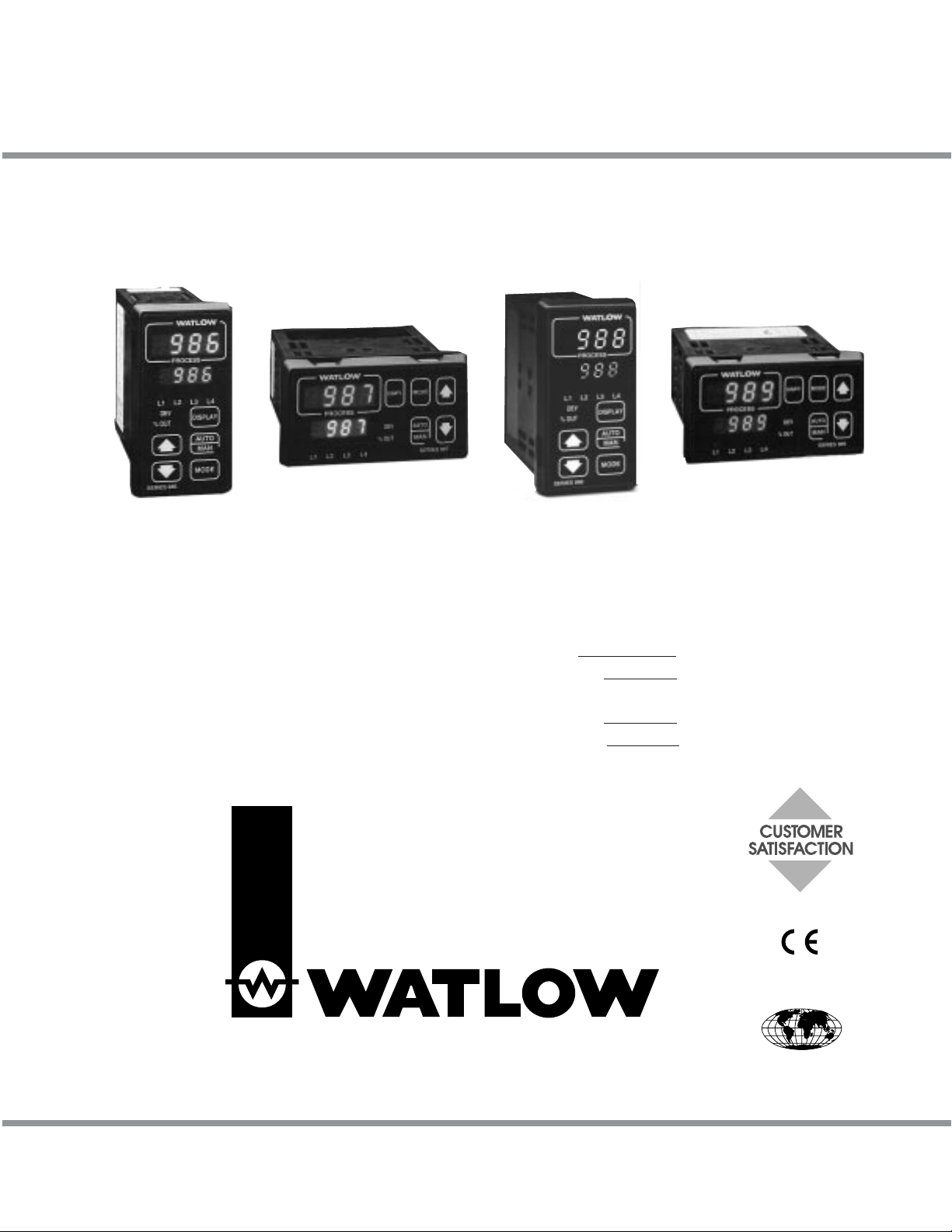
1/8 DIN Microprocessor-Based Temperature/Process Controller
0600-0009-0001 Rev AA
April 2002
Supersedes: 0600-0009-0001 Rev Y
$10.00
Made in the U.S.A.
User’s Manual
Includes 986, 987, 988 and 989
User Levels:
• New User........................... go to Introduction
• Experienced User................... go to page 4.1
Installers:
• Set-up..................................... go to page 1.1
• Wiring & Installation................ go to page 2.1
1241 Bundy Boulevard., Winona, Minnesota USA
Phone: +1 (507) 454-5300, Fax: +1 (507) 452-4507 http://www.watlow.com
TOTAL
3 Year Warranty
ISO 9001
Registered Company
Winona, Minnesota USA

WATLOW Series 988 User’s ManualTable of Contents
Ta ble of Contents
Introduction to the Watlow Series 988
Controllers
ii Using this Manual
ii Document Every Step
iii Notes, Cautions and Warnings
iii Technical Assistance
iii We Value Your Feedback
Chapter 1
Hardware Setup
1.1 Dip Switch Locations and Functions
Chapter 2
Installation and Wiring
2.1 Panel Cutout and Dimensions
2.2 Installing the Series 988
2.4 Wiring the Series 988
2.4 Input-to-output Isolation
2.4 Power Wiring
2.5 Sensor Installation Guidelines
2.6 Wiring Example
2.8 Input 1 Wiring
2.9 Input 2 Wiring
2.11 Event Input 1 Wiring
2.12 Output 1 Wiring
2.13 Output 2 Wiring
2.14 Output 3 Wiring
2.15 Output 4 Wiring
Chapter 3
Front Panel and Display Loop
3.1 Keys and Displays
3.2 Display Loop
Chapter 4
The Setup Menus
4.1 Navigating the Setup Menus
4.2 Input Menu
4.18 Output Menu
4.34 Global Menu
4.44 Communications Menu
Chapter 5
The Operation Menus
5.1 Navigating the Operation Menus
5.2 System Menu
5.9 PID A and PID B Menus
Chapter 6
The Factory Menus
6.1 Navigating the Factory Menus
6.2 Panel Lockout Menu
6.7 Diagnostics Menu
6.13 Calibration Menu
Chapter 7
Tuning, Manual Operation,
Alarms and Error Codes
7.1 Auto-tuning (Heat and/or Cool)
7.2 Manual Tuning
7.4 Manual and Automatic Operation
7.5 Changing the Output 3 Alarm Jumper
7.6 Using Alarms
7.8 Error Code E1 and E2 Messages
7.9 Error Code Actions
Chapter 8
General Software
8.2 Burst Fire
8.4 Communications
8.6 Dead Band
8.8 Digital Events
8.10 Heater Current
8.12 Input Filter
8.14 Input Linearization
8.16 Ramp to Set Point
8.18 Remote Set Point
8.20 Retransmit
8.22 Slidewire Feedback
Appendix
A.2 Glossary
A.4 Specifications
A.5 Warranty and Returns
A.6 Index
A.10 Menu Overview
A.11 Model Number – Ordering Information
A.12 Declaration of Conformity
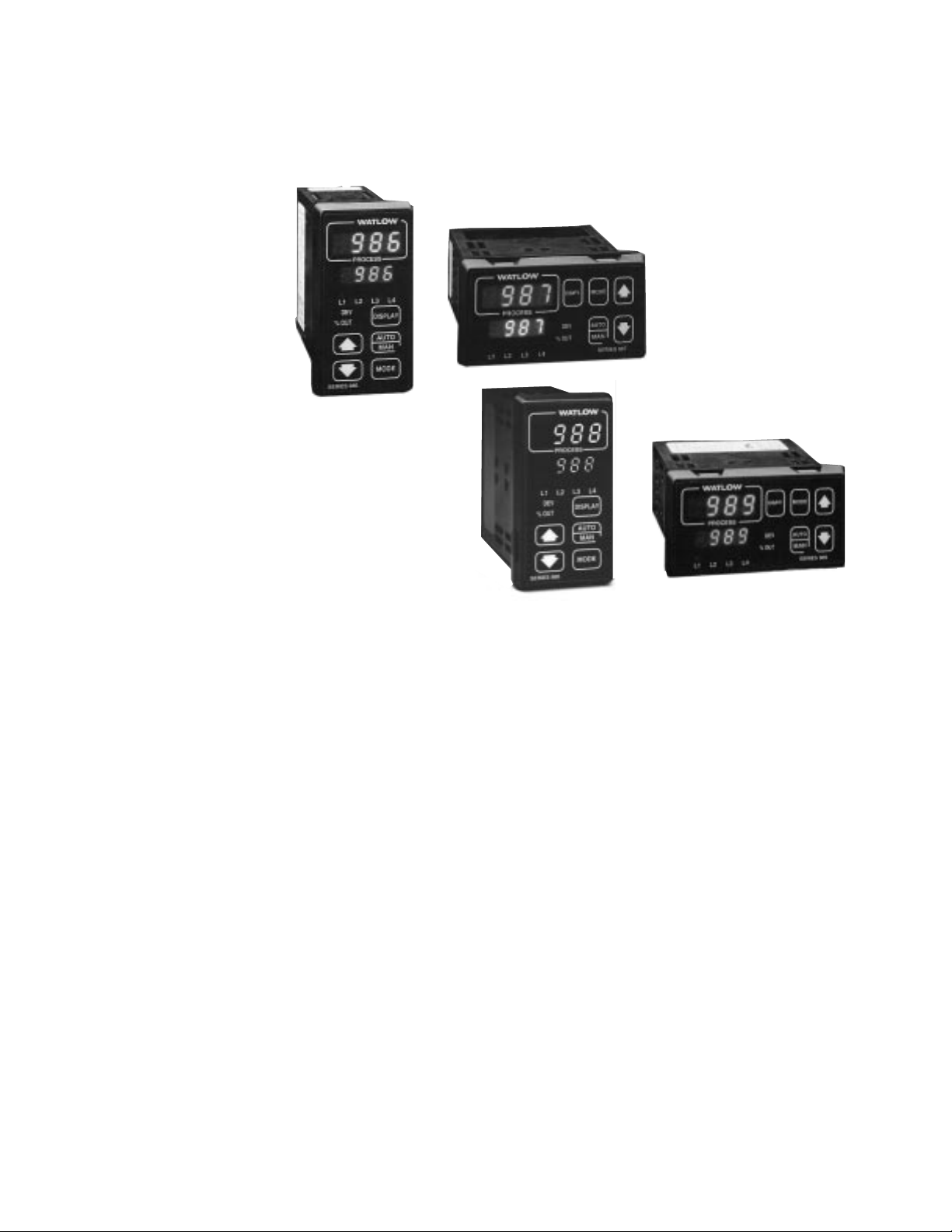
WATLOW Series 988 User’s Manual i
Introduction
Introduction to the
Watlow Series 988 Controllers
Figure Int.1 The Series 988
Controllers.
Watlow’s Series 988 controllers set a new standard in the controller industry by packing an impressive array of features into an 1/8-DIN package.
No other controller offers the flexibility, compact size and durability of the
Series 988. It can control a wide variety of temperature and process applications, with a broad range of input and output options that allow control
of virtually any process variable.
The Series 988 is the only 1/8 DIN controller that can provide single-unit
cascade control of a process. Its other features include heater current
monitoring, remote set point input, ratio control and valve control through
slidewire feedback. The Series 988 also delivers expanded auto-tuning
capabilities, increased alarm functionality and several unique control algorithms.
When we refer to the “Series 988” controller, we refer also to the horizontal
and low-voltage versions of the Series 988: the 986, 987, 988 and 989. We
recommend that you read all of this manual’s introduction to familiarize
yourself with the conventions and content of this manual and the steps to
setting up a Series 988 controller. Make sure you understand the
“Caution” and “Warning” symbols we use in the book.
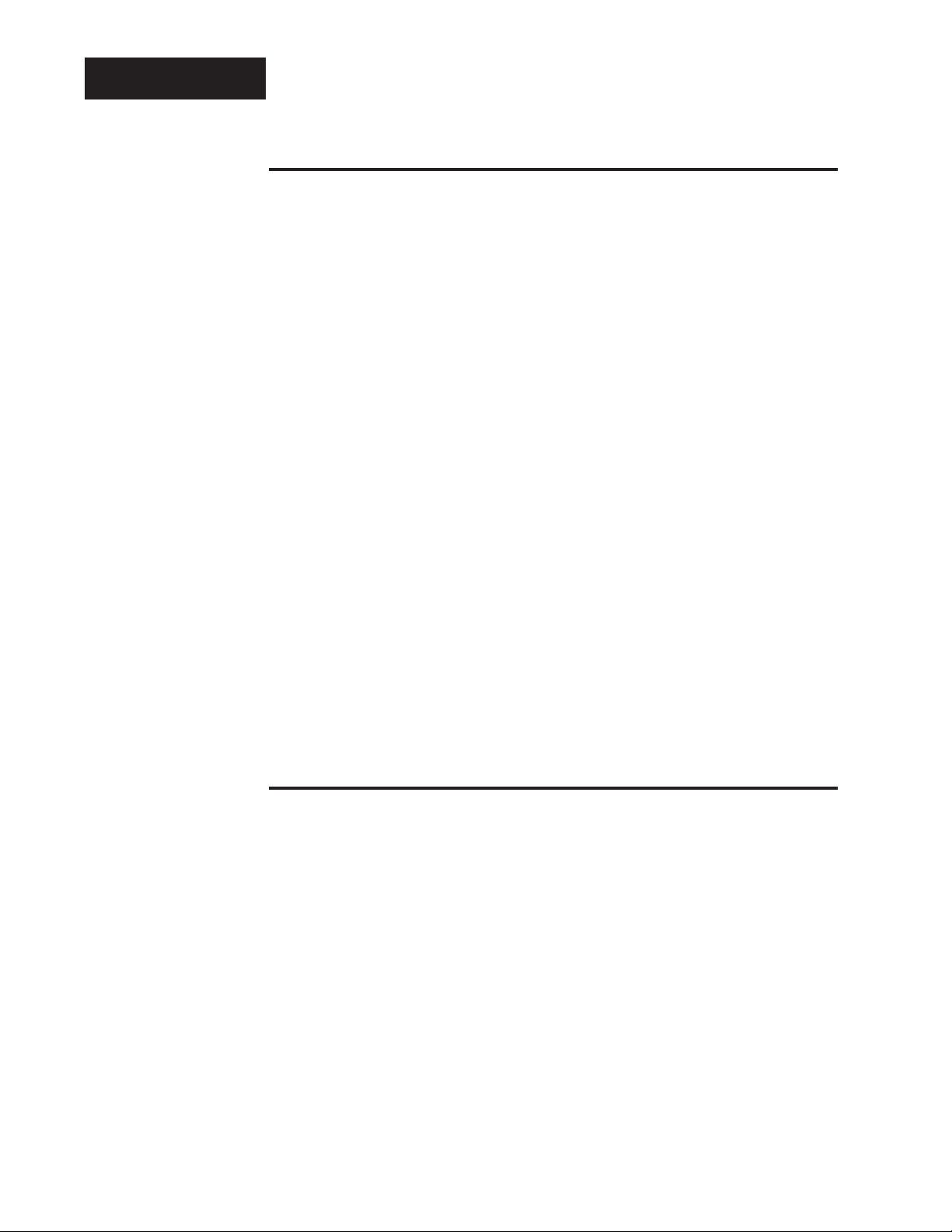
ii WATLOW Series 988 User’s Manual
Introduction
Introduction
Using this Manual
This manual provides the information you will need to install and operate
a Series 988 controller.
If you need information about Series 988 configurations and model numbers, refer to the Appendix of this manual or, for more detailed information, to Optimizing Your Process System with the Series 988 Controller: An
Application Guide for the Watlow Series 988 Family.
If your Series 988 controller will be used for data communications, you
will also need our communications manual, Data Communications with the
Watlow Series 988 Family of Controllers (green cover).
Series 988 controllers are calibrated in the factory, but if you need to do
periodic calibration you will need our calibration manual, Calibrating
Watlow Process Controllers, (blue cover).
This manual explains the five steps of setting up a Series 988 controller:
1. Set and document all of the DIP switches, if applicable: Chapter 1.
2. Mount the controller: Chapter 2.
3. Wire and document the controller wiring: Chapter 2.
4. Configure and document the controller software: Chapters 3-6.
5. Run, test and adjust your application. Update documentation.
Chapters 7 and 8 and the Appendix provide detailed advice, definitions
and specifications along with application examples to help you optimize
the safety and performance of your application. Use the Table of Contents
and Index to find specific information.
Document Every Step
The Series 988 provides powerful and complex features. Carefully document each step of the setup and any subsequent changes. This will make
it much easier to change, adjust and troubleshoot your application.
Make the configuration documentation available to engineers and technicians, on all shifts, who may need to work with the Series 988. We provide
space in this manual to record configurations. You may prefer to photocopy the blank forms and keep them in a separate binder. However you
maintain your documentation, be sure to replace all old copies of the documentation with updated versions whenever the controller configuration is
changed.
˜
NOTE:
The Menu Overview
in the Appendix
shows all the
menus and
prompts.
˜
NOTE:
The 12-digit number
is printed on the top
of the stickers on
each side of the
controller’s case
and on the righthand or top circuit
board.
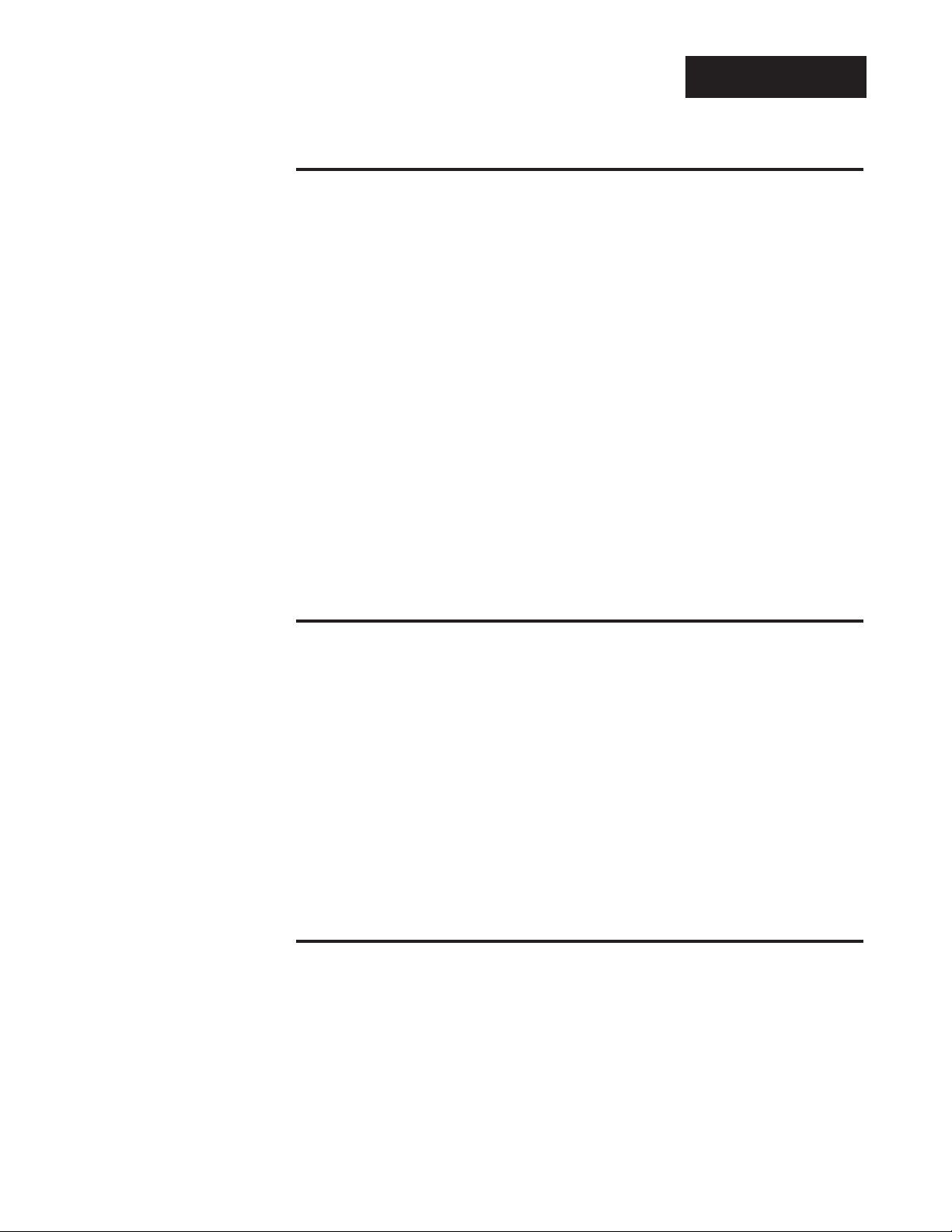
Introduction
WATLOW Series 988 User’s Manual iii
Introduction
Notes, Cautions and Warnings
We use note, caution and warning symbols throughout this book to draw
your attention to important operational and safety information.
A bold text “NOTE” marks a short message in the margin to alert you to
an important detail.
A bold text “CAUTION” safety alert appears with information that is
important for protecting your equipment and performance. Be especially
careful to read and follow all cautions that apply to your application.
A bold text “WARNING” safety alert appears with information that is
important for protecting you, others and equipment from damage. Pay
very close attention to all warnings that apply to your application.
The ç symbol (an exclamation point in a triangle) precedes a general
CAUTION or WARNING statement.
The Ó symbol (a lightning bolt in a triangle) precedes an electric shock
hazard CAUTION or WARNING safety statement.
Technical Assistance
If you encounter a problem with your Watlow controller, review all of your
configuration information for each step of the setup to verify that your
selections are consistent with your applications.
If the problem persists after checking all the steps, you can get technical
assistance by calling Watlow Controls at (507) 454-5300, between 7 a.m.
and 7 p.m. CST, and asking for an applications engineer. When you call,
have the following information on hand: the controller’s model number
(the 12-digit number is printed on the top of the stickers on each side of
the controller’s case and on the right-hand or top circuit board); your
user’s manual; all configuration information; and the Diagnostics Menu
readings.
We Value Your Feedback
Your comments and suggestions on this manual are welcome. Please send
them to, Technical Writer, Watlow Winona, 1241 Bundy Blvd., P.O. Box
5580, Winona, MN 55987-5580 or call (507) 454-5300 or fax (507) 452-
4507. The Series 988 User’s Manual is copyrighted by Watlow Winona,
Inc., © April 2002, with all rights reserved. (2220)
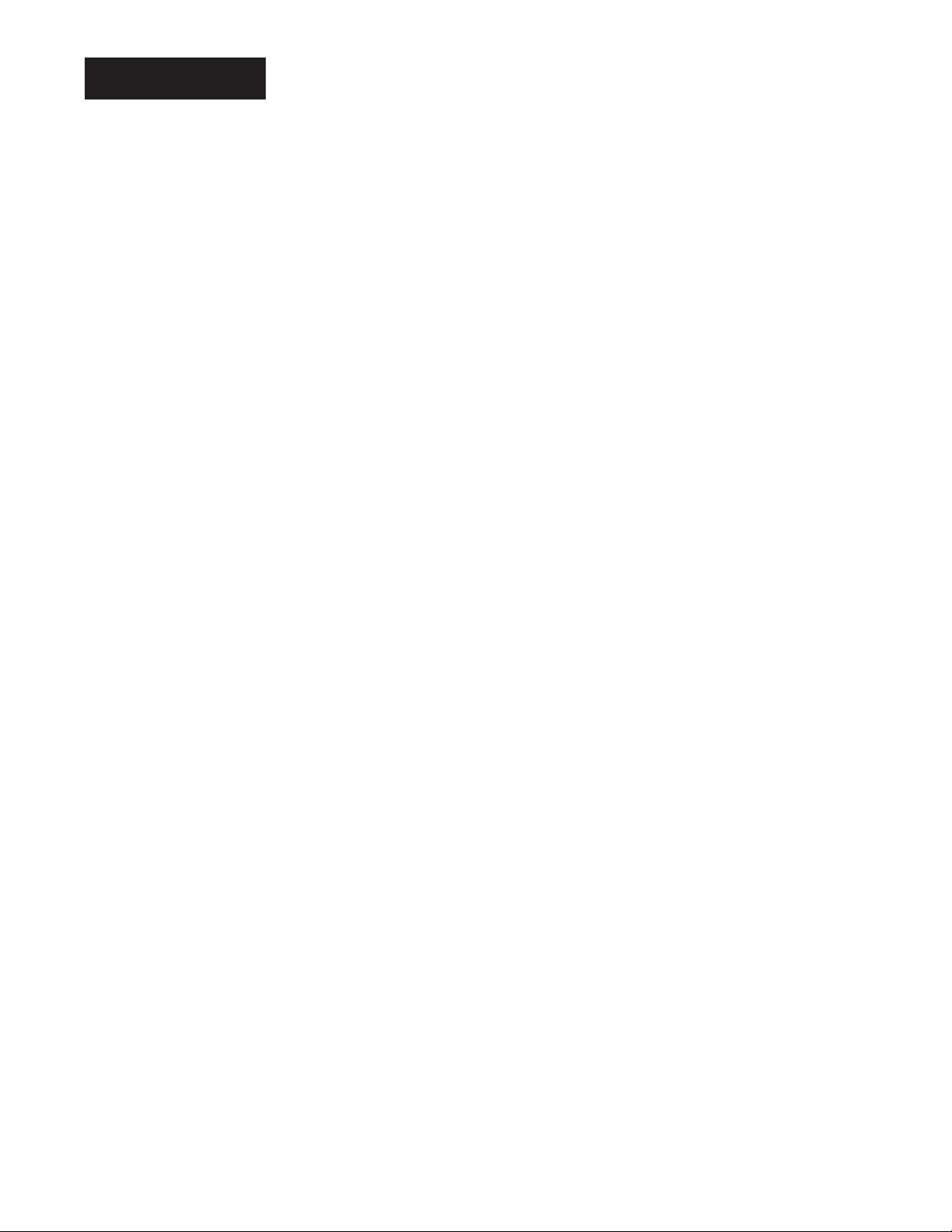
iv WATLOW Series 988 User’s Manual
Introduction
Notes
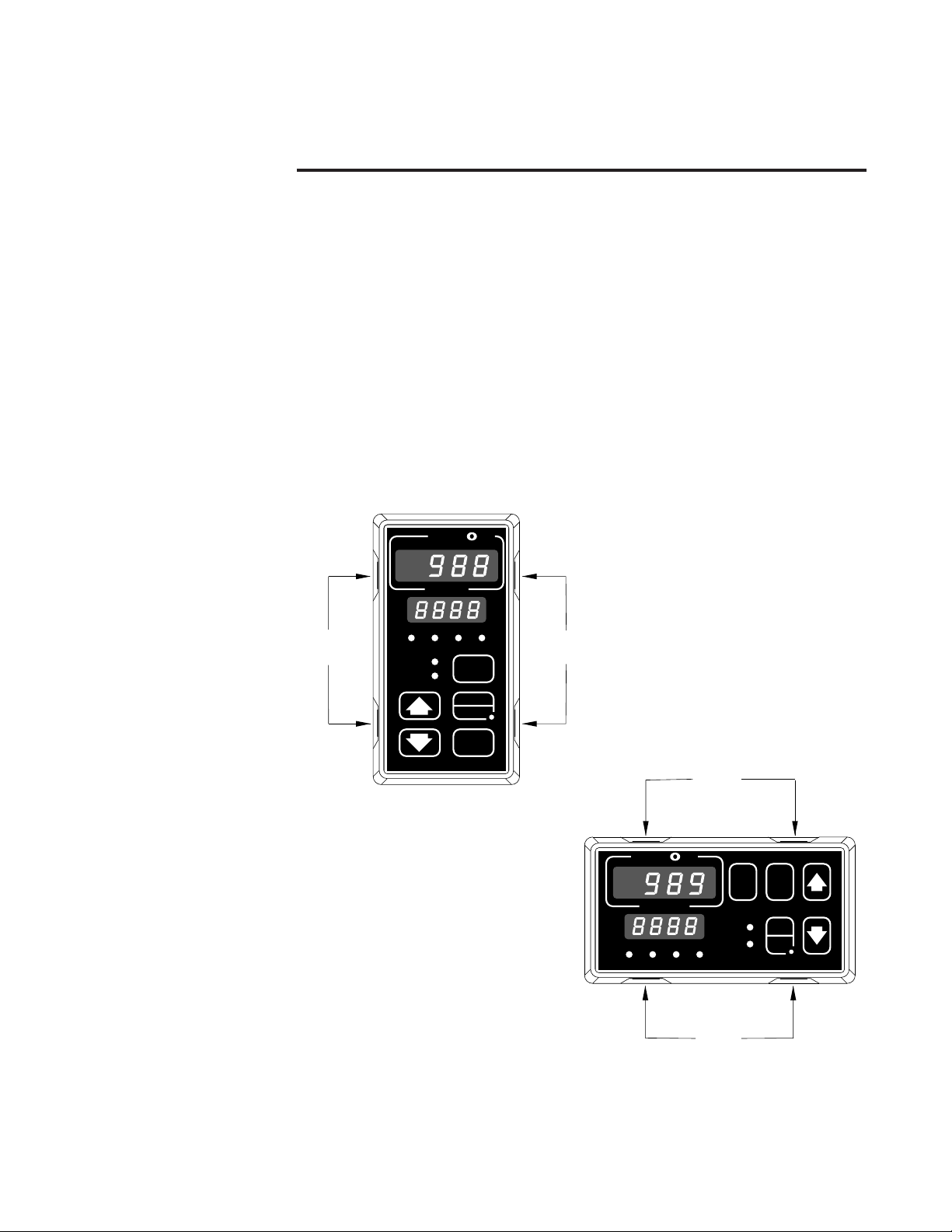
WATLOW Series 988 User’s Manual 1.1
Hardware Setup, Chapter 1
Chapter 1 Hardware Setup
DIP Switch Locations and Functions
The Watlow Series 988 has at least one and as many as six dual in-line
package (DIP) switches inside the controller, depending on the model
number. They allow users to configure the controller for a variety of input
sensors, to provide power for external signal conditioners or to lockout
front panel access to some functions.
To set any DIP switch:
• Remove the controller from the case by pressing firmly on the two release
tabs on one side or the top of the bezel until they unsnap. Then firmly
press the two release tabs on the opposite side or the bottom of the control until they unsnap. You will need to gently rock the bezel back and
forth to release it from the chassis.
• Use the illustrations on the following pages to locate and set each DIP switch.
Figure 1.1 - Press
the release tabs to
remove the controller chassis.
Release
Tabs
A
W
PROCESS
L1 L2 L3 L4
DEV
% OUT
SERIES 988
W
TL
DISPLAY
AUTO
MAN
MODE
Release
Tabs
W
A
TL
W
PROCESS
L1 L2 L3 L4
Release
Tabs
DEV
% OUT
DSPY
MODE
AUTO
MAN
SERIES 989
Release
Tabs
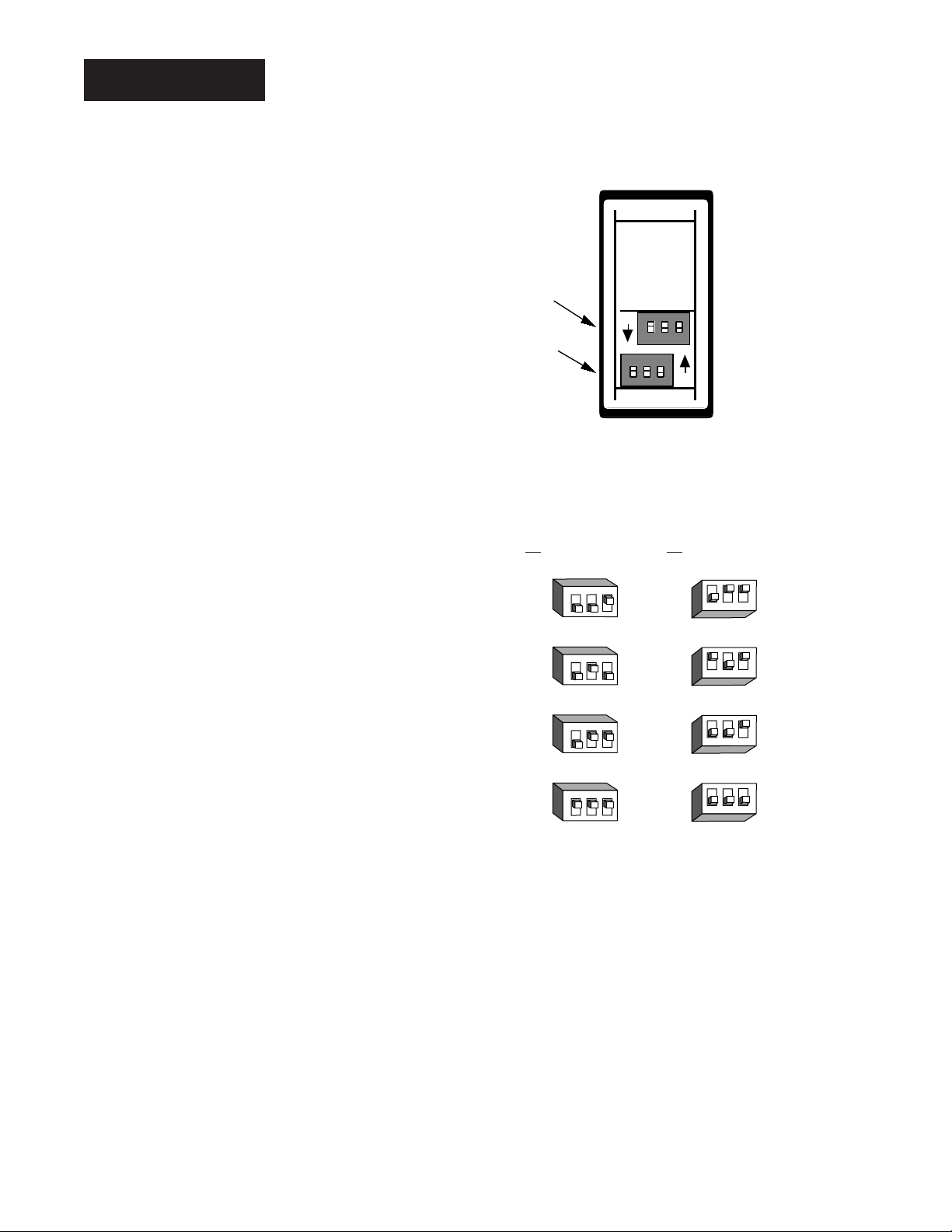
1.2 WATLOW Series 988 User’s Manual
Hardware Setup, Chapter 1
DIP Switches
Figure 1.2 Input DIP switches.
Input 1 Input 2
(98 _ _-2_ _ _-_ _ _ _) (98 _ _-_2_ _-_ _ _ _)
RTD (100 Ω)
thermocouple: R, S or B
thermocouple: J, K, T, N, E, C, D, Pt2
or 0-50mV (high impedance)
0-20 or 4-20mA; 0-5, 1-5 or 0-10V
1. Set the input DIP
switches to match the
sensors you are using
in your application.
Only controllers with
model number 98_ _2_ _ _-_ _ _ _ or 98_ __2_ _-_ _ _ _ have an
input DIP switch.
˜
NOTE:
The Input 2 DIP
switch is mounted
upside down.
˜
NOTE:
Only controllers
with the indicated
model numbers
have these DIP
switches.
Input 2 DIP
Input 1 DIP
ON
ON
Controller Chassis
Rear View
123
O
N
↑
123
O
N
↑
123
O
N
↑
123
O
N
↑
↑
N
O
123
↑
N
O
123
↑
N
O
123
↑
N
O
123
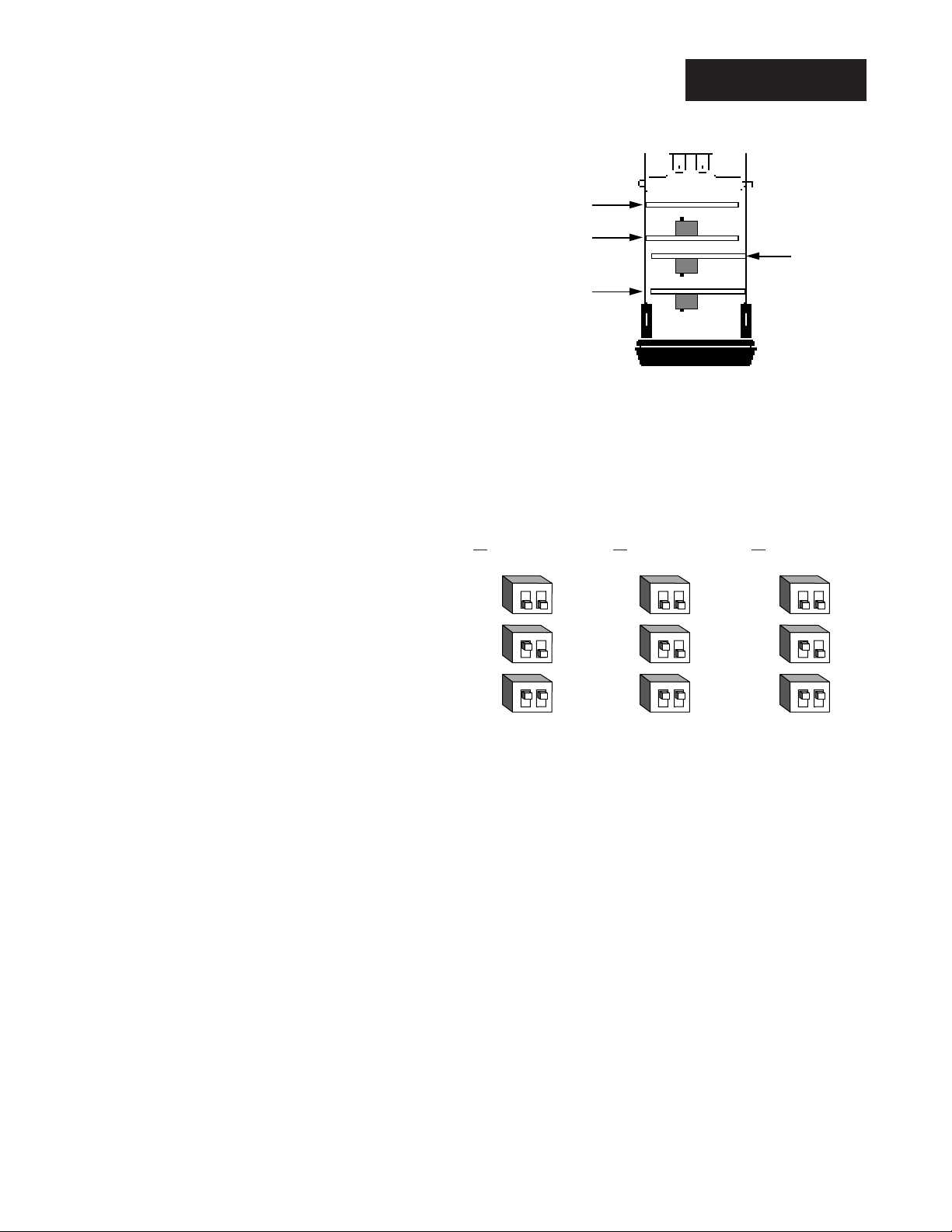
DIP Switches
WATLOW Series 988 User’s Manual 1.3
Hardware Setup, Chapter 1
Output 2
Option Board and DIP
Output 4
Option Board and DIP
Contro ller Chassis
Top View (986 & 988)
Left-side V iew (987 & 989)
Output 3
Option Board and DIP
Output 1
Option Board
offon
on
on
off
off
Figure 1.3 External signal conditioner power supply DIPs.
Output 2 Output 3 Output 4
(98 _ _-_ _ _T-_ _ _ _) (98 _ _-_ _ _ _-T_ _ _) (98 _ _-_ _ _ _-_T_ _)
20V ± 5% @ 30mA
12V ± 5% @ 30mA
5V ± 5% @ 30mA
2. Set DIP switches for
outputs equipped with
an external signal conditioner power supply.
Only controllers with
model number 98_ _-_
_ _T-_ _ _ _, 98_ _-_ _ _
_-T_ _ _ or 98_ _-_ _ _
_-_T_ _ have an external signal conditioner
power supply.
˜
NOTE:
For other voltages
or current settings
contact the factory.
3. When the DIP switches are set, gently insert the controller chassis into
the case and push it firmly into place until all four tabs snap into place.
˜
NOTE:
Only controllers
with the indicated
model numbers
have these DIP
switches.
12
O
N
↑
12
O
N
↑
12
O
N
↑
12
O
N
↑
12
O
N
↑
12
O
N
↑
12
O
N
↑
12
O
N
↑
12
O
N
↑
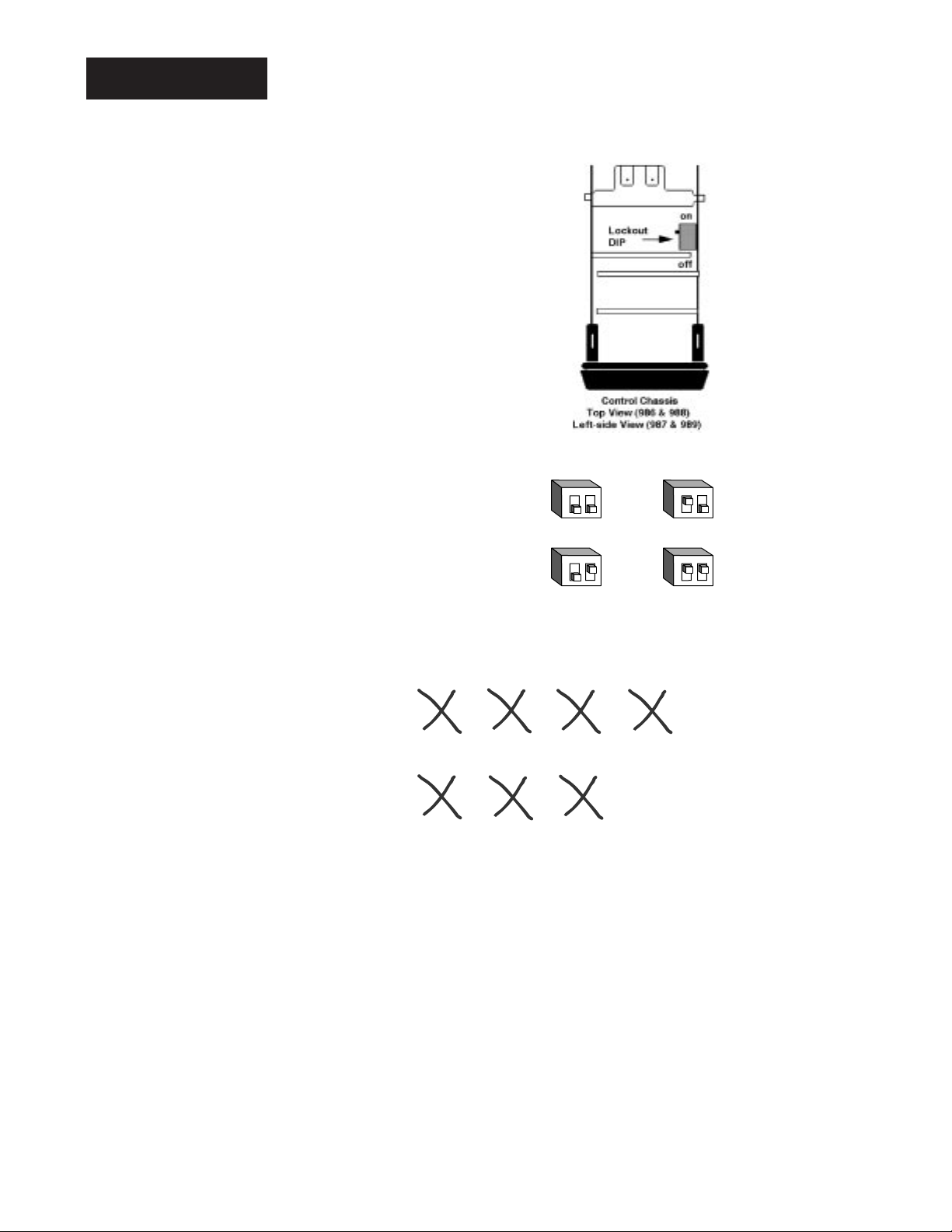
1.4 WATLOW Series 988 User’s Manual
Hardware Setup, Chapter 1
DIP Switches
Figure 1.4 Lockout DIP switch.
no hardware lockout or
(Switch 1 has no effect.)
lockout Setup and Factory menus or
(Switch 1 has no effect.)
4. The lockout DIP switch
hides the Setup Menus
(Input, Output, Global and
Communications) and the
Factory Menus (Panel
Lockout, Diagnostics and
Calibration). All units have
a lockout DIP switch.
ç
CAUTION:
The lockout DIP
switch makes the
Setup and Factory
menus unavailable.
Configure all the
Setup and Factory
menus before locking them out.
Failure to do so
could result in damage to equipment in
the event of a setup
error.
12
O
N
↑
12
O
N
↑
Input
[InPt]
[`SEt]
Panel
Lockout
[PLOC]
[Fcty]
Output Global
[OtPt]
[`SEt]
Diagnostics Calibration
[diAG]
[Fcty]
[GLbL]
[`SEt]
[`CAL]
[Fcty]
Communications
[CO
[`SEt]
12
O
N
↑
12
O
N
↑

WATLOW Series 988 User’s Manual 2.1
Installation and Wiring, Chapter 2
Chapter 2 Installation and Wiring
Figure 2.1 Series 988 and
Series 989
dimensions and
terminal number
layout.
˜
NOTE:
Adjustable mounting brackets can be
side-mounted.
˜
NOTE:
Space panel
cutouts at least 1.66
inches (42.2mm)
apart.
˜
NOTE:
Holes can be cut in
the panel using a
Greenlee 1/8 DIN
Hydraulic Kit
#60068 (punch
#60069, die #60070).
W
A
TL
W
PROCESS
L1 L2 L3 L4
DEV
% OUT
SERIES 988
2.18"
(55 mm)
DISPLAY
AUTO
MAN
MODE
4.03"
(102mm)
(102mm)
W
A
TL
W
PROCESS
L1 L2 L3 L4
4.03"
DEV
% OUT
DSPY
MODE
AUTO
MAN
2.18"
(55 mm)
SERIES 989
Panel Cutout
Maximum Panel
Thickness
0.38" (9.65mm)
3.62" + 0.03 -0.00
(92mm + 0.8)
1.77 + 0.02 -0.00
(45mm + 0.6)
1
21
2
3
4
5
6
7
8
9
231024
Panel
0.68"
(17 mm)
11
22
12
13
14
15
16
17
18
19
10
98 765432
23
24
19 18 17 16 15 14 13 12
20
4.06"
(103 mm)
Adjustable
Mounting Bracket
21
22
1
11
20
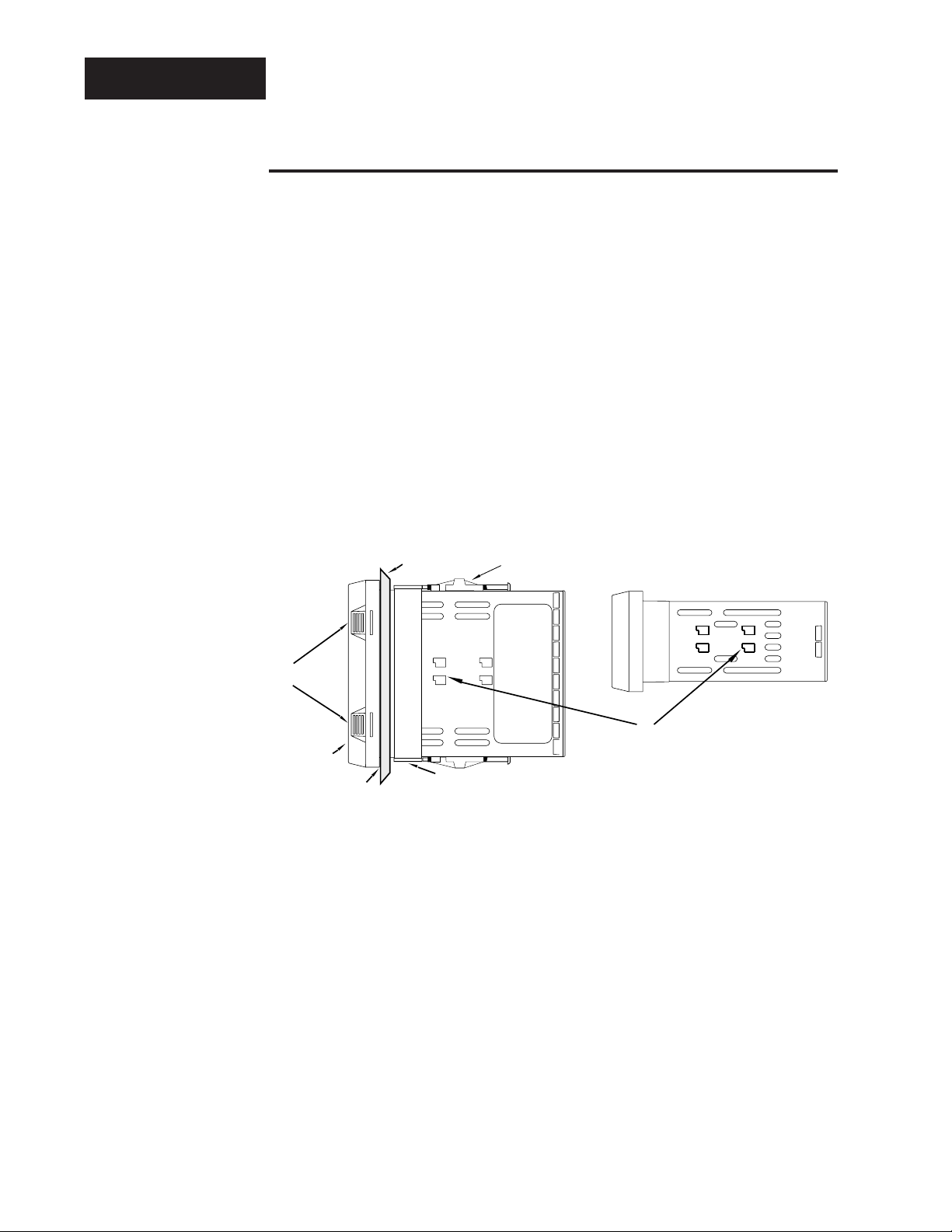
2.2 WATLOW Series 988 User’s Manual
Installation and Wiring, Chapter 2
Installation
Installing the Series 988
Installing and mounting requires access to the back of the panel.
1. Make a panel cutout using the panel cutout dimensions from the previous page.
2. To remove the controller chassis from its case, press in firmly on the two
tabs on one side or the top of the bezel until they unsnap, then unsnap
the two tabs on the opposite side or the bottom. Pull the chassis out of
the case by gently rocking it.
3. Slide the case into the panel cutout. Check to see that the gasket is not
twisted, and is seated within the case bezel flush with the panel. Slide
Panel
Adjustable
Mounting Bracket
Bezel
External Gasket
Mounting Collar
Release Tabs
Top and Bottom (986 or 988)
or Side (987 or 989) View
Mounting Slots
Side (986 or 988)
or Top and Bottom (987 or 989) View
˜
NOTE:
Removing the controller chassis from
its case makes
mounting easier.
Figure 2.2 Side and top view.
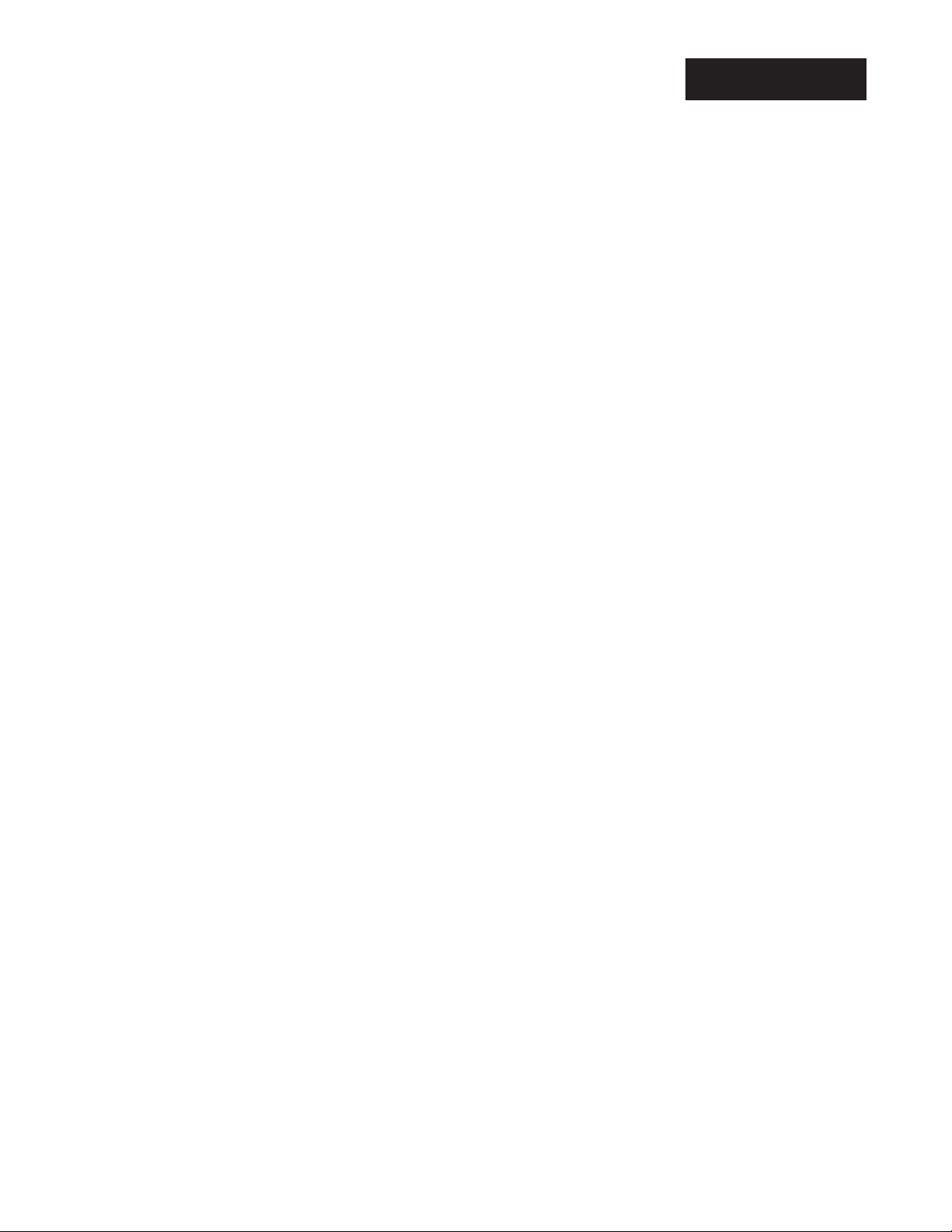
WATLOW Series 988 User’s Manual 2.3
Installation and Wiring, Chapter 2
the mounting collar over the back of the control.
4. Loosen the mounting bracket screws enough to allow for the mounting
collar and panel thickness. Place each mounting bracket into the
mounting slots (head of the screw facing the back of the controller).
Push each bracket backward then down to secure it to the control
case. To guarantee a proper NEMA 4X seal, Series 986 and 988
units (vertical) must have the mounting brackets located on either
side of the unit. When installing Series 987 and 989 units (horizontal) the brackets must be on the top and bottom of the unit.
5. Make sure the case is seated properly. Tighten the installation screws
firmly against the mounting collar to secure the unit. To ensure a
NEMA 4X seal, there should be no space between the bezel and
panel. Overtightening the screws will distort the case and make it diffi-
cult to remove or replace the controller.
6. Make sure the inside gasket is seated properly and not twisted.
Insert the controller chassis into its case and press the bezel until all
four tabs snap.
7. To release the mounting brackets, loosen the mounting bracket screws
and push the brackets forward, then pull it up and out.
ç
CAUTION:
Follow the installation procedure
exactly to guarantee
a proper NEMA 4X
seal. Make sure the
gasket between the
panel and the rim of
the case is not
twisted and is seated properly. Failure
to do so could
result in damage to
equipment.
Installation
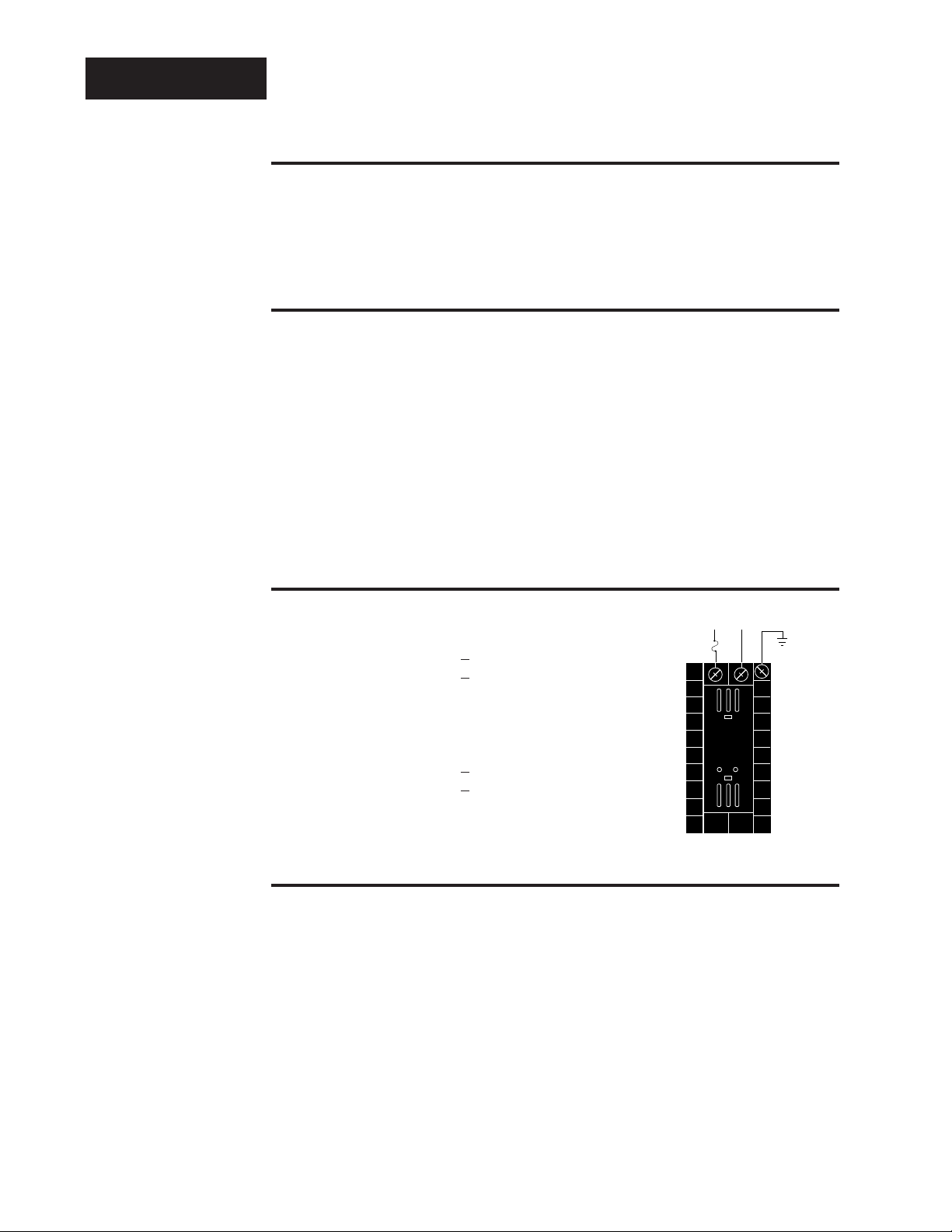
2.4 WATLOW Series 988 User’s Manual
Installation and Wiring, Chapter 2
Wiring
Wiring the Series 988
Wiring options depend on the model number and DIP switch settings.
Check the terminal designation stickers on either side of the controller
and compare your model number to those shown here and with the model
number breakdown on the inside back cover of this manual.
Input-to-output Isolation
The Series 988 uses optical isolation between the analog inputs and the
controller outputs/digital input. This isolation provides a 500VÅ (ac) barrier to prevent ground loops when using grounded sensors and/or peripheral equipment.
Here is a breakdown of the isolation barriers:
• Analog inputs 1 and 2 are grouped together.
• Outputs 1 through 4 and the standard event input are grouped together.
This does not apply to Output 4 when configured as communications.
• The digital communications output (4) is separate from the above
groups.
Power Wiring
100 to 240V‡‡(ac/dc) nominal, (85 to 264 actual)
Vertical Package 98 8 _ - _ _ _ _ - _ _ _ _
Horizontal Package 98 9
_ - _ _ _ _ - _ _ _ _
24 to 28 V‡‡(ac/dc) nominal, (20 to 30 actual)
Vertical Package 98 6
_ - _ _ _ _ - _ _ _ _
Horizontal Package 98 7 _ - _ _ _ _ - _ _ _ _
Sensor Installation Guidelines
Maintain isolation between input 1 and input 2 to prevent a ground loop.
A ground loop may cause incorrect readings, dashes across the upper display or the display of error codes.
Thermocouple input: Extension wire for thermocouples must be of the
same alloy as the thermocouple itself to limit errors.
Using grounded thermocouples for both input 1 and input 2 may create
ground loop problems. To correct this problem, replace at least one of the
grounded thermocouples with an ungrounded thermocouple. If the application requires grounded thermocouples, use an isolated transmitter,
such as a Watlow Gordon 5702 isolated transmitter.
fuse
22
21
earth ground
11
L2L1
+
-
∫
WARNING:
To avoid potential
electric shock, use
National Electric
Code (NEC) safety
practices when
wiring and connecting this unit to a
power source and
to electrical sensors
or peripheral
devices. Failure to
do so could result
in injury or death.
˜
NOTE:
Input-to-output isolation is defeated
when the external
signal conditioner
power supply is
used to power a
transmitter connected to input 1 or
input 2.
Figure 2.4 Power wiring.
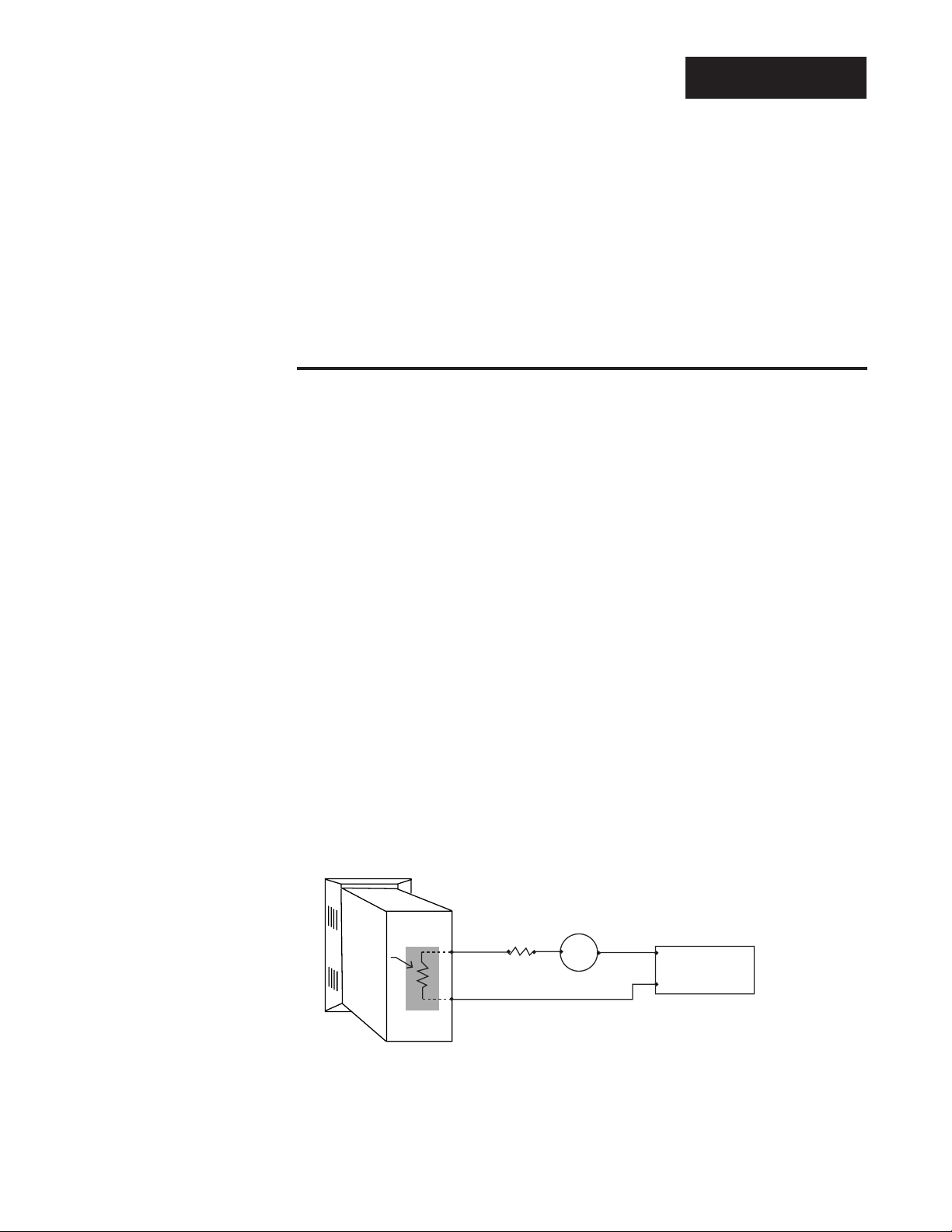
WATLOW Series 988 User’s Manual 2.5
Installation and Wiring, Chapter 2
Wiring
RTD (100 Ω) input: Each 1Ω of lead wire resistance can cause a +2°C
error when using a two-wire RTD. A three-wire RTD sensor overcomes this
problem. All three wires must have the same electrical resistance (i.e.,
same gauge, same length, multi-stranded or solid, same metal).
Process input: Isolation must be maintained between input 1 and input
2. If both input 1 and input 2 are used as process inputs, a separate
power supply and transmitter must be used for each input. Output option
T (external signal conditioner power supply) can be used to supply power
for only one input.
Wiring 0-20 and 4-20mA Process Inputs
Certain “transmitters” used in process input applications are producing internal resistor failures in the Watlow Series 988 family of controllers. This is only
apparent with the Series 988 family 1/8 DIN units with Process Inputs selected
(0-20mA or 4-20mA dc only).
We are noticing that an external resistor is required to prevent a high in-rush
current which burns out the Series 988 family controllers’ 7-ohm internal
resistor. This high in-rush current occurs initially on “power-up.” If the transmitter turns full on for a split second during power-up, the available current
weakens or damages the internal resistor.
Example: 20V / 7 ohms = 2,857mA (too much!).
The wiring diagram example below shows an application where a customer is
using a 4-20mA dc transmitter and power supply to feed the input of a Series
988 controller. The Rx range (100 to 400 ohms) for the external resistor is recommended. We suggest starting with 250 ohms.
Example: Customer is using a 24VÎ (dc) power supply to power up the 4-20mA
dc transmitter that inputs to the Series 988 terminals 8 (-) and 10 (+). To figure out what the internal Series 988’s handling current is for the 0-20mA or 420mA dc input to the Series 988 controllers, we need to apply Ohm’s Law: The
square root of Watts divided by Resistance equals Current. Applying that formula to the example below produces the following: Square Root of (0.125 Watts
/ 7 ohms) = 134 mA dc (handling input current). This is the acceptable input
current for the Series 988 universal input board.
Reminder, the input impedance of 7 ohms handles the majority of our customer applications; the external resistor (Rx) is only for certain
transducers/transmitters that spike on power-up or power-down. Please make
sure your customer’s transmitter / transducer fall within our Series 988 family
(1/8 DIN) of controllers’ Process Input specification of 7 ohms input impedance.
ç
CAUTION:
The Series 988 will
not function with
two grounded thermocouple inputs.
Avoid using a
grounded thermocouple for both
input 1 and input 2.
Failure to follow this
guideline could
result in damage to
equipment.
NOTE:
Input-to-output isolation is defeated
when the external
signal conditioner
power supply is
used to power a
transmitter connected to input 1 or
input 2.
988 Process
Input Control
Internal
Resistor
7Ω
1/8 Watt
+
—
R
x
100 to 400
ohms
4-20mA dc
Transmitter
—
+
+
24VÎ (dc)
Power Supply
—

2.6 WATLOW Series 988 User’s Manual
Installation and Wiring, Chapter 2
Wiring Example
Figure 2.6 System wiring
example.
∫
WARNING:
To avoid potential
electric shock, use
National Electric
Code (NEC) safety
practices when
wiring and connecting this unit to a
power source and
to electrical sensors or peripheral
devices. Failure to
do so could result
in injury or death.
ç
WARNING:
Install high or low
temperature limit
control protection
in systems where
an over temperature fault condition
could present a fire
hazard or other hazard. Failure to
install temperature
limit control protection where a potential hazard exists
could result in damage to equipment,
property and injury
to personnel.
ç
WARNING:
To avoid damage to
property and equipment, and/or injury
of loss of life, use
National Electric
Code (NEC) standard wiring practices to install and
operate the Series
988. Failure to do
so could result in
such damage,
and/or injury or
death.
L1
120VÅ (ac)
L2
eart h ground
(+)
9
10
(-)
red
120VÅ (ac)
1
2
3
4
5
6
7
8
9
10
11
12
13
high- li mit
mechani cal
fuse
11
2221
(+)
12
(-)
13
988A-10C A-AAR R
rear view
L1
1
1
1 2
1
proc ess sens or li mit sensor
3
4
(+)
5
(-)
1 CR-1
8
11
17
coil
contactor
10+11
heater
Series 146
limit control
R
15
13 14
-
norm ally open
momentary s witch
1CR
16
SSR- 240-10A- DC1
out
12
43
in
21 22
9
10
910
12
13
(+)
14
(-)
15
dc i nput
SSR
heater
Series 988
988A-10CA-AARR
temperature control
12 13
67
in
3-32VÎ (dc)
(+)
out
24-240VÅ (ac)
12
13
14
10
11
4
146E-1601-3000
limit control
11
SSR-240-10A-DC1
solid-state relay, dc input
(-)
146E-1601-3000
3
5
18
high-temperature light
high- temper ature
light
optional
L2
2
2
2
2

WATLOW Series 988 User’s Manual 2.7
Installation and Wiring, Chapter 2
Wiring Notes
ç
WARNING:
To avoid damage to
property and equipment, and/or injury
of loss of life, use
National Electric
Code (NEC) standard wiring practices to install and
operate the Series
988. Failure to do
so could result in
such damage,
and/or injury or
death.
Figure 2.7 Wiring notes.
˜
NOTE:
Sketch in your
application on this
page or a copy of it.
See wiring examples in this chapter
and in the Appendix.
L1 L2
earth ground
11
21 22
power

2.8 WATLOW Series 988 User’s Manual
Installation and Wiring, Chapter 2
Input 1 Wiring
Figure 2.8c —
0-5VÎÎ, 1-5VÎÎor 0-10VÎÎ(dc) Process
Universal signal conditioner
98 _ _ - 2 _ _ _ - _ _ _ _
Input impedance: 10KΩ
Figure 2.8a — Thermocouple or 0-50mV (high impedance)
Thermocouple only
98 _ _ - 1 _ _ _ - _ _ _ _ (no DIP switches)
Universal signal conditioner
98 _ _ - 2 _ _ _ - _ _ _ _
Input impedance: 20MΩ
Figure 2.8b — RTD (2- or 3-wire) (100 Ω)
Universal signal conditioner
98 _ _ - 2 _ _ _ - _ _ _ _
Figure 2.8d —
0-20mA or 4-20mA Process
Universal signal conditioner
98 _ _ - 2 _ _ _ - _ _ _ _
Input impedance: 7Ω
DIP Switch
Setting
R, S, B
DIP Settings
J, K, T, N, C, E, D, Pt2,
0-50mV DIP Settings
DIP Switch
Setting
DIP Switch
Setting
˜
NOTE:
Successful installation requires five
steps:
• Model number and
software choice
(Appendix);
• DIP switch settings (Chapter 1);
• Sensor match
(Chapter 2 and
Appendix);
• Sensor installation
(Chapter 2); and
• Wiring (Chapter 2).
Jumper
#9 to #10
for 2-wire
RTD
ç
CAUTION:
An external resistor
may be required for
0-20mA and 4-20mA
process wiring to
prevent a high inrush current which
could burn out the
controller’s 7-ohm
resistor. See page
2.5 for recommendations.
123
O
N
↑
123
O
N
↑
+
9
-
10
123
O
N
↑
S1
8
9
S2
10
8
S1
9
S2
10
S3
123
O
N
↑
123
O
N
↑
9-+
10
-
8
10
+

Figure 2.9d — 0-20mA or 4-20mA Process
Universal signal conditioner
98 _ _ - _ 2 _ _ - _ _ _ _
Input impedance: 7Ω
Figure 2.9c —
0-5VÎÎ, 1-5VÎÎor 0-10VÎÎ(dc) Process
Universal signal conditioner
98 _ _ - _ 2 _ _ - _ _ _ _
Input impedance: 10KΩ
Figure 2.9b —
RTD (2- or 3-wire) (100 Ω)
Universal signal conditioner
98 _ _ - _ 2 _ _ - _ _ _ _
WATLOW Series 988 User’s Manual 2.9
Installation and Wiring, Chapter 2
Input 2 Wiring
Figure 2.9a — Thermocouple or 0-50mV (high impedance)
Thermocouple only
98 _ _ - _ 1 _ _ - _ _ _ _ (no DIP switches)
Universal signal conditioner
98 _ _ - _ 2 _ _ - _ _ _ _
Input impedance: 20MΩ
Jumper
#19 to #20
for 2-wire
RTD
DIP Switch
Setting
R, S, B
DIP Settings
J, K, T, N, C, E, D, Pt2,
0-50mV DIP Settings
DIP Switch
Setting
NOTE:
Successful installation requires five
steps:
• Model number and
software choice
(Appendix);
• DIP switch settings (Chapter 1);
• Sensor match
(Chapter 2 and
Appendix);
• Sensor installation
(Chapter 2); and
• Wiring (Chapter 2).
ç
CAUTION:
An external resistor
may be required for
0-20mA and 4-20mA
process wiring to
prevent a high inrush current which
could burn out the
controller’s 7-ohm
resistor. See page
2.5 for recommendations.
↑
N
O
123
↑
N
O
123
↑
N
O
123
19
20
-
+
19
20
18S2S1
19
S3
20
+
-
0-50mV
↑
N
O
123
↑
N
O
123
19-+
20
18
20
-
+
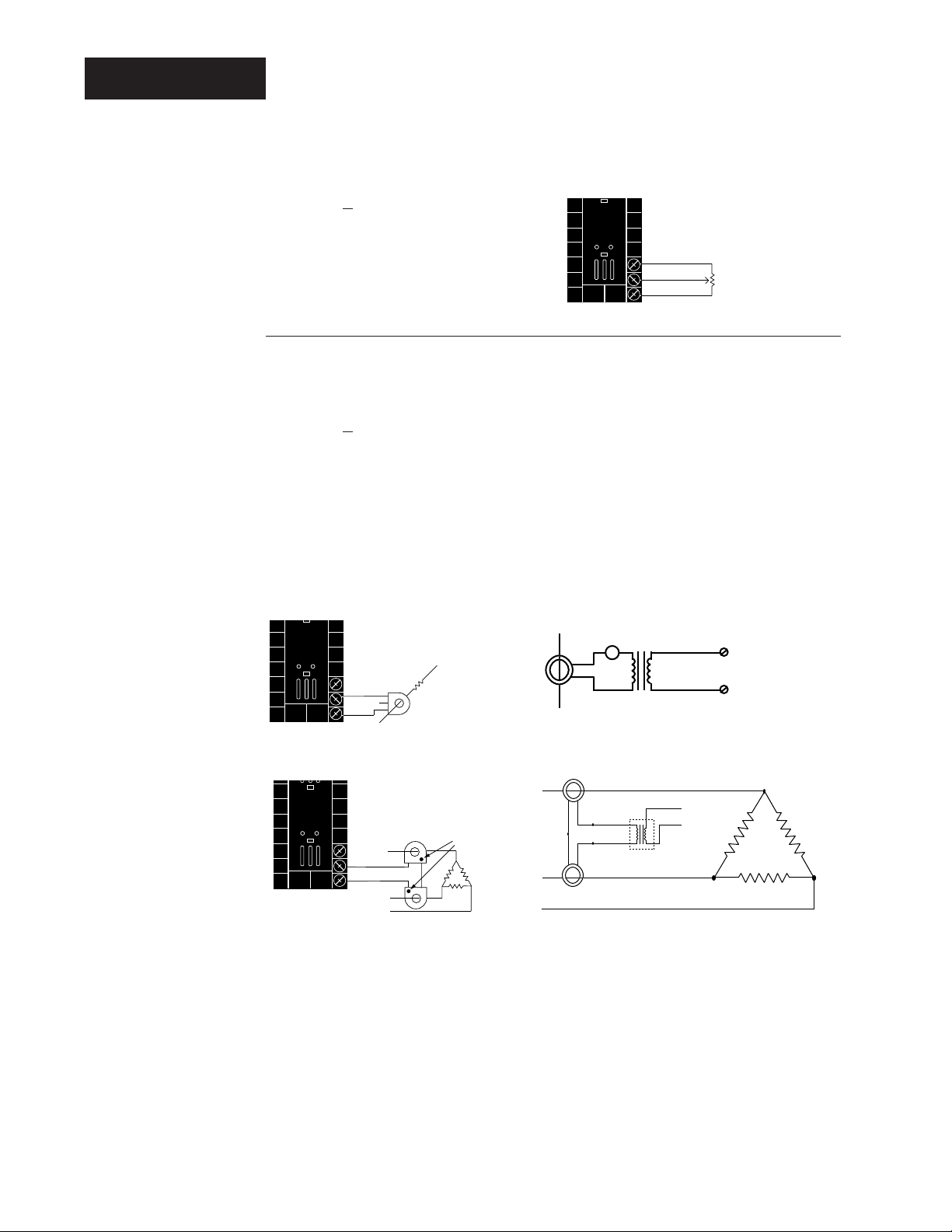
Figure 2.10b — Current Transformer Input
98 _ _ - _ 4 _ _ - _ _ _ _
The current transformer must be purchased separately. Watlow current
transformer part number is 16-0246 (up to 50 amps)..
Systems that use more than 50 Amps need an interstage transformer.
For example, if you use a 300A current transformer, part #16-0073, and
an interstage transformer, part #16-0176, the 300A current transformer
provides a 5A signal to the interstage transformer. In turn, the transformer
sends a 20mA maximum signal to the controller.
2.10 WATLOW Series 988 User’s Manual
Installation and Wiring, Chapter 2
Input 2 Wiring
20
19
L2
L1
CT
Load wire
Center leg not used
Figure 2.10a — Slidewire Feedback or Potentiometer Input
98 _ _ - _ 3 _ _ - _ _ _ _
NOTE:
See Chapter 8 for
information on
slidewire feedback.
˜
NOTE:
A process output
cannot be installed
on output 1 when
using a current
transformer input.
NOTE:
Successful installation requires five
steps:
• Model number and
software choice
(Appendix);
• DIP switch settings (Chapter 1);
• Sensor match
(Chapter 2 and
Appendix);
• Sensor installation
(Chapter 2); and
• Wiring (Chapter 2).
Single-phase
Single-phase current sensing up to 300 amps
3-phase using 2 current transformers
3-phase current sensing up to 300 amps
AC Load
T1
Phase
T1
19
20
T3
T2
dot
T3
T2
Wh Bk
Bk Wh
CT
0 to 5A
AC
A
5A
Bk
Bk
16-0176
Transformer
Red
20mA
Red
0 to
20mA
19
20
19
20

WATLOW Series 988 User’s Manual 2.11
Installation and Wiring, Chapter 2
Figure 2.11b — Digital Event Input 2
98 _ _ - _ 5 _ _ - _ _ _ _
open 0-3VÎ (dc) Event Input 2 off
closed 14-36VÎ (dc) Event Input 2 on
Figure 2.11a — Digital Event Input 1
Available on all units.
open 14-36VÎ (dc) Event Input 1 off
closed 0-3VÎ (dc) Event Input 1 on
NOTE:
Successful installation requires five
steps:
• Model number and
software choice
(Appendix);
• DIP switch settings (Chapter 1);
• Sensor match
(Chapter 2 and
Appendix);
• Sensor installation
(Chapter 2); and
• Wiring (Chapter 2).
Event Input 1 Wiring
+24VÎ (dc)
Internal Circuitry
+5VÎ (VDC)
Internal Circuitry
100Ω
4.7KΩ
1KΩ
.01µf
750Ω
18
19
20
4.99KΩ
10KΩ
OPTO
ISOLATOR
23
4.99KΩ
24
.01µf
750Ω
18
20
23 24
+-
19
+
20
-
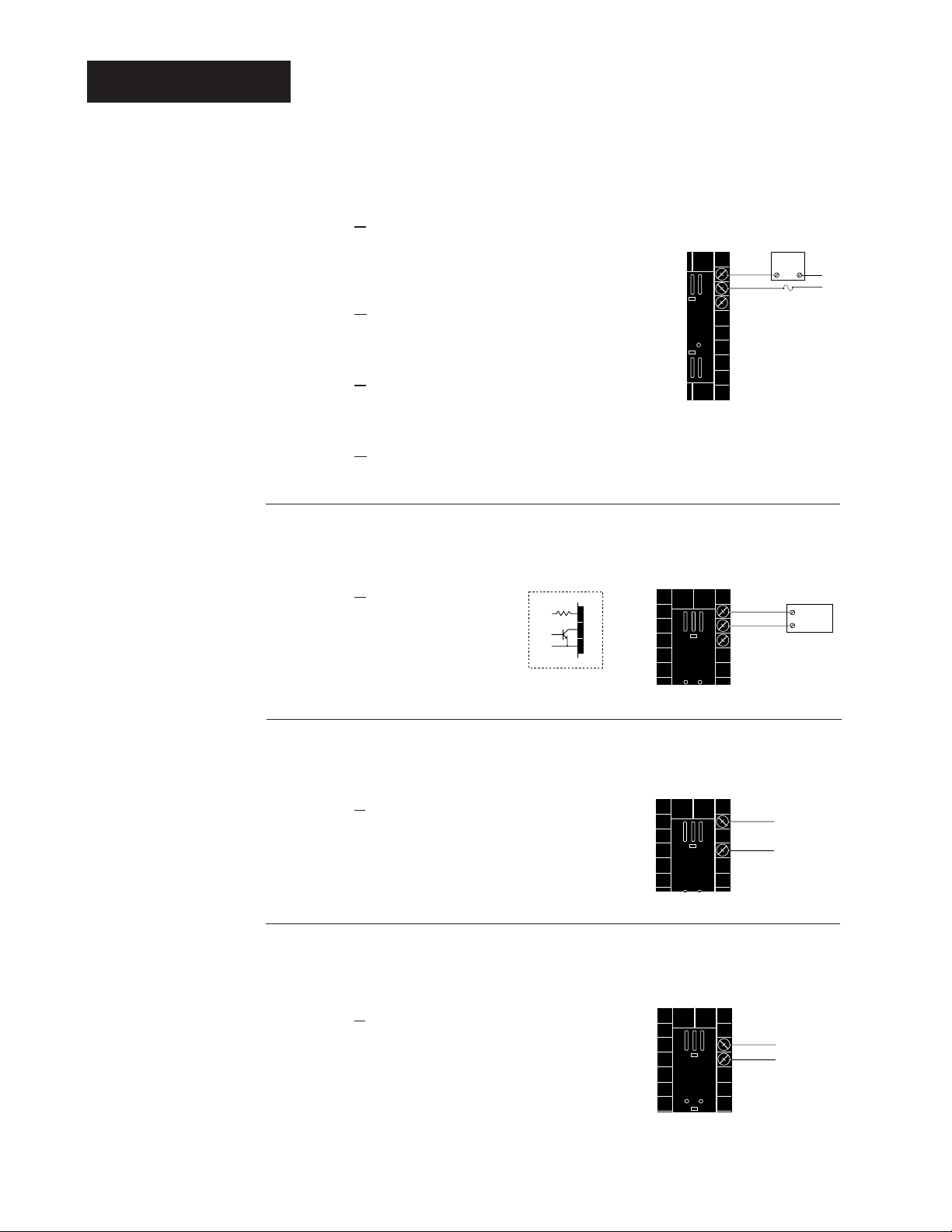
2.12 WATLOW Series 988 User’s Manual
Installation and Wiring, Chapter 2
Figure 12a —
AC Outputs
Solid-state Relay with Contact Suppression
98 _ _ - _ _ B _ - _ _ _ _
0.5 amps, minimum off-state impedance: 20KΩ
Electromechanical Relay with Contact Suppression
(Suppression between NO and COM contacts only)
98 _ _ - _ _ D _ - _ _ _ _
Form C, 5 amps, minimum off-state impedance: 20KΩ
Electromechanical Relay without Contact Suppression
98 _ _ - _ _ E _ - _ _ _ _
Form C, 5 amps off-state impedance: 31MΩ
Solid-state Relay without Contact Suppression
98 _ _ - _ _ K _ - _ _ _ _
0.5 amps, off-state impedance: 31MΩ
Output 1 Wiring
Figure 12b — Switched DC, Open Collector
98 _ _ - _ _ C _ - _ _ _ _
Maximum voltage: 42VÎÎ(dc)
Maximum current: 1A
Figure 12d — 0-5V
ÎÎ
, 1-5VÎÎand 0-10VÎÎ(dc) Process
98 _ _ - _ _ F _ - _ _ _ _
Minimum load impedance: 1KΩ
Figure 12c — 0-20mA and 4-20mA Process
98 _ _ - _ _ F _ - _ _ _ _
Maximum load impedance: 800Ω
NOTE:
Successful installation requires five
steps:
• Model number and
software choice
(Appendix);
• DIP switch settings (Chapter 1);
• Sensor match
(Chapter 2 and
Appendix);
• Sensor installation
(Chapter 2); and
• Wiring (Chapter 2).
NOTE:
Switching inductive
loads (relay coils,
solenoids, etc.) with
the mechanical
relay or solid state
relay output options
requires using an
R.C. suppressor.
Watlow carries the
R.C. suppressor
Quencharc brand
name, which is a
trademark of ITW
Paktron. Watlow
Part No. 0804-0147-
0000.
19 to 32VÎ (dc)
+
790Ω
Internal Circuitry
12
13
14
External
Load
NO
12
13
COM
14
(#14 for D & E outputs only)
Fuse
NC
12
+
External
-
13
14
COM
L2
L1
Load
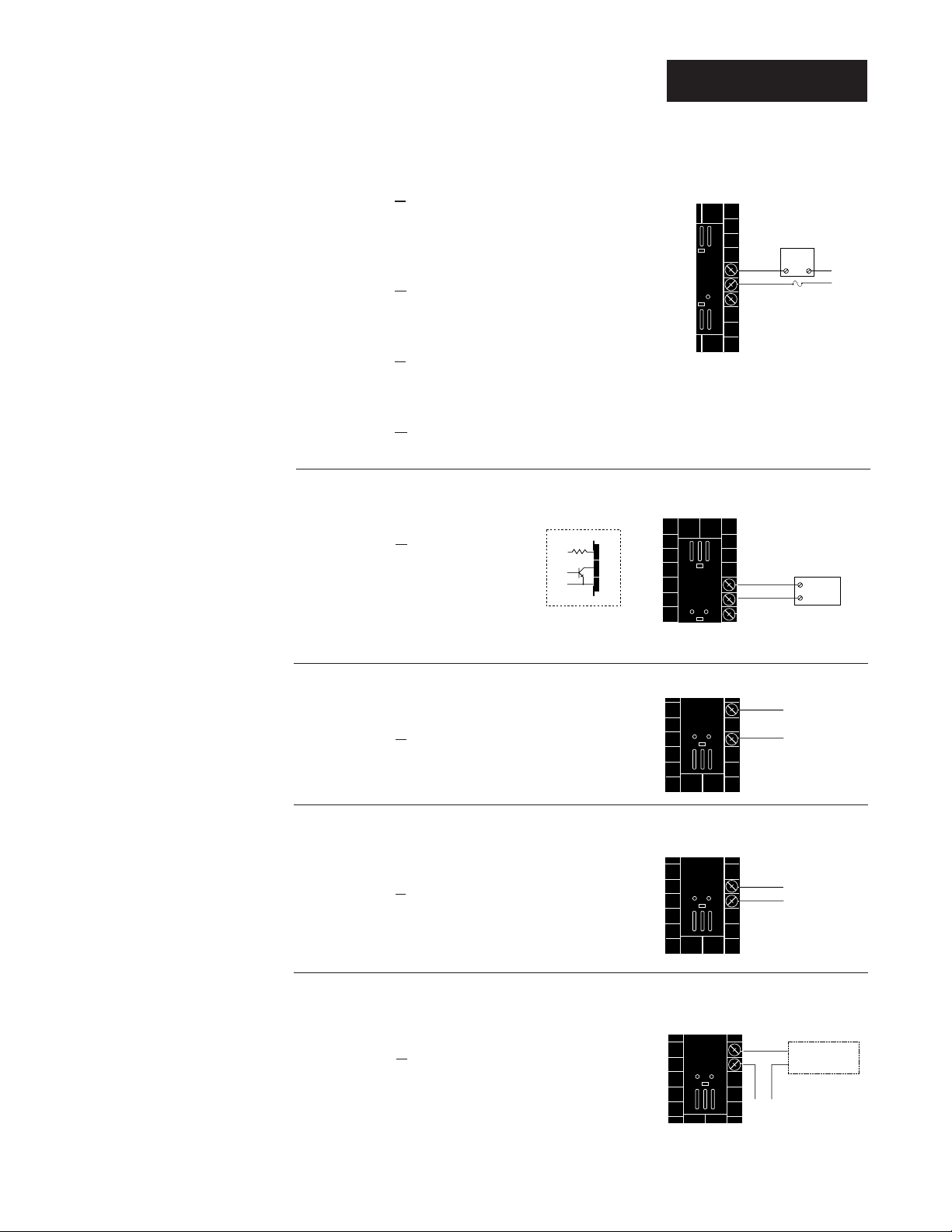
WATLOW Series 988 User’s Manual 2.13
Installation and Wiring, Chapter 2
Output 2 Wiring
Figure 13b — Switched DC, Open Collector
98 _ _ - _ _ _ C - _ _ _ _
Maximum voltage: 42VÎÎ(dc)
Maximum current: 1A
Figure 13d — 0-5V
ÎÎ
, 1-5VÎÎand 0-10VÎÎ(dc) Process
98 _ _ - _ _ _ F - _ _ _ _
Minimum load impedance: 1KΩ
Figure 13c — 0-20mA and 4-20mA Process
98 _ _ - _ _ _ F - _ _ _ _
Maximum load impedance: 800Ω
Figure 13e — External Signal Conditioner Power Supply
98 _ _ - _ _ _ T - _ _ _ _
Figure 13a —
AC Outputs
Solid-state Relay with Contact Suppression
98 _ _ - _ _ _ B - _ _ _ _
0.5 amps, minimum off-state impedance: 20KΩ
Electromechanical Relay with Contact Suppression
(Suppression between NO and COM contacts only)
98 _ _ - _ _ _ D - _ _ _ _
Form C, 5 amps, minimum off-state impedance: 20KΩ
Electromechanical Relay without Contact Suppression
98 _ _ - _ _ _ E - _ _ _ _
Form C, 5 amps off-state impedance: 31MΩ
Solid-state Relay without Contact Suppression
98 _ _ - _ _ _ K - _ _ _ _
0.5 amps, off-state impedance: 31MΩ
NOTE:
Successful installation requires five
steps:
• Model number and
software choice
(Appendix);
• DIP switch settings (Chapter 1);
• Sensor match
(Chapter 2 and
Appendix);
• Sensor installation
(Chapter 2); and
• Wiring (Chapter 2).
˜
NOTE:
Input-to-output isolation is defeated
when the external
signal conditioner
power supply is
used to power a
transmitter connected to input 1 or
input 2.
NOTE:
Switching inductive
loads (relay coils,
solenoids, etc.) with
the mechanical
relay or solid state
relay output options
requires using an
R.C. suppressor.
Watlow carries the
R.C. suppressor
Quencharc brand
name, which is a
trademark of ITW
Paktron. Watlow
Part No. 0804-0147-
0000.
Loop powered
19 to 32VÎ (dc)
+
790Ω
Internal Circuitry
15
16
17
External
Load
15
NO
COM
16
Fuse
NC
17
(#17 for D & E outputs only)
15
+
External
-
16
17
COM
L2
L1
Load
15
16
+
-
-
Input
1 or 2
1
Transmitter
+V
2
4-20mA out
-V
+

Figure 14c — Process Retransmit
0-20mA, 4-20mA, Load impedance: 600Ω max.
98 _ _ - _ _ _ _ - M _ _ _
0-5VÎÎ, 1-5VÎÎ, 0-10VÎÎ(VDC), Load impedance: 500Ω min.
98 _ _ - _ _ _ _ - N _ _ _
2.14 WATLOW Series 988 User’s Manual
Installation and Wiring, Chapter 2
NOTE:
Input-to-output isolation is defeated
when the external
signal conditioner
power supply is
used to power a
transmitter connected to input 1 or
input 2.
NOTE:
Successful installation requires five
steps:
• Model number and
software choice
(Appendix);
• DIP switch settings (Chapter 1);
• Sensor match
(Chapter 2 and
Appendix);
• Sensor installation
(Chapter 2); and
• Wiring (Chapter 2).
Figure 14d — External Signal Conditioner Power Supply
98 _ _ - _ _ _ _ - T _ _ _
Figure 14a —
AC Outputs
Solid-state Relay with Contact Suppression
98 _ _ - _ _ _ _ - B _ _ _
0.5 amps, minimum off-state impedance: 20KΩ
Electromechanical Relay without Contact Suppression
98 _ _ - _ _ _ _ - J _ _ _ _
Form A or B, 5 amps, off-state impedance: 31MΩ
Solid-state Relay without Contact Suppression
98 _ _ - _ _ _ _ - K _ _ _ _
0.5 amps, off-state impedance: 31MΩ
Figure 14b —
Switched DC
98 _ _ - _ _ _ _ - C _ _ _
Minimum load resistance: 500Ω
Form B
Form A
Form A or B
alarm jumper
settings (98______-J___ only)
˜
NOTE:
See Chapter 1 for
power supply DIP
switch information.
Output 3 Wiring
NOTE:
Switching inductive
loads (relay coils,
solenoids, etc.) with
the mechanical
relay or solid state
relay output options
requires using an
R.C. suppressor.
Watlow carries the
R.C. suppressor
Quencharc brand
name, which is a
trademark of ITW
Paktron. Watlow
Part No. 0804-0147-
0000.
Loop powered
19 to 32VÎ (dc)
1
790Ω
2
Internal Circuitry
NC Form B
External
L2
L1
Fuse
+
Load
NO Form A
COM
External
Load
or
-
+
-
1
2
-
1
2
1
+
2
-
Transmitter
4-20mA out
1
+
+V
2
-
-V
-
+
Input
1 or 2
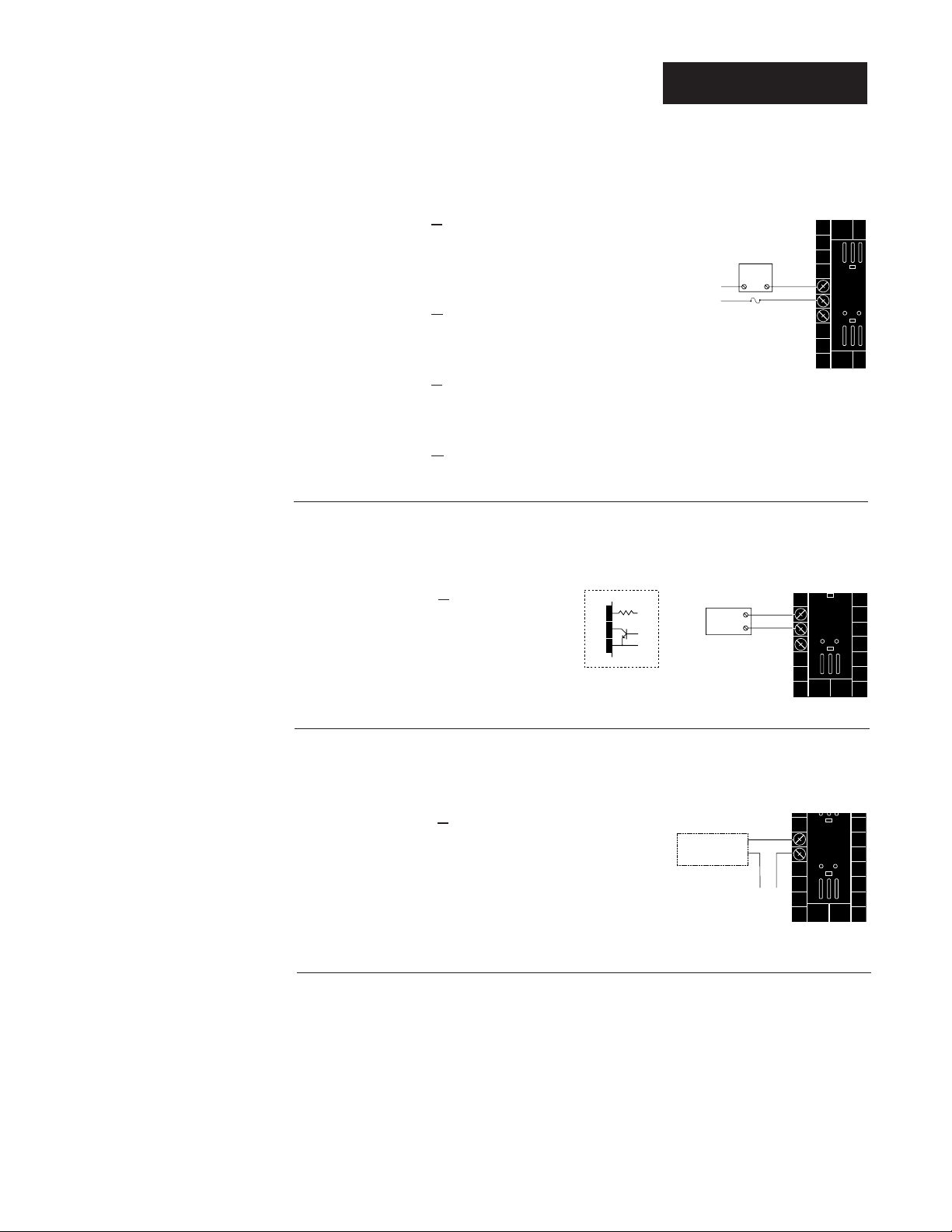
WATLOW Series 988 User’s Manual 2.15
Installation and Wiring, Chapter 2
Figure 15b — Switched DC, Open Collector
98 _ _ - _ _ _ _ - _ C _ _
Maximum voltage: 42VÎÎ(dc)
Maximum current: 1A
Figure 15a —
AC Outputs
Solid-state Relay with Contact Suppression
98 _ _ - _ _ _ _ - _ B _ _
0.5 amps, minimum off-state impedance: 20KΩ
Electromechanical Relay with Contact Suppression
(Suppression between NO and COM contacts only)
98 _ _ - _ _ _ _ - _ D _ _ _
Form C, 5 amps, minimum off-state impedance: 20KΩ
Electromechanical Relay without Contact Suppression
98 _ _ - _ _ _ _ - _ E _ _ _
Form C, 5 amps, off-state impedance: 31MΩ
Solid-state Relay without Contact Suppression
98 _ _ - _ _ _ _ - _ K _ _ _
0.5 amps, off-state impedance: 31MΩ
Output 4 Wiring
Figure 15c — External Signal Conditioner Power Supply
98 _ _ - _ _ _ _ - _ T _ _
5
6
+
-
+V
-V
Transmitter
4-20mA out
Input
1 or 2
+
-
Controllers with Output 4 (R, S, or U)
For data communications wiring refer to “Data Communications
with the Watlow Series 988 Family of Controllers” manual. This
manual can be downloaded from Watlow’s website at www.wat-
low.com, Product Technical Information - Controls.
NOTE:
Input-to-output isolation is defeated
when the external
transmitter power
supply is used to
power a signal conditioner connected
to input 1 or input 2.
˜
NOTE:
See Chapter 1 for
power supply DIP
switch information.
NOTE:
Successful installation requires five
steps:
• Model number and
software choice
(Appendix);
• DIP switch settings (Chapter 1);
• Sensor match
(Chapter 2 and
Appendix);
• Sensor installation
(Chapter 2); and
• Wiring (Chapter 2).
NOTE:
Switching inductive
loads (relay coils,
solenoids, etc.) with
the mechanical
relay or solid state
relay output options
requires using an
R.C. suppressor.
Watlow carries the
R.C. suppressor
Quencharc brand
name, which is a
trademark of ITW
Paktron. Watlow
Part No. 0804-0147-
0000.
Loop powered
External
L2
L1
Fuse
(#7 for D & E outputs only)
Load
NO
COM
NC
5
6
7
19 to 32VÎ (dc)
5
790Ω
6
7
Internal Circuitry
5
+
External
Load
COM
+
-
6
7

2.16 WATLOW Series 988 User’s Manual
Installation and Wiring, Chapter 2
Notes
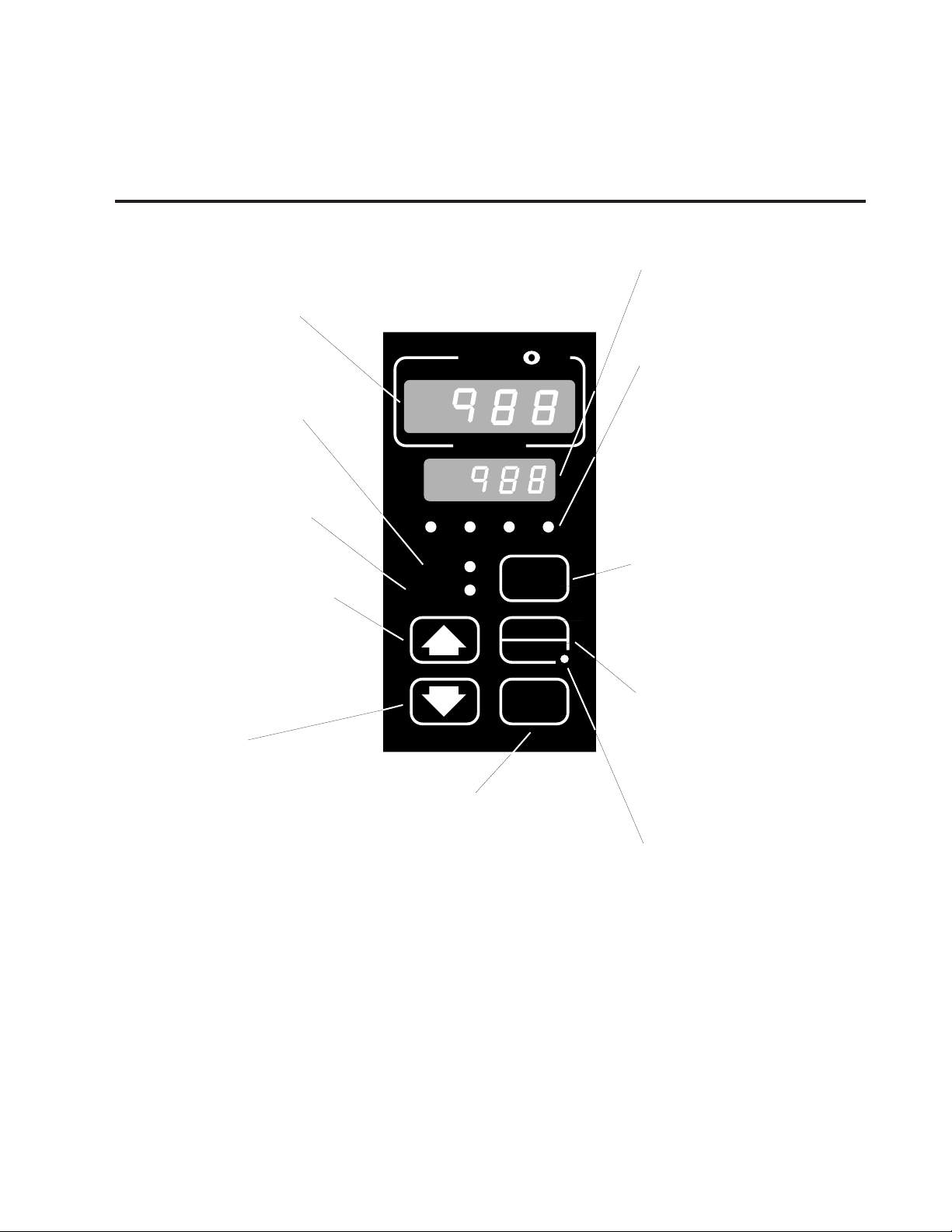
WATLOW Series 988 User’s Manual 3.1
Front Panel and Display Loop, Chapter 3
Chapter 3 Front Panel and Display Loop
Upper Display
Indicates the actual process value,
prompt parameter value or error
code.
DEV LED
When lit, the lower display shows
the most recent deviation unit from
the set point.
% OUT LED
When lit, the lower display shows
the current percent output.
Up-arrow Key
Increases the value or changes the
parameter in the upper display
(except for set point changes in the
Display Loop, which occur in the
lower display). Hold the key down
to increase the value rapidly. New
data takes effect in five seconds or
when the Mode key or Display key
is pressed.
Up + Down Keys
Press simultaneously for three seconds to go to the Setup Menu.
Continue to press both keys for
another three seconds to go to the
Factory Menu. Access to the Setup
and Factory menus can be disabled with lockout DIP switch.
Lower Display
Indicates the set point, deviation,
percent power, temperature unit,
menu prompt name or alarm code.
L1, L2, L3, L4
These LED’s indicate when output
1, 2, 3 or 4 are active. Outputs can
be configured as:
Ot1 Control
Ot2 Control or Alarm
Ot3 Alarm or Retransmit
Ot4 Alarm or Communications
(flashes on transmit and
receive)
Display Key
Pressing this key enters the
Display Loop. Press the Display
key at any time to return to this
loop. The next page has more
information on the Display Loop.
Auto/Man Key
In Manual mode the lower display
shows percent output. Pressed
once, it clears any latched alarm. If
pressed again within five seconds
it will toggle between Auto and
Manual mode.
Auto/Man LED
Lit when the control is in Manual
operation. Press the Auto/Man key
twice to enter Automatic operation.
When blinking, press the Auto/Man
key to toggle between Auto and
Manual. After five seconds without
pressing the Auto/Man key, the
LED stops blinking and returns to
its previous state.
Mode Key
Enters new data and steps to
the next prompt in the current
menu.
Mode + Up-arrow Keys
Hold the Mode key then press
the Up-arrow key to move
backwards through the current menu. Scrolling stops
when you reach the top of the
menu.
Figure 3.1 Series 988 Keys and Displays
Down-arrow Key
Decreases the value or changes
the parameter in the upper display
(except for set point changes in the
Display Loop, which occur in the
lower display). Hold the key down
to decrease the value rapidly. New
data takes effect in five seconds or
when the Mode key or Display key
is pressed.
Keys and Displays
W
TL
W
A
PROCESS
L1 L2 L3 L4
DEV
% OUT
DISPLAY
AUTO
MAN
MODE
SERIES 988
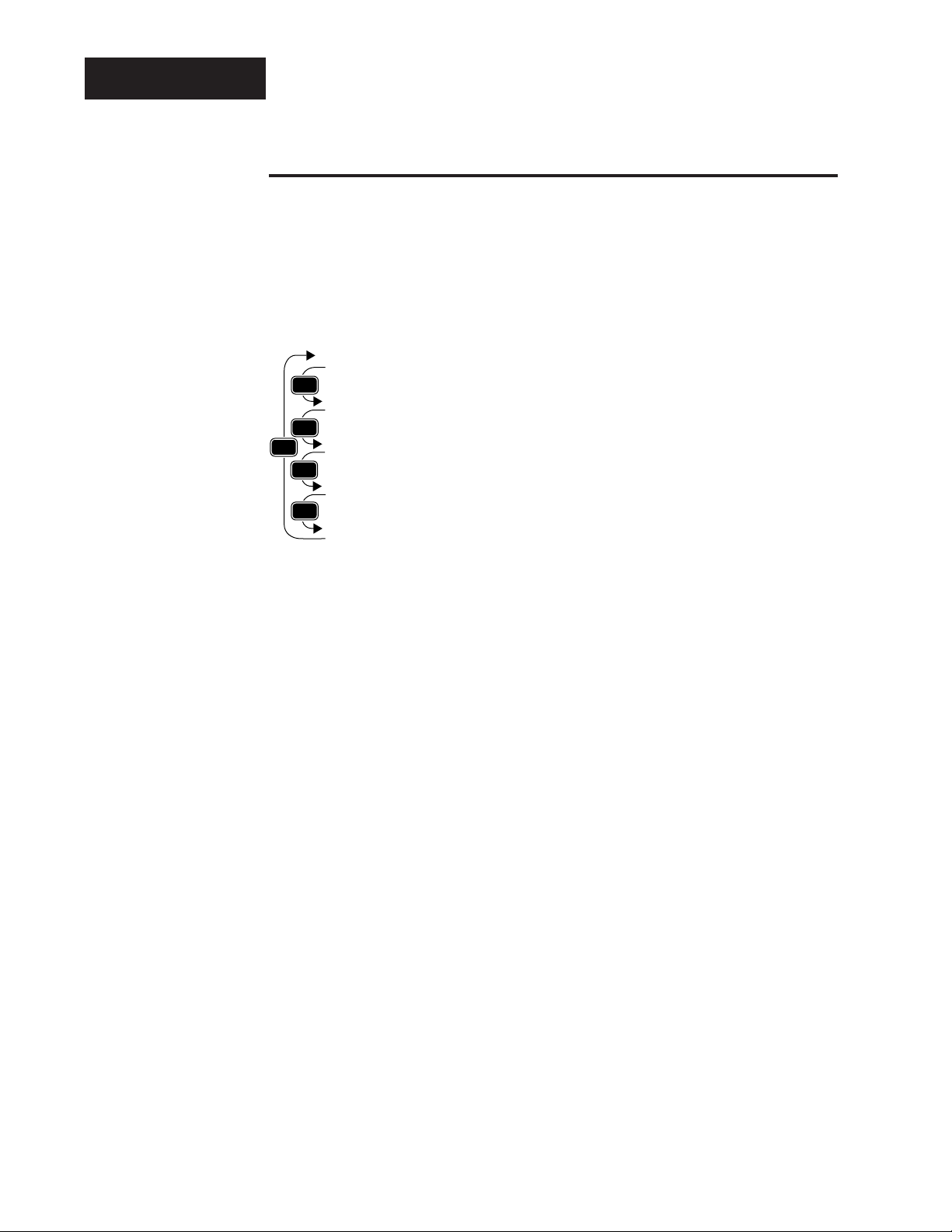
3.2 WATLOW Series 988 User’s Manual
Front Panel and Display Loop, Chapter 3
Display Loop
Display Loop
The Display Loop is the “home” state of the Series 988 controller. Pressing
the Display key ∂ returns the controller to the Display Loop from any
prompt in any menu. The controller automatically returns to the Display
Loop from any menu when a minute passes without any keys being
pressed.
Figure 3.2 The Display Loop
˜
NOTE:
If [``no] is selected
for [`In2], in the
Input Menu, the
[Pr`2] prompt will
not appear.
˜
NOTE:
For information on
input 1 [`In1] and
input 2 [`In2]
ranges, refer to
Chapter 4.
DISPLAY
DISPLAY
DISPLAY
DISPLAY
DISPLAY
DISPLAY
[`988]
[`988]
[`988]
[`988]
[`988]
[`988]
[`988]
current input 1 reading
set point 1 (change with Up-arrow > or Down-arrow < key)
current input 2 reading
[Pr`2]
input 2 process (appears only if controller equipped with input 2 hardware)
current input 1 reading
deviation from set point, process 1 minus set point 1 (DEV light on)
current input 1 reading
[`100]
percent output (%OUT light on)
current input 1 reading
[``°C]
units selected (units, °F or °C)
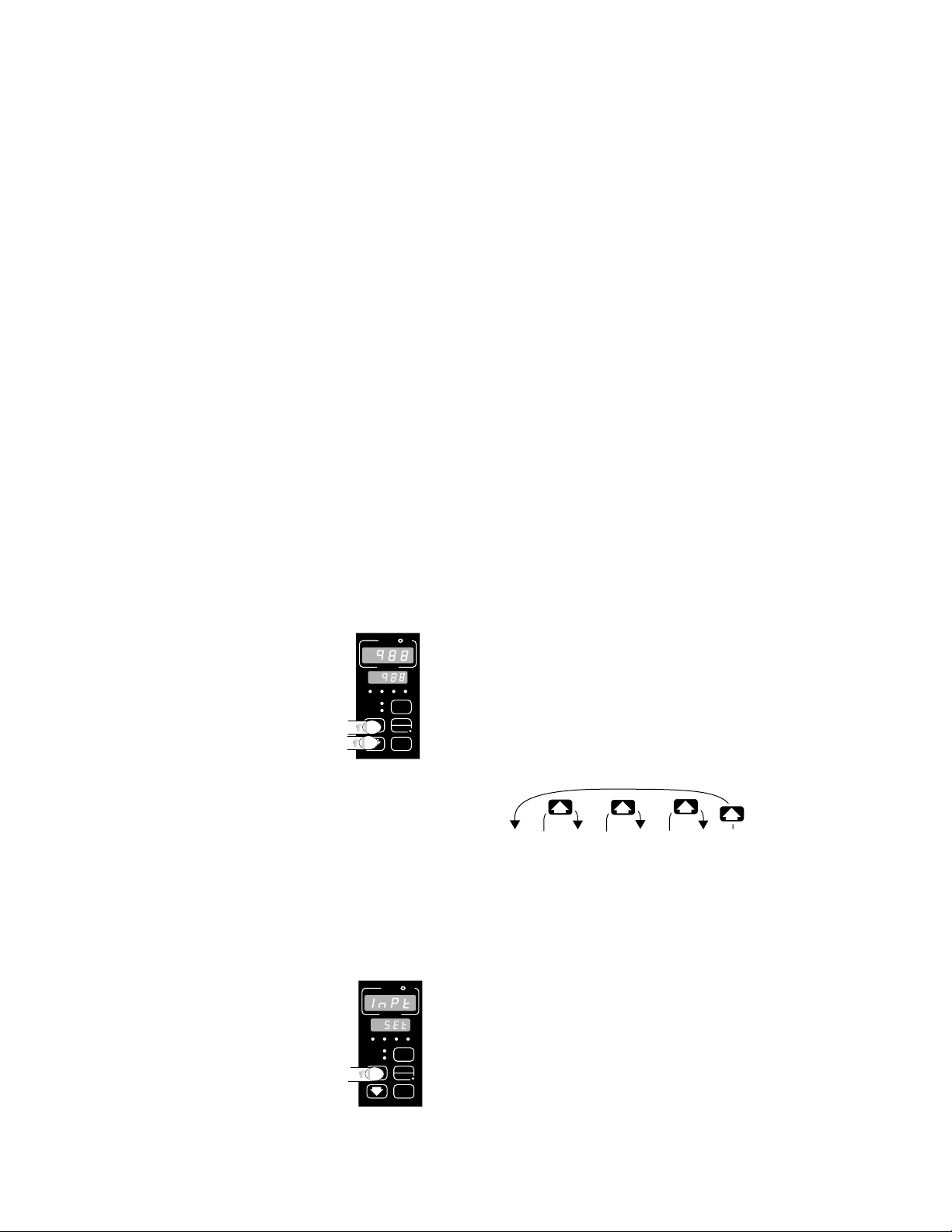
WATLOW Series 988 User’s Manual 4.1
Setup Menus, Chapter 4
Navigating the Setup Menus
To reach the Setup Menus, begin in the Display Loop and press both the Uparrow > and Down-arrow < keys for three seconds. The Setup Menu
prompt [`SEt] will appear in the lower display, and the Input Menu prompt
[InPt] will appear in the upper display. The four Setup Menus are: Input
[InPt]; Output [OtPt]; Global [GLbL]; and Communications [COM]. Use the
Up-arrow > or Down-arrow < key to select a menu and the Mode key µ
to step through a menu. The Communications Menu appears only on units
equipped with the data communications option.
You will not see every prompt in any of these menus. The unit’s configuration
and model number determine which prompts appear. After stepping through
each menu, the Series 988 returns to the Setup Menu prompt [`SEt]. Use
the Up-arrow > and Down-arrow < keys to select the next menu, or use
the Mode key µ to advance through the same menu again. To move backwards through the menu hold the Mode key µ down and press the Uparrow key >. Use the Up-arrow > or Down-arrow < key to change the
prompt setting.
Refer to the Appendix for model number options. For information about
communications and the communications prompts, refer to the supplemental manual Data Communications with the Watlow Series 988 Family of
Controllers.
Chapter 4 The Setup Menus
Figure 4.1 Navigating the
Setup Menus.
❶ Begin in the Display Loop, and press the Up-arrow
> and Down-arrow < keys simultaneously to
reach the Setup Menus.
❷ Press the Up-arrow key > to select one of the
Setup Menus.
˜
NOTE:
The lockout DIP
switch hides the
Setup Menus. See
Chapter 1.
˜
NOTE:
Press the Display
key ∂ to return to
the Display Loop
from any point in
any menu.
NOTE:
When navigating
through menus,
outputs will be disabled.
W
PROCESS
L1 L2 L3 L4
DEV
% OUT
SERIES 988
PROCESS
L1 L2 L3 L4
DEV
% OUT
SERIES 988
W
TL
A
DISPLAY
AUTO
MAN
MODE
TL
W
A
[Inpt]
[`Set]
Input
Menu
p. 4.2
W
[OtPt] [gLbL] [COm]
[`Set] [`Set]
Output
Menu
p. 4.18
Global
Menu
p. 4.34
[`Set]
Communications
Menu
p. 4.44
DISPLAY
AUTO
MAN
MODE

4.2 WATLOW Series 988 User’s Manual
Setup Menus, Chapter 4
Figure 4.2 The Input Menu.
Setup-Input
❸ Select the Input Menu, then press
the Mode key µ to step through the
prompts.
❹ Press the Up-arrow key > or the
Down-arrow key < to select one of
the prompt values.
*Prompts may not appear,
depending on controller
configuration.
Reaching the Input Menu
W
TL
W
A
PROCESS
L1 L2 L3 L4
DEV
DISPLAY
% OUT
AUTO
MAN
MODE
SERIES 988
…
…
[```0] [```1] [```2] [``60]
[Ftr1] [Ftr1] [Ftr1] [Ftr1]
[``no]
[Lin1]
[root]
[Lin1]
…
MODE
MODE
MODE
MODE
MODE
MODE
MODE
MODE
MODE
MODE
MODE
MODE
MODE
MODE
MODE
MODE
MODE
MODE
MODE
MODE
MODE
MODE
[Inpt]
[`Set]
[`In1]
[deC1]
[`rL1]
[`rH1]
[CAL1]
[rtd1]
[Ftr1]
[Lin1]
[`ln2]
[`rSp]
[deC2]
[`RL2]
[`RH2]
[LrnL]
[LrnH]
[CAL2]
[rtd2]
[Ftr2]
[Lin2]
[Hunt]
[SHYS]
Setup Prompt
Input 1
*Decimal 1
Range Low 1
Range High 1
Calibration Offset 1
*RTD Calibration Curve 1
Software Filter 1
*Linearization 1
*Input 2
*Remote Set Point
*Decimal 2
*Range Low 2
*Range High 2
*Learn Low
*Learn High
*Calibration Offset 2
*RTD Calibration Curve 2
*Software Filter 2
*Linearization 2
*Hunt
*Slidewire Hysteresis
Enter your settings,
from the controller's
upper display.
Input 1 (p. 4.3)
Input 2 (p. 4.9)
Slidewire (p. 4.16)