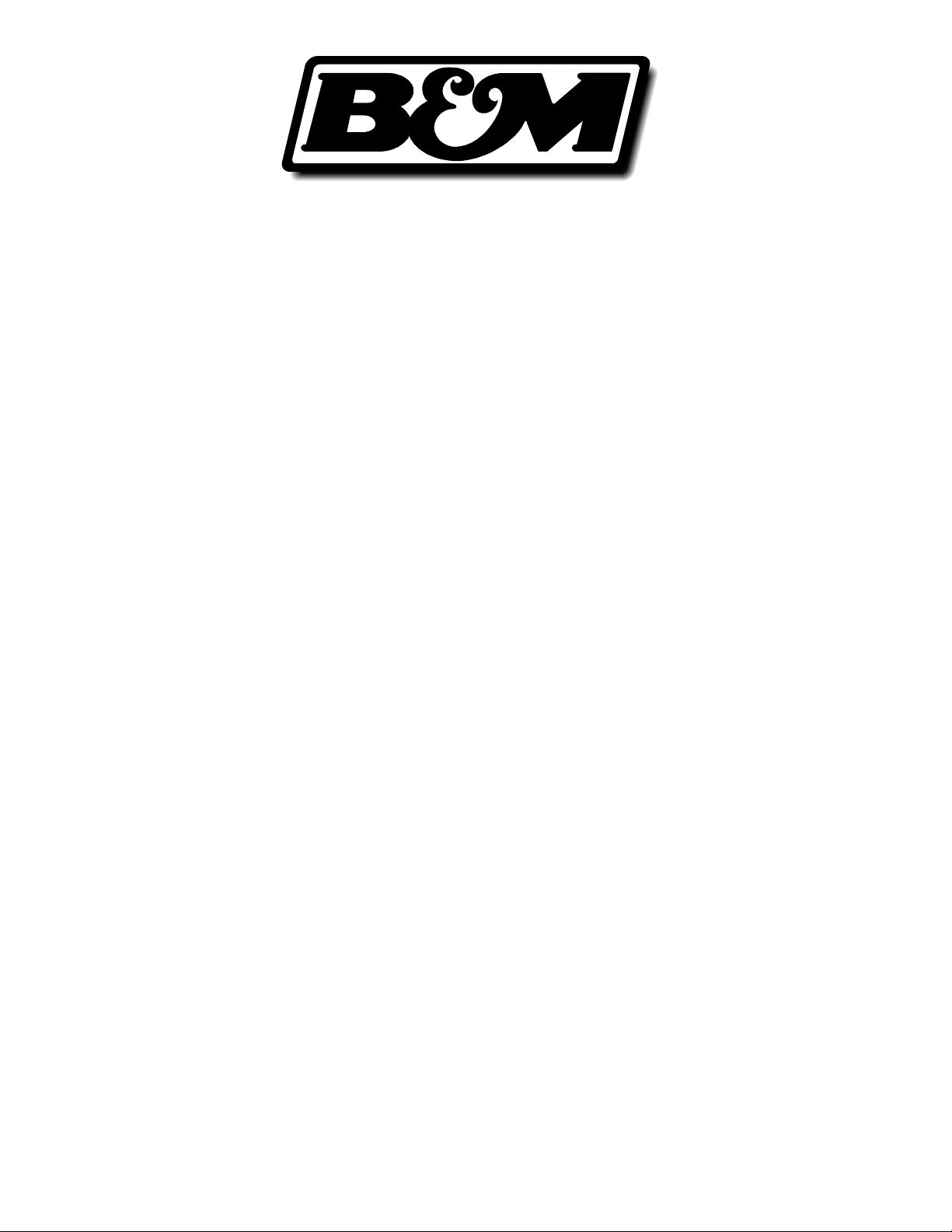
Torque Converter
Installation Instructions
for
General Motors
TH-350, TH-400, & Powerglide
© 2006, 2002, 1995 by B&M Racing and Performance Products
Congratulations. You have just
purchased the best performing and highest quality torque converter available.
We feel the installation instructions on
the following pages are as complete
and clear as possible. Anyone with a
minimum of mechanical experience
should be capable of installing a torque
converter using the proper tools and
following instructions. It is important to
closely follow the instructions. Read
each step and if you don’t understand
go back and read it again.
Included are part numbers for
flexplates and other components which
may aid in installation. Every attempt
has been made to assure the accuracy
of this information. These instructions
are aimed at making your installation
as easy and simple as possible.
INTRODUCTION
The torque converter in your automatic transmission is a unique device
and must perform several functions:
First, it must provide some slip at an
idle so the engine does not stall when
the vehicle is stopped and the engine is
running.
Second, it multiplies torque under initial accelerations to provide more power
to the rear wheels. The typical torque
multiplication of a torque converter is
about 2:1. This means that the torque
converter is actually doubling engine
torque or power on initial acceleration.
Some high stall converters have torque
multiplication as high as 2.6:1.
Printed in the U.S.A.
Third, the torque converter must have
as little slippage as possible under
normal driving conditions so the engine
operates efficiently. High stall speed
converters are designed to be as efficient as possible at high rpm for maximum mph.
Fourth, the torque converter must have
reverse coupling to slow the vehicle
when you downshift to second or low.
Traveler torque converters are designed
to give maximum deceleration for improved engine braking.
All of the above functions occur
automatically under various operating
conditions. The torque converter is a
simple and yet complex piece of equipment. Improper installation will re-
sult in poor performance and possible damage to the torque converter
and/or transmission. Read all in-
structions first to familiarize yourself
with the parts and procedures. Work
slowly and do not force any parts.
Burrs and dirt are the number one
enemies of automatic transmission
assembly. Cleanliness is very important. Avoid getting any dirt or foreign
particles in the transmission or torque
converter.
Automatic transmissions operate
at temperatures between 1500F and
2500F. It is suggested that the vehicle
be allowed to cool for a few hours to
avoid burns from hot oil and parts. The
vehicle should be off the ground for ease
of installation. Jack stands, wheel
ramps or a hoist will work fine. Make
sure the vehicle is firmly supported!! Try to raise it 1 - 2 feet so you have
plenty of room to work easily. Also
have a small box or pan handy to put
bolts in so they won’t be lost, and a
drain pan to catch oil. We suggest you
rent a transmission jack from a rental
yard to remove the transmission as the
transmission/converter assembly is
heavy. A regular floor jack may be used
if a transmission jack is unavailable.
Due to variations between different
car models, exact instructions for every
vehicle cannot be provided. These
instructions are sufficient for all vehicle
installations. You may find it necessary to disconnect and lower exhaust
pipes during transmission removal.
NOTE: All B&M Torque Converters
have fixed pitch stators and will not fit
1965-1967 Buick, Olds or Cadillac variable pitch TH-400 transmissions. Variable pitch transmissions can be identified by a 1" wide smooth bushing diameter directly behind the large spline of
the stator shaft on the front pump.
NOTE: B&M converters will not fit
TH-350's originally equipped witha clutch
converter except part number 30416.
STEP 1. Drain oil pan. This will make
less of a mess during transmission
removal. Some model TH-350 and
Powerglide transmissions have drain
plugs. TH-400 transmissions do not
have drain plugs. If yours has a drain
plug, remove it and allow the fluid to
drain, then install drain plug back into
9500197-09
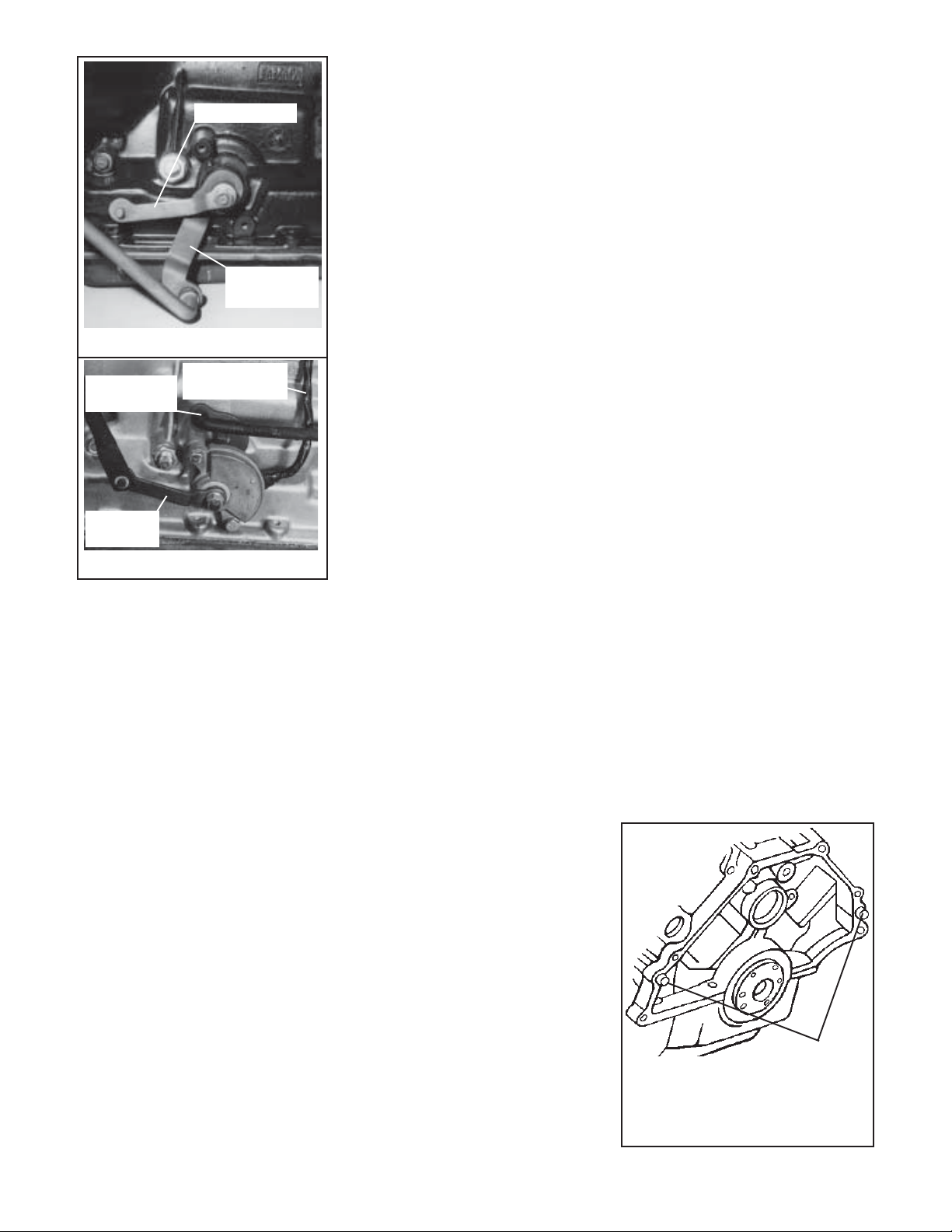
Kickdown lever
Column Shift
lever
Figure 1
Console Shift
lever
Kickdown
lever
pan. If you do not have a drain plug in
your tranmission oil pan, you should
consider installing a B&M Drain Plug
Kit, P/N 80250, while transmission is
out of vehicle. If your transmission
does not have a drain plug or a dipstick
tube in the oil pan, loosen the oil pan
bolts to allow the fluid to drain. After the
fluid has drained, snug the oil pan back
into place. You may wish to service
your transmission while changing the
converter.
STEP 2. Remove driveshaft. Be careful not to damage the smooth bushing
diameter on slip yoke models. Do not
let the cups fall off the U-joint crosses.
You may lose some of the needle
bearings if the cups fall on the ground.
It is a good idea to tape the cups to the
U-joint cross, so they won’t fall off.
Now is a good time to clean and inspect your U-joints. 4 Wheel Drive
models: Remove front drive shaft also.
STEP 3. Disconnect vacuum line to
vacuum modulator.
Powerglide: Disconnect throttle
pressure lever at transmission (See
Fig. 1).
Neutral saftey
switch harness
Figure 2
TH-350: Disconnect kickdown cable
at carburetor. Remove retaining bolt
from kickdown cable at transmission.
Pull cable out of transmission and
disconnect cable from detent wire
link (see Fig. 2). Allow cable to hang
free.
TH-400: Disconnect kickdown wire
from electrical connector on left side
of transmission (see Fig. 3). Allow
wire to hang free.
STEP 4. Disconnect shifter:
Column Shift Models: Remove cot-
ter key or clip and disconnect rod or
bellcrank from shift lever on transmission (see Fig. 4). Allow linkage to
hang free.
Console Shift Models: Remove cotter key or clip and disconnect shifter
rod or cable from shift lever on transmission (see Fig. 5). Allow rod or
cable to hang free. Cable shift units,
remove two bolts holding cable cracket
to pan and let cable andbracket hang
free.
4 Wheel Drive models: Remove
knob from transfer case shift lever.
STEP 5. Loosen and disconnect speedometer cable and pull cable out
ofspeedometer housing. Let the cable
hang free.
STEP 6. Disconnect oil cooler lines.
Use a fitting wrench, if available, to avoid
damage to compression nuts. We
recommend that the oil cooler lines be
flushed out to remove any foreign particles trapped in the cooler. Cooler lines
should be flushed in both directions with
solvent and air pressure. Aftermarket
coolers should be relaced if they are
contaminated due to torque converter
failure.
STEP 7. Remove dipstick and tube
assembly. Remove torque converter ,
cover pan bolts and remove converter
cover pan (see Fig. 6). Remove flexplate
to converter bolts (see Fig. 7). Use
starter motor to “bump” each bolt into
position.
STEP 8. Remove distributor cap to
prevent damage during transmission
removal. Support the transmission with
a jack. Remove transmission mount
bolts. Raise the transmission slightly
and remove the cross member. Be
sure the transmission jack supports
the transmission on a wide area so you
don't crush the transmission pan.
STEP 9. Remove the bellhousing bolts.
Lower transmission until the engine is
supported. Pull transmission back
slightly away from engine. Make sure
converter stays with transmission.
Lower transmission/converter assembly and remove from vehicle. Caution:
4 Wheel Drive Vehicles: Transmission/converter transfer case assembly
is heavy. Exercise care during removal if your transfer case bolts to the
transmission.
STEP 10. Pull converter off the front of
the transmission. Some oil will leak
out at this time. If you planto store your
original torque converter, drain it and
cover the neck to prevent entry of dirt.
STEP 11. Inspect your engine block
and engine plate. Make sure there are
no burrs that will prevent the transmission from bolting down flat against the
engine. File off any burrs that may be
present. Dowel pins should stick out of
the engine block a minimum of 1/2" for
proper alignment (see Fig. 8). Insufficient dowel pin engagement can cause
front seal and/or bushing failure due to
improper engine/transmission alignment. Bellhousing bolts alone will
not align the transmission properly.
STEP 12. Inspect your flexplate. Check
for distortion, excessive warpage or
Dowel pins must
stick out 1/2" for
proper transmission engagement
Figure 3