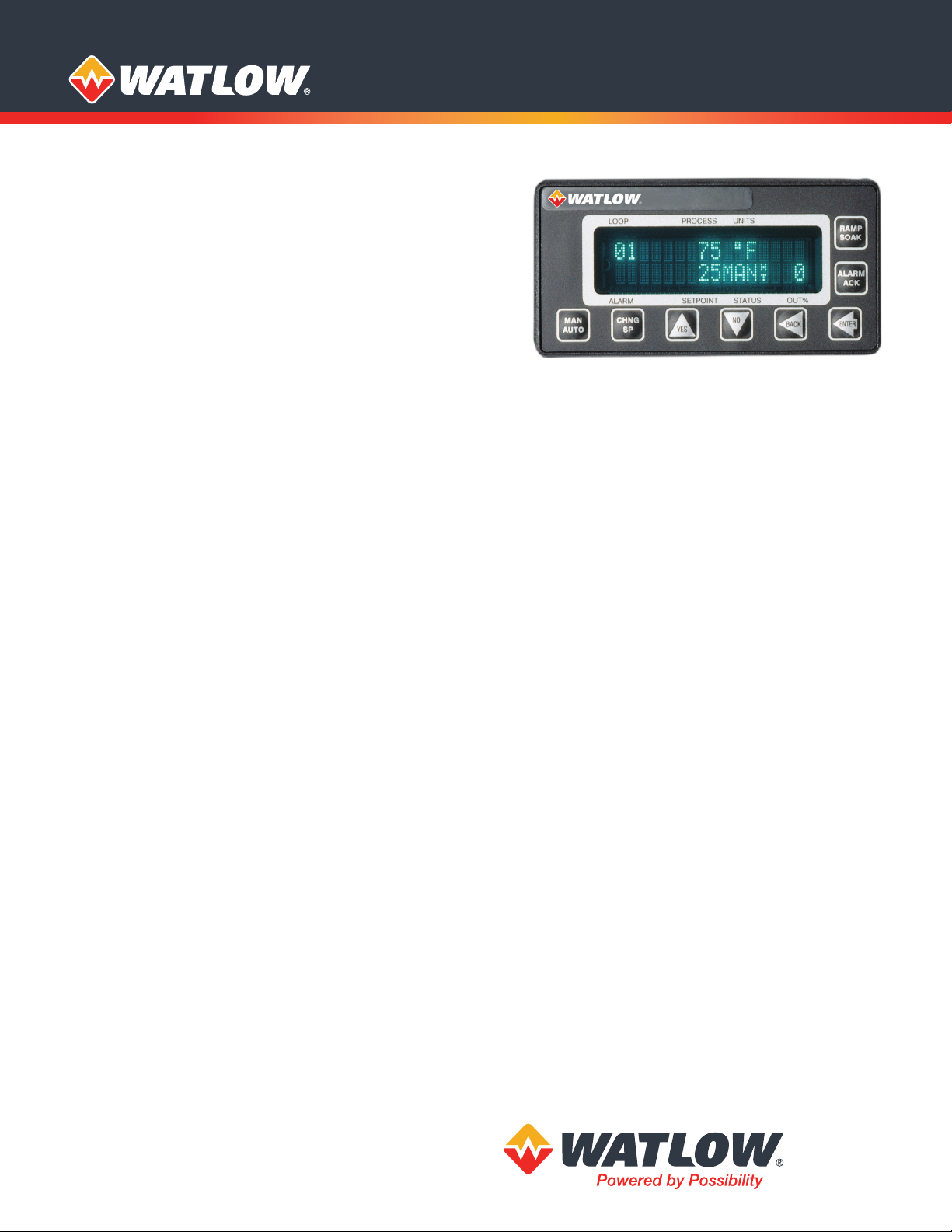
Compact Loop System,
Providing Powerful Control
in a 1/8 DIN Package
SPECIFICATION SHEET
Updated SERIES CLS200
Samples Available Now
Watlow’s SERIES CLS200 is a powerful line of controllers,
combining performance and flexibility with compact design.
The 4, 8 and 16 loop versions provide complete controller
solutions for a broad range of applications. Support for
multiple types of sensor inputs is available, including
thermocouples, RTDs, linear voltage, current and frequency.
Each controller includes built-in serial communications
for computer interface and data acquisition. Optional
programmable ramp and soak features allow complex
batch processing and sequencing. An enhanced feature
option offers cascade control, ratio control, differential control,
process variable retransmit and remote analog set point.
The SERIES CLS200 controllers are UL® and C-UL® listed,
RoHS by design and meet the requirements of the European
Community EMC Directive and carry the CE mark.
Features and Benefits
PID control of up to 16 heat and cool loops
• Minimizes panel space per loop
• Reduces installation time
• Increases reliability: fewer parts means fewer failures
Auto-tune
• Requires less time tuning
• Achieves excellent control with less expertise
Menu-guided operation with full text display
• Allows quick setup of the controller
• Simplies operation
Eight jobs stored and recalled
• Changes quickly from one process to another
Multiple and mixed inputs
• Accepts combinations of thermocouples, RTDs, linear dc
voltage and linear dc current sensors
• Reduces learning curve and inventory
Sensor failure detection
• Reduces time troubleshooting reversed, shorted and
open sensors
High/low process and deviation alarms for each input
• Integrates as needed with other automation controllers
34 digital outputs
• Provides exible conguration
• Allows use of outputs as needed for control and alarms
EIA/TIA-232 and 485 communications
• Connects to software for easy operation
• Allows integration with controllers and software
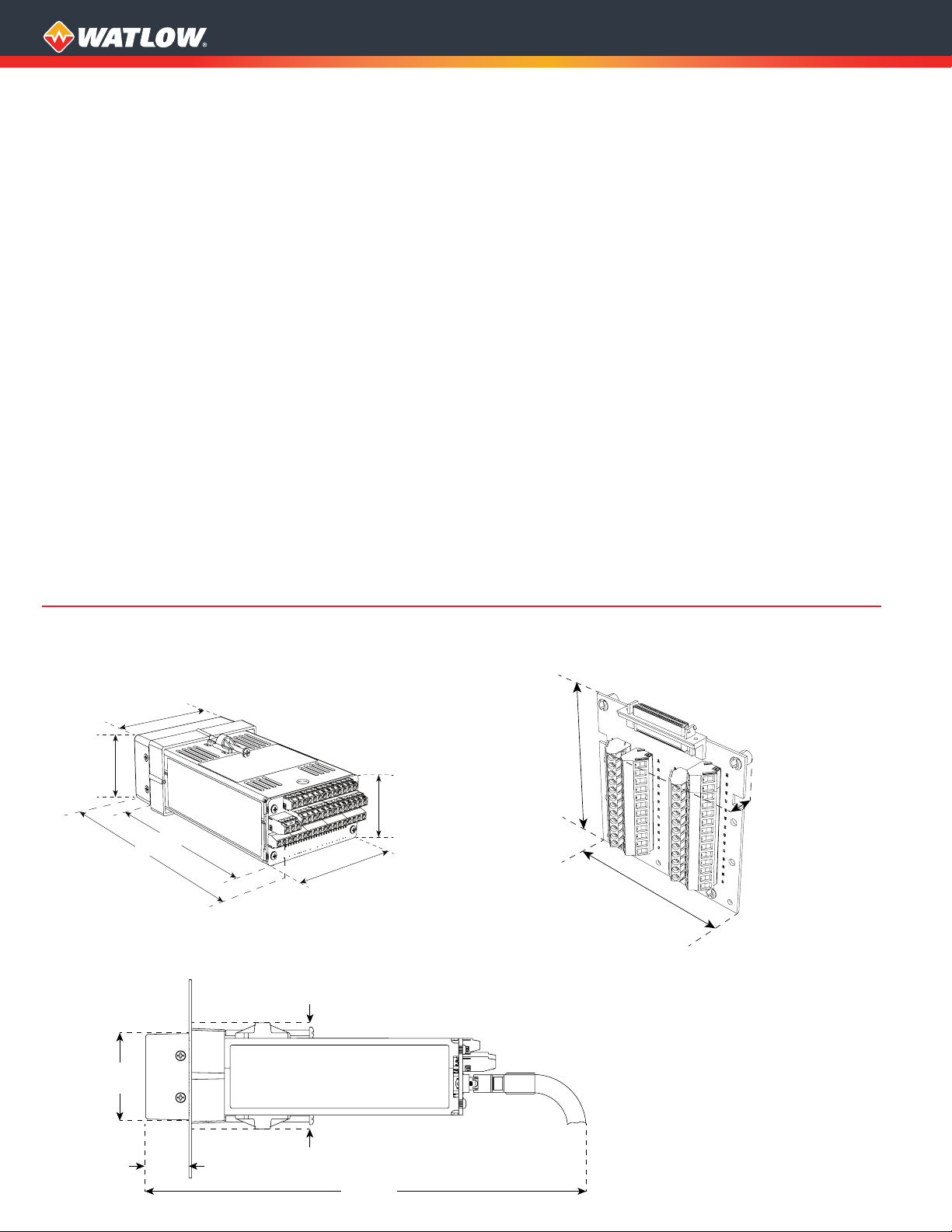
Firmware Options
3.55 in.
(90 mm)
3.80 in.
(96 mm)
1.98 in.
(50 mm)
6.12 in.
(155 mm)
8.00 in.
(203 mm)
1.76 in.
(45 mm)
1.00 in.
(25 mm)
1.98 in.
(50 mm)
10.00 in.
(254 mm)
2.44 in.
(62 mm)
Choose firmware with the features needed for the
application:
• Standard—includes closed-loop PID control, auto-tune,
alarms, job memory and failed sensor detection.
• Ramp and soak—includes the standard firmware
features with the addition of ramp and soak and process
variable retransmit. Each channel can be configured for
standard PID control or ramp and soak operation. Unused
control outputs on any channel can be configured to
retransmit a process value.
• Enhanced features— includes the standard firmware
features with the addition of process variable retransmit,
remote analog set point, cascade control, ratio control
and differential control algorithms. Each channel can be
configured for standard PID controller or one of the other
control algorithms. Each channel of cascade control or
remote analog set point requires two controller channels.
Unused control outputs on any channel can be
configured to retransmit a process value.
• Custom— application-specific, engineered solutions are
available. Contact your Watlow representative.
Digital Input/Output Options
Controllers with the mass termination option for digital
I/O termination have a 50-pin SCSI connector which allows
access to all digital inputs and outputs. SCSI cables and the
TB50 digital I/O termination board options are offered to
allow connection of field wiring.
Four and eight loop controllers can be configured with
screw terminal connections on the back for connecting
digital inputs and outputs, but this limits access to
15 outputs (10 of which can be used for control loops)
and three inputs.
Because the SERIES CLS200 has no onboard analog
outputs, applications that use process variable retransmit
typically require one SDAC module per retransmitted
signal.
DAC and SDAC Modules
The optional DAC and SDAC modules are available for
Watlow SERIES CLS200 controllers.
DAC
The DAC (digital to analog converter) converts one or two
of the controller’s distributed zero crossing (DZC) output
signals to analog signals. Each output is field configurable
for 4-20mVDC, 0-5VDC or 0-10VDC.
SDAC
The SDAC (serial digital to analog converter) converts
one controller output to a precise analog voltage or
current signal. The unit is typically used for process
variable retransmit, open-loop control, motor or belt speed
control, or phase-angle fired SCR power controllers. The
SDAC bears the CE mark and is UL® and C-UL® listed.
Dimensional Drawings
Figure 1 - TB18 Screw Terminals
Digital I/O Termination Option Shown
Figure 3 - Mass Termination (SCSI) Digital I/O Termination
and Cable Options
Figure 2 - TB50 Terminal Board Option
4.1 in.
(104 mm)
0.92 in.
(23 mm)
4.0 in.
(102 mm)
Note: Overall length in the application
depends on the Digital I/O Termination
option and bend radius of wiring and
cables used.
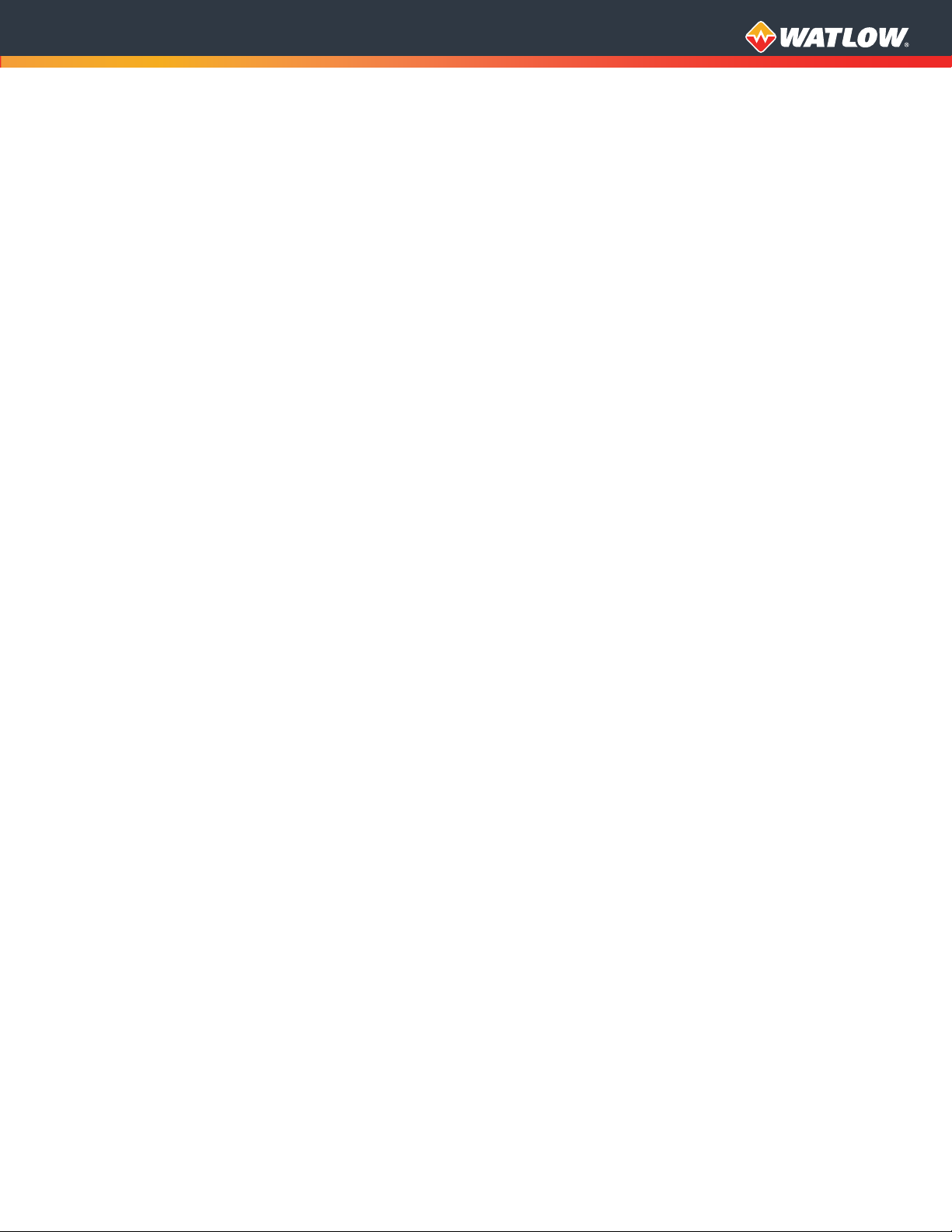
CLS200 Specifications
Operator Interface
• 32-character vacuum fluorescent display
• 8-key keypad to access guided menus and prompts,
enter passkey sequence, set values, switch between
single channel and multiple channel displays
• Controller configuration can be loaded via serial
communication
Analog Inputs
• 4-loop model: 4 differential inputs
• 8-loop model: 8 differential inputs
• 16-loop model: 16 single-ended inputs
Analog Over Voltage Protection
• ±20V referenced to digital ground
Maximum Common Mode Voltage
• 5V input to input or input to analog common
(4- and 8-loop models)
Common Mode Rejection (CMR)
• For inputs that do not exceed ±5V, >60dB dc to 1kHz and
120dB at selected line frequency
Noise Rejection
• 120dB at 60Hz
Sensors/Inputs
• Thermocouples: user-selectable type, direct connection,
linearization, reference junction compensation, reversed
and shorted thermocouple detection and upscale break
protection with output averaging
• RTD: (4 and 8 loop models only) 2- or 3-wire, platinum,
100Ω @ 0°C, DIN 0.003850Ω/Ω/°C curve, user-selectable
range. Two ranges offer different resolutions. Requires
scaling resistors. See ordering information.
• Linear: current and voltage signals from linear transmitters
• Pulse input
Input Range and Accuracy
Sensor Range (°C) Range (°F) Accuracy
Type B 66 to 1760°C 150 to 3200°F ±4.0°C
Type E -200 to 787°C -328 to 1448°F ±1.0°C
Type J -212 to 760°C -350 to 1400°F ±1.2°C
Type K -268 to 1371°C -450 to 2500°F ±1.3°C
Type R -18 to 1766°C 0 to 3210°F ±2.8°C
Type S -18 to 1760°C 0 to 3200°F ±2.8°C
Type T -268 to 399°C -450 to 750°F ±1.6°C
RTDs available on CLS204 and CLS208 only.
Sensor Range (°C) Range (°F) Accuracy
RTD1 -100 to 275˚C -148 to 527˚F ±1.1˚C
RTD2 -120 to 840˚C -184 to 1544˚F ±1.6˚C
Note: Accuracy @ 25˚C ambient. Valid for 10 to 100 percent
of span except Type B, which is specified for 800˚F to
3200˚F. RTD.
Linear Voltage and Current Inputs
Requires scaling resistors. See ordering information.
0-20mAVDC/4-20mAVDC
0-5VDC
0-10VDC
Temperature coefficient: 40ppm/°C
Other ranges available. Contact factory.
Pulse Input
• One TTL-level square wave input up to 2kHz
Input Sampling Rate at 60Hz
Each channel has the following scans per second:
• 4-loop model: 6 samples per second,
(update time: 0.167 sec.)
• 8-loop model: 3 samples per second,
(update time: 0.333 sec.)
• 16-loop model: 1.5 samples per second,
(update time: 0.667 sec.)
Internal Measurement Resolution
• 0.006 percent, greater than 14 bits
Calibration
• Automatic zero and full scale
Digital Inputs
• TTL-level used for selecting recipes or jobs, or R/S triggers
• 8 digital inputs and 1 pulse input with mass termination
(SCSI) digital I/O termination and TB50 terminal board
options
• 2 digital inputs and 1 pulse input with screw terminal
(TB18) digital I/O termination option
Digital Outputs
• 34 digital outputs with mass termination (SCSI) digital I/O
termination and TB50 terminal board options
• 11 control and alarm outputs with screw terminal (TB18)
digital I/O termination option
• 1 or 2 control outputs are user assigned for each loop
• Each control output can be configured for on-off time
proportioning, or distributed zero crossing
• Outputs sink up to 60mA each at 5VDC
• 350mA at 5VDC available from on-board supply
Alarm Outputs
• Independent process and deviation alarms for each
channel
• Alarms can operate any output not used for control
• User-programmable deadband, delay and startup
suppression
• Global alarm output activates when any alarm occurs
• Watchdog output indicates controller is functioning
correctly
Serial Interface
• EIA/TIA-232 or EIA/TIA-485
Baud Rate
• 2400, 9600 or 19200, user-selectable
Communications Protocols
• Form of ANSI X3.28-1976, (D1, F1) compatible with
Allen-Bradley PLC/2
• Modbus® RTU
Line Voltage/Power
• 15 to 24VDC ± 3VDC @ 1A (maximum),
300mA (no load)
Agency Approvals
• UL®, C-UL® listed: UL® 61010-1 safety requirements for
measurement, control and laboratory equipment
• CE Mark: See Declaration of Conformity for details
• RoHS by design