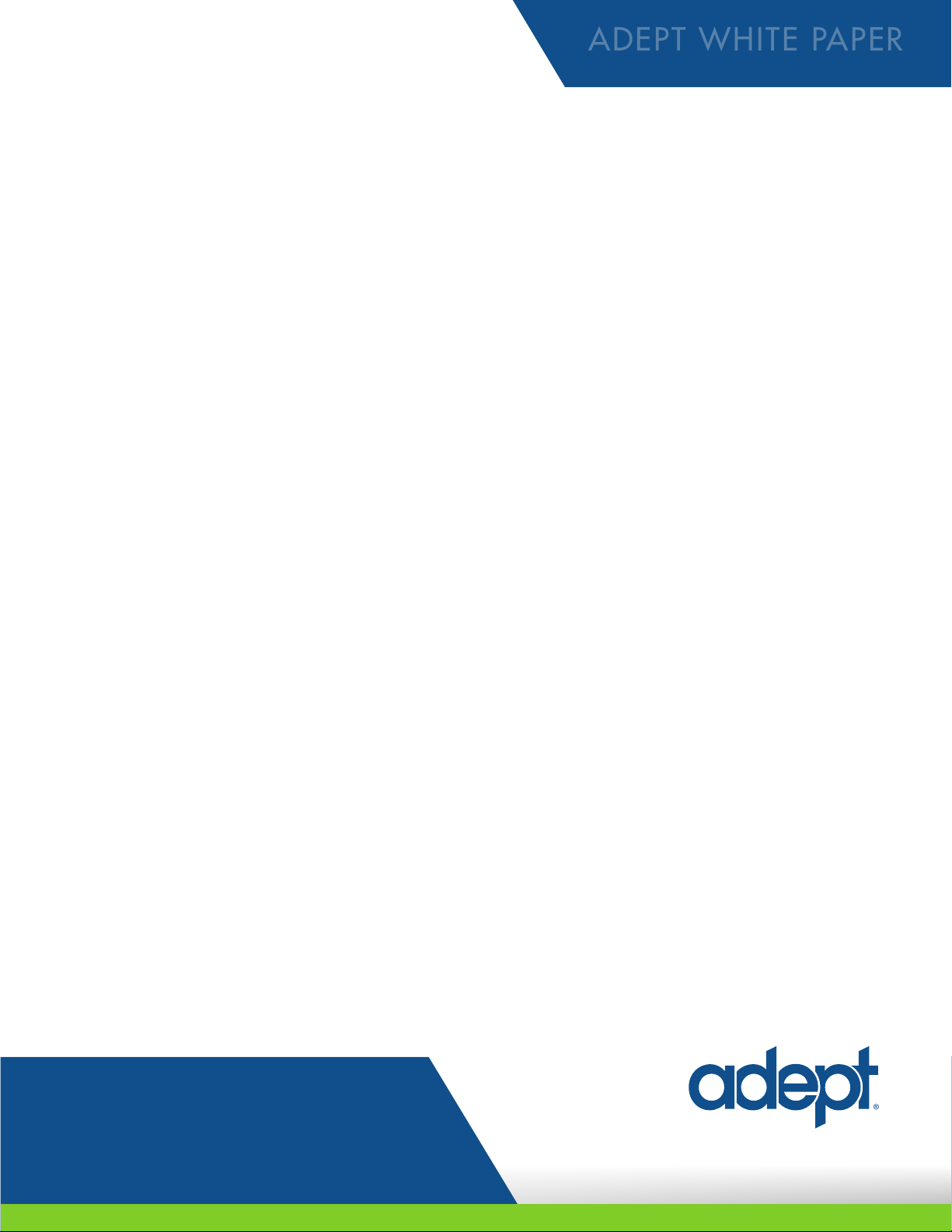
PLC Robot Programming: Familiar Programming, Reduced
Costs of Implementation and 21 CFR Part 11 Compliance
Introduction
Most manufacturers looking to remain competitive understand the advantages automation oers including
increased production rates, improved quality, and reduced product costs. e decision to automate however is
often approached with trepidation as the cost to implement just a single automated cell can seem a daunting
prospect. e cost of the robot alone may appear expensive but when you consider that much of the total cost
of deploying a robotic cell includes programming software, training, & maintenance, the evaluation can become
quite complex.
To meet this challenge, robotic equipment manufacturers are constantly exploring methods to not only reduce the
costs associated with implementation, but ways to simplify installation, programming, and subsequently lower the
total cost of ownership. e following looks at this cost of ownership issue, how end-users have traditionally been
tackling this issue, and new methods of simplifying programming and reducing the cost of ownership of a robotic
application by leveraging knowledge and hardware the end-user already maintains. Specically, the following
addresses the utilization of the end-user’s knowledge of programmable logic controls (PLC) or ladder logic to
program robotic cells.
An additional consideration for many manufacturers is the need to comply with FDA regulations such as 21 CFR
Part 11 which is a set of regulations that governs the way FDA regulated industries manage electronic records and
electronic signatures. Commonly known as Part 11, these regulations establish the criteria under which electronic
records and signatures can be considered equivalent to paper-based records and handwritten signatures. With
shorter product life-cycles increasing the risk of poor quality, standard methods of traceability are no longer
practical. Manufacturers need to electronically track when changes to software have been made in order to
demonstrate traceability within a process and ultimately overall accountability. e robotics industry, with its use
of proprietary controls platforms, has historically not permitted those required to adhere to these regulations to
realize the productivity gains associated with exible automation.
Cost of Ownership
Robot manufacturers oer proprietary software suites and controls platforms that deliver dierent and unique
installation and operational experiences for integrators and users. is means that in addition to the robot
purchase, robotic end-users incur additional costs to train their engineers on the proprietary programming
software and training operators to maintain & support these unique robotic solutions. e end-user must then
address where to obtain training, who will train them, and the scope and costs associated with training activities
such as travel, accommodations, and the time away from the competing obligations. is all aects the robotic
customer’s total cost of ownership and only marginally addresses ease of use.
YOUR INTELLIGENT ROBOTICS PARTNER
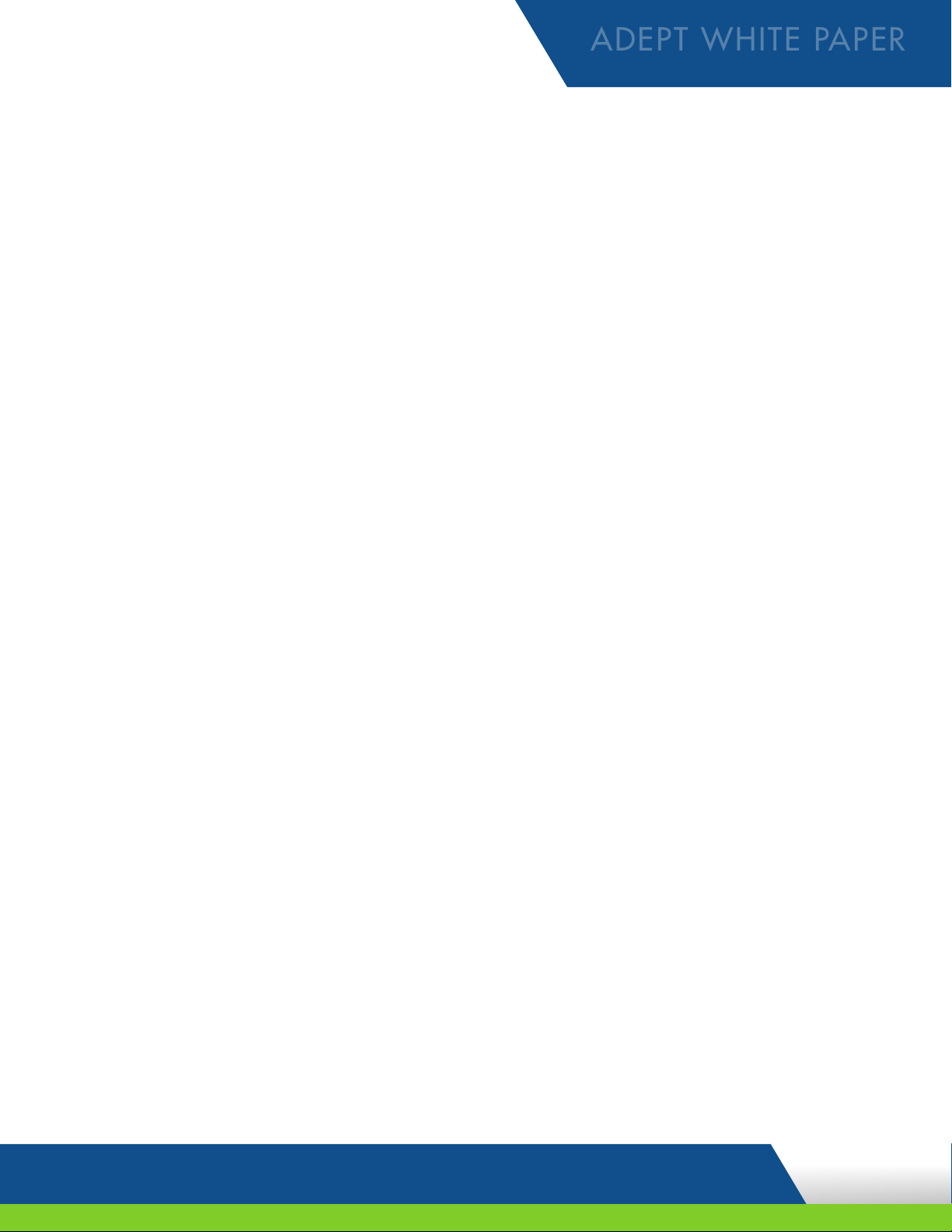
Historically the users of robots have relied on the robot manufacturer, an integrator, or third party consultant
to set-up and train the workers. is support may not be local to the end-user and more importantly can be
challenging to orchestrate, delaying installation and adding extra costs. Once set-up and training is scheduled,
even a single robot installation & subsequent employee training sessions can take days.
PLC Robot Programming
Robot manufacturers studying their customer’s needs and understanding what knowledge support personnel
already possess have developed new methods to more easily deploy and program robots. Specically, new solutions
utilizing the end-user’s existing knowledge of Programmable Logic Controller (PLC) software have been met with
increased adoption. Originally developed for the automotive industry, PLCs have been used by many industries
for a wide variety of machines for nearly 30 years and are therefore familiar control interfaces in most production
and manufacturing settings.
“With the ePLC, the robot becomes another peripheral device rather than the basis of the machine that
everything else has to be built around. We, and many of our customer’s maintenance sta, already know how
to program PLC ladder logic,” said Scott Gerold, senior software specialist of NACS, Inc a leading automation
integrator. “Leveraging that knowledge to program a robot just makes sense. We save both time and money with
regards to training internal engineers. We are able to keep the machine interface and user experience consistent
which also saves time on the technical documentation and customer training as well.”
Robot manufacturers and integrators have developed several options to use the PLC to automate robotic cells
including oering emulation solutions, robot & new PLC hardware & software, and robot software that works
directly with the end-user’s existing equipment.
Robot plus new PLC Solution
One solution has evolved from partnerships between robotic manufacturers and PLC manufacturers. Working
together, these manufacturers oer packages whereby the end-user purchasing a robot from the robot
manufacturer then purchases their desired PLC from a PLC manufacturer. ese two components work together
to program the robot using familiar PLC Ladder Logic software. Additional components may also be required
such as servo ampliers and potentially some additional software education depending on how custom the PLC
is to the robot. While this solution does leverage the end-user’s knowledge, it does require separate purchases and
potentially additional training.
Emulation Solution
Another solution from robotic manufacturers has been the development of software that emulates PLC Ladder
Logic software. While emulating PLC software attempts to shorten the learning curve associated with robot
software, it still requires the end-user to install and learn new software in order to program the robot. is
solution usually requires end-users to purchase multiple licenses from multiple vendors.
Leveraging Existing Equipment
Another solution introduced over 5 years ago is a unique solution that allows end-users and integrators to take
ownership quickly by utilizing the end-user’s existing PLC when deploying a robot. Although the original
deployment of Adept Technology’s ePLC Connect software was designed to be centric to Allen Bradley’s PLC,
which makes up 70-80 percent of the US market, it has since been shown to integrate with Schneider Electric
(formerly Modicon) and Siemens’ PLC’s.
PLC Robot Programming: Familiar Programming, Reduced Costs of Implementation and 21 CFR Part 11 Compliance
2

e ePLC Connect solution allows end-users or integrators to program the robot quickly, easily, and
inexpensively. It allows customers to program a robot 100% from an Allen Bradley (AB) ControlLogix or
CompactLogix through Ethernet IP. e ePLC Connect Server client simply connects through an Ethernet
connection to communicate with the AB PLC. Requiring no additional hardware or software on the PLC, this
robot solution is a plug and play programming solution whereby the end-user simply plugs into the PLC using
an Ethernet connection making it easy and readily programmed. When an end-user buys an Adept robot system
with the ePLC Connect software, all that’s needed is for them to plug a cable from the Adept controller to the AB
PLC or Ethernet network via an Ethernet cable. With this solution the end-user can have multiple robots on the
network. One (1) PLC/Ethernet network can control for example a Cobra SCARA, a Viper 6-Axis Articulated
robot, a Python Cartesian linear module, or Quattro parallel robot. Additionally, the ePLC Connect solution
supports vision guidance, which extends the exibility and capability of the robot system. Multiple cameras
can be used to take images to nd out where an object is located relative to the robot, update the robot location
accordingly, and then provide more accurate information in helping the robot system pick the object - all done
through the PLC.
“e ePLC Connect solution is the cleanest solution available for PLC robot programming,” said Rush LaSelle,
director of worldwide sales and marketing. “e system is simple and straight forward to install for operators
already familiar with PLC programming, requires very little training and bottom line can lower the end-user’s
total cost of owning a robot.”
“Using the Adept solution has made our job much simpler,” said Richard Bahr, president and CEO of MGS
Machine Corporation a leading robot system integrator. “We are able to program the robot in ladder logic then
create libraries of code that are easily re-deployable. is makes our next project even easier to do. We have
developed our code to a point where the robot can be added to any one of our machines and be functioning in a
matter of hours.”
e ePLC software communicates with the user-supplied PLC to exchange data automatically. It runs on the
Adept SmartController CX (ASCX), reading the command registers, executing the appropriate commands,
and then writing status information back to the PLC. e Ethernet IP protocol is the backbone of the
communication between the ASCX controller and the PLC, and Adept’s implementation makes use of the
implicit (I/O) messaging to exchange the necessary data. e ePLC connect software works in conjunction with
the Adept-supplied User Dened Data Structure (or UDT) to pass the command and status information back
and forth as appropriate.
“e biggest advantages we see with the ePLC Connect solution are the time & cost savings on implementing
the solution and the benets of increased eciency & increased production to our customers,” said Dave Deeb,
principle electrical engineer at EDAS Inc. a Midwest design & automation service provider. “We have found that
integrating these types of robots in a facility now takes hours instead of days, increases productivity and eciency
up to 10 fold and in one particular customer’s case saved as much as $450,000 in one year.”
Deeb added that EDAS Inc.’s customers are nding their payback on their initial investment is less than 10
months and the exibility the solution oers allows them to reallocate their resources when their products
change with just couple hours of programming and integration. is gives customers a fully exible cost eective
automation system that in turn signicantly increases their margins.
A testament to its simplicity and ease of use is that over the last 5 years of use, training an end-user was
accomplished with no more than a 2 hour WebEx meeting to review basic PLC concepts and how they pertain
PLC Robot Programming: Familiar Programming, Reduced Costs of Implementation and 21 CFR Part 11 Compliance
3

to the operation of a robot. Most end-users require no dedicated robot training saving them valuable time and
money. e system gives end-users the complete exibility to control how they want their robot to perform for
start up, fault recovery, teaching of locations, and manual/automatic modes of operation. Implementation of the
robot is truly left in the hands of the PLC programmer. Additionally, once an employee has programmed their rst
robot they have the ability to leverage that work going forward. e ability to develop and deploy standard HMI
interfaces for operators and overall robot functionality, can be used over and over again very quickly and easily.
Validation and Regulatory Benefits
Another distinct advantage for many of using PLC robot programming is the ability to validate the robot by
simply validating the PLC. End-users in numerous market segments are required to comply with the Food and
Drug Administration’s (FDA) Title 21 CFR Part 11 of the Code of Federal Regulations guidelines on electronic
records in the United States. is code denes the criteria under which electronic records and electronic signatures
are considered to be reliable. is validation puts a stamp on the system to assure traceability. Once a system is
validated the system cannot be changed without additional validation. Previously, both the PLC and robot would
need separate validation. Using the end-user’s existing PLC means that once the PLC is validated the robot is as
well using ePLC Connect. No additional cost for validation is required because the system uses the PLC software.
Conclusion
Programming a robotic application using PLC robot programming can save end-users implementation time and
money and lowers the robots cost of ownership while also simplifying robotic programming. Utilizing the end-
user’s existing knowledge and equipment makes the job that much easier and also makes the decision to automate
more palatable to the end-user’s business. With ePLC Connect from Adept, manufacturers who are required
to adhere to 21 CFR Part 11 are no longer precluded from beneting from the exibility and productivity
enhancements provided by implementing robotic systems.
About Adept Technology
Adept is a global, leading provider of intelligent robots and autonomous mobile solutions and services that enable
customers to achieve precision, speed, quality and productivity in their assembly, handling, packaging, testing,
and logistical processes. With a comprehensive portfolio of high-performance motion controllers, application
development software, vision-guidance technology and high-reliability robot mechanisms with autonomous
capabilities, Adept provides specialized, cost-eective robotics systems and services to high-growth markets
including Packaging, Medical, Disk Drive/Electronics, and Solar; as well as to traditional industrial markets
including machine tool automation and automotive components.
To nd out how your organization can benet from the ePLC Connect, contact our sales department by emailing
info@adept.com or calling 1-800-292-3378. www.adept.com
A special thank you to...
MGS Machine NACS, Inc. EDAS, Inc.
www.mgsmachine.com www.nacsinc.com 651-261-0494
YOUR INTELLIGENT ROBOTICS PARTNER
©2011 Adept Technology, Inc. ALL RIGHTS RESERVED. The information provided
in this communication or document is the property of Adept Technology, Inc. and
is protected by copyright and other intellectual property laws. In addition, any
references to any Adept Technology, Inc. products are the marks and property of
Adept Technology, Inc. [and may be registered trademarks]. All other trademarks or
tradenames are the property of their respective holders.
4