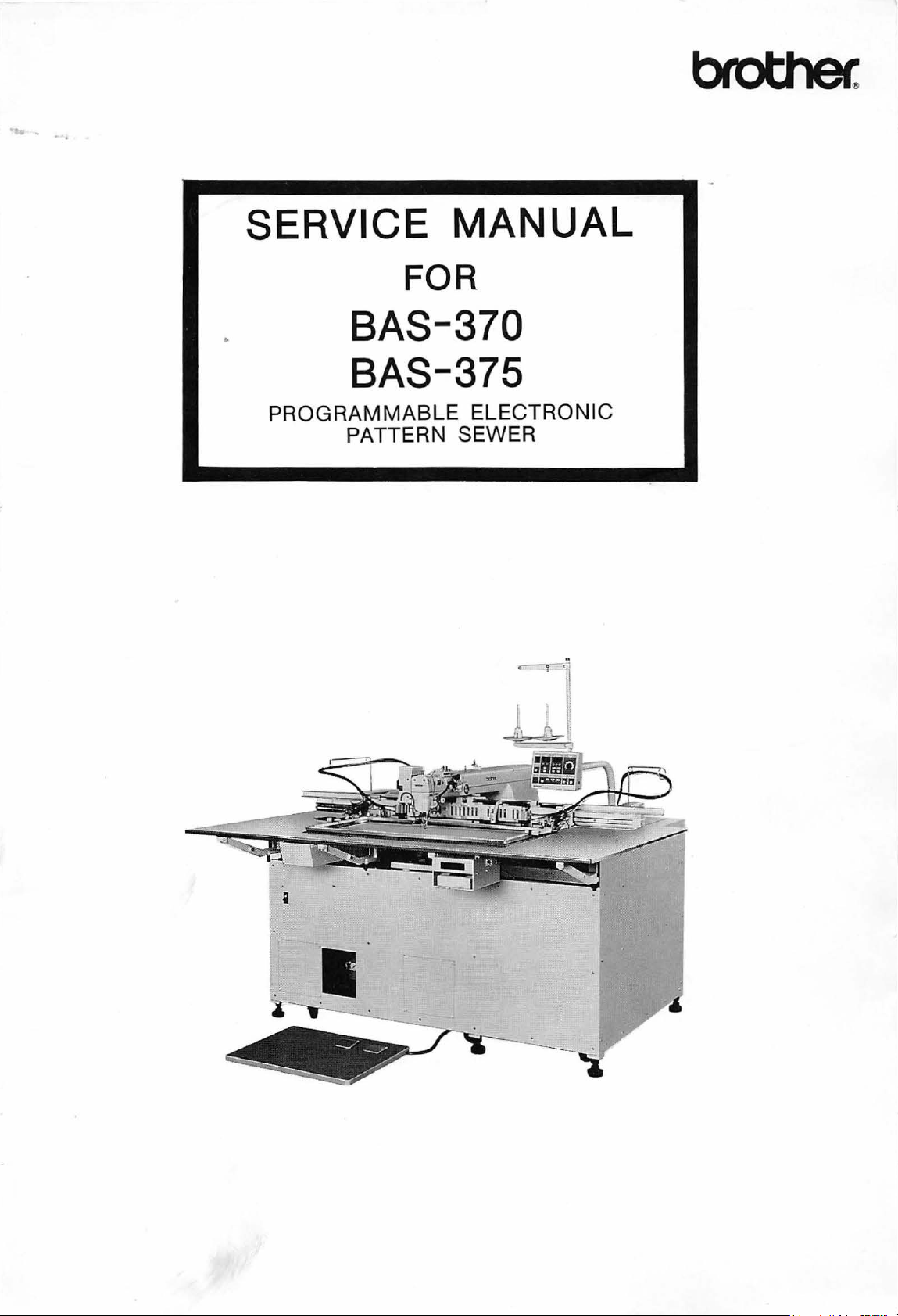
SERVICE MANUAL
FOR
•
BAS-370
BAS-375
PROGRAMMABLE
PATTERN SEWER
ELECTRONIC
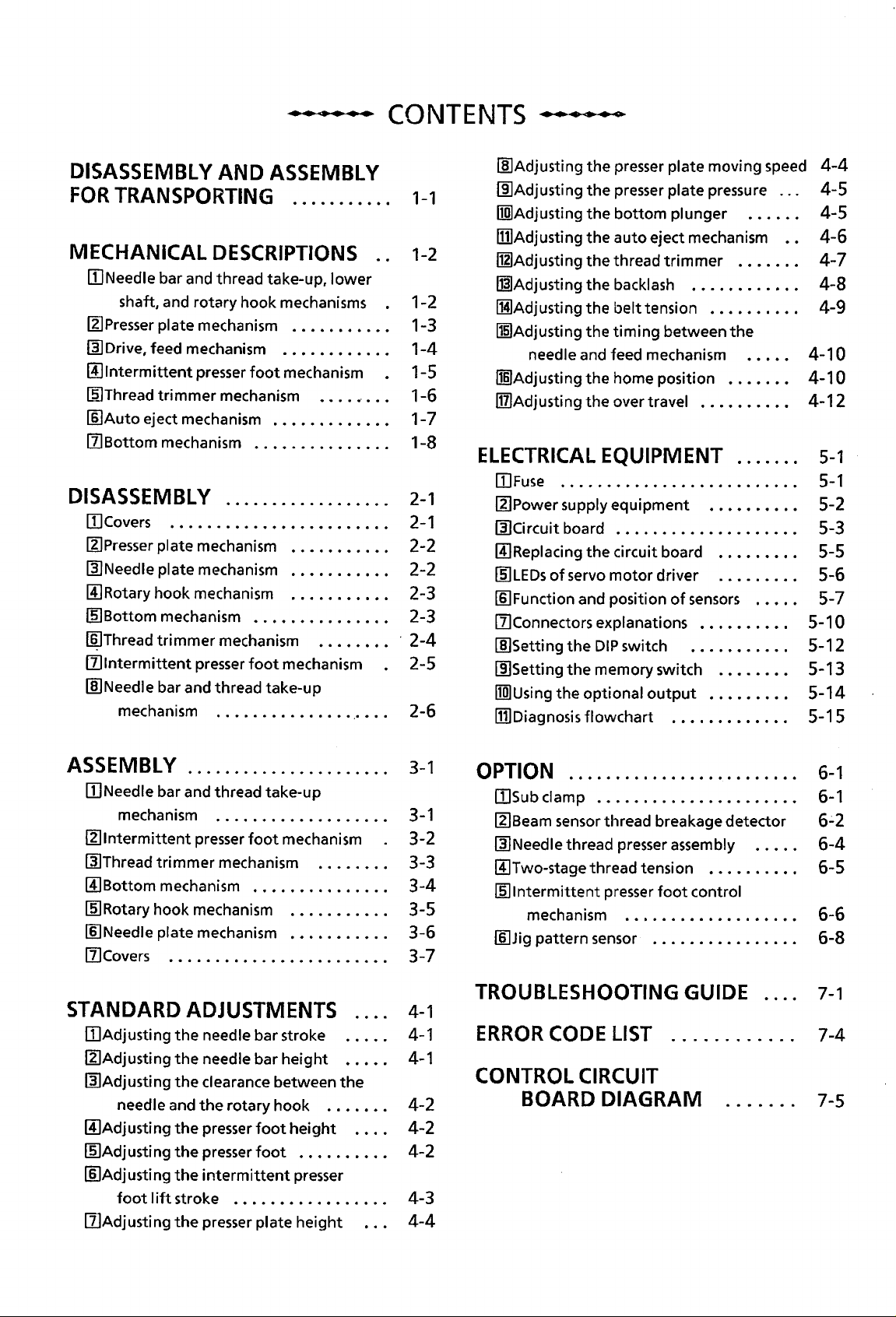
••
••••
CONTENTS
•••••o
DISASSEMBLY
FOR
TRANSPORTING
MECHANICAL
[]Needle
[Z]Presser
[ID
Drive, feed mechanism
!!]Intermittent
[§]Thread
[§]Auto eject mechanism
11]
Bottom mechanism
bar and thread take-up,
shaft, and rotary hook mechanisms •
plate mechanism
trimmer
DISASSEMBLY
[]]Covers
lZJPresser
~Needle
[!]Rotary hook mechanism
liD
Bottom mechanism
liD
Thread
11]
Intermittent
liD
Needle bar and thread take-up
mechanism
•••••.•••..••••.•••..•.•
plate mechanism
plate mechanism
trimmer
AND
DESCRIPTIONS
presser
mechanism
.................
mechanism
presser
................
ASSEMBLY
..........
lower
.....••••••
..•.•••••..•
foot
mechanism
••..•..•.
•••••.•.•..••
•.••••.••••.•..
••••••••.•.
••••..•.••.
......••••.
•.•••••..••.•..
foot
mechanism
..
• ...
.
.
1-1
1-2
1-2
1-3
1-4
1-5
1-6
1-7
1-8
2-1
2-1
2-2
2-2
2-3
2-3
. 2-4
2-5
2-6
!IDAdjusting
~Adjusting
lrn!Adjusting
lll!Adjusting
~Adjusting
~Adjusting
IM!Adjusting
ll§lAdjusting
needle and feed mechanism
li§JAdjusting
lll]Adjusting
the
presser plate moving speed
the
presser plate pressure
the
bottom
the
auto eject mechanism
the
thread
the
backlash
the
belt
the
timing
the
home position
the
over travel
plunger
trimmer
tension
between
••.••••.••••
••••••.•••
••.•••••••
ELECTRICAL EQUIPMENT
[]]Fuse
lZJPower supply equipment
@!Circuit board
[!]Replacing
liD
LEDs
liD
Function and position
ll]Connectors explanations
[IDSetti ng
~Setting
lrnl
Using
lll1
Diagnosis
••.••••••.••••.•••.••••.••
••••••.•••••••••••••
the
circuit board
of
servo
motor
the
DIP
the
memory switch
the
optional
flowchart
driver
of
switch
output
•••.••••••••.
••••••••••
sensors
••.•••••••
•.•.•••.•..
•••••••••
••••••
•••••••
the
•.••.••
......
•••••••••
..•..•.••
.••••
•••.••••
...
••
4-10
4-10
4-12
.
5-10
5-12
5-13
5-14
5-15
4-4
4-5
4-5
4-6
4-7
4-8
4-9
5-1
5-1
5-2
5-3
5-5
5-6
5-7
ASSEMBLY
[]]Needle bar and thread take-up
mechanism
[Z]Intermittent presser
[IDThread
[!]Bottom
[ID
Rotary hook mechanism
liD
Needle plate mechanism
llJCovers
.....................
••.•••••••••••.••.•
foot
trimmer
mechanism
....•....•..•...•....••.
mechanism
•.••.••..••.••.
mechanism
...•.••.
•••..••.•..
••...•..•..
STANDARD ADJUSTMENTS . . . .
[]]Adjusting
~Adjusting
[IDAdjusting
needle and
[!]Adjusting
i:IDAdjusting
[§]Adjusting
foot
[l]Adjusting
the
needle bar stroke • • • • .
the
needle bar
the
clearance between
the
rotary hook . . • • • • • 4-2
the
presser
the
presser
the
intermittent
lift
stroke • • • . • • • • • . • . • . . . . 4-3
the
presser plate
height
foot
height
foot
• • • . • • • • . . 4-2
presser
height
• . • • .
the
• • . • 4-2
.
3-1
3-1
3-2
3-3
3-4
3-5
3-6
OPTION
[i]Sub clamp
[Z]Beam sensor thread breakage detector
[IDNeedle thread presser assembly
[!]Two-stage thread tension
liD
Intermittent
IIDJig
................
•••.•.•.••.•••••••••••
presser
mechanism
pattern sensor
·~·
••••.•.••.
foot
control
••...•.••••••.•••••
••••••••••••••••
......
•••••
6-1
.
6-1
6.:.2
6-4
6-5
6-6
6-8
3-7
TROUBLESHOOTING GUIDE . . . . 7-1
4-1
4-1
ERROR
CODE LIST
7-4
4-1
CONTROL CIRCUIT
BOARD
DIAGRAM
7-5
4-4
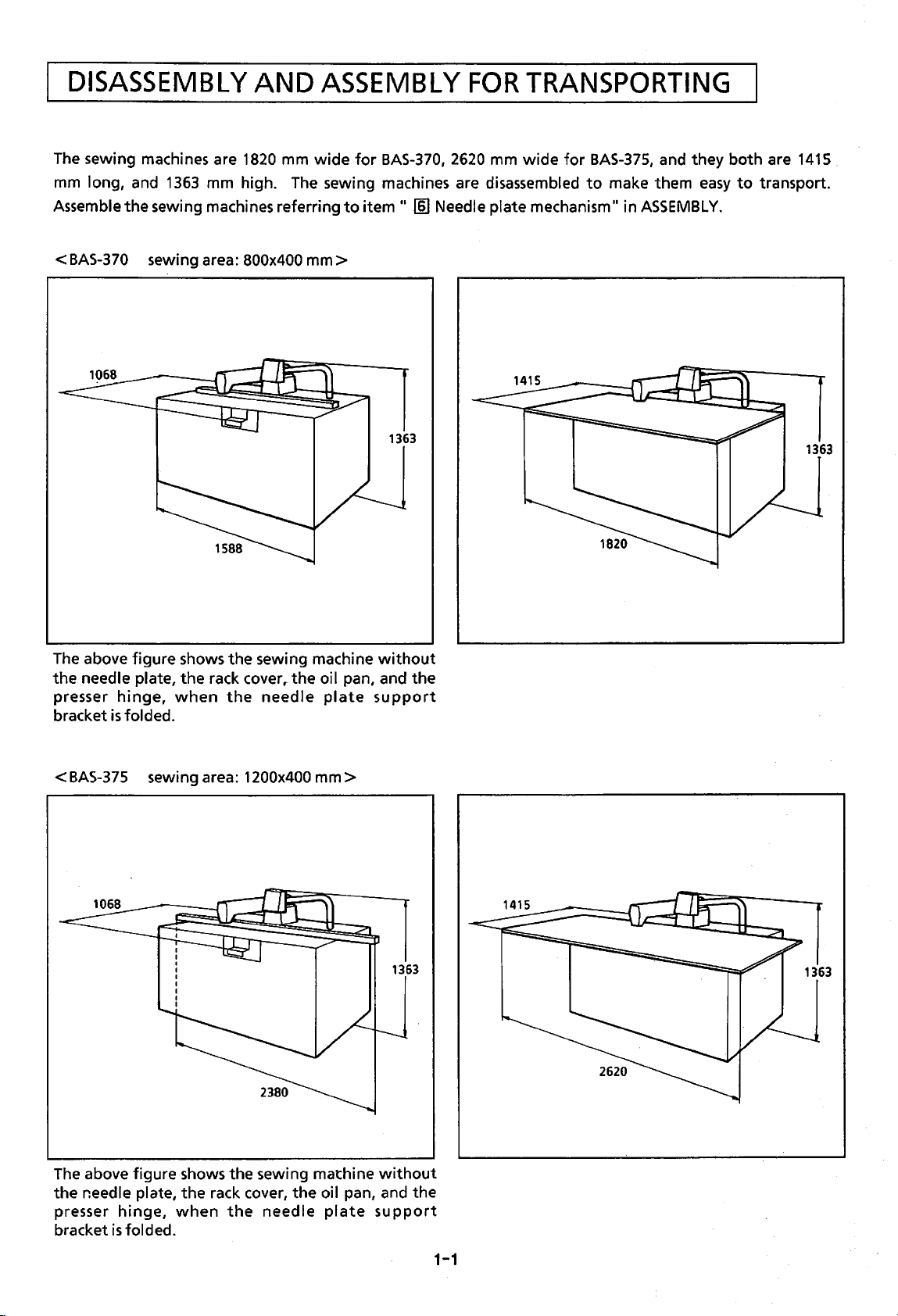
DISASSEMBLY
The
sewing machines are
mm
long,
and
1363
mm
Assemble
the
sewing machines referring
AND
1820
mm
high.
ASSEMBLY
wide
for
BAS-370,
The
sewing machines are disassembled
to
item
..
[§] Needle plate mechanism" in
FOR
2620
mm
TRANSPORTING
wide
for
BAS-375,
to
make them
and they both are
easy
to
ASSEMBLY.
1415
transport.
<BAS-370 sewing area: 800x400
The
above figure shows
the
needle plate, the rack
presser
bracket
hinge,
is
folded.
when
the
sewing machine
cover,.
the
needle
mm>
the
oil pan, and
plate
without
the
support
<BAS-375 sewing area: 1200x400
The
above figure shows the sewing mathine
the needle plate, the rack cover, the oil pan, and the
presser
bracket
hinge,
is
folded.
when
the
needle
mm>
plate
without
support
1-1
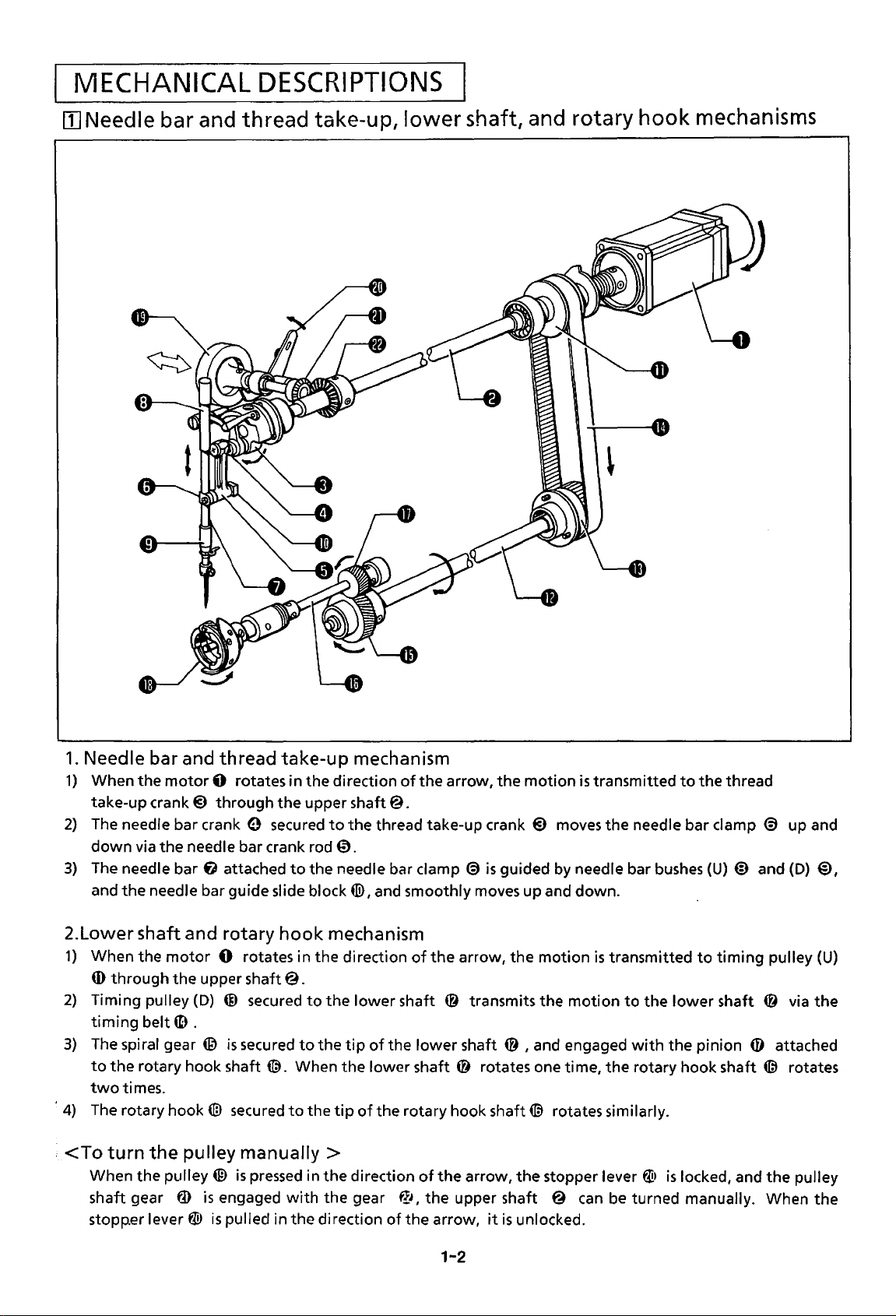
MECHANICAL
II1
Needle bar and thread take-up,
DESCRIPTIONS
lower
shaft, and rotary
hook
mechanisms
1.
Needle bar and
1)
When the
take-up crank@)
2)
The
down
3)
The needle bar
and
motor
needle bar crank e secured
via
the
the
needle bar guide slide
thread
0 rotates in the direction
through
needle bar crank rod
fl
attached
2.Lower shaft and rotary
1)
When the
ID
through
2)
Timing pulley
timing
3)
The
to
the
two
4)
The
,
<To
turn
When
shaft gear m
stopp.er lever W
motor
belt m .
spiral gear @
rotary hook shaft
times.
rotary
hook@
the
the
pulley®
0 rotates in
the
upper shaft@.
(D)
pulley manually >
is
engaged
is
@ secured
is
secured
secured
is
pulled in
take-up
the
to
hook
@.
to
pressed
with
the
mechanism
of
the arrow,
upper shaft@.
to
the
thread take-up crank
0.
the needle bar clamp @
block@,
and smoothly moves up and down.
mechanism
the
direction
to
the
lower
to
the
tip
When the
the
tip
of
in
the
direction
the gear
direction
of
the
shaft @ transmits the
of
the
lower
lower
shaft @ rotates
the rotary hook shaft@ rotates similarly.
of
the
fEJ,
the
of
the arrow,
the
motion
@)
is
guided by needle bar bushes
arrow,
shaft @ , and engaged
upper shaft @
arrow,
it
is
the
the
unlocked.
is
transmitted
moves
motion
onetime,
stopper lever
the
is
motion
the
can
to
the
thread
needle bar clamp @ up and
(U)
@ and
transmitted
to
the
with
rotary hook shaft @ rotates
@1
be
turned manually. When
to
timing
lower
the
is
shaft @ via the
pinion
locked, and
pulley
aJ
attached
the
(D)
@,
(U)
pulley
the
1-2
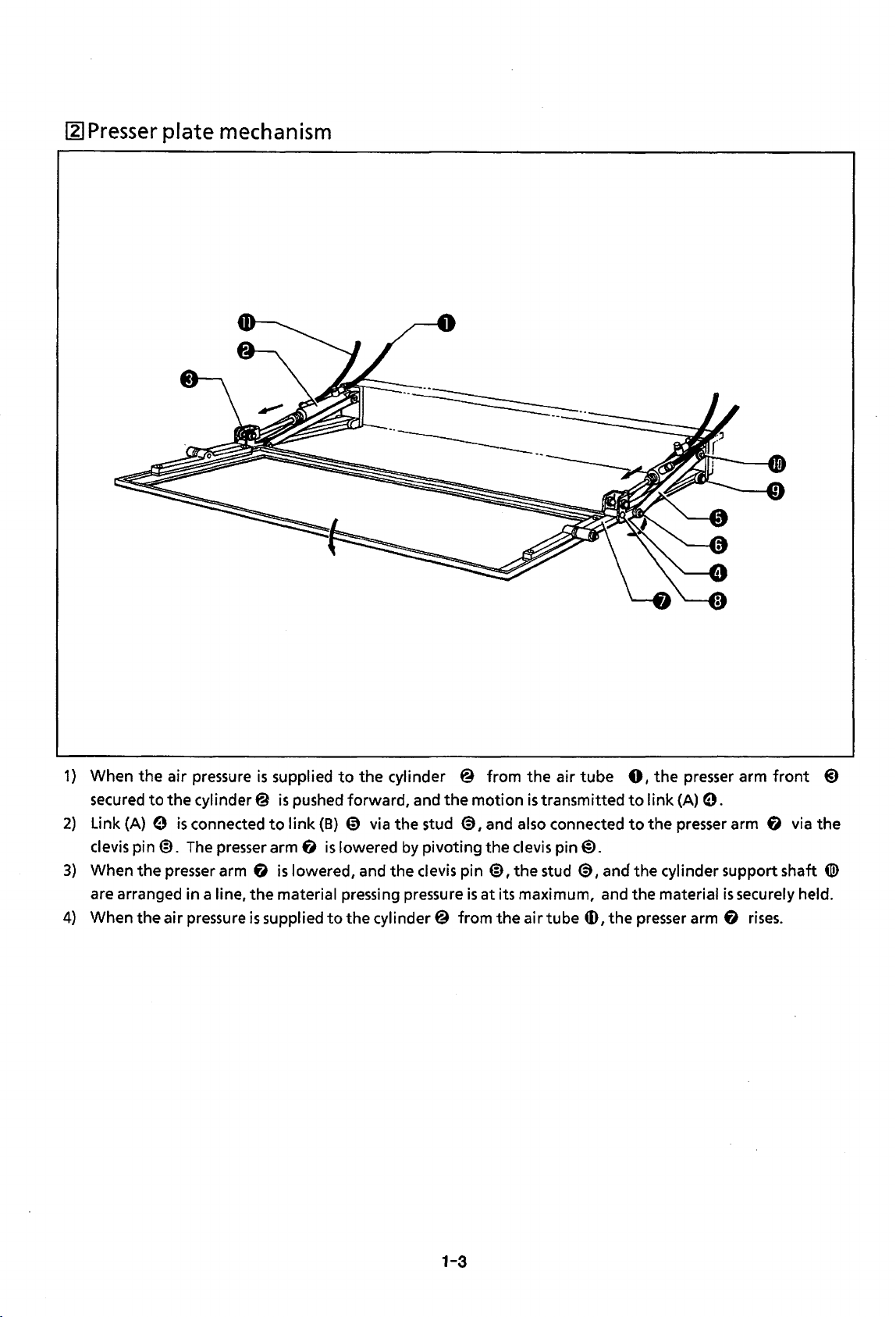
~Presser
plate
mechanism
1)
When
secured
2)
Link {A) 0
clevis
3)
When
are arranged in a line,
4)
When
the
air
to
the
is
pin@.
the
presser arm 6
the
air pressure
pressure
cylinder@
connected
The
presser arm 6
is
supplied
is
to
link
is
the
material pressing pressure
is
supplied
to
the
cylinder @ from
pushed forward, and
(B)
0 via the stud @),and also connected
is
lowered by pivoting the clevis pin@).
lowered, and
to
the
the
cylinder@ from
the
motion
clevis pin
is
the
air
tube
is
transmitted
@,the
at
stud
@,and
its maximum, and the material
the
air
tube
ID,
0,
the
to
link
to
the
the
cylinder support shaft
the
presser arm 6
presser arm
{A)
0.
presser arm 6 via
is
front
securely held.
rises.
@)
the
«!)
1-3
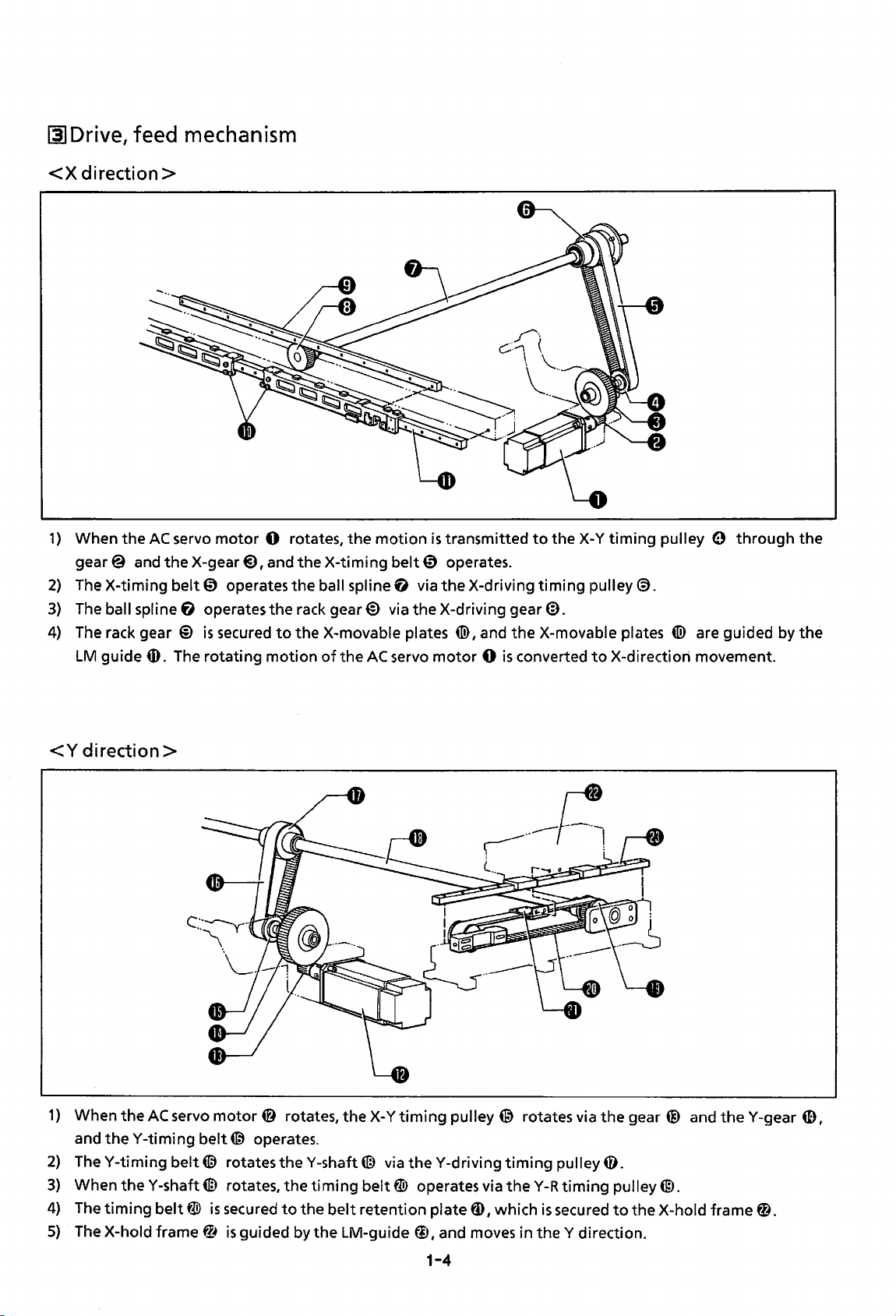
@]Drive, feed mechanism
<X
direction>
1)
When
gear@ and
2)
The X-timing
3)
The ball spline 6 operates
4)
The rack gear
the
AC
servo
the
X-gear@, and
belt
0 operates
@>
is
LM
guide ill. The rotating
motor
secured
0 rotates,
the
to
motion
the
motion
the
X-timing belt 0 operates.
the
ball spline
rack gear@) via the X-driving gear@.
the
X-movable plates ([!),and
of
the
AC
f)
via
servo
is
transmitted
the
X-driving
motor 0 is
to
timing
the
X-movable plates
converted
the
X-Y
timing
pulley@}.
to
X-directioli movement.
pulley 9
([!)
are guided by
through
the
the
<Y
direction>
1)
When
the
and
theY-timing
2)
TheY-timing
3)
When
theY-shaft@
4)
The
timing
5)
The X-hold frame
AC
belt
servo
belt@
belt@
tiD
fh
motor@
operates.
rotates
rotates,
is
secured
is
guided by
rotates, the X-Y
theY-shaft
the
timing
to
the
the
(ID
belt@) operates via
belt
retention plate
LM-guide@,
timing
via
theY-driving
and moves in
r---
L
..
pulley@
fD,
which
.-h
rotates via
timing
the
pulley
Y-R
is
secured
theY
timing
direction.
:
the
gear@
0).
pulley@.
to
the X-hold frame
and
theY-gear
ID,
0.
1-4
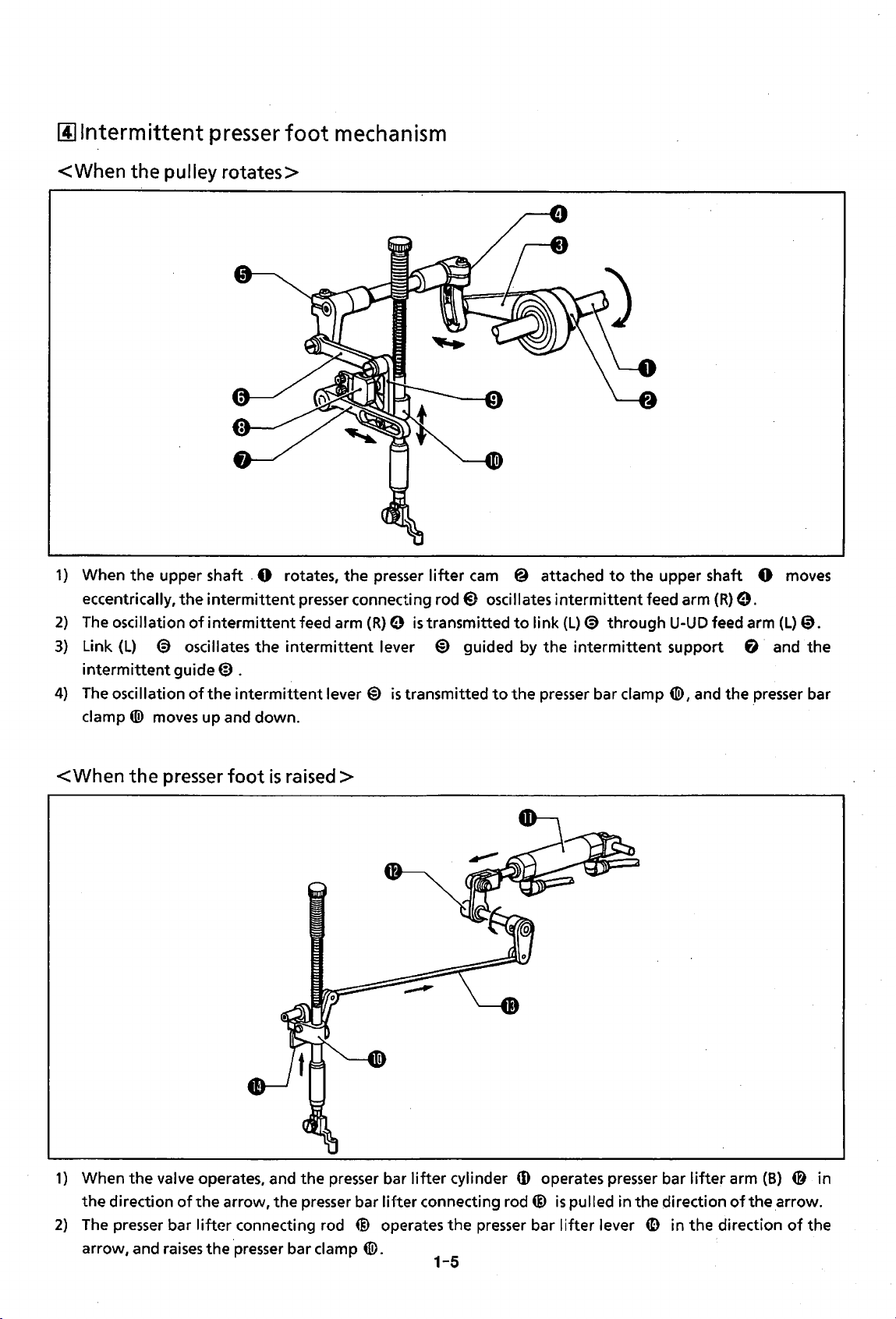
II)
Intermittent
presser
foot
mechanism
<When
1)
When
eccentrically,
2)
The
oscillation
3)
Link
intermittent
4)
The
oscillation
clamp
the
pulley
the
upper shaft . 0 rotates, the
(L)
€)
guide@) .
((i)
moves up and down.
rotates>
the
intermittent
of
intermittent
oscillates
of
the
the
intermittent
presser
feed arm (R) 9
intermittent
connecting
lever@
presser
lever @ guided by
lifter
rod@
is
transmitted
is
transmitted
cam
oscillates
to
the
@ attached
intermittent
to
link
(L)@)
the
intermittent
presser
bar clamp
to
the upper shaft 0 moves
feed arm
through
(R)
0.
U-UD
feed arm
support & · and
((i),
and the presser bar
(L)
0.
the
<When
1)
When the valve operates, and
the direction
2)
The
arrow, and
the
presser
presser
of
the
bar
lifter
raises
the
foot
arrow, the
·presser
is
raised>
the
presser
presser
connecting rod @ operates the
bar clamp ®.
bar
bar
lifter
cylinder (D operates
lifter
connecting rod@
1-5
presser
presser
is
pulled in the direction
bar
lifter
lever
bar
lifter
ID
in the direction
arm
(B)
of
the arrow.
@ in
of
the
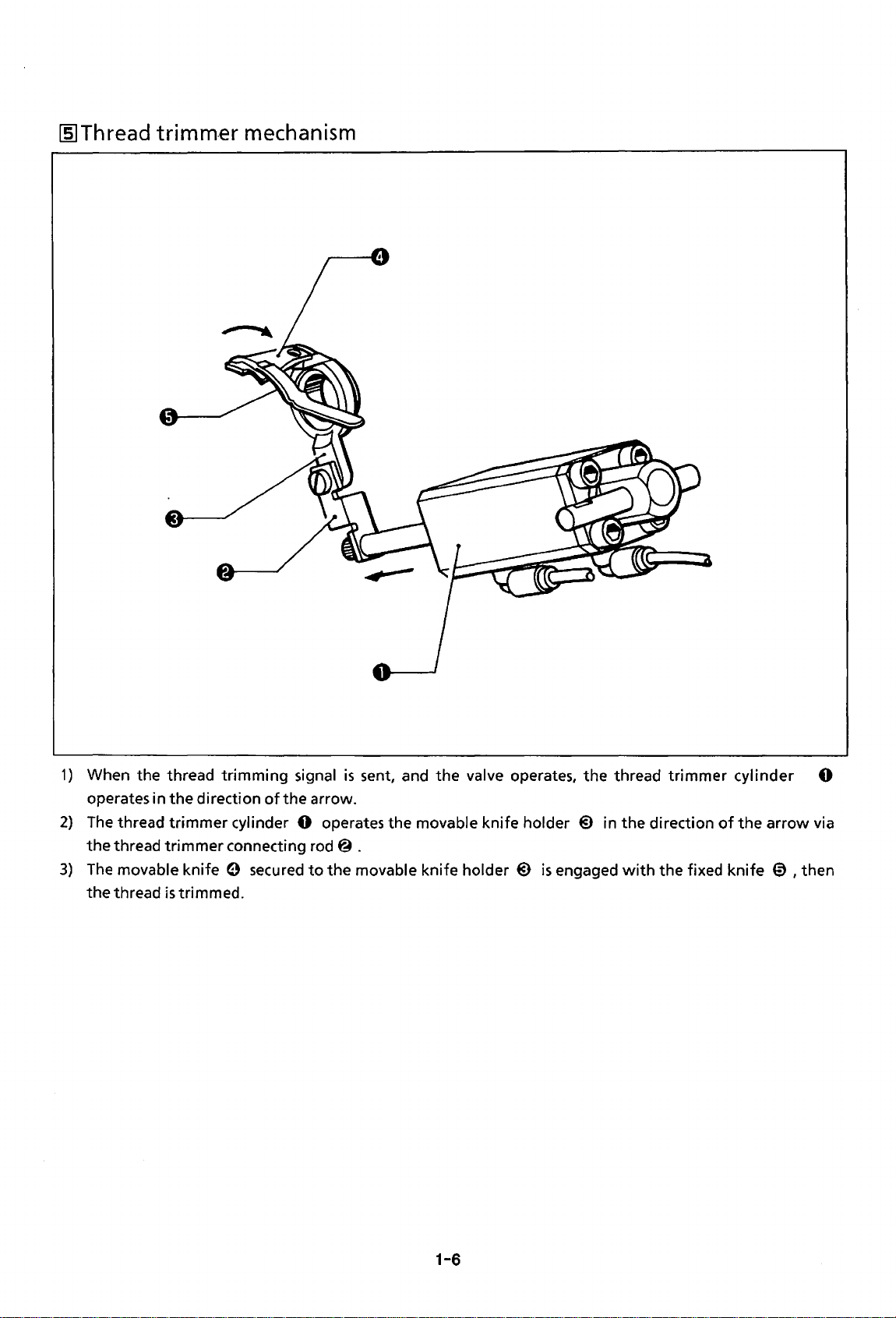
~Thread
trimm.er mechanism
1)
When the thread trimming signal
operates in the direction
2)
The
the thread
3)
The
the thread
thread
movable knife e secured
trimmer
trimmer
is
trimmed.
of
cylinder 0 operates the movable knife holder
connecting rod@ .
is
sent, and the valve operates,
the arrow.
to
the movable knife holder
@)
@)
is
engaged
the
thread
in the direction
with
the fixed knife 0 , then
trimmer
of
cylinder 0
the arrow via
1-6
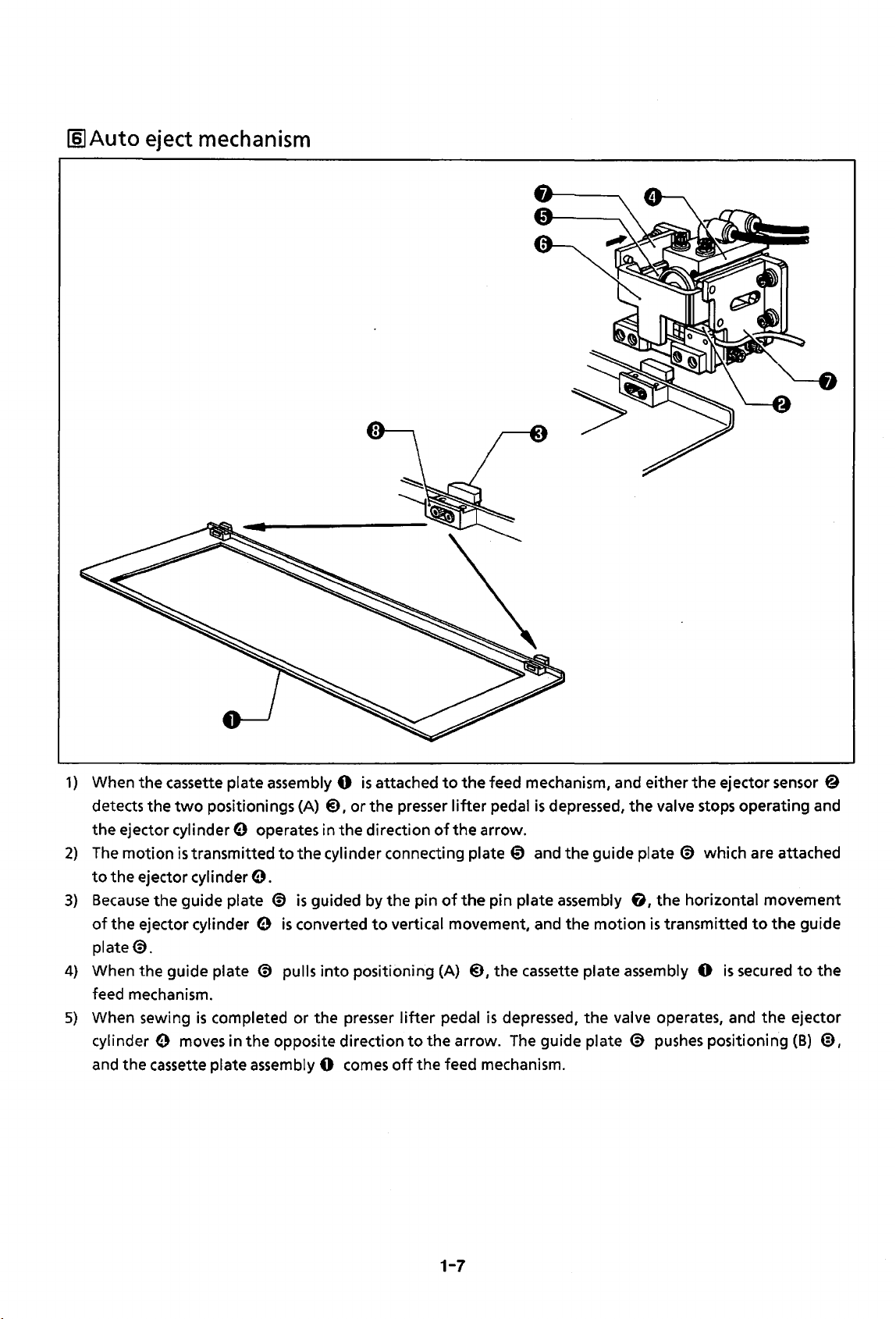
[§]Auto eject mechanism
1)
When
detects the
the
2)
The motion
to
3)
of
4) When the guide plate ® pulls
feed mechanism.
5)
When sewing
cylinder 9 moves in
and
the
cassette plate assembly 0
two
positionings {A) @),or
ejector cylinder 9 operates in
is
transmitted
the
ejector cylinder
Because
plate@.
the guide plate ®
the
ejector cylinder 9
the
cassette plate assembly 0 comes
is
e.
completed
the
to
the
is
is
converted
or
opposite direction
is
attached
the
the
direction
cylinder connecting plate 0 and
guided by
into
the presser
the
to
vertical movement, and the
positioning {A) @),the cassette plate assembly 0
off
to
the
presser
lifter
lifter
of
the
pin
of
the
pedal
to
the
arrow. The guide plate ® pushes positionin·g
the
feed mechanism.
feed mechanism, and either
pedal
is
depressed,
arrow.
the
guide plate @ which are attached
pin plate assembly
motion
is
depressed,
the
valve operates, and
the
ejector sensor @
the
valve stops operating and
fi,
the
horizontal movement
is
transmitted
to
is
secured
the
the
guide
to
the
ejector
{B)
@,
1-7
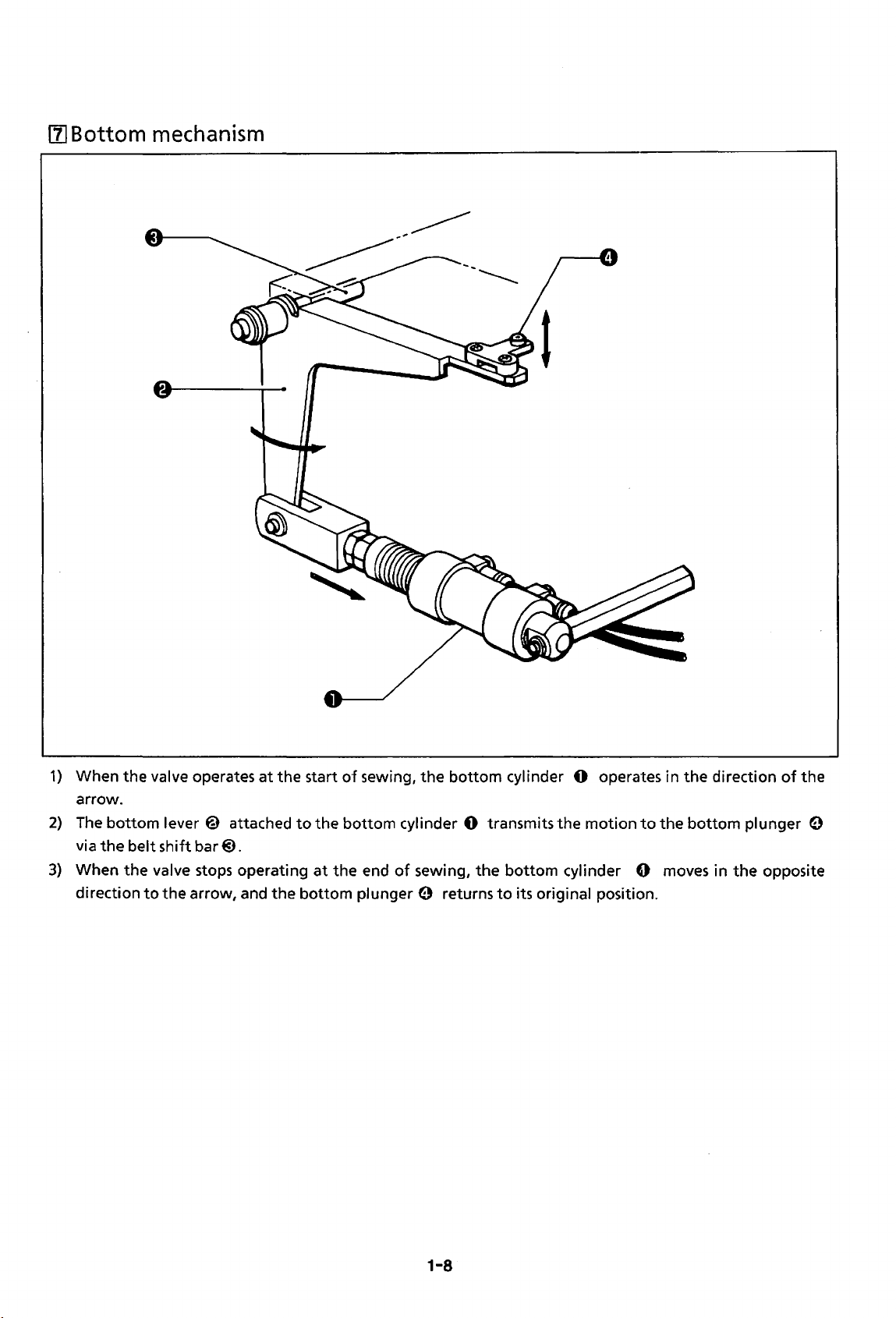
11]
Bottom
mechanism
1)
When
arrow.
2)
The
via
3)
When
direction
the
bottom
the
belt shift
the
valve operates
lever @ attached
bar@.
valve stops operating
to
the
arrow, and
at
the
the
start
to
the
at
the
bottom
of
sewing,
bottom
end
plunger 0 returns
the
bottom
cylinder 0 transmits
of
sewing,
cylinder 0 operates in
the
motion
the
bottom
to
its original position.
cylinder 0 moves in
to
the
the
direction
bottom
of
plunger 0
the
opposite
the
1-8
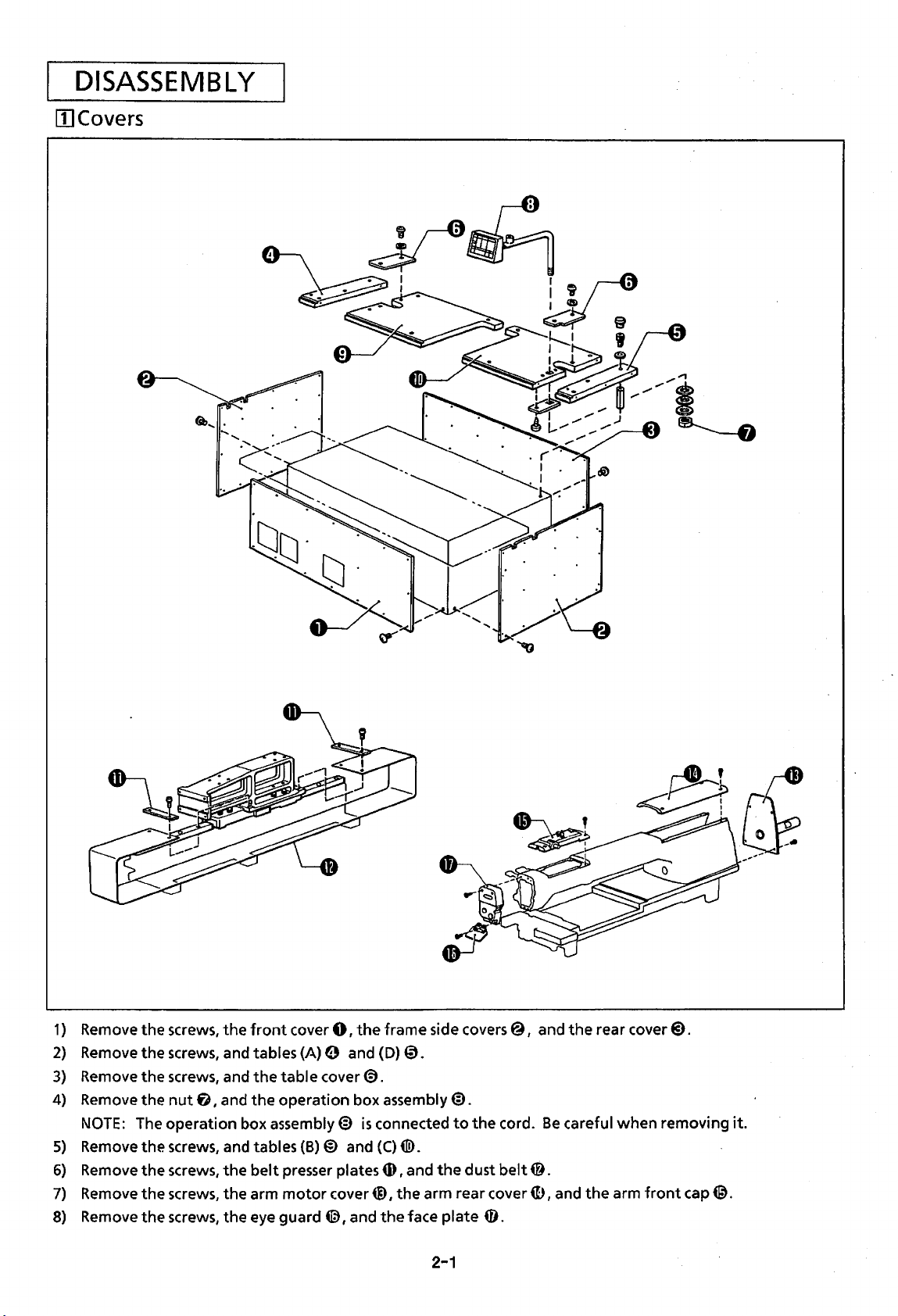
DISASSEMBLY
II]
Covers
1)
Remove the screws,
2)
Remove the screws, and tables {A) 0 and
3)
Remove the screws, and
4)
Remove the
NOTE:
5)
Remove
6)
Remove
7)
Remove
8)
Remove
nut
The operation box assembly@
the
screws, and tables {B)@ and
the
screws, the
the
screws, the arm
the
screws, the eye
6,
the
and
front
cover
0,
the
frame side covers@, and
(D)
0.
the
table
cover®.
the
operation box assembly@).
is
connected
{C)
«i>.
belt
presser plates
motor
guard@,
cover@, the arm rear cover
and
Q),
the
to
and
the
dust
face plate
the
4D.
cord.
belt@.
ID,
Be
careful when removing
and
2-1
the
rear cover@).
the
arm
front
cap
it.
{G).
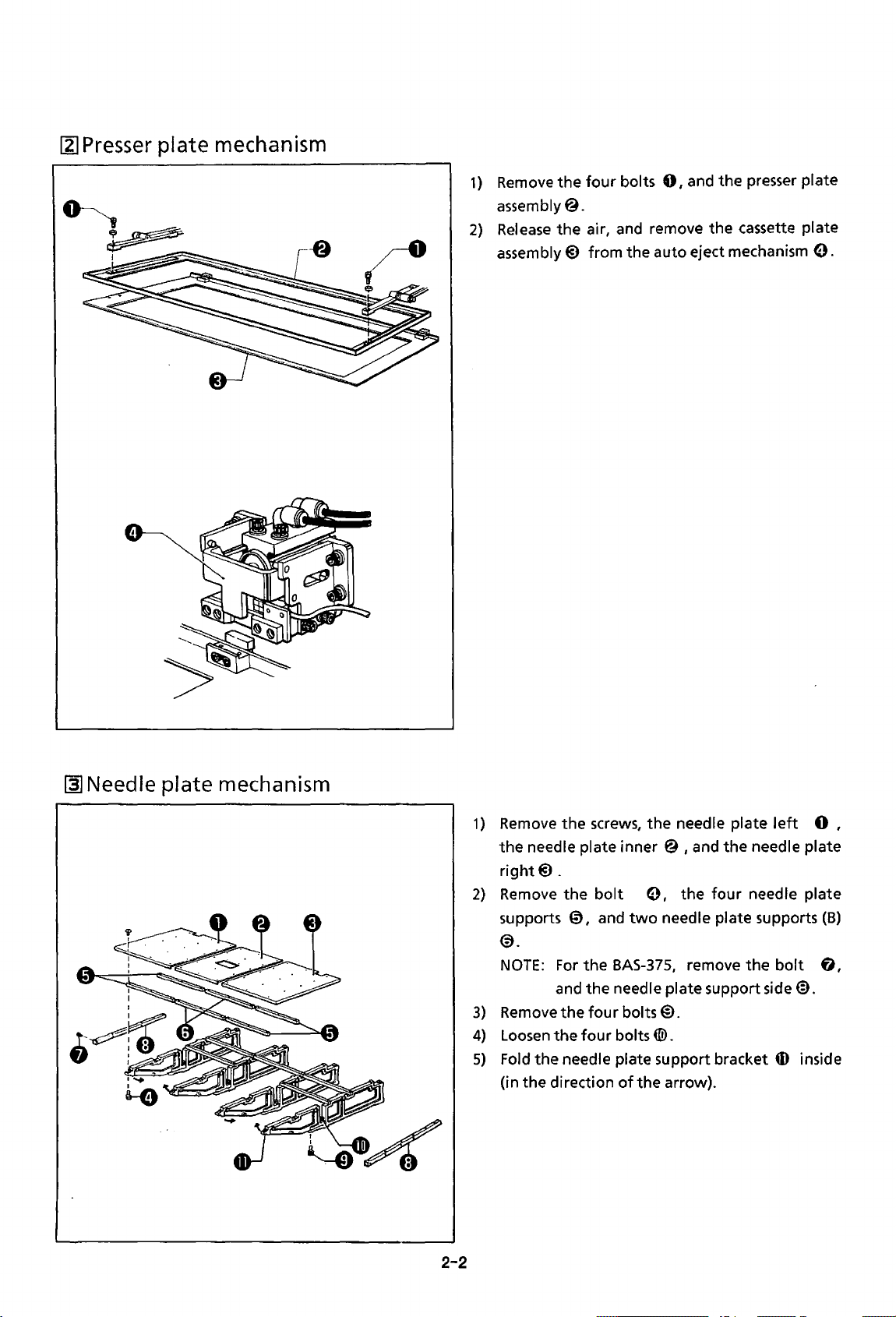
~Presser
plate
mechanism
1)
Remove
assembly@.
2)
Release
assembly@ from
the
the
four
bolts
0,
and
the
presser plate
air, and remove the cassette plate
the
auto eject mechanism e.
@1
Needle
plate
mechanism
1)
Remove the screws,
the
needle plate inner @ , and
right@.
2)
Remove
supports
@_
NOTE:
3)
Remove
4)
5)
Fold
(in
Loosen
the
€)
For
and
the
the
the
needle plate support bracket
the
direction
the
needle plate
the
bolt
and
1
the
the
four
four
9,
the
four
two
needle plate supports
BAS-375,
needle plate support side@.
bolts@.
bolts®.
of
the arrow).
remove the
left
0 ,
needle plate
needle plate
(B)
bolt
f)
ID
inside
1
2-2
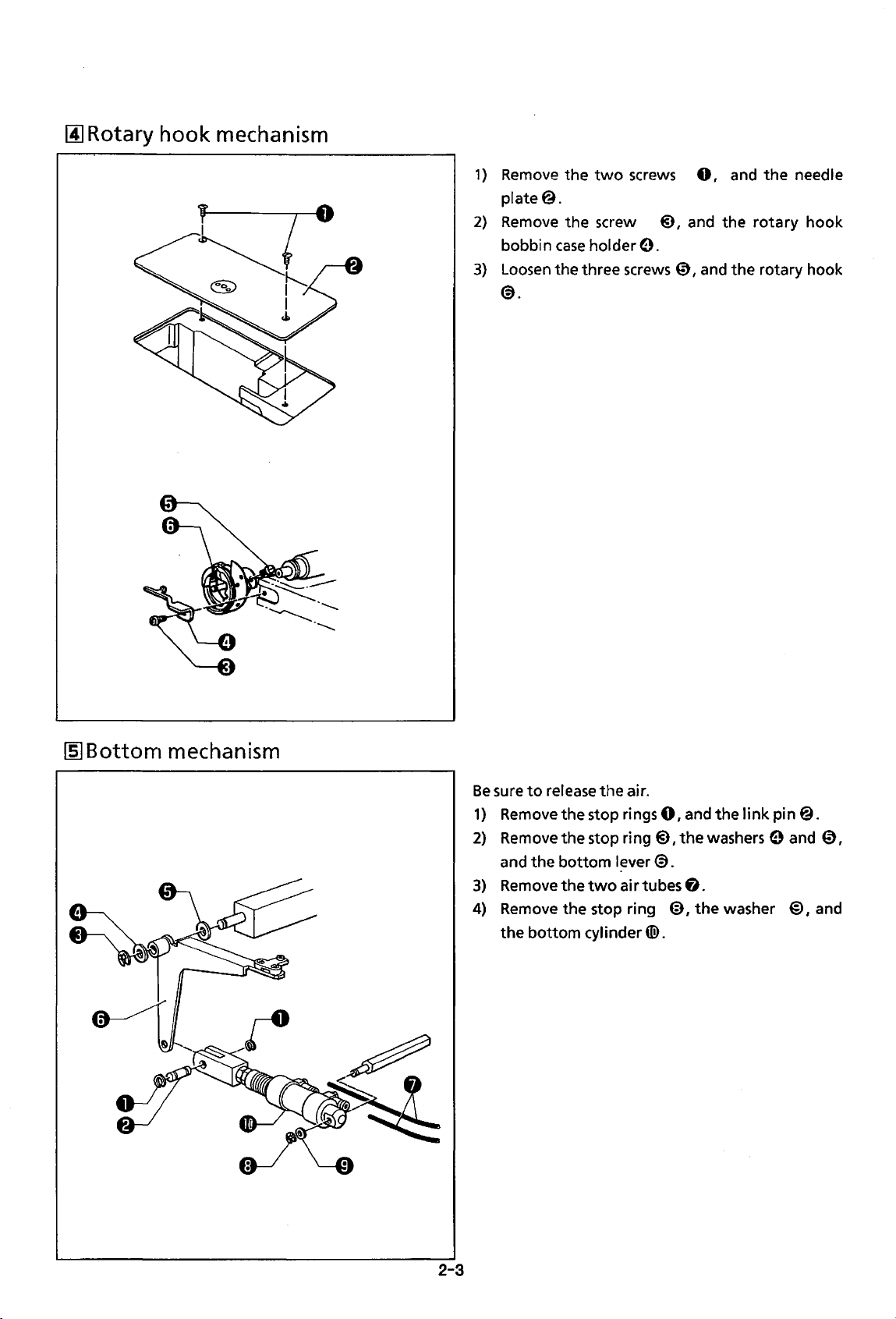
[!]Rotary
hook
mechanism
1)
2)
3)
Remove
plate@.
Remove
bobbin
Loosen
@.
the
two
the screw
case
holderS.
the three
screws
@),
screws
0,
and the needle
and the rotary hook
0,
and
the
rotary hook
~
Bottorrt
mechanism
Be
sure
to
release
1)
Remove
2)
Remove
and the bottom lever
3)
Remove
4)
Remove
the
the stop rings
the stop ring@),
the
two
the stop ring
bottom
cylinder®.
the
air.
0.
air tubes G.
0,
and the link
the
washers 0 and
@,the
washer
pin@.
@,
0,
and
2-3
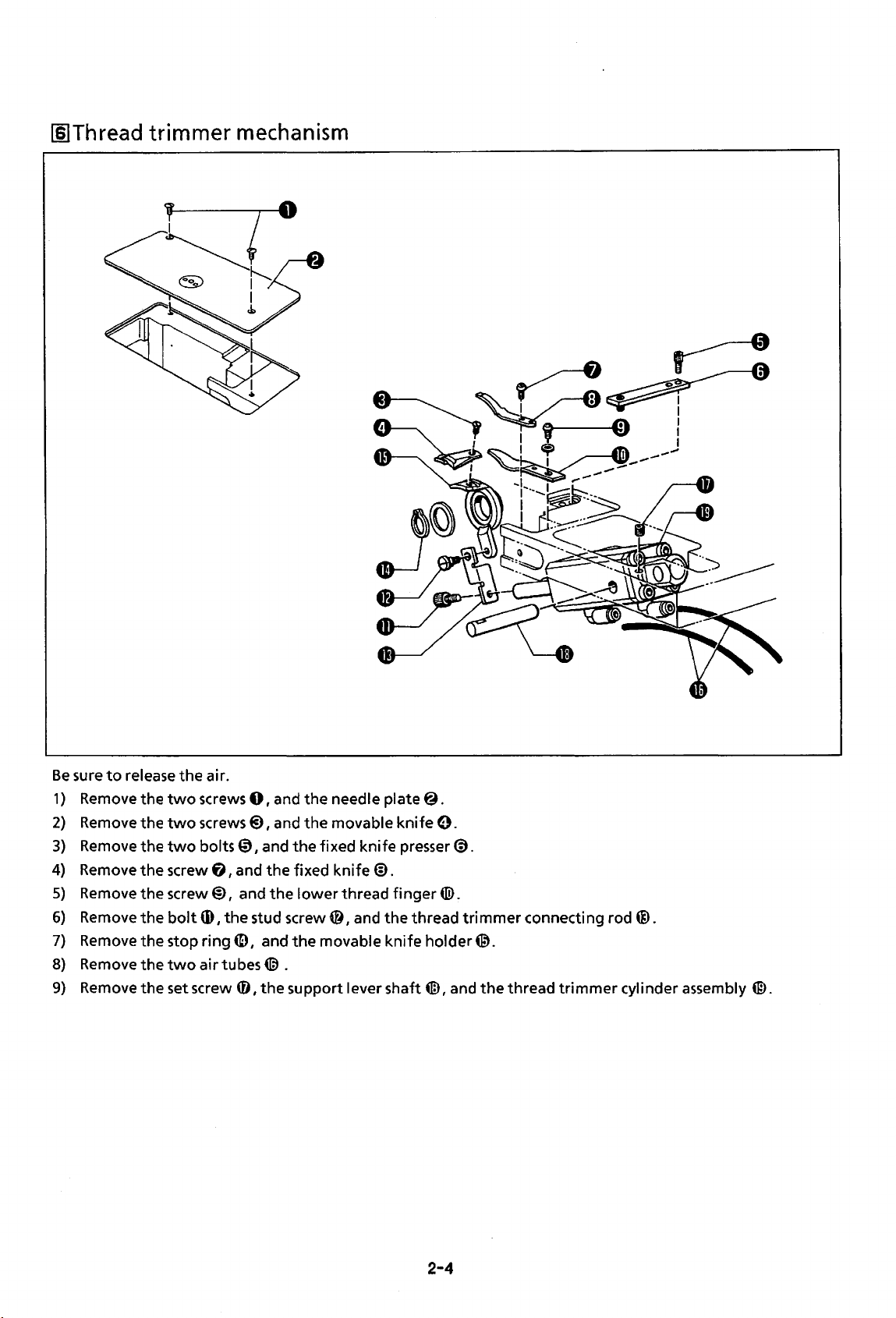
[§]Thread
trimmer
mechanism
Be
sure
to
release
1)
Remove the
2)
Remove the
3)
Remove the
4)
Remove
5)
Remove
6)
Remove
7)
Remove the stop ring
8)
Remove the
9)
Remove the set screw Q),
the
two
two
two
the
screw
the
screw@, and
the
bolt
two
air.
screws
screws@), and
bolts@,
ID,
air tubes@ .
0,
and the needle
the
movable knife
and the fixed knife presser@.
f),
and
the
fixed
knife@.
the
lower
the stud screw@, and the thread
ID,
and
the
movable knife
the
support lever
plate@.
thread finger
shaft@,
0.
4ll>.
trimmer
holder@.
and
the
connecting
thread
trimmer
rod@.
cylinder assembly
@.
2-4
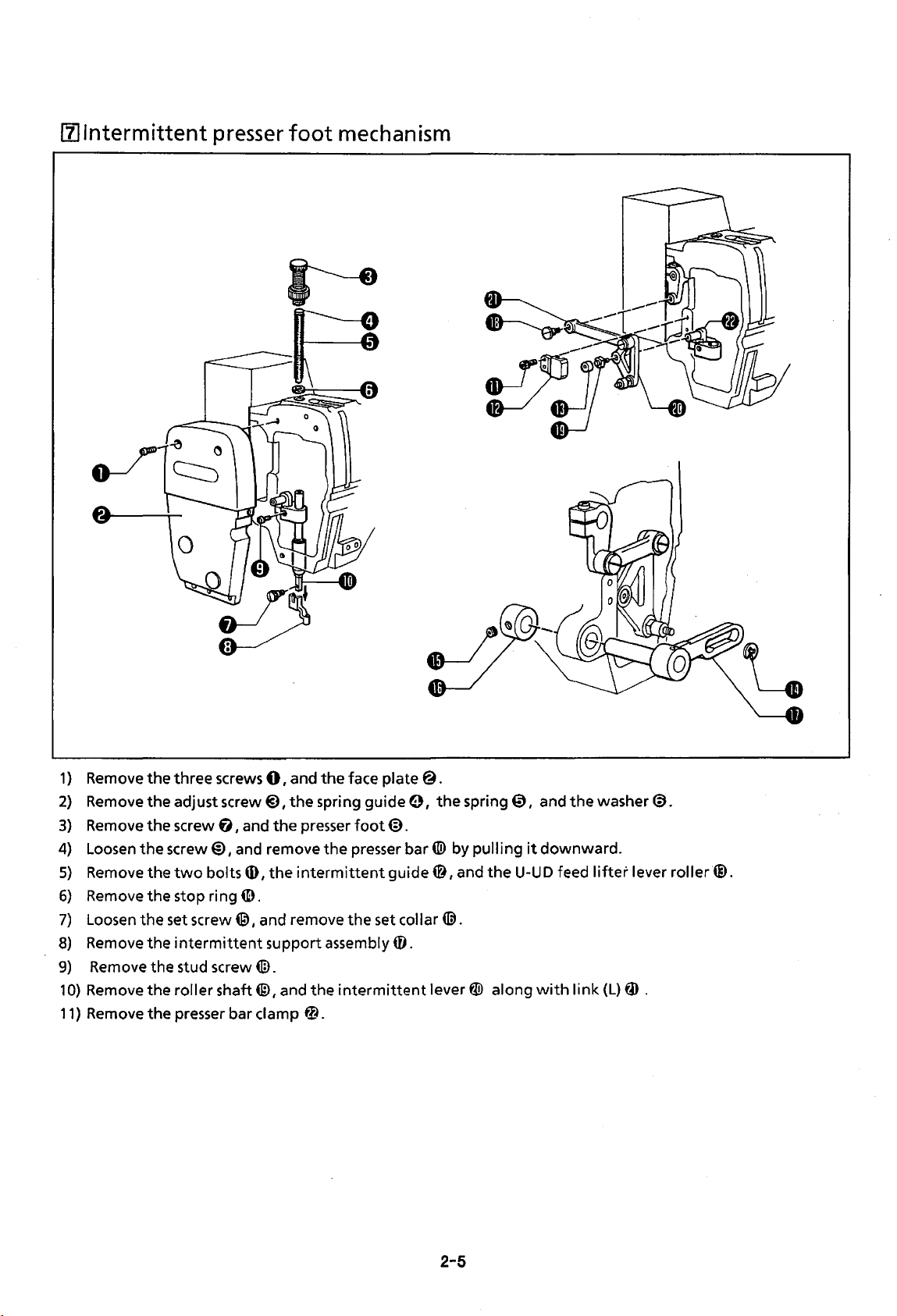
[Z]Intermittent presser
foot
mechanism
1)
Remove the three screws 0 I and
2)
Remove the adjust
3)
Remove the screw
4)
Loosen
5)
Remove the
6)
Remove the stop ring ffi.
7)
Loosen
8)
Remove the
9)
Remove
1
0)
Remove
11)
Remove the presser bar clamp
the
screw
the
set screw@ I and remove the set collar(@.
the
the
screw@) 1 the
f)
and
1
€>
and remove the presser bar
1
two
bolts m I
intermittent
stud screw@.
roller shaft@ I and the
the
face
pi
ate
spring guide 01 the
the
presser
the
intermittent
support assembly {f}.
foot@.
guide@
intermittent
0.
@.
spring 0 I and
4ID
by pulling
I and
lever
fli>
the
U-U
along
the
it
downward.
D feed
with
link
washer@.
lifter
lever
{L)
fD
.
roller@.
2-5
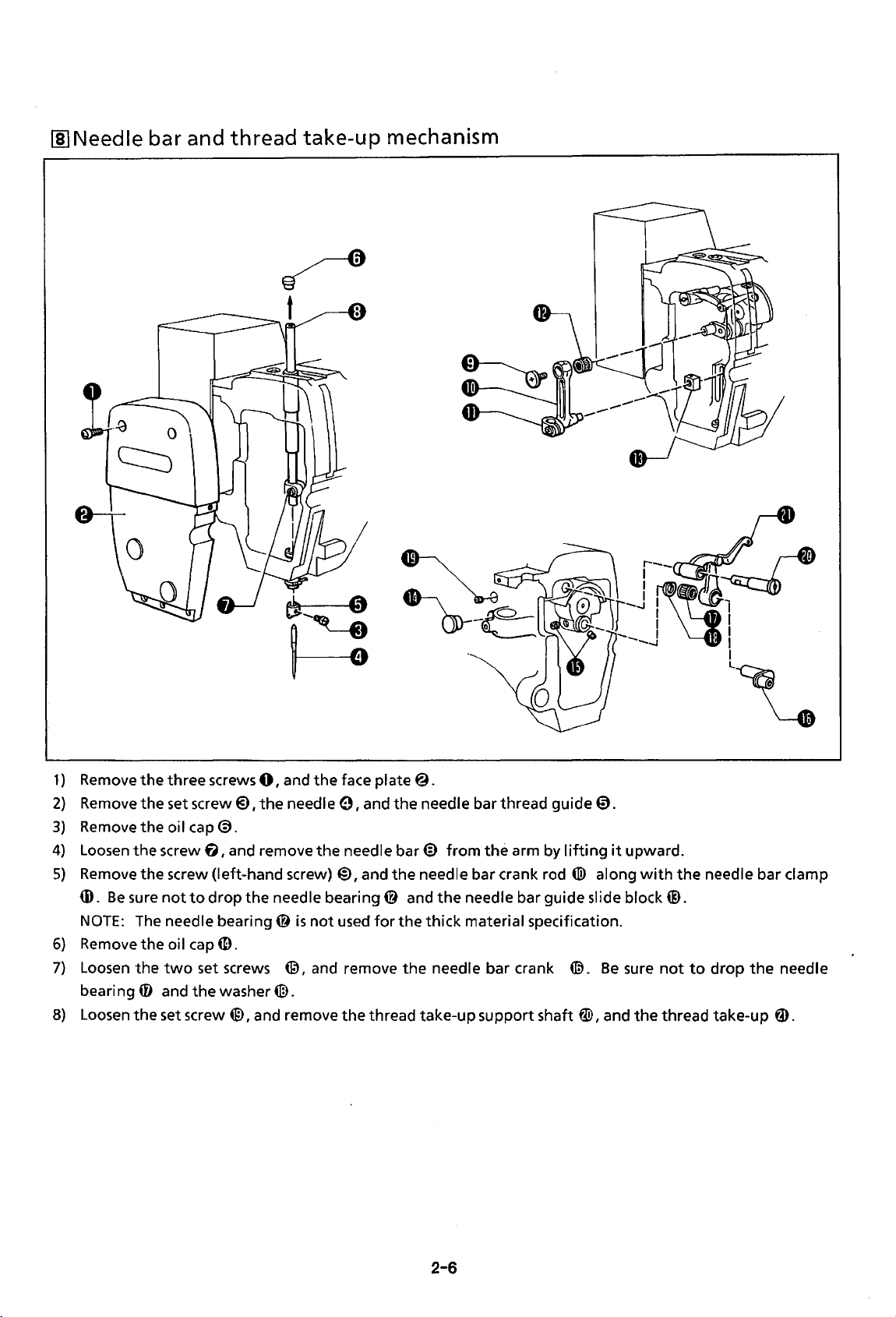
(I] Needle
bar
and
thread
take-up
mechanism
1)
Remove the three screws
2}
Remove the set screw@,
3)
Remove the oil cap@.
4)
Loosen
5}
Remove the screw (left-hand screw}
Q).
NOTE:
6)
Remove the oil cap ffi.
7)
Loosen the
bearing @ and the washer@.
8)
Loosen the set screw
Be
the
screw
f),
sure
not
to
drop
The
needle bearing@
two
set screws
0,
the
and remove the needle
the
®,and
and
the
face
plate@.
needle e, and the needle bar thread guide
bar@
@,and
needle bearing@ and
is
not
used
@,
and remove
remove
the
the needle bar crank rod ® along
for
the
thread take-up support shaft
from
the
arm by
the
needle bar guide slide block@.
thick material specification.
the
needle bar crank ®.
0.
lifting
it
upward.
with
the
Be
sure
not
W,
and the thread take-up
needle bar clamp
to
drop
the
needle
f1).
2-6
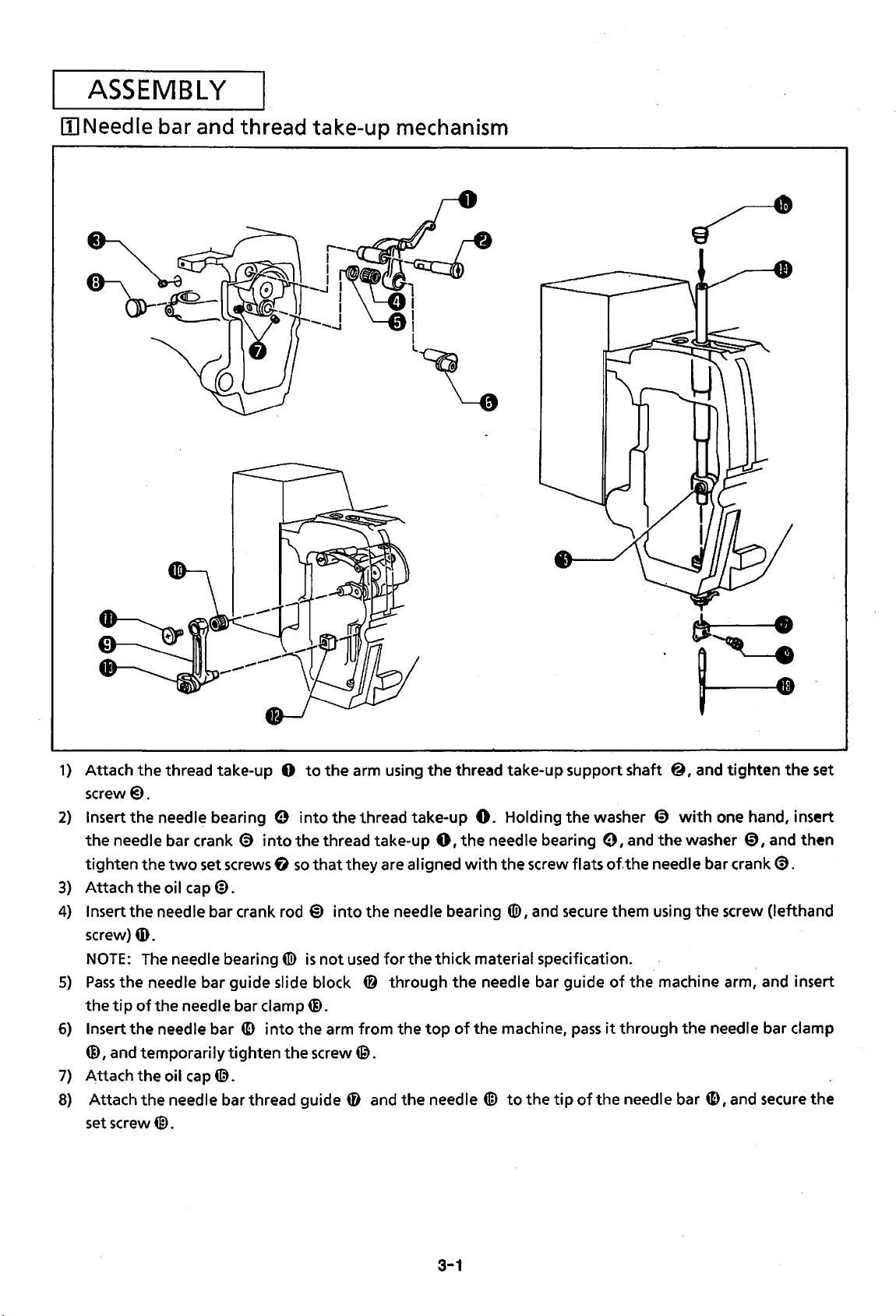
ASSEMBLY
[I]
Needle bar and thread take-up mechanism
1) Attach the thread take-up 0
screw@.
2)
Insert
the
needle bearing 0
the
needle bar crank @
tighten the
3)
Attach
4)
Insert the needle bar crank rod
screw)
NOTE:
5)
Pass
the needle bar guide slide block 0 through
the
tip
6)
Insert the needle bar
@,and
7)
Attach
8)
Attach the needle bar thread guide 0 and the needle
setscrew@.
two
set
screws
the
oil cap@.
ID.
The
needle bearing«!>
of
the needle bar clamp@.
4D
temporarily
the
oil cap@.
tighten
to
the
into
the
into
the
thread take-up
fi
so
that
@)
into
is
not
into
the arm from the
the
screw~.
arm using the thread take-up support shaft
thread take-up
they are aligned
the
needle bearing «!>,and
used
for
the thick material specification.
0.
Holding the washer
0,
the needle bearing
with
the screw flats of. the needle bar crank@.
the
needle bar guide
top
of
the machine,
tiD
to
the
0,
secure
pass
it
tip
of
the needle bar
@,and
€)
with
and
the
them using
of
the machine arm, and insert
through the needle bar clamp
tighten
one hand, insert
washer
the
€),
screw (lefthand
ID,
and secure the
the set
and then
3-1
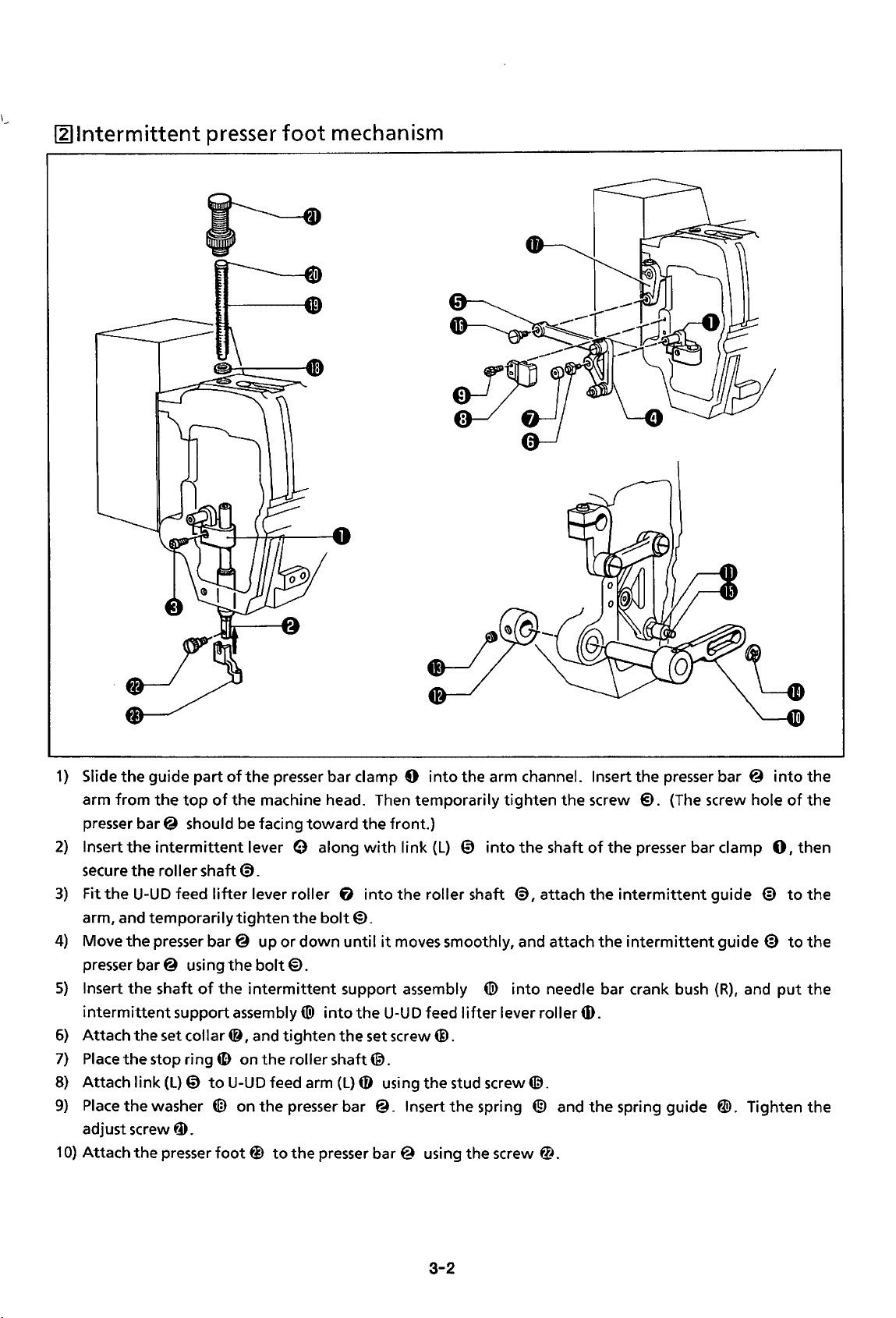
~Intermittent
presser
foot
mechanism
1)
Slide
the
guide
arm
from
the
presser
2)
Insert
secure
3)
Fit
arm, and temporarily
4)
Move
presser bar@ using
5)
Insert
intermittent
6)
Attach
7)
Place
8)
Attach
9)
Place
adjust screw
1
0)
Attach
the
bar@
the
intermittent
the
roller shaft ®.
U-UD
the
presser
the
shaft
the
set collar
the
stop ring
link
(L) 0 to
the
washer
the
presser
part
of
the
presser bar clamp 0
top
of
the
machine head. Then temporarily
should be facing
lever 9 along
feed
lifter
lever roller
tighten
bar@
the
of
the
support assembly®
0,
ID
on
U-UD
(ID
on
the
up
or
down
bolt@.
intermittent
and
tighten
the
roller
feed arm
the
presser bar
m.
foot
@)
to
the
into
the arm channel. Insert the presser bar @
toward
the
front.)
with
link
(L)
0
into
f'J
into
the roller shaft
bolt@.
until
it
moves smoothly, and attach
support assembly ®
into
the
U-U
D feed
the
set
screw®.
shaft@.
(L)
(f) using
@.
Insert
presser bar @ using the screw
lifter
the
stud screw@.
the
spring @ and
tighten
into
lever roller
the
screw
the
shaft
of
the
@,
attach
the
the
needle bar crank bush
ID.
the
@.
@.
(The screw hole
presser bar clamp
intermittent
intermittent
spring guide
guide @
(R),
guide @
and
f1i).
Tighten
into
of
0,
to
to
put
the
the
then
the
the
the
the
3-2
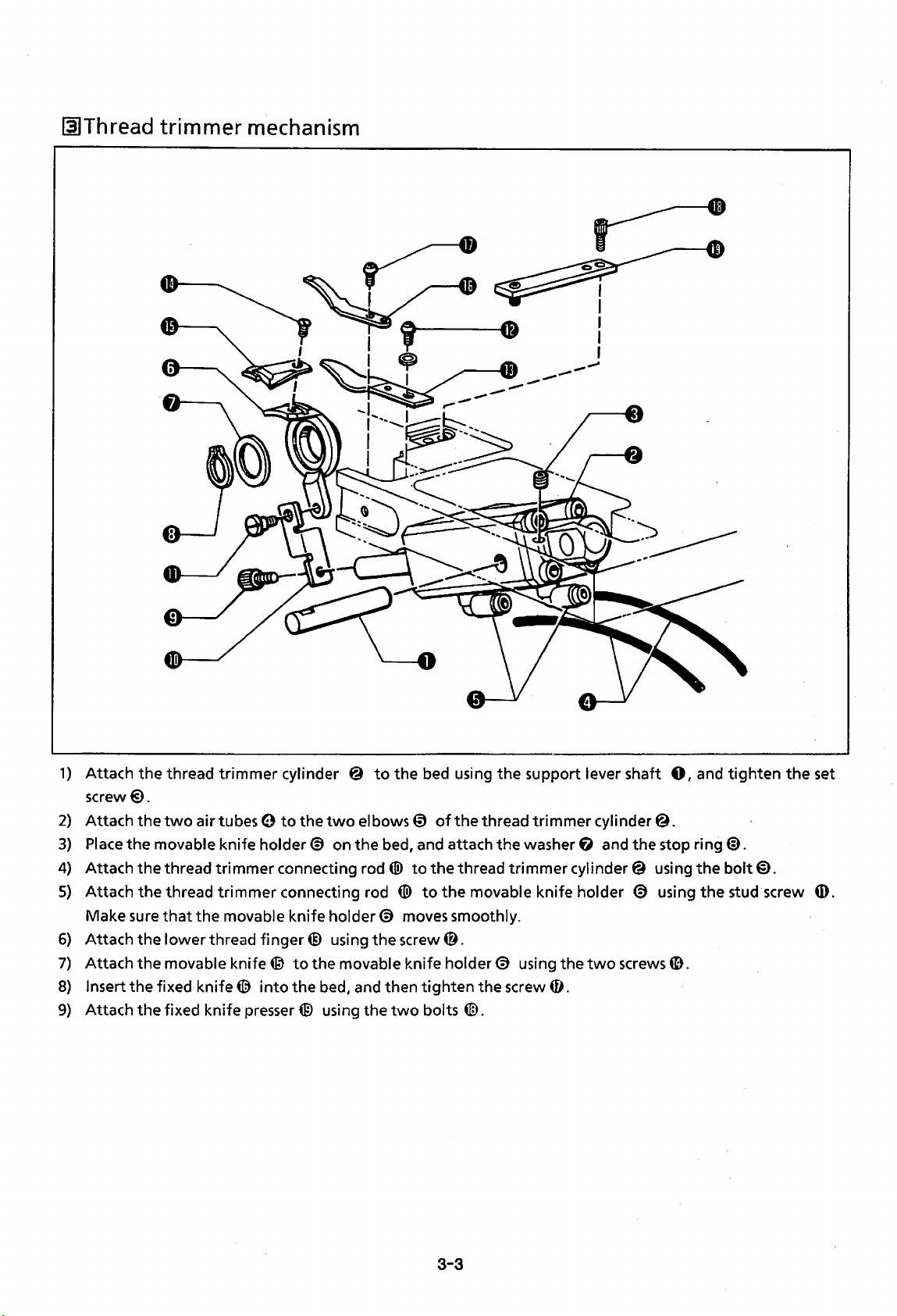
@)Thread
trimmer
mechanism
1)
Attach
screw@.
2)
Attach
3)
Place
4)
Attach
5)
Attach
Make sure
6)
Attach the
7)
Attach
8)
Insert
9)
Attach
the
thread
the
two
air tubes a
the
movable knife
the
thread
the
thread
that
the
lower
thread
the
movable
the
fixed
knife~
the
fixed knife presser
trimmer
trimmer
trimmer
movable knife
knife@
cylinder @
to
the
holder@
connecting
connecting rod ®
finger@
to
into
the
tiD
to
the
bed using
two
elbows
on
the
rod@
holder@
using
the movable knife holder@ using the
bed, and then
using the
€)
of
bed, and attach
to
the
to
the
moves smoothly.
the
screw@.
tighten
two
bolts
the
support lever shaft
the
thread
thread
movable knife holder @ using
the
@.
trimmer
the
washer
trimmer
screw
cylinder@ using
tTl.
0,
cylinder@.
fi
and the stop ring@).
two
screws
ID.
and
tighten
the
bolt@).
the
stud screw
the
set
0).
3-3
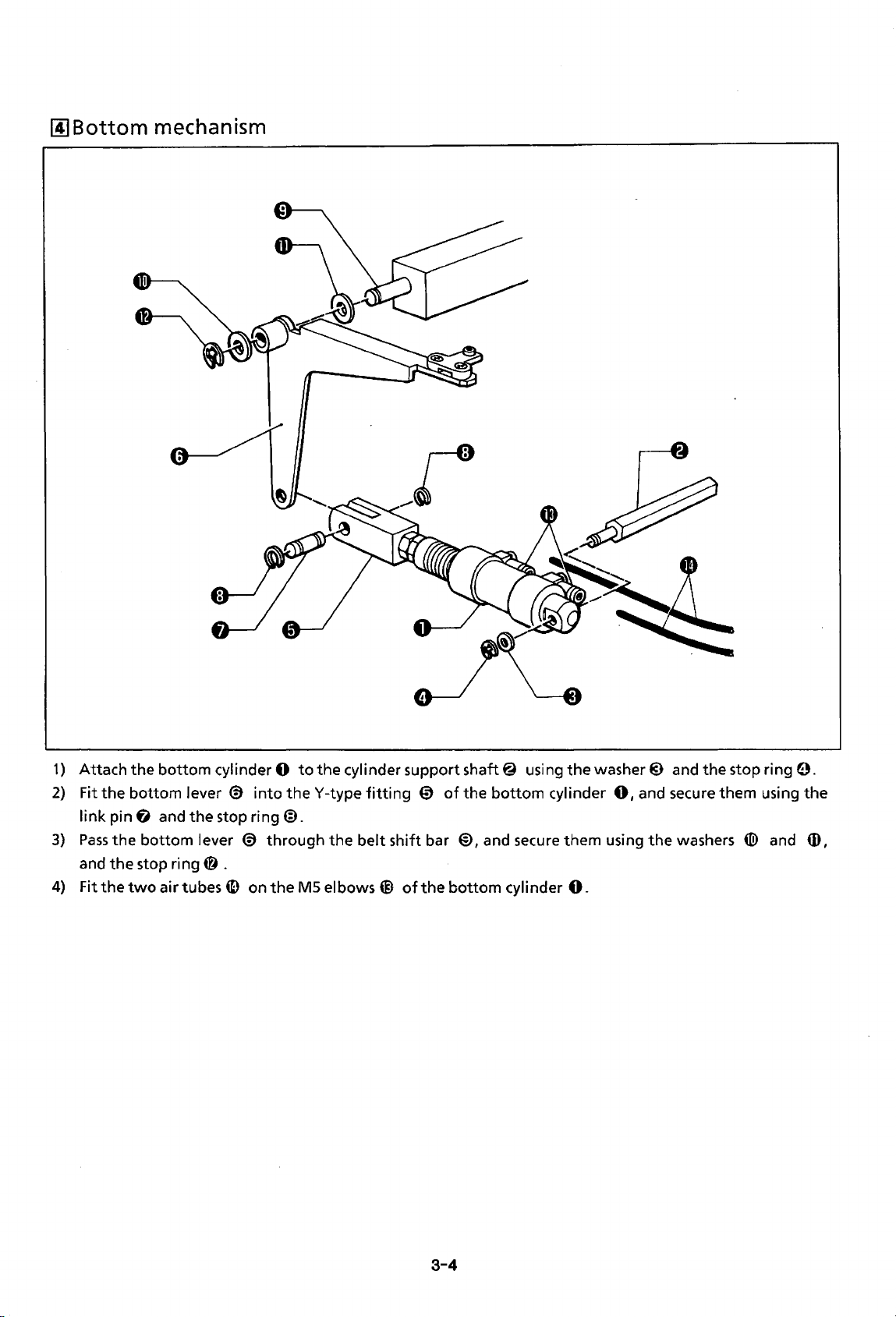
[4]Bottom mechanism
1)
2)
3)
4)
Attach
Fit
the
link
pin
Pass
the
and
the
Fit
the
the
bottom
bottom
fi
stop ring @ .
two
and
bottom
air tubes
lever
the
lever
cylinder 0
@}
into
stop
ring@.
@}
through
t0
on
the
to
the cylinder support shaft@ using
theY
-type
the
MS
elbows@
fitting 0 of
belt
shift bar @ 1 and secure them using
of
the
the
bottom
bottom
the
washer@) and
cylinder 01 and secure them using
the
cylinder
0.
the
washers
stop ring
«!>
and
0.
the
0),
3-4
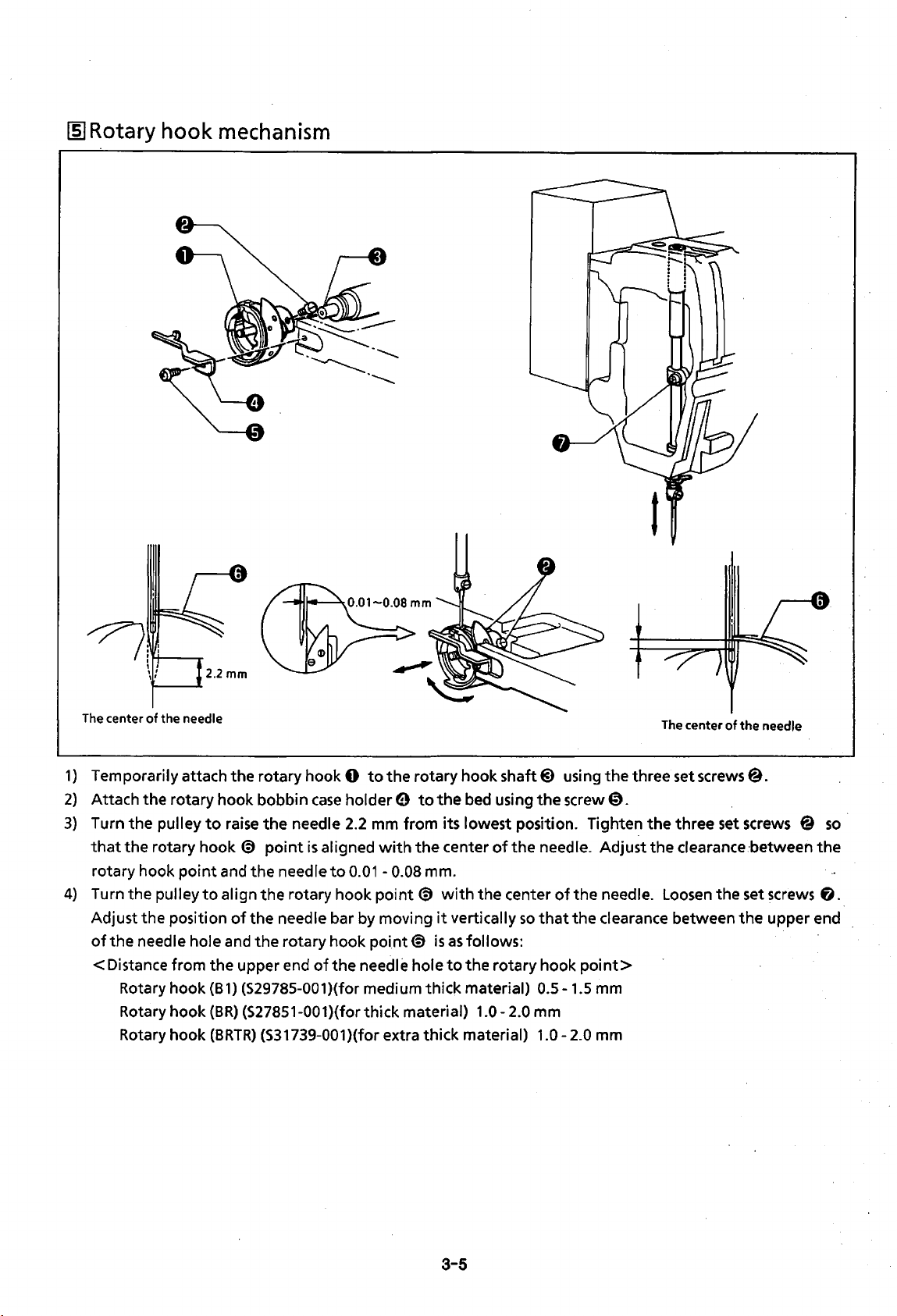
~Rotary
hook
mechanism
The center
1)
Temporarily attach the rotary hook 0
2)
Attach the rotary hook bobbin
3)
Turn the pulley
that
rotary hook
4)
Turn the pulley
Adjust the position
of
<Distance from
of
the
needle
to
the rotary hook
point
to
the needle hole
the
Rotary hook
Rotary hook
Rotary hook
{B
{BR)
{BRTR)
raise
the
needle
@)
point
and the needle
align the rotary hook point@)
of
the needle bar by moving
and
the
rotary hook point@)
upper end
1)
{S29785-001){for medium thick material) 0.5-
{S27851-001){forthick material) 1.0-2.0 mm
{531739-001
to
the rotary hook shaft@) using
case
is
aligned
to
holder 9
2.2
0.01
to
the
bed using
mm from its lowest position. Tighten the three
with
the
center
- 0.08 mm.
with
it
vertically
is
as
follows:
of
the needle hole
to
the rotary hook
){for extra thick material) 1.0-
the
of
the
needle. Adjust the clearance.between
the center
so
that
The center
the
three set screws@.
of
the
screw@.
set
of
the needle.
the
clearance between the upper end
Loosen
the set
point>
1.5
mm
2.0
mm
needle
screws
screws
@
so
the
fi
..
3-5
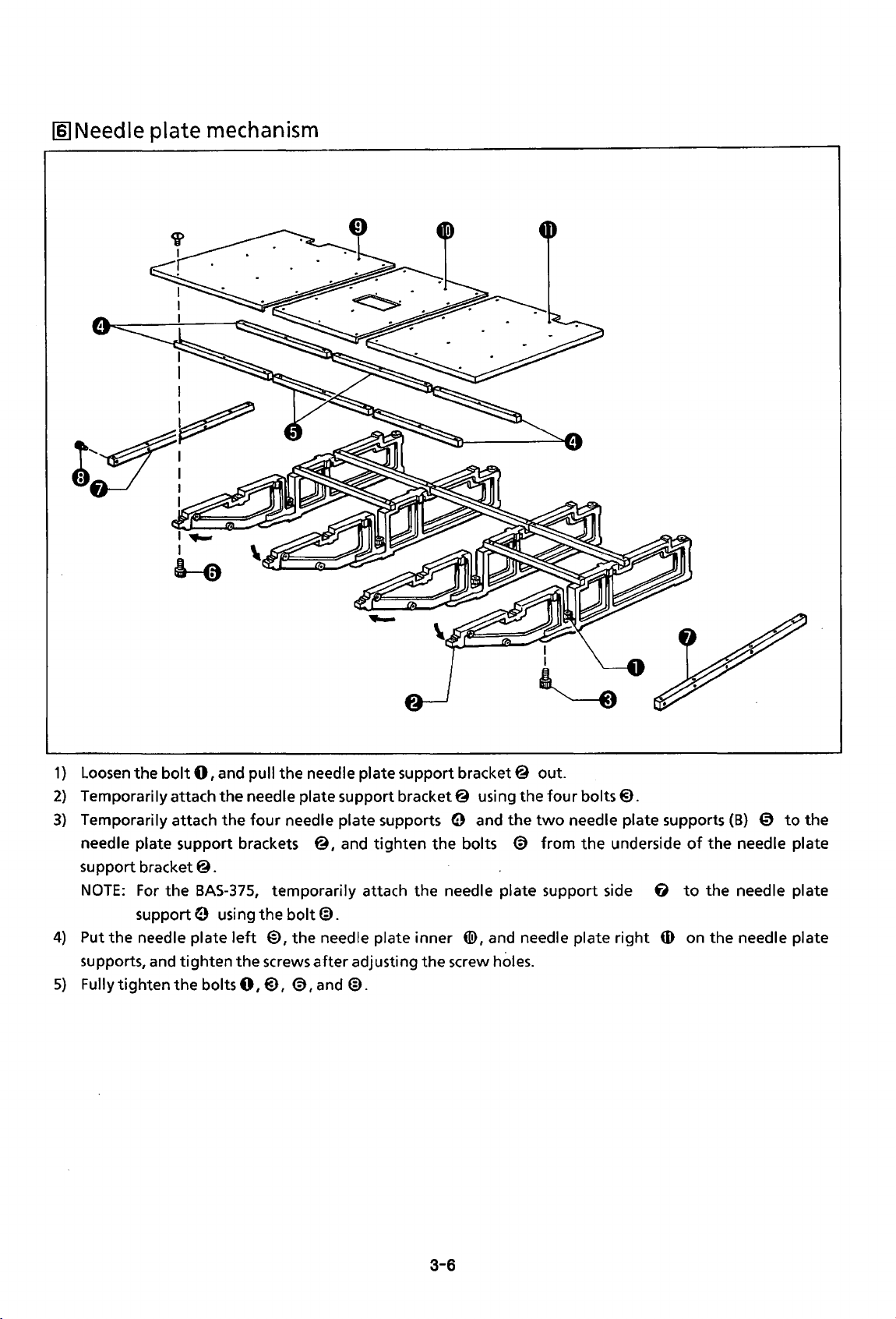
[§]Needle
plate
I
I
I
~
mechanism
t~i
I
1)
Loosen the
2)
Temporarily attach
3)
Temporarily attach
needle plate support brackets
support bracket@.
NOTE:
4)
Put
the
supports, and
5)
Fully
bolt
0
For
the
BAS-3751 temporarily attach
support 0 using
needle plate
tighten
tighten
the
bolts
and pull
1
the
needle plate support bracket@ using
the
four
the
left
@,the
the
screws
0,
@),
the
needle plate support bracket@ out.
needle plate supports G and
@,
and
tighten
bolt@.
needle plate inner
after
adjusting
@,
and
@.
the
bolts @ from
the
needle plate support side
([i)
and needle plate
1
the
screw holes.
the
the
four
bolts@).
two
needle plate supports
the
underside
right
f)
ID
of
to
on
(B)
the
needle plate
the
needle plate
the
needle plate
0
to
the
3-6
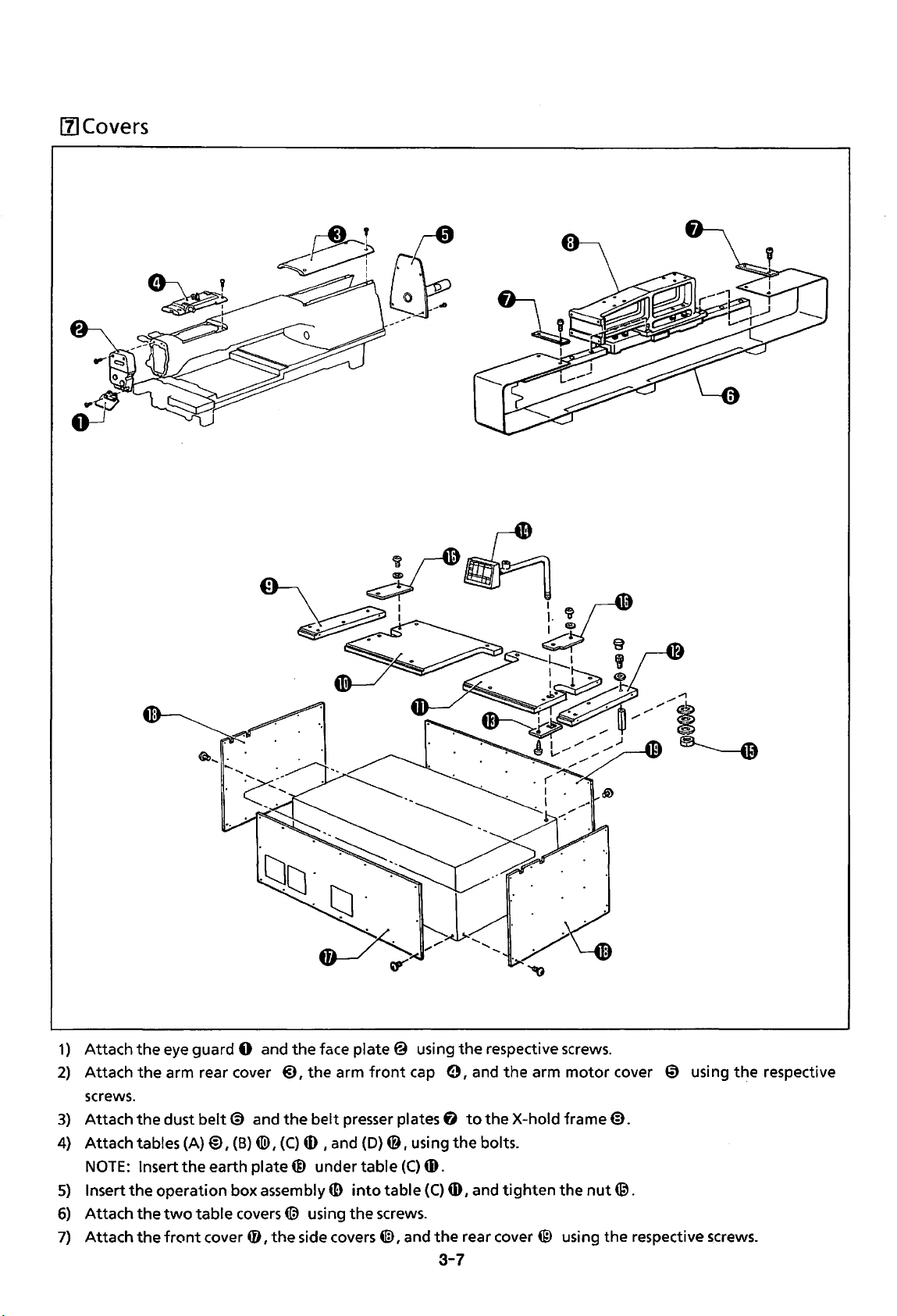
[l]Covers
1)
2)
Attach
Attach
the
eye
guard 0 and
the
arm rear cover
the
@)I
face
plate@
the arm
front
using
the
respective
cap 0 I and
the
arm
screws.
motor
screws.
3)
Attach
4)
Attach tables (A)@ I
NOTE:
5)
Insert
6)
Attach
7)
Attach
the
dust
belt@
Insert
the
the
operation box assembly m
the
two
table covers@ using the
the
front
cover 0 I
(B)
earth
and
the
tiD
I
(C)
plate@
the
belt
presser plates 6
ID
I and (D) 0 I using
under table
into
(C)
table
screws.
side covers@, and
to
the
the
X-hold
bolts.
frame@.
ID.
(C)
ID
I and
tighten
the
rear cover@ using the respective
the
3-7
cover 0 using
nut@.
the
screws.
respective