
USER'S GUIDE
Vaisala BAROCAP® Barometer
Module
PMB100
M010035EN-A
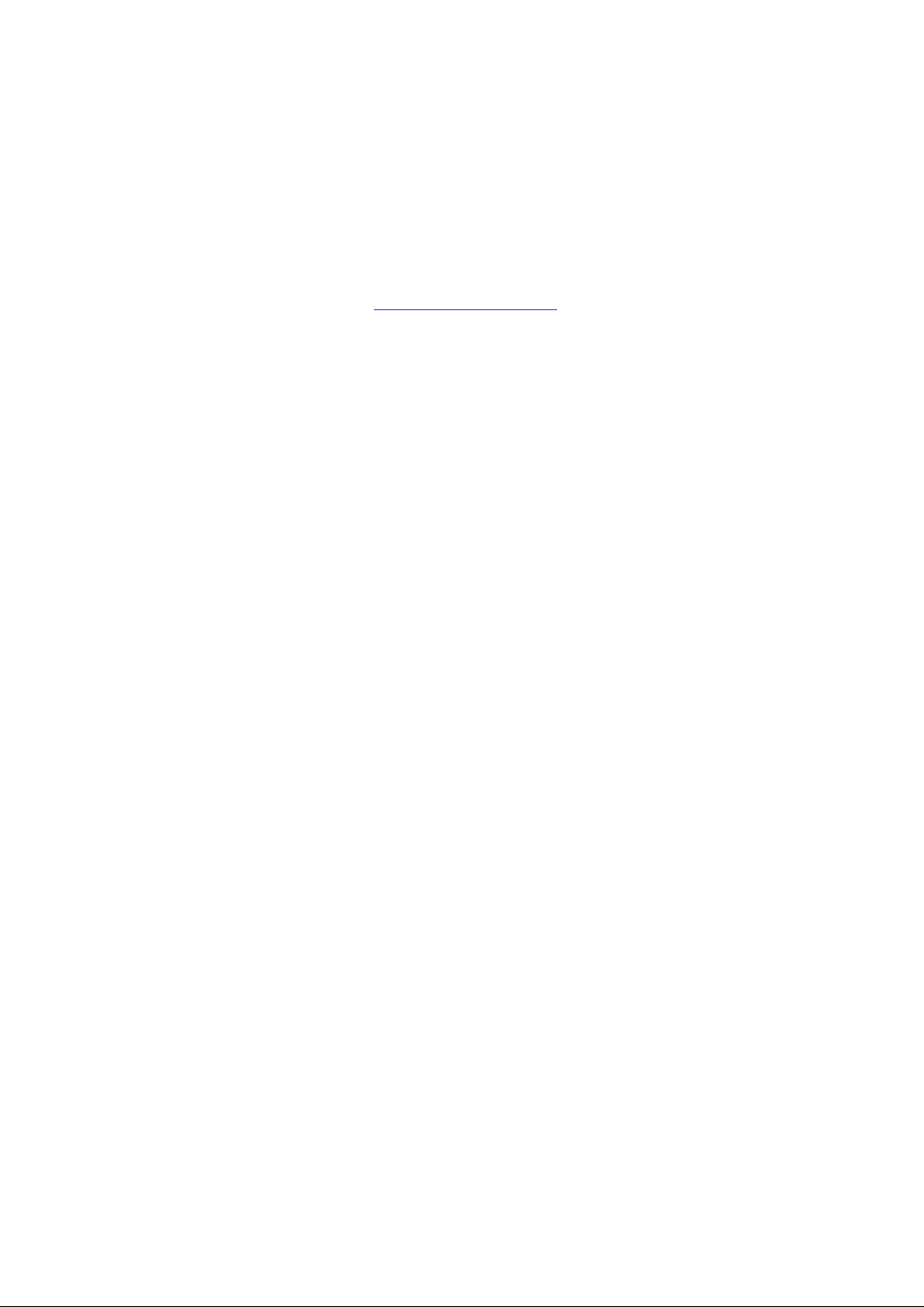
PUBLISHED BY
Vaisala Oyj Phone (int.): +358 9 8949 1
P.O. Box 26 Fax: +358 9 8949 2227
FIN-00421 Helsinki
Finland
Visit our Internet pages at http://www.vaisala.com/
© Vaisala 2006
No part of this manual may be reproduced in any form or by any means, electronic or
mechanical (including photocopying), nor may its contents be communicated to a third
party without prior written permission of the copyright holder.
The contents are subject to change without prior notice.
Please observe that this manual does not create any legally binding obligations for
Vaisala towards the customer or end user. All legally binding commitments and
agreements are included exclusively in the applicable supply contract or Conditions of
Sale.
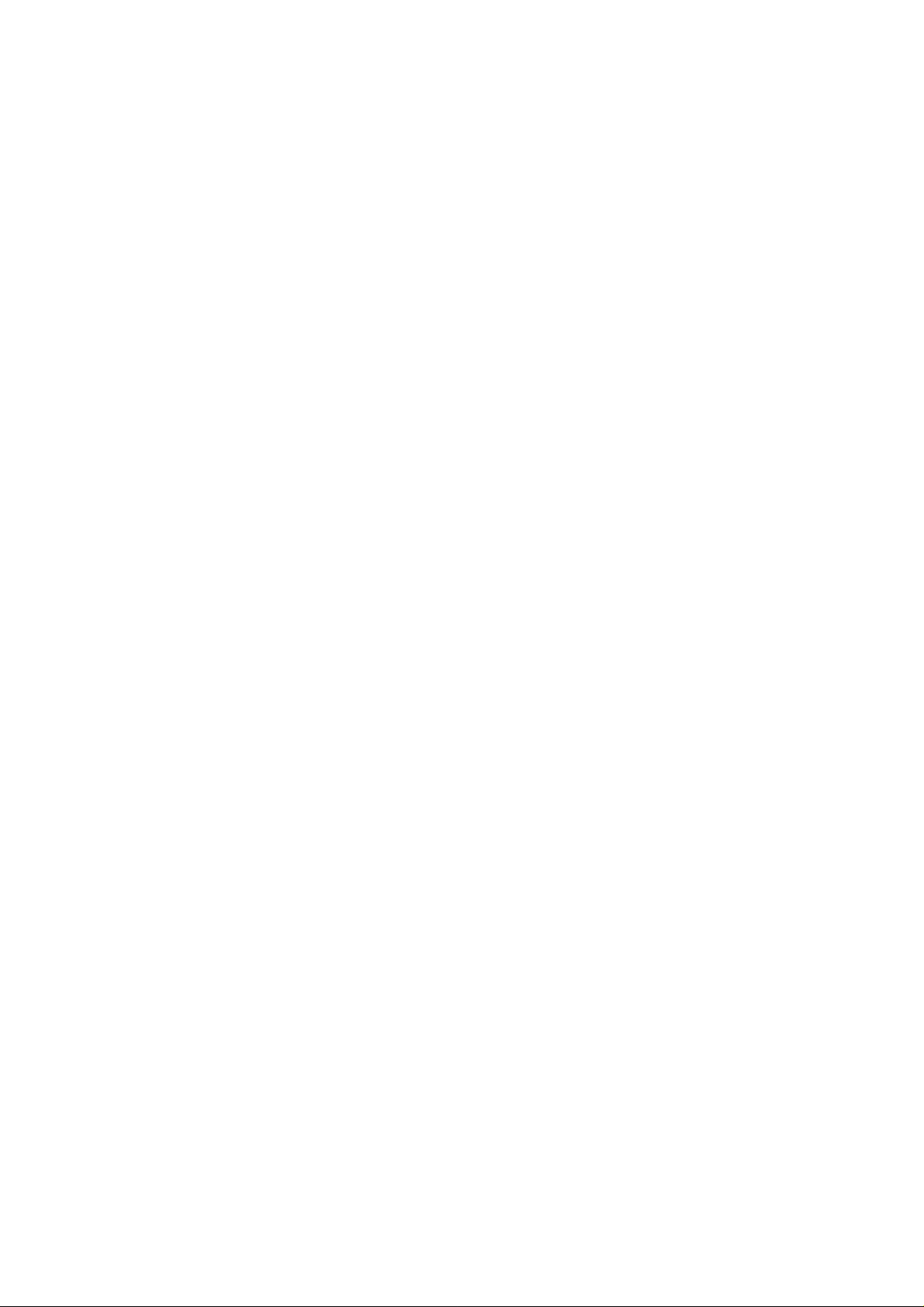
CHAPTER 1_______________________________________________________ GENERAL INFORMATION
Table of contents
CHAPTER 1
GENERAL INFORMATION ............................................................................4
Safety.........................................................................................4
Warranty ....................................................................................4
CHAPTER 2
PRODUCT DESCRIPTION.............................................................................5
BAROCAP® pressure sensor..................................................5
CHAPTER 3
OPERATION...................................................................................................7
Connections..............................................................................7
Dimensions in mm (in inches).................................................9
Pressure calculations...............................................................9
Offset/Gain corrections..........................................................10
CHAPTER 4
TECHNICAL DATA.......................................................................................11
Specifications .........................................................................11
Operating range..............................................................11
Accuracy.........................................................................11
General...........................................................................11
APPENDIX A
READING COEFFICIENTS FROM THE EEPROM......................................13
VAISALA __________________________________________________________________________ 3
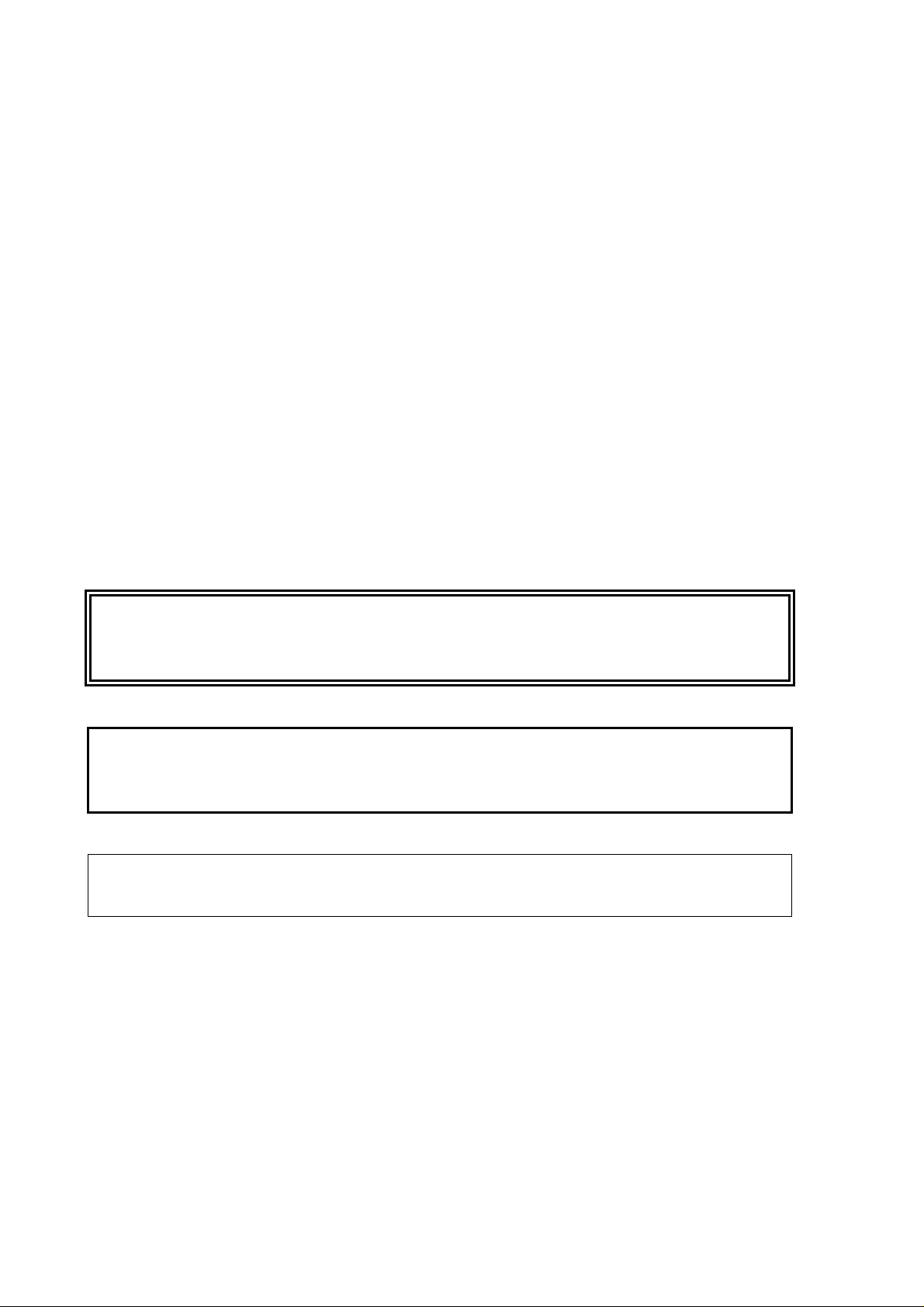
USER'S GUIDE_______________________________________________________________________
CHAPTER 1
GENERAL INFORMATION
Safety
Throughout the manual, important safety considerations are
highlighted as follows:
WARNING
CAUTION
NOTE
Warranty
Warning denotes a serious hazard. It calls attention to a procedure,
practice, condition or the like, which, if not correctly performed or
adhered to, could result in injury to or death of personnel.
Caution denotes a hazard. It calls attention to a procedure, practice,
condition or the like, which, if not correctly performed or adhered to,
could result in damage to or destruction of part or all of the product.
Note highlights important information. It calls attention to an
essential procedure, practice, condition or the like.
Vaisala issues a guarantee for the material and workmanship of this
product under normal operating conditions for one (1) year from the
date of delivery. Exceptional operating conditions, damage due to
careless handling and misapplication will void the guarantee.
4 ____________________________________________________________________ M010035EN-A
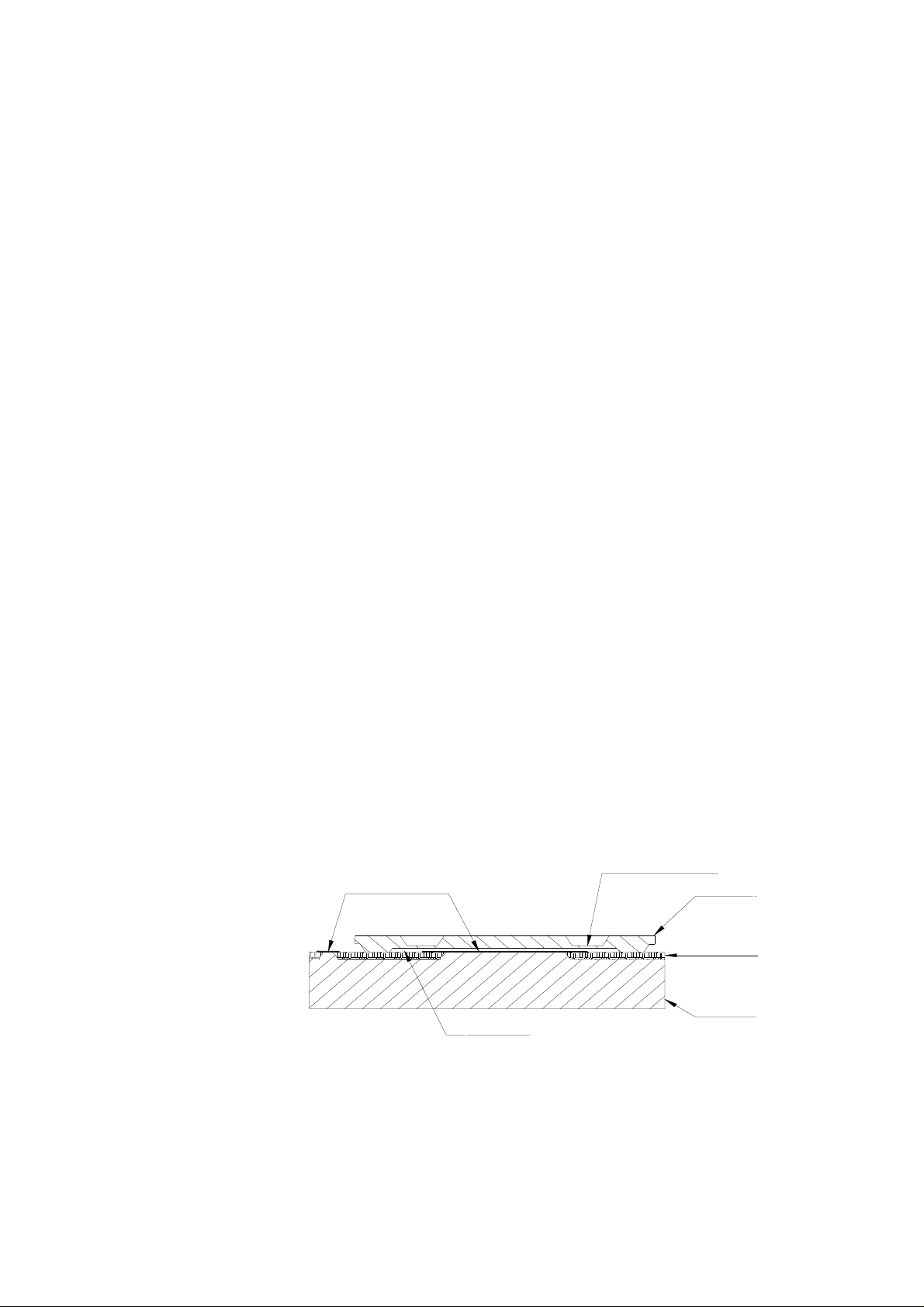
CHAPTER 2_______________________________________________________ PRODUCT DESCRIPTION
CHAPTER 2
PRODUCT DESCRIPTION
The PMB100 for OEM applications is a new circuit board mountable
barometric pressure transducer that is designed to interface with an
AD converter and a microprocessor.
The PMB100 module is characterized over 800 to 1100 hPa (mbar)
pressure range and over –5 to +45C temperature range. It ouputs
pressure dependant voltage within 0 and 2.5 VDC along with a
reference voltage of 2.5 VDC. All pressure and temperature related
coefficients are given in a module specific certificate and also stored
in an incorporated EEPROM, which uses the I2C interface. All the user
needs to do is to measure the temperature of the module and the two
voltage outputs and then calculate the compensated pressure reading
using the coefficients. A final offset correction against a high-class
pressure standard is recommended as a final touch.
BAROCAP® pressure sensor
The PMB100 barometer modules use the BAROCAP® silicon
capacitive absolute pressure sensor. The BAROCAP® sensor has
excellent hysteresis and repeatability characteristics, low temperature
dependence and a very good long-term stability. The ruggedness of
the BAROCAP® sensor is outstanding and the sensor is resistant to
mechanical and thermal shocks.
Thin film metallization
Vacuum gap
Figure 1 The BAROCAP® pressure sensor
The BAROCAP® pressure sensor consists of two layers of single
crystal silicon having a layer of glass between them. The thinner
silicon layer is etched on both sides to create an integrated vacuum
Silicon diaphragm
Silicon
Glass
Silicon
VAISALA __________________________________________________________________________ 5