
Instruction Manual
Form 5481
February 2009
Type 289P Pilot-Operated Relief Valve
Type 289P
W6834
Figure 1. NPS 1 Type 289P Pilot-Operated Relief Valve Figure 2. NPS 2 Type 289P Pilot-Operated Relief Valve
W3167-2
Introduction
Scope of Manual
This manual describes and provides instructions
and parts lists for the Type 289P pilot-operated relief
valve. Instructions and parts lists for any other Fisher®
equipment used with this relief valve will be found in
separate manuals.
Product Description
The Type 289P pilot-operated relief valve is used to
provide protection from overpressuring a downstream
system. This relief valve is suitable for service on
natural gas, air, propane, or any other operating
medium not corrosive to the internal parts. Smooth
opening action minimizes system pressure surges
during emergency action. Very little build-up over set
pressure is required to completely open the main valve
for maximum relief capacity. The external control line
provides quick, accurate pressure registration.
Specications
Some of the specications for a given relief valve as
it comes from the factory appear on the nameplate
attached to the Type 289P main valve spring case.
Other specications appear on the Type 6358B or
6365 pilot spring case.
www.emersonprocess.com/regulators
D102680X012

Type 289P
Specications
Body Size and End Connection Style
NPS 1 or 2, NPT
Maximum Relief (Inlet) Pressure
NPS 1: 50 psig (3,4 bar) over relief set
pressure or 110 psig (7,6 bar) whichever is lower
NPS 2: 15 psig (1,0 bar)
Relief Set Pressure Ranges
See Table 1
Pilot Information
See Tables 2 and 3
1. Relief pressure plus maximum allowable build-up over setting.
2. The pressure/temperature limits in this manual and any applicable standard or code limitation should not be exceeded.
WARNING
!
To avoid injury or damage, install,
operate, and maintain the Type 289P in
accordance with federal, state, and local
codes; rules and regulations; and these
instructions. The Type 289P cannot be
used as ASME safety relief valves.
Only a qualied person must install or
service the relief valve. Be certain the
main valve nameplate or pilot spring case
is updated to accurately indicate any eld
changes in equipment, materials, service
conditions or pressure settings.
If a leak develops in the system, it
indicates that service is required. Failure
to correct the situation immediately may
create a hazardous condition.
(1)(2)
Principle of Operation (Figure 3)
Inlet pressure registers on the underside of the main
valve diaphragm and underside of the pilot diaphragm.
As long as the inlet pressure is below the set pressure,
the pilot control spring keeps the pilot valve plug
closed. Inlet pressure passes through the pilot
restriction and registers as loading pressure on top of
the main valve diaphragm, keeping it closed.
When inlet pressure rises above the set pressure, the
pressure on the pilot diaphragm overcomes the pilot
control spring and opens the pilot valve plug. The
pilot exhausts the loading pressure from the top of the
Pressure Registration
External
Pilot Control Line and Vent Connections
1/4 NPT
Relief Valve Temperature Capabilities
With Nitrile (NBR): -20° to 180°F (-29° to 82°C)
With Fluorocarbon (FKM):
0° to 300°F (-18° to 149°C)
Approximate Weights
NPS 1: 5 pounds (2 kg)
NPS 2: 15 pounds (7 kg)
main valve diaphragm and plug assembly. While inlet
pressure is above the set pressure, the pilot continuously
exhausts gas. Inlet pressure unbalance overcomes the
main spring force and opens the main valve.
As the inlet pressure drops, the pilot control spring begins
to close the pilot valve plug and the exhaust slows. This
causes the inlet pressure to build in the main valve
diaphragm casing, allowing the control spring to close
the main valve. Once the main valve is closed, the pilot
valve plug closes and the exhaust stops.
Installation
Personal injury or system damage may
result if this relief valve is installed
where service conditions could exceed
the limits given on the pilot spring case
or main valve nameplate. Installations
should be adequately protected from
physical damage.
Overpressuring any portion of this
equipment may cause equipment
damage, leaks in the relief valve, or
personal injury due to bursting of
pressure-containing parts. System
operation within the Specications
section does not eliminate the
possibility of damage from external
sources or debris in the pipeline.
The relief valve should be inspected
for damage regularly and after any
overpressure condition.
WARNING
!
(2)
2

Type 289P
HOLLOW PASSAGE
IN VALVE PLUG STEM
UPPER PORTION
OF VALVE PLUG
LOWER PORTION
OF VALVE PLUG
EXPANDED VIEW OF THE TYPE 6358B
DIAPHRAGM ASSEMBLY AND VALVE PLUG
(FOR USE WITH NPS 1 AND 2 BODY SIZES)
INLET (CONTROLLED) PRESSURE
LOADING PRESSURE
OUTLET (EXHAUST) PRESSURE
ATMOSPHERIC PRESSURE
DIAPHRAGM
ASSEMBLY
DIAPHRAGM
ASSEMBLY
FIXED RESTRICTION
TO MAIN VALVE
DIAPHRAGM
TO EXHAUST PORT
NPS 1 TYPE 289P WITH TYPE 6358B PILOT
FIXED
RESTRICTION
TO MAIN VALVE
DIAPHRAGM
EXPANDED VIEW OF THE TYPE 6365 PILOT
DIAPHRAGM ASSEMBLY AND VALVE PLUG
(FOR USE WITH NPS 2 BODY SIZE ONLY)
INLET (CONTROLLED) PRESSURE
LOADING PRESSURE
OUTLET (EXHAUST) PRESSURE
ATMOSPHERIC PRESSURE
TO EXHAUST PORT
VALVE PLUG
NPS 2 TYPE 289P WITH TYPE 6358B PILOT
Figure 3. Type 289P Operational Schematics
3
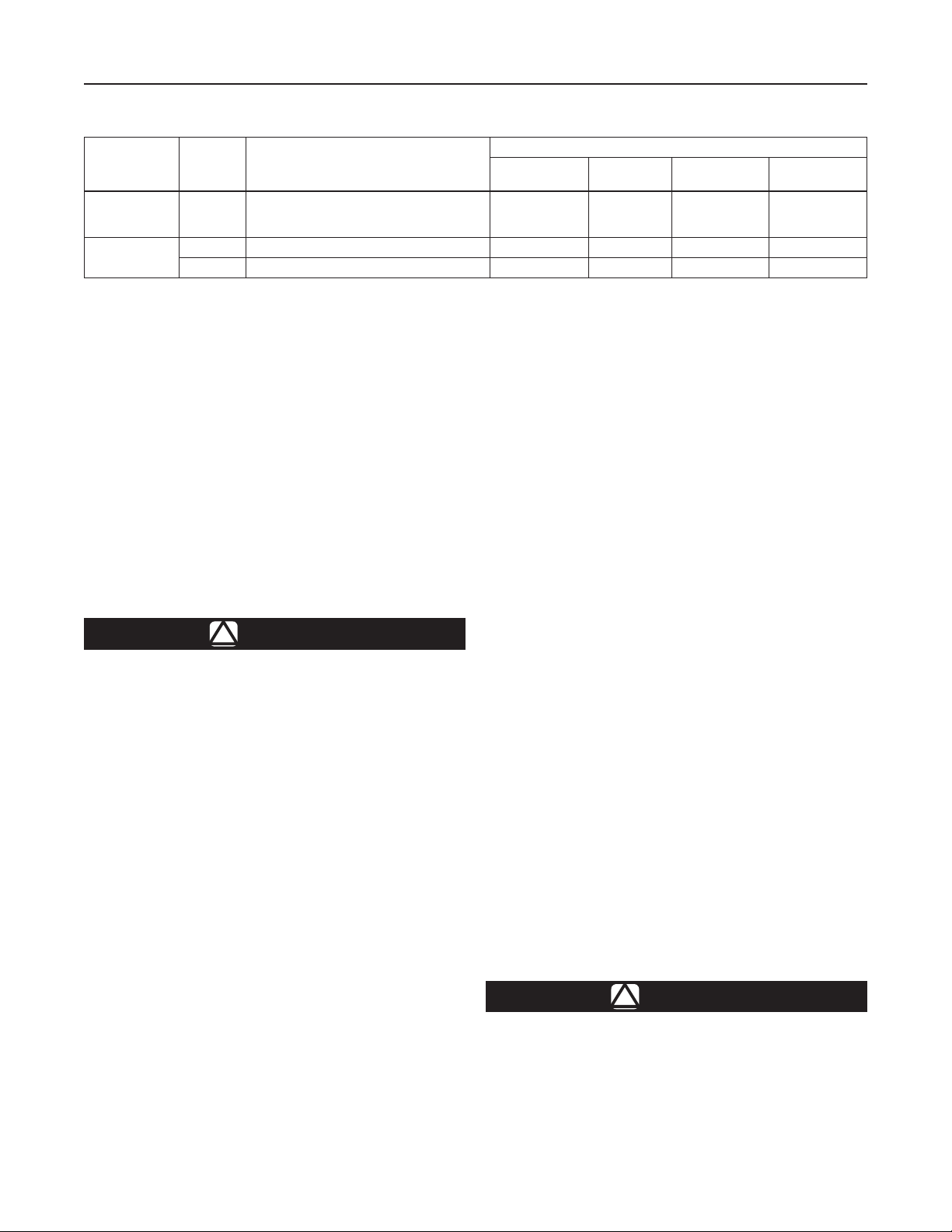
Type 289P
Table 1. Relief Set Pressure Ranges and Pilot Control Spring Infromation
MAIN VALVE
BODY SIZE,
NPS
1 6358B
2
PILOT
TYPE
6365 14-inches w.c. to 2 psig (35 mbar to 0,14 bar) 14A9672X012 Yellow 0.070 (1,78) 2.125 (54,0)
6358B 2 to 10 psig (0,14 to 0,69 bar) 14A9673X012 Black 0.102 (2,59) 2.125 (54,0)
RELIEF SET
PRESSURE RANGE
10 to 18 psig
18 to 30 psig
30 to 100 psig
(0,69 to 1,2 bar)
(1,2 to 2,1 bar)
(2,1 to 6,9 bar)
Before installing, inspect the main valve and pilot for
any shipment damage and any foreign material. Make
sure that the valve is oriented so that pipeline ow
enters the port labeled inlet. Apply pipe compound on
the pipe threads, but not on the body threads.
The typical pilot mounting position is shown in
Figures 1 and 2. To achieve other desired connections,
the pilot may be rotated on the pipe nipple.
The Type 289P requires a control line attached to the
1/4 NPT control connection. The control line should
be 3/8-inch (9,5 mm) outer diameter pipe or tubing or
larger and connected to a straight run of inlet piping.
If the pipeline contains dirt, install a lter in the control
line and/or upstream piping.
PILOT CONTROL SPRING INFORMATION
Part Number Color
1B986027212
1B788327022
1K748527202
Green
Unpainted
Red
Wire Diameter,
Inches (mm)
0.120
(3,05)
0.142
(3,61)
0.187
(4,75)
Free Length,
Inches (mm)
2.125
(54,0)
2.125
(54,0)
2.125
(54,0)
Note
Do not adjust the main valve spring.
Startup and Shutdown
With proper installation complete, slowly open
the upstream shutoff valve while using a gauge to
monitor inlet pressure to startup the relief valve or
backpressure regulator. If set pressure adjustment is
necessary, see the Pilot Adjustment section.
To shutdown, slowly close the upstream shutoff valves.
Release all pressure from the main valve and pilot by
opening a vent valve.
WARNING
!
If venting gas will accumulate and be
an explosion hazard under enclosed
conditions, such as in pit or underground
installations, make sure the installation
is remotely vented to a safe location.
To avoid possible injury or equipment
damage, never adjust the pilot control
spring to produce a set pressure higher
than the upper limit of the set pressure
range for that particular spring.
If it is necessary to vent the unit, install a 3/8-inch
(9,5 mm) exhaust line into the 3/8 NPT pilot exhaust
connection. This exhaust line may be vented directly
into the main valve outlet or separately to atmosphere.
In either case, the vent line or stack diameter should be
as large as practical with a minimum number of bends or
other restrictions.
A vent line or stack must be located to avoid venting
gas near buildings, air intakes, or any hazardous
location. The line or stack opening must be protected
against debris, weather, condensation, insects, or
anything else that might clog it.
Pilot Adjustment (See Figure 6 or 7)
If outlet pressure adjustment is necessary, monitor relief
(inlet) pressure with a gauge during the adjustment
procedure. Remove the pilot closing cap (key 12)
and loosen the locknut (key 11). Turn the adjusting
screw (key 10) into the spring case to increase the set
pressure. Turn the adjusting screw out of the spring
case to decrease the set pressure. When adjustment
is completed, tighten the locknut to lock the adjusting
screw in position and replace the pilot closing cap.
Maintenance
Relief valve parts are subject to normal wear and must
be inspected and maintained as necessary, depending
upon the service conditions.
WARNING
!
Avoid personal injury or damage
to property from sudden release
of pressure or uncontrolled gas or
other process uid. Before starting
to disassemble, carefully release all
4