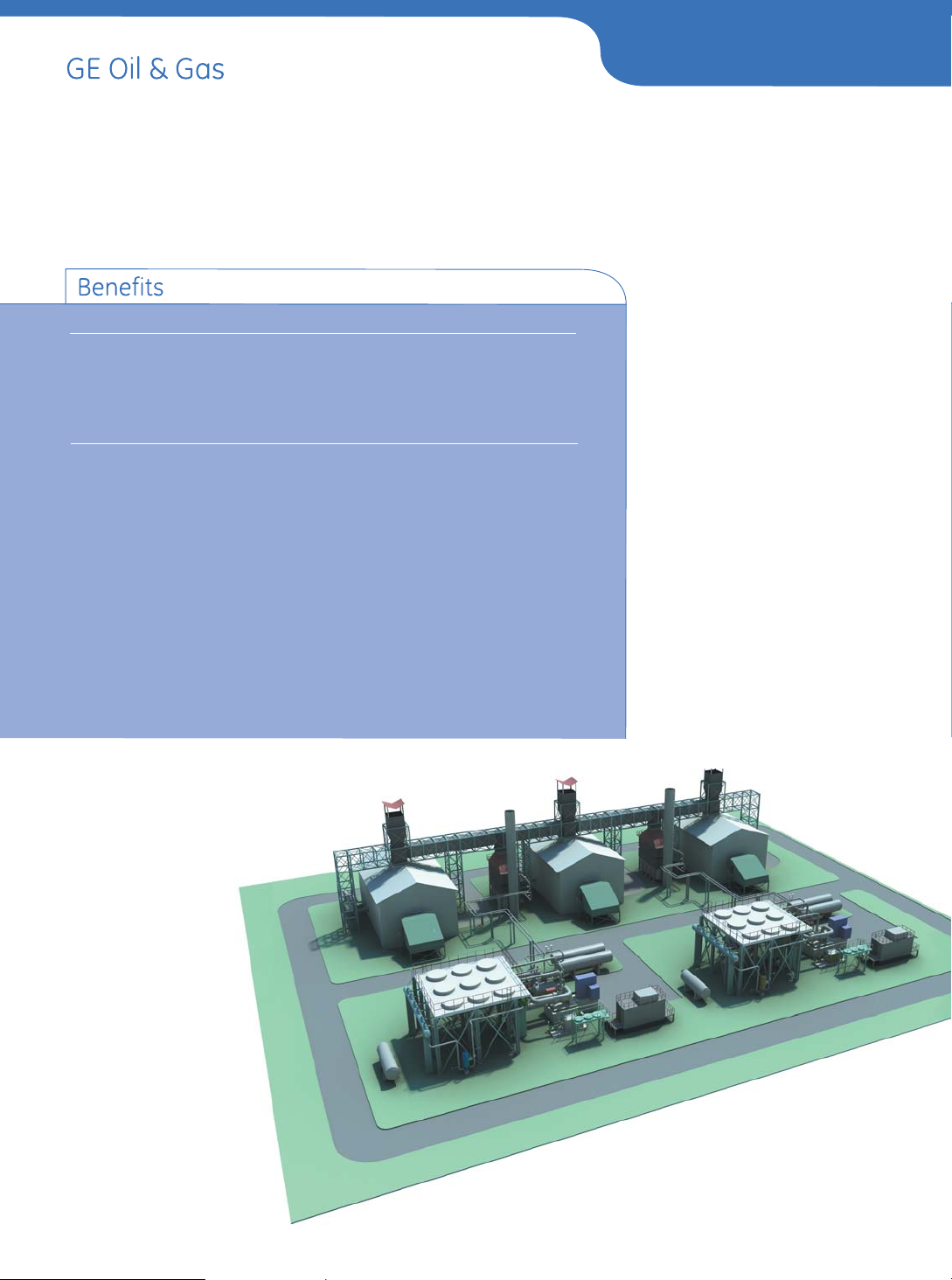
ORegen*
Waste Heat Recovery System
for GE and other OEM Gas Turbines
g g g
Increased production
g g g
Higher efficiency
g g g
Compliance with environmental regulations
c c c
Availability and Reliability
c c c
Life extension
Addressing environmental problems is becoming an important initiative
throughout the world. The reduction of CO
the path toward lowering the human contribution to climate change.
Many industrial processes generate waste energy that passes out of plant
stacks into the atmosphere and is lost.
Energy recovered from waste heat streams could supply part or all of the
electric power required by a plant, at no additional cost.
Therefore, heat recovery offers a great opportunity to conserve by
productively using this waste energy, to reduce overall plant energy
consumption and simultaneously decrease CO2emissions.
emissions is a key element in
2
Get more from your
Gas Turbines
* ORegen is a trademark of Nuovo Pignone S.p.A. and is available in select markets
a product of
ecomagination
SM
Layout of a plant equipped with the
ORegen waste heat recovery system
g
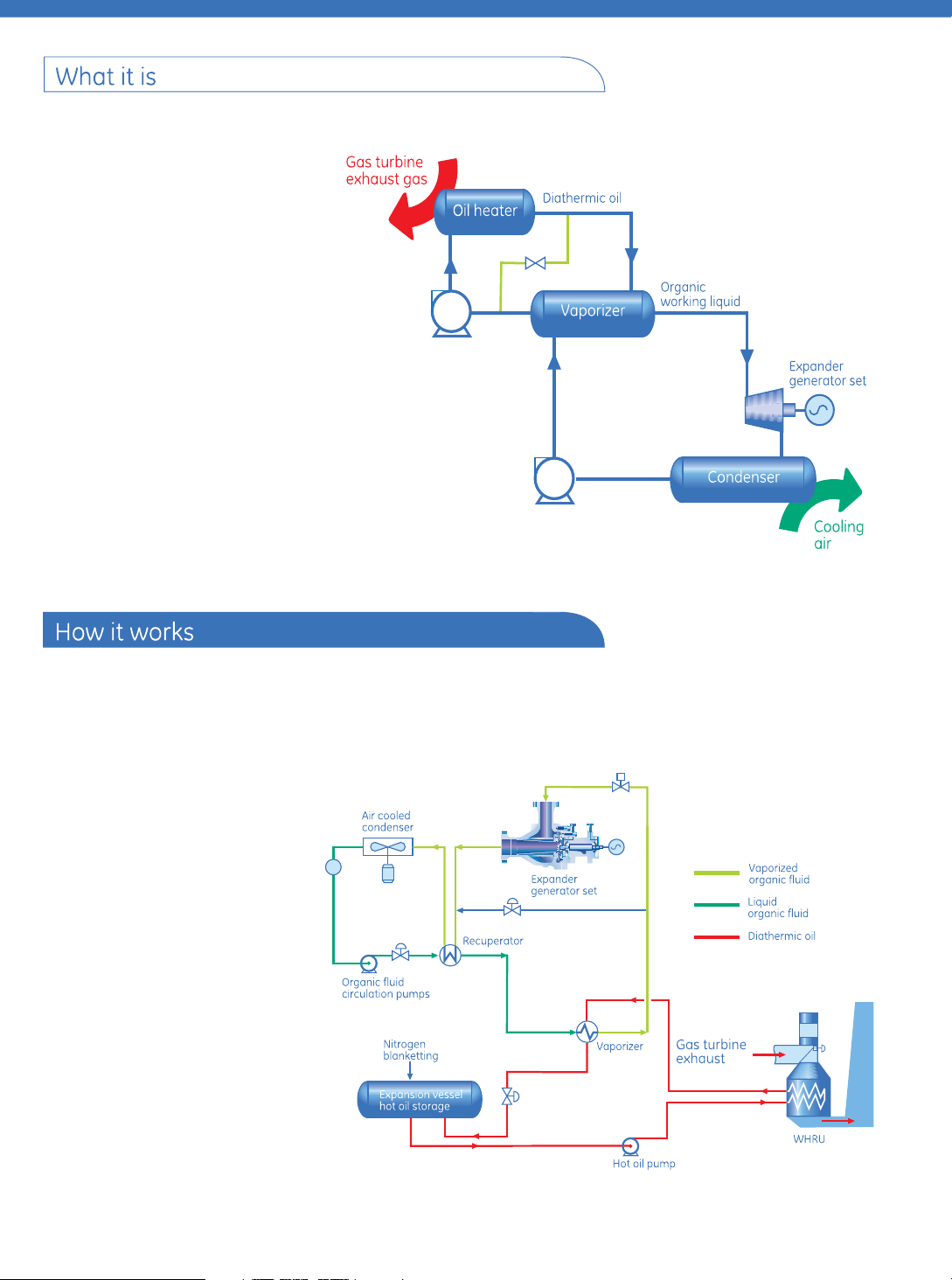
Power generation with zero additional
emissions
ORegen is a thermodynamic superheat
cycle that recovers waste heat from gas
turbine exhaust and converts it into
electric energy. The thermodynamic cycle
is based on an Organic Rankine Cycle
(ORC). Heat from the turbine exhaust is
transferred to a closed diathermic oil loop,
which is used to heat an organic fluid loop.
This lower temperature heat is then
converted into useful work that can
generate electricity. The ORC works with
a hydrocarbon fluid in place of water.
The system is similar to a conventional
steam bottoming cycle except for the
organic fluid that drives a turboexpander
that in turn drives the generator. The
diathermic oil and the organic fluid allow
low temperature heat sources to be
exploited efficiently to produce electricity
over a wide range of power output, from
a few MW up to 16 MW per unit.
Closed loop system
The organic working fluid is vaporized
and pressurized in the evaporator by
the application of heat taken from the
gas turbine exhaust stream. Then, the
vapor expands in the turboexpander
and is condensed using air-cooled
heat exchangers at ambient
conditions. The condensate is pumped
back to the evaporator, thus closing
the thermodynamic cycle. The
heating and cooling sources are not in
direct contact with the working fluid,
nor with the expander. For higher
temperature applications, a high
temperature thermal oil is used as
the heat carrier and a regenerator is
added to further improve the cycle
performance.
The selection of the working fluid is
key in a Rankine Cycle.
The features are:
• Low freezing point and high
temperature stability
• High heat of vaporization and
density
• Low environmental impact
• No additional EHS considerations
• Readily available at low cost

ORegen vs Steam Cycle
Features
ORegen Standard Steam
Combined Cycle
Water free *** *
Low maintenance *** *
Power flexibility *** *
Low investment ** *
Plant simplicity *** *
Reduced footprint *** *
No replenishment of working fluid *** *
Unmanned capability *** *
Additional output ** ***
Expected ORegen Power Output
for Mechanical Drive and Power Generation Gas Turbines
Gas Gas Turbine Exhaust Exhaust Gas Turbine ORegen Gross System
Turbine Power Flow Temp Efficiency Output Efficiency
Model (KW) (Kg/sec) (°C) (%) (MWe) (%)
PGT25 (*) 23,261 68.9 525 37.7 6.9 48.9
PGT25+ (*) 31,364 84.3 500 41.1 7.9 51.5
PGT25+ G4 (*) 33,973 89.0 510 41.1 8.6 51.5
MS5001 (*) 26,830 125.2 483 28.4 11.3 40.4
MS5002C (*) 28,340 124.3 517 28.8 12.4 41.4
MS5002D (*) 32,580 141.4 509 29.4 13.8 41.9
MS6001B (*) 43,530 145.0 544 33.3 15.6 45.2
LM6000 (**) 43,397 125.6 454 41.7 9.7 51.1
Reference data @ISO Conditions, 100% GT Turbine load, one to one configuration
(*) Values at gas turbine shaft
(**) Values at generator terminals for LM6000PC coupled to 60 Hz generator
Scope of Supply
The basic scope of supply includes the following:
• Organic fluid system
• Diathermic oil system
• Boilers and heat exchangers
• Turboexpander genset
• Piping and BOP components
• Air or water cooler
Waste Heat Recovery Unit
Organic Fluid System

g
GE imagination at work
GE Oil & Gas
Global Headquarters
Via Felice Matteucci, 2
50127 Florence, Italy
T +39 055 423 211
F +39 055 423 2800
Nuovo Pignone S.p.A.
Nuovo Pignone S.r.l.
E customer.service.center@ge.com
www.ge.com/oilandgas
GE, the GE Monogram,
and imagination at work
are registered trademarks of
the General Electric Company.
COMK/MARK 839/II - Designed by: Studio Tre Fasi
Printed by: Sagraf - 12-2011
©2011 General Electric Company
All Rights Reserved