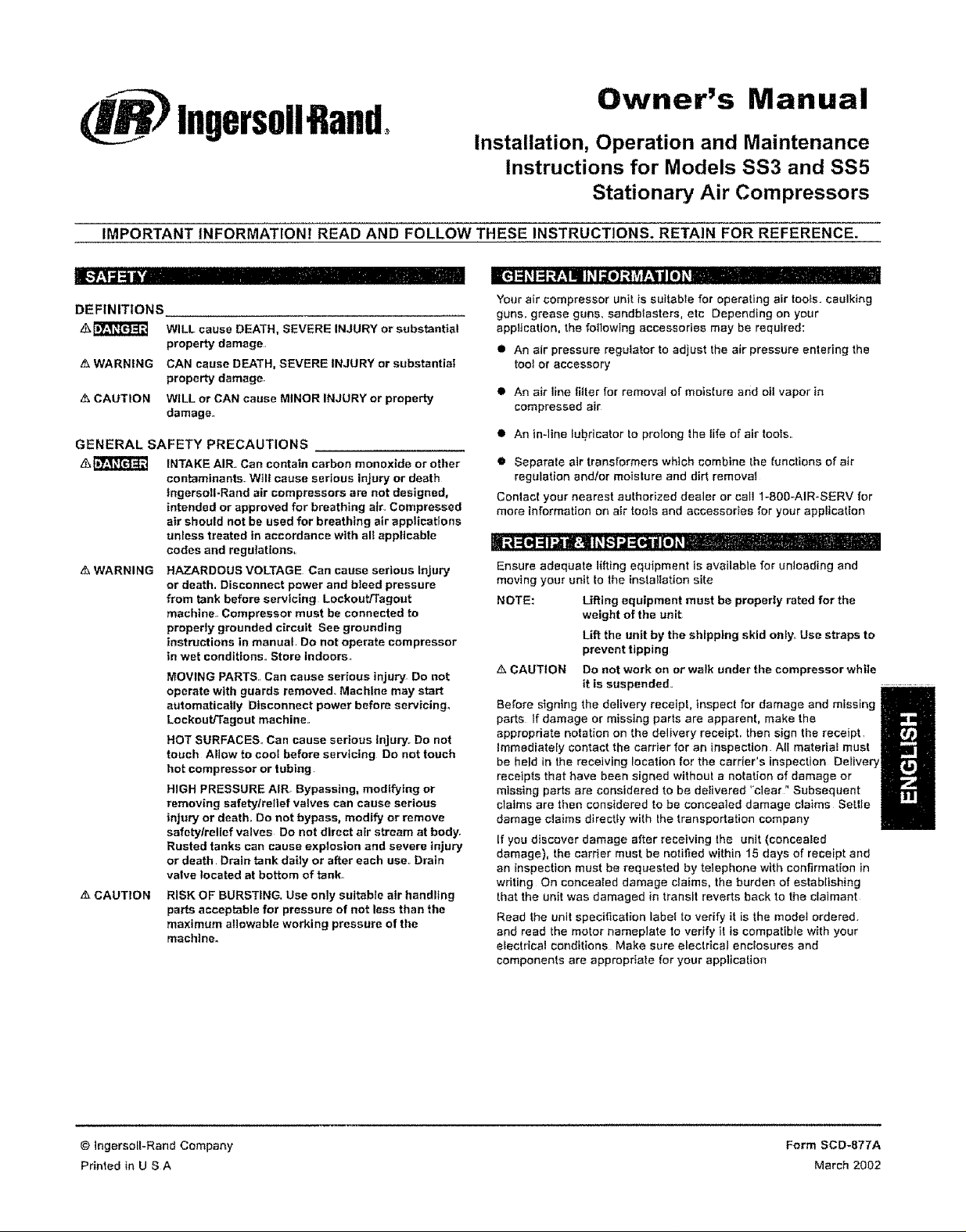
Owner's Manual
ingersoll
Installation, Operation and Maintenance
Instructions for Models SS3 and SS5
Stationary Air Compressors
IMPORTANT INFORMATION! READ AND FOLLOW THESE INSTRUCTIONS. RETAIN FOR REFERENCE.
ll_*-]r-1=1ulli"
DEFINITIONS
/k_ WILL cause DEATH, SEVERE INJURY or substantial
property damage
WARNING CAN cause DEATH, SEVERE INJURY or substantiaI
property damage,
CAUTION WILL or CAN cause MINOR INJURY or property
GENERAL SAFETY PRECAUTIONS
,_ _ iNTAKE AIR, Can contain carbon monoxide or other
WARNING HAZARDOUS VOLTAGE Can cause serious injury
z_ CAUTION
damage.
contaminants. Will cause serious injury or death
ingersoll-Rand air compressors are not designed,
intended or approved for breathing air Compressed
air should not be used for breathing air applications
unless treated in accordance with all applicable
codes and regulaUons,,
or death. Disconnect power and bteed pressure
from tank before servicing Lockout/Tagout
machine. Compressor must be connected to
properly grounded circuit See grounding
instructions in manuat, Do not operate compressor
tn wet conditions,, Store indoors
MOVING PARTS, Can cause serious injury Do not
operate with guards removed. Machine may start
automatically Disconnect power before servicing_
Lockout/Tagout machine,,
HOT SURFACES, Can cause serious injury, r DO not
touch Allow to cool before servicing Do not touch
hot compressor or tubing
HIGH PRESSURE AIR. Bypassing_ modifying or
removing safety/relief valves can cause serious
injury or death, Do not bypass, modify or remove
safety/relief valves Do not direct air stream at body.
Rusted tanks can cause explosion and severe injury
or death Drain tank daily or after each use. Drain
valve located at bottom of tank.
RISK OF BURSTING. Use only suitable air handling
parts acceptable for pressure of not less than the
maximum allowable working pressure of the
machine.
Your air compressor unitis suitable for operating air too_s, caulking
guns, grease guns, sandblasters, etc Depending on your
application, the following accessories may be required:
@ An air pressure regulator to adjust the alr pressure enlering the
toot or accessory
• An air line fitter for removal of moisiure and oil vapor in
compressed air
• An in-line lubricator to prolong lhe life of air tools.
ql, Separate air transformers which combine the !'unctions of air
regulation andlor moisture and dirt removal
Cenlact your nearest authorized dealer or cal! 1-800-AIR-SERV for
more information on air toots and accesser}as for your application
Ensure adequate lifting equipment is available for unloading and
moving your unit to the inslaIlatton site
NOTE: Lifting equipment must be property rated for the
weight of the unit.
Lift the unit by the shipping skid only,,Use straps to
prevent tipping
Lk CAUTION Do not work on or walk under the compressor while
it is suspended, -...........
Be[ore signing the deliveryreceipl,inspecl for damage and missing
parts If damage or missing parts are apparenL make the
appropriate notation on the delivery receipt, then sign the receipt.
Immediately contact the carrier for an inspection. All material must
be held in the receiving location for the carrier's inspection Deiivery
receipts that have been signed without a notation of damage or
missing parts are considered to be delivered "clear" Subsequent
claims are then considered to be concealed damage claims SeUle
damage claims directly with the transportation company
Lfyou discover damage after receiving the unit (concealed
damage), the carrier must be notified within 15 days of receipt and
an inspection must be requested by telephone with confirmation in
writing On concealed damage claims, the burden of establishing
that the unit was damaged in transit reverts back to the claimant
Read lhe unit specification labei to verify it is the mode! ordered.
and read the meier nameplate to verify il is compatibJe with your
e_ectrical conditions Make sure electrical enclosures and
componenls are appropriate for your applicafion
© IngersolL-Rand Company Form SCD-B77A
Printed in U S A March 2002
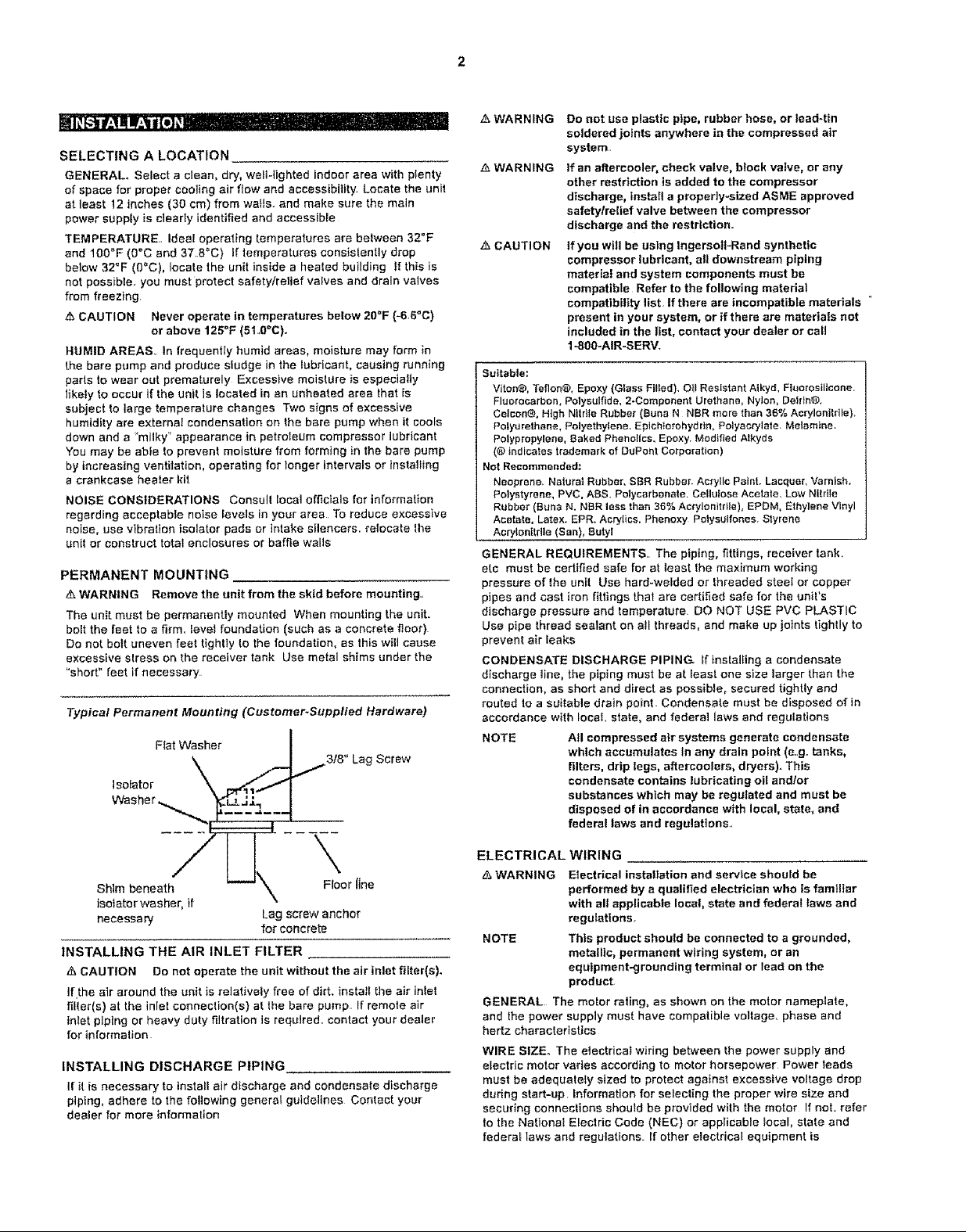
SELECTINGA LOCATION
GENERAL° Select a clean, dry, welt-lighted indoor area with plenty
of space far proper cooling air flow and accessibility. Locate the unit
at least 12 inches (30 cm) from wails, and make sure the main
power supply is clearly identified and accessible
TEMPERATURE.. Ideal operating temperatures are between 32"F
and 100°F (0°C and 37.B_C) If temperatures consistently drop
below 32°F (0"C), locale the unit inside a heated building !f th_s is
not possible, you must protect safety!relief valves and drain valves
from freezing
CAUTION Never operate in temperatures below 20°F (_6.6°C)
or above 125°F (5t.0°C)..
HUMID AREAS. In frequently humid areas, moisture may form in
the bare pump and produce sfudge in the lubricant, causing running
parts to wear out prematurely Excessive moisture is especially
likely to occur if the unit is located in an unheated area that is
subject to large temperature changes Two signs of excessive
humidity are external condensation on the bare pump when it cools
down and a "_mllky_appearance in petroleum compressor lubricant
You may be able to prevent moisture from forming in the bare pump
by increasing ventilation, operating for longer intervals or installing
a crankcase heater kit
NOISE CONSIDERATIONS Consull local officials [or information
regarding acceptable noise levels in your area To reduce excessive
noise, use vibralion isolator pads or intake silencers, relocate the
unit or construct total enclosures orbaffle waits
PERMANENT MOUNTING
WARNING Remove the unit from the skid before mounting..
The unit must be permanently mounted When mounting the unit.
bait the feet to a firm. fevel foundation (such as a concrete floor)
Do not bolt uneven feet tight}y to the foundation, as this will cause
excessive stress on the receiver tank Use metal shims under the
"short" feet if necessary
Typical Permanent Mounting (Customer.Supplied Hardware)
Fiat Washer
3/8" Lag Screw
Isofator
_ WARNING
,_.WARNING
z_ CAUTION
Suitable:
Viton®, Teflon@', Epoxy (Glass Fltied), O_1Resistant A_kyd, Fluorostllcone.
Fluorocarbon, Polysulflde, 2-Component Urethane, Nylon, DeSrln®.
Celcon®, High Nltrtle Rubber (Bane N NBR mare than 36% Aerylonltrlle).
Polyurethane, Polyethylene, Eplchtorohydr|n, Polyac_late. Melamine.
Potyprepylene, Baked PhenoIIce. Epoxy. Modified Alkyds
{® indicates trademark of DuPont Corporation)
Not Recommended:
Neoprene, Naturai Rubber, SBR Rubber. Acrylic Paint. Lacquer, Varnish.
Polystyrene, PVC, ABS. Poiycarbenate. Cellulos_ Acetate, Low Nttrtle
Rubber (Buna N. NBR less than 36% Actylonttdle), EPDM, Ethylene Vinyl
Acetate, Latex. EPR. Acrylics, Phenoxy Polysalfones. Styrene
Aorylenitrlte (San), Butyl
GENERAL REQUIREMENTS.. The piping, fittings, receiver tank.
etc must be certified safe for at least Ihe maximum working
pressure of the unit Use herd-welded or threaded steel or copper
pipes and cast iron fittings that are certified safe for the unit's
discharge pressure and temperature DO NOT USE PVC PLASTIC
Use pipe thread sealant on all threads, and make up joints tightly to
prevent air feaks
CONDENSATE DISCHARGE PIPING If inslalltng a condensate
discharge line, the piping must be at Ieast one size larger than the
connection, as short and direct as possible, secured tighBy and
routed to a suitable drain point Condensate must be disposed of in
accordance wffh local, state, and federal laws and regulations
NOTE All compressed air systems generate condensate
Do net use plastic pipe, rubber hose, or lead4in
soldered joints anywhere in the compressed air
system
If an afteroeoler, check valve, block vafve, er any
other restriction is added to the compressor
discharge, install a properly*sized ASME approved
safetytrelief valve between the compressor
discharge and the restriction.
If you will be using Ingerso!l-Rand synthetic
compressor lubricant, all downstream piping
material and system components must be
compatible Refer to the following material
compatibility list If there are incompatible materials
present in your system, or if there are materials net
included in the Hst, contact your dealer or cab
1=800-AIR-SERV.
which accumulates In any drain point (e.go tanks,
filters, drip legs, affercoolers, dryers). This
condensate contains lubricating oil and/or
substances which may be regulated and must be
disposed of in accordance with local, state, and
federal laws and regulations..
\
Shlm beneath Floor Jlne
isotater washer, if
necessary Lag screw anchor
INSTALLING THE A!R INLET FILTER
CAUTION Do not operate the unit without the air inlet filter(s).
If the air around the unit is relatively free of dirt, instant the air inter
filter(s) at the inlet conneclion(s) at the bare pump. If remote air
inlet piping or heavy duty filtration is required, contact your dealer
for information
INSTALLING DISCHARGE PIPING
If it is necessary to install air discharge and condensate discharge
piping, adhere to the following genera{ guidelines Conlact your
dee]or for more _nformation
for concrete
ELECTRICAL WIRING
_, WARNING Electrical installation and service shoutd be
performed by a qualified electrician who is familiar
with all applicable loca!, state and federal laws and
regu}attons r
NOTE This product should be connected to a grounded,
metallic, permanent wiring system, or an
equipment-grounding terminal or lead on the
product.
GENERAL The motor rating, as shown on the motor nameplate,
and the power supply must have compatible voltage, phase and
hertz characleristics
WIRE SIZE. The electrical wiring between the power supply and
electric motor varies according to motor horsepower Power leads
must be adequately sized to protect against excessive voltage drop
during start-up Information for selecting the proper wire size and
securing conneclions should be provided with the motor If not. refer
to the National EIeclric Code (NEC) or applicable local, stale and
federa_ laws and regulations. If other electrical equipment is
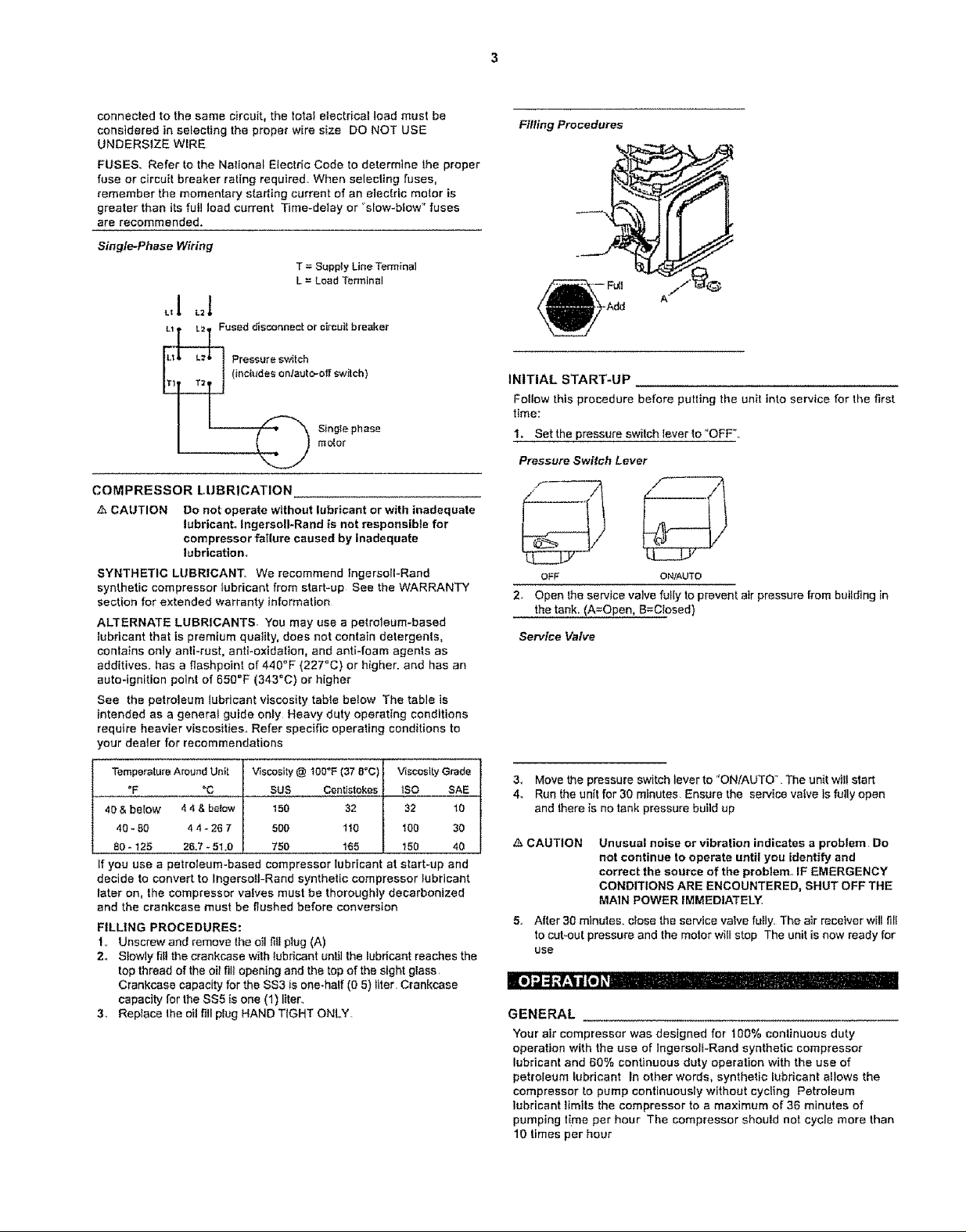
connected to the same circuit, the total electrica! load must be
considered in selecting the proper wire size DO NOT USE
UNDERSIZE WIRE
FUSES., Refer to the National Electric Code to determine the proper
fuse or circuit breaker rating required. When selecting fuses,
remember the momentary starting current of an electric motor is
greater than its full load current Time-delay or "slow-blow" fuses
are recommended.
Single-Phase Wiring
T = Supply Line Terminal
L = Load Terminal
uJ L=J
L1
Pressure switch
used disconnecLorclrcu_tbreaker
(inctltde_ on/auto-off switch)
Singie phase
m_or
COMPRESSOR LUBRICATION
CAUTION Do not operate without lubricant or with inadequate
lubricant. Ingersoll-Rand fs not responsible for
compressor failure caused by inadequate
lubrication
SYNTHETIC LUBRICANT. We recommend thgersolI-Rand
synthetic compressor lubricant from start-up See the WARRANTY
section for extended warranty information
ALTERNATE LUBRfOANTS. You may use a petroleum-based
lubricant that is premium quality, does not contain detergents,
contains only anti-rust, anti-oxidation, and anti-foam agents as
additives, has a fieshpoint of 440°F (227°C) or higher, and has an
auto-ignition polnt of 650=F (343°C) or higher
See the petroleum lubricant viscosity table below The table is
intended as a general guide only Heavy duty operating conditions
require heavier viscosities,, Refer specific operating conditions to
_our dealer for recommendations
Filling Procedures
INITIAL START-UP
Follow this procedure before putting the unit into service for the first
time:
t. Set the pressure swffch lever to "OFF"..
Pressure Switch Lever
OFF" ON/AUTO
2. Open the service valve fully to prevent air pressure from building in
the tank. (A=Open, B=Closed)
Service Valve
Temperature Around Unit Vlscosib' @ 100"F (37 8"C) Viscosity Grade
_F "C SUS Centtstokes 1SO SAE
40 & below 4 4 & below 150 32 32 10
40 - BO 44 - 26 7 500 t10 !00 30
80 - 125 26.7 - 51.0 750 165 '_50 40
you use a petroleum-based compressor lubricant at start-up and
decide to convert to Ingersoll-Rand synthetic compressor lubricant
later on, the compressor valves must be thoroughly decarbonized
and the crankcase must be flushed before conversion
FILLING PROCEDURES:
t,, Unscrew and remove the ell fillplug (A)
2. Slowly flit the crankcase with lubricant until the lubricant reaches the
top thread of the sit filI opening and the top of the sight glass
Crankcase capacity for the SS3 Is one-half (0 5) Iiter Crankcase
capacity for the SS5 is one (1) liter.,
3. Replace the oil fill plug HAND TIGHT ONLY
3. Move the pressure switch lever to "ON/AUTO _ The unit will start
4. Run the unit for 30 minutes Ensure the service vaive is fully open
and there is no tank pressure build up
CAUTION
Unusual noise or vibration indicates a problem Do
not continue to operate until you identify and
correct the source of the problem., IF EMERGENCY
CONDITIONS ARE ENCOUNTERED, SHUT OFF THE
MAIN POWER IMMEDIATELY,
5., After 30 minutes, close the service valve fully. The air receiver will fill
to cut-out pressure and the motor will stop The unit is now ready for
use
B[o]"J=1:_.,_II[=]h
GENERAL
Your air compressor was designed for f 00% continuous duty
operation with the use of Ingersoll-Rand synthetic compressor
lubricant and 60% continuous duty operation with the use of
petroleum lubricant In other words, synthetic lubricant allows the
compressor to pump continuously without cycling Petroleum
lubricant limits the compressor to a maximum of 36 minutes of
pumping time per hour The compressor should not cycle more than
10 times per hour

NORMAL START-UP
1 Set the pressure switch lever to "OFF"
2 Close the service valve
3 Attach hose and accessory
4., Move the pressure switch lever Io "ON/AUTO _ The coil will start
5. Allow tank pressure to build The motor will stop when tank pressure
reaches cut-out pressure,
6 Open the service valve The unit is now ready for use.
NOTE When the receiver tank pressure drops below the
factory pro-set minimum, the pressure switch resets
and restarts the unit,
WHEN YOU ARE FINISHED:
1 Set the pressure switch lever to "OFF"
2 Close the service valve fully
3 Remove the air loci er accessory
4 Slowly open the serv[ce valve to bleed air pressure down Io 20 psig
5 Slowly open the manual drain valve at the bottom of the tank ta
drain all condensate (water).,
6 Close the drain valve and the service vaIve for the next use
i I II'llI' ' I' '11I'lll'l
WARNING
Disconnect. lock and tag the main power supply and
release air pressure from the system before
performing maintenance.,
NOTE
All compressed air systems contain maintenance
parts (e g, lubricating oil, filters, separators) which
are periodically replaced,. These used parts may be,
or may contain, substances that are regulated and
must be disposed of in accordance with local, state,
and federal laws and regulations.
NOTE
Take note of the positions and locations of parts
during disassembly to make reassembly easier., The
assembly sequences and parts iliusfrated may differ
for your particular unit,,
NOTE
Any service operations not included in this section
should be performed by an authorized service
representative.
ROUTINE MAINTENANCE SCHEDULE
Dally or Before •
Eacl_ Operation •
Week{y •
Monthly Q
3!500 * •
12/2000 * •
" Indicates monthslopar_tlng hours, whichever occurs first;
Check lubricant leve_ Fil_ as needed
Drain receiver tank condensate Open the
manual drain vaive and cofiect and dispose of
condensate accordingly
• Check for unusual noise and vibration
• Ensure beltguards and covers are securely in
place
• Ensure area around compressor is free from
rags, tools, debris, and flammable or
explosive materials
Inspect air filter element Clean or replace if
necessary.
Inspec| for air leaks Squirt soapy water
around joints during compressor operation
and watch for bubbles
O
Check tightness of screws and botts,, Tighten
as needed
Clean exterior
Change petroleum lubricant while crankcase
is warm
Change synthetic lubricant while crankcase is
warm,
Replace filter element
FILTER REPLACEMENT (SS3)
1. Unscrew and remove the wing nut (A)
2. Remove the filter cover (B), baffle (C) and e_ement (D) from the
base (E)
3,, install a new efement and reassemble the filter assembly
NOTE The air intake holes in the baffle and cover must be
staggered t80 _.When reinstalling the assembly at
the inlet connection, ensure the intake hole in the
cover is on the bottom to minimize the entry of
foreign matter from the air
_J
FILTER REPLACEMENT (SS5)
1,, Unscrew and remove the wing nut (A) secudng the fitter housing (B)
to its base (C)
2., Remove the filter housing and withdraw lhe old fitler element (D)
Clean the elemen! wilh ajel of air or vacuum
3. Replace the f_ltarelement and housing, securing it in place with the
wing nut previously removed
OIL CHANGE
t. Remove the oil drain plug (A) and allow lhe lubricant 1o drain intoa
suitable container
2. Replace the oil dra_nplug
3. Follow the filfing procedures in OPERATION section
BELT ADJUSTMENT
CHECKING BELT TENSION Check bell tension occasionaf!y,
especially if looseness is suspected A quick check !o delermine if
adjustment is proper may be made by observing the stack side of
the bait for a slight bow when the unit is in operation if a slight bow
is evident, the belt is usuaily adjusted satisfactorily
TENSIONING BELTS Belt tensioning can be achieved by loosening
the motor anchor screws, pushing the motor away from the pump,
and reiightening tt_e motor anchor screws The motor can be easily
moved by placing a prying toot beneath it. A commercially available
spreader or other belt tensioning device can also be helpS'u1should
tensioning be necessary,