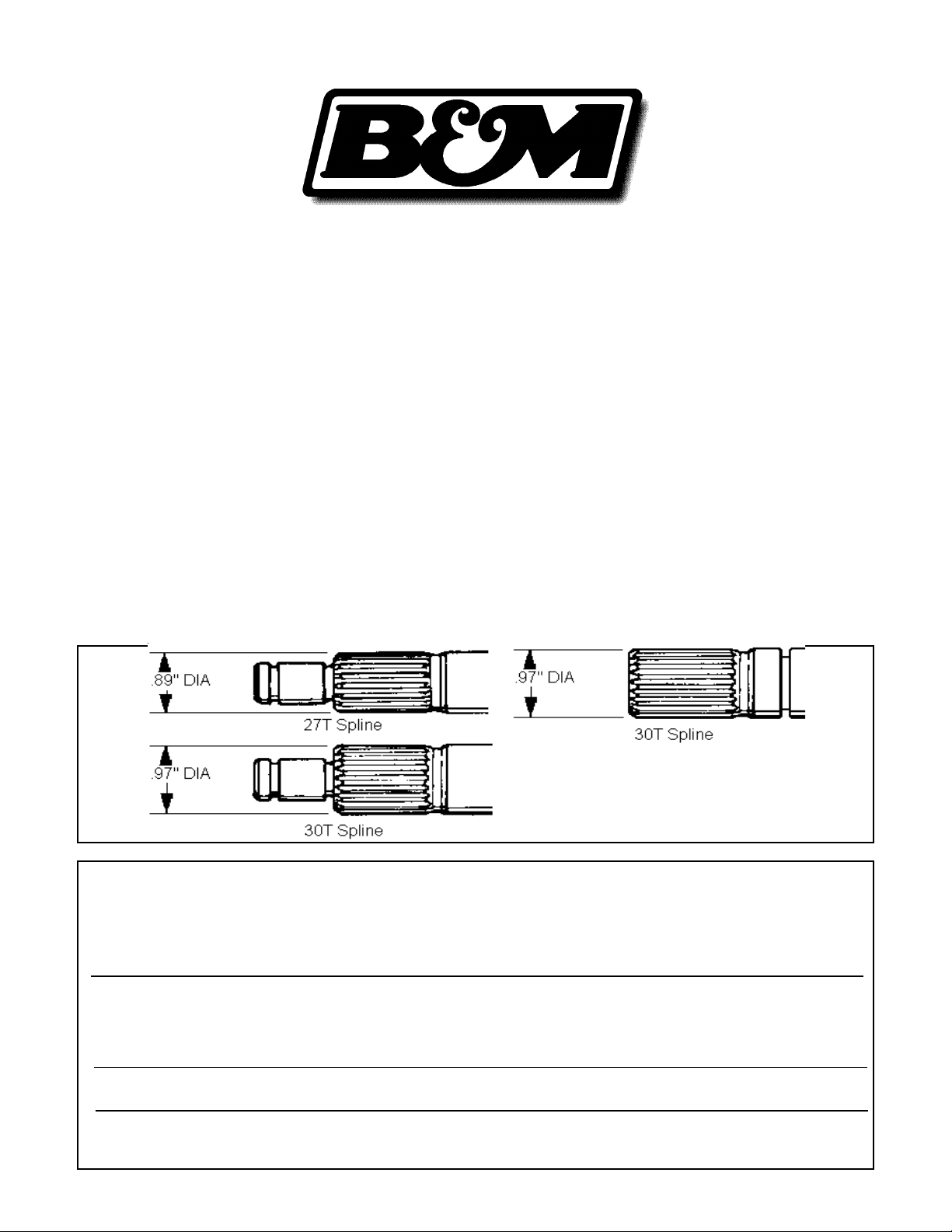
Torque Converter
Installation Instructions for
General Motors TH700-R4 (4L60), 4L60E,
TH200-4R and TH200C
Part Nos. 70415, 70416, 70417, 70418, 70419, 70420, 70422, 70425 , 70426, 70440 & 70441
(C) B&M Racing & Performance Products 1996, 1999, 2004
Congratulations! You have just purchased the best performing and highest
quality torque converter available. We
have endeavored to make these installation instructions as clear and complete
as possible. Anyone with a minimum of
mechanical experience should be capable of installing a torque converter
using proper tools and following the instructions. IMPORTANT: Read the instructions completely before beginning
the installation so you can familiarize
yourself with the procedures.
APPLICATIONS
These GM lockup clutch style (TCC)
torque converters are made in versions
for several automatic transmissions,
three different input shaft spline tooth
numbers and a range of stall speeds.
The chart below shows the applications.
The new B&M torque converter can
be used as either a lockup or non lockup
unit. If the vehicle currently has an operational TCC it will continue to operate if no
other changes are made to the vehicle.
Optionally the TCC can be bypassed
(except on 4L60E transmissions) if desired as covered in STEP 22 below.
If the torque converter is being installed into a vehicle that was not originally equipped with a transmission with
lockup torque converter the TCC will not
operate and the converter will be a nonlockup converter. The TCC in a TH700R4, 4L60, TH200-4R or TH350C can be
made to operate in this type of applica-
Fig. 1
Transmission Input Shaft Type Part No.
TH200-C 27 Tooth HoleShot 2400 70415
TH200-4R 27 Tooth HoleShot 2400 70415
TH700-R4 1982-84 27 Tooth HoleShot 2400 70415
TH200-C 27 Tooth HoleShot 2000 70416
TH200-4R 27 Tooth HoleShot 2000 70416
TH700-R4 1982-84 27 Tooth HoleShot 2000 70416
TH700-R4 1984-93 (4L60) & 1993-96 4L60E 30 Tooth HoleShot 2000 70417
TH700-R4 1984-93 (4L60) & 1993-96 4L60E 30 Tooth HoleShot 2400 70419
TH700-R4 1984-93 (4L60) & 1993-96 4L60E 30 Tooth Tork Master 2000 70420
TH700-R4 1984-93 (4L60) & 1993-96 4L60E 30 Tooth Tork Master 2400 70418
TH700-R4 1984-93 (4L60) & 1993-96 4L60E 30 Tooth Traveler 70422
TH700-R4 1984-93 (4L60) & 1993-96 4L60E 30 Tooth HoleShot 3000 70425
TH200-C 27 Tooth HoleShot 3000 70426
TH200-4R 27 Tooth HoleShot 3000 70426
TH700-R4 1982-84 27 Tooth HoleShot 3000 70426
4L60E 1998-04 & 2000-04 4L65E 30 Tooth HoleShot 2000 70440
4L60E 1998-04 & 2000-04 4L65E 30 Tooth HoleShot 2400 70441
Torque Converter Applications
Printed in the U.S.A.
9500354-04
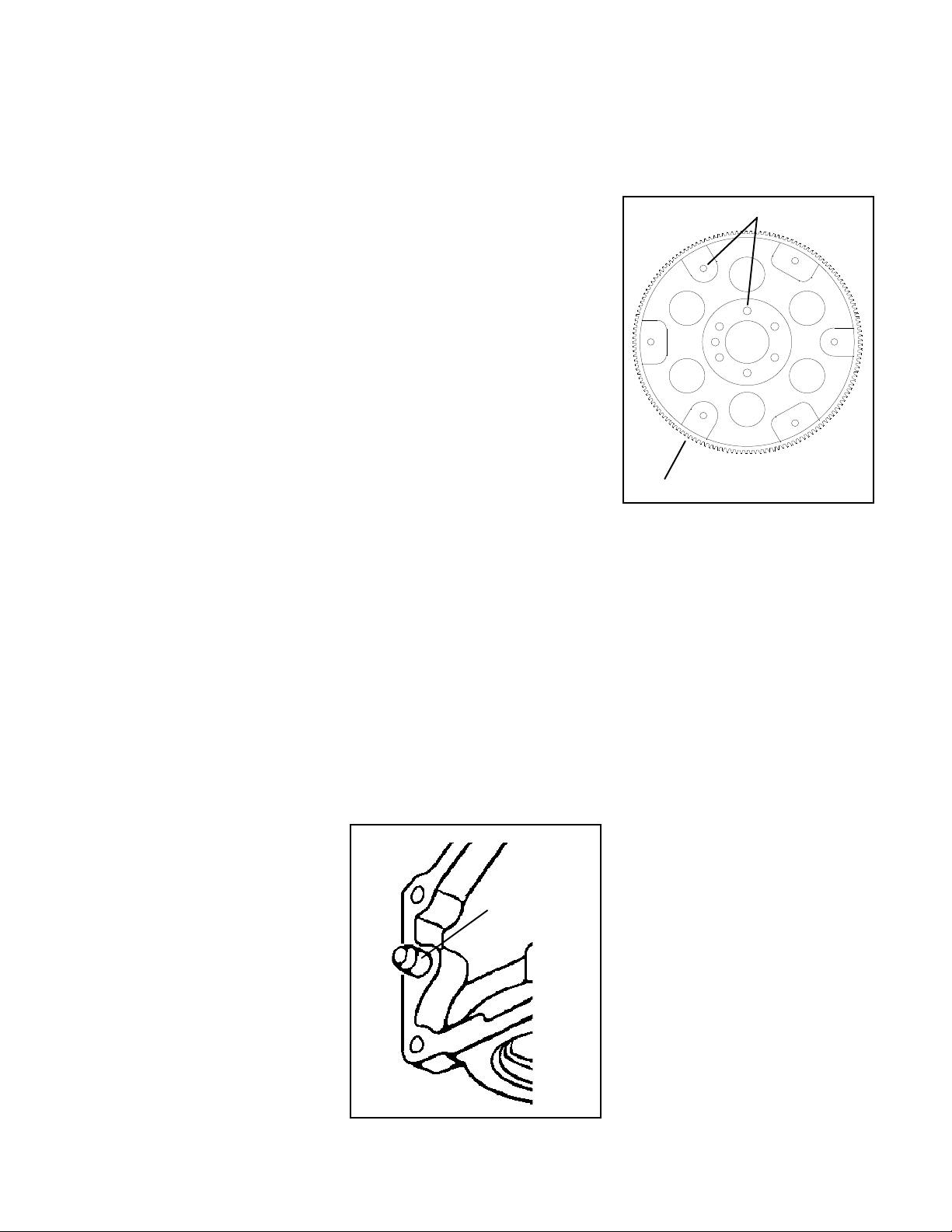
tion by using the B&M Converter Lockup
Control (#70244 for mechanical drive
speedometers, #70248 for GM electronic speed sensor applications).
These torque converters can be
used on the GM 4L60E electronically
controlled transmission used on 1993 96 Chevrolet and GMC trucks and 199497 Camaros and Firebirds. On later
model vehicles equipped with an LS1
type engine, the input shaft is longer and
can only use the 70440 and 70441 converters. For this transmission (4L60E)
you must not make any electrical connection changes. Using it as a non
lockup unit will cause error codes to be
generated and the "Check Engine" light
will be illuminated.
TRANSMISSION REMOVAL
The TH200C, TH200-4R, TH700-R4 and
4L60E are METRIC dimensioned and
have METRIC fasteners.
Because of variations between different vehicle models we cannot cover each
in detail. Instead we will outline a basic
removal and installation procedure. The
sequence of the following procedures
may have to be changed to suit different
vehicle installations. We recommend
you change the transmission fluid and
filter when installing your B&M torque
converter.
Automatic transmissions normally
operate between 150 F and 250 F. It is
recommended that the transmission be
allowed to cool thoroughly to avoid burns
from hot oil and parts. The vehicle must
be off the ground for ease of transmission removal. A vehicle hoist is best,
however jack stands or wheel ramps will
work fine. MAKE SURE THE VEHICLE IS
FIRMLY AND SECURELY SUPPORTED!! A
transmission jack should be used to
prevent personal injury and or transmission damage during removal and installation. Have a small box handy to put nuts
and bolts in so they don’t get lost. A drain
pan to catch oil is also required.
STEP 1. Place drain pan under the
transmission to catch the oil. Drain the oil
pan by first removing the front bolts then
working from the front loosen all the
remaining pan bolts. If the pan sticks use
a screwdriver to pry the pan loose. Again
working from front to rear allow the pan to
tilt down in the front and drain as the
remaining bolts are removed. Once
drained replace the oil pan and hold in
place with one bolt at each corner. To
avoid all this mess next time you service
your transmission, you may want to consider installing a B&M Drain Plug Kit,
#80250 while the oil pan is off the transmission.
STEP 2. Remove the driveshaft (and
torque arm if equipped) being careful not
to drop the U-joint bearings. It’s a good
idea to tape the bearings in place and
wrap the smooth seal diameter of the
slip yoke to prevent damage. It may be
necessary to remove or disconnect any
exhaust pipes and/or hangers during
transmission removal. Remove transfer
case if equipped.
STEP 3. Disconnect the cooler lines.
Use a fitting wrench to avoid damaging
the tube compression nuts. Some models are equipped with a T.V. cable that
runs from the transmission up to the
throttle linkage on the engine. Disconnect the T.V. cable at the engine end and
feed the cable down so it hangs freely
from the transmission. Disconnect any
electrical connectors from the sides of
the case. Be sure to note or label the
position of each corresponding connector. Disconnect the transmission shifter
cable from the shift lever. Disconnect the
speedometer cable or electrical Vehicle
Speed Sensor connector at rear of transmission.
STEP 4. Remove the bell housing dust
cover to expose the torque converter.
Remove the three converter bolts. The
converter should now rotate freely. If it
does not pry the converter back slightly
and free it from the crankshaft.
STEP 5. Place transmission jack under
transmission and take the load off the
crossmember. If the vehicle is equipped
with a rear mounted distributor on the
engine, it is advisable at this point to
remove the distributor cap so it will not be
damaged as the transmission is lowered. Remove the crossmember assembly.
Dowel pin must
protrude 1/2" for
proper transmission engagement
Fig. 2
STEP 6. Remove the bellhousing
bolts, it may be necessary to lower the
transmission slightly to gain clear access to the bolts. Finish lowering the
transmission until engine is balanced
on it’s mounts then pull the transmission
Inspect bolt holes
Inspect ring gear teeth
Fig. 3
slightly away from the engine. Make sure
the converter stays with the transmission and does not fall out. It may be
necessary to remove the dipstick tube at
this point to continue lowering the transmission. Remove transmission and
converter assembly from vehicle.
With the transmission completely out
of the vehicle the torque converter can
easily be removed by pulling it straight off
the front. Drain the torque converter as
completely as possible then cover the
hub to keep out dirt.
STEP 7. Inspect the engine block’s
transmission mounting face to be free of
any dirt or burrs. Make sure both dowel
pins are installed and stick out of the
block at least 1/2" to insure proper transmission alignment, see (Fig. 2).
STEP 8. Remove and inspect the
flexplate for distortion, cracks or damaged ring gear teeth, see (Fig. 3). If the
flexplate shows any damage it should be
replaced. Do not attempt to repair a damaged flexplate.
STEP 9. Assemble the flexplate to
crankshaft and align all holes before
installing the bolts. When properly installed the raised inner lip on the
flexplate should face away from the
crankshaft flange. Torque the bolts to 60
ft.lbs.
STEP 10. Carefully remove the front seal
from the oil pump housing. CAUTION:
The oil pump housing used in these
transmissions is made of an aluminum
2