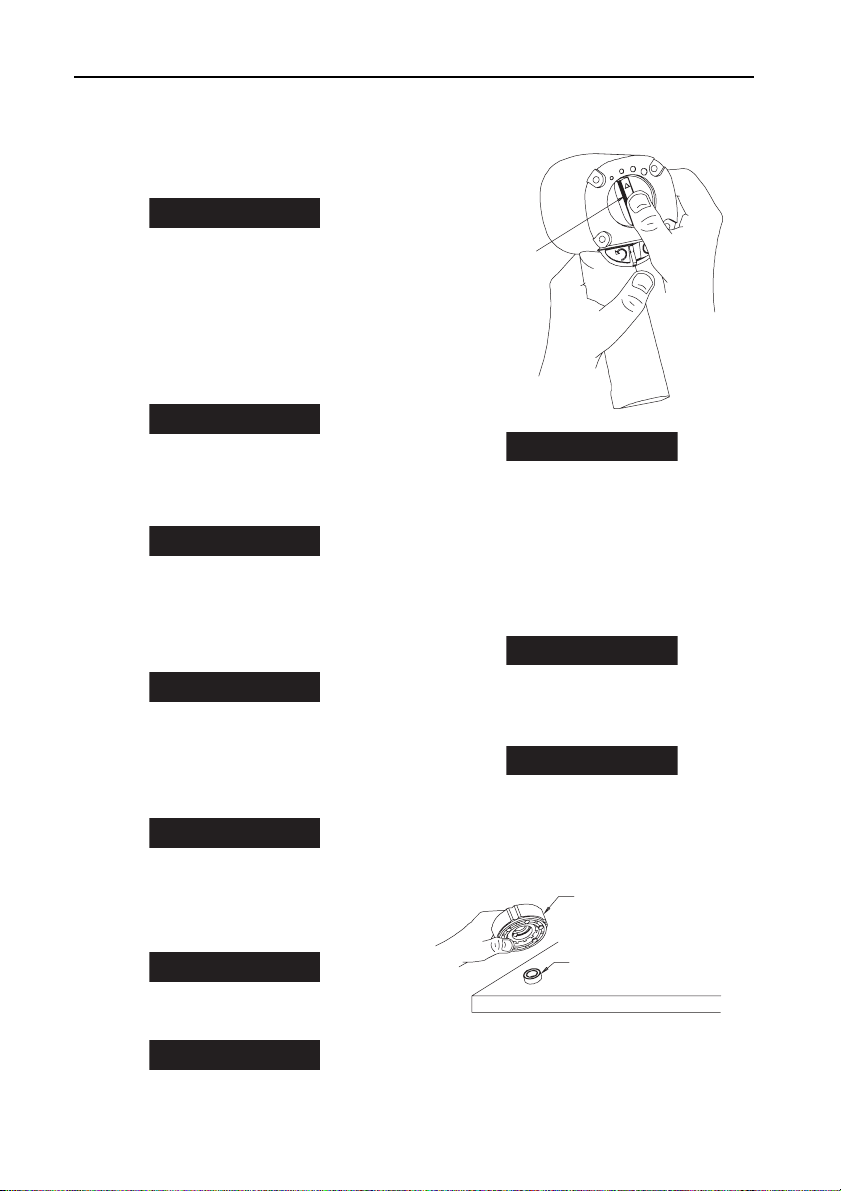
Disassembly
General Instructions
1. Do not disassemble the tool any further than necess ary to replace or
repair damaged parts.
2. Whenever grasping a tool or part in a vise, always use leathercovered vise jaws to protect the surface of the part and help prevent
distortion. This is particularly true of threaded memb ers and
housings.
NOTICE
Always use leather-covered vise jaws when clamping the handle in a
vise. Leather will conform to the shape of the handle an d allow the
tool to be held securely. To prevent damage to the exhaust diffuser,
never clamp only the bottom of the handle.
3. Do not remove any part which is a press fit in or on a subassembly
unless the removal of that part is necessary for repairs or
replacement.
4. Do not disassemble the tool unless you have a c omplete set of new
gaskets and O-rings for replacement.
Disassembly of the Impact Wrench
1. Clamp the handle of the impact wrench in a vise with leather-cove red
jaws with the square drive positioned horizontally.
NOTICE
Avoid excessive clamping pressure which can damage the Housing
and can cause difficulty when removing the parts.
2. Unscrew and remove the four Hammer Case Screws (12).
3. While lightly tapping on the end of the Anvil (9) wi th a plastic
hammer, lift off the Hammer Case (16) and Hammer Case Gasket
(19).
NOTICE
The Front End Plate (2) might come off during the removal of the
Hammer Case. Make sure that it does not drop on the floor or strike
a hard or metallic surface since it might be damaged.
4. Grasp the Hammer Frame (13) and carefully lift off the e ntire impact
mechanism, making certain not to drop the two Hammer P ins (14).
Disassembly of the Impact Mechanism
1. Set the mechanism, driver end up, on the workbench.
NOTICE
Note the twin hammers within the Hammer Frame. These are
identical, but must be placed in the Hammer Frame in a certain
relationship. Using a
felt-tipped pen, mark the top hammer “TÇ“ and the bottom hammer
“BÇ” with the arrows pointing upward. Mark both Hammers on the
same end.
2. With the mechanism sitting upright on the workbenc h, slowly rotate
the Anvil in a clockwise direction until it comes up solid.
NOTICE
If you continue to rotate the Anvil, it will cam the Hammers out of
engagement. Don’t do this; merely rotate the Anvil until it comes up
solid.
3. Hold the Hammer Frame firmly and without disturbi ng the hammers,
gently lift the Anvil while simultaneously rotating it c lockwise about 1/
8 of a turn, from the Hammer Frame.
4. With the Anvil removed, lift out the two Hammer Pins.
NOTICE
The twin hammers are now free to slide from the Hammer Frame. Be
careful do not to drop them.
Disassembly of the Motor
NOTICE
When pulling, disassembling or assembling the motor, we
recommend replacement of the Motor Gasket (8).
1. Remove the Motor Assembly from the Housing (20) by pushing on
Power Management Dial (42) from the back of the Hous ing. See
Dwg. TPD1322.
POWER
MANAGEMENT
DIAL
(Dwg. TPD1322)
NOTICE
If the Motor Assembly cannot be removed from the Housing by
pushing, tap the Power Management Dial lightly until the Motor
Assembly is free.
2. Remove the Power Management Dial from the rear of t he Cylinder
(1). Remove the Power Management Dial Seal (43) if it need s to be
replaced.
3. Remove the Front End Plate (2) from the Cylinder by tapping the
splined end of the Rotor (6) with a plastic hammer. If the Front End
Plate does not come loose, secure a center punch in a vise with the
point angled downward and outward from the vise. Grasp the
Cylinder and Front End Plate in one hand and position the hole in the
end of the Rotor against the punch.
NOTICE
Be careful not to drop the Cylinder since it can be damaged by
hitting a hard surface.
Using the other hand, tap the punch with a hammer while pr essing the
Rotor against the punch. After a few taps, the Front End Plate wi ll slide off
of the Cylinder.
NOTICE
To prevent damage to the Cylinder, do not tap or strike Cylinder on a
hard or metallic surface when removing the Rotor Bearings (3) and
(4).
To remove the Front Rotor Bearing, hold the Front End Plate with Front
Rotor Bearing down and tap the Front End Plate on a flat, nonmetallic
surface such as a work bench. This will loosen the F ront Rotor Bearing so
that it will drop out of the Front End Plate. See Dwg. TPD132 3.
FRONT END PLATE
FRONT ROTOR BEARING
BENCH WITH NONMETALLIC SURFACE
(Dwg. TPD1323)
2 Form 04583993-Edition 1
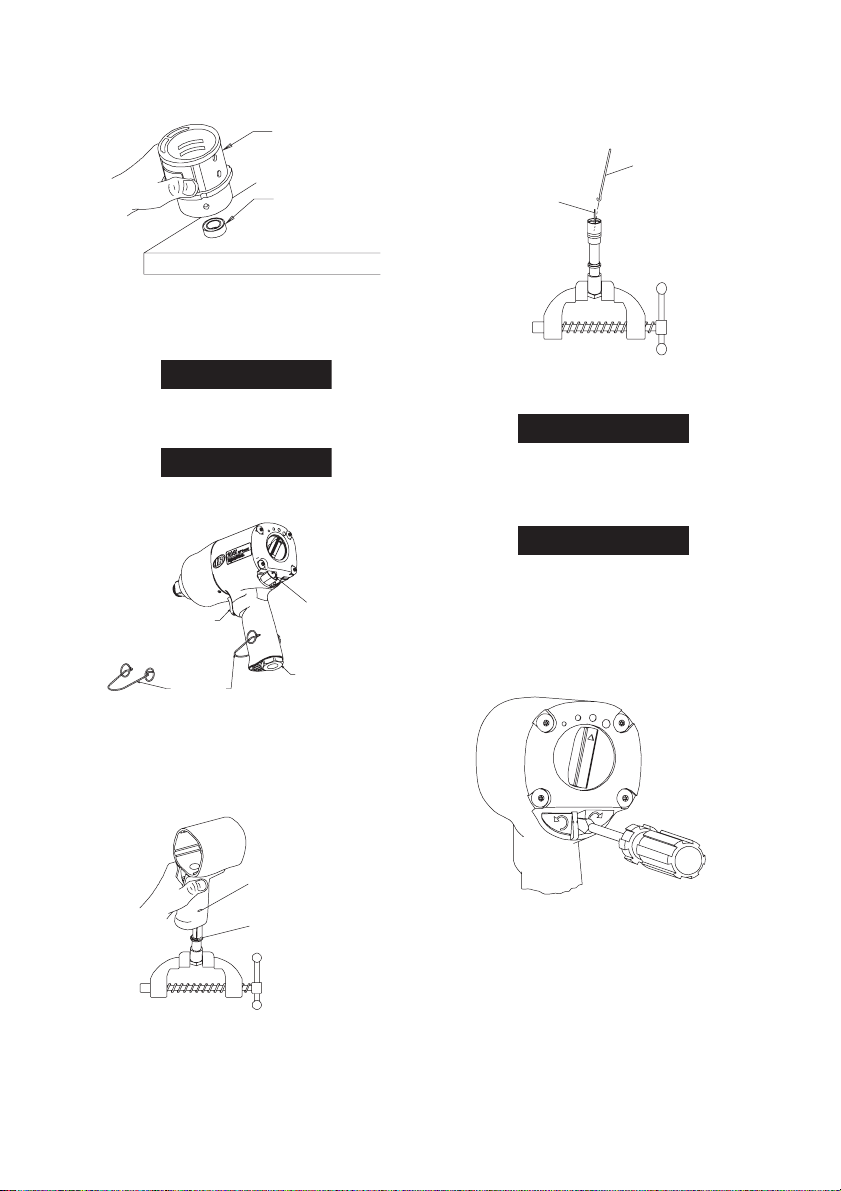
4. Remove the Rear Rotor Bearing Retainer (7) from the rear of th e
Rotor (6). The Rotor can now be removed from the Cylinder. Remove
the Vanes (5) from the Rotor if they need to be replaced.
CYLINDER
REAR ROTOR
BEARING
BENCH WITH NONMETALLIC SURFACE
(Dwg. TPD1324)
5. To remove the Rear Rotor Bearing, hold the Cylinder with the Rear
Rotor Bearing down and tap the Cylinder on a flat, nonmetallic
surface such as a work bench. This will loosen the Rear Rotor
Bearing so that it will drop out of the Cylinder. See Dwg. TPD1324.
6. Working from the rear of the Housing, push out the Motor Gasket (8).
NOTICE
When removing the Motor Gasket, do not use a scr ewdriver or any
other sharp object which could damage the Gasket an d/or Housing.
Disassembly of the Throttle Mechanism
NOTICE
For ease of disassembly, we recommend using the Inlet Clip
Removal Tool (44). See Dwg. TPD1812.
TRIGGER
INLET CLIP
REMOVAL
(Dwg. TPD1812)
1. Secure the Inlet Bushing in a vise. Press in both tabs of the Inlet
Retainer Clip (26) and pull upward on the Housing (20). This wi ll
allow the Inlet Bushing to come free from the Handle of the Housing.
See Dwg. TPD1326.
2. Pull the Trigger (34) from the front of the Housing and remov e the
Trigger O-ring (35).
TOOL
LEFT-HAND
BUTTON
INLET BUSHING
ASSEMBLY
3. With the Inlet Bushing still in the vise, remo ve the Tilt Valve Seat
Retainer (33) and Tilt Valve Seat Support (32). Use a hooked tool
with no sharp edges to remove the Tilt Valve Seat (31) from the Inlet
Bushing.
See Dwg. TPD1327.
HOOKED TOOL
TILT VALVE STEM
(Dwg. TPD1327)
4. Remove the Tilt Valve (30) and Tilt Valve Spring (29) if damaged.
5. Remove the Inlet Bushing Seal (28) and Inlet Retainer Clip (26) if
damaged.
NOTICE
Do not remove the Inlet Bushing Screen (25) from the Inlet Bushing
unless it is damaged. Clean the Inlet Bushing Screen by using a
suitable cleaning
solution in a well ventilated area.
Disassembly of the Reverse Valve Mechanism
NOTICE
The Reverse Valve Assembly cannot be removed without first
removing the Forward and Reverse Buttons (40) and (41). Therefore,
it is important that the procedure below be followed exactly.
1. Insert the screwdriver between the partition and the Button wh ich is
fully extended. Gently pry agai nst the Button to disengage the detent
so that the Button can be removed. After the Button is removed,
reach inside the Housing and rotate the Reverse Valve to extend the
remaining Button. Repeat the above procedure for t he remaining
Button. See Dwg. TPD1328.
REM OVA L OF
FOR WARD/
REVER SE
BUTT ONS
SLOT FOR TAB
(Dwg. TPD1326)
(BOTH SIDES)
TAB ON INLET
RETAINER CLIP
(BOTH SIDES)
(Dwg. TPD1328)
2. Insert thumb into the front of the Housing and push down on the
Reverse Valve so that it can be removed through the bottom of the
handle. See Dwg. TPD1329.
Form 04583993-Edition 1 3