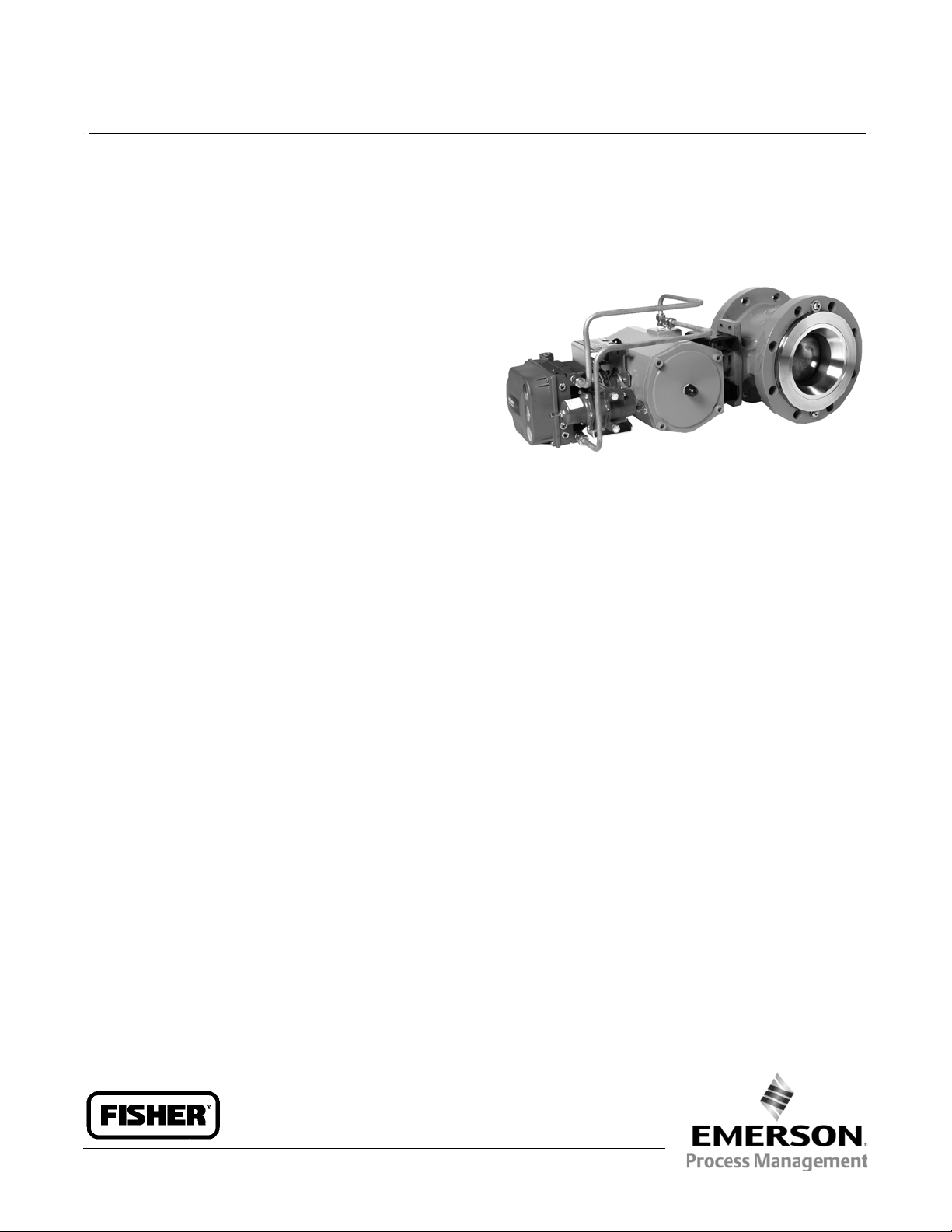
Slurry Vee-Ball Valve
D103154X012
Fisherr V150S
Slurry Vee-Ball™ Control Valve
The Fisher V150S Slurry Vee-Ball valve mates with
CL150 raised face flanges. Rugged construction, highly
wear-resistant trim materials, and an unrestricted
straight through flow path make the design ideal for
controlling the most abrasive of slurries.
A shaft with a choice of drive connections will allow a
variety of power operated actuators and valve
positioners or controllers to be used.
W8512
The design is particularly effective in minimizing
erosive damage to the adjoining pipework, thereby
providing greater operational safety and service life
when compared with other valve types.
Features
Fully protective trim–The valve body, shaft, and
bearings are fully protected by hard wear-resistant
trim materials.
Pipeline and flange protection–The throttled flow
stream is guided through a specially shaped flow
ring to minimize turbulence and impingement on
thepipewall.Thevalvecanbematchedtothebore
size of the inlet and outlet piping in order to prevent
turbulence being generated by the step resulting in
scouring erosion of the flange faces, unexpected
leakage, and expensive rework. In addition, both
the inlet and outlet valve flange faces are protected
by a portion of the hard trim.
Fisher V150S Slurry Vee-Ball Control Valve
Long Service Life–The Vee-Ball design, when used in
reverse flow mode, keeps the high velocity down
stream of the vena contracta within the flow ring
bore at the outlet of the valve. Compared with other
styles of valves, the exit flow is essentially parallel
with the flow ring wall and a minimum of flow
impingement occurs. Combined with a choice of
hard wear-resistant materials, a significantly long
life is obtained.
Easily replaceable trim parts allow the valve to be
overhauled at predetermined intervals and the
valve body used again during repeated operational
cycles.
Ease of installation–Full flanging on the valve body
allows the valve body to be easily aligned c entrally
with the pipe flanges, an essential requirement in
avoiding erosion across the flange faces.
Excellent Flow Control–Precise contouring of the
V-notch ball provides a modified equal percentage
flow characteristic. When combined with a valve
actuator/controller system having minimal lost
motion, improved process control can be obtained.
Product Bulletin
51.3:V150S
February 2013
(continued on page 2)
www.Fisher.com
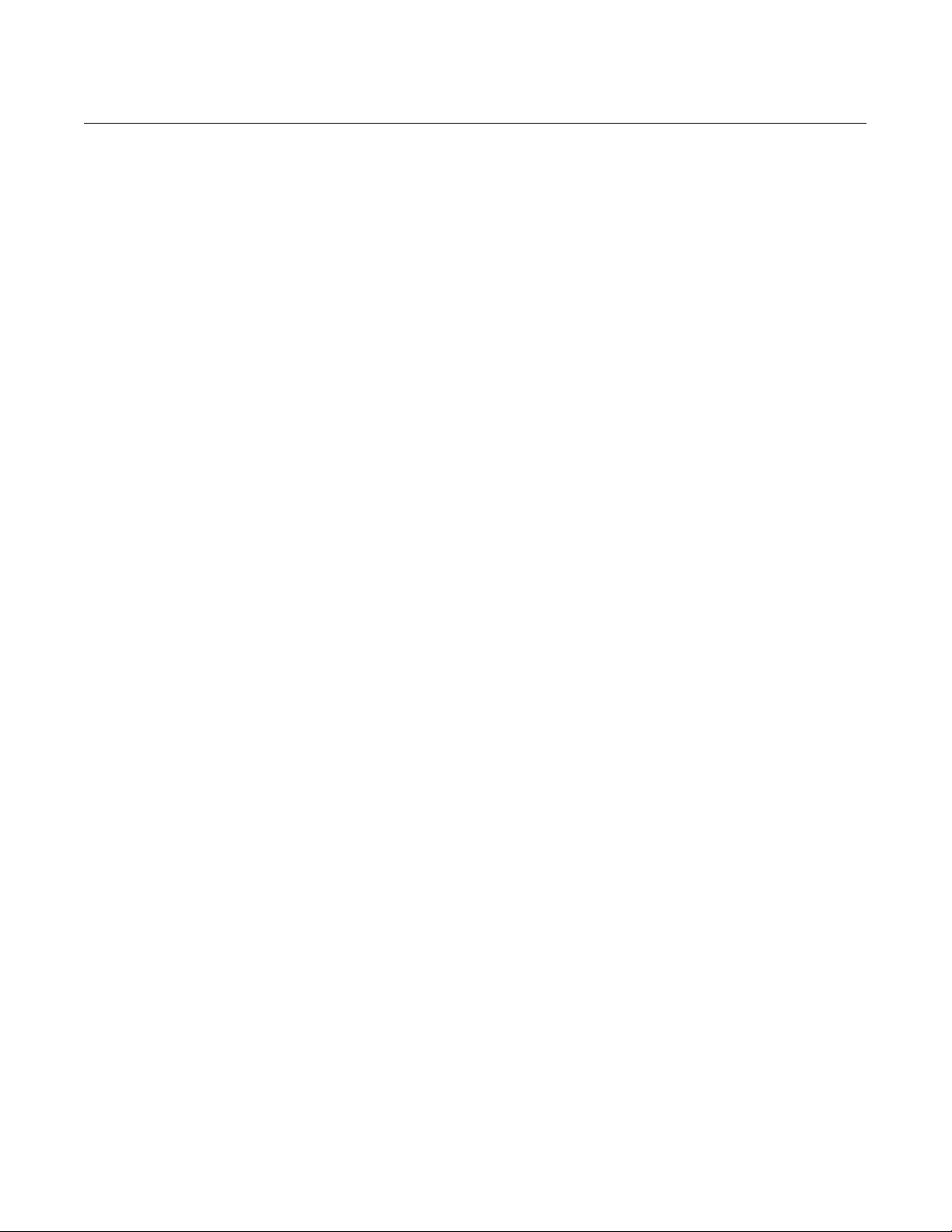
Product Bulletin
51.3:V150S
February 2013
Slurry Vee-Ball Valve
D103154X012
Features (continued)
Quick and Easy Maintenance–All trim parts are
retained without the use of press fits or screw
threads exposed to the process fluid. See figure 1.
Structural Integrity–The valve body, complete with
flanges, is made from a one-piece casting. No
welding is employed. No O-ring seals are used. Use
of a flanged valve body does not require the use of
extra long studs.
The shaft seal is made from well-proven PTFE
chevron ring packing with the means for external
adjustment.
Options
A PSZ (partially stabilized zirconia) ceramic flow ring
insert is available with HCI (high chrome iron) or PSZ
ceramic ball for particularly aggressive slurry
services with extended lifetime requirements. The
ceramic insert offers substantial increase in flow
ring lifetimes.
Trim materials are available to meet the
requirements of corrosive/erosive slurries.
See table 2.
The“FlowOvertheTop”V-NotchBalloffersan
alternative to the standard V-Notch Ball in scaling
applications.
The drive shaft is available with either a double D or
splined actuator connection to accommodate a
choice of actuation between a spring-opposed
diaphragm or a rack and pinion.
2

Slurry Vee-Ball Valve
D103154X012
Specifications
Product Bulletin
51.3:V150S
February 2013
Valve Sizes
J NPS 3, J 4, J 6, J 8, J 10, and J 12
End Connection
V150S: CL150 Raised-face flange
Face to Face Dimension
Seefigure2
Maximum Inlet Pressure
Consistent with pressure-temperature ratings per
ASME B16.34 but do not exceed the material
temperature capabilities shown below or the pressure
drop limitations
Maximum Shut Off Pressure
See tables 3 and 4
Shutoff Classification
Class I per ANSI/FCI 70-2 and IEC 60534-4
(Class II and better not available). A defined initial
maximum leak rate can be provided subject to review
of service conditions.
Construction Materials
Standard Construction: See table 1
Temperature Capability
For Trim 1: 427_C(801_F) maximum
For Trims 2 and 3: 230_C(446_F) maximum
For materials: See table 1
Flow Characteristic
Approximately equal percentage
Dimensions
See figures 2 and 3
Flow Direction
Reverse flow recommended (into concave face of
ball, out through the flow ring)
Flow Coefficients
See Fisher Catalog 12
Maximum Ball Rotation
90 degrees
Valve Installation
Shaft axis to be horizontal
Actuator Mounting
Right-hand or left-hand, as viewed from upstream
end of valve
Valve/Actuator Action
With diaphragm or piston rotary actuator and splined
shaft, the valve is field-reversible between PDTC or
PDTO:
rod closes valve) and
(extending actuator rod opens valve)
Actuator Size Selection
Contact your Emerson Process Management sales
office for information
Approximate Weight
NPS 3: 15 kg (33 lb)
NPS 4: 28 kg (62 lb)
NPS 6: 45 kg (99 lb)
NPS 8: 82 kg (180 lb)
NPS 10: 120kg(265lb)
NPS 12: 178kg(390lb)
J push-down-to-close (extending actuator
J push-down-to-open
3