
96M1374
Up to 8 units AP-V42AW/LV-22A/12SA
Up to 16 units FS-T2/M2/V12/V22/PS-T2/ES-M2
Operating status indicators
Set button
Display
Manual adjustment button
Expansion
protective cover
Mode button
Dust cover
Expansion
connector
Sensor head connector
Output 1
Output 2
AP-V41AW(P) AP-V42AW(P)
AI
Insert until it
clicks into place.
About
25 mm
About
25 mm
Connector
body
Connector
cover
Connector
lock
Orange
Brown
Blue
Gray
Pressure
connection
Wire-saving Digital
Pressure Sensor
AP-V41AW(P)/V42AW(P)
Instruction Manual
1. Safety Precautions
●
Do not use this product in safety circuits such as those designed to
protect human workers.
●
This product does not employ an explosion-proof construction. Do not
use it in the presence of flammable gasses, liquids, or powders.
●
This is a direct current power supply type sensor. Application of an
alternating current may result in explosion or fire.
3. Sensor Installation
●
●
Installation on a DIN track
1) Align the hook on the bottom
Installation using the included
mounting bracket
of the sensor to the DIN track
as shown below. Lower the sensor in the direction indicated by
➁while pressing on the sensor
in the direction indicated by ➀.
2) When removing the sensor, lift
the sensor as shown in ➂ while
pushing on the sensor in the direction indicated by ➀.
4. Additional Amplifier installation
A single AP-V41AW(P) sensor can be expanded
with the following number of slave units:
* The same applies to the PNP type of
the respective models.
1) Remove the AP-V41AW(P)
expansion protective cover.
2)Install the amps onto the DIN
track one at a time.
(AP-V41AW(P))
.
■ Accessories
●
1 sensor head
connector
●
1 mounting bracket
●
2 end units (included
with AP-V42AW(P))
●
Units sticker
(included with APV41AW(P))
2. Part Names
●
1 expansion seal
(included with
AP-V42AW(P))
●
1 instruction
manual
3) Insert the 2 hooks on each slave
unit into the groove on the APV41AW(P) until they click into
place.
4) Attach an end unit to each side
of the chain of amp units.
Sandwich the amps securely
between the end units and use
a Phillips head screwdriver to
tighten the screws on the top of
the end units (2 screws for each
unit).
5. Sensor Head Installation
1) Cut the cable to an appropriate
length and strip away about 25
mm of the outermost insulation.
Note: It is not necessary to
remove insulation from the
core wires.
2) Insert the cables after aligning
them with the colors on the seal
on top of the connector body.
3) Press together the body and the
connector cover into which the
cables were inserted to make a
connection (use a pair of pliers
or similar tool to press them together).
4) Insert the sensor head connector into the hole on the front of
the amp unit.
To remove the connector, depress the connector lock and
pull it out.
1
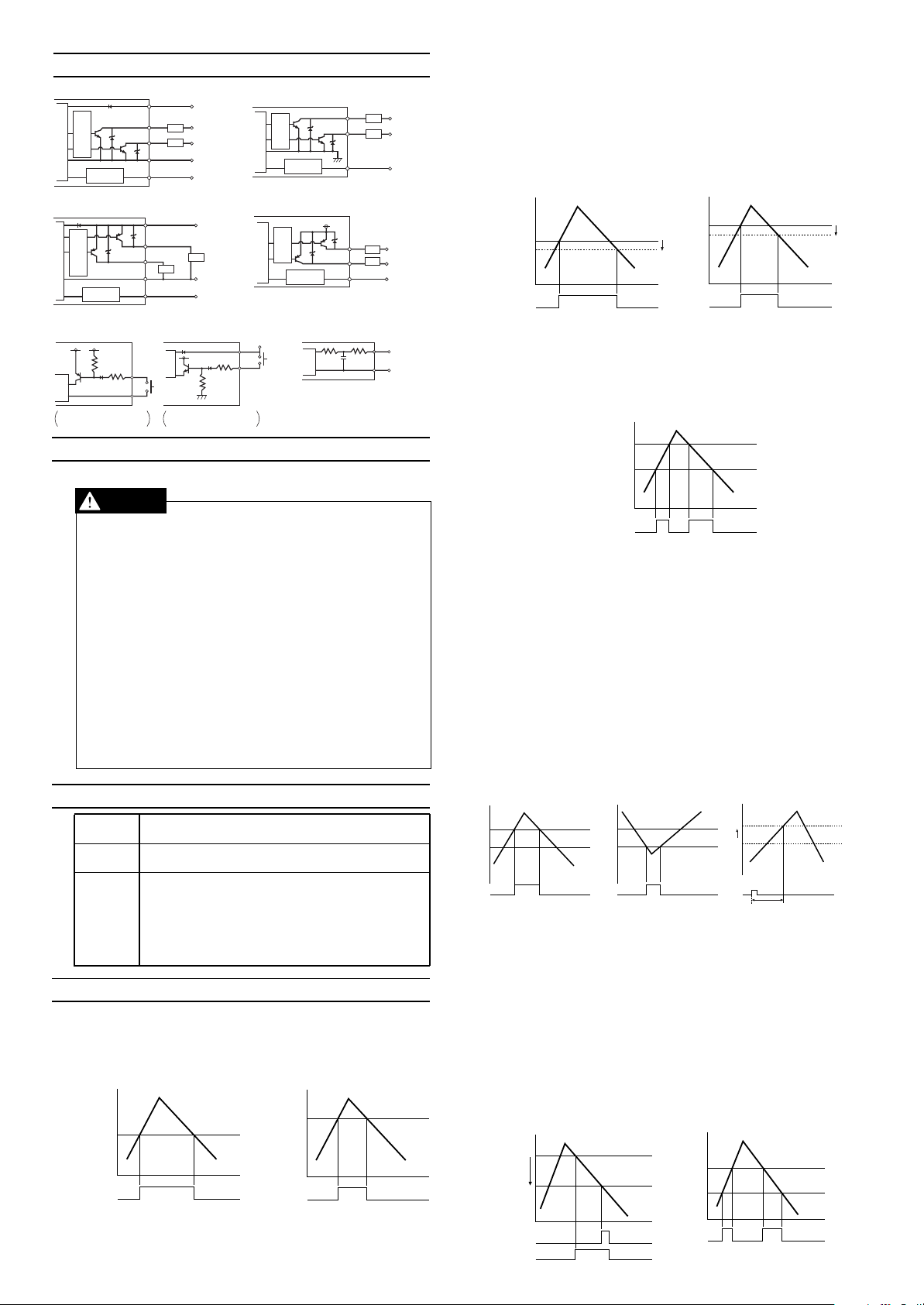
<Output 1>
P1
0
Output 1
OFF ON OFF
P2
0
OFF ON OFF
<Output 2>
Output 2
Hi
Lo
Output1/Output2
OFF ON ONOFF OFF
<Output 1/Output 2>
0
<Output 1>
P1
Output 1
OFF ON OFF
0
<Output 2>
0
Output 2
OFF ON OFF
P2
0
0
Shift
Zero shift input
T1
<Zero shift>
6. Connection Diagram
12 to 24 VDC
5 to 40 VDC
5 to 40 VDC
0V
Main circuit
Overcurrent
protection circuit
Load
Load
Input/output
circuit
Analog output/
zero shift input: switchable
Brown
Blue
Black
Control
output 1
Control
output 2
White
Pink
0 V
Load
Load
Zero shift input
5 to 40 VDC
Main circuit
Overcurrent
protection circuit
Input circuit
Black
White
Pink
5 to 40 VDC
Control
output 1
Control
output 2
12 to 24 VDC
0V
Main circuit
Overcurrent
protection circuit
Input/output
circuit
Analog output/
zero shift input: switchable
Brown
Blue
Black
White
Pink
Load
Load
Control
output 1
Control
output 2
12 to 24 VDC
0V 20mA max.
0V 20mA max.
Load
Load
Zero shift input
Main circuit
Overcurrent
protection circuit
Input circuit
Black
White
Pink
Control
output 1
Control
output 2
Short-circuit current AP-V41AW 5 mA max.
AP-V42AW 1 mA max.
Main
circuit
Blue
Pink
12 to 24 VDC
Main
circuit
Pink
Brown
Short-circuit current AP-V41AWP 5 mA max.
AP-V42AWP 1 mA max.
Analog
output (1 to 5 V)
0 V
Main
circuit
Blue
Pink
<Output 1>
P1
H1
Output 1
OFF ON OFF
0
P2
OFF ON OFF
H2
0
<Output 2>
Output 2
<Output 2>
Hi
Lo
Output 2
OFFONOFF OFF
ON
<Output 1>
P1
Output1
Zero shift input
OFF ON
OFF ON
0
Input/output circuit (AP-V41AW) Input/output circuit (AP-V42AW)
Input/output circuit (AP-V41AWP) Input/output circuit (AP-V42AWP)
■ Variable hysteresis mode (F-2)
Two detection points may be user-configured, and hysteresis for both
may also be set.
Control output 1
: Turns ON when pressure exceeds setting P1. Turns OFF
when pressure drops the selected hysteresis amount
below P1.
Control output 2:
Turns ON when pressure exceeds setting P2. Turns OFF
when pressure drops the selected hysteresis amount
below P2.
Zero shift input circuit
(AP-V41AW•V42AW)
Zero shift input circuit
(AP-V41AWP•V42AWP)
Analog output circuit
(AP-V41AW(P) only)
7. Precautions for Safe Use
Follow these guidelines. Failure to do so may result in product damage.
■
Connections
●
Always ground the frame ground terminal when using an off-the-shelf
switching regulator.
●
Use separate conduits for power line and high voltage lines, since use
of a common conduit may result in device malfunction.
●
Improper wiring may result in the device becoming excessively hot or
in device damage.
●
Sensor head connectors that have been pressure-connected once cannot be used again.
■
Notice about CE marking
●
Attach the ferrite core (OP-87505) if you extend a sensor head cable/
amplifier power cable to 3 m or more to use.
(Attachment position: within 100 mm from the amplifier unit of a
power cable, Number of turns: 2)
■
Other
●
Do not use this sensor with corrosive gasses or liquids.
●
Do not insert objects such as wire into the pressure insertion area.
Doing so may result in the device failing to operate properly due to
damage to the pressure-sensitive elements.
●
Do not use sharp-tipped objects to press the setting keys.
8. About Sensor Head Installation
Common Do not subject the case to pressure sufficient to deform
AP-41(M) • Use a torque of 0.3 N
43 • 44 for the sensor head conduits.
AP-48 Use a torque of 5 N
its shape during installation.
•
m or lower to tighten the screws
•
m or lower to tighten the screws for
the sensor head conduits.
Take care that no foreign objects enter the sensor when
opening one of the pressure ports to atmospheric air.
Take care not to bend the pressure ports.
Connect the “High” port to the high-pressure side of the
system and the “Low” port to the low-pressure side.
9. Detection Mode Operation
■ General-purpose mode (F-1)
This mode allows the user to configure 2 detection points.
Control output 1: Turns ON when pressure exceeds setting P1.
Control output 2: Turns ON when pressure exceeds setting P2.
■ Window mode (F-3)
The user may select a pair of upper (Hi) and lower (Lo) thresholds, and
the sensor turns OFF when the pressure falls outside of the resulting
range.
*Control output 1 uses a hysteresis of 0.5% of F.S., while control out-
put 2 uses a hysteresis of 0.
■ Application mode 1 (A-1)
This detection mode is optimum for use in suction detection applications.
Recommended heads: AP-41/41M/44
Control output 1:
Suction pressure detection.
Turns ON when pressure exceeds setting P1.
Control output 2:
Detection and confirmation of vacuum burst pressure
detection (or vacuum ultimate pressure).
Turns ON when the pressure falls below setting P2.
Zero shift: Shifts the zero point immediately after setting the zero
shift timer once zero shift input is received.
P1: Pressure setting for control output 1.
T1: Zero shift timer setting (ms)
P2: Pressure setting for control output 2.
*P2 is unrelated to zero shift and is always based on the current ambi-
ent pressure.
■ Application mode 2 (A-2)
This mode is optimum for use in leak test applications.
Recommended head: AP-43
Control output 1
: Leak pressure detection.
Turns ON when pressure falls below setting P1.
*Output only when zero shift input is ON.
Control output 2:
Window comparator output for detection of fill pressure.
Turns OFF when pressure falls outside the range deter-
mined by upper (HI) and lower (Lo) thresholds.
P1: Pressure setting for control output 1.
Hi: Upper threshold setting for control output 2.
Lo: Lower threshold setting for control output 2.
*The HI and Lo values are unrelated to zero shift and are always based
on the current ambient pressure.
*Hysteresis during general-purpose mode and application mode 1/2
operation is 0.5% of F.S. during standard and high-speed mode operation, and is 0.1% of F.S. during high-resolution mode operation.
2