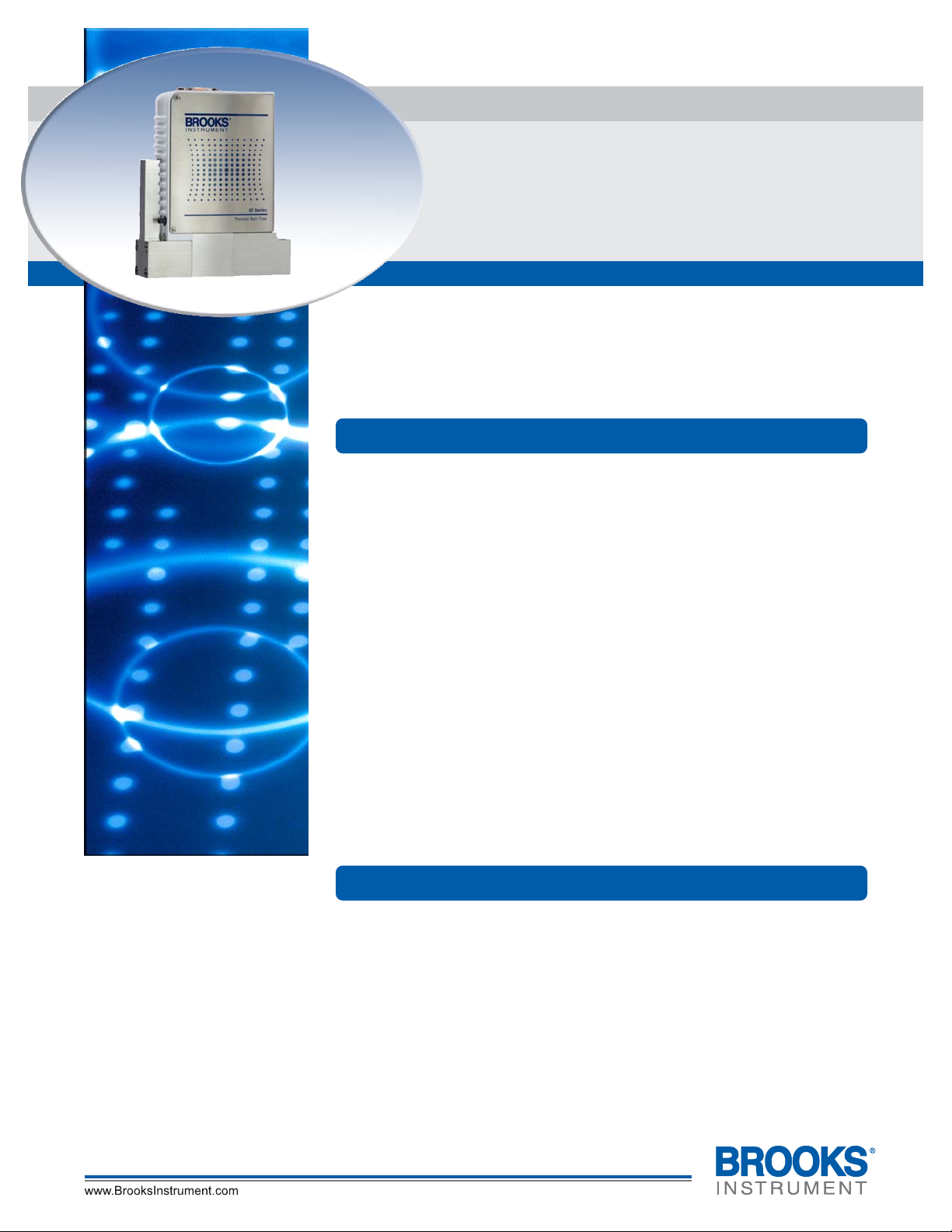
DS-TMF-GF135-MFC-eng
November, 2017
Data Sheet
GF135
Digital Mass Flow Controller
Model GF135
Thermal Mass Flow
Pressure Transient Insensitive
Mass Flow Controller with Real-Time
Flow Error Detection and Advanced Diagnostics
OverviewOverview
Overview
OverviewOverview
Designed for the next step in semiconductor etch, thin film and other advanced process
gas control applications, the GF135 combines all of the benefits provided by the most
advanced pressure transient insensitive mass flow controller (MFC) and adds real-time
flow error detection with advanced diagnostics.
Device manufacturers are driving programs to improve wafer level yield. The current
downstream quality control approach can allow hundreds of wafers to be processed
before issues are detected. Process gas stability and repeatability have been identified as
critical to meeting yield enhancement goals and MFC accuracy has been identified as
critical to maintaining process control.
The GF135 provides third generation pressure transient insensitivity, market leading
process gas accuracy and ultra fast flow settling times for reduced process cycle time and
to address advanced 3D device processing requirements. This platform also offers patent
pending real-time flow error trending using Rate of Decay (ROD) techniques that are
immune to typical MFC failure/degradation modes ensuring accurate and reliable
diagnostic capabilities. After a baseline is established at tool start-up, the GF135 can
detect changes in flow rate to within 2% of set point. These advanced diagnostic
capabilities provide a shift from downstream quality control to real-time quality
assurance and predictive maintenance resulting in higher yield and improved uptime.
PrPr
oduct Descriptionoduct Description
Pr
oduct Description
PrPr
oduct Descriptionoduct Description
The GF135, with integral real-time ROD flow error detection, drops into the standard
ultra high purity surface mount or VCR® MFC footprint providing an easy path to upgrade
critical gas lines on existing systems.
With the GF135, the user will be able to take advantage of enhanced process gas
accuracy, market leading pressure transient performance and MFC health indicators such
as automatic trending of sensor stability and valve shutdown (leak-by). Using these
health indicators and user programmable alarm limits, via MFC service port or remote
digital commands, the user can establish limits to improve the yield and/or manage
maintenance schedules to maximize uptime.
1
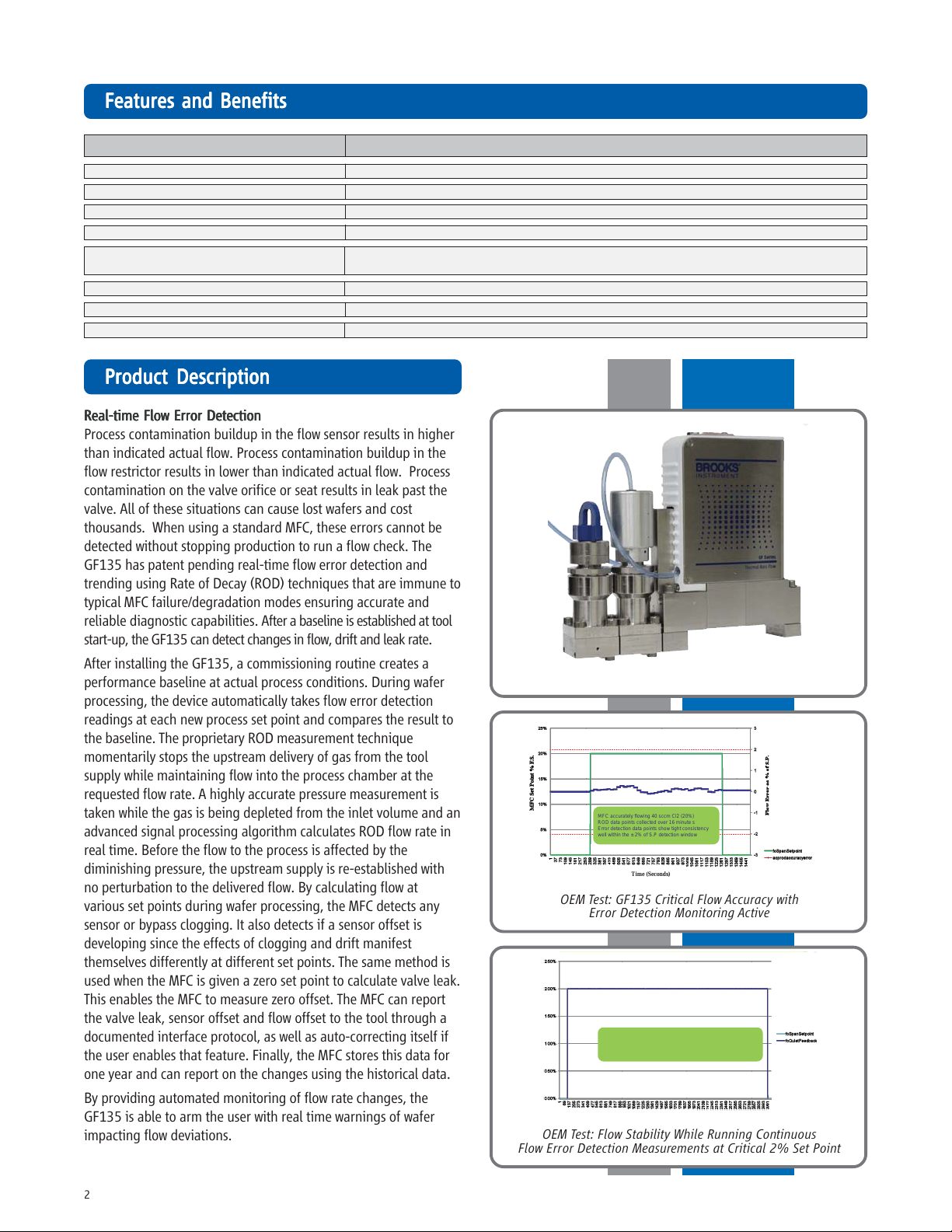
FeaturFeatur
Featur
FeaturFeatur
FeaturFeatur
Featur
FeaturFeatur
Real-time flow error detection Support yield improvement programs by capturing wafer impacting flow deviations
Sensor stability tracking Improves system uptime by supporting predictive maintenance
Valve leak-by tracking Allows user to monitor and set limits to minimze first wafer effects
Enhanced process gas accuracy Meet process gas chemistry control challenges at 10nm
Market leading ultra-fast flow settling time Optimize wafer process cycle time by reducing non-productive flow stabilizaton steps.
Enhanced pressure insensitivity Superior process gas control for enhanced etch and deposition control
Corrosion resistant Hastelloy
Drop-in upgrade for surface-mount and VCR MFCs Easy upgrade for critical gas lines on existing systems
PrPr
Pr
PrPr
Real-time Flow Error DetectionReal-time Flow Error Detection
Real-time Flow Error Detection
Real-time Flow Error DetectionReal-time Flow Error Detection
es and Benefitses and Benefits
es and Benefits
es and Benefitses and Benefits
eses
es
eses
®
sensor Provides unmatched long-term sensor stability ensuring maximum yield and throughput
oduct Descriptionoduct Description
oduct Description
oduct Descriptionoduct Description
BenefitsBenefits
Benefits
BenefitsBenefits
Supports advanced 3D device processing
Process contamination buildup in the flow sensor results in higher
than indicated actual flow. Process contamination buildup in the
flow restrictor results in lower than indicated actual flow. Process
contamination on the valve orifice or seat results in leak past the
valve. All of these situations can cause lost wafers and cost
thousands. When using a standard MFC, these errors cannot be
detected without stopping production to run a flow check. The
GF135 has patent pending real-time flow error detection and
trending using Rate of Decay (ROD) techniques that are immune to
typical MFC failure/degradation modes ensuring accurate and
reliable diagnostic capabilities. After a baseline is established at tool
start-up, the GF135 can detect changes in flow, drift and leak rate.
After installing the GF135, a commissioning routine creates a
performance baseline at actual process conditions. During wafer
Model GF135 on Gas Stick
processing, the device automatically takes flow error detection
readings at each new process set point and compares the result to
the baseline. The proprietary ROD measurement technique
momentarily stops the upstream delivery of gas from the tool
supply while maintaining flow into the process chamber at the
requested flow rate. A highly accurate pressure measurement is
taken while the gas is being depleted from the inlet volume and an
advanced signal processing algorithm calculates ROD flow rate in
MFC accurately flowing 40 sccm Cl2 (20%)
ROD data points collected over 16 minute s
Error detection data points show tight consistency
well within the ± 2% of S.P detection window
real time. Before the flow to the process is affected by the
diminishing pressure, the upstream supply is re-established with
no perturbation to the delivered flow. By calculating flow at
various set points during wafer processing, the MFC detects any
sensor or bypass clogging. It also detects if a sensor offset is
OEM Test: GF135 Critical Flow Accuracy with
Time (Seconds)
Error Detection Monitoring Active
developing since the effects of clogging and drift manifest
themselves differently at different set points. The same method is
used when the MFC is given a zero set point to calculate valve leak.
This enables the MFC to measure zero offset. The MFC can report
the valve leak, sensor offset and flow offset to the tool through a
documented interface protocol, as well as auto-correcting itself if
the user enables that feature. Finally, the MFC stores this data for
MFC flowing 4 sccm Cl2 (2% of F.S.) for 50 minutes
ROD measurements taken at 5 second intervals
No spiking or overshoot after each ROD measurement
one year and can report on the changes using the historical data.
By providing automated monitoring of flow rate changes, the
GF135 is able to arm the user with real time warnings of wafer
impacting flow deviations.
OEM Test: Flow Stability While Running Continuous
Flow Error Detection Measurements at Critical 2% Set Point
2
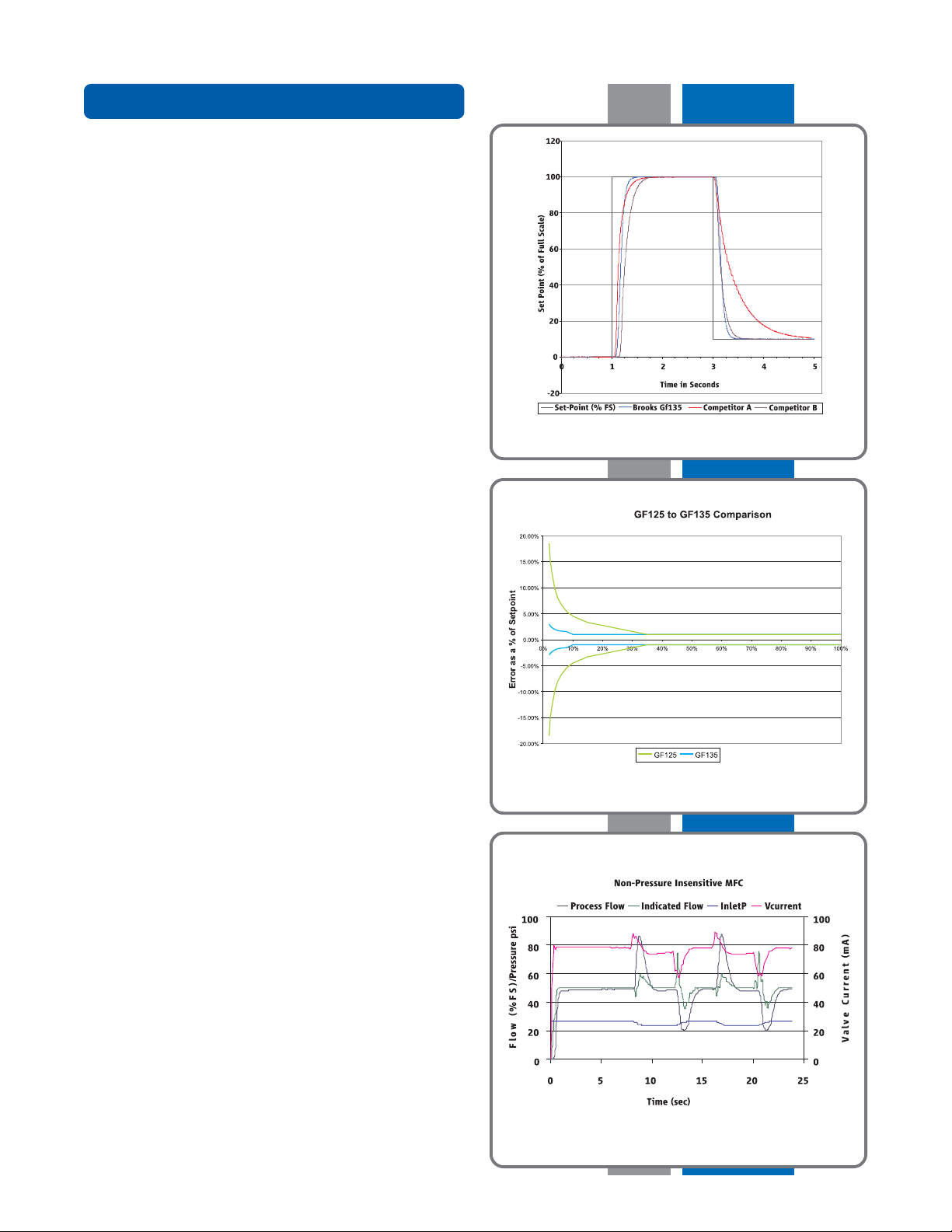
PrPr
oduct Description (conoduct Description (con
Pr
oduct Description (con
PrPr
oduct Description (conoduct Description (con
Ultra-Fast ResponseUltra-Fast Response
Ultra-Fast Response
Ultra-Fast ResponseUltra-Fast Response
By combining Brooks’ patented flow sensor technology with a
high speed ARM processor and fast acting diaphragm free valve
assembly, the GF Series delivers up to 3 times faster response
and settling time compared to other mass flow controllers,
enabling:
• Improved wafer throughput by reducing nonproductive flow
settling steps
• Critical Etch and 3D device processes requiring ultra-fast sub
500 millisecond etch steps
• Reduced diverted gas consumption and associated
abatement costs
• Time-sensitive gas delivery steps in Atomic Layer Deposition (ALD)
• Processes requiring a slow ramped gas turn-on or time
critical transitions between flow rates with user
programmable ramp function
Enhanced Process Gas AccuracyEnhanced Process Gas Accuracy
Enhanced Process Gas Accuracy
Enhanced Process Gas AccuracyEnhanced Process Gas Accuracy
A major advancement over traditional single point gas
conversion factors, Brooks delivers up to a three-times
improvement in process gas accuracy. This is achieved through
advanced gas modeling optimized through actual gas testing
providing compensation for non-linear gases.
tinued)tinued)
tinued)
tinued)tinued)
Comparison of GF135 vs Competititor’s Response Time
to Ascending & Descending Set Points
The GF135 is a gas and range specific device for critical gas
process applications requiring the widest working range with
tightest flow control accuracy. A typical application is for multistep processes requiring a high flow rate (up to 5 slpm) and a
very accurate low flow rate. Traditionally this has been
addressed by using two mass flow controllers. With wide
turndown (100:1) and superior accuracy offered by the GF135,
it is often possible to replace two mass flow controllers with
one, providing immediate cost savings while freeing up a gas
line for greater gas panel flexibility.
Pressure Transient InsensitivityPressure Transient Insensitivity
Pressure Transient Insensitivity
Pressure Transient InsensitivityPressure Transient Insensitivity
Cost and space constraints have driven gas panel designers to
remove point of use pressure regulators and pressure
monitoring components, placing more burden on the mass flow
controller to control accurately under dynamic pressure
conditions. Conventional mass flow controllers react strongly to
small inlet pressure fluctuations resulting in unstable
performance and unpredictable accuracy (see Non-Pressure
Insensitive MFC). This drove Brooks to develop Pressure
Transient Insensitive mass flow controller technology (PTI-MFC).
The GF135 PTI-MFC is a third generation PTI-MFC utilizing a
patented control algorithm that inverts the pressure signal,
compares it to the pre-fluctuation signal and drives real-time
valve position compensation to maintain stable flow. Enhanced
pressure transient insensitivity is achieved through faster
sensing, faster processing, and a reduction in internal dead
volume between the sensors and valve orifice.
Pressure Fluctuations in Non-Pressure Transient Insensitivity MFC
3