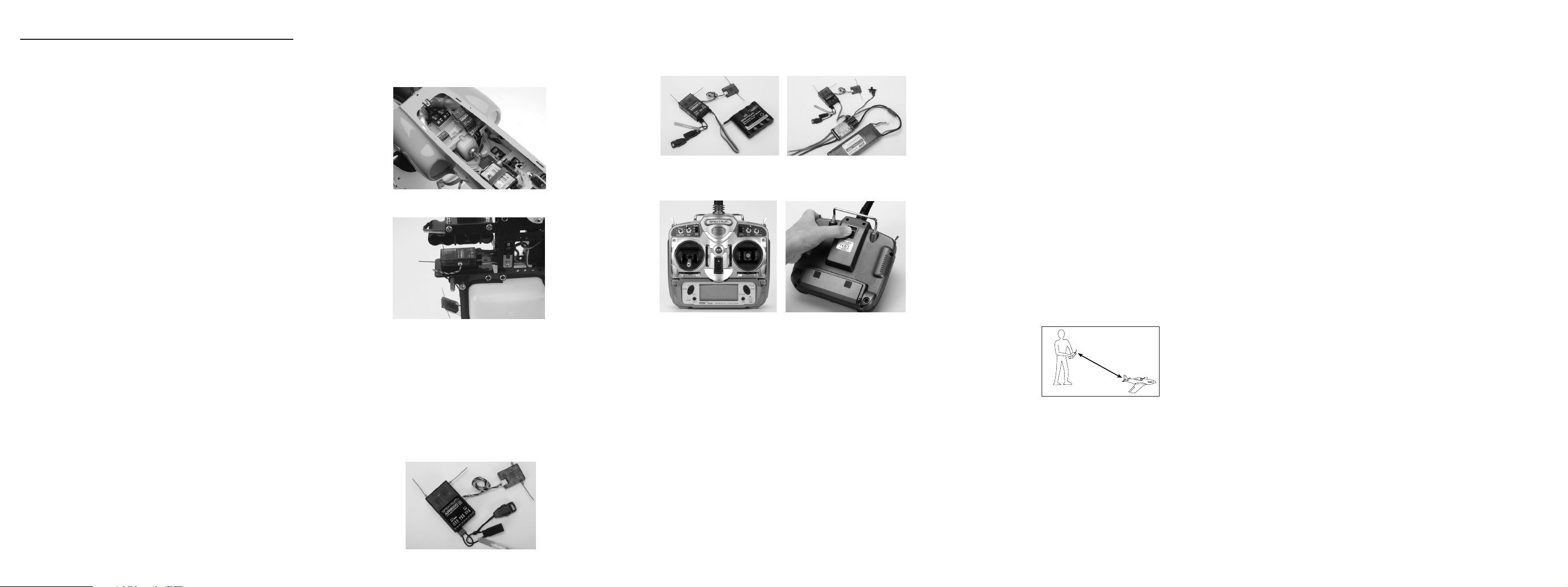
AR9000 User Guide
Pull and hold the Trainer Switch
30 paces (90 feet/28 meters)
The AR9000 full range 9-channel receiver features DSM2™ technology and is compatible with all
Spektrum™ and JR® aircraft radios that support DSM2 technology including JR12X, JRX9303,
Spektrum DX7, Spektrum DX6i, Spektrum DX5e, Spektrum Module Systems.
Note: The AR9000 receiver is not compatible with the Spektrum DX6 parkflyer transmitter.
Features:
• 9-Channel Full Range Receiver
• Patented MultiLink™ receiver technology with up to 4 receivers
• Includes two internal and one remote receiver
• Two type of failsafe SmartSafe™ and Preset Failsafe
• QuickConnect™ with Brownout Detection
• Flight Log Compatible (optional)
Applications
Full Range Up to 9 channel aircraft Including:
All types and sizes of glow, gas and electric powered airplanes
All types and sizes of no-powered gliders
All types and sizes of glow, gas and electric powered helicopters
Note: Not for use in airplanes that have full carbon fuselages.
Specications:
Type: DSM2 Full Range Receiver
Channels: 9
Modulation: DSM2
Dimension (WxLxH): 1.25 X 1.90 X .55 in (31 x 48.4 x 13.9mm)
Weight: .53 oz (15 g) main receiver
Input Voltage Range: 3.5–9.6V
Resolution: 2048
Compatibility: All DSM2 Aircraft Transmitters and Module Systems
Receiver
The AR9000 incorporates two internal receivers, and requires one external receiver (included)
offering the security of multi path RF redundancy. Two internal receivers are located on the main
PC board, while a third external receiver must be attached to the main board with an extension.
Additionally an optional fourth receiver can be added offering the ultimate in RF link security and
redundancy. By locating each receiver in slightly different locations in the aircraft, each receiver is
exposed to its own RF environment, greatly improving path diversity (the ability for the receiver to
see the signal in all conditions).
Antenna Polarization
For optimum RF link performance it’s important that the antennas be mounted in an orientation that
allows for the best possible signal reception when the aircraft is in all possible attitudes and positions. This is known as antenna polarization. The antennas should be oriented perpendicular to each
other; typically vertical and horizontal and at different angles (see Receiver Installation below). The
remote receiver antenna should be mounted in a position perpendicular at least 2 inches away from
the main receiver’s antenna using double-sided foam tape.
Receiver Installation in Aircraft
In gas and glow aircraft install the main receiver using the same method you would use to install a
conventional receiver in your aircraft. Typically, wrap the main receiver in protective foam and
fasten it in place using rubber bands or hook and loop straps. Alternately, in electric airplanes
or helicopters, it’s acceptable to use thick double-sided foam tape to fasten the main receiver in
place. The AR9000 requires at least one remote receiver to operate. Mounting this remote receiver
in a slightly different location, even just inches away from the primary receivers, gives tremendous
improvements in path diversity. Essentially, each receiver sees a different RF environment and this
is key to maintaining a solid RF link, even in aircraft that have substantial conductive materials (e.g.
larger gas engines, carbon fiber, pipes, etc.), which can weaken the signal. Using servo tape, mount
the remote receiver keeping the remote antennas at least 2 inches away from the primary antennas.
Ideally, the antennas will be oriented perpendicularly to each other. In airplanes, we’ve found it best
to mount the primary receiver in the center of the fuselage on the servo tray and to mount the remote
receiver to the side of the fuselage or in the turtle deck. A fourth antenna can be added for additional
RF link security.
In helicopters, there is generally enough room on the servo tray to achieve the necessary separation. If necessary a mount can be fashioned using clear plastic to mount the external receiver.
Important: Y-Harnesses and Servo Extensions
When using a Y-harness or servo extensions in your installation, it’s important to use standard nonamplified Y-harnesses and servo extensions as this can/will cause the servos to operate erratically
or not function at all. Amplified Y-harnesses were developed several years ago to boost the signal
for some older PCM systems and should not be used with Spektrum equipment. Note that when
converting an existing model to Spektrum be certain that all amplfied Y-harnesses and/or servo
extensions are replaced with conventional non-amplified versions.
Binding
The AR9000 receiver must be bound to the transmitter before it will operate. Binding is the process
of teaching the receiver the specific code of the transmitter so it will only connect to that specific
transmitter.
1. To bind an AR9000 to a DSM2 transmitter, insert the bind plug in the BATT/BIND port on the receiver.
Note: To bind an aircraft with an electronic speed controller that powers the receiver through the
throttle channel (ESC/BEC), insert the bind plug into the BATT/BIND port in the receiver and the
throttle lead into the throttle (THRO) port. Proceed to Step #2.
2. Power the receiver. Note that the LED on the receiver should be flashing, indicating that the receiver
is in bind mode and ready to be bound to the transmitter.
Shown using a separate receiver pack. Shown using an ESC/BEC and a flight pack.
(Battery can be plugged into any open port.)
3. Move the sticks and switches on the transmitter to the desired failsafe positions (low throttle and
neutral control positions).
4. Follow the procedures of your specific transmitter to enter Bind Mode, the system will connect
within a few seconds. Once connected, the LED on the receiver will go solid indicating the system
is connected.
5. Remove the bind plug from the BATT/BIND port on the receiver before you power off the transmitter
and store it in a convenient place.
6. After you’ve set up your model, it’s important to rebind the system so the true low throttle and
neutral control surface positions are set.
IMPORTANT: Remove the bind plug to prevent the system from entering bind mode the next time the
power is turned on.
Failsafe functions
The Powersafe features two types of failsafe: SmartSafe and Preset Failsafe.
SmartSafe
This type of failsafe is recommended for most types of aircraft. Here’s how SmartSafe works.
When the transmitter and receiver are turned on the receiver connects to the transmitter and normal
control of all channels occurs. If loss of signal occurs, SmartSafe drives the throttle servo only to its
preset failsafe position (low throttle) that was set during binding. All other channels hold their last
position. When the signal is regained, the system immediately regains control.
Preset Failsafe
Preset failsafe is ideal for sailplanes and is preferred by some modelers for their glow- and gaspowered aircraft.
When the transmitter and receiver are turned on and the receiver connects to the transmitter normal
control of all channels occurs. If loss of signal occurs Preset failsafe drives all servos to
their preset failsafe positions. For sailplanes it’s recommended that the spoilers/flaps deploy to dethermalize the aircraft, preventing a flyaway. Some powered modelers prefer to use this failsafe system
to program a slight turn and low throttle to prevent their aircraft from flying away. When the signal is
regained, the system immediately regains control.
Programming SmartSafe
During the binding process the bind plug is left in throughout the process and is removed only after
the receiver connects to the transmitter. After the connection is made, confirmed by operating the
servos, the bind plug can be removed. The receiver is now programmed for SmartSafe.
Programming Preset Failsafe
During the binding process the bind plug is inserted in the bind port, then the receiver is powered
up. The LEDs in each receiver should blink, indicating that the receiver is in bind mode. Now before
binding the receiver to the transmitter and with the receiver in bind mode, remove the bind plug. The
LEDs will still be blinking. With the control sticks and switches in the desired failsafe positions, bind
the transmitter to the receiver. Follow the procedures of your specific transmitter to enter Bind Mode.
The system should connect in less than 15 seconds. The receiver is now programmed for preset
failsafe.
Note: Failsafe positions are stored via the stick and switch positions on the transmitter during binding.
Receiver Power Only
• With SmartSafe or Preset Failsafe, when the receiver only is turned on (no transmitter signal is
present), the throttle channel has no output, to avoid operating or arming the electronic speed control.
• All other channels are driven to their preset failsafe positions set during binding.
Note: Some analog servos may coast slightly even though no signal is present. This is normal.
Plugging in the Leads
Plug the servo leads into the appropriate servo ports in the receiver noting the polarity of the
servo connector.
Range Testing
Before each flying session and especially with a new model, it is important to perform a range check.
All Spektrum aircraft transmitters incorporate a range testing system which, when activated, reduces
the output power, allowing a range check.
1. With the model restrained on the ground, stand 30 paces (approx. 90 feet/28 meters) away from
the model.
2. Face the model with the transmitter in your normal flying position and place your transmitter into
range check mode.
3. You should have total control of the model with the button depressed at 30 paces (90 feet/28 meters).
4. If control issues exist, call the Spektrum Service Center in the U.S. at 1-877-504-0233 for further
assistance. In the UK or Germany use one of the following addresses.
European Union: +49 4121 46199 66 (Deutschland)
or email service@horizonhobby.de
+44 (0) 1279 641 097 (United Kingdom)
or email sales@horizonhobby.co.uk
Advanced Range Testing
For sophisticated models that have significant conductive material in them, the Advanced range test
using a flight log is recommended. The advanced range check will confirm that the internal and remote
receivers are operating optimally and that the installation (position of the receivers) is optimized for
the specific aircraft. This Advanced Range Check allows the RF performance of each receiver to be
evaluated and to optimize the locations of the remote receiver.
Advanced Range Test
1. Plug a Flight Log (SPM9540 - optional) into the data port in the AR9000 and turn on the system
(Tx and Rx).
2. Advance the Flight Log until F- frame losses are displayed by pressing the button on the Flight Log.
3. Have a helper hold your aircraft while observseving the Flight Log data.
4. Standing 30 paces away from the model, face the model with the transmitter in your normal flying
position and put your transmitter into range test mode. This causes reduced power output from the
transmitter.
5. Have your helper position the model in various orientations (nose up, nose down, nose toward the
Tx, nose away from the Tx, etc.) while your helper watches the Flight Log noting any correlation
between the aircraft’s orientation and frame losses. Do this for 1 minute. The timer on the transmitter
can be used here.
Receiver Power System Requirements
Inadequate power systems that are unable to provide the necessary minimum voltage to the receiver
during flight have become the number one cause of in-flight failures. Some of the power system
components that affect the ability to properly deliver adequate power include
• Receiver battery pack (number of cells, capacity, cell type, state of charge)
• The ESC’s capability to deliver current to the receiver in electric aircraft
• The switch harness, battery leads, servo leads, regulators etc.
The AR9000 has a minimum operational voltage of 3.5 volts; it is highly recommended the power
system be tested per the guidelines below.
Recommended Power System Test Guidelines
If a questionable power system is being used (e.g. small or old battery, ESC that may not have a BEC
that will support high-current draw, etc.), it is recommended that a voltmeter be used to perform the
following tests.
Note: The Hangar 9 Digital Servo & Rx Current Meter (HAN172) or the Spektrum Flight Log
(SPM9540) is the perfect tool to perform the test below.
Plug the voltmeter into an open channel port in the receiver and with the system on, load the control
surfaces (apply pressure with your hand) while monitoring the voltage at the receiver. The voltage
should remain above 4.8 volts even when all servos are heavily loaded.
Note: The latest generations of Nickel-Metal Hydride batteries incorporate a new chemistry
mandated to be more environmentally friendly. These batteries when charged with peak detection
fast chargers have tendencies to false peak (not fully charge) repeatedly. These include all brands
of NiMH batteries. If using NiMH packs, be especially cautious when charging, making absolutely
sure that the battery is fully charged. It is recommended to use a charger that can display total charge
capacity. Note the number of mAh put into a discharged pack to verify it has been charged to full
capacity.
QuickConnect™ With Brownout Detection
Your AR9000 features QuickConnect with Brownout Detection.
• Should an interruption of power occur (brownout), the system will reconnect immediately when
power is restored (QuickConnect).
• The LED on the receiver will ash slowly indicating a power interruption (brownout) has occurred.
• Brownouts can be caused by an inadequate power supply (weak battery or regulator), a loose
connector, a bad switch, an inadequate BEC when using an Electronic speed controller, etc.
• Brownouts occur when the receiver voltage drops below 3.5 volts thus interrupting control as the
servos and receiver require a minimum of 3.5 volts to operate.
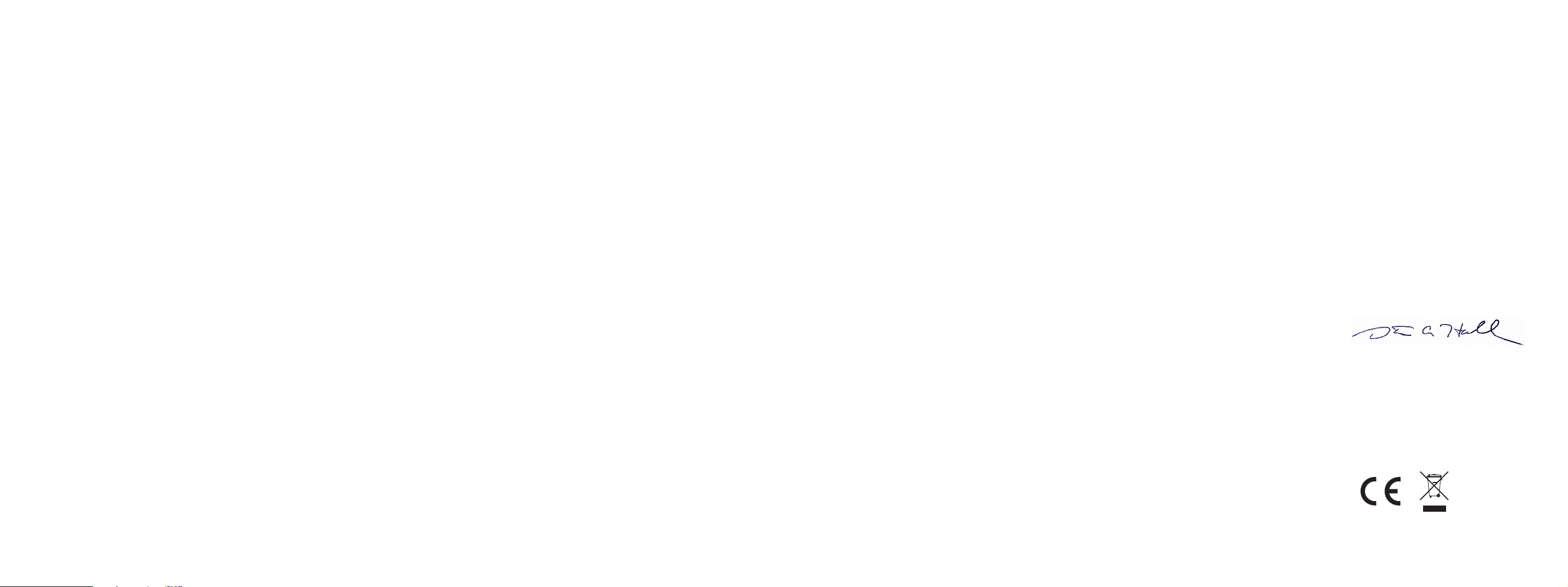
How QuickConnect With Brownout Detection Works
• When the receiver voltage drops below 3.5 volts the system drops out (ceases to operate).
• When power is restored the receiver immediately attempts to reconnect to the last two frequencies
that it was connected to.
• If the two frequencies are present (the transmitter was left on) the system reconnects typically about
4/100 of a second.
QuickConnect with Brownout Detection is designed to allow you to fly safely through most short
duration power interruptions, however, the root cause of these interruptions must be corrected before
the next flight to prevent a crash.
Note: If a brownout occurs in flight it is vital that the cause of the brownout be determined and corrected.
Flight Log (SPM9540 Optional)
The Flight Log is compatible with the AR9000. The Flight Log displays overall RF link performance as
well as the individual internal and external receiver link data. Additionally it displays receiver voltage.
Using the Flight Log
After a flight and before turning off the receiver or transmitter, plug the Flight Log into the Data port on
the AR9000. The screen will automatically display voltage e.g. 6v2= 6.2 volts.
Note:
When the voltage reaches 4.8 volts or less, the screen will flash indicating low voltage.
Press the button to display the following information:
A – Antenna fades on internal antenna A
B – Antenna fades on internal antenna B
L – Antenna fades on the left external antenna
R – Antenna fades on the right external antenna
F – Frame loss
H – Holds
Note:
– – – (three dashed lines) will appear if the antenna is not attached
Antenna fades—represents the loss of a bit of information on that specific antenna.
Typically it’s normal to have as many as 50 to 100 antenna fades during a flight. If any single antenna
experiences over 500 fades in a single flight, the antenna should be repositioned in the aircraft to
optimize the RF link.
Frame loss—represents simultaneous antenna fades on all attached receivers.
If the RF link is performing optimally, frame losses per flight should be less than 20. A hold occurs
when 45 consecutive frame losses occur. This takes about one second. If a hold occurs during a flight,
it’s important to evaluate the system, moving the antennas to different locations and or checking to be
sure the transmitter and receivers are all working correctly.
Note: A servo extension can be used to allow the Flight Log to be plugged in more conveniently.
On some models, the Flight Log can be plugged in, attached and left on the model using
double-sided tape. Mounting the Flight Log conveniently to the side frame is common with
helicopters.
Tips on Using Spektrum 2.4GHz
ModelMatch™
Some Spektrum and JR transmitters offer a patent pending feature called ModelMatch. ModelMatch
prevents the possibility of operating a model using the wrong model memory, potentially preventing a
crash. With ModelMatch each model memory has its own unique code (GUID) and during the binding
process the code is programmed into the receiver. Later, when the system is turned on, the receiver will
only connect to the transmitter if the corresponding model memory is programmed on screen.
Note: If at any time you turn on the system and it fails to connect, check to be sure the correct
model memory is selected in the transmitter. Please note that the DX5e and Aircraft Modules do
not have ModelMatch.
While your DSM equipped 2.4GHz system is intuitive to operate, functioning nearly identically to
72MHz systems, following are a few common questions from customers.
1. Q: Which do I turn on rst, the transmitter or the receiver?
A: If the receiver is turned off first —all servos except for the throttle will be driven to their preset
failsafe positions set during binding. At this time the throttle channel doesn’t output a pulse
position preventing the arming of electronic speed controllers or in the case of an engine
powered aircraft the throttle servo remains in its current position. When the transmitter is
then turned on the transmitter scans the 2.4GHz band and acquires two open channels. Then
the receiver that was previously bound to the transmitter scans the band and finds the GUID
(Globally Unique Identifier code) stored during binding. The system then connects and
operates normally.
If the transmitter is turned on first—the transmitter scans the 2.4GHz band and acquires two
open channels. When the receiver is then turned on for a short period (the time it takes to
connect) all servos except for the throttle are driven to their preset failsafe positions while the
throttle has no output pulse. The receiver scans the 2.4GHz band looking for the previously
stored GUID and when it locates the specific GUID code and confirms uncorrupted repeatable
packet information, the system connects and normal operation takes place. Typically this takes
2 to 6 seconds.
2. Q: Sometimes the system takes longer to connect and sometimes it doesn’t connect
at all?
A: In order for the system to connect (after the receiver is bound) the receiver must receive a large
number of consecutive uninterrupted perfect packets from the transmitter in order to connect.
This process is purposely critical of the environment ensuring that it’s safe to fly when the system
does connect. If the transmitter is too close to the receiver (less than 4 ft.) or if the transmitter
is located near metal objects (metal TX case, the bed of a truck, the top of a metal work bench,
etc.) connection will take longer and in some cases connection will not occur as the system is
receiving reflected 2.4GHz energy from itself and is interpreting this as unfriendly noise. Moving
the system away from metal objects or moving the transmitter away from the receiver and
powering the system again will cause a connection to occur. This only happens during the initial
connection. Once connected the system is locked in and should a loss of signal occur (failsafe)
the system connects immediately (4ms) when signal is regained.
3. Q: I’ve heard that the DSM system is less tolerant of low voltage. Is this correct?
A: All DSM receivers have an operational voltage range of 3.5 to 9.6 volts. With most systems this
is not a problem as in fact most servos cease to operate at around 3.8 volts. When using multiple
high-current draw servos with a single or inadequate battery/power source, heavy momentary
loads can cause the voltage to dip below this 3.5-volt threshold thus causing the entire system
(servos and receiver) to brown out. When the voltage drops below the low voltage threshold
(3.5 volts), the DSM receiver must reboot (go through the startup process of scanning the band
and finding the transmitter) and this can take several seconds. Please read the receiver power
requirement section as this explains how to test for and prevent this occurrence.
4. Q: Sometimes my receiver loses its bind and won’t connect requiring rebinding.
What happens if the bind is lost in ight?
A: The receiver will never lose its bind unless it’s instructed to. It’s important to understand that
during the binding process the receiver not only learns the GUID (code) of the transmitter but
the transmitter learns and stores the type of receiver that it’s bound to. If the transmitter is placed
into bind mode, the transmitter looks for the binding protocol signal from a receiver. If no signal
is present, the transmitter no longer has the correct information to connect to a specific receiver
and in essence the transmitter has been “unbound” from the receiver. We’ve had several DX7
customers that use transmitter stands or trays that unknowingly depress the bind button and the
system is then turned on losing the necessary information to allow the connection to take place.
We’ve also had DX7 customers that didn’t fully understand the range test process and pushed the
bind button before turning on the transmitter also causing the system to “lose its bind.”
Age Recommendation: 14 years or over. This is not a toy. This product is not intended for use by
children without direct adult supervision.
Warranty Period
Exclusive Warranty- Horizon Hobby, Inc., (Horizon) warranties that the Products purchased (the “Product”)
will be free from defects in materials and workmanship for a period of 1 year from the date of purchase by
the Purchaser.
Limited Warranty
(a) This warranty is limited to the original Purchaser (“Purchaser”) and is not transferable. REPAIR OR
REPLACEMENT AS PROVIDED UNDER THIS WARRANTY IS THE EXCLUSIVE REMEDY OF THE
PURCHASER. This warranty covers only those Products purchased from an authorized Horizon dealer.
Third party transactions are not covered by this warranty. Proof of purchase is required for warranty claims.
Further, Horizon reserves the right to change or modify this warranty without notice and disclaims all other
warranties, express or implied.
(b) Limitations- HORIZON MAKES NO WARRANTY OR REPRESENTATION, EXPRESS OR IMPLIED,
ABOUT NON-INFRINGEMENT, MERCHANTABILITY OR FITNESS FOR A PARTICULAR PURPOSE OF THE
PRODUCT. THE PURCHASER ACKNOWLEDGES THAT THEY ALONE HAVE DETERMINED THAT THE
PRODUCT WILL SUITABLY MEET THE REQUIREMENTS OF THE PURCHASER’S INTENDED USE.
(c) Purchaser Remedy- Horizon’s sole obligation hereunder shall be that Horizon will, at its option, (i)
repair or (ii) replace, any Product determined by Horizon to be defective. In the event of a defect, these are
the Purchaser’s exclusive remedies. Horizon reserves the right to inspect any and all equipment involved
in a warranty claim. Repair or replacement decisions are at the sole discretion of Horizon. This warranty
does not cover cosmetic damage or damage due to acts of God, accident, misuse, abuse, negligence,
commercial use, or modification of or to any part of the Product. This warranty does not cover damage due
to improper installation, operation, maintenance, or attempted repair by anyone other than Horizon. Return
of any goods by Purchaser must be approved in writing by Horizon before shipment.
Damage Limits
HORIZON SHALL NOT BE LIABLE FOR SPECIAL, INDIRECT OR CONSEQUENTIAL DAMAGES, LOSS OF
PROFITS OR PRODUCTION OR COMMERCIAL LOSS IN ANY WAY CONNECTED WITH THE PRODUCT,
WHETHER SUCH CLAIM IS BASED IN CONTRACT, WARRANTY, NEGLIGENCE, OR STRICT LIABILITY.
Further, in no event shall the liability of Horizon exceed the individual price of the Product on which liability
is asserted. As Horizon has no control over use, setup, final assembly, modification or misuse, no liability
shall be assumed nor accepted for any resulting damage or injury. By the act of use, setup or assembly, the
user accepts all resulting liability.
If you as the Purchaser or user are not prepared to accept the liability associated with the use of this Product,
you are advised to return this Product immediately in new and unused condition to the place of purchase.
Law: These Terms are governed by Illinois law (without regard to conflict of law principals).
Safety Precautions
This is a sophisticated hobby Product and not a toy. It must be operated with caution and common sense
and requires some basic mechanical ability. Failure to operate this Product in a safe and responsible
manner could result in injury or damage to the Product or other property. This Product is not intended
for use by children without direct adult supervision. The Product manual contains instructions for safety,
operation and maintenance. It is essential to read and follow all the instructions and warnings in the
manual, prior to assembly, setup or use, in order to operate correctly and avoid damage or injury.
Questions, Assistance, and Repairs
Your local hobby store and/or place of purchase cannot provide warranty support or repair. Once assembly,
setup or use of the Product has been started, you must contact Horizon directly. This will enable Horizon to
better answer your questions and service you in the event that you may need any assistance. For questions
or assistance, please direct your email to productsupport@horizonhobby.com, or call 877.504.0233 toll
free to speak to the Product Support department.
Inspection or Repairs
If this Product needs to be inspected or repaired, please call for a Return Merchandise Authorization (RMA).
Pack the Product securely using a shipping carton. Please note that original boxes may be included, but
are not designed to withstand the rigors of shipping without additional protection. Ship via a carrier that
provides tracking and insurance for lost or damaged parcels, as Horizon is not responsible for merchandise
until it arrives and is accepted at our facility. A Service Repair Request is available at www.horizonhobby.
com on the “Support” tab. If you do not have internet access, please include a letter with your complete
name, street address, email address and phone number where you can be reached during business days,
your RMA number, a list of the included items, method of payment for any non-warranty expenses and a
brief summary of the problem. Your original sales receipt must also be included for warranty consideration.
Be sure your name, address, and RMA number are clearly written on the outside of the shipping carton.
Warranty Inspection and Repairs
To receive warranty service, you must include your original sales receipt verifying the proof-of-purchase
date. Provided warranty conditions have been met, your Product will be repaired or replaced free of charge.
Repair or replacement decisions are at the sole discretion of Horizon Hobby.
Non-Warranty Repairs
Should your repair not be covered by warranty the repair will be completed and payment will be required
without notification or estimate of the expense unless the expense exceeds 50% of the retail purchase cost.
By submitting the item for repair you are agreeing to payment of the repair without notification. Repair
estimates are available upon request. You must include this request with your repair. Non-warranty repair
estimates will be billed a minimum of ½ hour of labor. In addition you will be billed for return freight.
Please advise us of your preferred method of payment. Horizon accepts money orders and cashiers checks,
as well as Visa, MasterCard, American Express, and Discover cards. If you choose to pay by credit card,
please include your credit card number and expiration date. Any repair left unpaid or unclaimed after 90
days will be considered abandoned and will be disposed of accordingly. Please note: non-warranty repair is
only available on electronics and model engines.
Electronics and engines requiring inspection or repair should be shipped to the following address:
Horizon Service Center
4105 Fieldstone Road
Champaign, Illinois 61822
All other Products requiring warranty inspection or repair should be shipped to the following address:
Horizon Product Support
4105 Fieldstone Road
Champaign, Illinois 61822
Please call 877-504-0233 or e-mail us at productsupport@horizonhobby.com with any questions or
concerns regarding this product or warranty.
European Union:
Electronics and engines requiring inspection or repair should be shipped to one of the following addresses:
Horizon Hobby UK
Units 1-4 Ployters Rd
Staple Tye, Harlow
Essex CM18 7NS
Please call +44 (0) 1279 641 097 or email sales@horizonhobby.co.uk
with any questions or concerns regarding this product or warranty.
Please call +49 4121 46199 66 or email service@horizonhobby.de
with any questions or concerns regarding this product or warranty.
United Kingdom
Horizon Technischer Service
Hamburger Str. 10
25335 Elmshorn
Germany
FCC Information
This device complies with part 15 of the FCC rules. Operation is subject to the following two
conditions: (1) This device may not cause harmful interference, and (2) this device must accept any
interference received, including interference that may cause undesired operation.
Caution: Changes or modifications not expressly approved by the party responsible for
compliance could void the user’s authority to operate the equipment.
This product contains a radio transmitter with wireless technology which has been tested and found
to be compliant with the applicable regulations governing a radio transmitter in the 2.400GHz to
2.4835GHz frequency range.
Declaration of Conformity
(in accordance with ISO/IEC 17050-1)
No. HH20081023
Product(s): AR9000 Receiver
Item Number(s): SPMAR9000
The object of declaration described above is in conformity with the requirements of the specifications listed below, following the provisions of the European R&TTE directive 1999/5/EC:
EN 300-328, v1.7.1 ERM requirements for wideband transmission systems
EN 301 489-1 v.1.6.1 General EMC requirements for Radio equipment
EN 301 489-17 v.1.2.1
Signed for and on behalf of:
Horizon Hobby, Inc.
Champaign, IL USA
Oct. 23, 2008
Steven A. Hall
Vice President
International Operations and Risk Management
Horizon Hobby, Inc.
Instructions for Disposal of WEEE by Users in the
European Union
This product must not be disposed of with other waste. Instead, it is the user’s responsibility
to dispose of their waste equipment by handing it over to a designated collection point for the
recycling of waste electrical and electronic equipment. The separate collection and recycling of your
waste equipment at the time of disposal will help to conserve natural resources and ensure that it is
recycled in a manner that protects human health and the environment. For more information about
where you can drop off your waste equipment for recycling, please contact your local city office,
your household waste disposal service or where you purchased the product.
© 2008 Horizon Hobby, Inc. Spektrum radios and accessories are distributed exclusively by Horizon Hobby, Inc.
4105 Fieldstone Road, Champaign, IL 61822 Call toll-free, 877-504-0233.
DSM and DSM2 are trademarks or registered trademarks of Horizon Hobby, Inc.
The Spektrum trademark is used with permission of Bachmann Industries, Inc.
US patent number 7,391,320. Other patents pending.
operating in the 2.4 GHz ISM band
Revised 11/08 10653.1