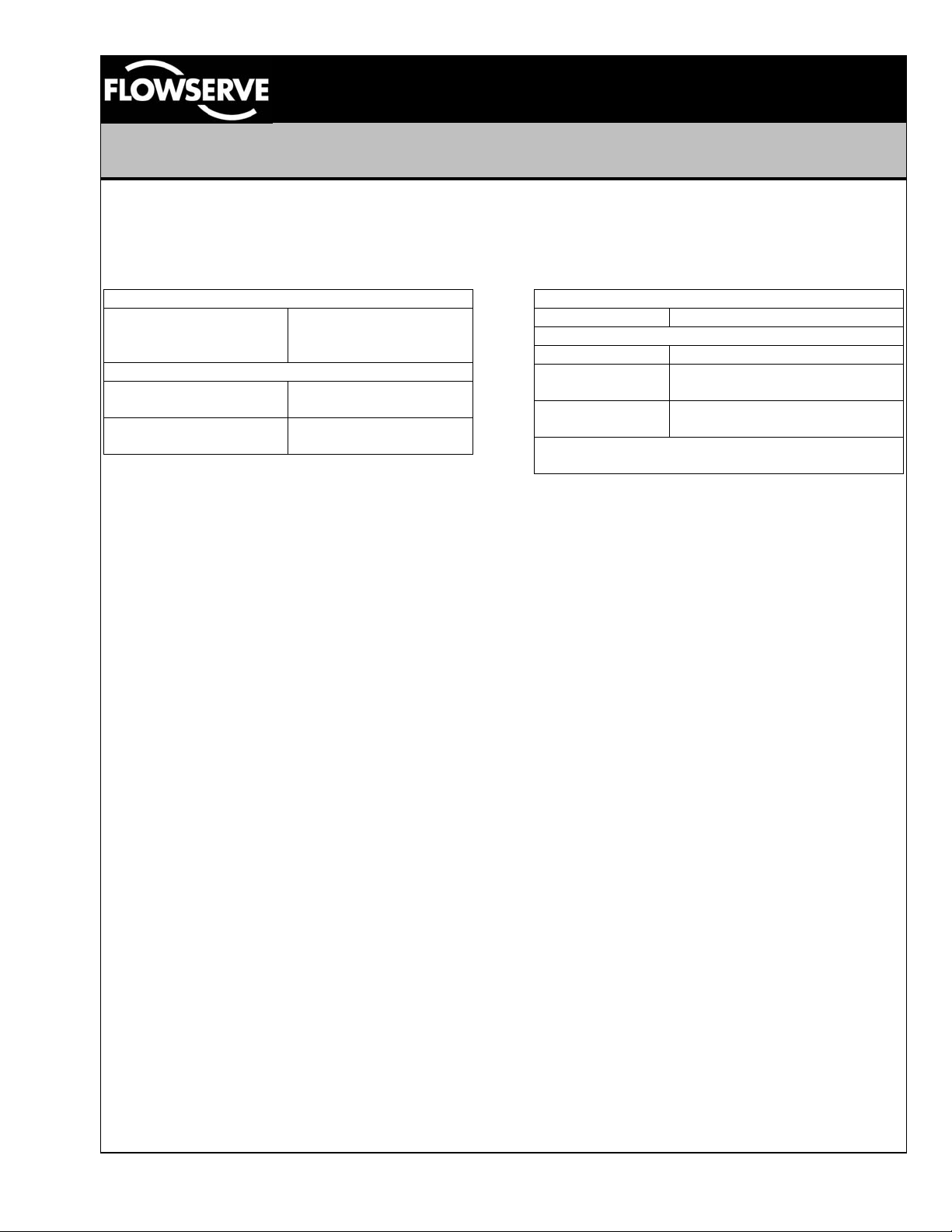
Automax BUSwitchTM – Profibus-DP
Flowserve Corporation
Flow Control Division
Installation, Operating & Maintenance Instructions
Electronic Printed Circuit
Board Specifications
Power requirements
XA0231 Profibus-DP
Interface Card
Temperature
Operational
† To operate, an external 24 VDC source must be locally
supplied to the interface card.
†
Storage
- 675 mA max with
solenoid activated.
-40 °F to +185 °F
(-40 °C to +85 °C)
-40 °F to +250 °F
(-40 °C to +120 °C)
Principles of Operation
Flowserve’s BUSwitch is a valve automation and
control product that uses the Profibus-DP
communication protocol to operate and monitor
position as well as provide predictive and
preventative maintenance functions. In response to
a command from the operator, the BUSwitch
energizes the appropriate solenoid valve, which
shifts a spool valve, directing the pneumatic force to
the appropriate actuator port, thereby operating the
valve actuator.
solenoid coil is mounted internal to the BUSwitch
housing to protect it from the environment. A 4-way
spool valve is bolted externally to the housing. The
fail direction of the actuator can be established
based on which set of terminals (open or closed) the
solenoid coil is connected to. For dual coil
operation, externally mounted solenoid valves must
be used as the housing will not accommodate two
internal coils. Upon reception of an open or close
command, a timer is started whose value is
compared to a user-defined setpoint for that
particular operation. If this timer value exceeds the
setpoint, an alarm is sent back to the control
operator to indicate a possible problem exists at the
valve. In addition, an odometer counter totals the
number of transitions the valve has made, which is
then compared to a user-defined limit. If this limit is
exceeded an indication is sent back to the control
operator. The odometer limit can be reset by the
control operator after maintenance has been
performed. During operation the valve status (open,
closed or in-transit) is continuously available to the
control operator. The Profibus-DP Interface Board
(XA0231) requires 24 VDC at 175 mA maximum.
For single coil operation, the
765 South 100 East
Provo, Utah 84606
www.flowserve.com
24 VDC
Email: actuators@flowserve.com
Phone: 801 373 3028
Facsimile: 801 489 2228
Profibus
Information
Manufacturer
Device
GSD File AMAX0867.GSD
Firmware
Revision
Transmission
GSD file supplied on diskette included with every
device.
ID 0867 (Hex)
Speed
12 MBaud maximum
Current consumption with a solenoid activated will
be the sum of the solenoid current plus 175 mA.
Mechanical Installation
Installation is best performed with Flowserve
NAMUR mounting kits. These kits allow direct
mounting of the BUSwitch shaft to the actuator
pinion without a coupler. The NAMUR mounting kits
will work with any actuator conforming to the
NAMUR standard for accessory mounting hole
locations and pinion dimensions. Simply attach the
bracket to actuator and BUSwitch to the bracket with
the included fasteners. The BUSwitch shaft features
an integral alignment pin that engages the tapped
pinion hole. Flowserve also offers a full line of nonNAMUR kits.
Spool and Tubing Configuration
1. For spring return actuators, a 4-way spool valve
is provided with port #2 plugged. For double
acting actuators, the same valve is provided with
no plugs. Make sure the correct spool is
selected before installing tubing. (Note: the
Flowserve APS2 purge module can be supplied
on spring return actuators to purge the spring
chamber with supply air.)
2. Make sure all air pressure is removed before
installing tubing.
3. Attach tubing according to Figures 1 or 2 below,
depending upon application. Attach supply
tubing to Port 1 and use 3 and 5 for exhaust.
4. To prolong actuator life use only clean, dry plant
air. Lubricated air is not required, although it is
recommended, particularly for high cycle
applications.
1.13
LML0012-0 8/99 Page 1 of 6
©1999, Flowserve Corporation, Provo, Utah
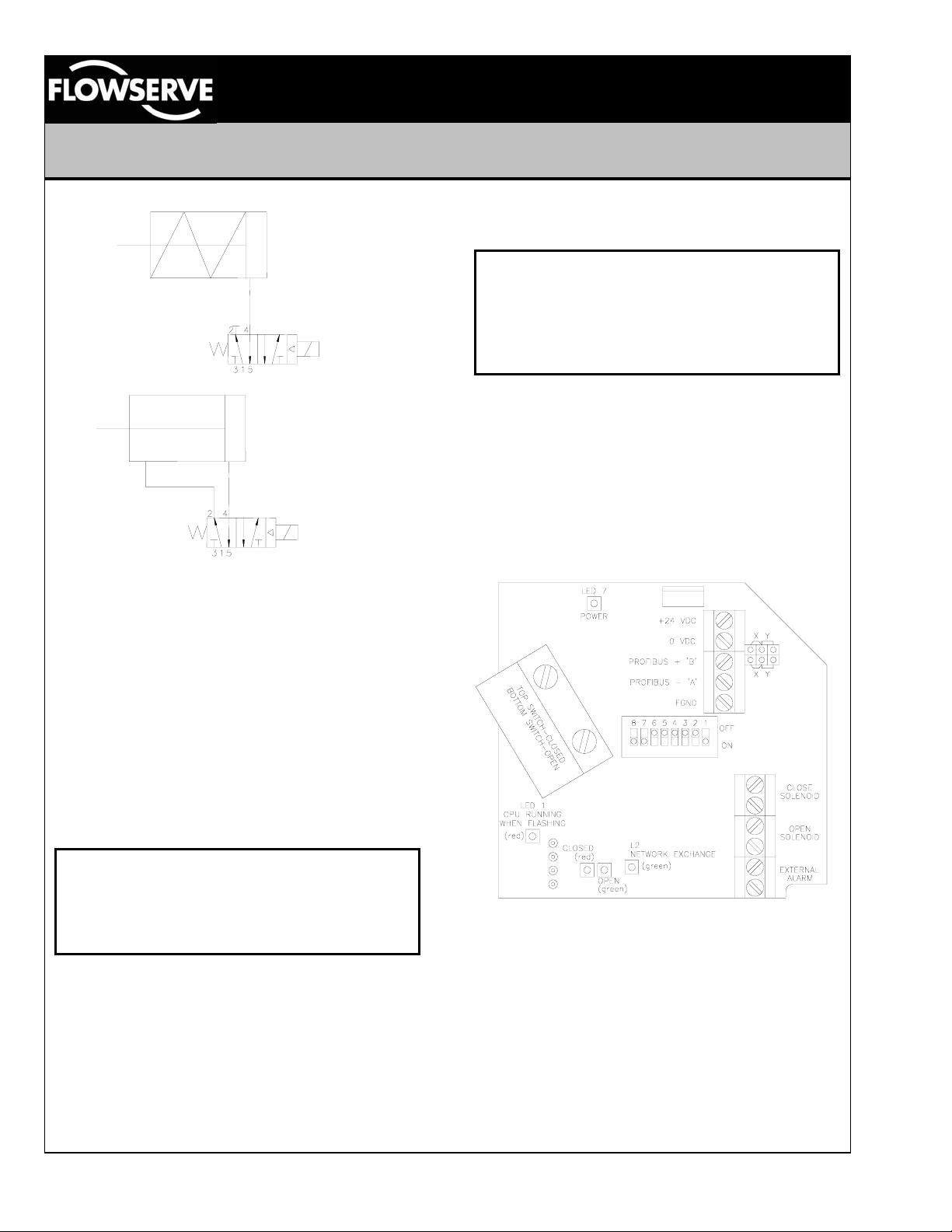
Flowserve Corporation
Flow Control Division
Automax BUSwitchTM – Profibus-DP
765 South 100 East
Provo, Utah 84606
www.flowserve.com
Email: actuators@flowserve.com
Phone: 801 373 3028
Facsimile: 801 489 2228
Figure 1
Figure 2
Lubrication
All BUSwitch™ spool valves are pre-lubricated and
will operate dry (with no additional lubrication). The
use of lubricated air will not interfere with the
BUSwitch’s functioning. If air lubrication is used, the
oils listed below are popular, easily obtainable, fluids
that are recommended for use with the BUSwitch
spool valve: Gulf Harmony 47, Mobil DTE Medium,
Shell Tellus 29, Texaco Rondo B, Sohivis 47 and
Sunnis 921. Many other lubricants are acceptable
providing they do not contain detergents that will
attack Buna-N or Viton Seals.
Electrical Connections
marked ‘OPEN’ and ‘CLOSE’. External power (24
VDC) is connected to the indicated location.
CAUTION
BE SURE TO OBSERVE CORRECT POLARITY
OF THE EXTERNAL POWER CONNECTIONS
OR DAMAGE TO THE PRINTED CIRCUIT
BOARD WILL OCCUR!
A ‘dry-contact’ device can be connected to the
terminals marked ‘EXTERNAL ALARM’, the
meaning of which is determined by the customer.
Refer to figure three. The data cable connection is
made to the locations marked PROFIBUS + B and
PROFIBUS – A, observing polarity. If this is the last
device on the segment, move the shorting jumpers
to the Y position to enable the termination resistor.
Refer to figure three for data cable connection
locations.
CAUTION
To prevent ignition of hazardous atmospheres,
keep cover bolts tight while circuits are live.
Disconnect supply circuit before opening.
Entry into the BUSwitch housing is made through
three ½” NPT conduit entries. All electrical
connections (power, data, external alarm, open and
close solenoids) are made to captive screw cage
terminal strips located on the Profibus-DP Interface
board (XA0231). BUSwitch models with an internal
pilot valve will have the valve connected to the
appropriate circuit board terminals by the factory.
For dual solenoid applications, connect the
respective solenoids to the terminal strip locations
For hazardous locations, Underwriters Laboratories
(UL) and the National Electric Code (NEC) require
an approved sealing fitting within eighteen inches of
the switch enclosure. Sealing fittings are not
required for Division 2 non-incendive applications.
Open conduit entries must be closed after
installation using a close-up plug approved for
hazardous locations. Conduit and plugs must
engage a full five threads. Flowserve can provide
the sealing fitting with a union and junction box for
‘daisy chain’ wiring applications.
LML0012-0 8/99 Page 2 of 6
©1999, Flowserve Corporation, Provo, Utah
Profibus-DP Interface Card (XA0231)
Figure 3