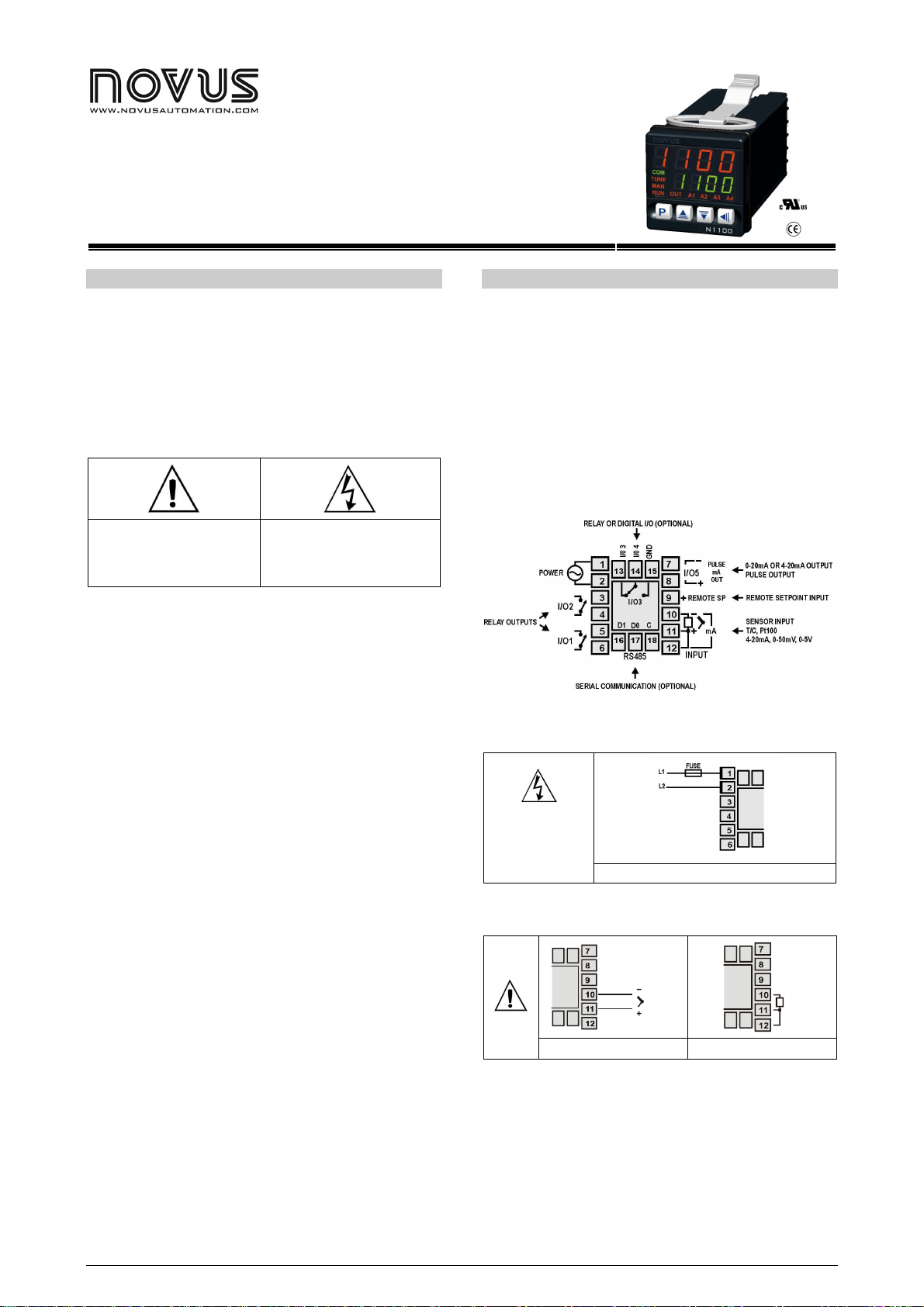
Controller N1100
UNIVERSAL PROCESS CONTROLLER – INSTRUCTIONS MANUAL V2.1x
PRESENTATION
The N1100 is a process controller incorporating a PID algorithm and
universal inputs (sensor and standard signals) and outputs (logical,
relay and analog outputs). It holds in one single instrument all de main
features that are needed for the vast majority of industrial processes.
SAFETY SUMMARY
The symbols below are used on the equipment and throughout this
document to draw the user’s attention to important operational and
safety information.
CAUTION or WARNING:
Read complete instructions prior
to installation and operation of the
unit.
CAUTION or WARNING:
Electrical Shock Hazard
All safety related instructions that appear in the manual must be
observed to ensure personal safety and to prevent damage to either
the instrument or the system. If the instrument is used in a manner
not specified by the manufacturer, the protection provided by the
equipment may be impaired.
OVER-TEMPERATURE PROTECTION
When designing any control system it is essential to consider what
will happen if any part of the system should fail. In temperature
control applications the primary danger is one in which the heating
remains constantly on. In any application where physical injury or
destruction of equipment might occur, it is recommend to install an
independent protection equipment, with a separate temperature
sensor, to disable the heating circuit in case of overheating. Please
note that the alarm relays within the controller will not give protection
under all failure conditions.
INSTALLATION
Insert the unit into the panel cut-out and slide the mounting clamp
from the rear to a firm grip at the panel.
ELECTRICAL CONNECTIONS
All electrical connections are made to the screw terminals at the rear
of the controller. They accept wire sizes from 0.5 to 1.5 mm2 (16 to
22 AWG). The terminals should be tightened to a torque of 0.4 Nm
(3.5 lb in).
To minimize the pick-up of electrical noise, the low voltage DC
connections and the sensor input wiring should be routed away from
high-current power conductors. If this is impractical, use shielded
cables. In general, keep cable lengths to a minimum.
• Power Wiring
If high voltage is applied
irreversible damage will
• Thermocouple and Voltage (Volts and mV) input connect as in
Figure 3.
to a low voltage input,
occur
Figure 3 – T/C and Voltage wiring Figure 4 - RTD input wiring
Figure 1 - Backpannel terminals
Figure 2 – High and Low Voltage AC power wiring
NOVUS AUTOMATION 1/8
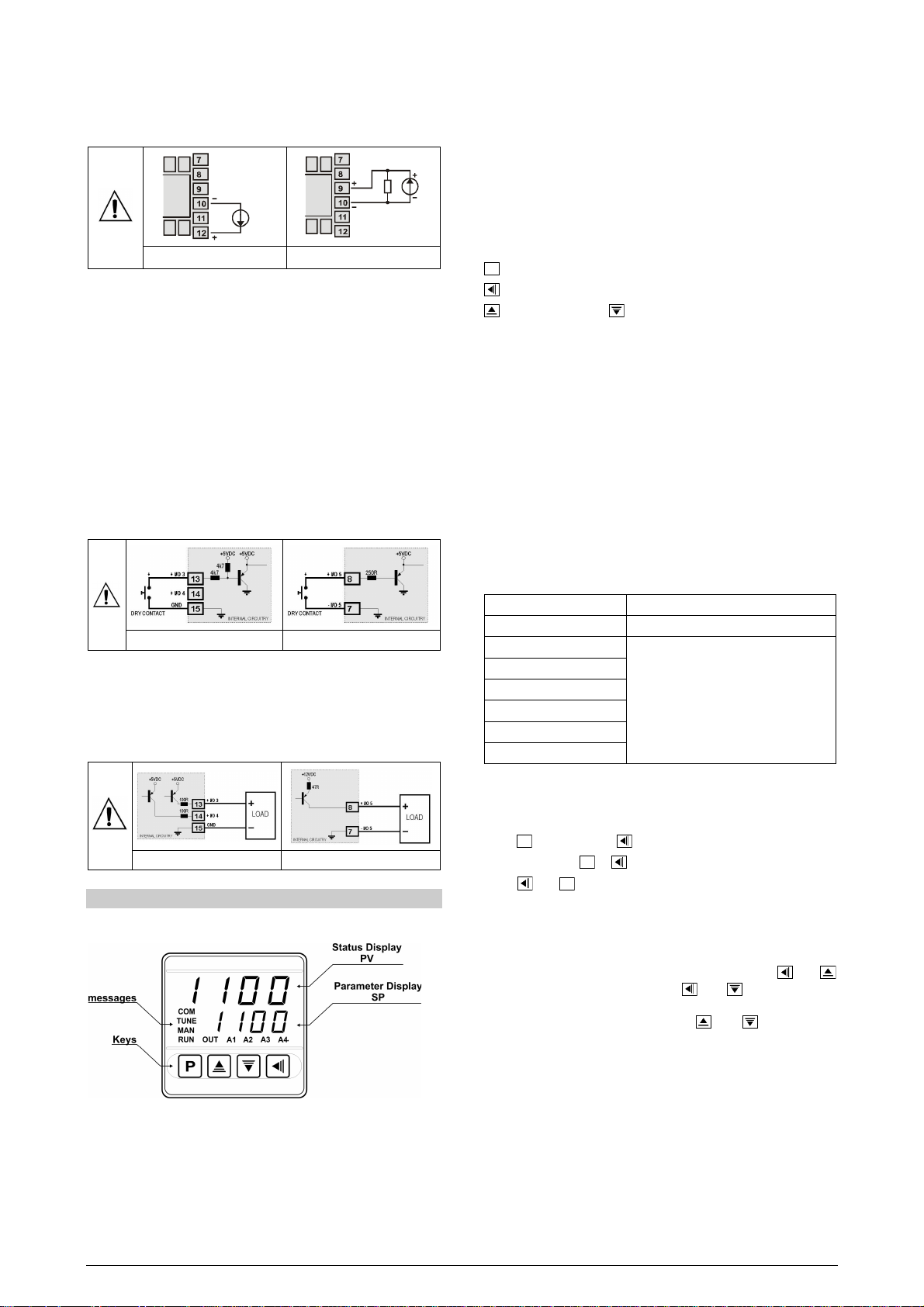
Controller N1100
• RTD (Pt100)
Figure 4 shows the Pt100 wiring, for 3 conductors. Terminals 10, 11
and 12 must have the same wire resistance for proper cable length
compensation. For 2 wire Pt100, short circuit terminals 11 and 12.
4-20mA
100R
Figure 5 – Current wiring Figure 6 – Remote SP input
4-20mA
• 4-20 mA
Refer to Figure 5. (The controller provides an internal electronic
shunt for the input current. No changes in the circuit are necessary).
• Remote setpoint
Input available at terminals 9 and 10. The user must connect a 100 Ω
resistor shunt as indicated in Figure 6.
• Digital Input
I/O3 and I/O4 can be used as digital inputs, accepting either dry
contact or NPN open collector signals. Figure 7a shows a switch
driving the I/O3 digital input. I/O4 can be used analogously. The
digital input at I/O5 is driven only by dry contact signals. Figure 7b
shows a typical digital input wiring for I/O5.
COM Indicator: Flashes when communication messages are sent by
the controller.
TUNE Indicator: Lights during the execution of PID automatic tunning.
MAN Indicator: Lights when the controller is in manual.
RUN Indicator: Lights when the controller is active, with control and
alarm outputs enabled.
OUT Indicator: For relay or pulse control output, reflects the actual
state of the output. If an analog output is assigned for control, lights
continuously.
A1, A2, A3 and A4 Indicators: Status of the alarms.
- PROG key: used to walk through the menu cycles
- BACK key: go back to the previous displayed parameter
- INCREASE and - DECREASE keys: Used to change
parameter values
When the controller is turned on, its firmware version is displayed for
3 seconds, after which the controller starts normal operation. The
values of PV and SV are displayed and the outputs are enabled.
Before the controller is ready to be used in a given process, it
requires some basic configuration, such as:
• input type (T/C, Pt100, 4-20 mA,...) at the “tYPE
tYPE” prompt,
tYPEtYPE
according to Table 1.
• output type at “I/O 1”, “I/O 2”,... “I/O 5” prompts (see Table 2).
• setpoint variable SV. Set the remaining parameters.
• PID parameters (or hysteresis for ON / OFF control).
Other functions, including alarms, ramp and soak, timer, digital input,
etc., may be useful for a better system performance. The parameters
are grouped in 7 cycles.
CYCLE ACCESS
Figure 7a – Digital input at I/O3 Figure 7b – Digital input at I/O5
• Digital Output
I/O3, I/O4 and I/O5 can also be configured as digital outputs (I/O3 and
I/O4 provide a 5 Vdc output signal whereas I/O5 a 12 Vdc signal). An
example of usage is shown in Figure 8 for the I/O3 and in Figure 9 for
the I/O5. I/O5 is electrically isolated from the sensor input.
1- Operation Free access parameters *
2- Tuning
3- R&S Program
4- Alarms
5- Input Configuration
6- I/Os
7- Calibration
Reserved access parameters **
* These parameters can be viewed but not changed if the cycle is
protected.
** Requires a key combination to access the cycle.
Figure 8 – I/O3 driving a SSR. Figure 9 – I/O5 digital output wiring.
OPERATION
The front panel is shown in Figure 10.
Press
Keep pressing the
Press and
to advance and to go back in the menu cycle.
or key to move fast forward or backward.
simultaneously to move from one cycle to the next
one.
At the end of each cycle the controller returns to the operation cycle.
PROGRAM SECURITY
Each menu cycle can be locked (protected) by pressing and
simultaneously for 3 seconds. Press and for 3 seconds to
unlock. A short blink of the display confirms the lock/unlock change.
This will alternately lock or unlock the and keys to avoid
tampering.
For further protection, the unlock operation through the keypad may
be disabled by changing the position of an internal strap inside the
Figure 10 - Front panel parts
Status display/PV: shows the value of PV (Process Variable). When
in programming mode, shows the parameter name.
Parameter display/SV: shows the SV (Setpoint Variable) value and
the value of other parameters of the controller.
controller:
When PROT is OFF, the user is allowed to lock and unlock the
cycles using the keypad as explained above. If PROT is ON, the
cycles lock / unlock operation is disable.
NOVUS AUTOMATION 2/8
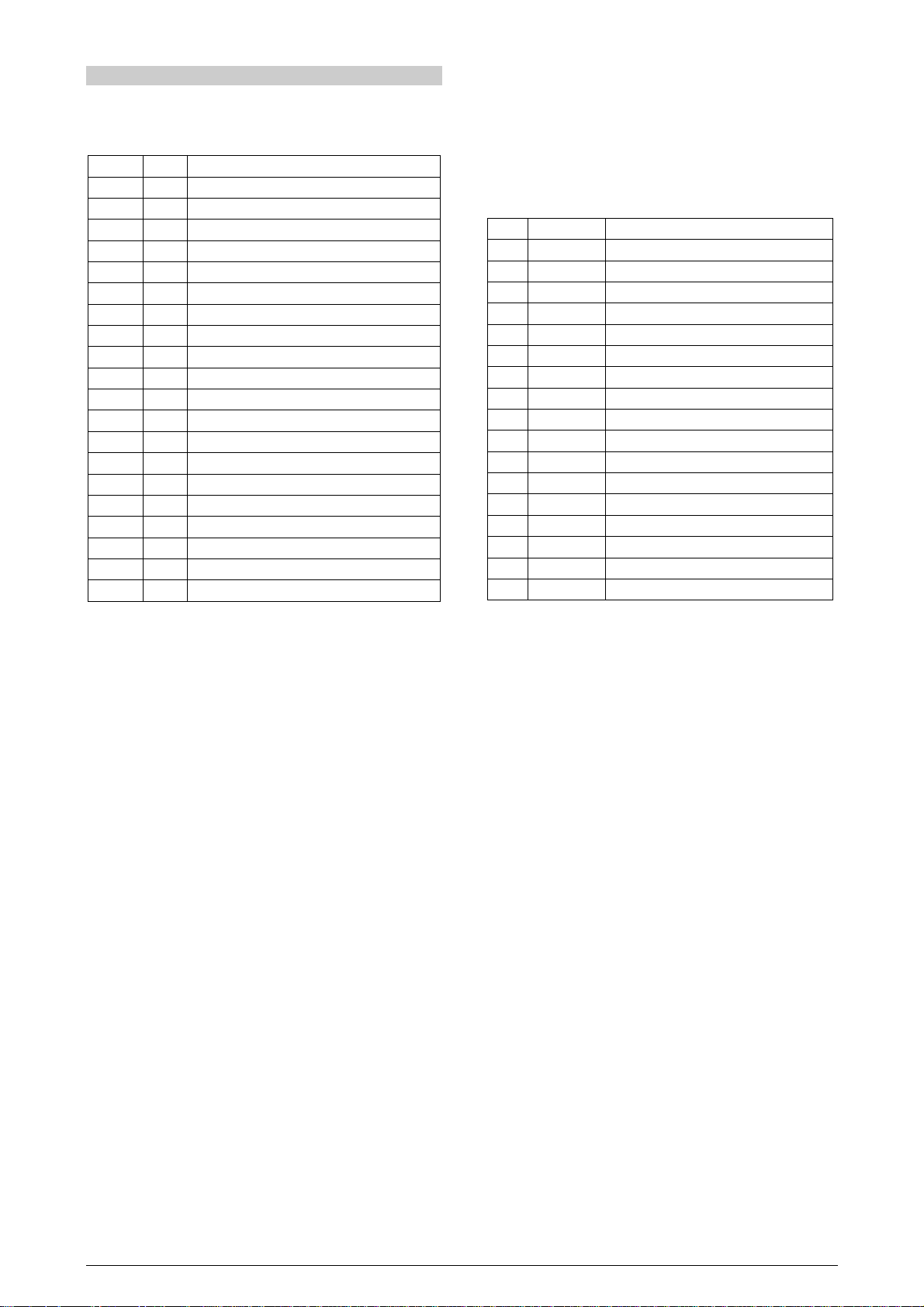
Controller N1100
CONFIGURATION
INPUT TYPE SELECTION
Select the input type (in parameter “tYPE
TYPE CODE CHARACTERISTICS
J
K
T
N
R
S
Pt100
Pt100
4-20 mA
4-20 mA
4-20 mA
4-20 mA
4-20 mA
4-20 mA
4-20 mA
4-20 mA
0-50 mV
4-20 mA
0-5 Vdc
4-20 mA
Range: -50 to 760 °C (-58 to 1400 ºF)
0000
Range: -90 to 1370 °C (-130 to 2498 ºF)
1111
Range: -100 to 400 °C (-148 to 752 ºF)
2222
Range: -90 a 1300 °C (-130 a 2372 ºF)
3333
Range: 0 a 1760 °C (32 a 3200 ºF)
4444
Range: 0 to 1760 °C (32 to 3200 ºF)
5555
Range: -199.9 to 530.0 °C (-328.0 to 986.0 ºF)
6666
Range: -200 to 530 °C (-328 to 986 ºF)
7777
J linearization. Programmable range: -110 to 760 °C
8888
K linearization. Programmable range: -150 to 1370 °C
9999
T linearization. Programmable range: -160 to 400 °C
10
10
1010
N Linearization. Programmable range: -90 a 1370 °C
11
11
1111
R Linearization. Programmable range: 0 a 1760 °C
12
12
1212
S linearization. Programmable range: 0 to 1760 °C
13
13
1313
Pt100 linearization. Prog. Range:-200.0 to 530.0 °C
14
14
1414
Pt100 linearization Prog. Range:-200 to 530 °C
15
15
1515
Linear. Programmable indication -1999 to 9999
16
16
1616
Linear. Programmable indication -1999 to 9999
17
17
1717
Linear. Programmable indication -1999 to 9999
18
18
1818
Square Root Extraction
19
19
1919
tYPE”) from Table 1 below.
tYPEtYPE
Table 1 - Input Types
• CODE 7 - Digital input - Standard for I/O5 and optional for I/O3 and
I/O4. Start/Stop input (“rvn
rvn” : YES / no).
rvnrvn
Closed : outputs enabled
Opened: outputs disabled
• CODE 8 - Digital input - Standard for I/O5 and optional for I/O3 and
I/O4.
Closed: remote SP (4-20 mA in remote SP input)
Opened: main SP (internal programmed SV)
CODE I/O TYPE I/O FUNCTION
Digital Output Digital Output to be set by the serial comm.
0000
Digital Output Alarm 1 Output
1111
Digital Output Alarm 2 Output
2222
Digital Output Alarm 3 Output
3333
Digital Output Alarm 4 Output
4444
Digital Output PWM Control Output
5555
Digital Input Automatic/Manual mode change
6666
Digital Input Run/Stop mode change
7777
Digital Input Select Remote Set Point Input
8888
Digital Input Executes/Holds selected ramp and soak profile
9999
Digital Input Enable/Disable R&S profile 1 selection
10
10
1010
Analog Output 0 to 20mA Analog control output
11
11
1111
Analog Output 4 to 20mA Analog control output
12
12
1212
Analog Output 0 to 20mA PV retransmission
13
13
1313
Analog Output 4 to 20mA PV retransmission
14
14
1414
Analog Output 0 to 20mA SP retransmission
15
15
1515
Analog Output 4 to 20mA SP retransmission
16
16
1616
Table 2 - I/O channel functions
OUTPUTS, ALARMS AND DIGITAL INPUTS CONFIGURATION
The controller input/output channels can assume multiple functions,
depending on configuration: control output, alarm output, digital
output, digital input, and PV or SV analog retransmission. These
channels are identified as I/O1, I/O2, I/O3, I/O4 and I/O 5.
The basic controller model comes loaded with:
• I/O1 - relay output
• I/O2 - relay output
• I/O5 - analog output (0-20 or 4-20mA), pulse 10V max, digital I/O
The options available are:
• I/O3 - 3rd relay (option 1)
• I/O3 and I/O4 - 2 digital input/output (option 2)
• Heater break protection (option 3).
The function code of each I/O can be selected among the options on
Table 2. Only valid function codes are displayed for each I/O (for
example, I/O1, which is a relay, can be configured with functions 0 to
5 only; on the other hand, I/05 can perform all 16 functions).
The description for the functions follows:
• CODE 0 - No function. The I/O channel programmed with code 0
will not be used by the controller. It is available to be used by serial
communication as digital output.
• CODES 1 to 4 - Alarm output - Available for all I/O channels. The
selected channel can be used as output to Alarms 1 to 4.
• CODE 5 - PWM control output - Available for all I/O channels.
• CODE 9 - Digital input - Standard for I/O5 and optional for I/O3 and
I/O4.
Opened: enables R&S program
Closed: holds R&S program (the program resumes when the
contact is opened again)
• CODE 10 - Digital input - Standard for I/O5 and optional for I/O3 and
I/O4. Selects R&S program 1. Used to alternate between the main
Setpoint and a second Setpoint defined by the R&S program 1.
Closed : selects program 1
Opened: uses main Setpoint
• CODE 11 - Analog control output - I/O5 only. 0-20 mA control
output.
• CODE 12 - Analog control output - I/O5 only. 4-20 mA control
output.
• CODES 13 to 16 - Analog retransmission. I/O5 only. Configures
I/O5 to output a 0-20 mA or 4-20 mA analog signal proportional to
PV or SP.
ALARM FUNCTIONS
The controller has 4 independent alarms. They can be programmed
to operate with nine different functions, represented in Table 3.
• Open sensor
It is activated whenever the input sensor is broken or disconnected.
• Event alarm
It activates alarm(s) in specific segments of the program.
• CODE 6 - Digital input - Standard for I/O5 and optional for I/O3 and
I/O4.
Closed : Manual control
Opened: Automatic control
NOVUS AUTOMATION 3/8
• Resistance fail
Detects a heater broken condition, by monitoring the load current
when the control output is activated. This alarm function requires an
optional device (option 3). Details of the "resistance fail" option can
be found in a specific documentation that is sent with the product
when the option is purchased.