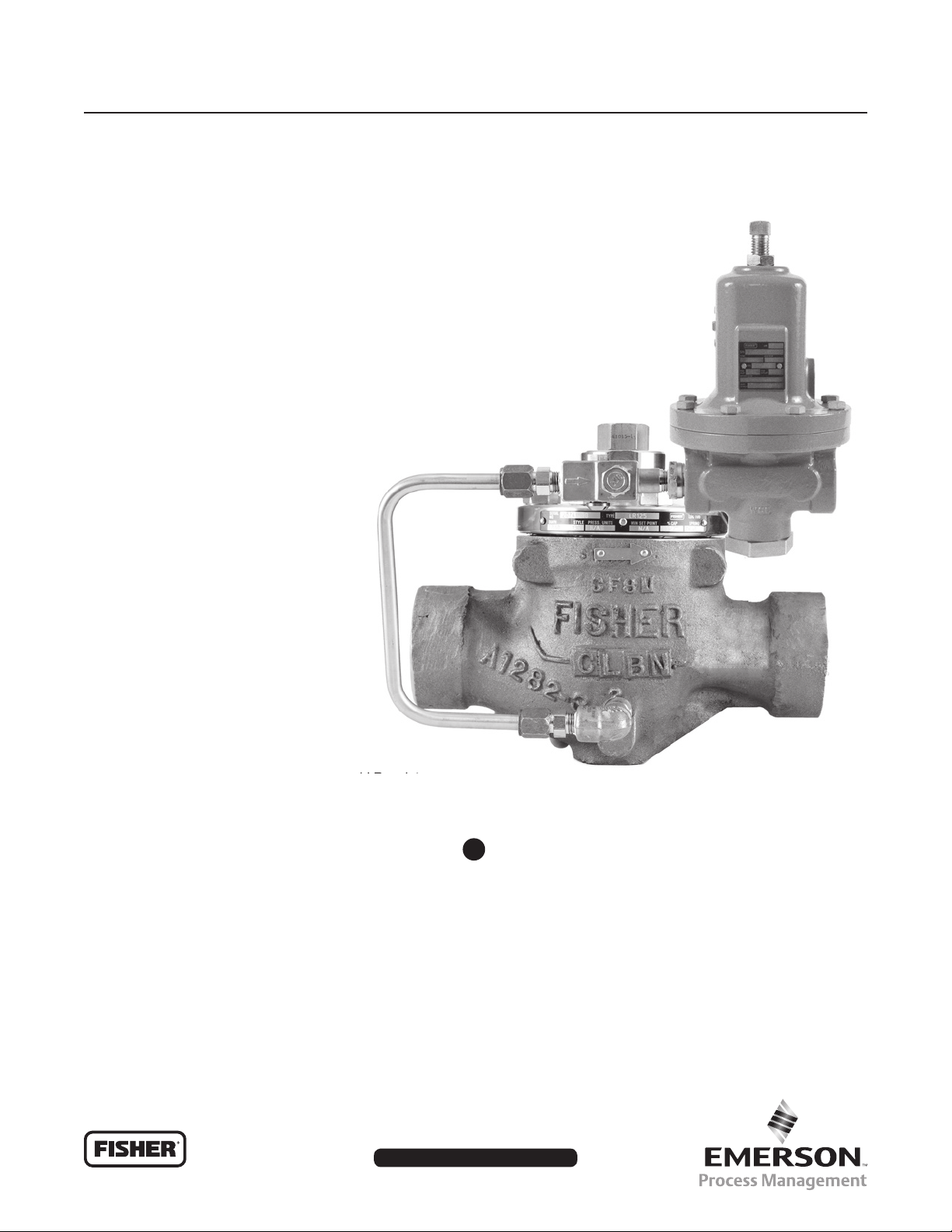
Bulletin 71.2:LR125
November 2014
Type LR125 Pressure Reducing Liquid Regulator
• Rugged design
• Reliable
• Thoroughly tested
• Internally actuated
• Compact
• 1, 2, 3, 4 in. body sizes
• Recommended for water
and oil applications
• Full SST construction
available for harsh
environments
• API 614 Compliant
Figure 1. Type LR125 Pressure Reducing Liquid Regulator
Introduction
The Type LR125 pilot-operated, pressure reducing
regulator is designed for liquid industrial/commercial
applications. The Type LR125 provides smooth
operation, tight shutoff and long life. Its internally
actuated metal plug eliminates disadvantages
associated with exible element style regulators, and
the specially engineered ow path de ects debris,
protecting the seat from damage and erosion. The
Type LR125 is used in conjunction with a Type MR95H
pilot and Type 112 restrictor. An internal inlet strainer
prevents large particles from entering the main valve,
limiting damage to internal parts.
Features and Bene ts
1
Tight Shutoff—The Type LR125 uses a diaphragm
and metal plug, eliminating the disadvantages of
exible element style regulators. When open, the
metal plug de ects particles and debris away from
the diaphragm. The result is enhanced resistance to
particle erosion, which provides excellent shutoff over
an extended life. When closed, loading pressure and
the main spring push the diaphragm onto the taperededged seat on the cage.
www.fisherregulators.com
D103575X012
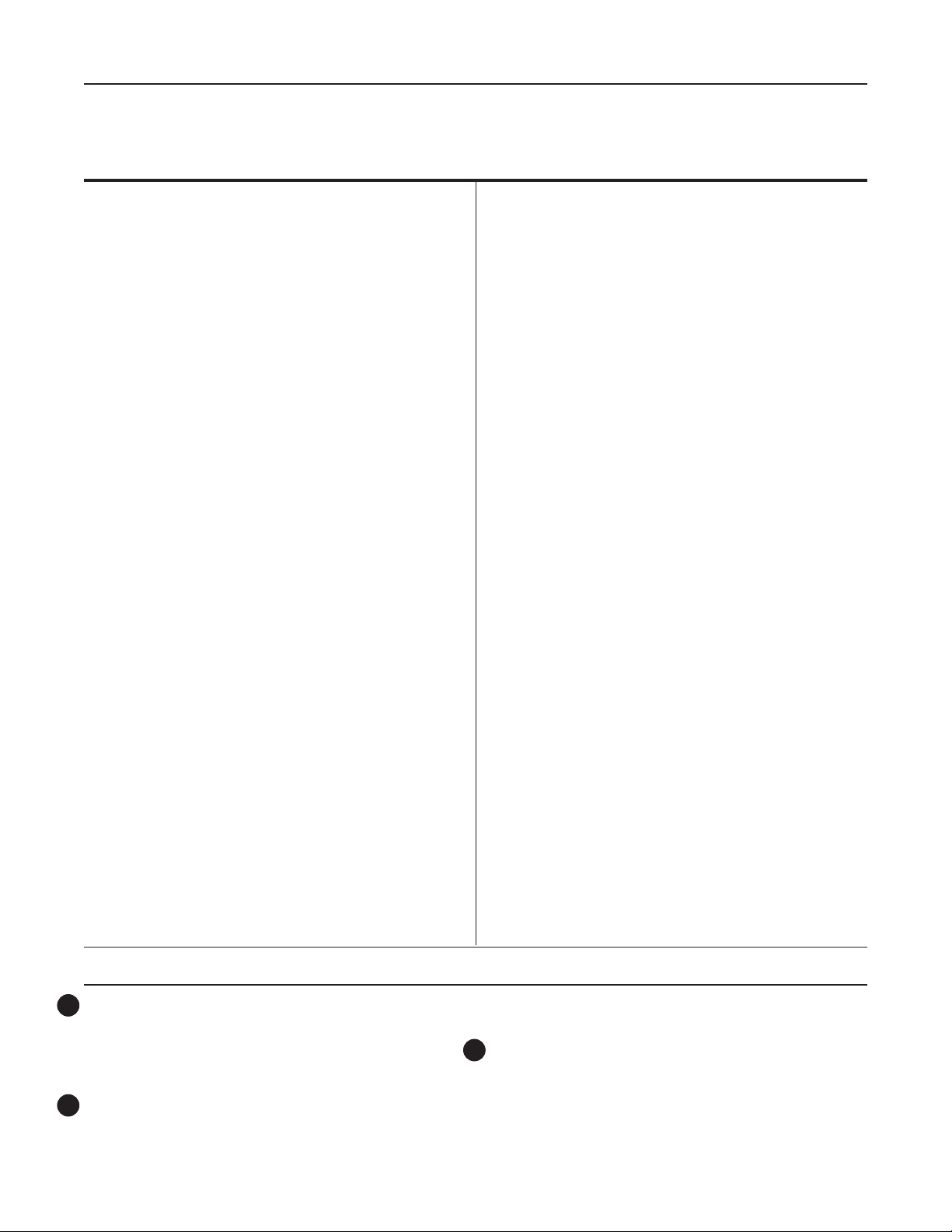
Bulletin 71.2:LR125
Specications
The Specications section lists the specications for the Type LR125 regulator. Factory specication is stamped
on the nameplate fastened on the regulator at the factory.
Main Valve Body Sizes, End Connection Styles and
Structural Design Ratings
(1)(2)
See Table 1
Maximum Inlet Pressures
(1)
Type LR125 Main Valve: See Table 1
Type MR95H Pilot: See Table 2
Type 112 Restrictor: 1500 psig / 103 bar
Maximum Outlet Pressure
Type LR125 Main Valve: See Table 1
Type MR95H Pilot: See Table 2
Outlet (Control) Pressure Ranges
See Table 3
Main Valve Plug Travel
1 in. / DN 25: 0.37 in. / 9.4 mm
2 in. / DN 50: 0.68 in. / 17 mm
3 in. / DN 80: 0.98 in. / 25 mm
4 in. / DN 100: 1.19 in. / 30 mm
Main Valve Minimum Differential Pressures
(1)
See Table 5
Temperature Capabilities
(1)
See Table 4
Main Valve Flow Direction
Up through the center of the cage and down
through the cage slots
Main Valve Internal Inlet Strainer Sizes
1 in. / DN 25: 12 Mesh (0.0661 in. / 1.68 mm)
(3)
2, 3 and 4 in. / DN 50, 80 and 100:
10 Mesh (0.0787 in. / 2 mm)
(3)
Regulating Capacities
See Table 11
Flow and IEC Sizing Coefcients
Type LR125 Main Valve: See Table 6
Type MR95H Pilot: See Table 7
Type 112 Restrictor: See Table 8
Pressure Registration
External: 1/2 NPT
Spring Case Vent
Type Y602-12
Approximate Weights
Options
• Pre-piped Pilot Supply
• Travel Indicator
Construction Materials
Type LR125 Main Valve
Body: WCC Steel, CF8M or CF3M Stainless Steel
Bonnet: Steel or Stainless Steel
Bonnet Bushing: Steel or Stainless Steel
Cage: Stainless steel
Spring: Stainless steel
Top Plug: Stainless steel
Bottom Plug: Stainless steel
Internal Inlet Strainer: Stainless steel
Diaphragm: Nitrile (NBR) or Fluorocarbon (FKM)
O-rings: Nitrile (NBR) or Fluorocarbon (FKM)
Flanged Locknut: Stainless Steel
Backup Rings: Polytetrauoroethylene (PTFE)
Upper Spring Seat: Stainless steel
Indicator Protector and Cover: Plastic
Indicator Stem: Stainless steel
Indicator Fitting: Stainless steel
Travel Indicator Plug: Stainless steel
Type MR95H Pilot
Body: WCC Steel or CF8M Stainless Steel
Spring Case: WCC Steel or CF8M Stainless Steel
Orice: Stainless Steel
Diaphragm: Neoprene (CR) or Fluorocarbon (FKM)
Disk: Nitrile (NBR) or Fluorocarbon (FKM)
Mounting Parts
Pilot Mounting Pipe Nipple: Plated steel or
Stainless steel
Pipe Fittings: Plated steel or Stainless steel
Tubing: Stainless Steel
Type 112 Restrictor
Body: 15-5 Stainless Steel
Groove Valve: Stainless steel
Retainer: Stainless steel
Pipe Plug: Stainless steel
O-rings: Nitrile (NBR) or Fluorocarbon (FKM)
See Table 9
1. The pressure/temperature limits in this Bulletin and any applicable standard or code limitation should not be exceeded.
2. Ratings and end connections other than ASME standards can usually be provided; contact your local Sales Ofce.
3. Nominal sieve opening
2
Debris Protection—The specially engineered ow
path, along with the metal plug, allows ow through the
regulator without seat impingement. The addition of an
internal inlet strainer prevents large particles from entering
the regulator, minimizing damage to internal parts.
3
High Accuracy—Multiple control pressure ranges
offered by Type MR95H pilot and lower accuracy class
2
inherent to pilot operated pressure regulator design
provide the Type LR125 with tight and accurate control.
Long Life—The robust design of the Type LR125 with
4
its metal plug and specially engineered ow path allows
ow through the regulator without seat impingement.
The diaphragm design eliminates the possibility of
taking a “set”, a common problem with exible element
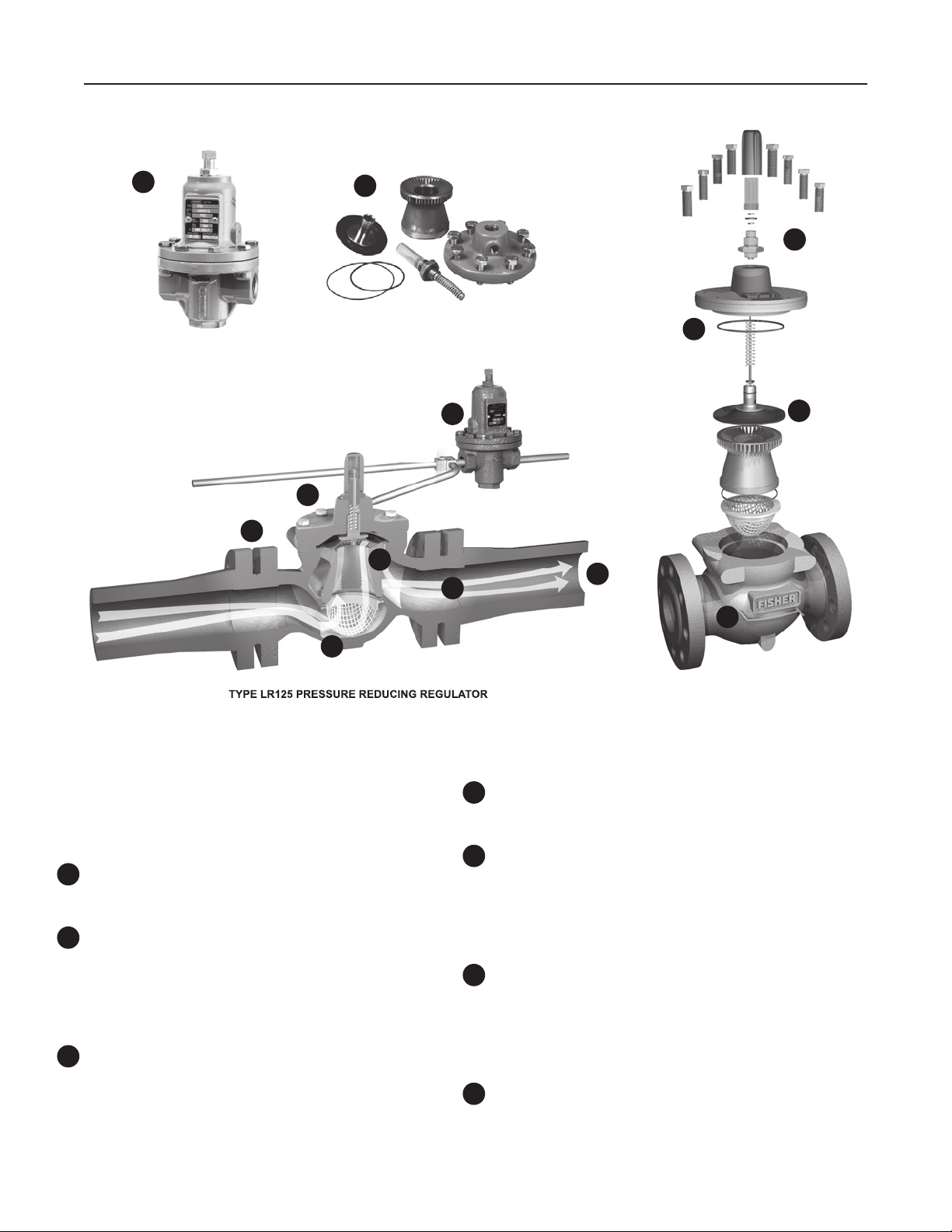
Bulletin 71.2:LR125
TYPE LR125 PRESSURE REDUCING REGULATOR
3
W5092
TYPE MR95H PILOT
10
7
7
W7398
TRIM PACKAGE
11
9
1
TYPE MR95H PILOT
5
6
8
4
12
2
W7344
TYPE LR125 PRESSURE REDUCING REGULATOR
Figure 2. Type LR125 Features and Bene ts
style regulators. To prevent damage, the diaphragm is
fully supported in both the open and closed positions.
These features enable the Type LR125 components to
work longer with less wear and tear.
5
Full Usable Capacity—Fisher® branded regulators
are laboratory tested. One hundred percent of the
published ow capacity can be used with con dence.
Thorough Laboratory Testing—Emerson Process
6
Management Regulator Technologies, Inc. (Emerson™)
state-of-the-art ow laboratory allows thorough testing of
all new designs. Tests are conducted on Fisher branded
regulators for performance features such as ow,
strength, shutoff and material compatibility.
7
Easy In-Line Maintenance—Top-entry design
reduces maintenance time. Trim parts can be
inspected, cleaned and replaced without removing
the body from the pipeline. No special alignment is
required when replacing the diaphragm.
W7345
8
O-ring Design—The Type LR125 uses elastomer
O-rings instead of gaskets, reducing maintenance and
assembly time.
9
In-Service Travel Indicator—The optional travel
indicator responds to the precise movement of the
diaphragm and plug assembly and shows the actual
valve position. The travel indicator makes in-service
inspection and troubleshooting easy. Also, it can be used
for remote alarming and monitoring stem position.
Versatility—The Type LR125 uses the E-body, making
10
available the standard construction materials and end
connections (ASME and EN) used by other E-body
regulators and control valves. Type MR95H can handle
inlet pressures up to 300 psig / 20.7 bar and outlet
pressures from 15 to 150 psig / 1.0 to 10.3 bar.
11
Easy-to-Maintain—The pilot is designed to allow quick
and simple in-line trim inspection and parts replacement.
3
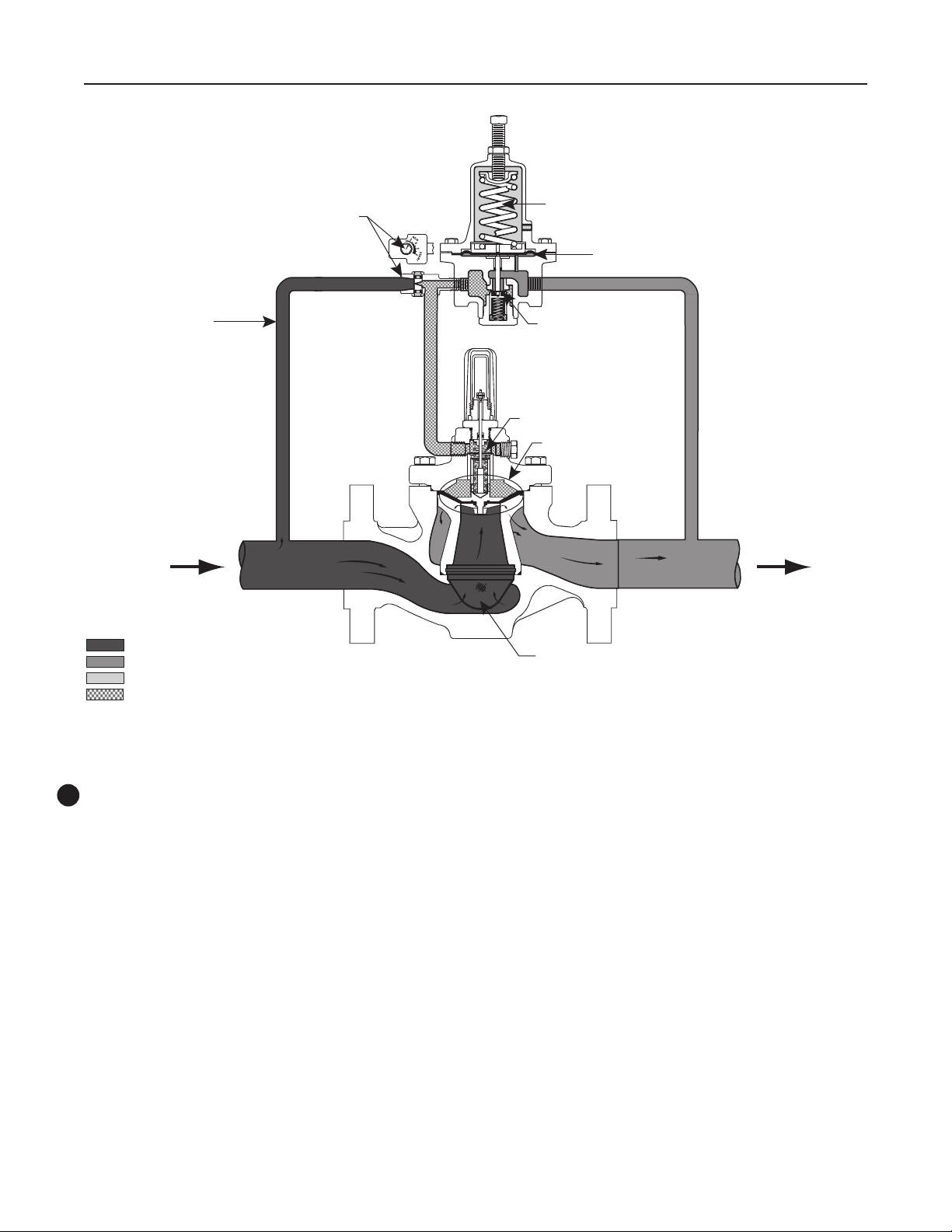
Bulletin 71.2:LR125
TYPE MR95H PILOT
SUPPLY LINE
M1215
INLET PRESSURE
OUTLET PRESSURE
ATMOSPHERIC PRESSURE
LOADING PRESSURE
TYPE 112 RESTRICTOR
CONTROL SPRING
VALVE PLUG
MAIN SPRING
DIAPHRAGM AND
PLUG ASSEMBLY
INTERNAL STRAINER
DIAPHRAGM
TYPE LR125 WITH TYPE MR95H PILOT AND TYPE 112 RESTRICTOR
Figure 3. Type LR125 Operational Schematic
Powder Paint Coating—Carbon steel body is powder
12
paint coated providing superior impact, abrasion and
corrosion resistance.
Pilot Type Description
Type MR95H—High-pressure pressure reducing pilot
for 15 to 150 psig / 1.0 to 10.3 bar outlet pressures.
Designed to handle inlet pressures up to 300 psig /
20.7 bar.
Principle of Operation
As long as the outlet (control) pressure is above the
outlet pressure setting, the pilot valve plug or disk
remains closed (Figure 3). Force from the main spring, in
addition to inlet pressure bleeding through the restrictor,
provide downward loading pressure to keep the main
valve diaphragm and plug assembly tightly shutoff.
When the outlet pressure decreases below the pilot
outlet pressure setting, the pilot plug or disk assembly
opens. Loading pressure bleeds downstream through
the pilot faster than it can be replaced through the
supply line. This reduces loading pressure on top of
the main valve diaphragm and plug assembly and
lets the unbalanced force between inlet and loading
pressure overcome the main spring force to open the
Type LR125 diaphragm and plug assembly.
As the outlet pressure rises toward the outlet pressure
setting, it compresses the pilot diaphragm against
the pilot control spring and lets the pilot valve plug
or disk close. Loading pressure begins to build up
on the Type LR125 diaphragm and plug assembly.
The loading pressure, along with force from the main
spring, pushes the diaphragm and plug assembly onto
the tapered-edge seat, producing tight shutoff.
4