-
per
instructions
per
instructions
unit
per
4-1
and
verify
connected
per
instruc-
per
instructions
PCB
4-1.
per
15,
(Test
step
control
module
operational
16,
(Test
steps
voltage
readings
puts
58) All
are
60
and
fields
not
61)
Improper
at
analog
on
the
out-
a.
Unit
b.
Faulty
Figure
c,
Faulty
ule
4.
Faulty
Figure
a.
Fauliy
Figure
b.
Faulty
item
c.
Faulty
Figure
not
assembled
connector
4-5
keypad
item
10,
Figure
properly
PCB
in
control
4-5
CPUPCBinitem
4-3
CPU
PCBinitemli,
4-3
power
controller
7,
Figure
4-3
connector
4-5
PCB
item
14,
mod-
11,
PCB
item
14,
a.
Carefully
instructions
that
all
cables
properly.
=
Replace
instructions
c.
Replace
Table
4.
Replace
in
a.
Replace
in
b.
Replace
instructions
с.
Replace
instructions
keypad
4-1.
Table
Table
open
the
unit
in
Table
are
connected
connector
CPU
4-1.
CPU
4-1.
power
connector
PCB
in
Table
per
instructions
PCB
per
PCB
per
controller
in
Table
PCB
in
Table
per
4-1
and
verify
per
4-1.
in
instructions
instructions
PCB
per
4-1.
per
4-1.
3-10
Part
No.
Y-780551-00A
Rev.
B
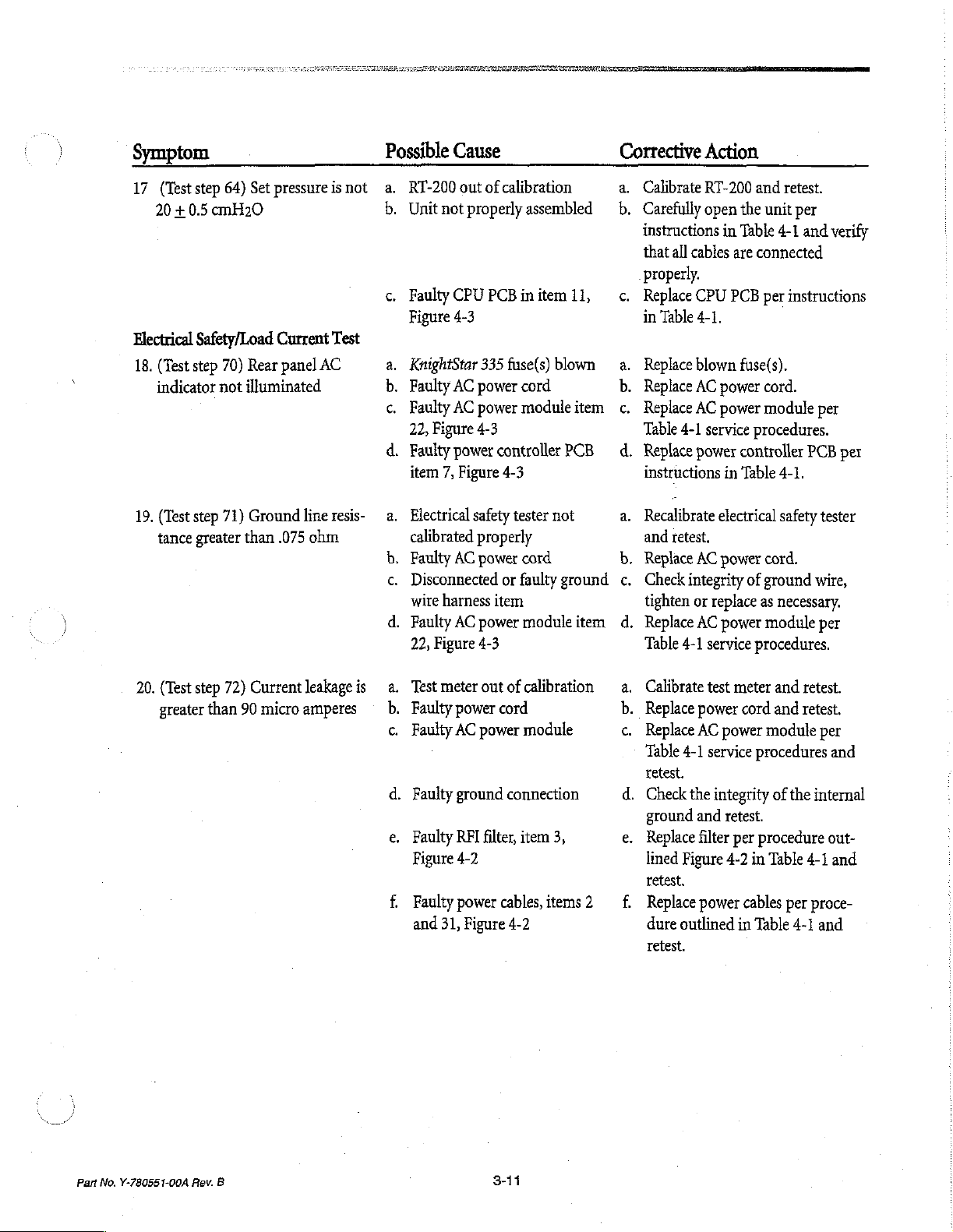
neo
`
Symptom
17
(Test
step
20 + 0.5
Electrical
18.
(Test
indicator
19.
(Test
tance
cmH20
Safety/Load
step
70)
not
step
71)
greater
64)
Set
pressure
Current
Rear
panel
illuminated
Ground
than
.075
AC
line
ohm
isnot
Test
resis-
Possible
а.
s
с.
a.
b.
с.
d.
a.
Cause
RT-200
Unit
Faulty
Figure
KnightStar
Faulty
Faulty
22,
Faulty
item
Electrical
out
not
properly
CPU
4-3
AC
AC
Figure
power
7,
Figure
calibrated
b.
Faulty
AC
с.
Disconnected
wire
harness
d.
Faulty
AC
22,
Figure
of
calibration
assembled o b.
PCB
initem
335
fuse(s)
power
cord
power
module
4-3
controller
4-3
safety
tester
properly
power
cord
or
faulty
item
power
module
4-3
11,
blown
item
PCB
not
ground
item
Corrective
a.
Calibrate
Carefully
instructions
that
all
cables
Action
RT-200
open
in
properly.
с.
Replace
in
a.
Replace
b.
Replace
с.
Replace
Table
d.
Replace
instructions
a.
Recalibrate
and
b.
Replace
c.
Check
tighten
d.
Replace
Table
CPU
Table
4-1.
blown
AC
AC
4-1
service
power
retest.
AC power
integrity
or
replace
AC power
4-1
service
power
power
in
electrical
and
retest.
the
unit
per
Table
4-1
and
are
connected
PCB
per
instructions
|
fuse(s).
cord.
module
procedures.
controller
Table
of
procedures.
PCB
4-1.
safety
cord.
ground
as
necessary.
module
verify
per
per
tester
wire,
per
20.
(Test
greater
step
72)
than
Current
90
micro
leakage
is a.
amperes
Test
b.
Faulty
c.
Faulty
d.
Faulty
e.
Faulty
Figure
f.
Faulty
and
meter
power
AC
power
ground
RFI
4-2
power
31,
Figure
out
of
calibration
cord
module
connection
filter,
item
cables,
4-2
a.
Calibrate
b.
Replace
с.
Replace
Table
retest.
d.
Check
ground
3,
e.
Replace
lined
retest.
items 2 (Of
Replace
dure
retest.
test
meter
power
cord
AC
power
4-1
service
the
integrity
and
retest.
filter
per
Figure
4-2
power
cables
outlined
in
and
retest.
and
retest.
module
procedures
of
procedure
in
Table
Table
per
the
internal
4-1
per
proce-
4-1
and
out-
and
and
Part
No.
Y-780551-00A
Rev.
B
3-11
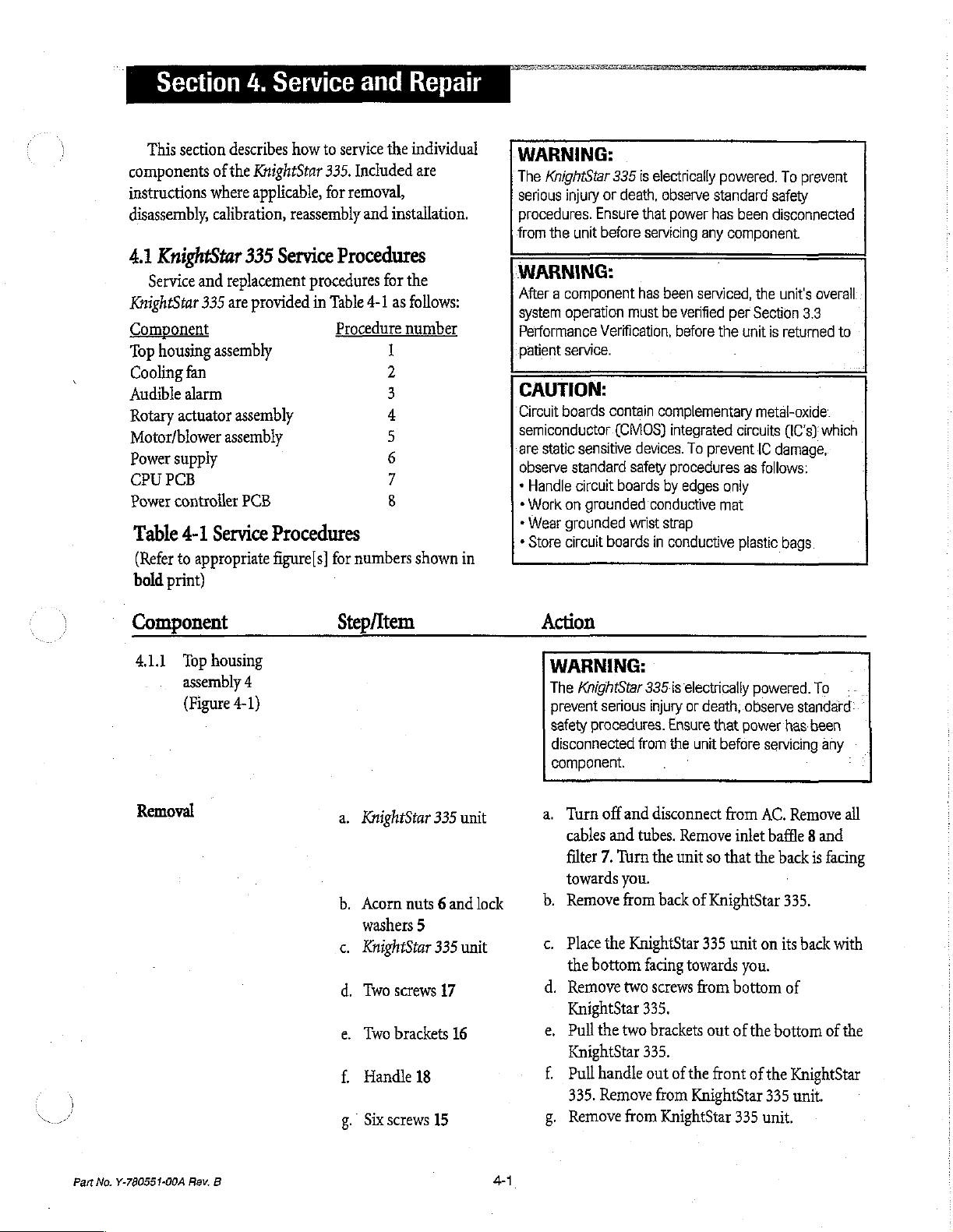
Section
4.
Service
and
Repair
[a
This
section
components
instructions
disassembly,
4.1
KnightStar
Service
KnightStar
Component
Top
housing
Cooling
Audible
Rotary
Motor/blower
Power
supply
CPU
PCB
Power
controller
Table
(Refer
bold
print)
actuator
4-1
to
describes
of
the
where
calibration,
and
replacement
335
are
assembly
fan
alarm
assembly
assembly
Service
appropriate
how
to
KnightStar
applicable,
335.
for
reassembly
335
Service
procedures
provided
PCB
in
Procedures
figure[s]
service
the
individual
Included
are
removal,
and
installation.
Procedures
for
the
Table
4-1
as
follows:
Procedure
for
numbers
number
1
NN
a
U qa
03d
shown
in
WARNING:
The
KnightStar
serious
procedures.
from
WARNING:
After a component
injury
the
system
operation
Performance
patient
service.
335
or
death,
Ensure
unit
before
Verification,
CAUTION:
Circuit
boards
semiconductor.
are
static
observe
*
Handle
*
Work
*
Wear
*
Store
contain
(CMOS)
sensitive
standard
circuit
boards
on
grounded
grounded
circuit
boards
ts
electrically
observe
that
power
servicing
has
been
must
be
verified
before
complementary
integrated
devices.
safety
wrist
To
procedures
by
edges
conductive
strap
in
conductive
powered.
standard
has
been
any
component.
serviced,
per
Section
the
unit
circuits
prevent
as
only
mat
plastic
To
prevent
safety
disconnected
the
unit's
overall
3.3
is
returned
metal-oxide
(IC's}
which
IC
damage,
follows:
bags
to
Component
4.1.1
Top
assembly
(Figure
Removal
housing
4
4-1)
Step/Item
a.
KnightStar
b.
Acorn
nuts 6 and
washers
с.
KnightStar
d.
Two
e.
Two
f.
Handle
g.
Six
5
screws
brackets
18
screws
335
335
17
16
15
unit
lock
unit
Action
WARNING:
The
KnightStar
prevent
safety
disconnected
component.
a.
>
c.
d.
e.
f.
g.
serious
procedures.
Turn
off
cables
and
filter
7.
Turn
towards
Remove
Place
the
the
bottom
Remove
KnightStar
Pullthe
KnightStar
Pull
handle
335.
Remove
Remove
335s
electrically
injury
or
Ensure
from
the
unit
and
disconnect
tubes.
Remove
the
unit
you.
from
back
of
KnightStar
facing
towards
two
screws
335.
two
brackets
335.
out
of
the
from
KnightStar
from
KnightStar
powered.
death,
observe
that
power
before
servicing any
from
AC.
inlet
so
that
the
KnightStar
335
unit
on
you.
from
bottom
cut
ofthe
front
of
the
335
335
unit.
To
standard
has-been
Remove
baffle 8 and
back
is
facing
335.
its
back
with
of
bottom
of
the
KnightStar
unit.
all
Part
No.
Y-780551-00A
Rev.
B
41