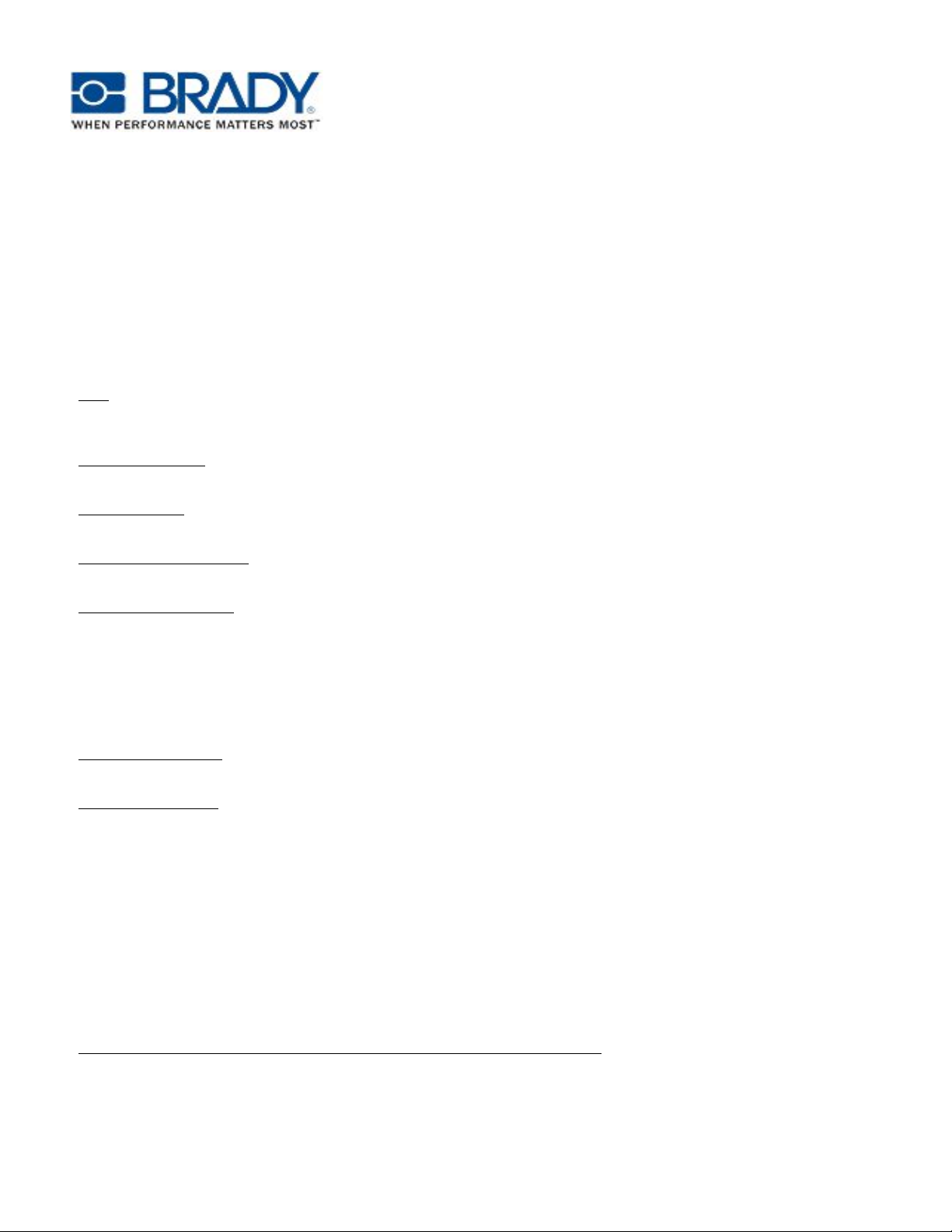
Technical Data Sheet
BRADY B-7569 VINYL FILM WITH PERMANENT ADHESIVE
TDS No. B-7569
Effective Date: 10/20/2011
Description:
Brady B-7569 is a thermal transfer printable flexible vinyl film coated with a permanent pressure sensitive acrylic adhesive.
B-7569 is designed to be used with the MINIMARK
37 printers (per regional availability) as well as for pre-printed labeling and floor marking.
Details:
Use:
B-7569 is used for Pipe Markers, Arrow Tape, Warehouse Marking, Floor Marking, Warning Panels, Safety Signs and
Hazardous Substance Identification.
Special Properties:
Permanent acrylic adhesive
Substrate Type:
Vinyl film
Standard Material Colors:
White, red, yellow, green, blue, orange and black
Recommended ribbons
MINIMARK
Standard performance black and white (R-7968), red, green and blue (R-7969)
HIgh performance black (R-6000), white, red, green and blue (R-4400)
Globalmark®, Powermark®:
Standard Ribbons
BBP® 31:
R-10000
Thickness (PSTC-33):
Total: 0.105 mm (0.004 in.)
Adhesive Properties:
Adhesion to Stainless Steel (PSTC-1)
Ultimate Dwell (72 Hrs.) (Avg.) -- 130 N/100mm (120 oz/in)
Adhesion to Powder Coated Metal (PSTC-101)
Ultimate Dwell (72 Hrs.) -- 50 N/100mm (45 oz/in)
Adhesion to Polypropylene (PSTC-101)
Ultimate Dwell (72 Hrs.) (Avg.) -- 60 N/100mm (55 oz/in)
Adhesion to Textured ABS (PSTC-101)
Ultimate Dwell (72 Hrs.) (Avg.) -- 25 N/100mm (25 oz/in)
Tack (ASTM D 2979) (Avg.) -- 700 g (7 N)
Abrasion Resistance (Method 5306 of U.S. Federal Test Method Std. No. 191A):
CS-10 wheels, 250 g wts.
After 100 cycles the legend printed with R-7968 has a moderate fading
Print legible up to 300 cycles with R-10000 ribbon
Print legible up to 500 cycles with R-4400 ribbon
Print legible up to 1000 cycles with R-6000 ribbon
TM
:
TM
, Globalmark®, Powermark® and BBP® 31, BBP® 33, BBP® 35, BBP®
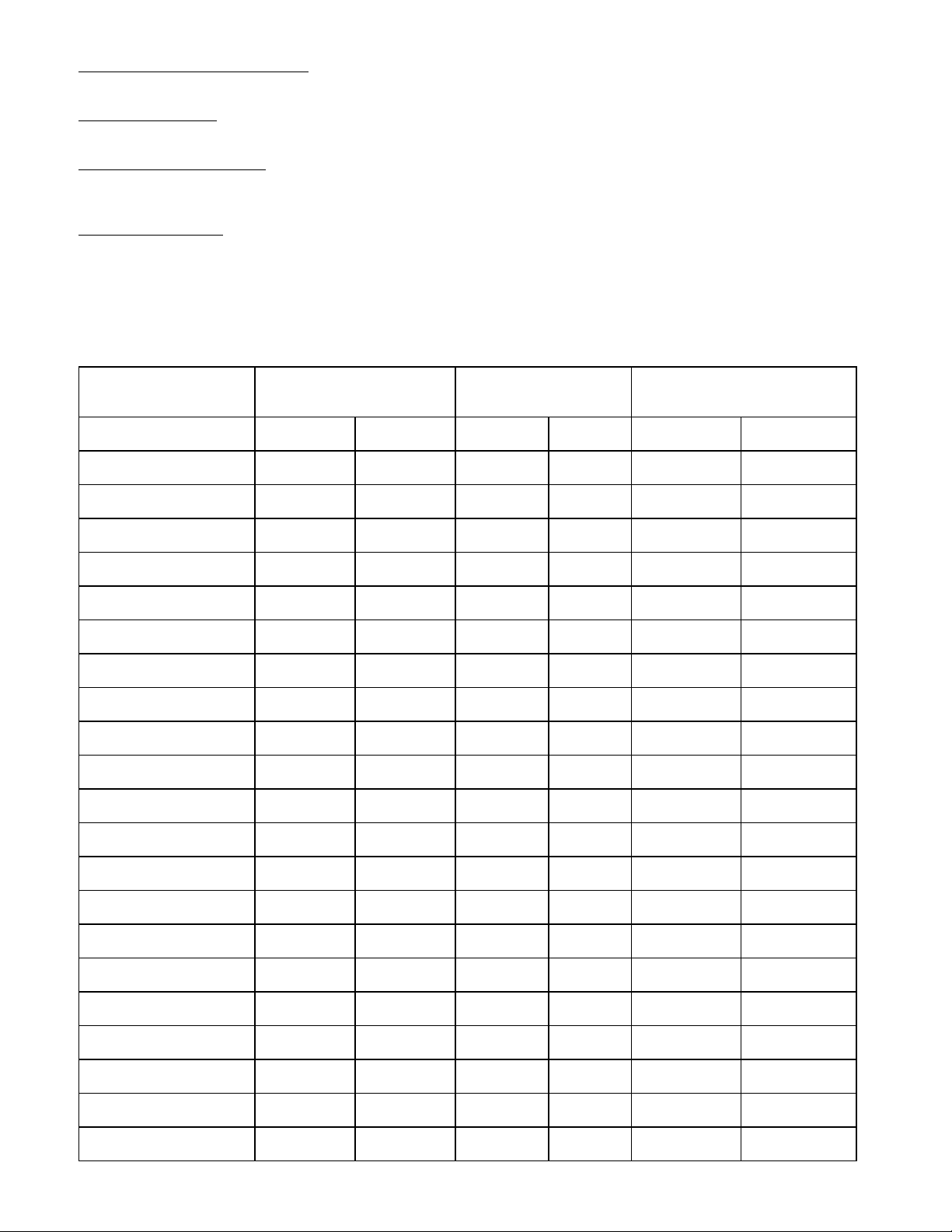
Minimum Application Temperature
Standard Performance
Ribbons
10°C (50°F)
Service Temperature
-20°C to 75°C (-4°F to 167°F)
Average Outdoor Durability:
Up to 3 years (Average expected outdoor life of product will depend on user definition of failure, climatic conditions,
mounting techniques, and material color.)
Chemical Resistance:
Samples were printed with the standard performance ribbons R-7968/R-7969 and the high performance ribbons
R-6000/R-4400 using the MINIMARK
TM
thermal transfer printer. Additional samples were printed with the R-10000 ribbon
using the BBP® 31 thermal transfer printer. Printed samples were laminated to aluminum and allowed to dwell 24 hours prior
to testing. Testing conducted at room temperature. Testing consisted of 5 cycles of 10 minute immersions in the specified
test fluid followed by a 30 minute recovery period. After final immersion the samples were rubbed 10 times with a cotton
swab saturated with test fluid.

NE = No Effect
F = Failed (affected sample)
Shelf Life and Fitness for Use: Product testing, customer feedback, and history of similar products, support a customer
performance expectation of one year from the date of receipt for this product as long as this product is stored in its original
packaging in an environment below 80°F (27°C) and 60% RH. However, it remains the responsibility of the user to assess the
risk of using such product. We encourage customers to develop functional testing protocols that will qualify a product's fitness
for use, in their actual applications.
Trademarks:
ASTM: American Society for Testing and Materials (U.S.A)
Alconox® is a registered trademark of Alconox Co.
BBP® 31 is a registered trademark of Brady Worldwide, Inc.
BIOACT® is a registered trademark of Brady Worldwide, Inc.
TM
EC-7R
is a trademark of Petroferm Inc.
Formula 409® is a registered trademark of the Chlorox Company
Globalmark® is a registered trademark of Brady Worldwide, Inc.
MINIMARK
Northwoods
TM
is trademark of Brady Worldwide, Inc.
TM
is a trademark of the Superior Chemical Corporation
PSTC: Pressure Sensitive Tape Council (U.S.A.)
Powermark® is a registered trademark of Brady Worldwide, Inc.
SAE: Society of Automotive Engineers (U.S.A.)
Note: All values shown are averages and should not be used for specification purposes.
Test data and test results contained in this document are for general information only and shall not be relied upon by Brady
customers for designs and specifications, or be relied on as meeting specified performance criteria. Customers desiring to
develop specifications or performance criteria for specific product applications should contact Brady for further information.
Product compliance information is based upon information provided by suppliers of the raw materials used by Brady to
manufacture this product or based on results of testing using recognized analytical methods performed by a third party,
independent laboratory. As such, Brady makes no independent representation or warranties, express or implied, and assumes
no liability in connection with the use of this information.