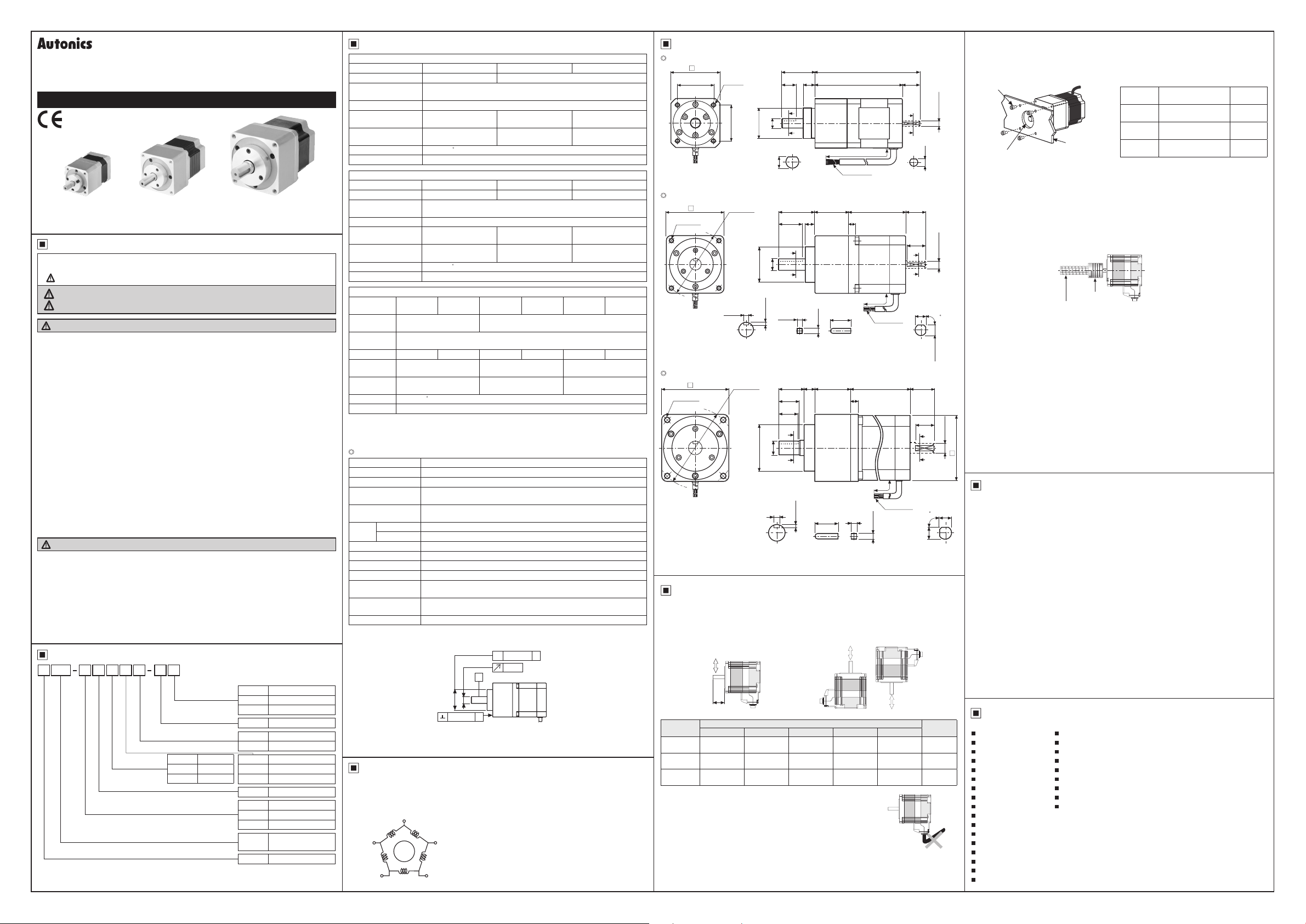
DRW161300AB
Autonics
GEARED TYPE 5 PHASE
STEPPER MOTOR
I N S T R U C T I O N M A N U A L
[Frame size 42mm] [Frame size 60mm] [Frame size 85mm]
Please read the following safety considerations before use.
Safety Considerations
Please observe all safety considerations for safe and proper product operation to avoid
※
hazards.
symbol represents caution due to special circumstances in which hazards may occur.
※
Warning
Caution
Warning
1. Fail-safe device must be installed when using the unit with machinery that may
cause serious injury or substantial economic loss. (e.g. nuclear power control,
medical equipment, ships, vehicles, railways, aircraft, combustion apparatus, safety
equipment, crime/disaster prevention devices, etc.)
Failure to follow this instruction may result in re, personal injury, or economic loss.
2. Fix the unit on the metal plate.
Failure to follow this instruction may result in personal injury, or product and ambient
equipment damage.
3. Do not connect, repair, or inspect the unit while connected to a power source.
Failure to follow this instruction may result in re.
4. Install the unit after considering counter plan against power failure.
Failure to follow this instruction may result in personal injury, or economic loss.
5. Check 'Connections' before wiring.
Failure to follow this instruction may result in re.
6. Do not disassemble or modify the unit.
Failure to follow this instruction may result in electric shock or re.
7. Install the motor in the housing or ground it.
Failure to follow this instruction may result in electronic shock, re, or personal injury.
8. Make sure to install covers on motor rotating components.
Failure to follow this instruction may result in personal injury.
9. Do not touch the unit during or after operation for a while.
Failure to follow this instruction may result in burn due to high temperature of the surface.
10. Turn OFF the power directly when error occurs.
Failure to follow this instruction may result in electric shock, re, or personal injury.
Caution
1. Use the unit within the rated specications.
Failure to follow this instruction may result in re or product damage.
2. Use dry cloth to clean the unit, and do not use water or organic solvent.
Failure to follow this instruction may result in re.
3. Do not use the unit in the place where ammable/explosive/corrosive gas, humidity,
direct sunlight, radiant heat, vibration, impact, or salinity may be present.
Failure to follow this instruction may result in re or explosion.
4. The motor may overheat depending on the environment.
Install the unit at the well-ventilated environment and forced cooling with a cooling fan.
Failure to follow this instruction may result in product damage and degrada ion.
Ordering Information
Max. holding torque
Item
The above specications are subject to change and some models may be discontinued without notice.
※
Be sure to follow cautions written in the instruction manual and the technical descriptions
※
(catalog, homepage).
Thank you for choosing our Autonics product.
Failure to follow these instructions may result in serious injury or death.
Failure to follow these instructions may result in personal injury or product damage.
M 4A 5 5 W10K
Motor phase
Rated current
Motor frame size
L
_______
G 5
-rl
Motor type
Shaft type
Motor length
4 42×42mm
6 60×60mm
Jf---------+--------+-----------1
9 85×85mm
Gear ratio
5 1:5
7.2 1:7.2
10 1:10
G Geared type
No mark Single shaft
W Dual shaft
5 47mm
6 59 5mm
~~
9 98mm
5 5 phase
S 0.75 A/Phase
M 1.4 A/Phase
G 2.8 A/Phase
kgf.cm (Refer to
Square
motor specication)
A Autonics motor
Specications Dimensions
Frame size 42mm
Model A10K-S545(W)-G5 A15K-S545(W)-G7.2 A15K-S545(W)-G10
Max. holding torque
F===+===~=====r:::===~
Rotor moment of
※
2
inertia
Rated current 0.75A/Phase
Basic step angle
Permissible speed
range
Backlash [min] ±35' (0.58
※
3
Weight
Frame size 60mm
Model A35K-M566(W)-G5
Max. holding torque
Rotor moment of
※
2
inertia
Rated current 1.4A/Phase
Basic step angle
Permissible speed
range
Backlash [min] ±20' (0.33
※
3
Weight
Frame size 85mm
Model
Max. holding
※
1
torque
Rotor moment
of inertia
Rated current 1.4A/Phase 2.8A/Phase 1.4A/Phase 2.8A/Phase 1.4A/Phase 2.8A/Phase
Basic step
angle
Permissible
speed range
Backlash [min] ±15' (0 25
※
3
Weight
※
1: Max. holding torque is standard torque when supply the rated current and stop the motor for
comparing the specifications of motors.
※
2: Moment of rotor inertia indicates a part, except Gear Head part.
※
3:
The weight includes packaging. The weight in parenthesis is for unit only.
Common specications
Operation type Planetary Geared type
Insulation class B type (130℃)
Insulation resistance Over 100MΩ (at 500VDC megger) between motor coil-case
Dielectric strength
Temperature rise
Environment
Stop angle error
Shaft vibration
Radial movement
Axial movement
Concentricity for shaft
of setup in-low
Perpendicularity of set-
up plate shaft
Protection structure IP30 (IEC34-5 standard)
※
1: Specifications are for full-step angle, with no-load (values may vary by load size.)
※
2: T.I R (Total Indicator Reading) - The difference between the maximum and minimum readings of a
※
3: Amount of radial shaft displacement when adding a radial load (5N) to the tip of the motor shaft.
※
4: Amount of axial shaft displacement when adding a axial load (10N) to the shaft.
※
Rotation direction of the Motor and the Gear Head output axis is same.
※
Environment resistance is rated at no freezing or condensation.
~
Connection Diagram
00
Autonics 5-phase stepper motors use pentagon wiring methods.
Therefore, it is a proper product for the driver working as a bipolar pentagon driving method of 5
phase stepper motor drivers.
The wiring colors for each phase and lead-wire are as follows:
E Phase
Black
D Phase B Phase
WI
Green
※
1
10 kgf cm (1.0 N.m) 1.5 kgf cm (1.5 N.m)
68 g.cm2 (68x10-7 kg m2)
0.144 /0.072
(Full/Half step)
0 to 360 rpm 0 to 250 rpm 0 to 180 rpm
)
Approx. 0.68kg (approx. 0.58kg)
※
1
35 kgf.cm (3.5 N.m) 40 kgf cm (4.0 N.m) 50 kgf.cm (5 0 N.m)
280 g.cm2 (280x10-7 kg.m2)
0.144 /0.072
(Full/Half step)
0 to 360 rpm 0 to 250 rpm 0 to 180 rpm
)
Approx. 1 57kg (approx. 1.3kg)
A140KM599(W)-G5
140 kgf.cm (14 N.m) 200 kgf.cm (20 N.m)
2,700 g cm2 (2,700x10-7 kg m2)
※
2
0.144 / 0.072
(Full/Half step)
0 to 360 rpm 0 to 250 rpm 0 to 180 rpm
Approx. 4.88kg (approx. 4.4kg)
Ambient temp.
I
Ambient humi.
I
※
1
※
2
※
3
※
A140KG599(W)-G5
I I I
I I I
)
1 kVAC (at 0.75 A/Phase is 0.5 kVAC) 50/60Hz for 1 min between motor coil-
case
5-phase excitation for rated current, below 80℃ at stopped
(resistance method)
-10 to 50℃, storage: -25 to 85℃
35 to 85%RH, storage: 35 to 85%RH
±3' (±0.05 )
0.05mm T.I R.
Max. 0.025mm (Load 5N)
Max. 0.075mm (Load 10N)
0.075mm T.I.R.
0.075mm T.I.R.
dial gauge during one complete revolution of monitored reference.
Ø0 075 A
0.1 /0.05
(Full/Half step)
A40K-M566(W)-G7.2 A50K-M566(W)-G10
0.1 /0 05
(Full/Half step)
A200KM599(W)-G7.2
0.1 / 0 05
(Full/Half step)
A
A200KG599(W)-G7.2
◎ Ø0.075 A
0.05
-----l
Blue
A Phase
Red
C Phase
Orange
or Yellow
0.072 /0.036
(Full/Half step)
0.072 /0 036
(Full/Half step)
A200KM599(W)-G10
0.072 / 0 036
(Full/Half step)
A200KG599(W)-G10
00
Frame size 42mm
42
□
0
※
±0.2
60
88
4-M4
DP 8
±0.2
-0.01
-0.02
31
0
4
-0.03
Sectioned A-A'
-0.01
Ø26
Sectioned A-A' Sectioned B-B'
±0.5
Ø70
0
0
-0.025
Ø37
0
+0.0
2.5
±0 5
Ø104
0
0
-0.03
Ø61
Sectioned A-A'
31
Frame size 60mm
□
4-M5
DP 10
Frame size 85mm
4-M8
DP 15
These dimensions are for dual shaft models. Single shaft models do not include shafts indicated in
the dotted lines.
Installation
1. Mounting direction
Motor can be mounted in any directions-facing up, facing down and side ways. No matter which
direction motors to be mounted, be sure not to apply overhung or thrust load on the shaft.
Refer to the table below for allowable shaft overhung load / thrust load.
※
1: The distance from the shaft in front (mm)
Motor size
Frame size
42mm
Frame size
60mm
1 1 1 1 1 1 1 r
Frame size
85mm
Do not apply excessive force on motor cable when mounting motors.
Do not forcibly pull or insert the cable. t may cause poor connection or
disconnection of the cable.
In case of frequent cable movement required application, proper safety
countermeasures must be ensured.
Side ways
Overhung
load
1
※
n
ru
D
The distance from the shaft in front (mm), Allowable overhung load [kgf (N)]
D=0 D=5 D=10 D=15 D=20
7 3 (73) 8.4 (84) 10 (100) 12.3 (123)
25 (250) 27 (270) 30 (300) 34 (340) 39 (390) 10 (100)
48 (480) 54 (540) 60 (600) 68 (680) 79 (790) 30 (300)
-0 015
Ø8
-0 018
Ø12
-0.018
Ø18
6
7
4
+0.1
0
28
A
A'
38
25 10
A
A'
0
-0.03
±1
33
26
25
A
A'
0
+0.1
3.5
±1
±1
35
25
0
-0.03
4
Parallel key
4714
±0.2
25
Parallel key
Thrust
load
.)
~ y
89.5
74 51012
Min. 600
AWG 26
UL 3266
±1
59.5
7
.
---
Min. 600
±0.2
AWG 24
UL 3266
Sectioned B-B'
98
10
Min. 600
0
6
0
-0.03
-0.03
6
Facing up, down
-
15
B
B'
21
20
B
---
..
B'
7.5
AWG 22
UL 3266
Sectioned B-B'
Thrust
load
=
:q
(unit: mm)
±1
-0.003
-0.008
Ø5
4.5
±1
±0.25
0
-0.015
Ø8
- I
·~
±0.15
90
,
±0.15
7.5
±1
32
±0.25
25
0
-0 018
B
Ø14
85
B'
±0.15
13
90
±0.15
13
i·
Allowable
thrust load
5 (50)
i~
2. Motor mounting
With considering heat radiation and vibration isolation, mount the motor as tight as possible against
a metal panel having high thermal conductivity such as iron or aluminum.
When mounting motors, use hexagon socket screws, spring washers and flat washers.
Refer to the table below for allowable thickness of mounting plate and using bolt.
Hexagon socket screw
Mounting plate
Flange In Low
(Counter bore or Through hole)
3. Connection with load
When connecting the load, be sure of the center, tension of the belt, and parallel of the pulley.
When connecting the load such as a pulley
and shock. Tighten the screw for a coupling or a pulley not to be unscrewed.
If the center of the load is not matched to that of shaft, it may cause severe vibration, shaft damage
or shortened life cycle of bearings.
When connecting a coupling or a pulley on the motor shaft, be sure of damage of the motor shaft
and the motor shaft bearing.
Please contact us if necessary.
4. Installation condition
Install the motor in a place that meets certain conditions specified below.
It may cause product damage if instructions are not following.
①
The inner housing installed indoor
(This unit is manufactured for attaching to equipment. Install a ventilation device.)
②
Within -10 to 50
③
Within 35 to 85%RH (at non-dew status) of ambient humidity
④
The place without explosive, flammable and corrosive gas
⑤
The place without direct ray of light
⑥
The place where dust or metal scrap is not entered into the unit
⑦
The place where water
⑧
The place where strong alkali or acidity does not exist closely
⑨
The place where easy heat dissipation could be made
⑩
The place where no continuous vibration or severe shock
⑪
The place with less salt content
⑫
The place with less electronic noise occurs by welding machine, motor
⑬
The place where no radioactive substances and magnetic fields exist.
t shall be no vacuum status as well.
Do not disassemble or modify motor shaft to connect with the load.
Ball screw or TM screw
℃ (at non-freezing status) of ambient temperature
Flexible coupling
※
Use Autonics flexible coupling (ERB Series).
, oil, or other liquid are not touched
Motor size
Frame size
42mm
Frame size
60mm
Frame size
85mm
, a belt, be sure of the allowable thrust load, radial load,
The thickness of
mounting plate
Min. 5mm M4
Min. 8mm M5
Min. 12mm M8
, etc.
Using bolt
Cautions during Use
1. Follow instruc ions in 'Cautions during Use'. Otherwise, It may cause unexpected accidents.
2. Using motors at low temperature may cause reducing ball bearing's grease and gear part
consistency and friction torque is increased.
Start the motor in a steady manner since motor's torque is not to be influenced.
3. Be careful of backlash when positioning the motors in bo h CW/CCW directions.
Geared type stepper motor use he high accuracy gear for positioning and it realizes low
backlash. However, when positioning the motor in bo h CW/CCW directions, it may cause
problem.
Therefore, make sure that motor positioning will be made in one single direction in case of
geared type motors.
4. For using motor, it is recommended to maintenance and inspection regularly.
Unwinding bolts and connec
①
Strange sound from ball bearing of the unit
②
Damage and stress of lead cable of the unit
③
Connection error wi h driver
④
Inconsistency between the axis of motor output and the center, concentric (eccentric,
⑤
declination) of the load, etc.
5. This unit may be used in the following environments.
Indoors (in the environment condition rated in 'Specifications')
①
Altitude max. 2,000m
②
Pollution degree 2
③
Installation category II
④
ion parts for he unit installation and load connection
Major Products
Photoelectric Sensors Temperature Controllers
Fiber Optic Sensors Temperature/Humidity Transducers
Door Sensors SSRs/Power Controllers
Door Side Sensors Counters
Area Sensors Timers
Proximity Sensors Panel Meters
Pressure Sensors Tachometer/Pulse (Rate) Meters
■
Rotary Encoders Display Units
Connector/Sockets Sensor Controllers
Switching Mode Power Supplies
Control Switches/Lamps/Buzzers
~
I/O Terminal Blocks & Cables
Stepper Motors/Drivers/Motion Controllers
■
Graphic/Logic Panels
■
Field Network Devices
■
Laser Marking System (Fiber, CO₂, Nd: YAG)
■
Laser Welding/Cutting System
■
■
■
■
■
■
■
■
■
■
DRW16130 0A B