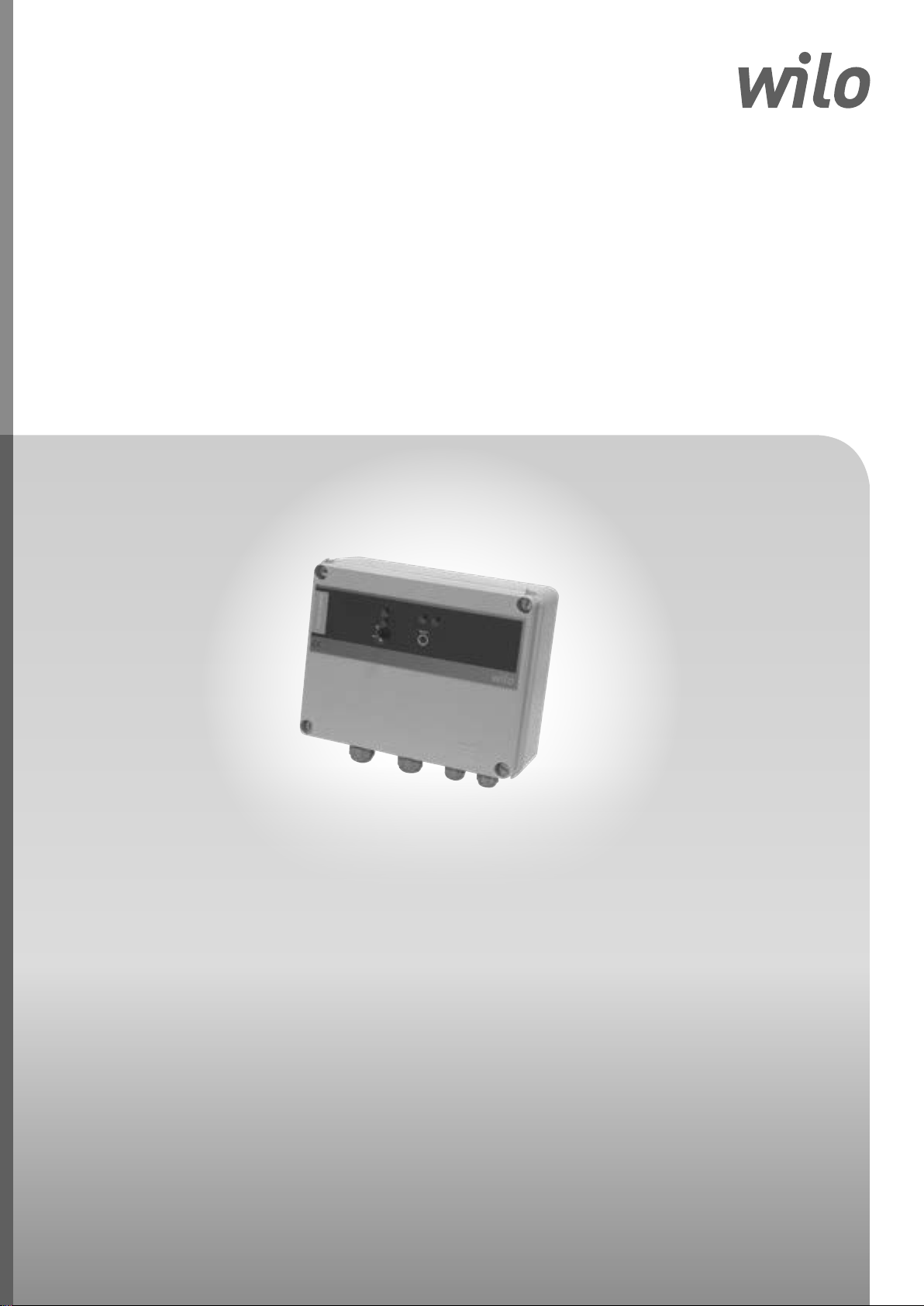
Pioneering for You
Wilo-Control ESK, PSK
de Einbau- und Betriebsanleitung
en Installation and operating instructions
fr Notice de montage et de mise en service
Instrucciones de instalación y funcionamiento
es
2 543 184-Ed.01 / 2015-12-Wilo
it
Istruzioni di montaggio, uso e manutenzione
ru Инструкцияпомонтажуиэксплуатации
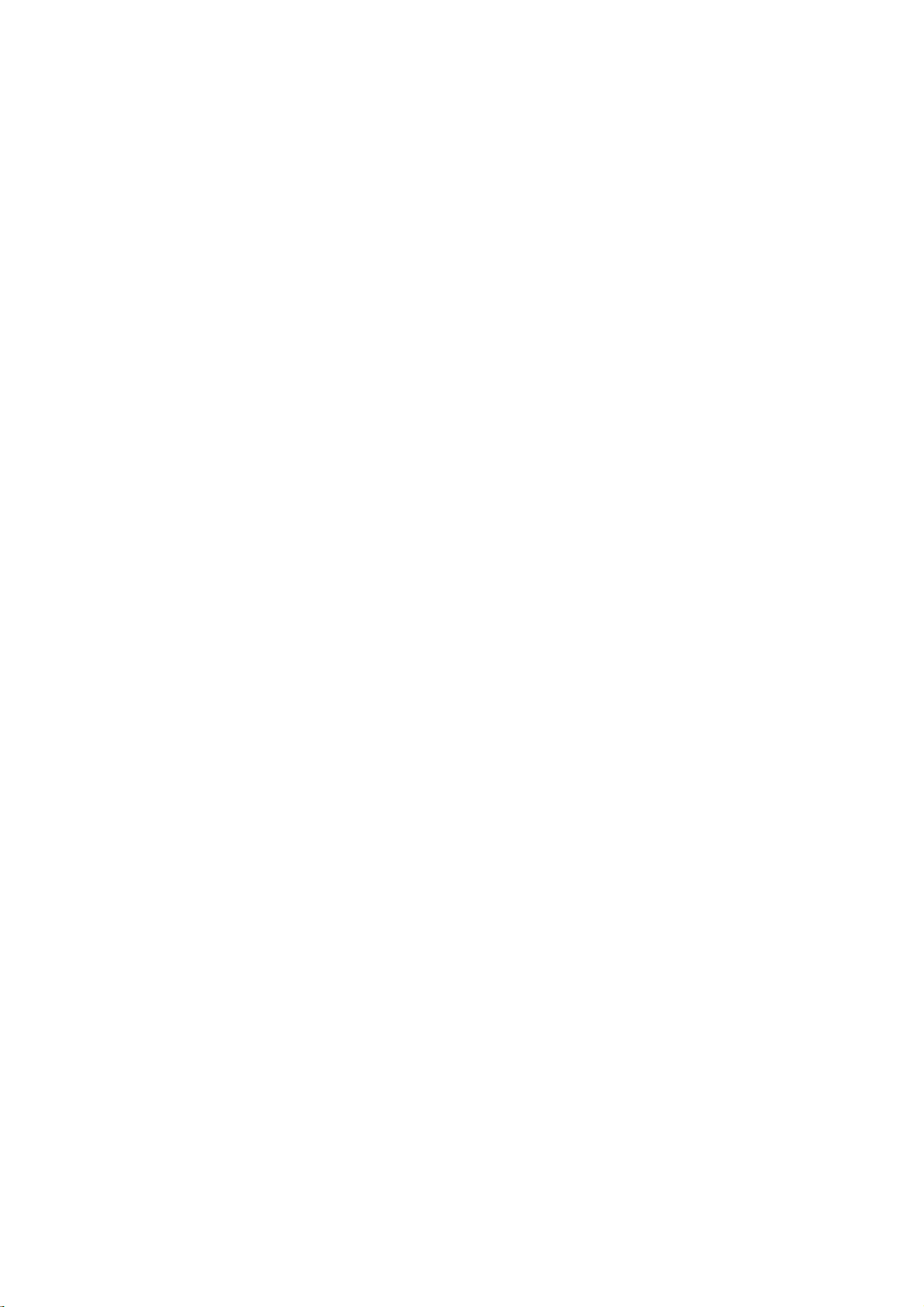
English
1 General ..................................................................................................................................................11
2 Safety.....................................................................................................................................................11
2.1 Symbols and signal words in the operating instructions ................................................................................11
2.2 Personnel qualifications.......................................................................................................................................11
2.3 Danger in the event of non-observance of the safety instructions ..............................................................11
2.4 Safety consciousness on the job ........................................................................................................................ 11
2.5 Safety instructions for the operator .................................................................................................................12
2.6 Safety instructions for installation and maintenance work ...........................................................................12
2.7 Unauthorised modification and manufacture of spare parts ..........................................................................12
2.8 Improper use ........................................................................................................................................................12
3 Transport and interim storage ...........................................................................................................12
4 Intended use .........................................................................................................................................12
5 Product information ..........................................................................................................................13
5.1 Technical data ....................................................................................................................................................13
5.2 Scope of delivery .................................................................................................................................................. 13
5.3 Accessories (optional) .........................................................................................................................................13
6 Description ...........................................................................................................................................13
6.1 Front side of the switchgear ..............................................................................................................................13
6.2 Single components in the housing ................................................................................................................... 13
7 Installation and electrical connection ...............................................................................................14
7.1 Installation ............................................................................................................................................................14
7.2 Electrical connection ...........................................................................................................................................14
7.2.1 Connection of the pump engine .........................................................................................................................14
7.2.2 Connection of external elements ......................................................................................................................14
7.2.3 Mains connection .................................................................................................................................................14
8 Commissioning .....................................................................................................................................14
8.1 Selecting the operating mode ............................................................................................................................14
8.2 Settings and tests ................................................................................................................................................14
8.2.1 Overload protection ............................................................................................................................................14
8.2.2 Check direction of rotation (3-phase motor only) ..........................................................................................15
8.3 Selecting the operating mode ............................................................................................................................15
8.3.1 Installation with two electrodes ........................................................................................................................ 15
8.3.2 Installation with one electrode ..........................................................................................................................15
8.3.3 Installation with flow meter ...............................................................................................................................15
8.3.4 Pumping operation ..............................................................................................................................................15
8.3.5 Pressure boosting................................................................................................................................................. 16
9 Maintenance..........................................................................................................................................16
10 Faults, causes and remedies................................................................................................................16
11 Spare parts ............................................................................................................................................17
10 WILO SE 12/2015