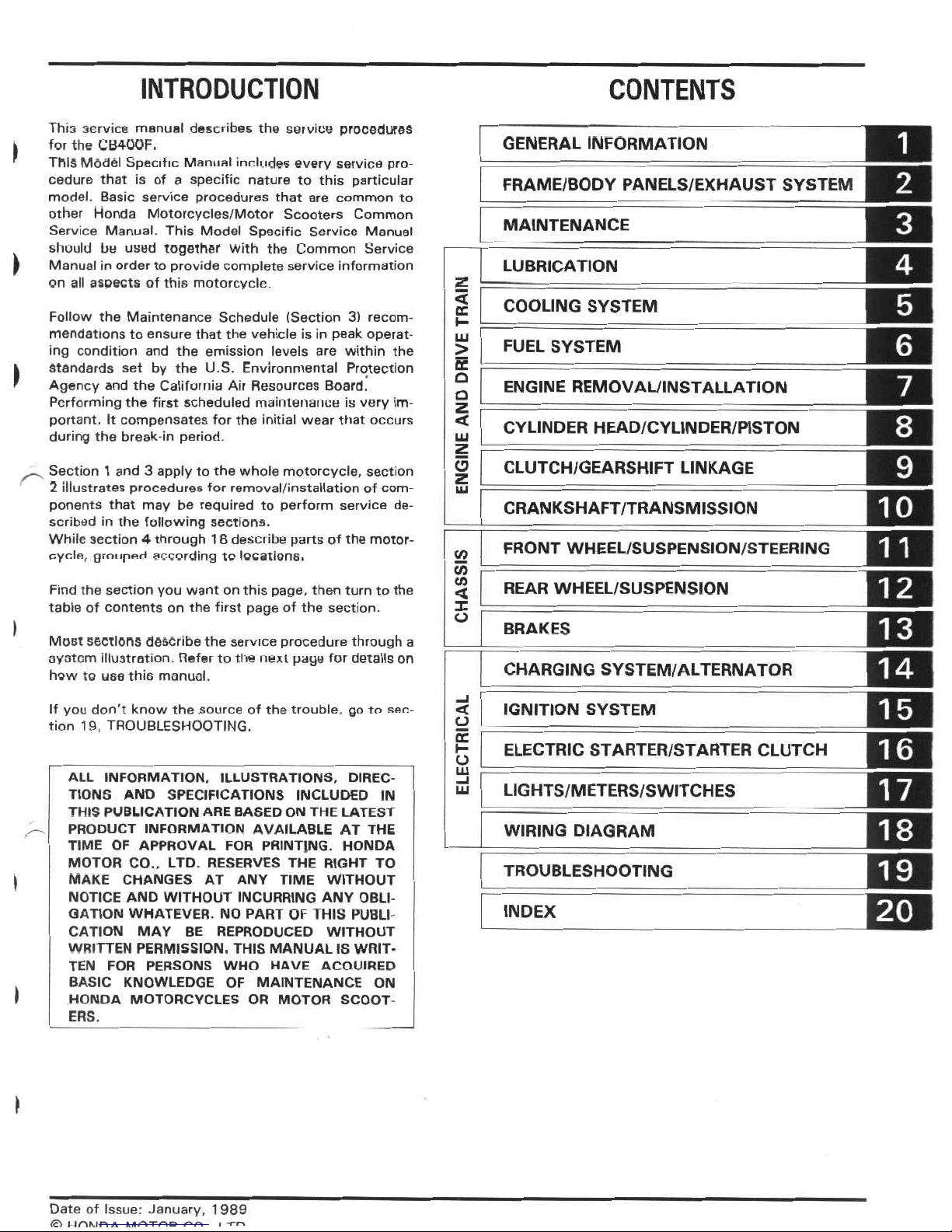
INTRODUCTION
CONTENTS
This
service
manual
describes
the
service
procedures
for
the
CB400F.
This
Model
Specific
Manual
includes
every
service
pro¬
cedure
that
is
of
a
specific
nature
to
this
particular
model.
Basic
service
procedures
that
are
common
to
other
Honda
Motorcycles/Motor
Scooters
Common
Service
Manual.
This
Model
Specific
Service
Manual
should
be
used
together
With
the
Common
Service
Manual
in
order
to
provide
complete
service
information
on
all
aspects
of
this
motorcycle
1
GENERAL
INFORMATION
I
FRAME/BODY
PANELS/EXHAUST
SYSTEM
MAINTENANCE
>
*
LUBRICATION
<
COOLING
SYSTEM
GC
Follow
the
Maintenance
Schedule
(Section
3)
recom¬
mendations
to
ensure
that
the
vehicle
is
in
peak
operat¬
ing
condition
and
the
emission
levels
are
within
the
standards
set
by
the
U.S.
Environmental
Protection
Agency
and
the
California
Air
Resources
Board.
Performing
the
first
scheduled
maintenance
is
very
im¬
portant.
It
compensates
for
the
initial
wear
that
occurs
during
the
break-in
period.
LU
FUEL
SYSTEM
>
ce
)
Q
ENGINE
REMOVAL/INSTALLATION
o
z
<
8
CYLINDER
HEAD/CYLINDER/PISTON
LU
CLUTCH/GEARSHIFT
LINKAGE
Section
1
and
3
apply
to
the
whole
motorcycle,
section
2
illustrates
procedures
for
removal/installation
of
com¬
ponents
that
may
be
required
to
perform
service
de¬
scribed
in
the
following
sections.
While
section
4
through
1
8
desetibe
parts
of
the
motor¬
cycle,
grouped
according
to
locations.
Z
LU
CRANKSHAFT/TRANSMISSION
FRONT
WHEEL/SUSPENSION/STEERING
2
C/5
C/5
REAR
WHEEL/SUSPENSION
Find
the
section
you
want
on
this
page,
then
turn
to
the
table
of
contents
on
the
first
page
of
the
section.
<
I
O
I
BRAKES
Most
sections
describe
the
service
procedure
through
a
ayatem
illustration.
Refer
to
the
next
page
for
details
on
hew
to
use
this
manual.
IF1
CHARGING
SYSTEM/ALTERNATOR
IGNITION
SYSTEM
If
you
don't
know
the
.source
of
the
trouble,
go
to
sec¬
tion
19,
TROUBLESHOOTING.
<
O
cc
ELECTRIC
STARTER/STARTER
CLUTCH
A
o
LU
ALL
INFORMATION,
ILLUSTRATIONS,
DIREC¬
TIONS
AND
SPECIFICATIONS
INCLUDED
IN
THIS
PUBLICATION
ARE
BASED
ON
THE
LATEST
PRODUCT
INFORMATION
AVAILABLE
AT
THE
TIME
OF
APPROVAL
FOR
PRINTING.
HONDA
MOTOR
CO..
LTD.
RESERVES
THE
RIGHT
TO
MAKE
CHANGES
AT
ANY
TIME
WITHOUT
NOTICE
AND
WITHOUT
INCURRING
ANY
OBLI¬
GATION
WHATEVER.
NO
PART
OF
THIS
PUBLI¬
CATION
MAY
BE
REPRODUCED
WITHOUT
WRITTEN
PERMISSION.
THIS
MANUAL
IS
WRIT¬
TEN
FOR
PERSONS
WHO
HAVE
ACQUIRED
BASIC
KNOWLEDGE
OF
MAINTENANCE
ON
HONDA
MOTORCYCLES
OR
MOTOR
SCOOT¬
ERS.
LIGHTS/METERS/SWITCHES
LU
WIRING
DIAGRAM
TROUBLESHOOTING
!
EH
INDEX
I
Date
of
Issue:
January,
1989
(51
nnMfi
A
n/inxoe
r-n
I
m

GENERAL
INFORMATION
MODEL
IDENTIFICATION
I
O
0
D
0,
c
o.
'CbJ
f0
Vÿ\
(1)
FRAME
SERIAL
NUMBER
\
0
L
I
The
frame
serial
number
is
stamped
on
the
right
side
of
the
steering
head.
(2)
ENGINE'SERIAL
NUMBER
c
V
m
\
\
o
V/
4$
I
ft
s.
\r\
(3)
VEHICLE
IDENTIFICATION
NUMBER
'
rs,
o.
The
engine
serial
number
is
stamped
on
the
right
side
of
the
crankcase.
The
Vehicle
Identification
Number
(VIN)
is
located
on
the
safety
certification
label
on
the
right
side
of
the
frame
tube.
I
(4)
CARBURETOR
IDENTIFICATION
NUMBER
V
l\
y
(CM
4L
>
\
&
37
N
Sm
__
_
(5)
COLOR
CODE
LABEL
>
The
carburetor
identification
number
is
on
the
rear
side
of
oach
carburetor.
The
color
code
label
is
attached
on
the
left
frame
tube
under
the
seat.
When
ordering
a
color
coded
part,
always
specify
its
designated
color
code.
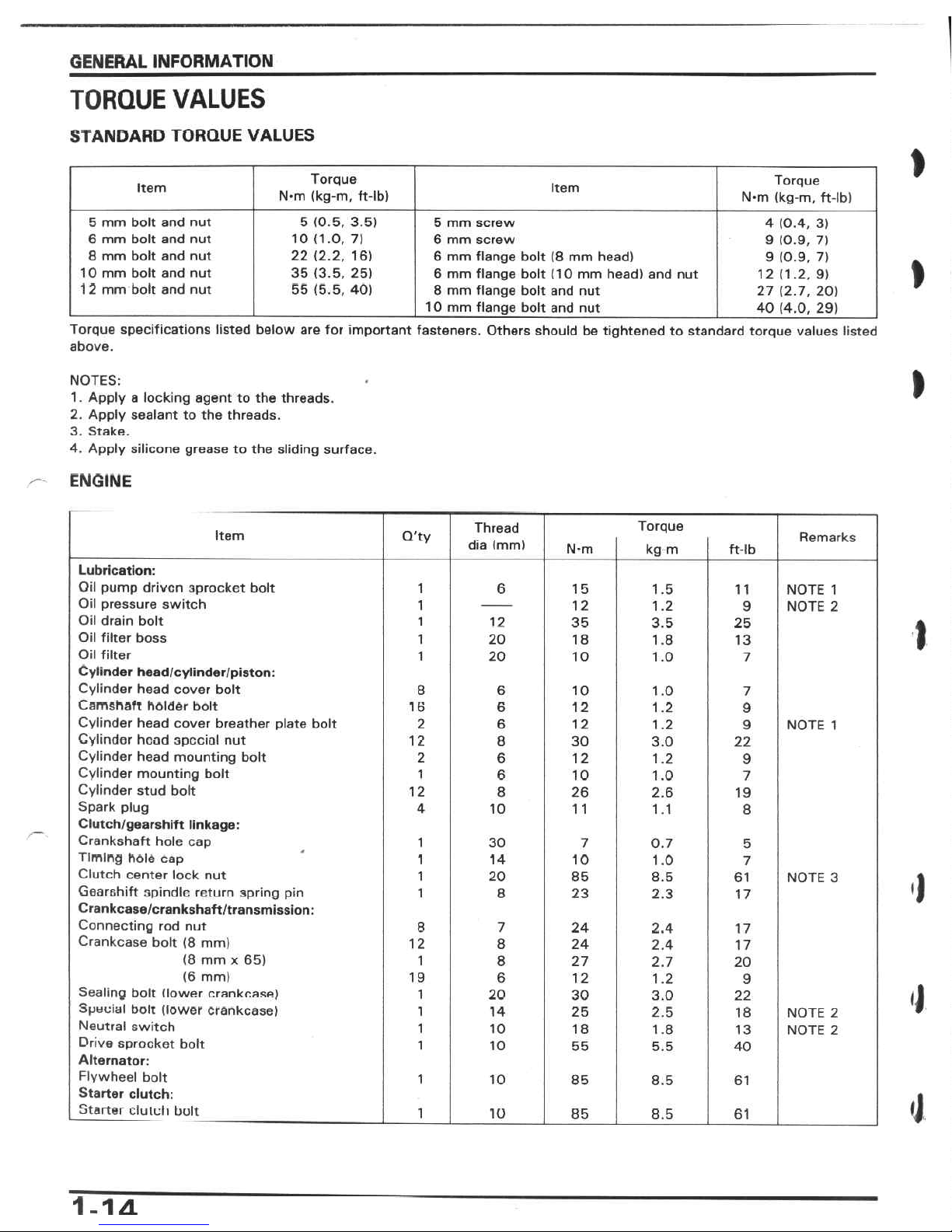
GENERAL
INFORMATION
TORQUE
VALUES
STANDARD
TORQUE
VALUES
I
Torque
N-m
(kg-m,
ft-lb)
Torque
N*m
(kg-m,
ft-lb)
Item
Item
5
(0.5,
3.5)
10
(1.0,
7)
22
(2.2,
16)
35
(3.5,
25)
55
(5.5,
40)
5
mm
bolt
and
nut
6
mm
bolt
and
nut
8
mm
bolt
and
nut
1
0
mm
bolt
and
nut
1
2
mm
bolt
and
nut
5
mm
screw
6
mm
screw
6
mm
flange
bolt
(8
mm
head)
6
mm
flange
bolt
(10
mm
head)
and
nut
8
mm
flange
bolt
and
nut
10
mm
flange
bolt
and
nut
4
(0.4,
3)
9
(0.9,
7)
9
(0.9,
7)
12
(1.2,
9)
27
(2.7,
20)
40
(4.0,
29)
t
Torque
specifications
listed
below
are
for
important
fasteners.
Others
should
be
tightened
to
standard
torque
values
listed
above.
I
NOTES:
1
.
Apply
a
locking
agent
to
the
threads.
2.
Apply
sealant
to
the
threads.
3.
Stake.
4.
Apply
silicone
grease
to
the
sliding
surface.
ENGINE
Torque
kg
m
Thread
dia
(mm)
Item
Q'ty
Remarks
N-m
ft-lb
Lubrication:
Oil
pump
driven
sprocket
bolt
Oil
pressure
switch
Oil
drain
bolt
Oil
filter
boss
Oil
filter
Cylinder
head/cylinder/piston:
Cylinder
head
cover
bolt
Camshaft
holder
bolt
Cylinder
head
cover
breather
plate
bolt
Cylinder
head
special
nut
Cylinder
head
mounting
bolt
Cylinder
mounting
bolt
Cylinder
stud
bolt
Spark
plug
Clutch/gearshift
linkage:
Crankshaft
hole
cap
Timing
hole
cap
Clutch
center
lock
nut
Gearshift
spindle
return
spring
pin
Crankcase/crankshaft/transmission:
Connecting
rod
nut
Crankcase
bolt
(8
mm)
(8
mm
x
65)
(6
mm)
Sealing
bolt
(lower
crankcase)
Spueial
bolt
(lower
crankcase)
Neutral
switch
Drive
sprocket
bolt
Alternator:
Flywheel
bolt
Starter
clutch:
Starter
clutch
bolt
1
6
15
1.5
11
NOTE
1
NOTE
2
1
12
1.2
9
1
12
35
3.5
25
I
1
20
18
1.8
13
1
20
10
1.0
7
8
6
10
1.0
7
IB
6
12
1.2
9
2
6
12
1.2
9
NOTE
1
12
8
30
3.0
22
2
6
12
1.2
9
1
6
10
1.0
7
12
8
26
2.6
19
4
10
1 1
1.1
8
1
30
7
0.7
5
1
14
10
1.0
7
1
20
85
8.5
61
NOTE
3
1
1
8
23
2.3
17
8
7
24
2.4
17
12
8
24
2.4
17
1
8
27
2.7
20
19
6
12
1.2
9
<1
1
20
30
3.0
22
1
14
25
2.5
18
NOTE
2
NOTE
2
1
10
18
1.8
13
1
10
55
5.5
40
1
10
85
8.5
61
•J
1
10
85
8.5
61
1-1
a.
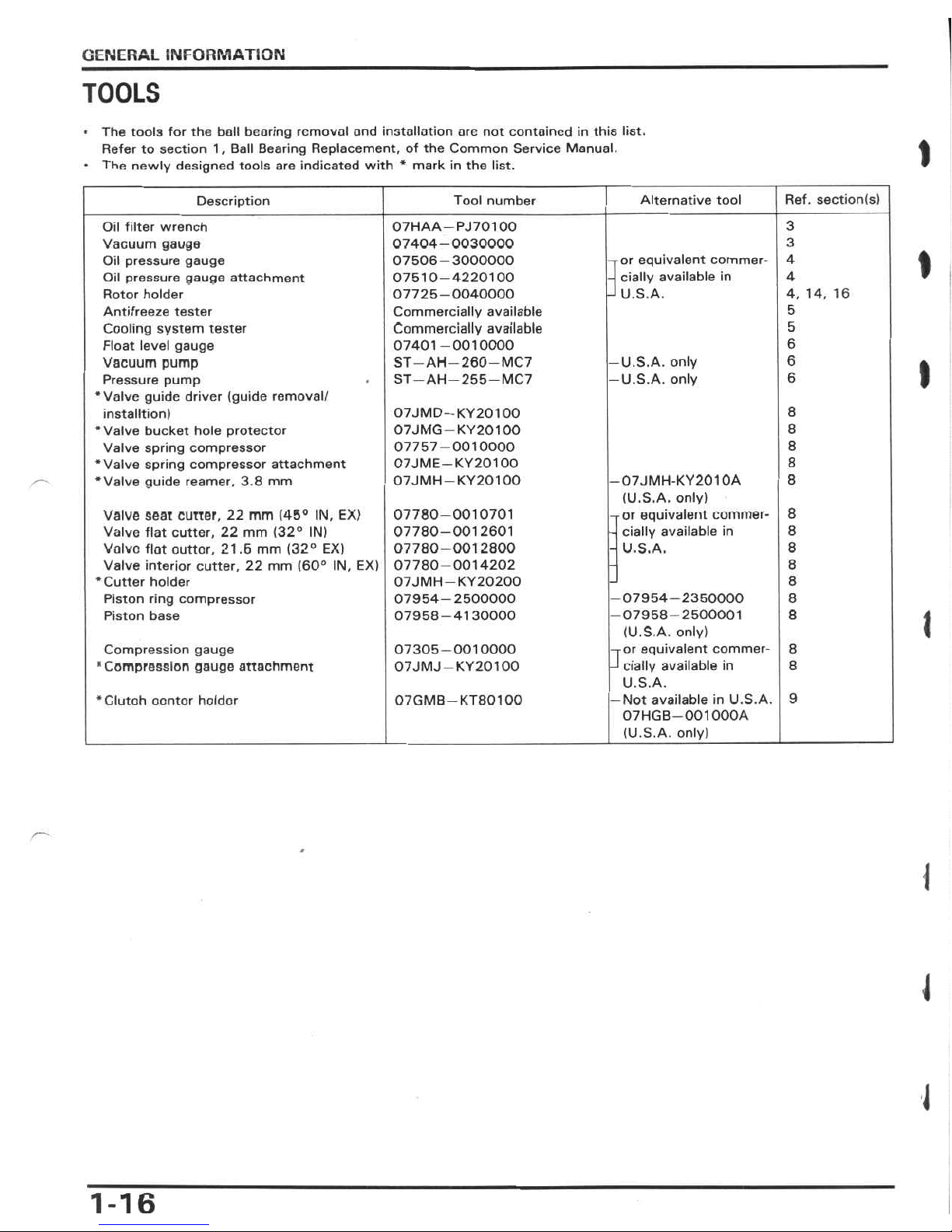
GENERAL
INFORMATION
TOOLS
•
The
tools
for
the
boll
bearing
removal
and
installation
arc
not
contained
in
this
list.
Refer
to
section
1
,
Ball
Bearing
Replacement,
of
the
Common
Service
Manual.
•
The
newly
designed
tools
are
indicated
with
*
mark
in
the
list.
1
Ref.
section(s)
Alternative
tool
Tool
number
Description
3
07HAA—PJ701
00
07404-0030000
07506-3000000
07510-4220100
07725-0040000
Commercially
available
Commercially
available
07401-0010000
ST
—AH—
260
—
MC7
ST
—
AH
—
255
—
MC7
Oil
filter
wrench
Vacuum
gauge
Oil
pressure
gauge
Oil
pressure
gauge
attachment
Rotor
holder
Antifreeze
tester
Cooling
system
tester
Float
level
gauge
Vacuum
pump
Pressure
pump
‘Valve
guide
driver
(guide
removal/
installtion)
•Valve
bucket
hole
protector
Valve
spring
compressor
•Valve
spring
compressor
attachment
•Valve
guide
reamer,
3.8
mm
3
I
4
-ror
equivalent
commer-
-
daily
available
in
J
U.S.A.
4
4,
14,
16
5
5
6
6
—
U.S.A.
only
—
U.S.A.
only
I
6
8
07JMD
—
KY20100
07JMG
—
KY201
00
07757-0010000
07JME
—
KY201
00
07JMH
—
KY201
00
8
8
8
—
07JMH-KY201
OA
(U.S.A.
only)
-ror
equivalent
cummer-
-
dally
available
in
-
U.S.A.
8
8
07780-0010701
07780-0012601
07780-0012800
07780-0014202
07JMH
—
KY20200
07954-2500000
07958-4130000
valve
seat
cutter,
22
mm
(45°
IN,
EX)
Valve
flat
cutter,
22
mm
(32°
IN)
Volvo
flat
outtor,
21.6
mm
(32°
EX)
Valve
interior
cutter,
22
mm
(60°
IN,
EX)
•Cutter
holder
Piston
ring
compressor
Piston
base
8
8
8
8
-07954-2350000
-07958-2500001
(U.S.A.
only)
or
equivalent
commer¬
cially
available
in
U.S.A.
—
Not
available
in
U.S.A.
07HGB
—
001
000A
(U.S.A.
only)
8
8
1
8
07305-0010000
07JMJ
—
KY20100
Compression
gauge
"Compression
gauge
attachment
J
8
9
07GMB
—
KT801
00
•Clutoh
oontor
holdor
l
J
J
1-16
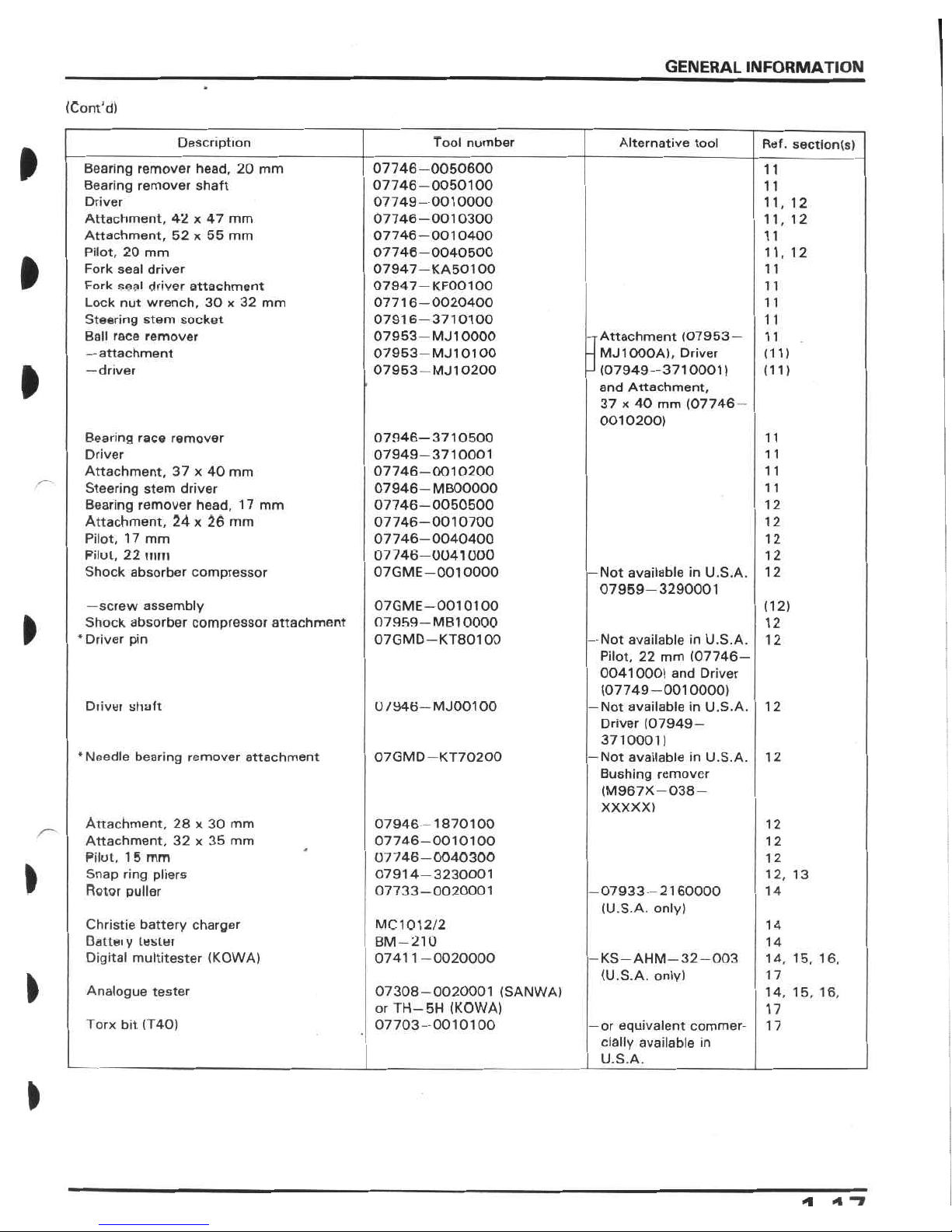
GENERAL
INFORMATION
(Corn'd)
Tool
number
Description
Alternative
tool
Ref.
section(s)
ft
07746-0050600
07746-0050100
07749-0010000
07746-0010300
07746-0010400
07746-0040500
07947-
KA501
00
07947
-KF001
00
07716-0020400
07916-3710100
07953-
MJ
10000
07953
—
MJ1
01
00
07953
—
MJ
10200
Bearing
remover
head,
20
mm
Bearing
remover
shaft
Driver
Attachment,
42
x
47
mm
Attachment,
52
x
55
mm
Pilot,
20
mm
Fork
seal
driver
Fork
seal
driver
attachment
Lock
nut
wrench,
30
x
32
mm
Steering
stem
socket
Ball
race
remover
—
attachment
—driver
1
1
11
11,
12
11,
12
11
11,
12
ft
11
11
11
11
-ÿAttachment
(07953
—
-
MJ1000A),
Driver
-l
(07949-3710001)
and
Attachment,
37
x
40
mm
(07746
—
0010200)
1
1
(11)
ft
(11)
Bearing
race
remover
Driver
Attachment,
37
x
40
mm
Steering
stem
driver
Bearing
remover
head,
17
mm
Attachment,
24
x
26
mm
Pilot,
1
7
mm
Pilot,
22
mm
Shock
absorber
compressor
07946-3710500
07949-3710001
07746-0010200
07946-
MB00000
07746-0050500
07746-0010700
07746-0040400
07746-0041000
07GME
—
001
0000
1 1
11
11
1
1
12
12
12
12
—
Not
available
in
U.S.A.
07959-3290001
12
—screw
assembly
Shock
absorber
compressor
attachment
‘Driver
pin
07GME
—
0010100
07959
—
MB1
0000
07GMD
—
KT801
00
(12)
ft
12
—
Not
available
in
U.S.A.
Pilot,
22
mm
(07746
—
0041000)
and
Driver
(07749-0010000)
—
Not
available
in
U.S.A.
Driver
(07949-
3710001)
—
Not
available
in
U.S.A.
Bushing
remover
(M967X—
038
—
XXXXX)
12
U
/946—
MJ001
00
Diivur
shaft
12
‘Needle
bearing
remover
attachment
07GMD
—
KT70200
12
Attachment,
28
x
30
mm
Attachment,
32x35
mm
Pilot,
1
5
mm
Snap
ring
pliers
Rotor
puller
07946-1870100
07746-0010100
07746-0040300
07914-3230001
07733-0020001
12
12
12
ft
12,
13
-07933-2160000
(U.S.A.
only)
14
Christie
battery
charger
Qatteiy
tester
Digital
multitester
(K0WA)
MC1012/2
BM-210
07411-0020000
14
14
—
KS
—
AHM
—
32
—
003
(U.S.A.
only)
14, 15,
16,
17
ft
Analogue
tester
07308-0020001
(SANWA)
or
TH-5H
(K0WA)
07703-0010100
14,
15,
16,
17
Torx
bit
(T40)
—
or
equivalent
commer¬
cially
available
in
U.S.A.
17
ft
<1
4
1