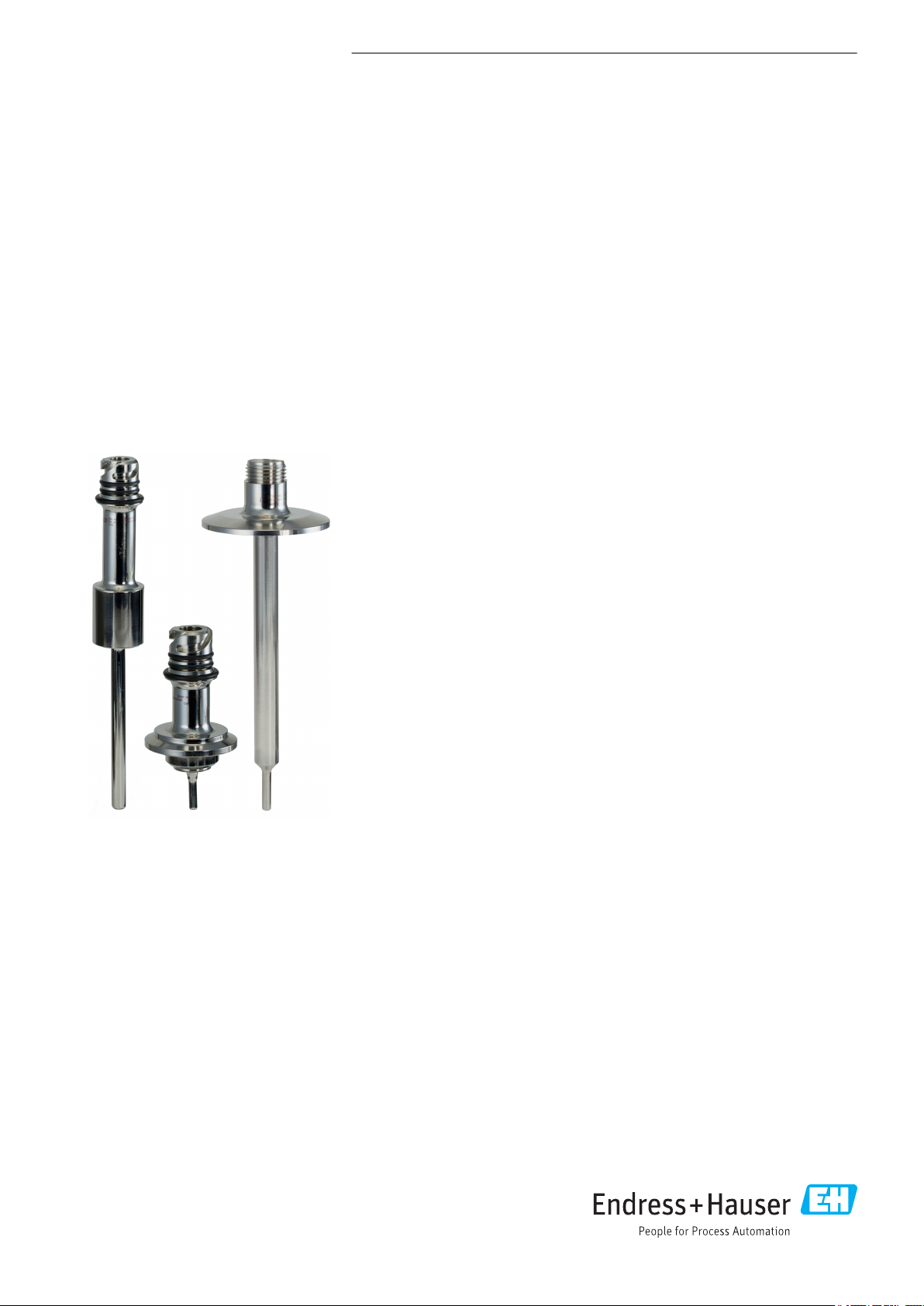
TI01350T/09/EN/02.18
71418574
2018-11-05
Products Solutions Services
Technical Information
iTHERM TT412
Thermometer protection tube for hygienic and
aseptic applications
Applications
• Specially designed for use in hygienic and aseptic applications in the
Food & Beverages and Life Sciences industries
• Pressure range up to 40 bar (580 psi)
• For increased protection requirements of the temperature sensor regarding
physical and chemical effects
• For use in pipes and containers or tanks
• Ideally suited to all measuring points that require regular recalibration by simply
replacing the insert in closed processes
Your benefits
• iTHERM QuickNeck – cost and time savings thanks to simple, tool-free
recalibration of the insert used
• All common hygienic process connections
• International certification: 3-A Sanitary Standard, EHEDG, ASME BPE, FDA, TSE
Certificate of Suitability
• Fast response time owing to reduced tips with thin walls
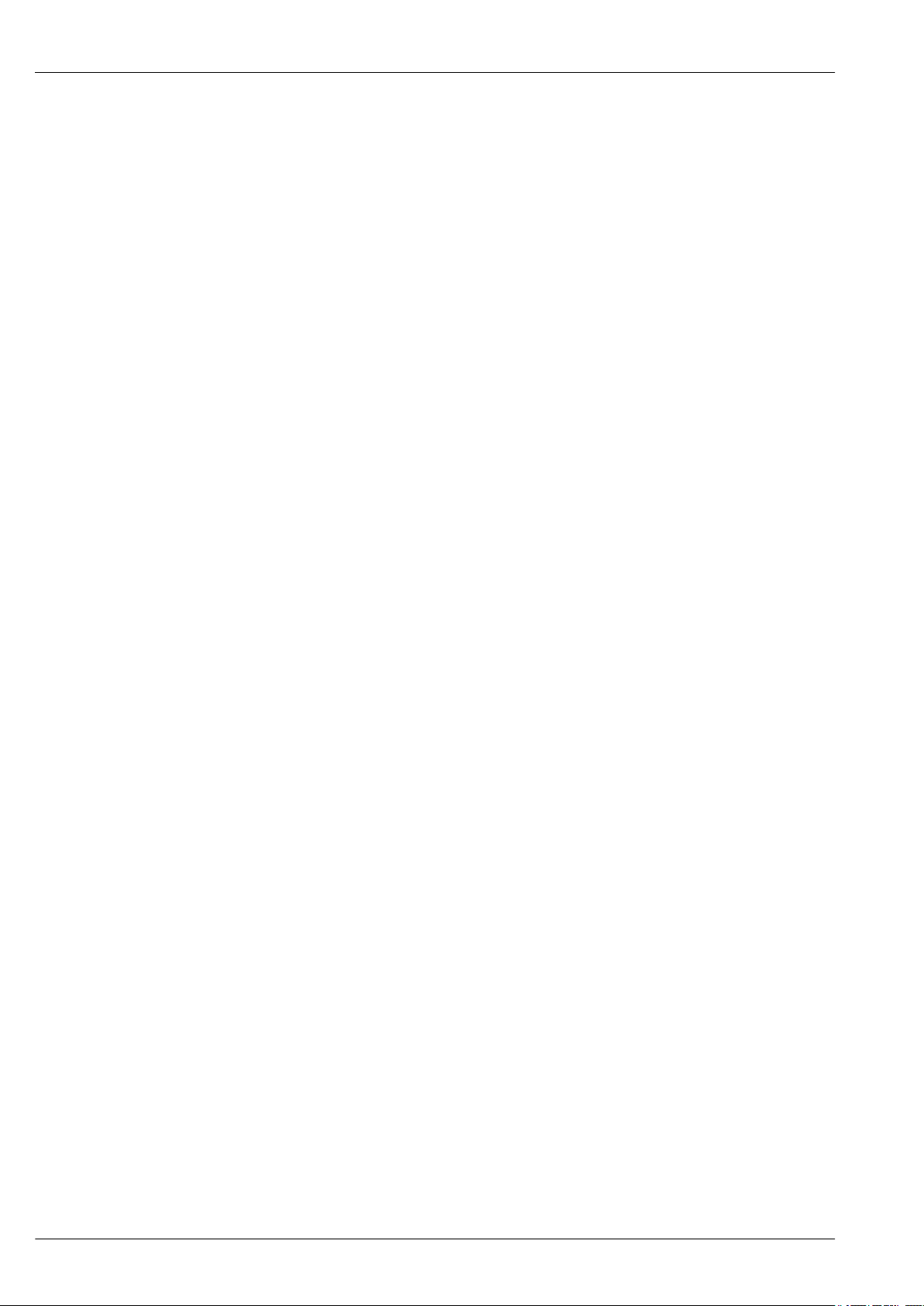
Table of contents
Installation ................................ 3
Orientation ................................. 3
Installation instructions ......................... 3
Process ................................... 5
Process temperature range ....................... 5
Thermal shock ............................... 5
Process pressure range .......................... 5
Medium - state of aggregation ..................... 5
Mechanical construction ...................... 6
Design, dimensions ............................ 6
Weight .................................... 7
Material ................................... 7
Surface roughness ............................. 7
Process connections ............................ 8
Tip shape .................................. 10
iTHERM TT412
Certificates and approvals ................... 11
CE mark ................................... 11
Hygiene standard ............................ 11
Other standards and guidelines ................... 11
Parts in contact with the medium .................. 11
CRN approval ............................... 11
Surface purity ............................... 11
Material resistance ........................... 11
Material certification .......................... 11
Protection tube testing and load capacity calculation ..... 11
Ordering information ....................... 12
Accessories ............................... 13
Device-specific accessories ...................... 13
Service-specific accessories ...................... 14
Documentation ............................ 14
2 Endress+Hauser
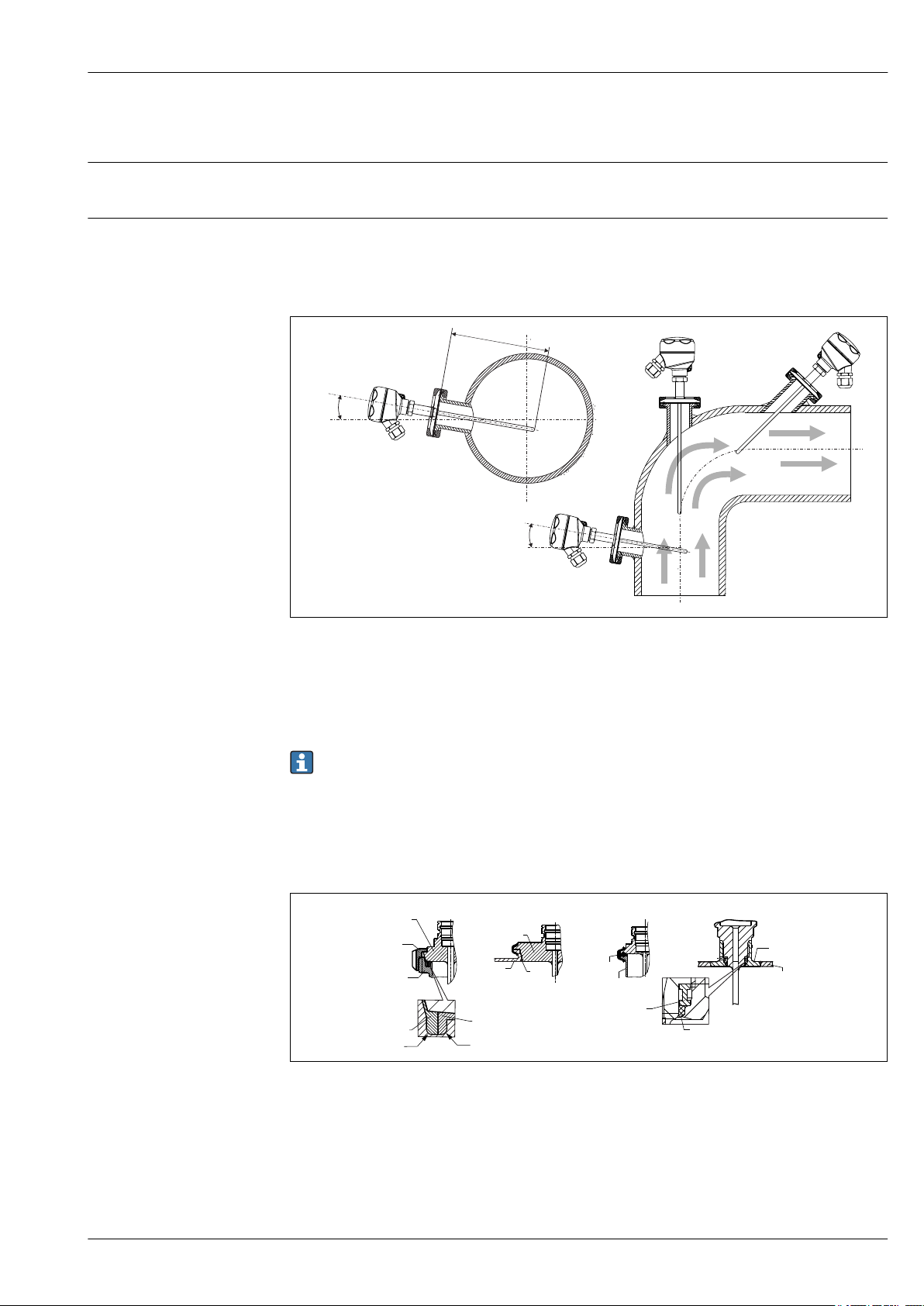
iTHERM TT412
1 2
3
4
R0.4
R0.4
Pressure ring
Sensor with
milk pipe
connection
Sensor with Varivent
connection
Shaped
gasket
Companion
connection
O-ring
Groove
slip-on nut
Centering ring
Sealing
Companion
connection
Companion
connection
O-ring
Welding boss
Vessel wall
Installation
Orientation
Installation instructions
No restrictions. However, self-draining in the process must be guaranteed. If there is an opening to
detect leaks at the process connection, this opening must be at the lowest possible point.
The immersion length of the thermometer can influence the accuracy. If the immersion length is too
small then errors in the measurement are caused by heat conduction via the process connection. If
installing into a pipe then the immersion length should ideally be half of the pipe diameter.
Installation possibilities: Pipes, tanks or other plant components
A0008946
1 Installation examples
1, 2 Perpendicular to flow direction, installed at a minimum angle of 3° to ensure self-draining
3 On elbows
4 Inclined installation in pipes with a small nominal diameter
U Immersion length
Endress+Hauser 3
In the case of pipes with a small nominal diameter, it is advisable for the tip of the thermometer
to project well into the process so that it extends past the pipe axis. Installation at an angle (4)
could be another solution. When determining the immersion length or installation depth all the
parameters of the thermometer and of the medium to be measured must be taken into account
(e.g. flow velocity, process pressure).
The use of iTHERM QuickSens inserts is recommended for immersion lengths U <
70 mm (2.75 in).
2 Detailed installation instructions for hygiene-compliant installation
1 Sanitary connection according to DIN 11851, only in connection with EHEDG-certified and self-centering
sealing ring
2
Varivent® process connection for VARINLINE® housing
3 Clamp according to ISO 2852, only in connection with seal according to EHEDG position paper
4 Liquiphant-M G1" process connection
A0011758-EN
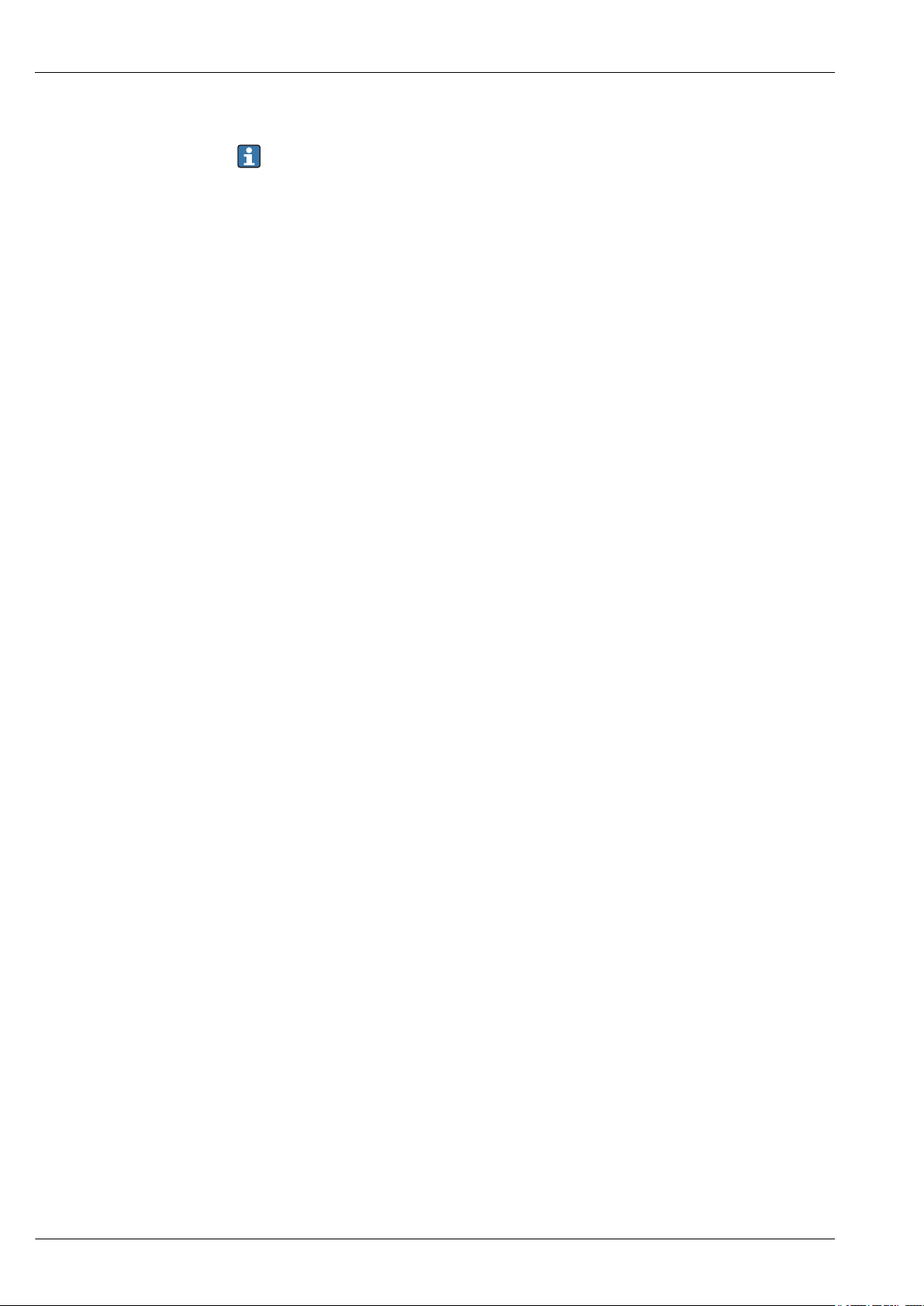
iTHERM TT412
The counterpieces for the process connections and the seals or sealing rings are not included in
the scope of supply for the thermometer. Liquiphant M weld-in adapters with associated seal
kits are available as accessories.
Procedure in case of seal failure:
• Disassembling of the thermometer, validated cleaning procedure of thread and sealing ring
groove
• Replacement of the seal or sealing ring
• CIP after re-assembly
In the case of weld-in connections, exercise the necessary degree of care when performing the
welding work on the process side:
• Suitable welding material
• Flush-welded or with welding radius > 3.2 mm (0.13 in)
• No recesses, folds or gaps
• Honed and polished surface, Ra ≤ 0.76 µm (30 µin)
4 Endress+Hauser
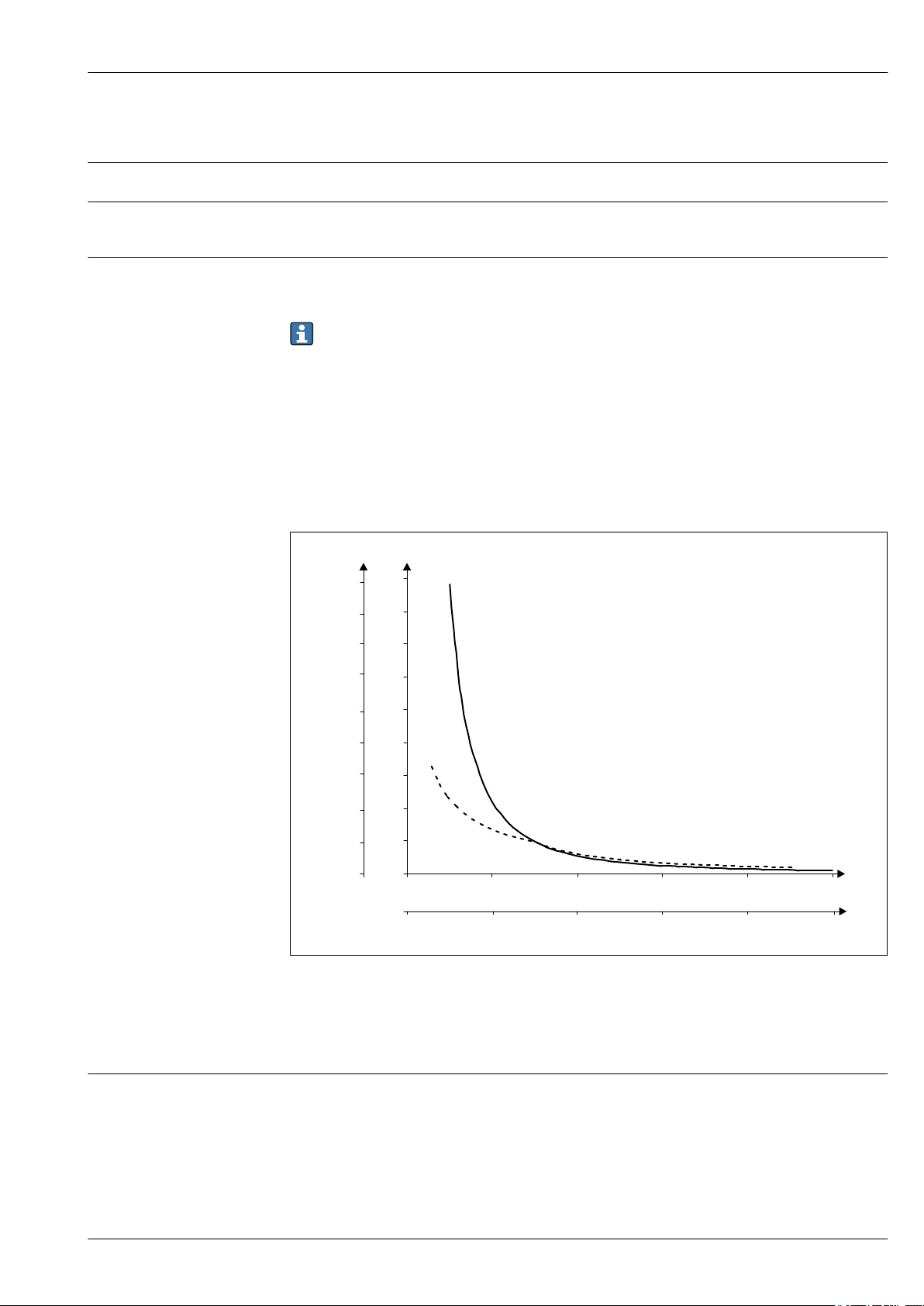
iTHERM TT412
L (mm)
A
0
10
20
30
40
50
60
70
80
90
100 200 300 400 500
v (m/s)
B
0
4 8 12 16 20
L (in)
0
30
65
100
130
160
200
230
260
290
v (ft/s)
Process
Process temperature range
Thermal shock
Process pressure range
Maximum –200 to +650 °C (–328 to +1 202 °F)→ 7
Thermal shock resistance in CIP/SIP process with a temperature increase from
+5 to +130 °C (+41 to +266 °F) within 2 seconds.
The maximum possible process pressure depends on various influencing factors, such as the design,
process connection and process temperature. For information on the maximum possible process
pressures for the individual process connections, see the 'Process connection' section. → 8
It is possible to check the mechanical loading capacity as a function of the installation and
process conditions online in the Thermowell (TW) Sizing Module for protection tubes in the
Endress+Hauser Applicator software. See 'Accessories' section.
Example of the permitted flow velocity depending on the immersion length and process
medium
The highest flow velocity tolerated by the protection tube diminishes with increasing insert
immersion length exposed to the stream of the fluid. In addition, it is dependent on the diameter of
the tip of the protection tube, the medium type, process temperature and process pressure. The
following figures exemplify the maximum permitted flow velocities in water and superheated steam
at a process pressure of 40 bar (580 PSI).
3 Permitted flow velocities, protection tube diameter 9.53 mm (3/8 in)
A Medium water at T = 50 °C (122 °F)
B Medium superheated steam at T = 400 °C (752 °F)
L Immersion length exposed to flow
v Flow velocity
Medium - state of
aggregation
Gaseous or liquid (also with high viscosity, e.g. yogurt).
Endress+Hauser 5
A0008967