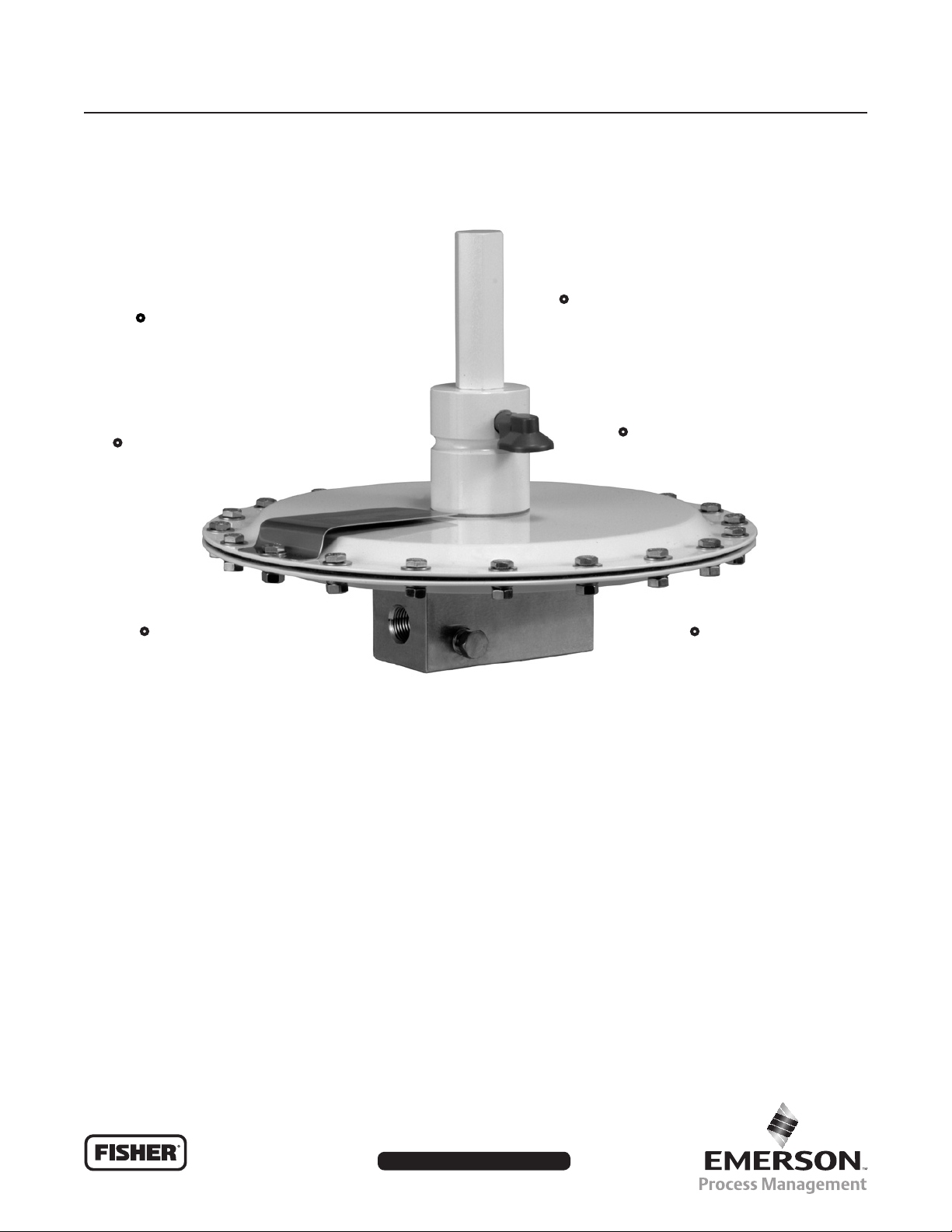
Bulletin 74.1:ACE95JR
Type ACE95jr Tank Blanketing Valve
Features
• Stainless Steel
• Fully Balanced Plug
Design Reduces Inlet
Pressure Sensitivity
Construction Available
April 2012
• High Sensitivity
• Bubble
Tight
Shutoff
W8157
Figure 1. Type ACE95jr Tank Blanketing Valve
Introduction
Tank blanketing is the process of using a gas, usually an
inert gas such as nitrogen, to maintain a slightly positive
pressure in an enclosed storage tank. Tank blanketing
prevents a stored product from vaporizing into the
atmosphere, reduces product combustibility, and prevents
oxidation or contamination of the product by reducing
its exposure to air. Tank blanketing is utilized with
various products, including: adhesives, pharmaceuticals,
pesticides, fertilizers, fuels, inks, photographic chemicals,
and food additives.
• Self-Contained
• Vacuum
Settings
Available
Type ACE95jr valves are self-contained, fully
balanced, and used for accurate pressure control on
tank blanketing systems. These valves help control
emissions and provide protection against atmospheric
contamination. Type ACE95jr valves maintain a positive
tank pressure which reduces the possibility of tank wall
collapse during pump out operations and prevents a
stored product from vaporizing to atmosphere.
www.sherregulators.com
D102722X012
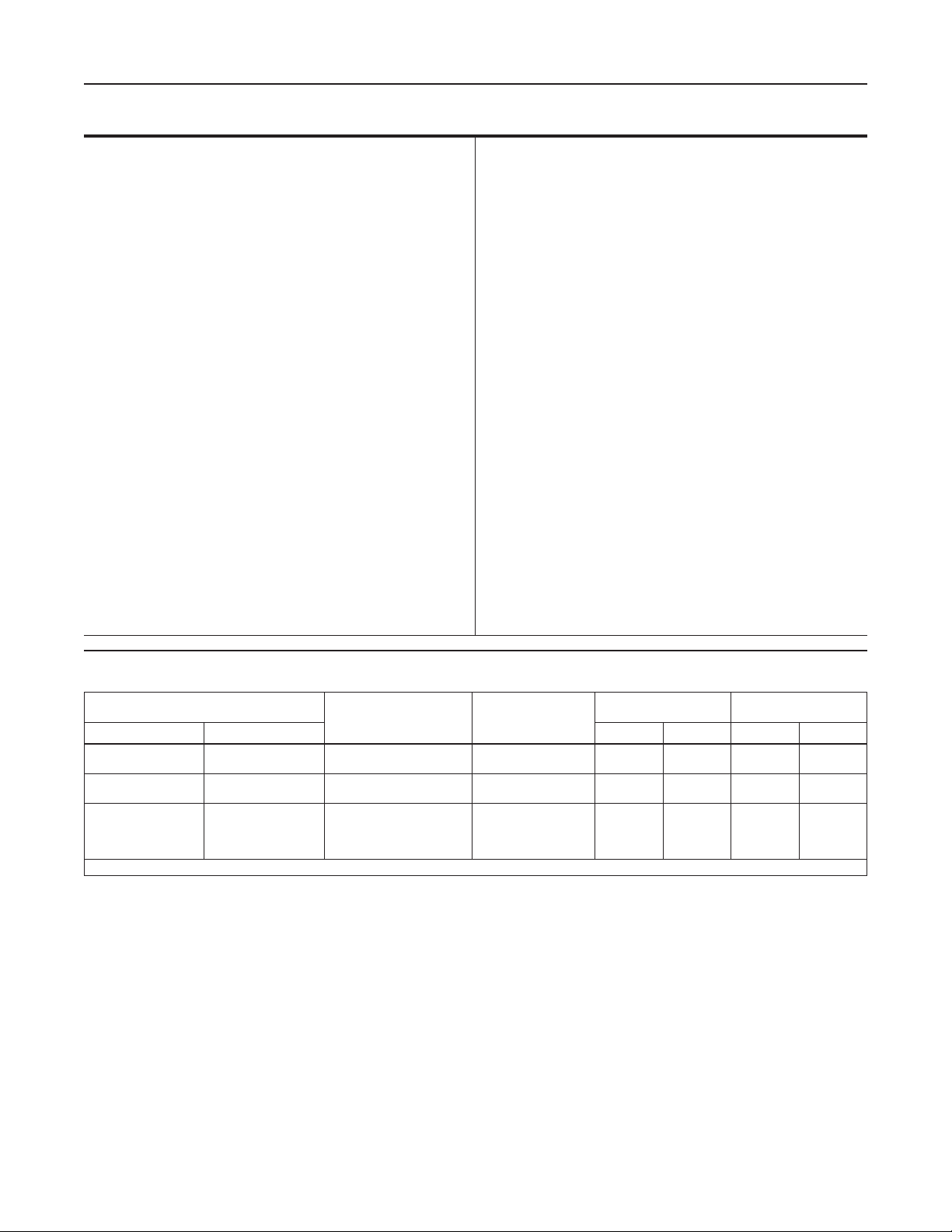
Bulletin 74.1:ACE95JR
Specications
Sizes and End Connection Styles
1/2 NPT
1 x 1/2 NPT
1 NPT
NPS 1/2 / DN 15, CL150 RF
NPS 1 / DN 25, CL150 RF
NPS 1 x 1/2 / DN 25 x 15, CL150 RF
NPS 1 / DN 25, Sanitary Flange
Maximum Operating Inlet Pressure
(1)
200 psig / 13.8 bar
Maximum Emergency Outlet (Casing) Pressure
20 psig / 1.4 bar
Maximum Operating Control Pressure
(1)
1.5 psig / 0.10 bar
Control Pressure Ranges
(1)
See Table 1
Maximum Differential Pressures
Up to 200 psig / 13.8 bar
Main Valve Flow Characteristic
Linear
Pressure Registration
External
Capacities
See Table 4
Temperature Capabilities
Nitrile (NBR):
(1)
-20 to 180°F / -29 to 82°C
Fluorocarbon (FKM):
0 to 212°F / -18 to 100°C
Ethylenepropylene (EPDM - FDA):
-20 to 212°F / -29 to 100°C
Peruoroelastomer (FFKM):
-20 to 212°F / -29 to 100°C
Flow Coefcients for Relief Valve Sizing
(1)
(110% of rated Cv)
Cv 0.2 use Cv 0.22
Cv 0.4 use Cv 0.44
IEC Sizing Coefcients
XT: 0.655; FD: 0.86; FL: 0.89
Construction Materials
Body: 316 Stainless Steel
Trim: 304 Stainless Steel and 316 Stainless Steel
Elastomers: Nitrile (NBR), Fluorocarbon (FKM),
FDA-Ethylenepropylene (EPDM), or
Peruoroelastomer (FFKM)
Diaphragm: Polytetrauoroethylene (PTFE)
Actuator: 316 Stainless Steel or Carbon Steel
Approximate Weight (with all accessories)
30 pounds / 14 kg
1. The pressure/temperature limits in this Bulletin, and any applicable standard or code limitation should not be exceeded.
Table 1. Control Pressure Ranges
OUTLET (CONTROL PRESSURE RANGE)
inches w.c. mbar inches mm inches mm
-5 to -0.5 -12 to -1 GC220701X22 Stainless Steel
-1 to 1 -2 to 2 GC220701X22 Stainless Steel
0.5 to 5
4 to 10
8 to 15
0.5 to 1.5 psig
1. The second spring is located under the diaphragm assembly.
1 to 12
10 to 25
20 to 37
34 to 103
Features and Benets
Large PTFE Diaphragm—Resistant to corrosion and
highly sensitive to changes in tank pressure.
Fully Balanced—Eliminates setpoint changes caused by
variations in inlet pressure.
Large Actuator—Large actuator diaphragm increases
sensitivity to tank pressure changes.
Rolling Diaphragm—The rolling diaphragm balances the
pilot valve and eliminates friction, resulting in extremely
accurate control.
SPRING PART NUMBER SPRING MATERIAL
GC220701X22
GC220702X22
GC220703X22
GC220708X22
Stainless Steel
Stainless Steel
Stainless Steel
Stainless Steel
Options and Accessories
Inlet Pressure Gauge—Displays pressure of blanketing
gas supply to the tank blanketing valve.
Control Pressure Gauge—Low-pressure gauge to
measure control pressure (tank pressure).
Purge Meter (Rotameter)—Maintains a small amount of
ow through the sensing or main line. Prevents corrosive
tank vapors from damaging upstream equipment.
Pressure Switch—Allows installation of an alarm system
to indicate low or high-pressure on the tank.
SPRING
FREE LENGTH
2.75
0.88
2.75
1.60
2.75
2.00
2.00
2.75
69.8
22.4
69.8
40.6
69.8
50.8
50.8
69.8
(1)
(1)
SPRING WIRE
0.080
0.085
0.080
0.065
0.080
0.112
0.125
0.225
DIAMETER
2.03
2.16
2.03
1.65
2.03
2.84
3.17
5.71
(1)
(1)
2

Bulletin 74.1:ACE95JR
POPPET
CAGE
O-RING SEAT
ROLLING
DIAPHRAGM
VALVE CLOSED
SENSING
CONECTION
INLET
VALVE OPEN
E0205
INLET PRESSURE
ATMOSPHERIC PRESSURE
TANK PRESSURE
Figure 2. Operational Schematic
Outlet Check Valve—Prevents corrosive gases and
vapors from owing back into the blanketing system
through the delivery line.
Single Array Manifold (SAM)—Provides sense line
connection and main valve connection through a single
tank nozzle.
Inlet Filter—Screens out any foreign material upstream
that may cause blockage in the gas ow.
Principle of Operation
The Type ACE95jr tank blanketing valve controls the
vapor space pressure over a stored liquid. When liquid is
pumped out of the tank or vapors in the tank condense, the
pressure in the tank decreases. Tank pressure is sensed
by the large actuator diaphragm. When tank pressure is
less than the valve set pressure, spring force moves the
actuator diaphragm downward.
TO TANK
When the actuator moves downward, it pushes open the
valve plug which allows ow in to the tank. See Figure 2.
When pressure in the tank increases above setpoint, the
large actuator diaphragm is pushed upward, allowing the
valve plug to close.
The valve plug is balanced (inlet pressure creates equal
upward and downward force on these components);
therefore, the outlet (control) pressure of the unit is not
affected by uctuating inlet pressure.
Installation
The Type ACE95jr tank blanketing valve was assembled
and preset to the customer specied pressure and
setpoint at the factory. The outlet (control) pressure range
of the valve is stamped on the nameplate fastened to the
upper actuator case. The gas blanketing setpoint is the
only adjustable feature on this unit.
3