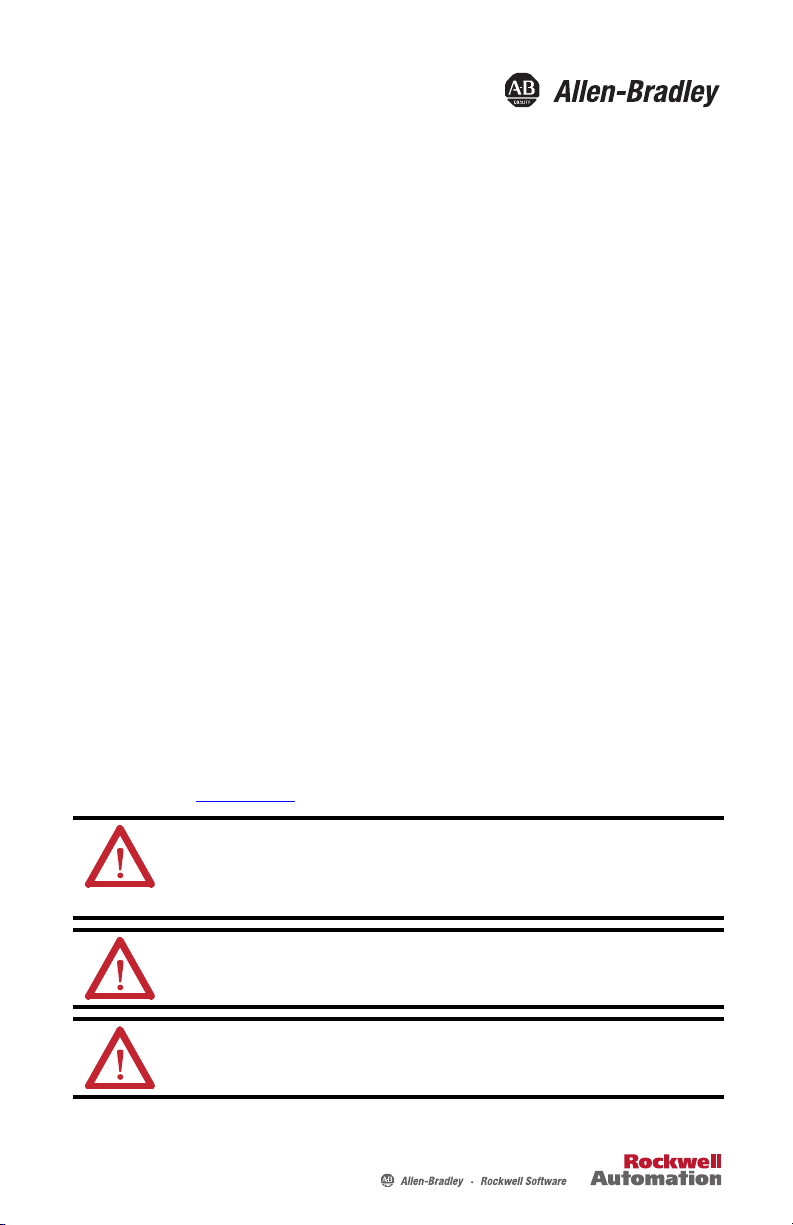
Installation Instructions
Single Motor Cables with Circular DIN
Connector Type 923
Catalog Numbers 2090-CSBM1DF-14AAxx, 2090-CSBM1DF-14AFxx,
2090-CSBM1DF-18AAxx, 2090-CSBM1DF-18AFxx, 2090-CSWM1DF-14AAxx,
2090-CSWM1DF-18AAxx
About Single Motor Cables
These single motor cables have an M23 SpeedTec connector at the motor end, and flying leads at
the drive end. These cables can be bent or reformed during installation or maintenance. The list
below describes the standard and continuous-flex operations for the cables:
• Use 2090-CSBM1DF-xxAFxx cables in continuous-flex operations
(available only with brake).
• Use 2090-CSxM1DF-xxAAxx cables in standard (non-flex) operations
(available with or without brake).
Installing Single Motor Cables
Follow these safety notices when installing this cable between a servo drive and a motor.
Additional precautions are noted in the Kinetix Motion Accessories Specifications Technical
Data, publication GMC-TD004.
ATTENTION: Always remove power to the ser vo drive before connec ting or disconnecting
cables at the drive or at the motor.
Arcing or unexpected motion can occur if the cable is connected or disconnec ted while power is
applied to the drive.
ATTENTION: Always ground the overall shield of the cable. Doing so improves system EMC/EMI
performance and helps to provide uninterrupted operation. Electrical noise can cause
communication signals to fail.
ATTENTION: Do not tightly gather or coil a cable that transfers power. Heat is generated within
a cable whenever power is applied and only an uncoiled cable can freely dissipate that heat.

2 Single Motor Cables with Circular DIN Connector Type 923
Limited-bend Zone
or
Continuous-flex Zone
Installation
Area
Installation
Area
Signal
Labels
Exposed Shield
Shrink
Wrap
Refer to Specifications
on page 4 for recommended
bend and flex zone radius values.
Exposed
Shield
2090-CSBM1DF-xxAAxx cable and
2090-CSBM1DF-xxAFxx cable shown.
76.2 mm
(3.0 in.)
76.2 mm
(3.0 in.)
Bend
Radius
Bend Radius
The feedback wire pair (Data+/Data-) requires a metallic feedback connector kit for proper
signal termination. Refer to Additional Resources on page 4 for the installation instructions for
the feedback connector kit and other related publications.
The feedback connector kit is included with the Kinetix® 5500 servo drive.
Follow these guidelines when installing a single motor cable:
• Do not bend the cable within 76.2 mm (3.0 in.) of the connector or the flying lead end.
See the Installation Guidelines
illustration.
• Do not exceed the bend radius limitation specified in the Specifications on page 4.
• Refer to Cable Pinouts and Schematics on page 3 to identify each wire and its respective
drive connection.
• Remove and discard the protective sleeve from the data signal wires shortly before you
install these wires on the Kinetix 5500 feedback connector kit.
• Connect unused brake conductors to the drive to prevent accidental contact.
For continuous-flex cables, follow these additional installation requirements:
• The continuous-flex zone is the area where the cable can repeatedly flex up to its
specified bend radius.
• Installation areas require rigid mounting to prevent the cable from flexing where it
connects to other components.
Installation Guidelines
Rockwell Automation Publication 2090-IN040B-EN-P - May 2013