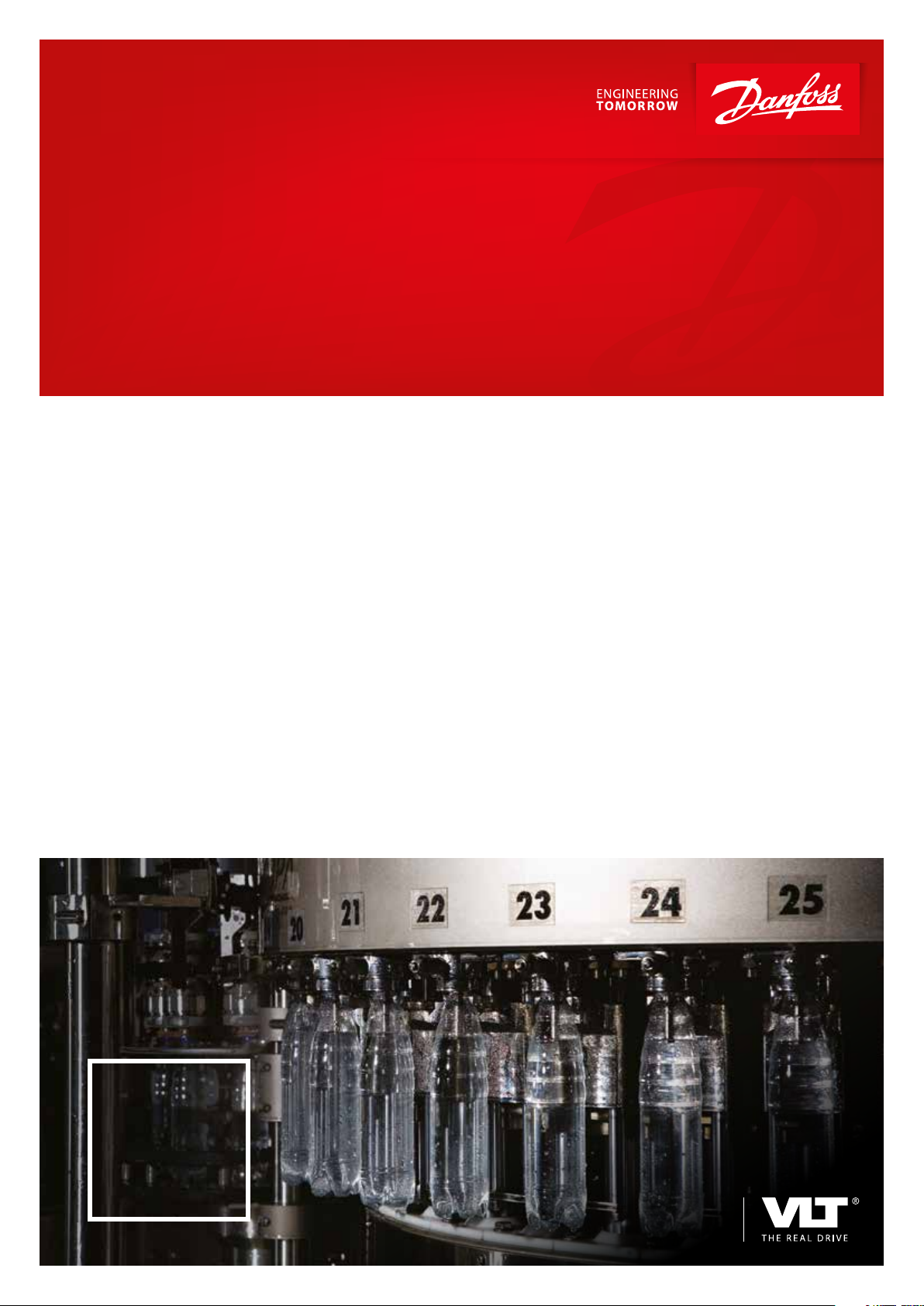
VLT® AutomationDrive & VLT® Motion Control Option MCO 305
Replace complexity with flexibility
Control your PM motors
with a VLT® drive
Improve productivity and cost efficiency without sacrificing precision.
For many years servo technology has been an industry
favourite due to its dynamics and precision in synchronising and positioning applications. This level of performance comes at a price, as servo drives may require that
2000-4000 parameters are set during commissioning. A
process that adds complexity to the system, including
extra time and eort for setup.
VLT® control of PM motors
By replacing a servo drive with a Danfoss VLT® frequency
converter to control direct torque, permanent magnet (PM)
motors, it is possible to achieve precision and consistency
with less system complexity.
VLT drives are easy to install and commission, and provide
accurate dynamic motion control, synchronisation,
positioning, cam-control, monitoring, and protection. This
means that owners can maintain high quality processes,
which increase productivity and minimise costs. In fact, it is
possible to save up to 40% on costs by choosing a VLT®
AutomationDrive and control options, compared with a
PLC and servo system.
Increase performance with MCO 305
When combined with the Motion Control Option
MCO 305, the AutomationDrive can control extremely
complex applications where direct drive and/or torque
control are required.
This option is built directly into the drive and the setup is
handled via the VLT® Software Tool MCT10. The PC tool
includes a programming editor with program examples,
graphical cam prole editor and “testrun” and “scope”
functions for controller optimisation.
Globally supported standard products
A major advantage of a VLT drive is that it has built on
standard components. Extra options are built directly into
the drive. VLT drives are available in a wide variety of frame
sizes. For customers who already use VLT® AutomationDrives, the fact that the drives can be used to control PM
motors enables them to reduce the number of suppliers.
40%
Cost savings with
VLT® AutomationDrive and MCO 305
compared with a PLC
and servo system
www.danfoss.com/drives
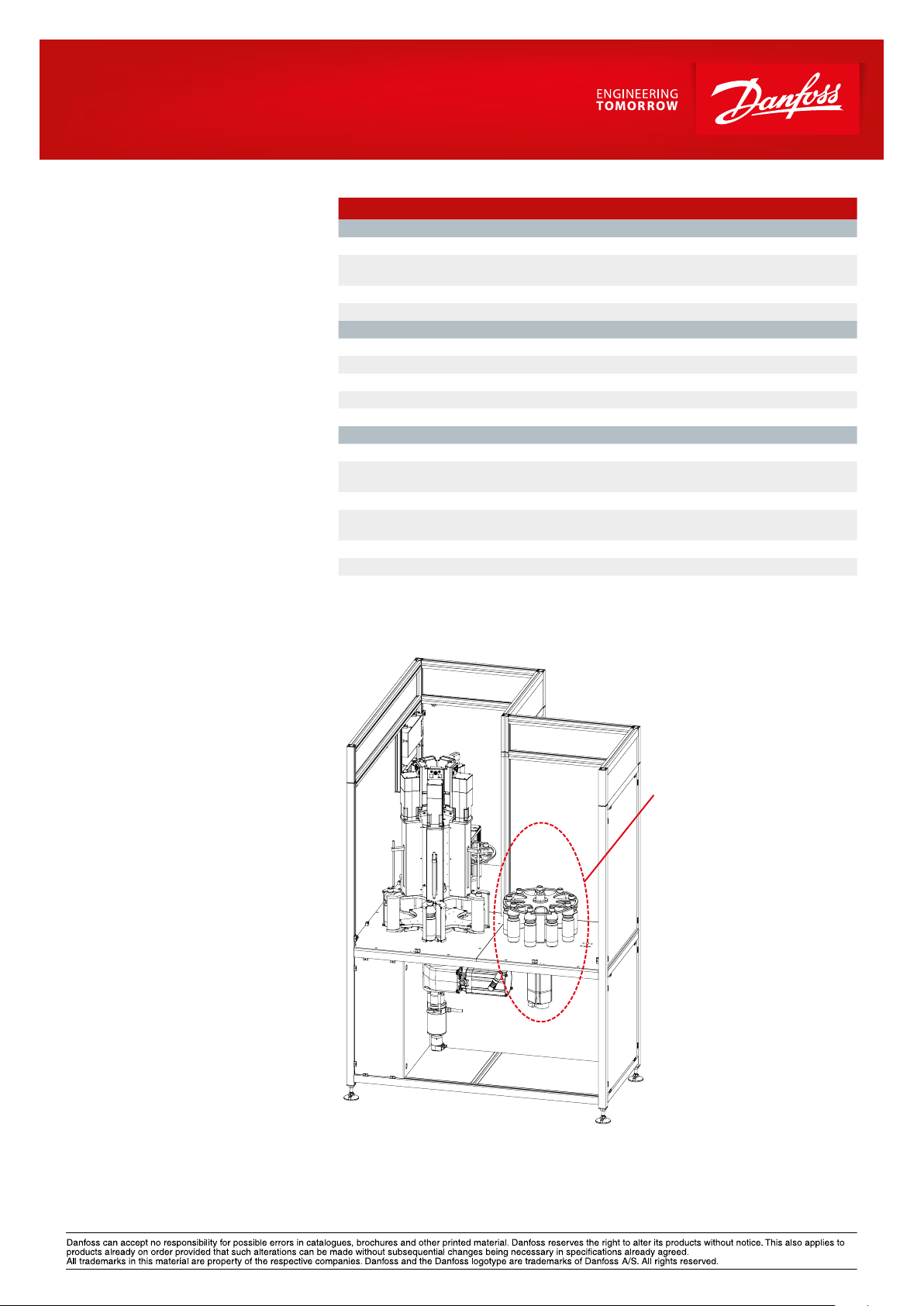
A system built around standard
components is also benecial when
application support is needed.
Finding local help and support is easy.
Customers already acquainted with
VLT drives will benet from working
with a known platform. New users will
quickly see why Danfoss is a leading
global supplier of drive solutions.
VLT® AutomationDrive
Power range
n 3 x 200-240 V, 0.25-37 kW
n 3 x 380-480/500, 0.37-800 kW
n 3 x 525-600 V, 0.75-75 kW
n 3 x 535-690 V, 37-1200 kW
Motion Control MCO 305
benets
n Accurate and dynamic motion
control
n Synchronisation (electronic shaft)
n Positioning and electronic cam
control
n Monitoring and error handling
n Limited jerk function
n Programmable logical functions
VLT® AutomationDrive
Feature Benet
Reliable Maximum uptime
Ambient temperature 50 °C without derating Less need for cooling or oversizing
Available in IP 00, 20, 21, 54, 55 and 66
enclosures
Resistant to wear and tear Low lifetime cost
Back-channel cooling for frame D, E and F Prolonged lifetime of electronics
User-friendly Saves commissioning and operating costs
Plug-and-play technology Easy upgrade and change over
Awarded control panel User-friendly
Intuitive VLT® interface Saves time
Pluggable cage clamp connectors Easy connection
Exchangeable languages User-friendly
Intelligent Design exibility
Intelligent warning systems Warning before controlled stop
Safe stop
Advanced plug-in features Easy commissioning
STO: Safe Torque O (IEC 61800-5-2)
Intelligent heat management Excess heat eectively removed
Suitable for harsh and wash down areas
Safety cat. 3 (EN 954-1), PL d (ISO 13849-1),
Stop cat. 0 (EN 60204-1)
SIL 2 (IEC 61508)
SIL CL 2 (IEC 62061)
Synchronising functions
n Speed synchronising
n Position synchronising
n Position synchronising with marker
corrections
n Electronic cam with dynamic curve
calculations
Positioning functions
n Absolute positioning
n Relative positioning
n Touch-probe positioning
Encoder feedback support
n SSI
n Incremental
n Encoder output (virtual master)
n Resolver (with B-option)
n Sine-cosine encoder
n CANopen encoder
n Hiperface® encoder
n EnDat® encoder
Direct torque control
n
Accurate application control
n
No gearbox with power loss
n
No mechanical backlash
Danfoss VLT Drives, Ulsnaes 1, DK-6300 Graasten, Denmark, Tel. +45 74 88 22 22, Fax +45 74 65 25 80
www.danfoss.com/drives, E-mail: info@danfoss.com
DKDD.PM.303.A2.02 VLT® is a trademark of Danfoss A/S Produced by PE-MSMBM 2014.09