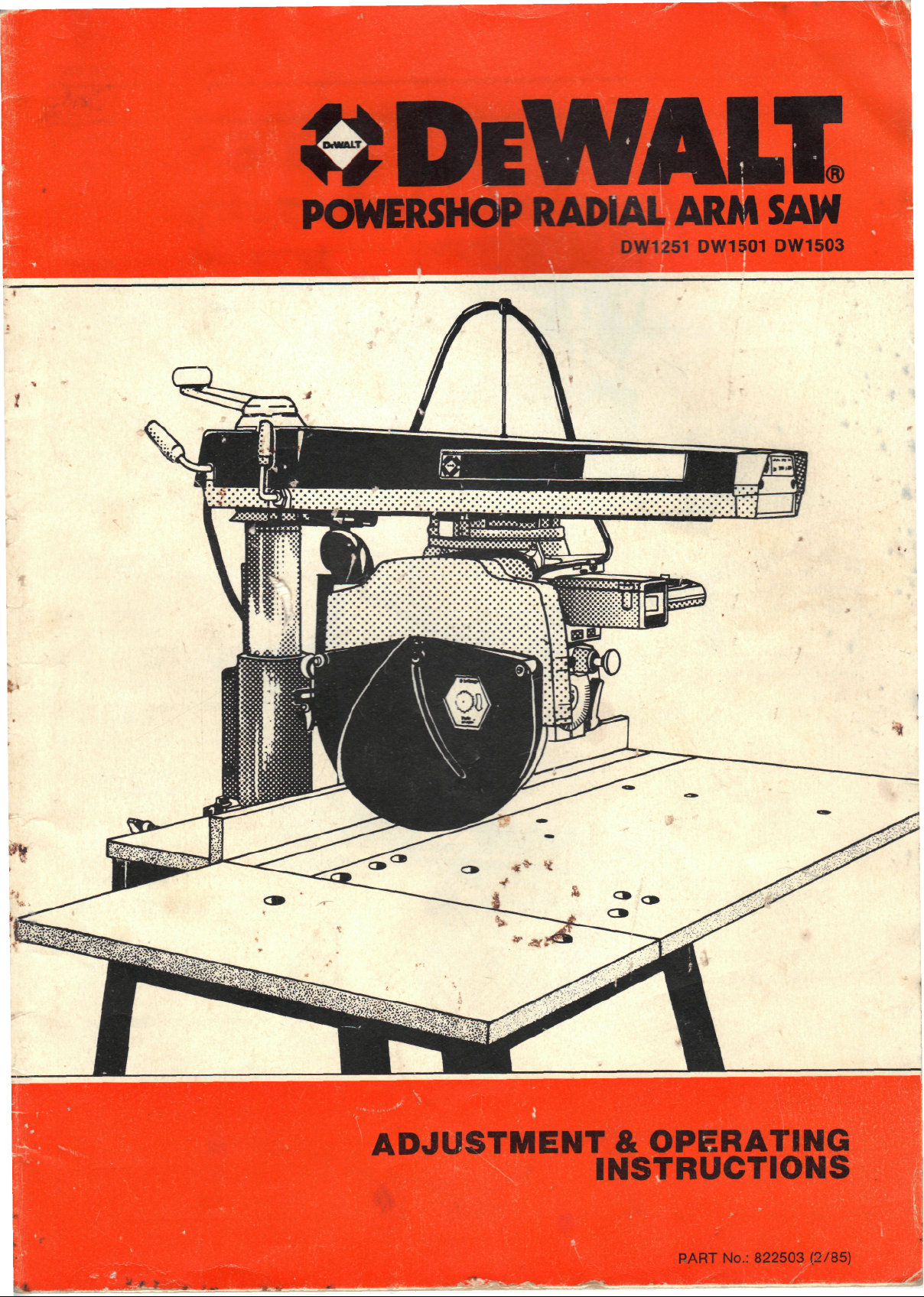
POWERSHOP
RADIAL
W1251
ARM
DW1501 DW1503
SAW
ADJUSTMENT
&
OPERATING
INSTRUCTIONS
PART
No.:
822503
(2/85)

THE
CONTROLS
1.
MITRE SCALE
18.
MITRE CLAMP
19.
MIRE
17.
YOKE
16.
TABLE CLAMP
15.
FENCE
LATCH
—i
2.
ARM
END-CAP
3. ARM
4.
RIP-LOCATING
SLIDE
BAR
5.
WORKTABLE
8.
ROLLER
YOKE
14.
BEVEL
13.
BEVEL
12.
BEVEL
HEAD/
ASSEMBLY
LATCH
SCALE
CLAMP
-
-
6.
ELEVATING
HANDLE
7.
RIPLOCK
10.
YOKE CLAMP
9.
COLUMN
11.
COLUMN
BASE
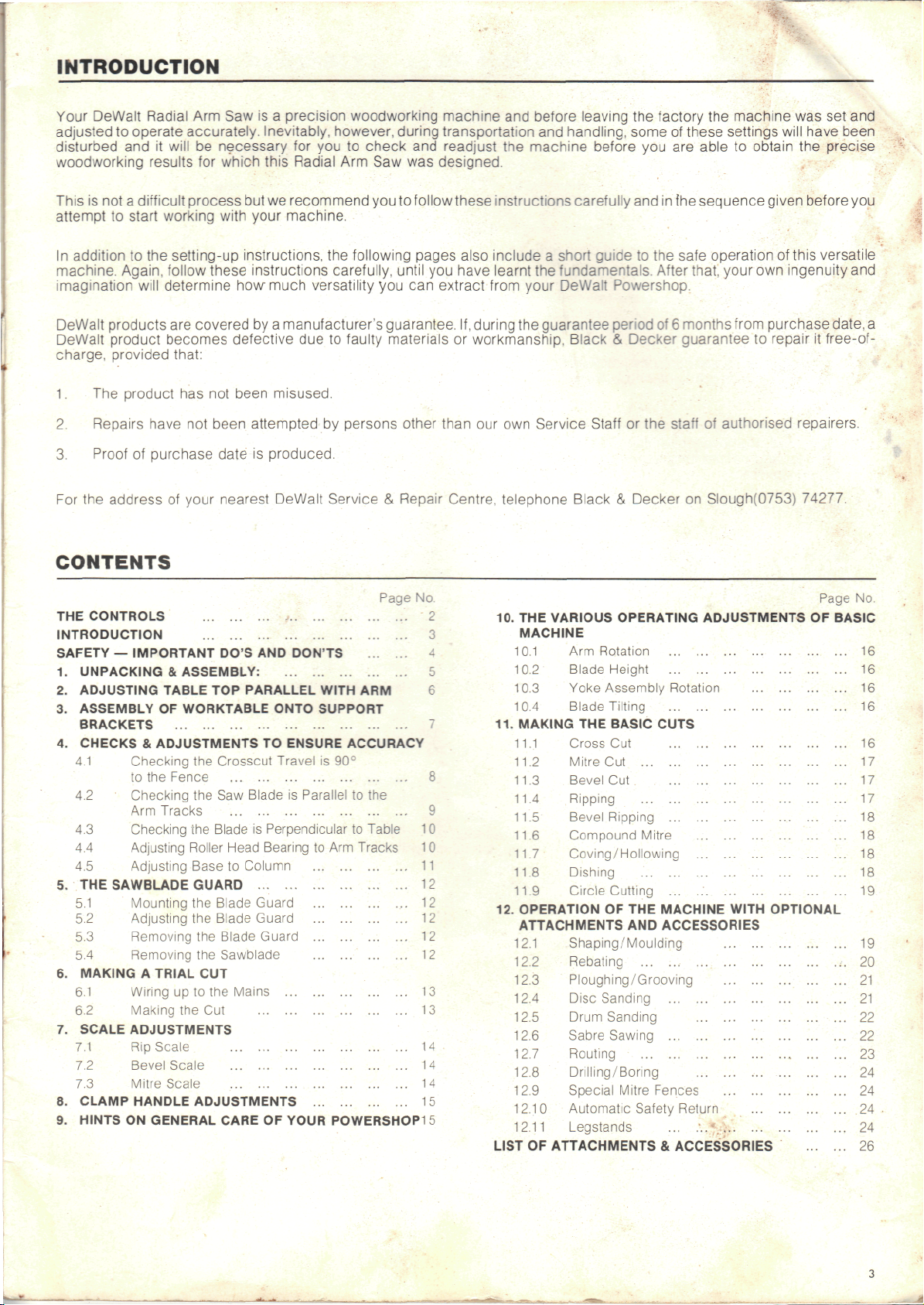
INTRODUCTION
Your
DeWalt Radial
adjusted
disturbed
to
operate accurately.
and it
woodworking
This
is not a
attempt
In
addition
difficult
to
start working with your machine.
to the
machine. Again,
imagination will determine
Arm Saw is a
will
be
results
necessary
for
which this Radial
process
setting-up instructions,
follow
these instructions carefully, until
'
precision woodworking
Inevitably,
for you to
but we
recommend
how
much versatility
however, during transportation
check
Arm Saw was
you
the
following pages also include a short
you can
and
machine
readjust
and
before leaving
and
the
handling, some
machine before
designed.
to
follow these instructions carefully
guide
you
have learnt
the
fundamentals. After
extract from your DeWalt Powershop.
the
factory
of
you are
and
in
to the
the
machine
these settings
able
to
fhe
sequence given before
safe operation
that,
your
will
obtain
of
own
was set and
this versatile
ingenuity
have
the
been
precise
you
and
DeWalt products
DeWalt
product becomes defective
are
covered
charge, provided that:
1.
The
2.
Repairs
3.
Proof
For
the
product
have
of
purchase date
address
has not
not
of
your nearest DeWalt Service & Repair Centre, telephone Black & Decker
been misused.
been attempted
CONTENTS
THE
CONTROLS
INTRODUCTION
SAFETY — IMPORTANT DO'S
1.
UNPACKING & ASSEMBLY:
2.
ADJUSTING TABLE
3.
ASSEMBLY
BRACKETS
4.
CHECKS & ADJUSTMENTS
4.1
Checking
4.2
Checking
4.3
Checking
4.4
Adjusting
4.5
Adjusting Base
THE
5.
5.1
Mounting
5.2
Adjusting
5.3
Removing
5.4
Removing
6.
MAKING A TRIAL
6.1
Wiring
6.2
Making
7.
SCALE ADJUSTMENTS
7.1
Rtp
7.2
Bevel Scale
7.3
Mitre Scale
8.
CLAMP
9.
HINTS
OF
to
the
Arm
Tracks
SAWBLADE
Scale
HANDLE
ON
GENERAL CARE
TOP
WORKTABLE ONTO SUPPORT
the
Crosscut Travel
Fence
8
the Saw
9
the
Blade
Roller
Head Bearing
to
GUARD
the
Blade Guard
the
Blade Guard
the
Blade Guard
the
Sawblade
CUT
up to the
the Cut
Mains
ADJUSTMENTS
by a
manufacturer's guarantee.
due to
is
produced.
AND
DON'TS
PARALLEL WITH
TO
ENSURE ACCURACY
Blade
is
is
Perpendicular
Column
... 12
11
12
12
...
OF
YOUR POWERSHOP1
faulty materials
by
persons other than
.
.
ARM
C
is
90
Parallel
to Arm
to the
to
Table
Tracks
Page
No.
... 2
... 5
10
10
If,
during
the
or
workmanship. Black & Decker
our own
3
4
6
12
12
13
13
14
14
14
15
5
guarantee period
Service
10. THE
11
12.
LIST
VARIOUS OPERATING
MACHINE
101
Arm
10.2
Blade Height
10.3
Yoke Assembly Rotation
10.4
Blade
MAKING
11.1
CrossCut
11.2
Mitre
11.3
Bevel
11.4
Ripping
11.5
Bevel Ripping ...'
11.6
Compound Mitre
11.7
Coving/Hollowing
11.8
Dishing
11.9
Circle
OPERATION
ATTACHMENTS
12.1
12.2
12.3
12.4
12.5
12.6
12.7
12.8
12.9
12.10
12.11
OF
Shaping/Moulding
Rebating
Ploughing/Grooving
Disc Sanding
Drum Sanding
Sabre
Routing
Drilling/Boring
Special Mitre Fences
Automatic Safety Return
Legstands
ATTACHMENTS & ACCESSORIES
of 6
months from purchase date,
guarantee
Staff
or the
staff
of
on
ADJUSTMENTS
Rotation
Tilting
THE
Cut 17
Cut 17
OF THE
Sawing
16
BASIC
Cutting
CUTS
17
18
18
18
'
MACHINE
AND
ACCESSORIES
19
20
21
21
22
' 22
... ...
to
repair
it
authorised repairers.
Slough(0753) 74277.
OF
18
19
WITH
OPTIONAL
free-of-
Page
No.
BASIC
a
16
16
16
16
23
24
24
24
24
26
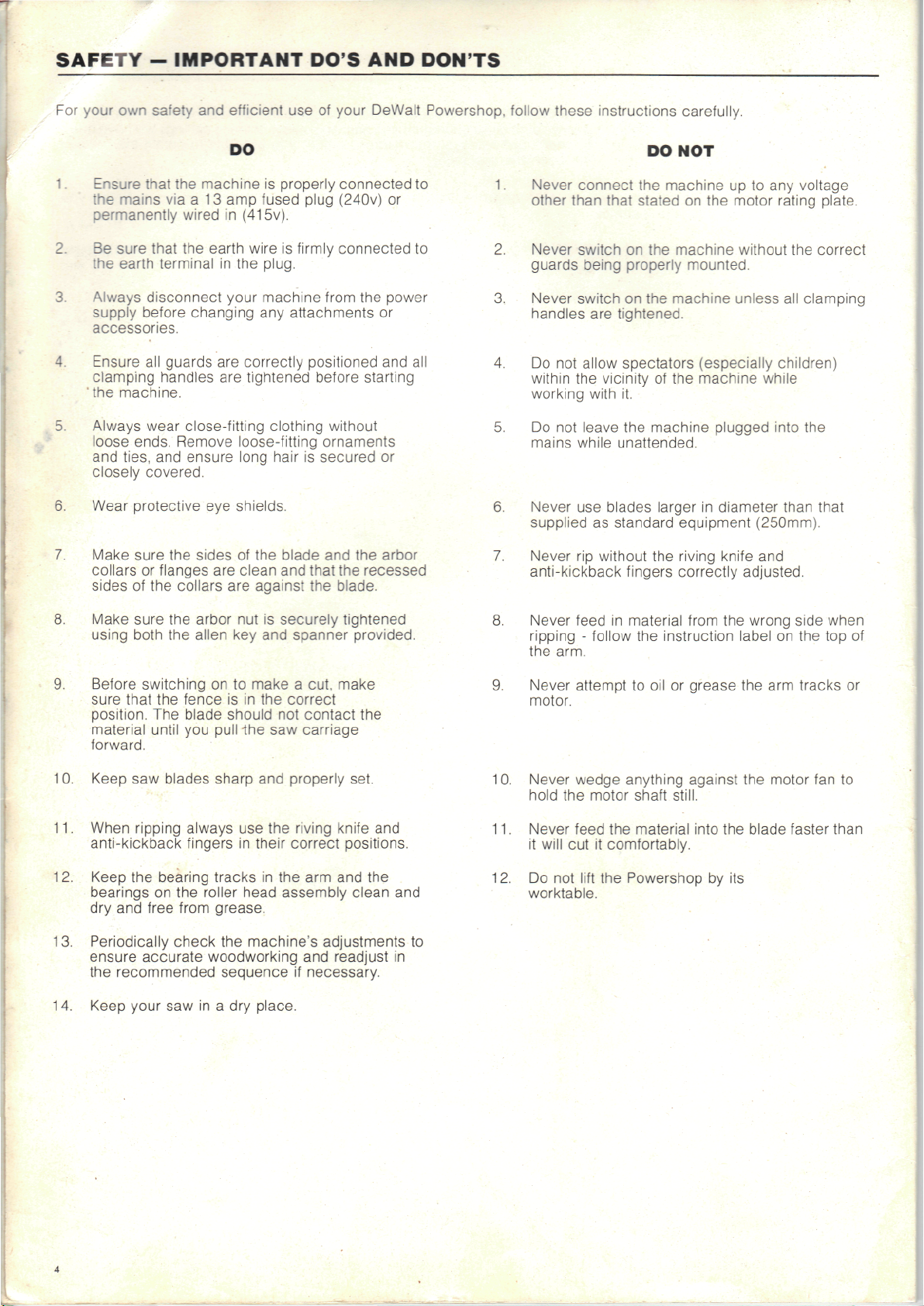
SAFETY - IMPORTANT DO'S
For
your
own
safety
and
efficient
use of
your DeWalt Powershop. follow these instructions carefully.
AND
DON'TS
DO
Ensure
the
permanently wired
Be
the
Always disconnect your machine from
supply before changing
accessories.
4.
Ensure
clamping
'
the
5.
Always wear close-fitting clothing without
loose ends. Remove loose-fitting ornaments
and
closely
6.
Wear protective
7.
Make sure
collars
sides
that
the
mains
sure that
earth terminal
all
machine.
ties,
covered.
or
of the
machine
via a
the
guards
handles
and
ensure long hair
the
sides
flanges
collars
is
13
amp
in
earth wire
in the
are
are
eye
are
are
properly connected
fused plug (240v)
(415v).
is
firmly
plug.
any
attachments
correctly positioned
tightened before starting
is
secured
shields.
of the
blade
and
and the
that
the
clean
against
connected
the
blade.
or
the
power
or
and all
or
arbor
recessed
to
1.
to 2.
3.
DO
Never connect
other
than
Never switch
guards being properly mounted.
Never switch
handles
4.
Do not
5.
Do not
6.
Never
7.
Never
allow spectators (especially children)
within
the
working
leave
mains while unattended.
use
supplied
rip
anti-kickback
the
that stated
are
tightened.
vicinity
with
blades larger
as
standard equipment (250mm).
without
machine
on the
on the
of the
it.
the
machine plugged into
the
fingers correctly adjusted.
NOT
up to any
on the
machine without
machine
riving knife
motor rating plate.
unless
machine
in
while
diameter than that
and
voltage
the
all
clamping
the
correct
8.
Make sure
using both
9.
Before switching
sure that
position.
material
forward.
10.
Keep
11.
When ripping always
anti-kickback
12.
Keep
bearings
dry and
13.
Periodically
ensure accurate woodworking
the
recommended sequence
14.
Keep your
the
arbor
the
alien
on to
the
fence
The
blade should
until
you
pull-the
saw
blades sharp
fingers
the
bearing tracks
on the
free from grease.
roller head assembly clean
check
saw in a dry
nut is
securely tightened
key and
is in the
use the
in
the
spanner provided.
make a cut, make
correct
not
contact
saw
carriage
and
properly set.
riving knife
their
correct positions.
in the arm and the
machine's adjustments
place.
and
readjust
if
necessary.
the
and
and
to
in
Never feed
ripping - follow
the
arm.
9.
Never attempt
motor.
10.
Never wedge anything against
hold
the
11.
Never feed
it
will
12.
Do not
worktable.
in
motor shaft
the
cut it
comfortably.
lift
the
material from
the
instruction label
to oil or
material into
Powershop
grease
still.
the
wrong side when
the arm
the
motor
the
blade faster than
by its
on the top of
tracks
or
fan to
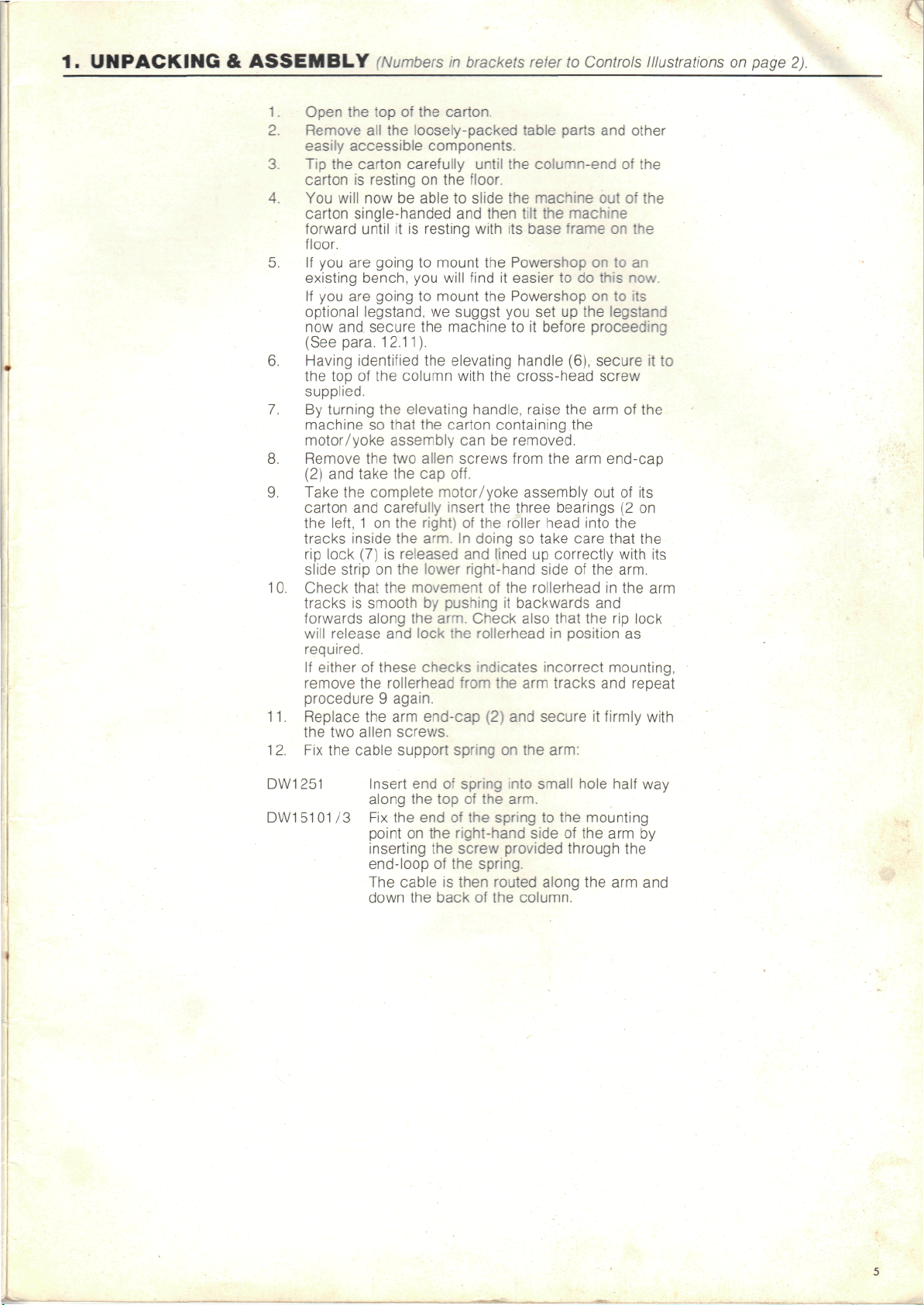
1.
UNPACKING & ASSEMBLY
1.
Open
2.
Remove
easily
3.
Tip the
carton
4. You
carton single-handed
forward
floor.
5.
If you are
existing
If
you are
optional
now
(See
6.
Having identified
the top of the
supplied.
7.
By
machine
motor/yoke assembly
8.
Remove
(2)
9.
Take
carton
the
tracks
rip
slide
10.
Check that
tracks
forwards
will
required.
If
either
remove
procedure 9 again.
11.
Replace
the two
12.
Fix the
(Numbers
the top of the
all the
accessible components.
carton carefully until
is
resting
will
now be
until
it is
going
bench,
going
legstand,
and
secure
para.
12.11).
turning
and
left,
lock
release
the
so
that
the two
take
the cap
the
complete motor/yoke assembly
and
carefully insert
1 on the
inside
the
(7) is
strip
on the
the
is
smooth
along
and
of
these checks indicates incorrect mounting,
the
rollerhead from
the arm
alien screws.
cable support spring
in
brackets
carton.
loosely-packed table parts
on the
able
to
you
to
the
column with
elevating handle, raise
the
alien screws from
right)
arm.
released
lower right-hand side
movement
by
the
lock
end-cap
floor.
to
slide
and
then
resting with
mount
mount
we
the
arm.
the
will find
the
suggst
machine
elevating handle (6), secure
the
carton containing
can be
off.
the
of the
In
doing
and
lined
of the
pushing
Check
the
rollerhead
the arm
(2) and
refer
to
Controls Illustrations
the
column-end
the
machine
tilt
the
its
base frame
Powershop
it
easier
Powershop
you set up the
to it
before proceeding
cross-head screw
removed.
the arm
three bearings
roller head into
so
take care
up
rollerhead
it
backwards
also that
in
secure
on the
arm:
out of the
machine
on to an
to do
this now.
on to its
the arm of the
the
out of its
correctly
of the
and
the rip
position
tracks
it
and
other
of the
on the
legstand
it to
end-cap
(2 on
the
that
the
with
its
arm.
in the arm
lock
as
and
repeat
firmly
with
on
page
2).
DW1251
DW1
51 01
Insert
/3
Fix the end of the
end of
along
the top of the
point
on the
inserting
end-loop
The
cable
down
the
the
spring into small hole
right-hand side
screw provided through
of the
is
then routed along
back
arm.
spring
spring.
of the
to the
of the arm by
column.
half
way
mounting
the
the arm and
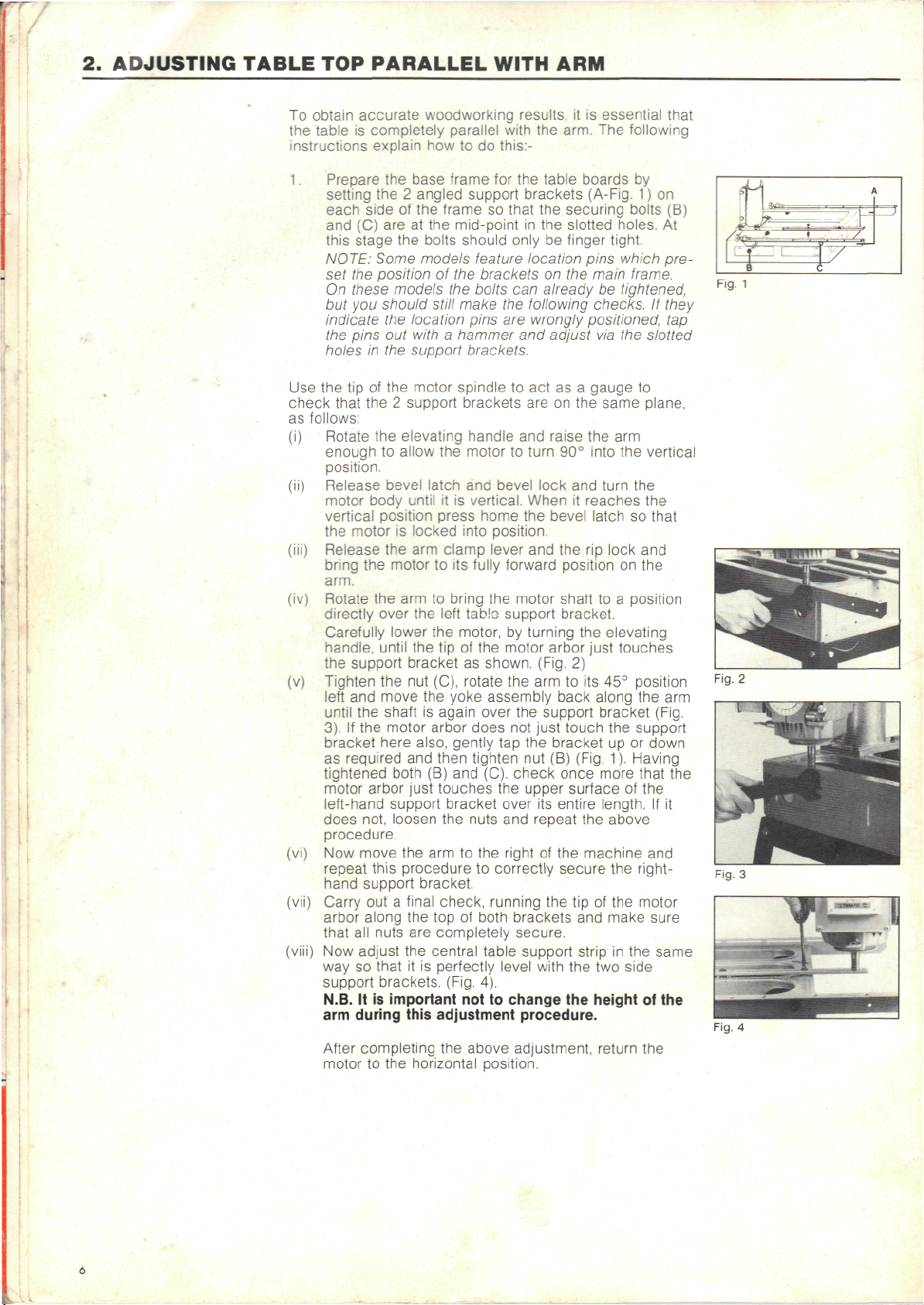
7
2.
ADJUSTING TABLE
TOP
To
obtain accurate woodworking results,
the
table
instructions explain
1.
Prepare
PARALLEL WITH
is
completely parallel with
how to do
the
setting
each side
and (C) are at the
this
stage
NOTE: Some
set
the
On
these
but you
indicate
the
pins
holes
base frame
the 2
angled
of the
the
bolts should only
models
position
models
should
the
out
in the
still make
location
with a hammer
support brackets.
frame
mid-point
of the
the
this:-
for the
support
so
that
feature
brackets
bolts
can
the
pins
are
brackets
in the
location
and
ARM
it is
the
arm.
table boards
the
on the
already
following
wrongly
(A-Fig.
securing bolts
slotted holes.
be
finger
pins which
checks.
positioned:
adjust
essential that
The
following
by
1)
on
(B)
tight.
main frame.
be
via the
At
pre-
tightened,
If
they
tap
slotted
Fig.
1
Use the tip of the
check that
as
follows:
Rotate
(i)
enough
position.
Release bevel latch
motor
vertical position press home
the
motor
Release
bring
the
arm.
(iv)
Rotate
directly over
Carefully
handle,
the
support bracket
(v)
Tighten
left
and
until
the
3). If the
bracket here also, gently
as
required
tightened both
motor
left-hand support bracket over
does
not,
procedure.
Now
move
repeat this
hand support bracket.
(vii)
Carry
arbor
along
that
all
Now
adjust
way
so
support
N.B.
It is
arm
during this adjustment
After
completing
motor
motor spindle
the 2
support brackets
the
elevating handle
to
allow
the
body
until
it is
is
locked into position.
the arm
motor
the arm to
lower
until
the nut
move
shaft
motor arbor does
arbor just touches
out a
nuts
that
brackets. (Fig.
important
to the
clamp
to its
bring
the
left
the
the tip of the
(C),
the
yoke assembly back along
is
again over
and
then tighten
(B) and
loosen
the
the arm to the
procedure
final check, running
the top of
are
completely secure.
the
central table support strip
it is
perfectly level with
the
horizontal position.
to act as a
are on the
and
motor
to
turn
and
bevel lock
vertical. When
fully
tablo
motor,
as
rotate
nuts
to
not to
above adjustment, return
the
lever
and the rip
forward position
the
motor
support bracket.
by
turning
motor arbor just touches
shown. (Fig.
the arm to its 45°
the
support bracket
not
just touch
tap the
nut (B)
(C).
check
the
upper surface
its
and
repeat
right
of the
correctly
both brackets
4).
the tip of the
change
procedure.
gauge
same plane,
raise
the arm
90°
into
and
turn
it
reaches
bevel latch
lock
shaft
to a
the
elevating
2)
(Fig.
once
the
machine
and
the two
the
height
the
up or
more that
above
the
make sure
in the
bracket
entire length.
secure
to
the
vertical
the
the
so
and
on the
position
position
the arm
support
down
1).
Having
of the
and
right motor
side
of the
the
that
(Fig.
the
If it
same
Fig.
Fig.
2
4
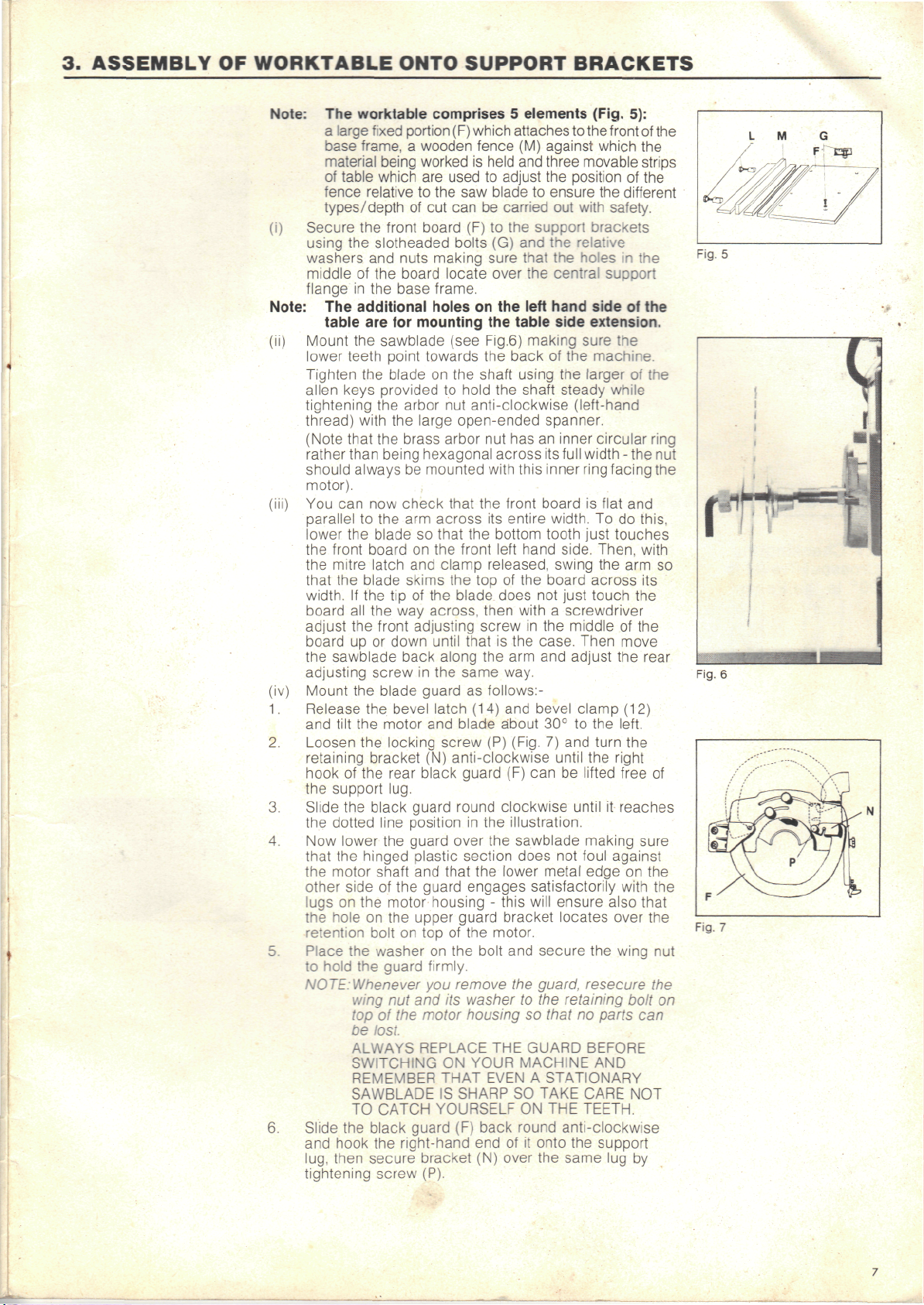
3.
ASSEMBLY
OF
WORKTABLE
Note:
(i)
Secure
Note:
(ii)
Mount
(iii)
You can now
(iv)
Mount
1.
Release
2.
Loosen
3.
Slide
4.
Now
6.
Slide
ONTO
The
worktable comprises 5 elements (Fig.
a
large fixed
base
frame, a wooden fence
material being worked
of
table which
fence
types/depth
using
washers
middle
flange
The
lower
Tighten
alien keys provided
tightening
thread)
(Note
rather
should always
motor).
parallel
lower
the
the
that
width.
board
adjust
board
the
adjusting
and
retaining
hook
the
the
that
the
other
lugs
the
retention bolt
Place
to
NOTE:Whenever
and
lug,
tightening
the
the
of the
in the
additional holes
table
are for
the
teeth point towards
the
with
that
than being hexagonal across
to the arm
the
front
mitre latch
the
blade skims
If the tip of the
all the way
the
up or
sawblade back along
the
tilt
the
the
of the
support lug.
the
dotted line position
lower
the
hinged plastic section does
motor shaft
side
on the
hole
the
hold
the
wing
top of the
be
ALWAYS
SWITCHING
REMEMBER
SAWBLADE
TO
the
hook
then
portion
are
relative
front board
slotheaded bolts
and
nuts making sure that
board locate over
base frame.
sawblade (see
blade
the
the
the
blade
board
front adjusting screw
down until that
screw
blade guard
the
bevel latch
motor
locking screw
bracket
rear
black guard round clockwise until
the
of the
motor housing - this will ensure also that
on the
on top of the
washer
guard
nut and its
lost.
CATCH YOURSELF
black
the
right-hand
secure bracket
screw (P).
used
to the saw
of cut can be
mounting
on the
to
arbor
nut
large open-ended spanner.
brass arbor
be
mounted with this inner ring facing
check that
across
so
that
on the
and
clamp released, swing
the top of the
across, then with a screwdriver
in the
and
(N)
anti-clockwise until
black guard
guard over
and
that
guard engages satisfactorily with
upper guard bracket locates over
on the
firmly.
you
motor
REPLACE
ON
THAT EVEN A STATIONARY
IS
guard
SUPPORT
(F)
which attaches
(M)
is
held
and
to
adjust
blade
carried
(F) to the
(G) and the
on the
the
table side extension.
Fig.6)
the
back
shaft
hold
the
front
blade,
same way.
as
blade about
in
remove
washer
housing
SHARP
(F)
using
the
anti-clockwise (left-hand
(14)
the
YOUR MACHINE
end of it
shaft steady
nut has an
the
front board
its
entire
bottom tooth just touches
left
hand side. Then, with
does
is the
the arm and
follows:-
and
(P)
(Fig.
(F) can be
the
illustration.
the
sawblade making sure
lower metal edge
motor.
bolt
and
the
to the
so
THE
SO
ON THE
back round anti-clockwise
(N)
over
BRACKETS
to
the
against which
three movable strips
the
position
to
ensure
support
the
left
hand side
making sure
of the
its
width.
board across
not
in the
case. Then move
bevel clamp (12)
30° to the
7) and
secure
guard,
that
GUARD BEFORE
TAKE CARE
onto
the
the
out
with safety.
brackets
relative
the
holes
central support
machine.
the
larger
inner circular ring
full
width
is
To do
the arm so
just
touch
middle
adjust
turn
the
lifted
not
foul
the
resecure
retaining bolt
no
parts
AND
TEETH.
the
support
same
5):
front
of the
different
in the
of the
the
of the
while
- the nut
flat
and
of the
the
left.
the
right
free
it
reaches
against
on the
wing
NOT
lug by
of
the
this,
its
the
rear
of
the
the
nut
the
can
the
the
on
Fig.
Fig.
Fig.
f
5
-
i
«t
'
I
6
7
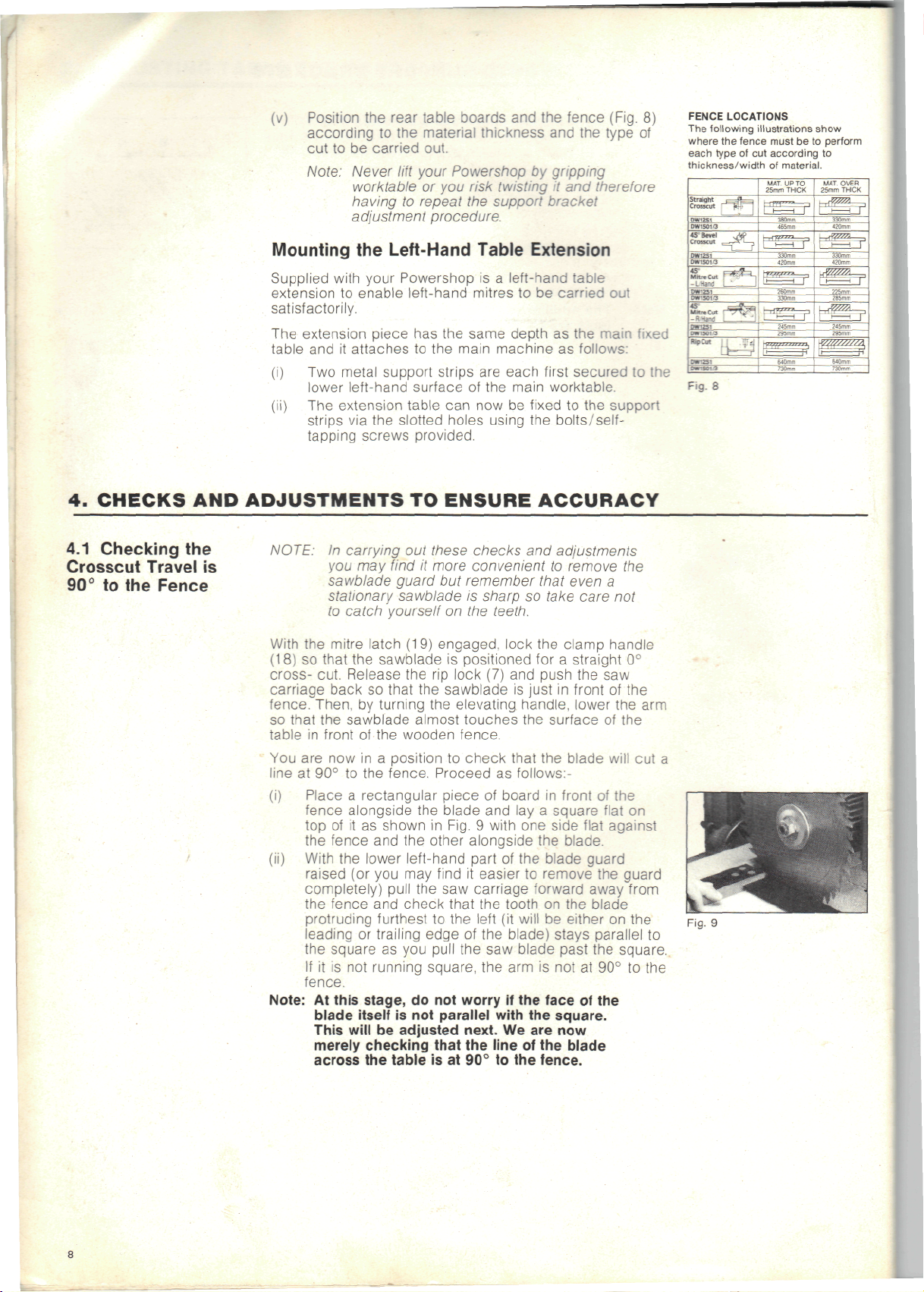
(v)
Position
according
cut to be
Note: Never
the
rear table boards
to the
carried
worktable
having
lift
to
your
material
out.
Powershop
or you
repeat
thickness
risk twisting
the
support bracket
adjustment procedure.
and the
and the
by
gripping
it and
fence (Fig.
type
therefore
of
8)
FENCE LOCATIONS
The
following
where
each
thickness/width
the
type
illustrations
fence
of cut
of
must
according
be to
material.
show
perform
to
4.
CHECKS
4.1
Checking
Crosscut
90° to the
AND
the
Travel
Fence
Mounting
Supplied with your Powershop
extension
satisfactorily.
The
extension
table
and it
(i)
Two
(ii)
The
ADJUSTMENTS
NOTE:
is
With
the
(18)
so
crosscarriage back
fence. Then,
so
that
table
in
You are now in a
line
at 90° to the
(i)
Place a rectangular piece
(ii)
With
Note:
At
the
Left-Hand
to
enable left-hand mitres
piece
attaches
has the
to the
main machine
metal support strips
lower
left-hand surface
extension table
strips
via the
slotted holes using
can now be
tapping screws provided.
TO
ENSURE ACCURACY
In
carrying
you may
sawblade guard
out
these
find
it
more convenient
but
stationary sawblade
to
catch
yourself
mitre latch
that
the
sawblade
cut. Release
so
that
by
turning
the
sawblade almost touches
front
of the
position
on the
(19)
engaged, lock
is
the rip
lock
the
sawblade
the
elevating handle, lower
wooden fence.
to
fence. Proceed
fence
alongside
top of it as
the
fence
the
lower left-hand part
raised
(or you may
completely) pull
the
fence
protruding furthest
leading
square
If
it is not
or
the
the
shown
and the
blade
in
Fig. 9 with
other alongside
find
the saw
and
check that
to the
trailing edge
as you
pull
the saw
running square,
fence.
this stage,
blade itself
This
will
do not
is not
be
parallel with
adjusted next.
worry
merely checking that
across
the
table
is at 90° to the
Table
same depth
are
of the
checks
remember that even
is
Extension
is a
left-hand
to be
as the
each
first
main worktable.
fixed
the
and
to
sharp
so
take care
table
carried
out
main
as
follows:
secured
to the
to the
support
bolts/self-
adjustments
remove
the
a
not
teeth.
the
clamp handle
positioned
(7) and
is
for a
push
just
straight
the saw
in
front
0°
of the
the arm
the
check that
as
follows:-
of
board
and lay a
one
of the
it
easier
to
surface
the
in
square
side
the
blade guard
remove
of the
blade will
front
of the
flat
flat
blade,
the
on
against
guard
carriage forward away from
the
tooth
left
(it
will
be
of the
blade) stays parallel
blade past
on the
blade
either
the
on the
square.
the arm is not at 90° to the
if the
face
the
of the
square.
We are now
the
line
of the
blade
fence.
fixed
cut a
to
Fig.
Fig.
8
9

Fig.
10
To
Adjust
(i)
With
slacken
(ii)
Loosen
shown
(ill)
Release
the
arm
required, loosen
either
needs
the
right
If
the
move
left
and
flanges a little
latch
blade
overtighten
will
be too
(iv)
Once
retighten
Fig.
(v)
Adjust
registers
the
Crosscut
the
mitre latch engaged
the
mitre clamp.
the
lock nuts
in
Fig.
10.
the
mitre latch
needs
to
side
to go to the
of the arm and
opposite
to the
tighten
and
relative
satisfied
the
and
of the arm
is the
right, loosen
the
at a
clamp
and
to the
the
adjusting flanges
stiff
to
operate
that
lock nuts
10).
the
pointer
0° in
this
Travel
on
each
and
move
to
give
tighten
(Fig.
left,
loosen
tighten
case,
the
flange
time
the
on the
position.
on the
and
check
fence
with a square.
easily.
crosscut travel
on
each side
mitre scale
in the 0°
side
of the
depending
the
the
11)
and the arm
re-engage
the
true
adjusting
if the
front
the
adusting
the
flange
adjusting
right.
crosscut travel
or the
of the arm (as in
so
position.
arm.
on
which
90°
crosscut
flanges
of the arm
flange
on the
needs
flange
Adjust
the
mitre
Do not
mitre
is
accurate,
that
it
on the
the
latch
as
way
on
on
left.
to
of the
Fig.
11
4.2. Checking
Saw
Blade
to
the Arm
is
Tracks.
the
Parallel
This check
position,
run
"dog fashion" (Fig.
adjusted
set of the
would
being
To
Check
(i)
Place a square
To
Adjust
The
illustration
yoke
with yoke
to
the
(i)
Firstly,
(ii)
Then,
(iii)
Having adjusted
(iv)
Now
is to
the
blade
in
this way.
blade (distance across
also tend
cut.
with
the
crosscut
lock)
parallel
is
assembly.
yoke
movement
nut
locating slide
release
(J)
until
therefore
all
in
carriage
surface
clamp
is
the
carriage
the
If
the
accurate
sawblade just
position
check that
to the
necessary.
(Fig.
(17)
is
by the
grasp yoke
(H)
which increases
if the
the
(Fig.
13/13a)
the
blade
also parallel
nuts.
this
way,
forward.
of the
release
and
facing
the
the
slide
bar and the
backwards until
fence.
blade
fence,
parallel
ensure that,
runs true across
it
to
cause scorch marks
against
the
square.
13)
The
precise alignment
made
locking nuts (J).
left
or
bar (K) and
blade
yoke
clamp
and
is in
the
release
table
the rip
then rotate
fence
is
completely flat, across
this
will
in the
12).
If the
blade
will produce
the
fence
in
(lock
shows
possible
right,
is
Raise
confirm
rip
front
it in
left
in
still
fact parallel
blade parallel
the rip
by
locating
and
yoke clamp. Then push
cutting.
that position
hand face
If it is not
the
by
both hands
if
there
the
nylon
not
parallel
(10)
turn
yoke slightly
to the arm
lock
the saw
turning
the
yoke
lock
the
that
straight
the
a cut
the
of the
components
collar
is
friction between
and
the
slide
it
into
blade
the saw
90°
table
is
tips
on the
as in
of the
parallel,
of
and
movement tighten
block
loosen
to the
tracks. Then
to the arm
and
blade just above
elevating handle.
bar and the
90° so
that
is
cross-
and
incorrectly
wider than
of the
teeth).
timber
Fig. 9 and,
fence
with
blade
adjustment
of the
rollerhead
(I)
which
check
(L).
to the
square.
the
to
left
square
pull
the saw
that
position
resting against
its
face against
will
cut
does
not
the
It
in the 90°
the rip
is
(8)
is
fixed
it for
the rip
lock nuts
or
right
and
tighten
tracks
the
yoke
the
blade
with
the saw
perform
Fig.
Fig.
Fig.
12
13
133