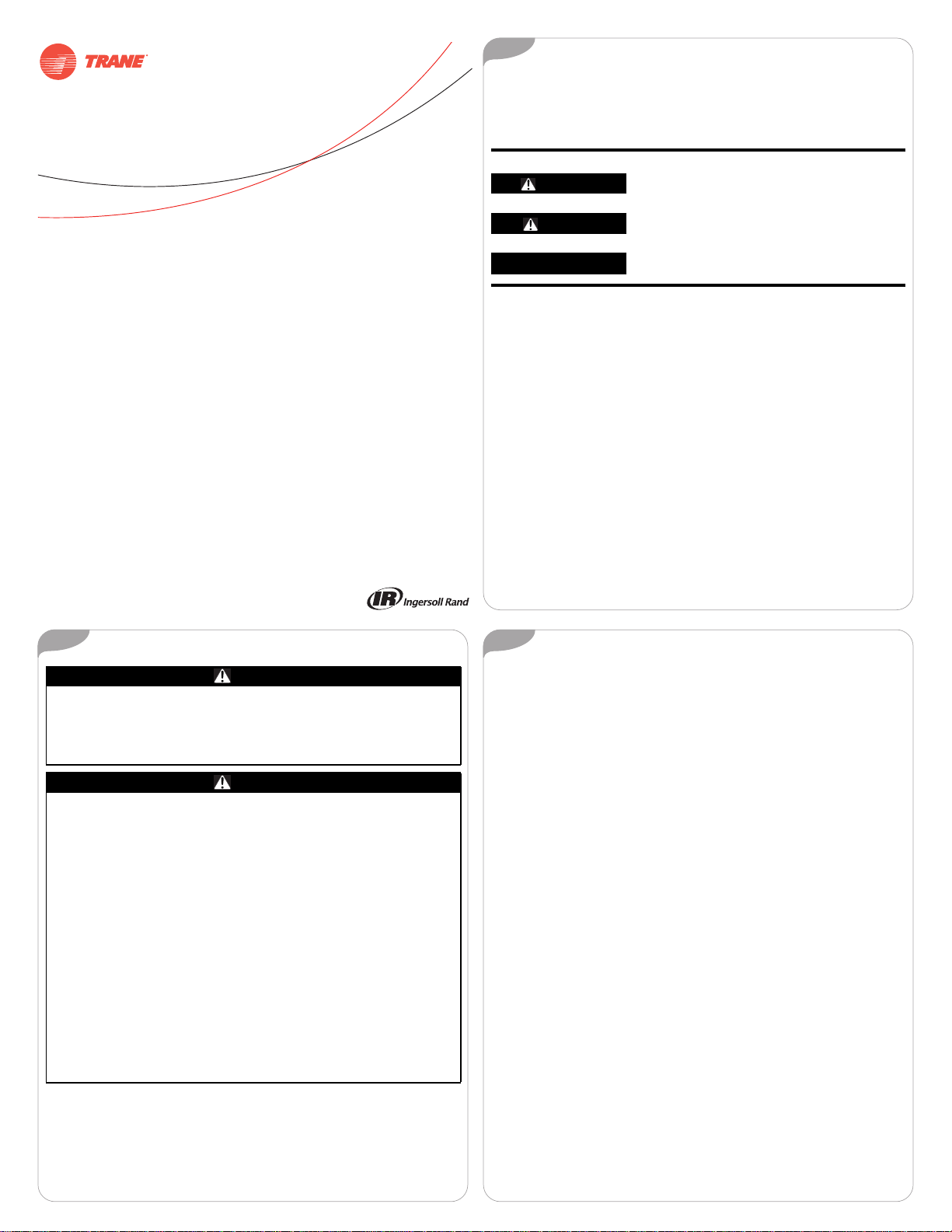
Installation Instructions
1
Warnings, Cautions, and Notices
Read this manual thoroughly before operating or servicing this unit.
Safety advisories appear throughout this manual as required.Your
personal safety and the proper operation of this machine depend upon
the strict observance of these precautions.
The three types of advisories are defined as follows:
WARNING
CAUTION
NOTICE
Indicates a potentially hazardous situation
which, if not avoided, could result in death or
serious injury.
Indicates a potentially hazardous situation
which, if not avoided, could result in minor or
moderate injury. It could also be used to alert
Indicates a situation that could result in
equipment or property-damage only accidents.
VAV Piping Package
September 2014
2
Proper Field Wiring and Grounding Required!
Failure to follow code could result in death or serious injury. All field wiring
MUST be performed by qualified personnel. Improperly installed and grounded
field wiring poses FIRE and ELECTROCUTION hazards. To avoid these hazards,
you MUST follow requirements for field wiring installation and grounding as
described in NEC and your local/state electrical codes.
Personal Protective Equipment Required!
Installing/servicing this unit could result in exposure to electrical, mechanical
and chemical hazards.
• Before installing/servicing this unit, technicians MUST put on all PPE
required for the work being undertaken (Examples; cut resistant gloves/
sleeves, butyl gloves, safety glasses, hard hat/ bump cap, fall protection,
electrical PPE and arc flash clothing). ALWAYS refer to appropriate Material
Safety Data Sheets (MSDS)/ Safety Data Sheets (SDS) and OSHA guidelines
for proper PPE.
• When working with or around hazardous chemicals, ALWAYS refer to the
appropriate MSDS/SDS and OSHA/GHS (Global Harmonized System of
Classification and Labelling of Chemicals) guidelines for information on
allowable personal exposure levels, proper respiratory protection and handling
instructions.
• If there is a risk of energized electrical contact, arc, or flash, technicians
MUST put on all PPE in accordance with OSHA, NFPA 70E, or other countryspecific requirements for arc flash protection, PRIOR to servicing the unit.
NEVER PERFORM ANY SWITCHING, DISCONNECTING, OR VOLTAGE TESTING
WITHOUT PROPER ELECTRICAL PPE AND ARC FLASH CLOTHING. ENSURE
ELECTRICAL METERS AND EQUIPMENT ARE PROPERLY RATED FOR
INTENDED VOLTAGE.
Failure to follow instructions could result in death or serious injury.
VAV-SVN012A-EN
© 2014Trane All Rights Reserved
WARNING
WARNING
Important Environmental Concerns
Scientific research has shown that certain man-made chemicals can
affect the earth’s naturally occurring stratospheric ozone layer when
released to the atmosphere. In particular, several of the identified
chemicals that may affect the ozone layer are refrigerants that contain
Chlorine, Fluorine and Carbon (CFCs) and those containing Hydrogen,
Chlorine, Fluorine and Carbon (HCFCs). Not all refrigerants containing
these compounds have the same potential impact to the environment.
Trane advocates the responsible handling of all refrigerants-including
industry replacements for CFCs such as HCFCs and HFCs.
Important Responsible Refrigerant Practices
Trane believes that responsible refrigerant practices are important to the
environment, our customers, and the air conditioning industry. All
technicians who handle refrigerants must be certified.The Federal Clean
Air Act (Section 608) sets forth the requirements for handling,
reclaiming, recovering and recycling of certain refrigerants and the
equipment that is used in these service procedures. In addition, some
states or municipalities may have additional requirements that must
also be adhered to for responsible management of refrigerants. Know
the applicable laws and follow them.
3
General Information
1. Clean the lines of all foreign material, (welding slag, pipe scale, dirt,
thread chips, etc.). Upstream installation of a strainer may be
necessary in dirty systems.
2. Air should be eliminated from the system prior to startup to assure
quiet operation and freedom from water hammer.
3. Flow control valves may be installed horizontally, vertically or any
angle in between. Additional straight sections of pipe upstream or
downstream of the automatic flow control valves are unnecessary for
proper operation.
4. Standard reducing bushings or flanges may be directly connected to
the hose ends if required.
5. The ATC actuator may be mounted above or along side of piping but
must never be mounted where condensation can accumulate or
come in contact with electrical or mechanical components.
6. Automatic control valves are marked with direction of flow.
Automatic valves will be labeled with the GPM and the water valve Cv.
Important: The arrow must point in the direction of flow for proper
operation.
7. Automatic flow control valves must be located in the RETURN Line.
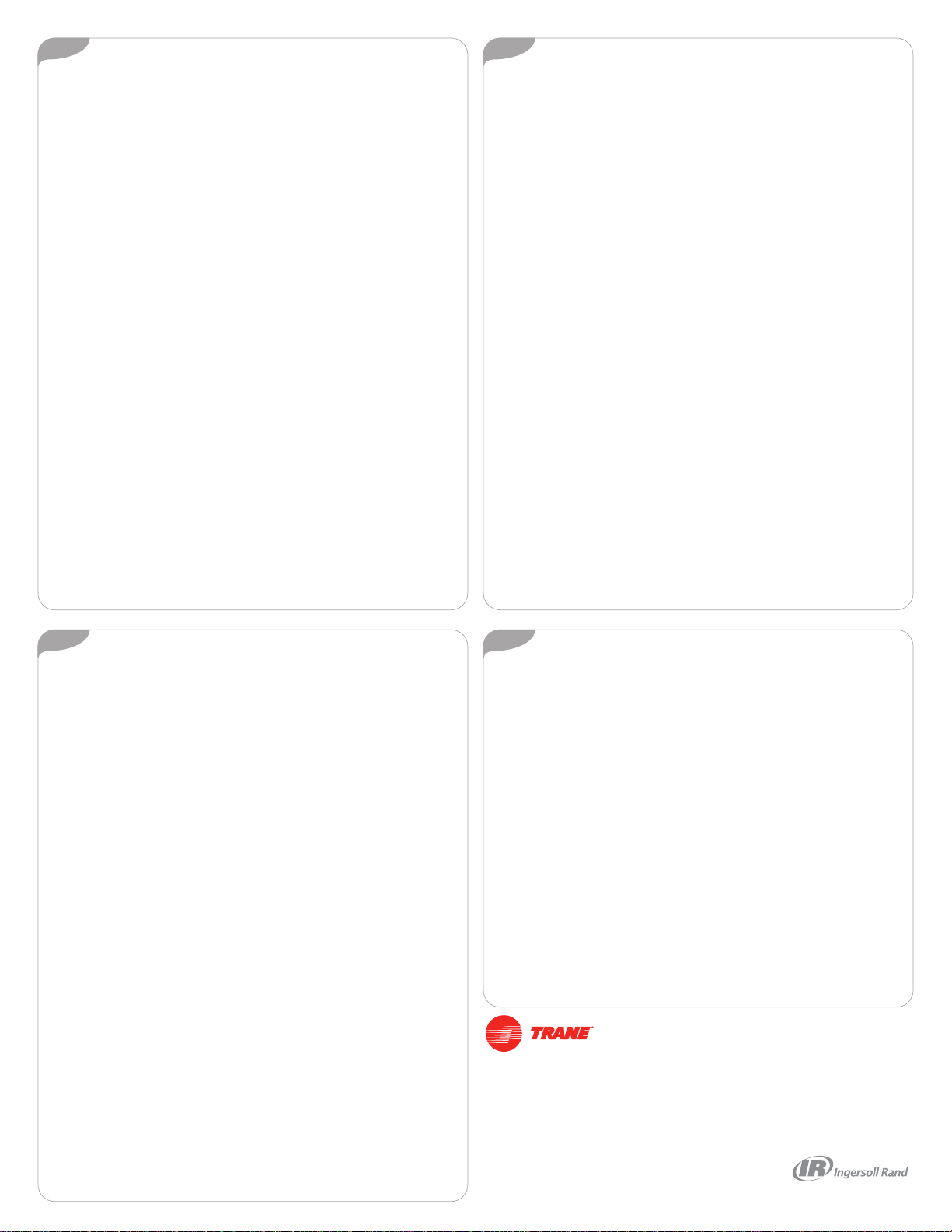
4
Installation
1. Field threaded connections are made with the inchseries NPT threads
in accordance with ANSI STD B1.20.1 and are intended for use in
building services piping meeting the requirements of ASME B 31.9.
2. Determine whichis the supply section and which is the return section.
The strainer is only on the supply side. Flow controls and the
proportional water valve are only on the return side.
3. Apply thread sealant to male pipe threads, starting with the second
or third thread from the end.
Important: If factory applied thread sealant is present, DO NOT ADD
ADDITIONAL SEALANT.
4. Torque the connection to 75 ft-lbs per inch of pipe size minimum.
Example: 1/4”,.25x75=19ftlbMin
5. Rotate the components having pressure/temperature ports or
pressure taps so they are not pointing down.
6. Sweat connections according to the following information:
a. Coil sweat fitting valves have their end connections formed to
ANSI STD B16.22 requirements and are intended for use in
building services piping meeting the requirements of ASME B
31.9.
b. The temperature/pressure rating of the solder joint is dependent
upon the type of solder used. ANSI STD B16.22 pressure ratings
should be reviewed prior to selecting a solder and sweating.
c. UNIONS, UNION END PIECES ON VALVES ANDTHREADED
SWEAT ADAPTERS ARE SHIPPED LOOSE AND SHOULD BE
UNATTACHED DURING SWEATING.
d. O-rings in the union end pieces must be removed and stored on
the valve handle or on a nearby PT fitting during the sweating
operation.
e. Ball valves must be in the closed position during sweating.
f. The outside of the tubing, and the inside of the fitting are to be
mechanically cleaned and then lightly coated with solder flux.
g. The tube is then inserted one diameter into the fitting and the
CENTRAL PORTION OFTHE VALVE BODYWRAPPED WITH
A WET RAG, WET SPONGE OR HEAT ABSORBING PUTTY.
5
h. Heat is never to be applied to the automatic temperature control
valve body, without first removing all plastic parts and actuators.
i. Valveswithout removable parts are to be set to the open position
to prevent thermal damage.
j. Heat may be applied, either to the tubing or to the end of the
fitting so as to achieve solder flow.
k. When the parts have achievedthe necessary temperature; solder
is to be added to the joint and the joint allowed to cool.
l. Theheat is to be applied for the shortest time possible, and never
directly to the area where the solder is being applied.
m. The internal parts of the piping packages are capable of
continuous use at 300°F, but will be quickly damaged at higher
temperatures.
n. When soldering vertical assemblies care must be taken to
prevent excess solder from dripping into the valve.
o. Heat discoloration from the sweating operation should not
extend to the major diameter of the valve body.
p. If disassembled, the valve must be reassembled in the reverse
order, with all of the parts returned to their original positions.
q. Automatic flow valves, strainers, and unions are equipped with
o-ring seals in the union connection.These seals provide
reliable, easy to use connections, but care must be taken to
prevent damage during installation.
r. Do not heat valve assembly with the o-ring in place. When
installing, be sure the o-ring is fully seated in the channel and not
twisted or misaligned.
s. The seal is the last item installed prior to tightening the union
nut. (The union nut is shipped loose on sweat fitting 2500 and
2400 series products.) Torque to the following values:
• 80 ft-lbs. for the 2514/2405 products
• 130 ft-lbs for the 2524/2407 products
t. If chlorinated flux has been used, all parts are to be flushed
thoroughly to avoid premature corrosion failure.
7. Inspect installation for leaks, kinks, twists, sharp bends, stretching
and chafing.
6
Operation
1. For optimum operation, air entrapment in the system must be
prevented.The flow control valve must remain filled with fluid. The
system must be clean and free of foreign materials.
2. The piping packages must only be used with fluids that are
compatible with iron, brass, santoprene and EPDM materials. The
temperature during operation must be limited to the range of 32 ° F
to 225 ° F.
3. Piping packages are fully compatible with ethylene glycol and
propylene glycol with all concentrations.
7
Maintenance
General maintenance is not required for piping packages. However, if
the system experiences large amounts of pipe scale due to poor water
conditions, as sometimes is found in older or retrofit systems, some
maintenance may be required. Provisions should be made to keep the
system clean. Proper water treatment is also recommended.
Trane optimizes the performance of homes and buildings around the world. A business of
Ingersoll Rand, the leader in creating and sustaining safe, comfortable and energy efficient
environments, Trane offers a broad portfolio of advanced controls and HVAC systems,
comprehensive building services, and parts. For more information, visit www.IRCO.com.
Trane has a policy of continuous product and product data improvement and reserves the right
to change design and specifications without notice.
© 2014 Trane All rights reserved
VAV-SVN012A-EN 02 Sep 2014
(NEW)
We are committed to using
environmentally conscious print
practices that reduce waste.