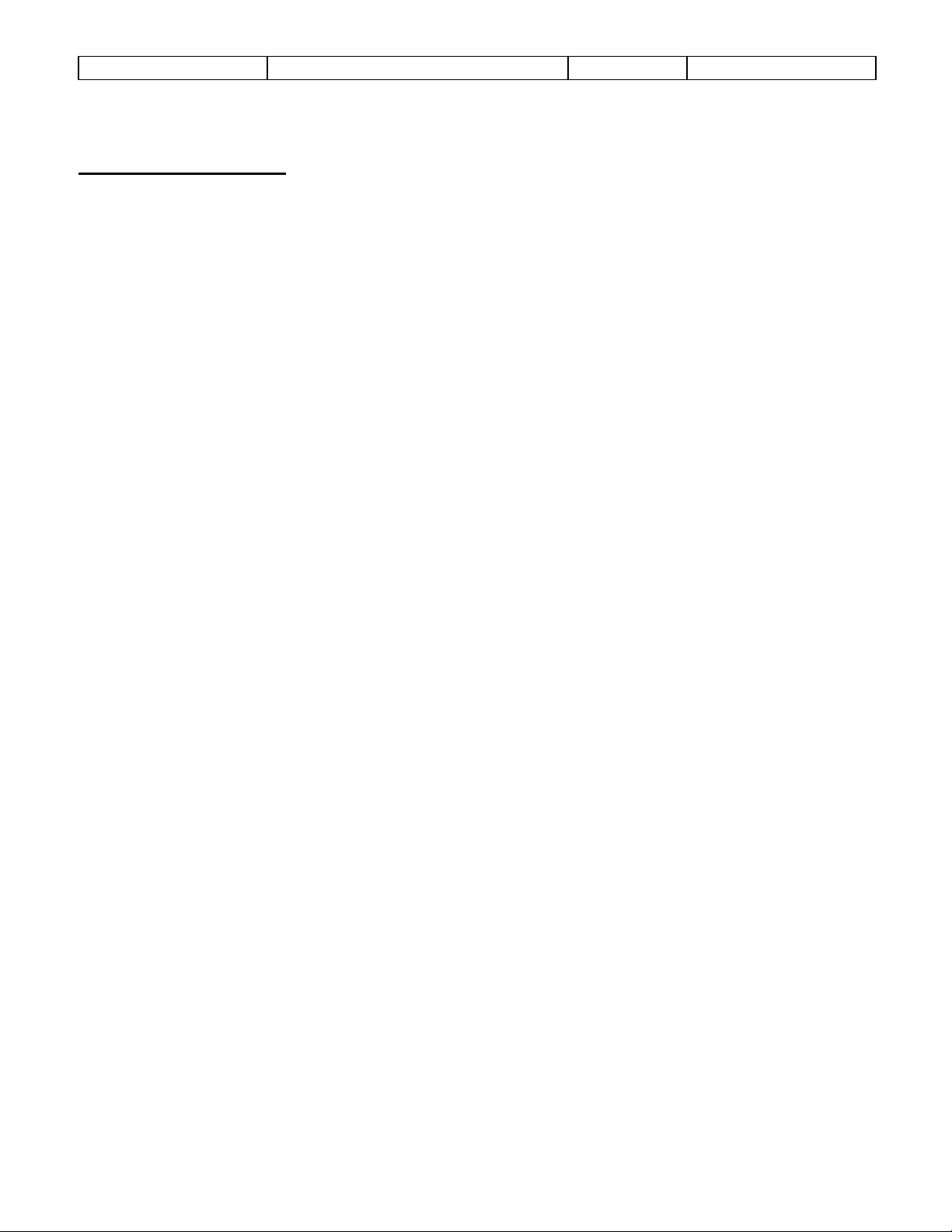
Minimum = 7 V + (20mA X RL)
4mA @ 0 Hz, 20mA @ desired full scale frequency
Mounts directly on flowmeter
FM Approved, CSA Certified
SPECIFICATIONS
Operating -40 to 85°C
Storage -65 to 125°C
Maximum = 28 V + (4mA X RL)
Protected against polarity reversal
Signal Input:
Amplitude 50 mV – 35 V sine or square wave
Sensitivity field adjustable
Impedance 50K
Analog Output
Full scale range -- 100 Hz-10 KHz selectable
Response time -- 95% of change in 1 second
Linearity -- .3% F/S
Tempco -- < 2% of reading over entire temperature range
Class I Groups B, C, D
Class II Groups E, F, G
The SP712-2 is a 2-wire loop powered analog transmitter designed to linearly convert a
frequency input to an equivalent 4-20mA current output. When it incorporates with a turbine
flowmeter a current representation proportional to flow is obtainable. Data transmission in a
current format exhibits excellent noise immunity and the capability of long distance
transmission.
A full-scale frequency range of 100 Hz-10 KHz is selectable, via S1. The span adjustment
establishes the frequency point at which a 20mA output is achieved. The sensitivity adjustment
permits the SP712-2 to discriminate between a signal input and noise by increasing (CCW) or
decreasing (CW) the input signal amplitude necessary to process a valid signal. ‘Test’ S2 when
depressed, illuminates D1 if loop voltage and input signal both are present.
Installation of the SP712-2 requires only 2 wires because it is a true 2-wire transmitter: input
power and signal output utilizes the same wires.
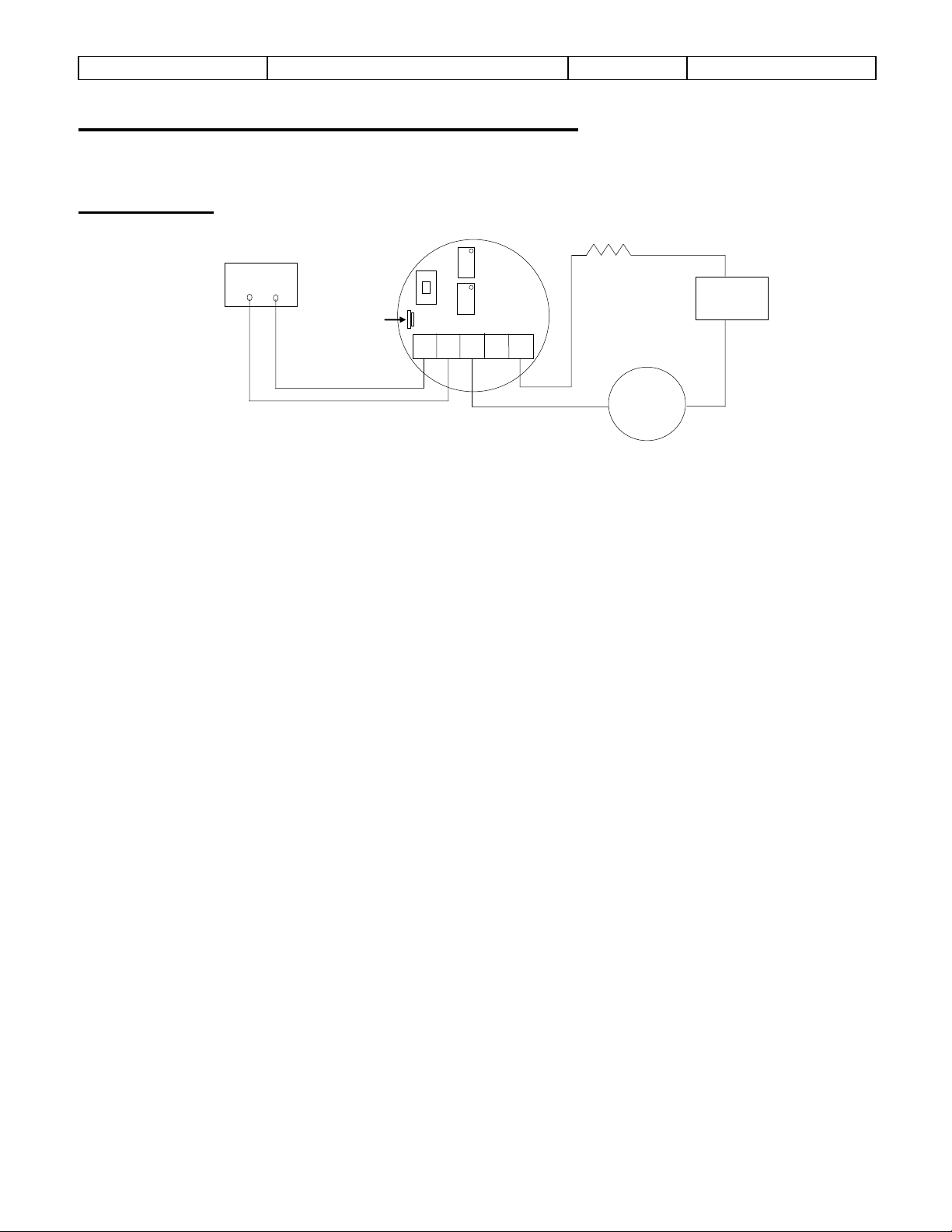
Connect DMM positive lead to power supply positive, connect DMM negative lead to J1-3,
set DMM function to mA DC
Connect power supply negative lead to 250 Ω resistor, connect other r esist or leg to J1-5
Connect frequency generator posit ive & negat ive leads to J1 -1,2; respectively. Set output
to sinewave & amplitude to zero
Set S1 for desired freq uency range
Turn power supply & frequency generator ‘ON’, DMM should indicate approximately
4.00mA
Adjust ‘ZERO’ (R25) for 4.00mA DMM indication (record data)
Set ‘Sensitivity’ adjust (R1) fully clockwise
Adjust signal amplitude of f r equency generator to 50mv & freq uency to m aximum desir ed
point (full scale frequency) ( r ecor d data)
Reduce signal amplitude of freq uency g ener ator to zero, adjust ‘ZERO’ (R25) for 4. 00mA
DMM indication if necessary
Adjust signal amplitude of f r equency generator to 50mv, adjust ‘SPAN’ (R19) for 20.00mA
DMM indication if necessary
Adjust frequency of frequency generator to exactly 50% of maximum frequency point in
frequencies(record dat a)
6 + 4 = 10; DMM should indicate 10.00mA @ 750 Hz input
B ENCH TEST CALIBRATION PROCEDURE
Required Equipment: Power Supply 12-28v, Digital Multimeter (DMM), Frequency Generator, &
Frequency Counter
Test Procedure:
Gen/Ctr
0 = 100-1000Hz
1 = 1 KHz-10KHz
SENSITIVITY
Z
E
R
S
P
SP712-2
A
R1
N
Supply
~
DC
E)
H)
Adjust ‘SPAN’ (R19) for 20.00mA DMM indication (record data)
K)
step H, DMM should indicate 12.00mA ± .06. Repeat for 25% & 75% full scale
To check linearity @ any frequency point, incorpor at e t he following formula:
(F/F
X 16) + 4 = mA
max
(Where F = Flowrate frequency in Hz)
(F
= Frequency in Hz at which 20mA is set)
max
Ex. Assume maximum frequency point = 2000 Hz (20.00mA) Check for linearity @ 750
Hz point
750/2000 = .375
16 X .375 = 6
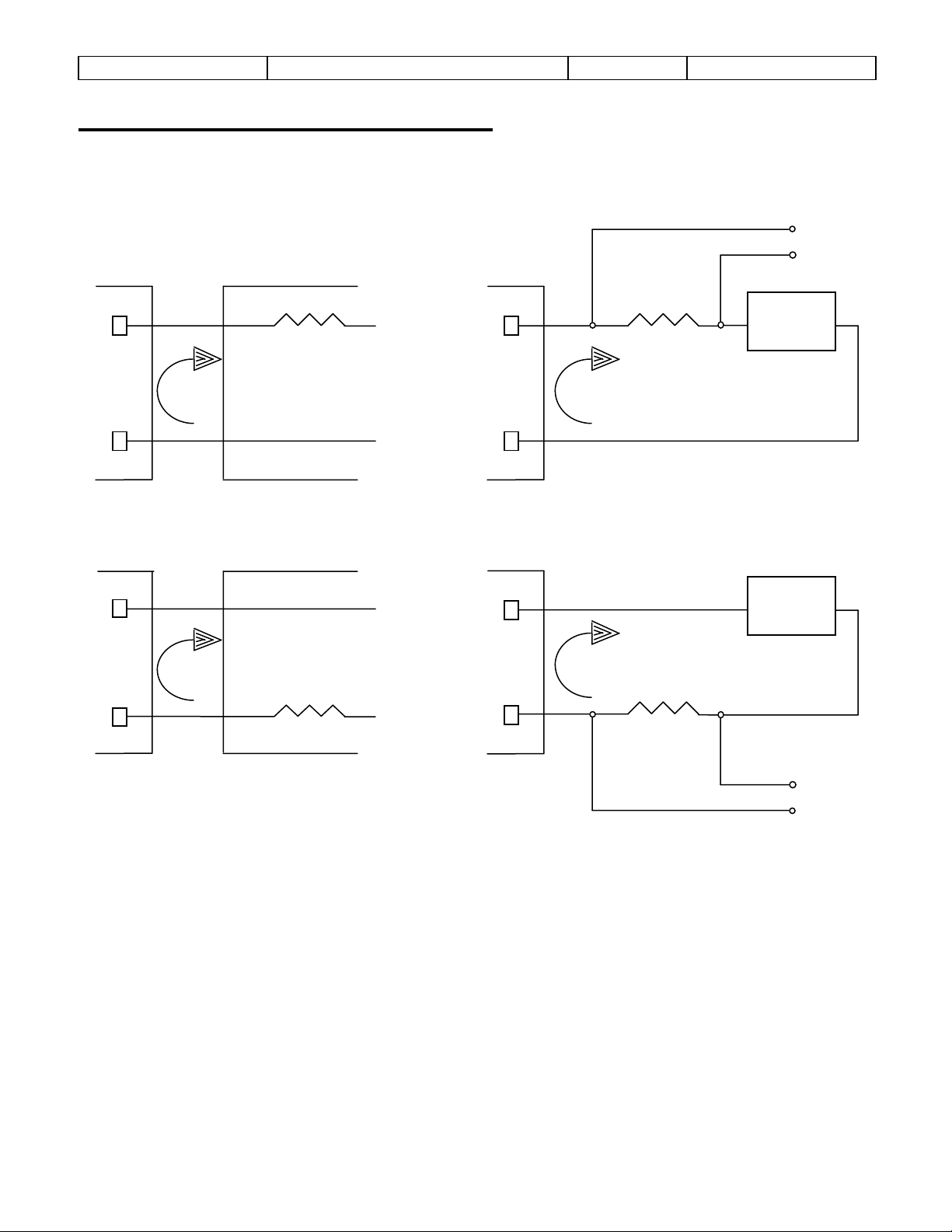
TYPICAL LOOP CONFIGURATIONS
POWER
SUPPLY
POWER
SUPPLY

NOTE: DIMENSIONS ARE IN INCHE S
D1 WILL ILLUMINATE IF
SIGNAL AND POWER BOTH
PRESENT WHILE S2 IS
DEPRESSED