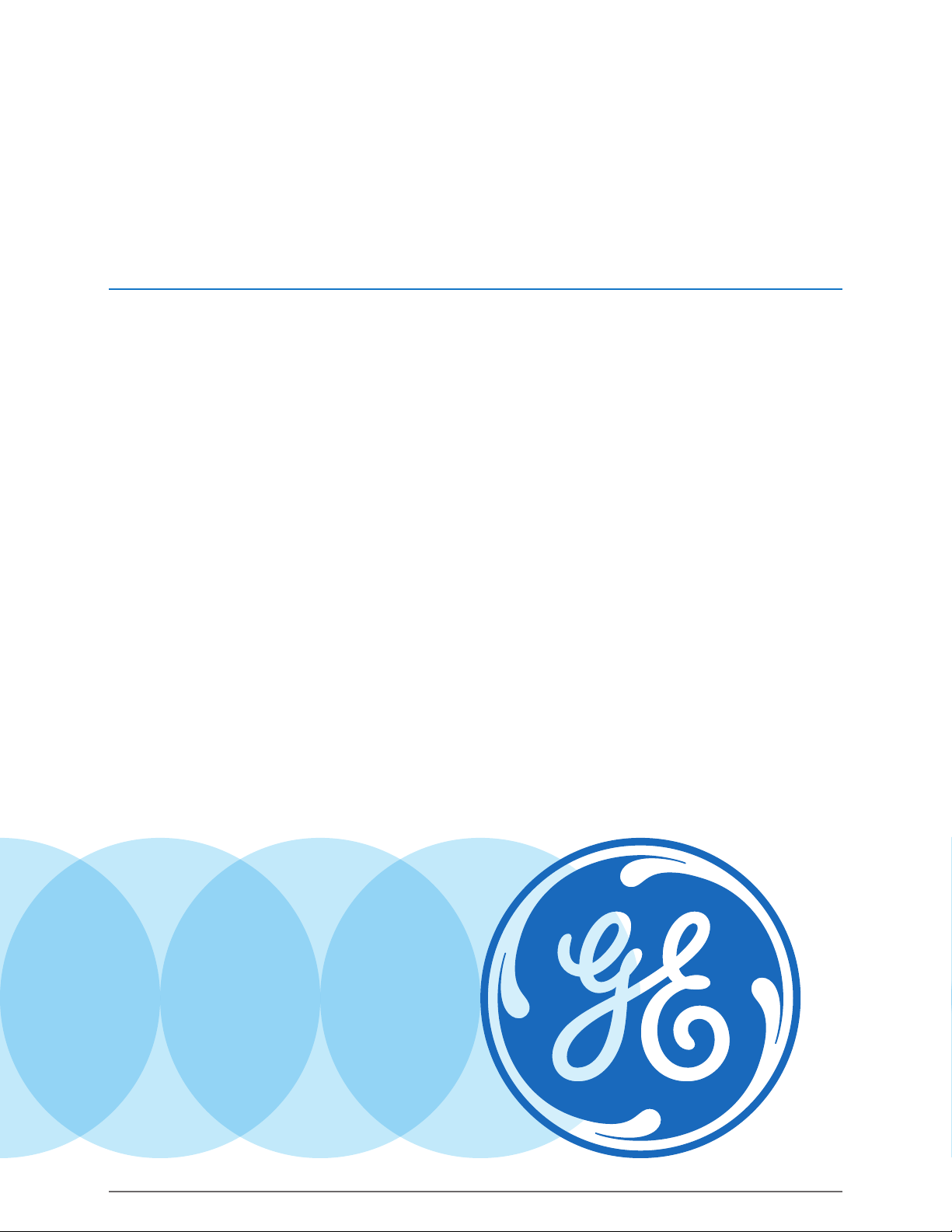
Aurora TDLAS analyzers
for Hydrogen Recycle
Applications
Technical White Paper
Topics:
Introduction ...................................................................................................................................................... 2
Online Moisture Measurement for Catalytic Reformer Units ..................................................................2
Aurora TDLAS platform ................................................................................................................................... 3
Aurora H2O Performance in H2 Recycle Process Stream .......................................................................... 4
References ......................................................................................................................................................... 8
Aurora TDLAS analyzers for Hydrogen Recycle Applications
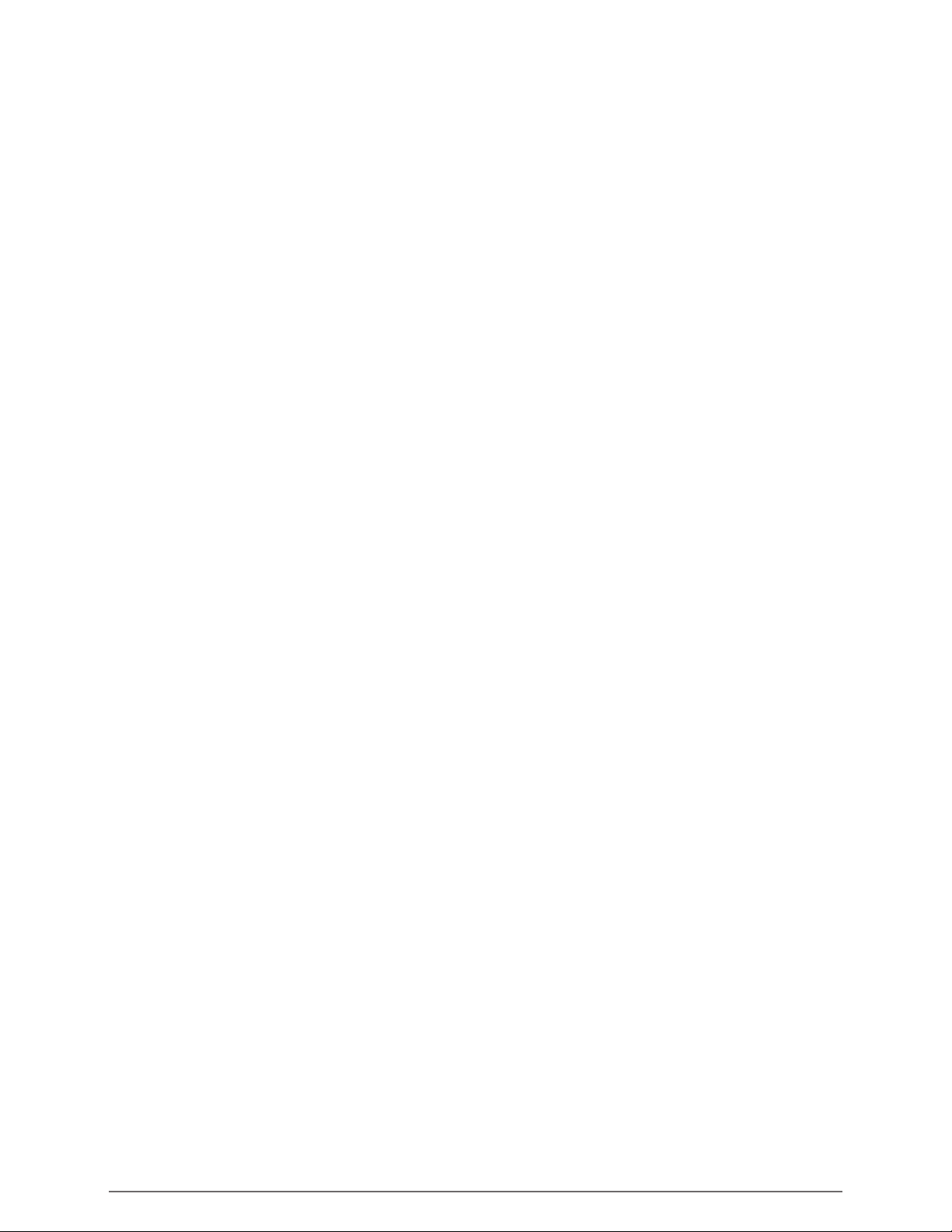
1. Introduction
The objective of the petroleum rening process is to convert crude oil into useful and protable end
products such as gasoline, jet fuel, diesel oil, liqueed petroleum gas and fuel oils. Hydrogen is widely
used in these downstream rening processes for the following reasons:
• increase the eciency or throughput of the chemical reaction,
• optimize the yield of the desired end product,
• improve quality of end product,
• remove undesired contaminants in fuels, such as sulfur, and
• maximize catalyst life
Clean fuels regulations are being implemented in many parts of the world including Europe and the
USA, and are going to become stricter as time progresses. Major oil renery upgrades are necessary
in order to meet these specications, and one of the consequences is that hydrogen demand will
increase dramatically. Various sub-processes used in rening include hydro-treating, hydrocracking,
catalytic reforming, isomerization, alkylation and several others. These sub-processes vary depending
on the input feed stock and the desired modication to that feed stock. Process objectives include
conversion of petroleum renery naphthas distilled from crude oil (typically having low octane
ratings) into high-octane liquid reformates, sulfur removal, and producing specic end products, such
as diesel oil.
It is estimated that the total hydrogen consumption in oil reneries is 12.4 BCF/day or approximately
100-200 SCF/bbl of oil processed. Hydrogen consumption is growing at 5–10% CAGR driven by low
sulfur in diesel fuel requirements, increasing use of low quality heavy crude oil, which requires more
hydrogen to rene, and increased global oil consumption driven by emerging markets such as China
and India. Therefore, management of hydrogen and its associated cost is critical to the protability of
reneries [1].
The moisture content in H2 recycle processes can vary from the sub-part per million by volume
(PPMv) level to higher concentration of ~20 – 30 PPMv. For example, in isomerization, the moisture
content must be tightly controlled to less than 1 PPMv to prevent poisoning of the Pt/metal oxide
catalysts due to hydrogen removal, consequently reducing catalyst lifetime and driving up costs. For
catalytic reforming of crude oil, moisture is a necessary component of the reaction chemistry and
must be maintained at the 15–20 PPMv level [2].
2. Online Moisture Measurement for Catalytic Reformer Units
The eciency of producing desired chemical reactions, and therefore, output yield of the required
petroleum products is adversely aected if moisture content in the recycle gas is not maintained
in the optimum range 20 to 30 PPMv. Hydrocarbon crackers incur signicant cost from inaccurate
and slow responding online moisture sensors. Current technology utilized to monitor moisture
levels in hydrogen recycle gas mixtures includes Quartz crystal microbalance (QCM) analyzers
and Aluminum Oxide based probes. These methods have several drawbacks that can delay
the moisture measurement, resulting in process excursions and o-specication product. QCM
technology requires the sensor to be continually compared with a reference “zero” gas, which results
in a non-continuous measurement. The self-verication requires the ability to generate a known
moisture content using a desiccant, permeation tube and precise gas ow rates. As such, a QCM
analyzer has a fairly complex internal sample handling system increasing the CAPEX and requiring
signicant maintenance, which increases OPEX as well. Aluminum oxide sensors are generally slower
responding to very dry gas and can drift over time [3].
While Tunable Diode Laser Absorption Spectroscopy (TDLAS) provides fast and accurate analyzers
with a higher initial cost compared to other technologies, the return on investment is achieved
by speed of response, reliability, repeatability, and negligible maintenance requirements (i.e.,
recalibration and replacement of moisture probes). Maintenance requirements include cost of
Aurora TDLAS analyzers for Hydrogen Recycle Applications
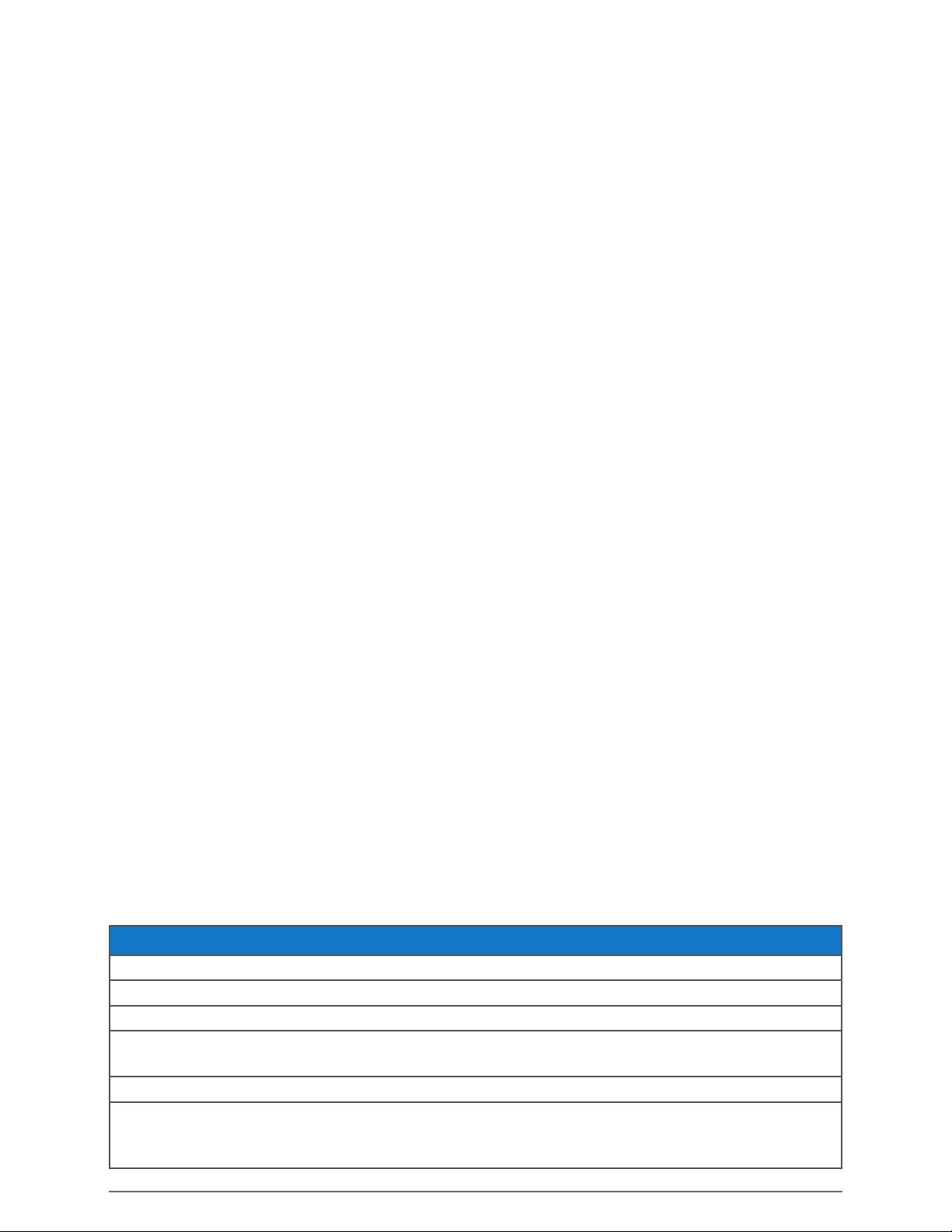
uninstalling, replacing the probe, shipment to a service center, calibration fees, return shipment to
the site and reinstallation. QCM analyzers require replacement of the desiccant and maintenance to
the internal sample system periodically. The recommended cycle for recalibrating Aluminum Oxide
sensors is 6 – 12 months, while TDLAS has no required factory service.
During “turnarounds” or process upsets, TDLAS technology has been proven to provide the fastest
response and recovery once the process upset is corrected or dissipates, and to run for years without
the need of any major maintenance or recalibration [4]. Key advantages of TDLAS include:
• Fast real-time measurement with no wet up or dry-down delays – responds to changes in H2O
concentration in the process gas in seconds
• Virtually maintenance free with no routine eld calibration and/or expensive consumable
requirements
• Non-contact continuous moisture measurement with no damage to critical sensor components
(tunable diode laser and detection optics) from HCl and other contaminants in the process by
sample conditioning to isolate them from the process gas
• Sample conditioning and reduced pressure high-resolution spectroscopy (Aurora Trace) can
minimize interference to moisture measurement from other compounds in the process gas
3. Aurora TDLAS platform
GE’s Aurora analyzer employs TDLAS to rapidly and accurately measure moisture content in a variety
of background gases including N2, H2, CO2, and hydrocarbons. This analyzer is suitable for installation
in hazardous areas and operates over a wide range of environmental conditions. We present below
key performance attributes of the Aurora moisture analyzer for use in online measurement of the H2
recycle stream in various types of downstream rening processes.
The Aurora H2O is the base model wherein a single-pass absorption cell operates at atmospheric
pressure to provide a lower detection limit of 5 PPMv. It uses a near-infrared diode laser rapidly tuned
over a narrow band of optical frequencies that includes the molecular absorption peak of H2O to
directly measure the partial pressure of water vapor in the background gas [5]. With the simultaneous
measurement of sample pressure and temperature, the Aurora generates the following moisture
content readings simultaneously at a rate of ~5 per second:
• Molar volume ratio in parts per million by volume (PPMv)
• Absolute humidity in pounds per million standard cubic feet (lbs/mmscf) or milligrams per cubic
meter (mg/m3)
• Saturation temperature of Dew point/Frost point in °C or °F
• Equivalent dew point at line pressure in °C or °F
Table 1: Detailed performance specications for Aurora TDLAS high-precision moisture analyzers
as relevant to the H2 recycle downstream applications.
PARAMETER AURORA H2O SPECIFICATION
RANGE
Calibrated range 0 to 5000 PPMv
Lower Detection Level 5 PPMv
Dew/Frost Point -85.9° to 27.3°F (-65.5° to –2.6°C) frost point @ STP of 25°C, 14.696
psia
ACCURACY
Parts Per Million by Volume ±2% of reading or 4 PPMv at nominal gas composition with up
to 5% variation in H2 and 1% variation in C2H6 from nominal gas
composition
Aurora TDLAS analyzers for Hydrogen Recycle Applications