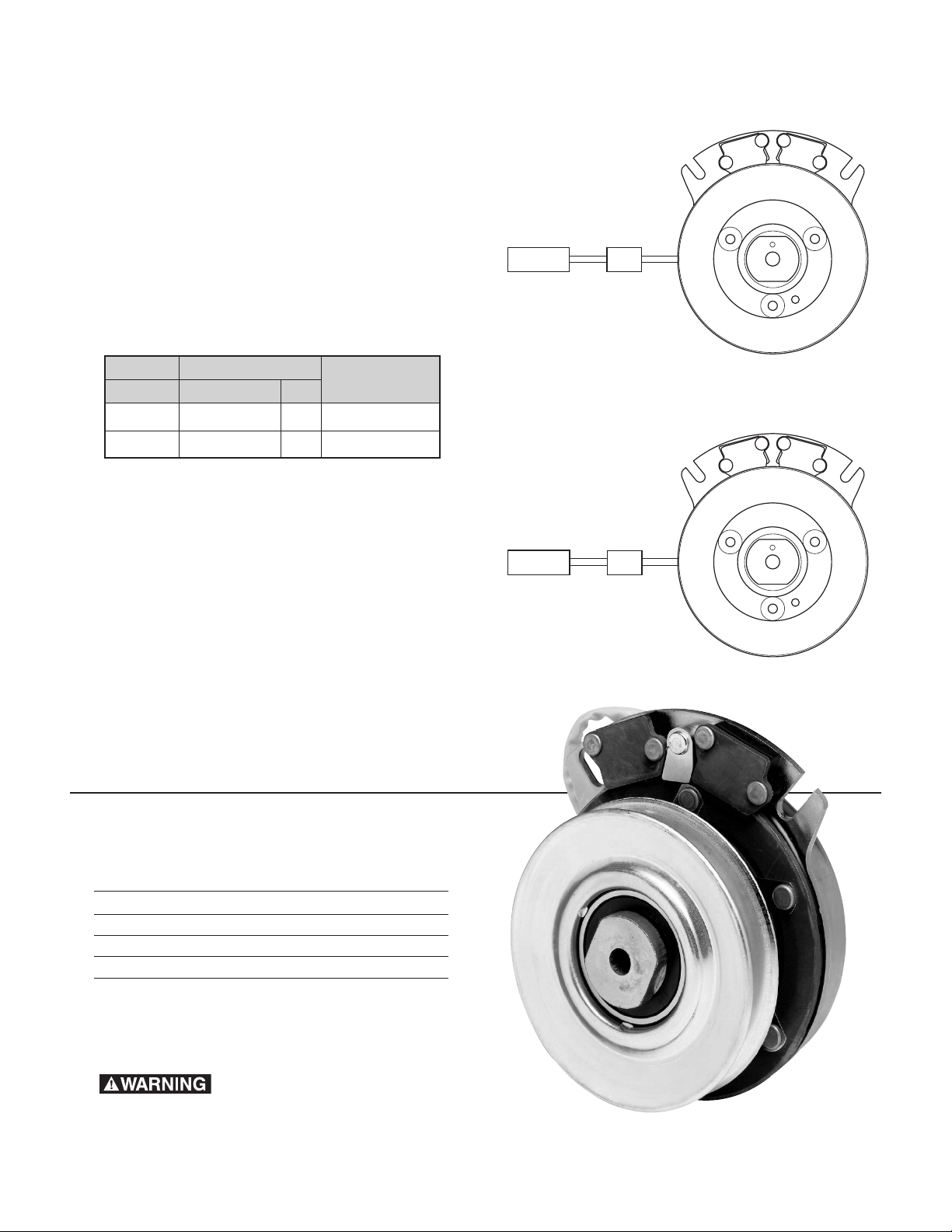
Warner Electric Commercial MagStop Clutch/Brake
Electrical Evaluation
Step 1 How to Measure Clutch Coil resistance
(Figure 1)
. Turn engine and PTO switch off.
1
2. Disconnect clutch at clutch connector.
. Select meter setting for ohm reading.
3
4. Connect meter leads to clutch.
5. Check meter reading and refer to the chart
below for correct clutch resistance reading.
(values are @68° F)
If reading falls in acceptable range proceed to
step 2, if not replace clutch.
Table
Torque Resistance
Model (ft-lb) Nom. Nm (ohms)
CMS-175 175 237 2.45 - 2.71
CMS-200 200 271 1.74 - 1.93
Note: If bench tested with 12 volts applied, armature
may not pull away from brakepoles. Rotational motion
is required to engage clutch
Figure 1
Resistance Measurement
Step 2 Measure the supply voltage at the clutch
(Figure 2)
1. Turn engine off.
2. Connect meter leads at the clutch connector.
3. Select meter setting for voltage reading.
4. Make sure wires will not become entangled in rotating
components of clutch.
5. Start engine and engage PTO switch.
6. Measure voltage across the leads at the connectors.
7. Voltage should be 12-14 volts DC. If clutch still
fails to operate, replace the clutch.
8. If voltage is not within 12-14 volt range consult OEMs
service manual.
Installation and operating notes
Clutch mounting bolt torque is critical. Failure to torque mounting bolt to
prescribed values will lead to premature failure of the clutch.
Grade 5 Mounting Bolt
Thread Size Torque Required N-m
3/8-24” UNF* 40-45 lb.ft. 54-61
7/16-20” UNF** 50-55 lb.ft. 67-75
M 10 X 1.50 55-60 N-m 55-60
* 3/8 -24 UNF Grade 5 bolt is unacceptable
** 7/16-20 UNF Grade 5 or 8 bolt is acceptable
Note: All values are for dry (unlubricated) plated bolts, please consult
fastener manufacturer if any type of locking element (thread lock
compound, patch etc.) is to be used.
Figure 2
Voltage Measurement
Failure to torque bolt to requirements will
degrade clamping and can allow the clutch to separate from
the shaft, causing risk of personal injury.
Engage deck at less than full engine RPM to increase clutch life. Once
clutch is engaged engine RPM can be increased to full RPM.
Warner Electric LLC
31 Industrial Park Road • New Hartford, CT 06057
815-389-3771
www.warnerelectric.com
819-0459 P-1177-2 8/11 Printed in U.S.A.
• Fax: 815-389-2582
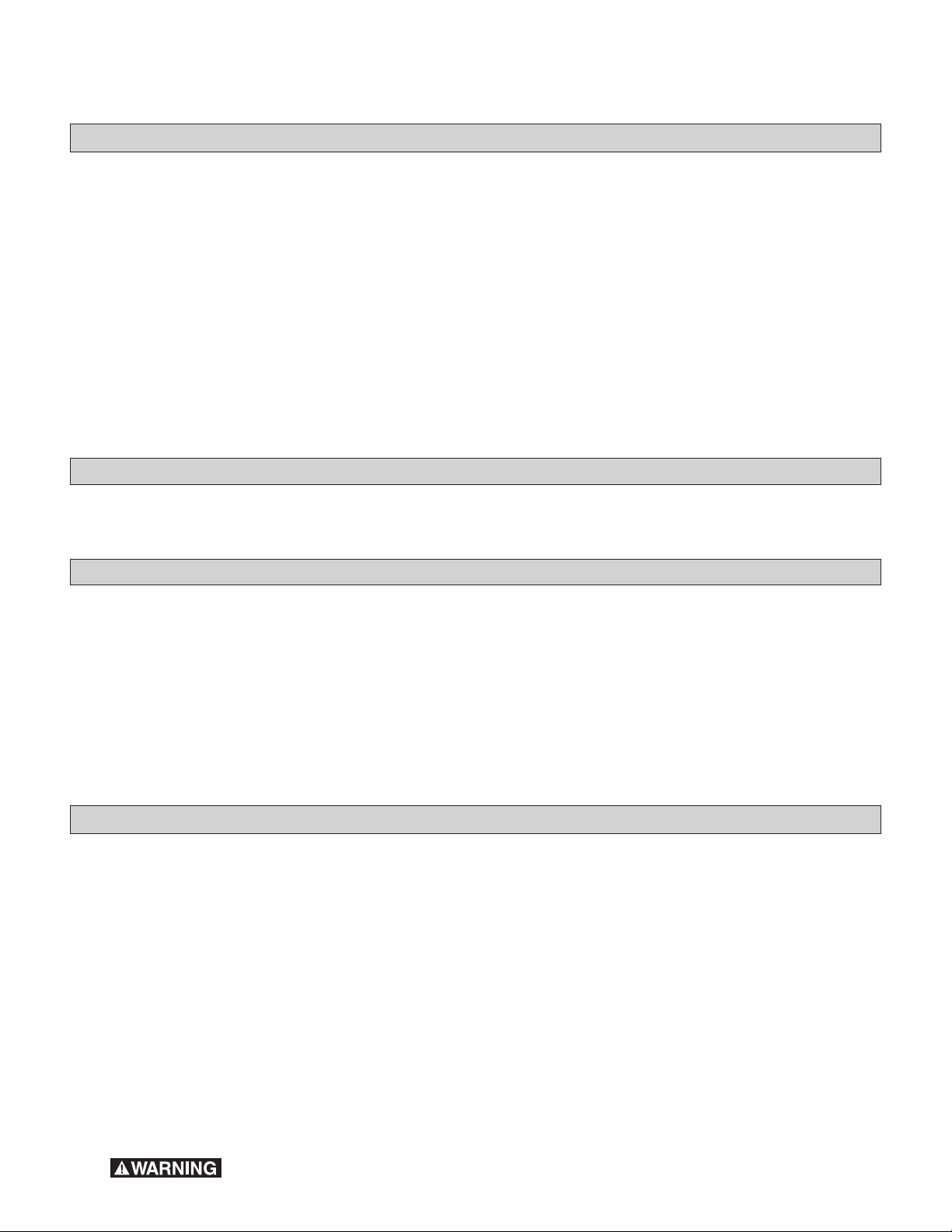
Warner Electric Commercial MagStop Clutch/Brake
Troubleshooting Checklist
A. Symptom: Clutch will not engage
Problem Possible Causes Solution
- Blown fuse - Low coil resistance - Replace with new MagStop unit
- Low voltage supply - Defective battery - Replace
(Less than 12 VDC at clutch) - Faulty charging system - Repair or replace
- Incorrect coil resistance - Damaged coil - Replace with new MagStop unit
(see Step 1)
- Inadequate current supply - Broken clutch lead wire - Repair
- Rotor/armature airgap too large - Rotor/armature wear. End of usable life - Replace with new MagStop unit
(greater than .125 inch/3.18 mm
B. Brake will not engage
Problem Possible Causes Solution
- Armature/brake poles wore out - End of usable life - Replace with new MagStop unit
- Contaminated friction surfaces - Engine oil leak on brake - Repair leak
C. Clutch slip
- Defective battery - Replace
- Faulty charging system - Repair or replace
- Bad wiring or connections, PTO switch - Repair or replace
Bad wiring or connectors, PTO switch - Repair or replace
-
- Faulty electrical system - Measure clutch coil resistance
and supply voltage at the clutch. If
both are correct, electrical system
is faulty. Repair or replace.
- Replace with new MagStop unit
Problem Possible Causes Solution
- Low voltage supply - Defective battery - Replace
(less than 12 VDC at clutch) - Faulty charging system - Repair or replace
- Inadequate current supply - Broken clutch lead wire - Repair
- Overloaded clutch - Clogged deck, bad spindle, etc. - Remove excess grass
- Contaminated friction surfaces - Engine oil leak on clutch - Repair leak
D. Symptom: Noisy clutch/Vibration
- Bad wiring or connectors, PTO switch - Repair
- Faulty electrical system - Measure clutch coil resistance
and supply voltage at the clutch. If
both are correct, electrical system
is faulty. Repair or replace.
- Replace spindle
- Replace with new MagStop unit
Problem Possible Causes Solution
- Failed bearing - Loose mounting (bolt not torqued properly) - Replace, torque to spec.
- Adapter plate rattles against - Some noise is normal - If noise is excessive, repair or
anti-rotation pin pin replace anti-rotation device.
- Clutch loose on shaft - Loose mounting (bolt not torqued properly) - Tighten mounting bolt to specification.
- Clutch not mounted square - Ground Drive Spacer mounting shoulder - Replace
- Broken spring - Loose mounting - Replace clutch
- Field assembly movement restricted - Confirm proper Anti-rotation
(Follow OEM’s Specifications.
- Mounting bolt too long and bottoms - Use correct length bolt
in engine shaft before clamping clutch
- Mounting washer too thin and
deforms when bolt is tightened.
- Shaft bottomed on D-drive - Use proper spacer 1/4" thick min.
not square
- Clutch integral key hitting end of keyway - Space clutch away from radius
in engine shaft in shaft keyway.
- Incorrect or no chamfer on ground - Increase chamfer on ground drive
drive spacer. spacer.
A clutch with broken rivets or springs may separate from the shaft and cause personal injury.