
GE Oil & Gas
Masoneilan* Products
78400/18400 Series LincolnLog
High-Pressure, Anti-Cavitation Control Valves
Integrated smart engineered
solutions for severe service
applications
*
• Long term reliability
• Longer service life
• Industry leading
technology
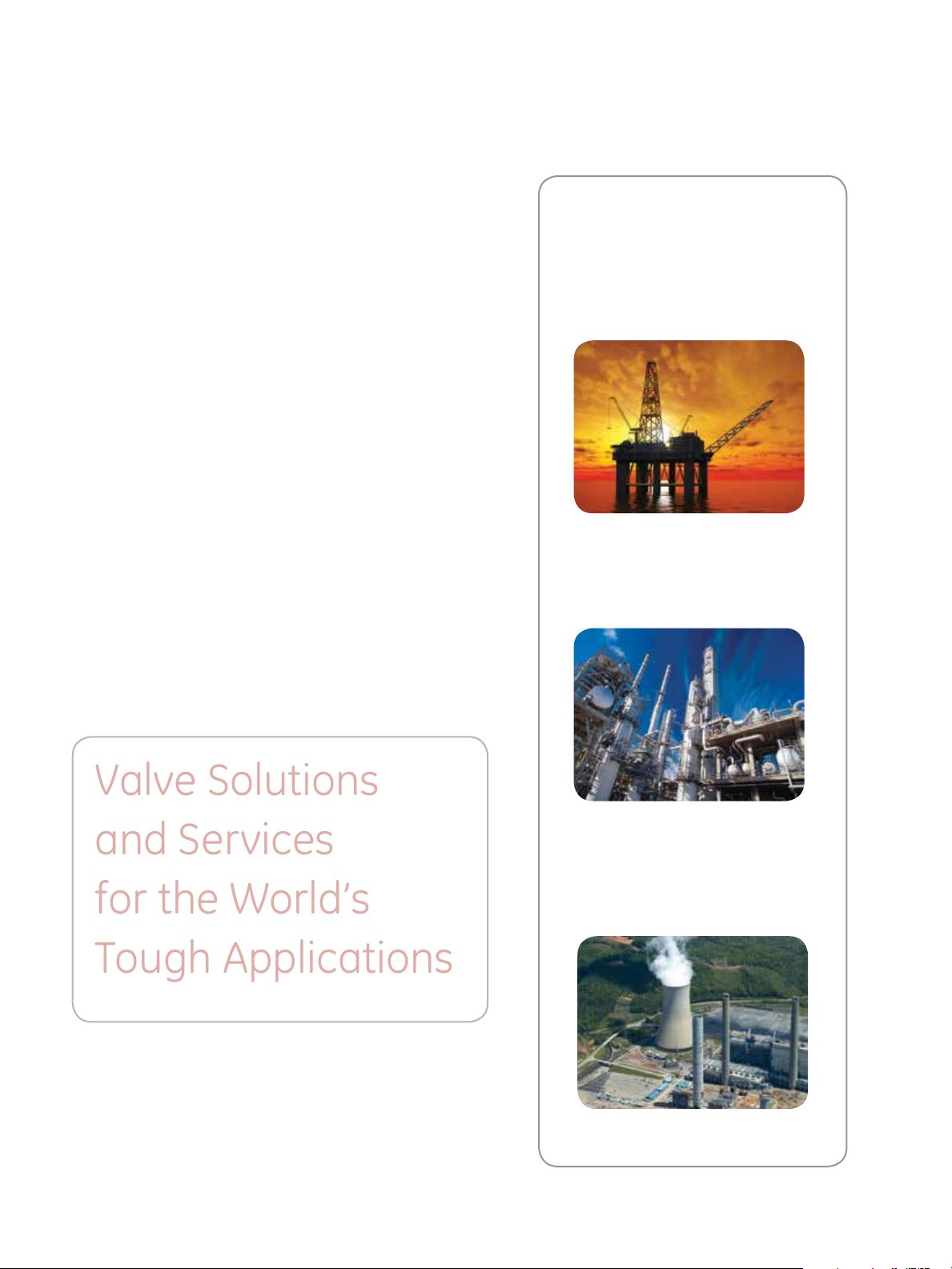
LincolnLog Reliability
Valve Solutions
and Services
for the World’s
Tough Applications
Long-term Reliability
The Masoneilan LincolnLog valve from GE Oil & Gas offers longterm reliability in high-pressure, liquid-letdown, anti-cavitation
control valve applications. Engineering knowledge and
expertise has made us a leader in control valve applications
with products such as Flexible Better Fit severe-service
solutions. The LincolnLog valve is a control valve solution of
choice throughout the wide spectrum of severe-service liquidflow applications.
Proven Performance
The Masoneilan LincolnLog valve design has more than 20
years of proven field performance as the industry’s premier
high-pressure, liquid-letdown solution. The Masoneilan
LincolnLog is a reliable and robust anti-cavitation control
valve package with enhanced multi-stage and axial flow-trim
technology incorporated into a rugged valve design. Over the
years, the LincolnLog valve has successfully met the challenges
of thousands of severe-service applications around the globe.
Industries and Applications
UPSTREAM OIL and GAS
REFINING
• Pump Recirculation
• Produced Water Injection
• High Pressure Separator
• Rich Amine Service
• Cold High Pressure Separator Letdown
2 | GE Oil & Gas
POWER GENERATION
• Pump Recirculation
• Boiler Feedwater StartUp
• High Pressure Spraywater Control
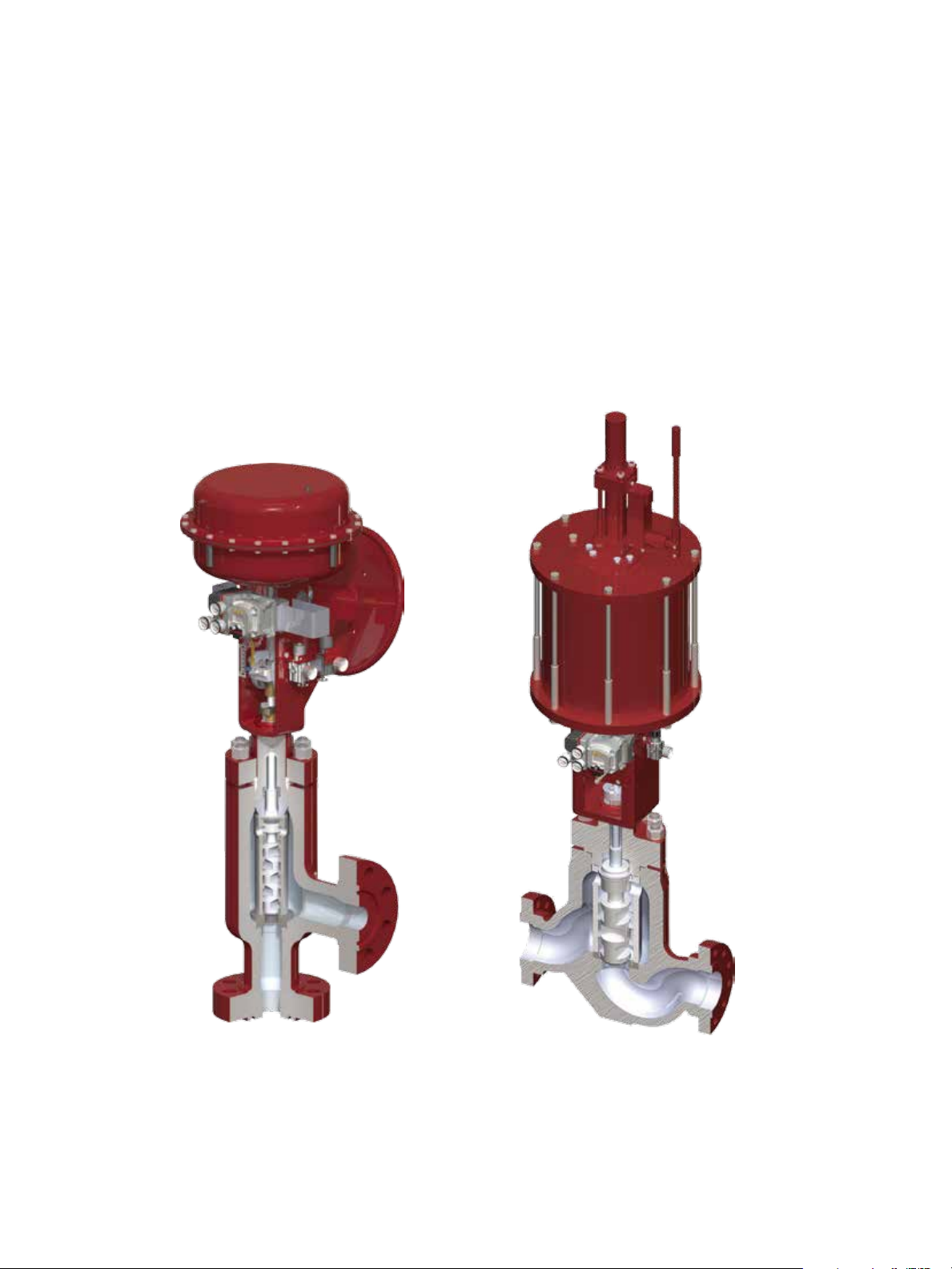
Innovative Solutions
Meeting Exacting Industry Specifications
The LincolnLog* valve is available in a variety of body
configurations, sizes, materials, ratings and trim types. The wide
variety of trim designs in the LincolnLog valve includes options
that offer up to a 150:1 turndown ratio, enabling response to a
wide range of process conditions. With a number of combinations
of forged or cast valve bodies, standard or exotic alloys, API or
ANSI-rated construction, and globe or angle configurations,
the LincolnLog valve meets or exceeds exacting industry
specifications such as corrosive service (NACE) and Pressure
Equipment Directive (PED) compliance.
78400 Series
Angle Style LincolnLog
18400 Series
Globe Style LincolnLog
78400/18400 Series LincolnLog High Pressure, Anti-Cavitation Control Valves | 3
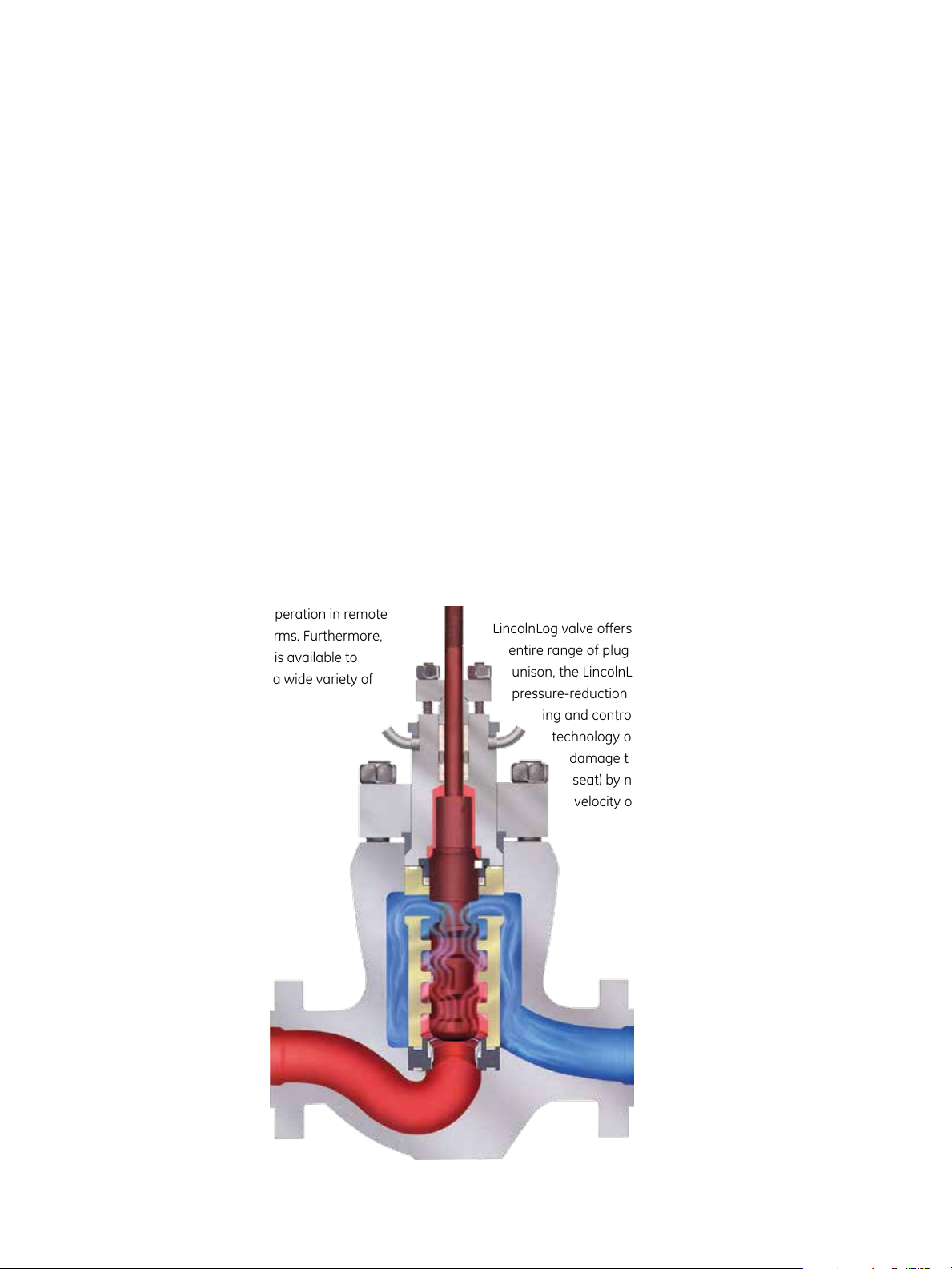
Reliability in Performance
Reliable, Long Term Performance
The leading cause of poor control valve performance and
premature failure in high-pressure, liquid-letdown service
is cavitation. Some liquid applications cavitate so severely
that the valve can experience diminished performance or
even mechanical failure within hours of commissioning. The
multistage design of the LincolnLog valve reduces cavitation
by directing the fluid through a series of three-dimensional,
high-impedance pressure-reduction areas, or stages. This
highly tortuous flow path helps prevent cavitation by managing
the pressure reduction and fluid velocity through every stage,
promoting repeatable performance during the valve’s life.
The LincolnLog valve offers reliable, long-term performance
in the most extreme applications such as inaccessible
high-pressure, liquid-letdown, wellhead-injection valves.
The LincolnLog anti-cavitation control valve can be custom
engineered with as many as 10 stages of pressure reduction
for applications with extreme pressure drops in excess of 8000
psi (550 Bar). These valves control the pressure drop
in multiple stages for confident operation in remote
locations such as offshore platforms. Furthermore,
a flexible range of staging ratios is available to
customize the pressure drop for a wide variety of
fluids and conditions.
Multi-Stage, Axial Flow Technology
High trim velocity can intensify cavitation damage inside the
control valve. This damage is common in many single-stage
valve designs, which take the full pressure drop across a single
region within the trim. This single region is typically the leading edge of the plug and seat — an area that experiences the
highest velocity. Consequently, it receives the most severe and
excessive damage.
Similarly, many radial trim designs, such as drilled- hole cages
and stacked disks, often experience the same fate under
extreme pressure drops. Unlike the axial flow design of the
LincolnLog valve, many radial designs throttle the pressure
drop at the innermost radial stage adjacent to the plug-seating
surface. When this radial trim is only partially open, the outermost stages are oversized, essentially becoming inactive and
voiding any intended staging. In this case, the full pressure
drop is taken across the final stage, resulting in high energy
release right at the controlling and seating surface of the plug.
In contrast, the axial flow design of the GE Oil & Gas;s
LincolnLog valve offers reliable performance throughout the
entire range of plug travel. By throttling at all stages in
unison, the LincolnLog valve reduces short-circuiting of any
pressure-reduction stage, decreasing wear along the lead-
ing and controlling edge of the plug. The axial flow
technology of the LincolnLog valve helps eliminate
damage to any controlling surface (plug, cage or
seat) by not exposing any one stage to excessive
velocity or the full pressure drop.
4 | GE Oil & Gas
Axial Flow Technology