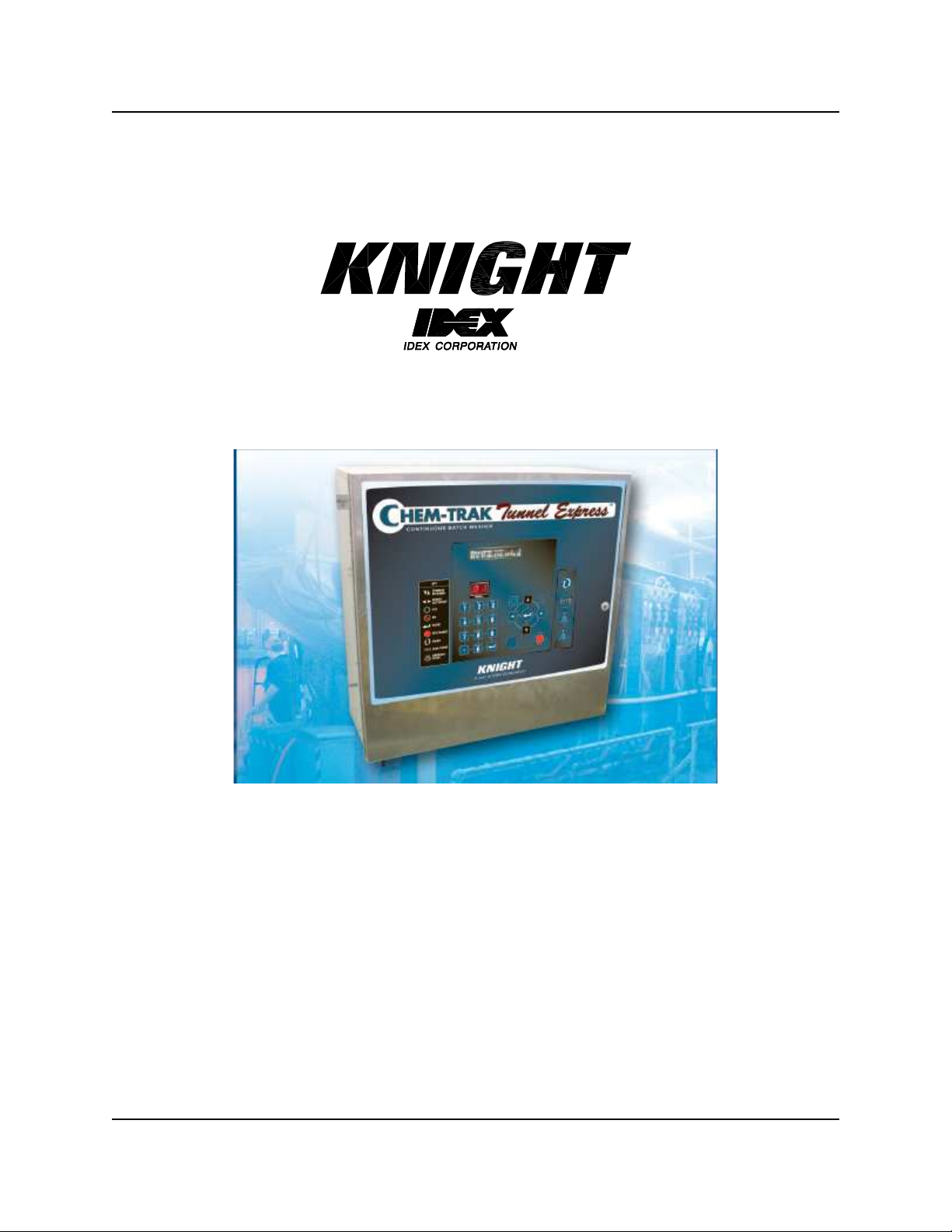
Chem-Trak Tunnel
Installation & Operation
0900854 Rev: REL (12/07) Page 1 of 12
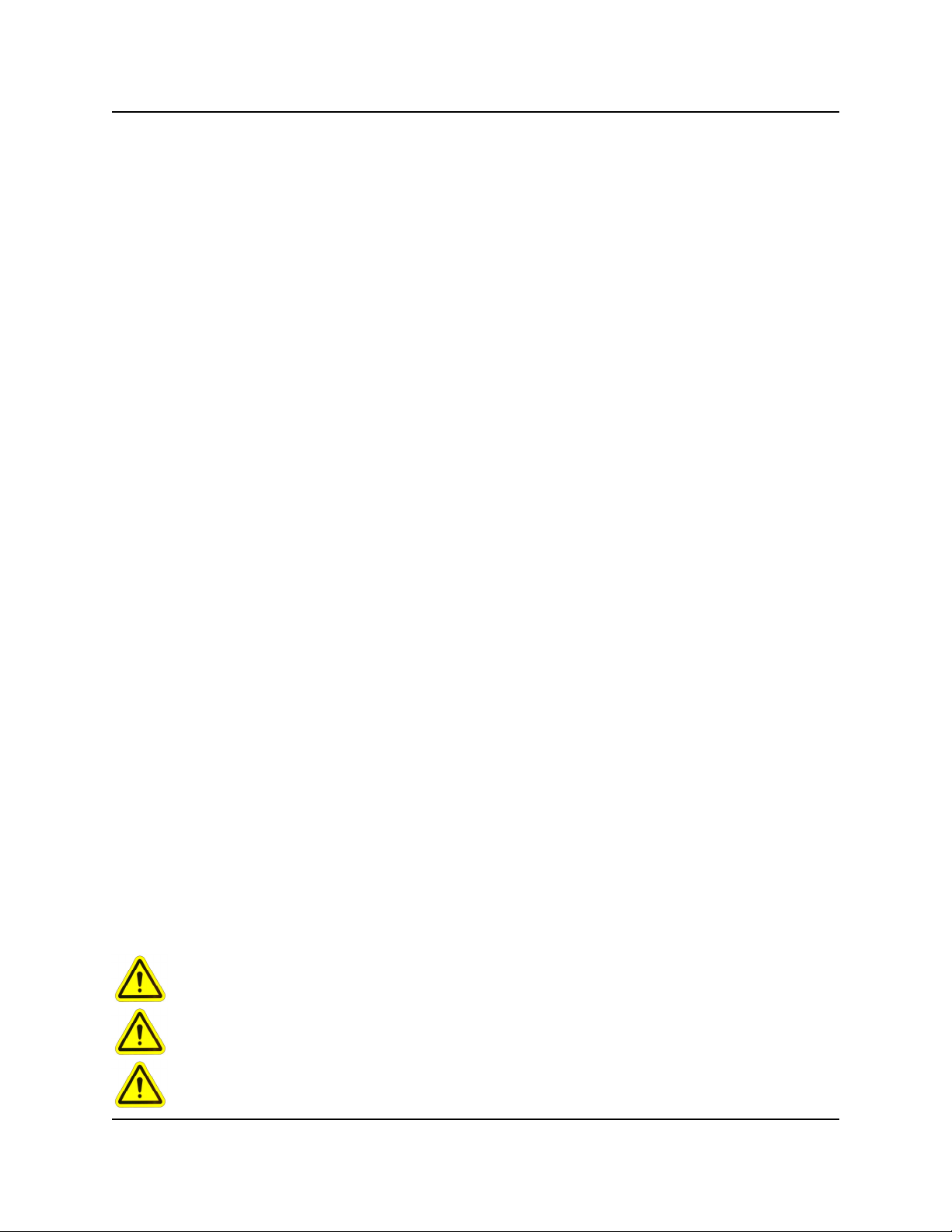
TABLE OF CONTENTS
System Overview.................................................................................................. 3
System Components ............................................................................................ 3
System Components (pictures) ............................................................................ 4
Pre-Installation...................................................................................................... 5
Control Box & Power Supply Installation .............................................................. 5
Peristaltic Pump Installation (optional).................................................................. 5
Air Pump Installation (optional)............................................................................. 6
EDP Pump Installation (optional).......................................................................... 6
Flush Manifold Installation (optional) .................................................................... 7
Wiring Diagram..................................................................................................... 8
EDP Wiring Diagram ............................................................................................ 9
SIB Installation.................................................................................................... 10
Module Injection Assembly (optional) ................................................................. 11
Warranty Information .......................................................................................... 12
Knight Locations ................................................................................................. 12
CAUTION: Wear protective clothing and eyewear when dispensing chemicals or
other materials. Observe safety handling instructions (MSDS) of chemical mfrs.
CAUTION: To avoid severe or fatal shock, always disconnect main power when
servicing the unit.
CAUTION: When installing any equipment, ensure that all national and local
safety, electrical, and plumbing codes are met.
Page 2 of 12 0900854 Rev: REL (12/07)
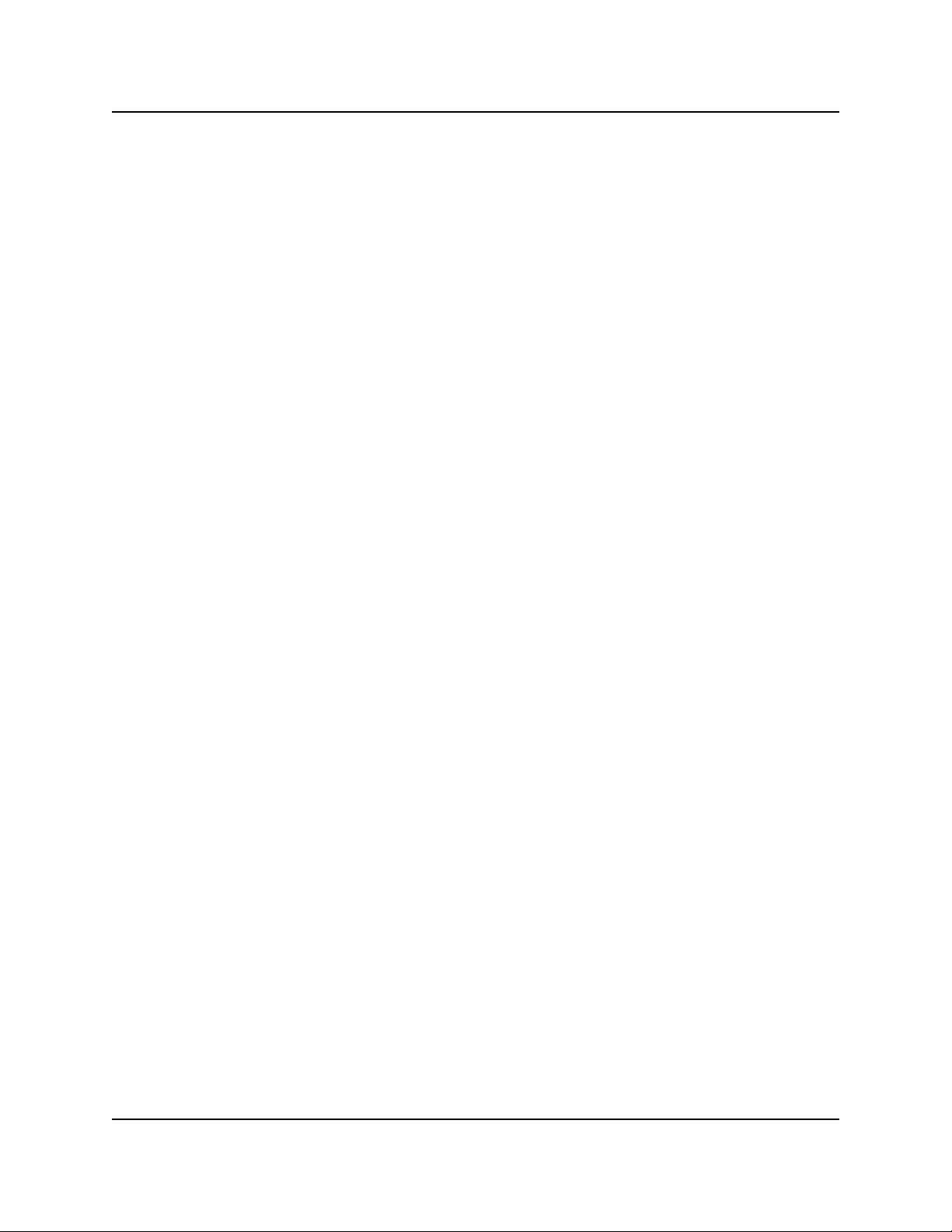
INTRODUCTION
Chem-Trak Tunnel Express is the ultimate in modularity, allowing versatile configurations to fit your laundry tunnel.
With the ability to add various pumps, valves, and other accessories, Chem-Trak Tunnel Express ensures consistent
wash quality and predictable costs in any plant.
•
Can run up to 12 chemical pumps (without flush) or 10 chemical pumps (with flush)
•
The only tunnel dispenser system with AODD and EDP available: Air Operated Double Diaphragm Pumps (6.8
GPM)(25.7 LPM) and Electric Diaphragm Pumps (3.2 GPM)(12.1 LPM)
•
Less service and maintenance is required with the AODD and EDP pumps because there are no tubes that need to
be replaced
•
High speed injection with flow rates up to 12 GPM (45.4 LPM) with improved accuracy / resolution of chemical
dosing (+/- 2%)
•
Exclusive module injection assembly allows for simple, fast, and non-invasive one person calibration
•
Precision metering of pumps to +/- .10 oz/second
•
Flush or no flush configurations
•
Simple, multi-lingual control panel (English, Spanish, French, German, Italian, Dutch)
•
Data management reports (Excel)
•
Networkable with multi-washer and conventional Knight dispensers
SYSTEM COMPONENTS
See the diagram on the following page for identification of the system components listed below. The available pump
options for the Chem-Trak Tunnel system consist of Air Operated Diaphragm, Peristaltic, or Electric Diaphragm. If
necessary, various pump configurations can be utilized to meet specific application requirements.
(A) Power Supply: (not shown) Isolates high voltage system operating power from the control box. The power
supply box contains a transformer and electrical noise filter for added protection.
(B) Control Box: Contains all system electronics and is the main command center for operation. The keypad allows
programming of all system operating parameters. Also housed inside the control box are an air filter, air
solenoids, and water flush valves.
(C) Air Operated Diaphragm Pumps: Available in 3/8” for tunnel wash applications. Use of air operated diaphragm
pumps provides high volume product delivery up to 6.8 GPM with a wide range of chemical compatibility. The
pumps are controlled via air solenoids in the system control box.
(D) Peristaltic Pumps: Available in 155 oz/min or 226 oz/min configurations. Use of peristaltic pumps provides easy
installation and maintenance, and does not require an air supply. The pumps are controlled via POB circuit board
inside the peristaltic pump cabinet.
(E) Electric Diaphragm Pumps: Available in .66 GPM (76 oz/min) and 1.5 GPM flow rates. These pumps are
controlled via the POB circuit board. A separate POB Enclosure is available for this application, or the pumps
can utilize extra (unused) pump outputs on a POB board that is inside of a peristaltic pump cabinet.
(F) Flush Manifold (optional): Used for diluting chemicals with water. The system has two separate water flush
solenoids that can be setup for single or dual manifold configuration. The use of flush manifolds allows water
flush delivery to multiple injection points on the tunnel washer.
(G) SIB Module: The SIB signal input module provides an interface between the Chem-Trak Tunnel system and
external washer signals. Connection from the SIB to the Chem-Trak Tunnel control box is through low voltage
data cable.
(H) High Voltage POB Box: The Pump Output Board mounted in a separate stainless steel enclosure controls on-
off operation of electric diaphragm pumps and isolates all high voltage from the main controller.
(I) Manifold Injection Assembly: Controlling pump flow rates and calibrating pumps is easy with this key system
component. A special ball metering valve provides variable orifice diameters that control the flow rate of chemical
from an air operated or electric diaphragm pump.
0900854 Rev: REL (12/07) Page 3 of 12
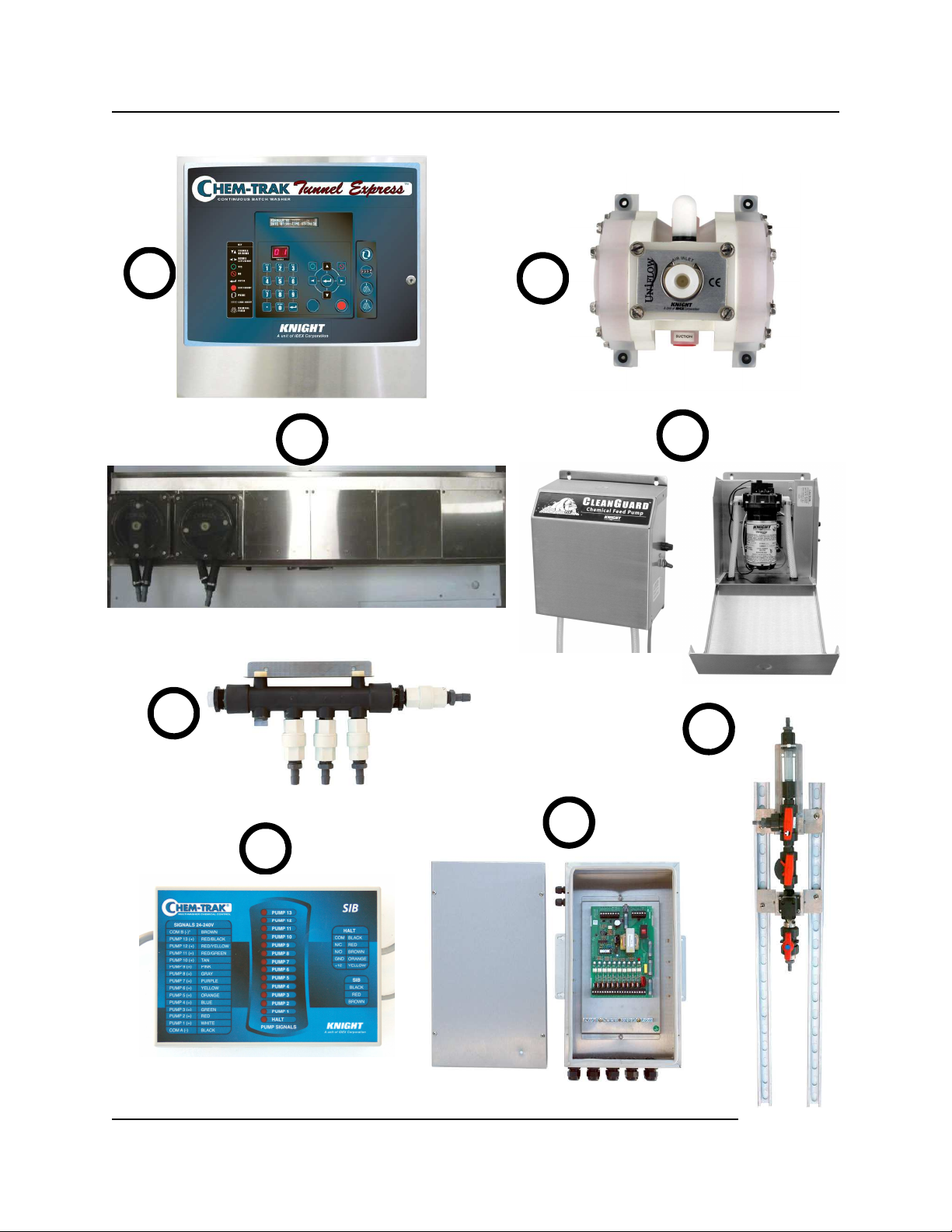
SYSTEM COMPONENTS
B
F
D
C
E
I
H
G
Page 4 of 12 0900854 Rev: REL (12/07)