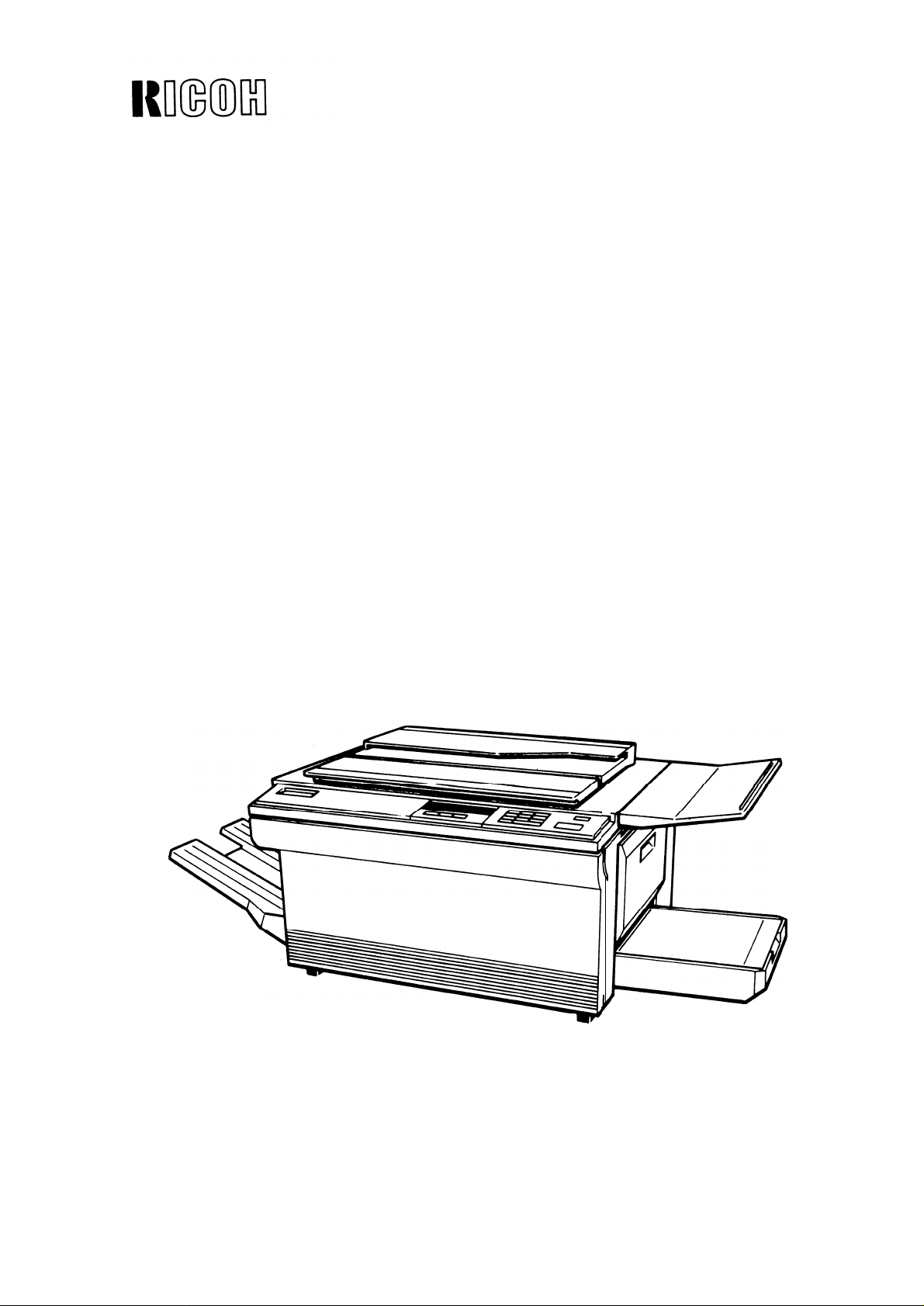
FT3320
FIELD SERVICE MANUAL
ICOH COMPANY, LTD.
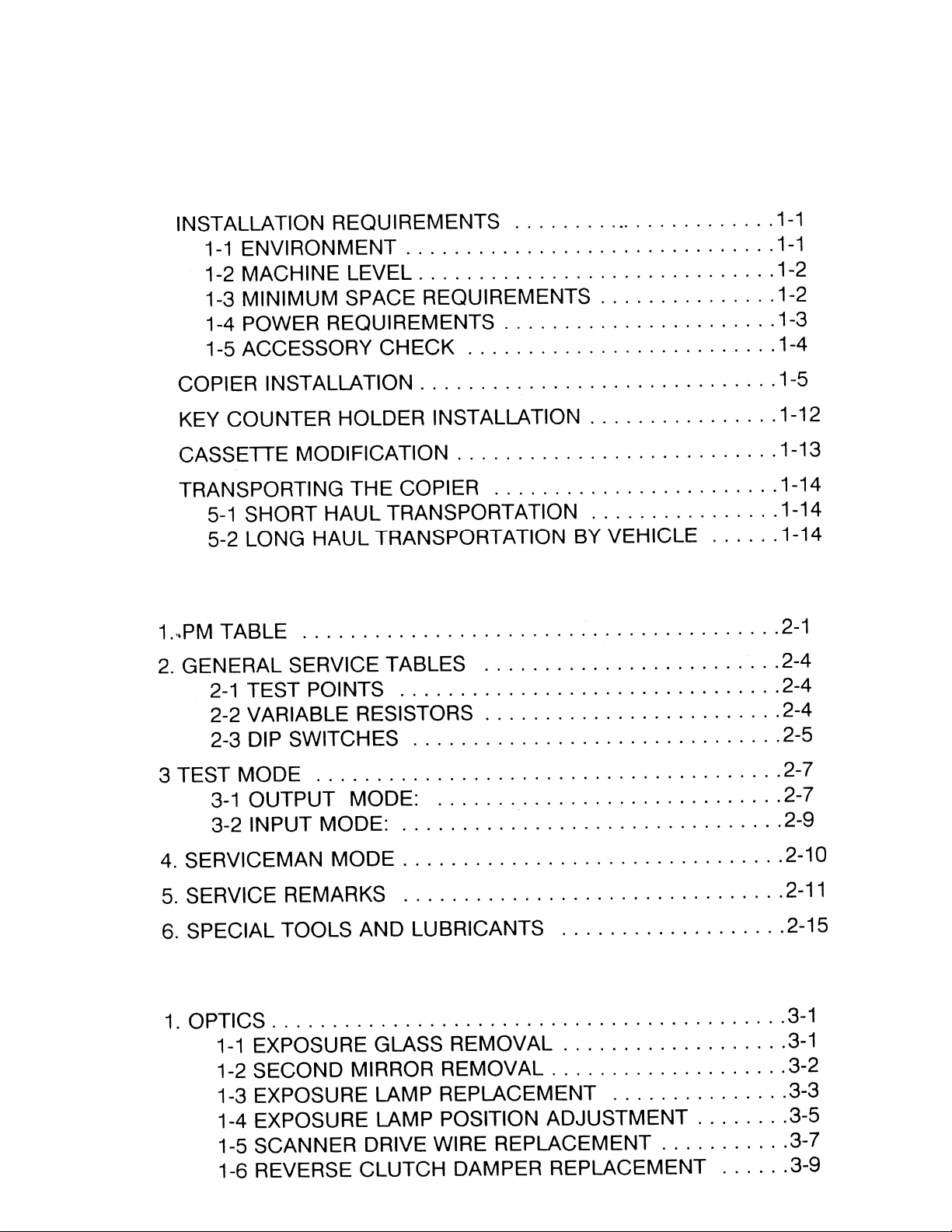
INSTALLATION
1
.
2
3
4
5
Table of Contents
SERVICE TABLES
REPLACEMENT AND ADJUSTMENT
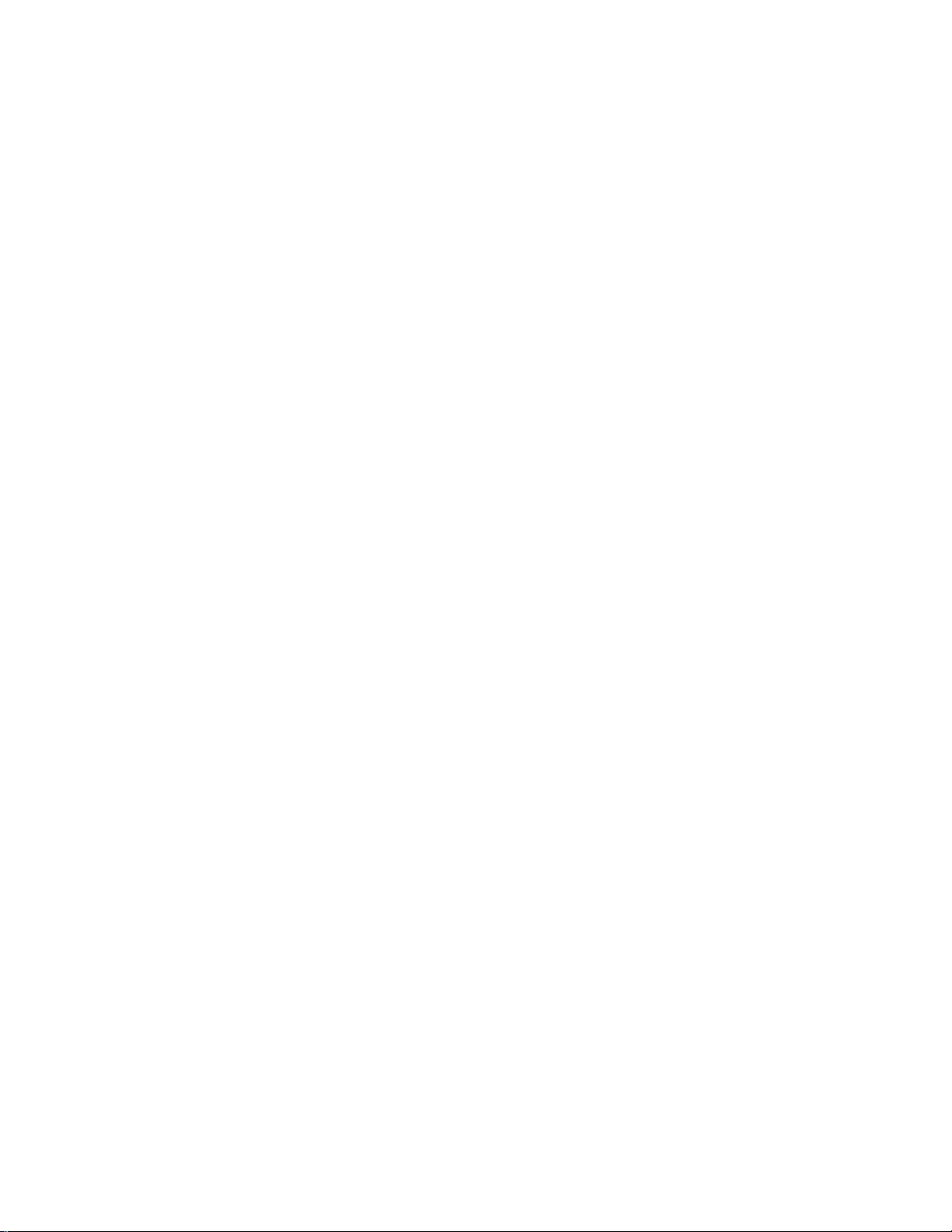
VINYL ENVELOPE
POINT-TO-POINT
ELECTRICAL COMPONENT AND CONNECTOR LAYOUTS
TABLE OF ADJUSTMENTS
SERVICE TABLES
●

Q
SECTION 1
INSTALLATION
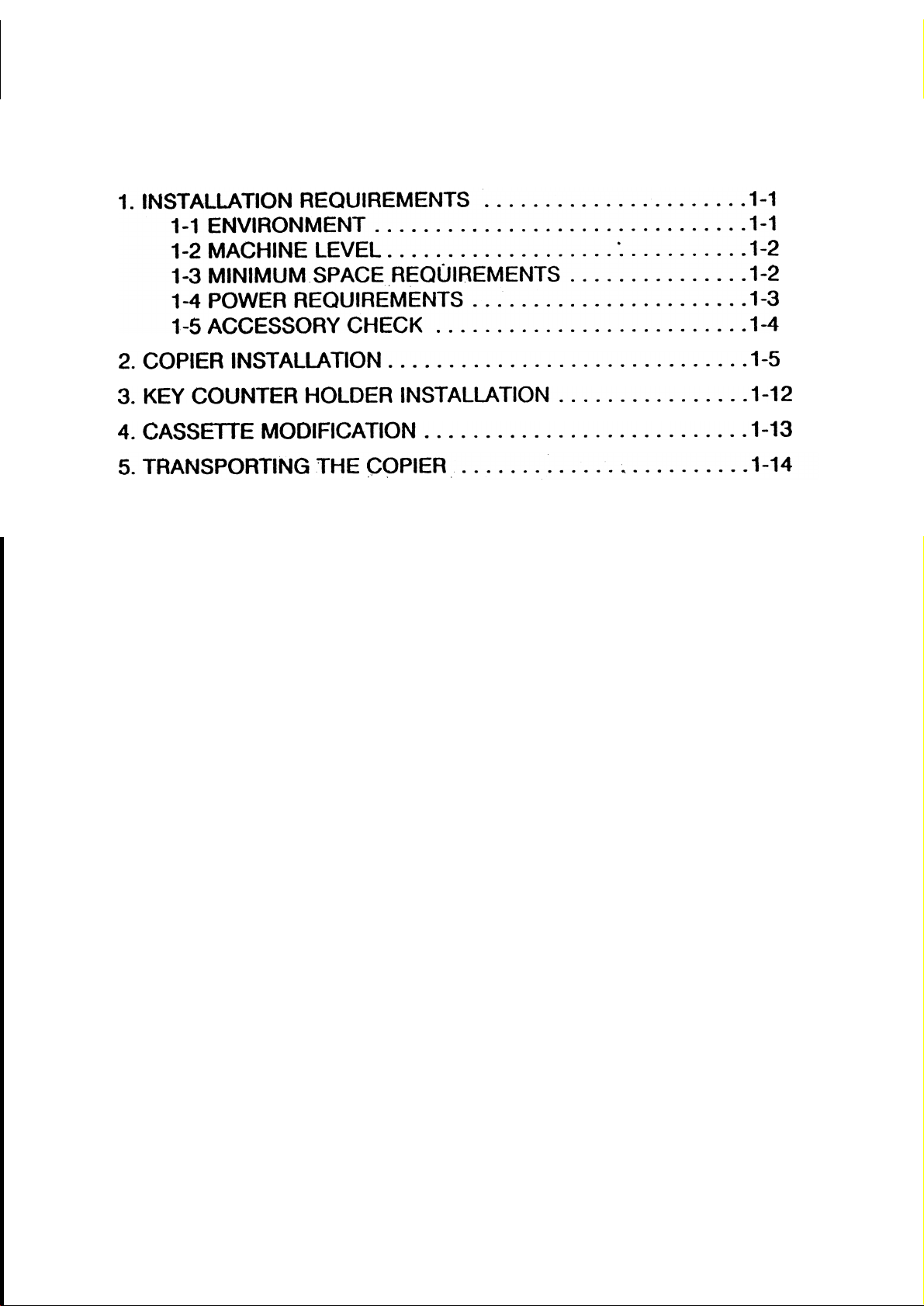
INSTALLATION
5-1 SHORT HAUL TRANSPORTATION .............................1-14
5-2 LONG HAUL TRANSPORTATION BY VEHICLE ..... ...1-14
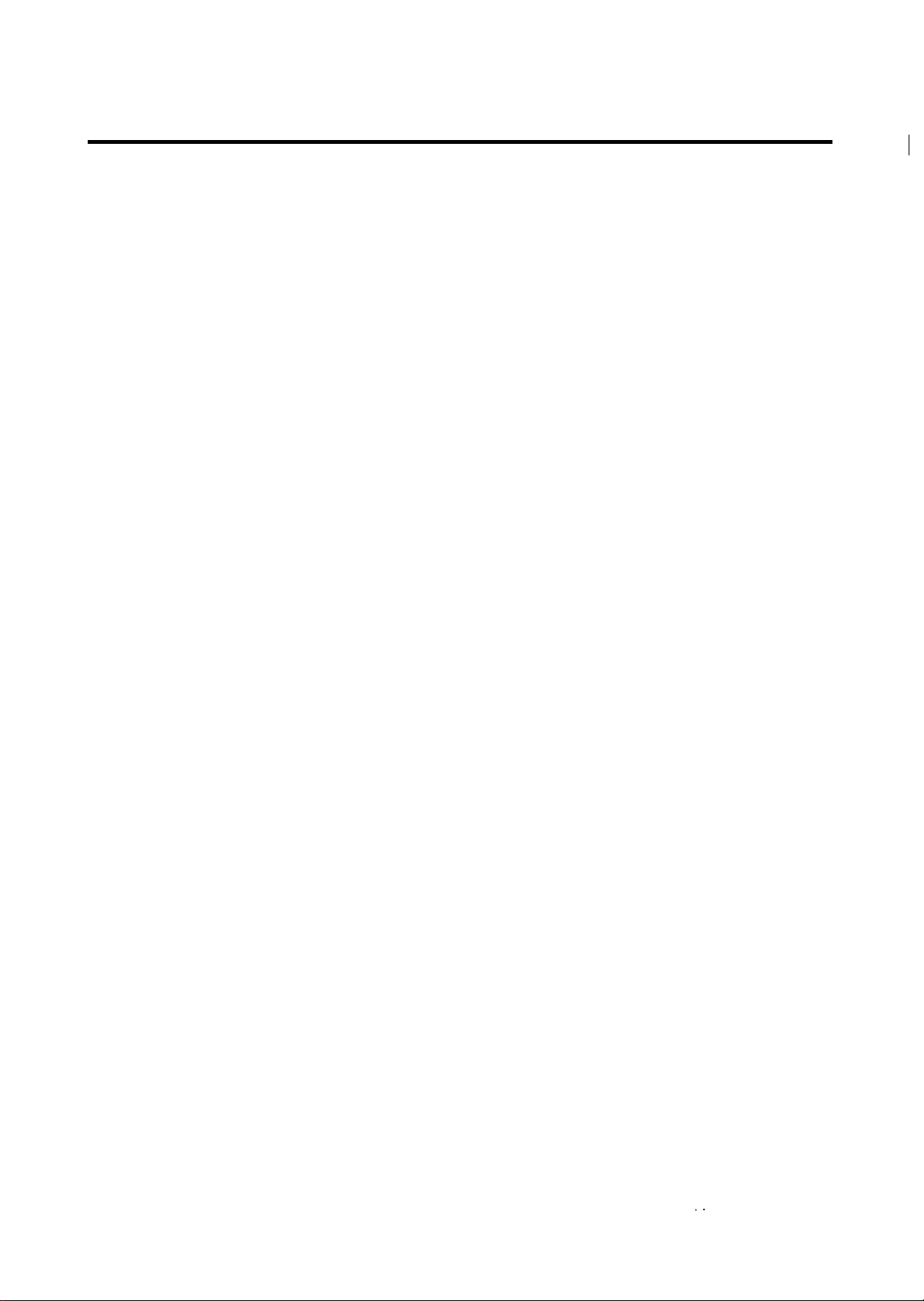
1. INSTALLATION REQUIREMENTS
1-1 ENVIRONMENT
1 NOV. ’87
1. Temperature Range:
2. Humidity Range:
3. Ambient Illumination:
10*C to 30°C (50°F to 86°F)
15% to 90% RH
Less than 1,500 Iux (Do not expose to direct
sunlight.)
4. Ventilation:
5. Ambient Dust: Less than 0.15 mg/m
6. Room Size:
Room air should turn over at least 3 times/hour.
3
(4 x 10
-3
oz/yd3)
More than 10 m3 (13.4 yd3)
7. If the installation place is air-conditioned or heated, place the machine:
Where it will not be subjected to sudden temperature changes.
●
Where it will not be directly exposed to cool air from an air conditioner
●
in the summer.
Where it will not be directly exposed to reflected heat from a space
●
heater in winter.
8. Avoid placing the copier in an area filled with corrosive gas.
9. Avoid any areas higher than 2,000 meters (6,500 feet) above sea level.
10. Place the copier on a strong and level base.
11. Avoid any areas where the copier may be subjected to frequent strong
vibration.
1-1
,.
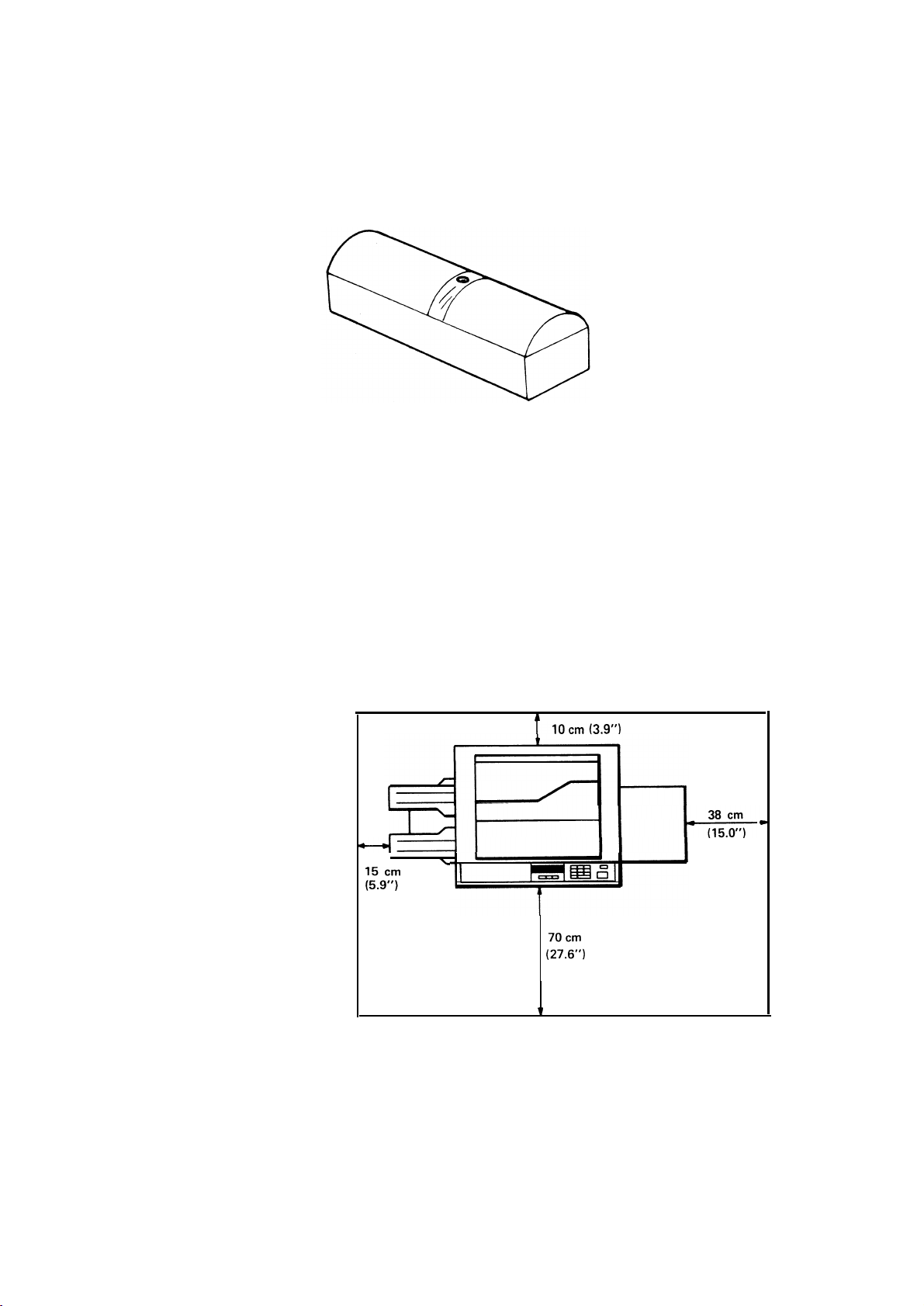
1 Nov. ’87
1-2 MACHINE LEVEL
1. Front to back: Within 5 mm (0.2”) of level.
2. Right to left: Within 5 mm (0.2”) of level.
Set a carpenter’s level on the exposure glass to check the machine level.
1-3 MINIMUM SPACE REQUIREMENTS
1. Front :70 cm (27.6”).
2. Back :10 cm (3.9”).
3. Right :38 cm (31 .5”).
4. Left
:15 cm (3.9”).
1=2
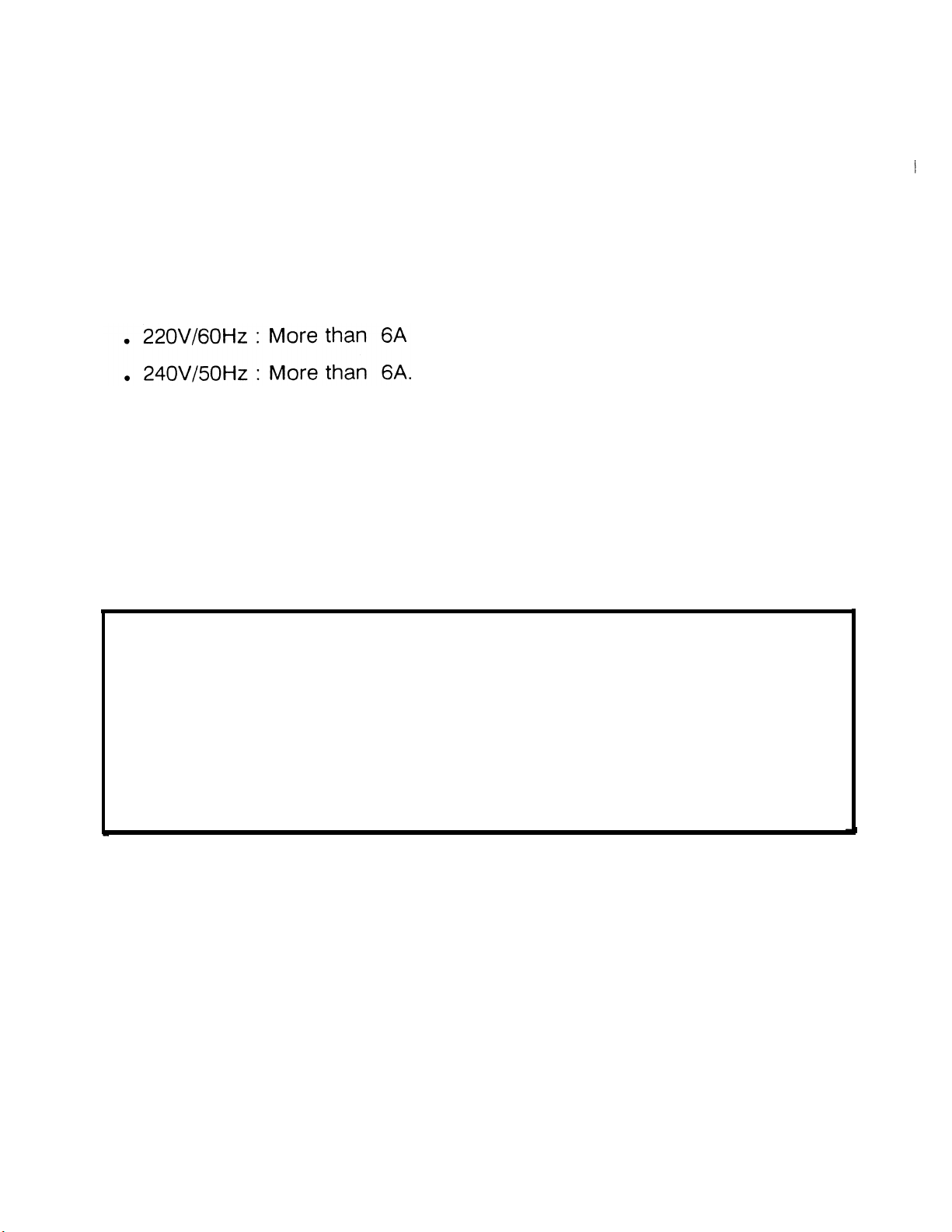
1 Nov. ’87
1-4
POWER REQUIREMENTS
1. Input voltage level:
• 110V/60Hz : More than 12A
ž115V/60Hz : More than 12A
220V/50Hz : More than 6A
•
2. Permissible voltage fluctuation: 10%.
3. Permissible extension
cord:
At least 300V, 30A capacity and less than 5
meters (16.4 ft) long.
Be sure to ground the machine.
(Do not connect the grounding wire
to a gas pipe.)
Make sure the plug is firmly inserted in the outlet.
Avoid multi-wiring.
Do not set anything on the power cord.
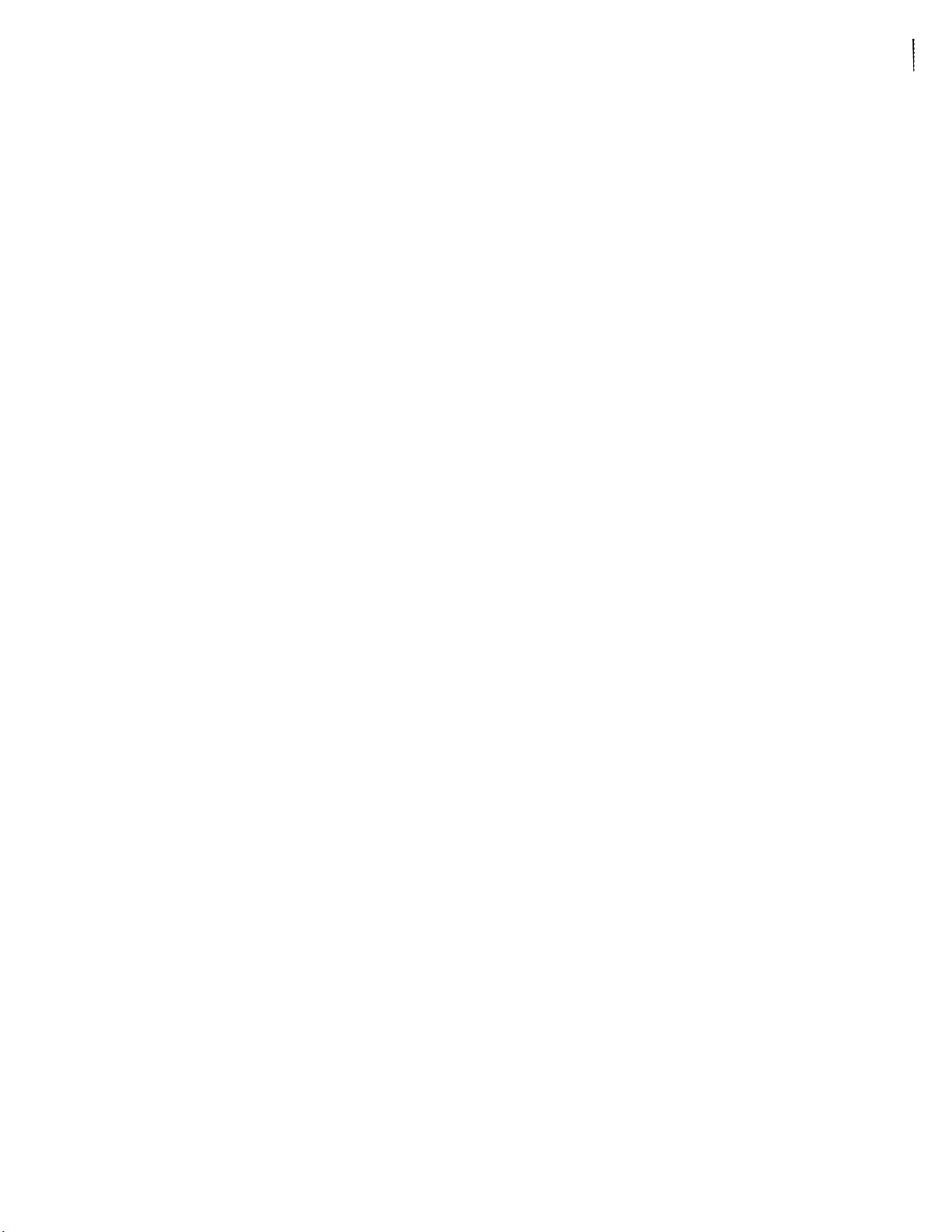
1 Nov. ’87
1-5 ACCESSORY CHECK
Check the accessories and their quantities according to the following list:
Cassette
Copy Tray
Drum
Operating Instructions
NECR
Envelope for NECR (1 15V only)
Multi-lingual Decal (220/240V only)
Paper Size Decal
1 pc
1 pc
1 pc
1 pc
1 pc
1 pc
1 pc
1 pc.
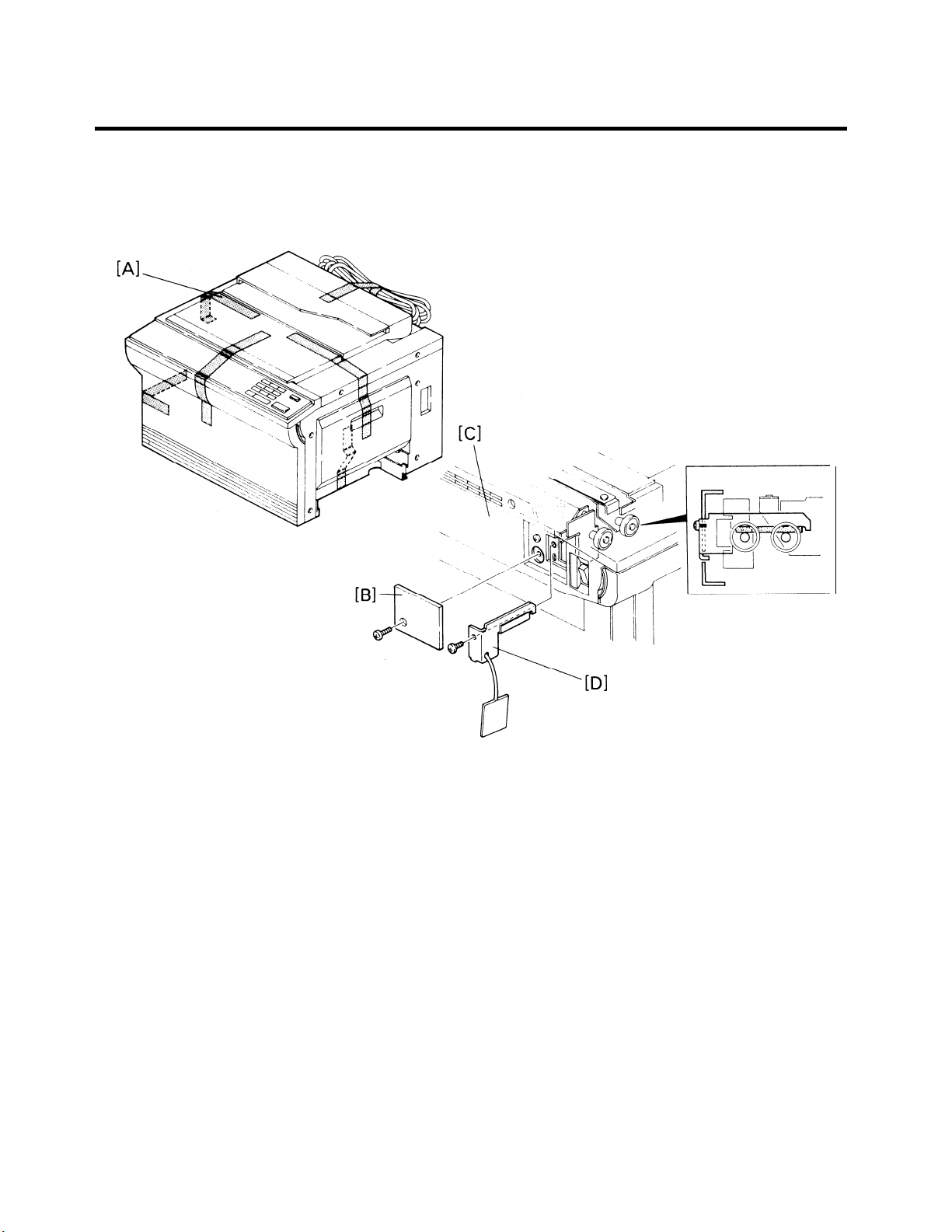
2. COPIER INSTALLATION
1 Nov. '87
1. Remove the 6 strips of shipping tape [A].
2. Remove the lock plate cover [B] from the left cover [C] (1 screw).
3. Remove the scanner lock plate [D] (1 screw).
4. Re-install the lock plate cover.
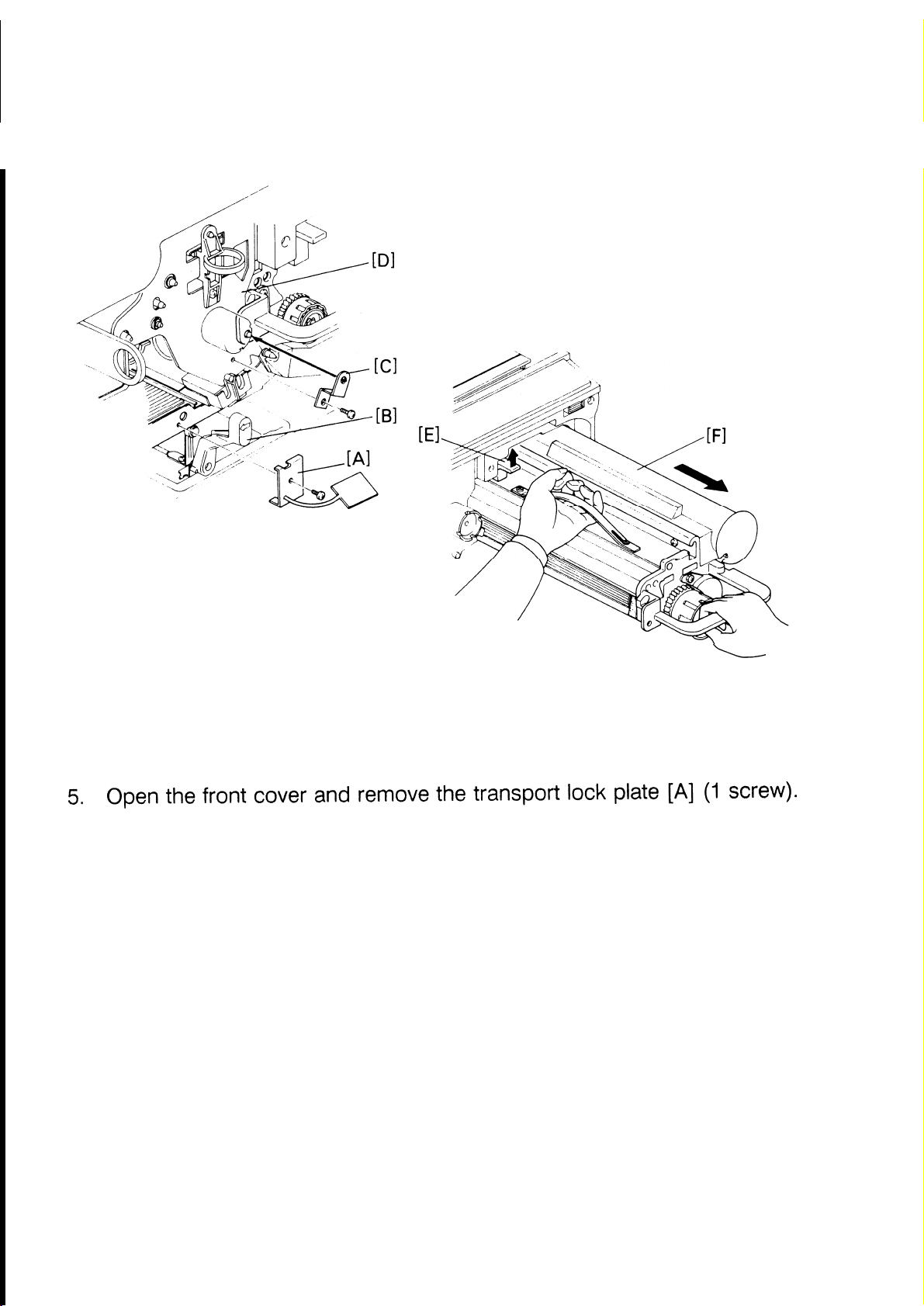
1 NOV. ’87
NOTE: When the transport lock plate is removed, the transport unit may fall
and be damaged; to prevent this, gently lower the transport unit
using the transport release lever [B].
6. Remove the development retainer plate [C] from the drum stay [D] (1
screw).
7. Raise the development lock lever [E] and pull out the development unit
[F]
●
1-6
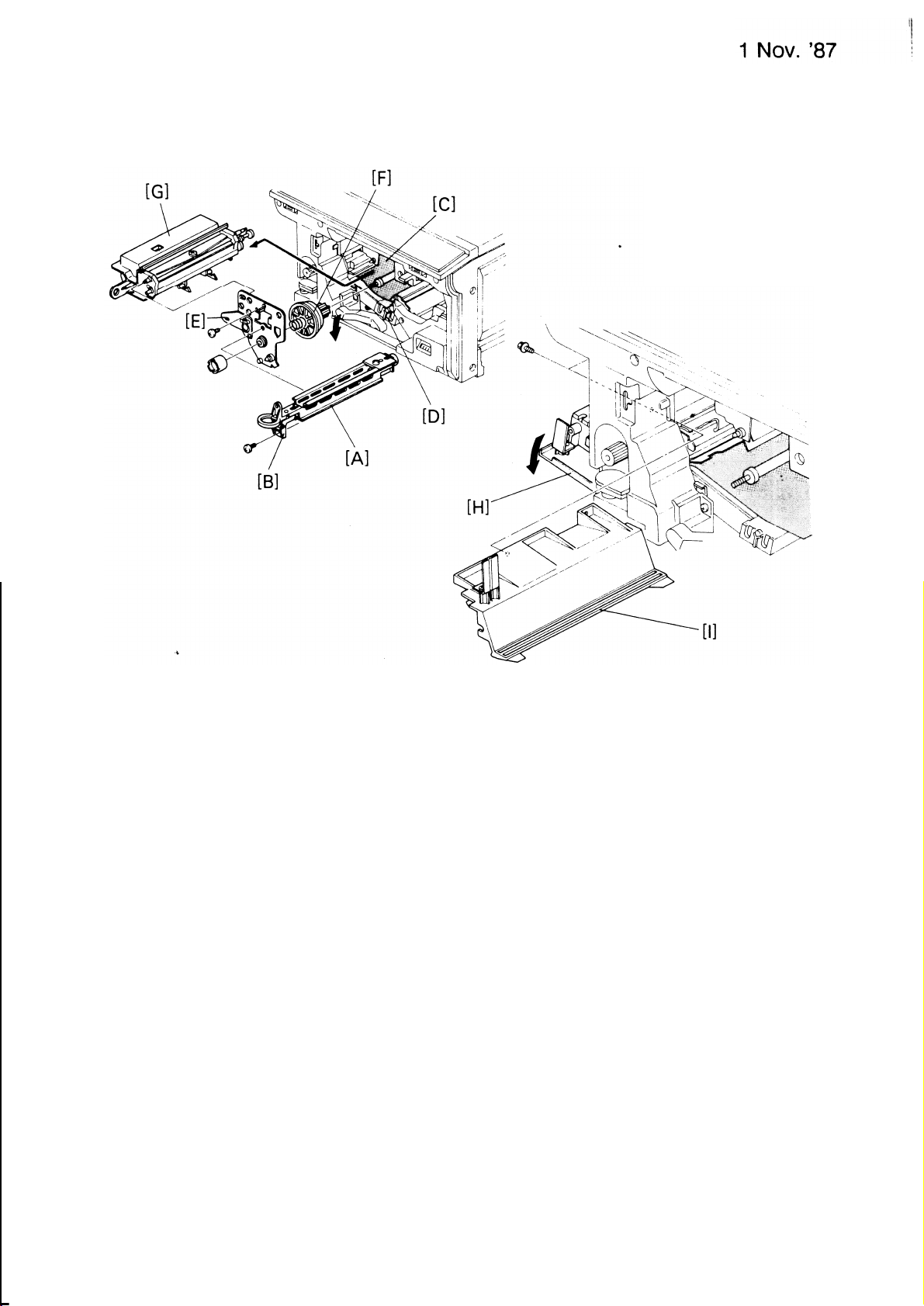
8. Remove
screw).
the charge corona unit [A] together with the wire cleaner [B] ( 1
9. Place a sheet of paper [C] over the
T/S
corona unit [D].
10. Remove the drum stay [E] (1 screw and 1 knob).
NOTE:
11
12
13.
The drum stay knob is reverse threaded.
Remove the drum flange [F], and the cleaning unit [G].
.
w
Open the exit cover [H].
Remove the fusing cover
[1] from the inside of the copier ( 2 screws).
1-7
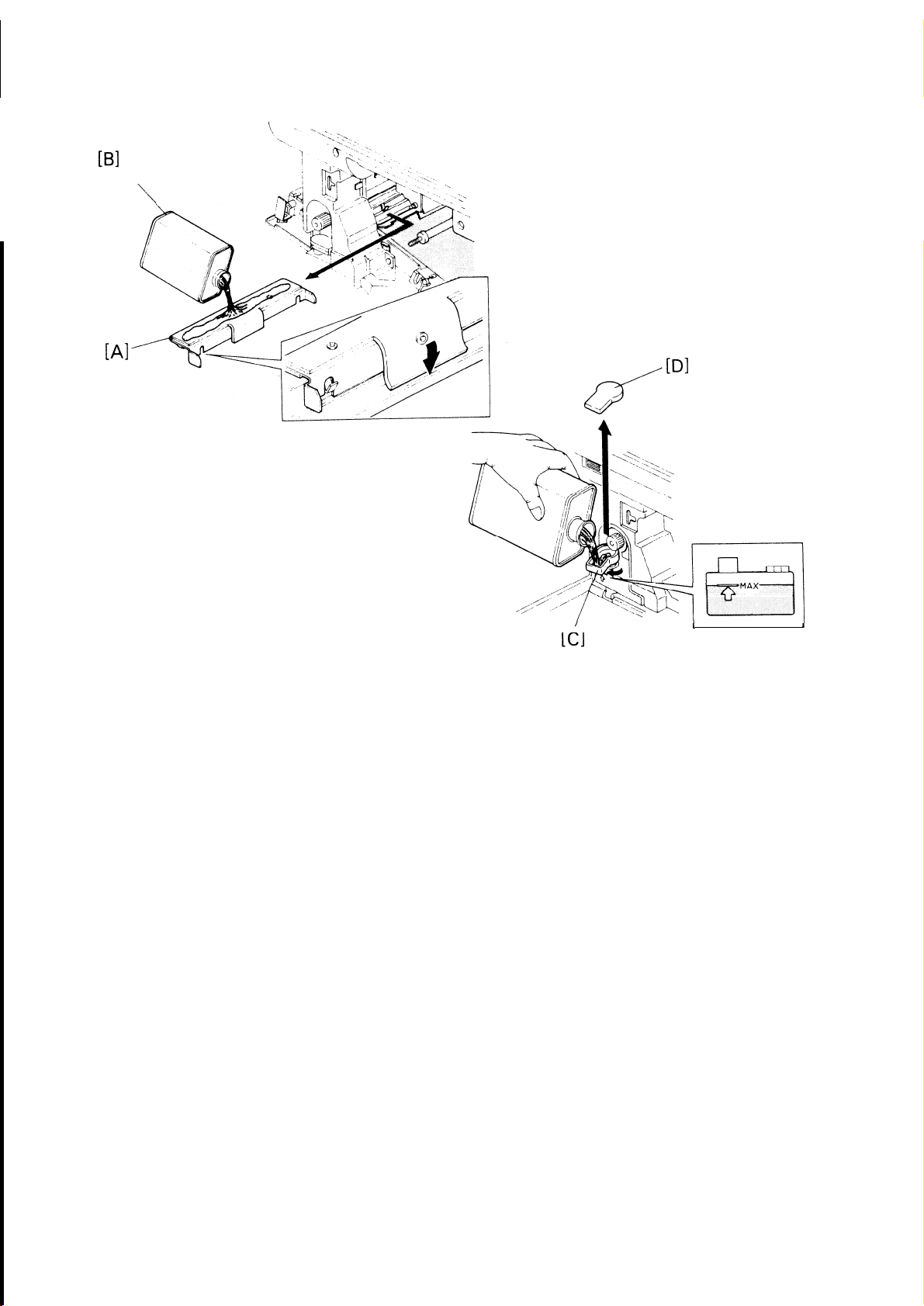
1 Nov. ’87
I
14
●
Remove the oil supply pad [A].
Prime the oil supply pad with silicone oil [B].
15
●
16
.
Re-instaH the oil supply pad.
i
NOTE: Two notches of the oil supply pad must rest on the two hooks, The
tail of the oil supply pad must be in the oil sump.
17
.
Re-install the fusing cover and close the exit cover.
18
.
Turn the mouth of the silicone oil tank [C] to the front.
19
.
Remove the silicone oil tank cap [D] and pour silicone oil into the tank.
Replace the silicone oil tank cap and
20
.
tion.
NOTE: Clean up any oil that was spilt.
turn the mouth to its original posi-
1-8
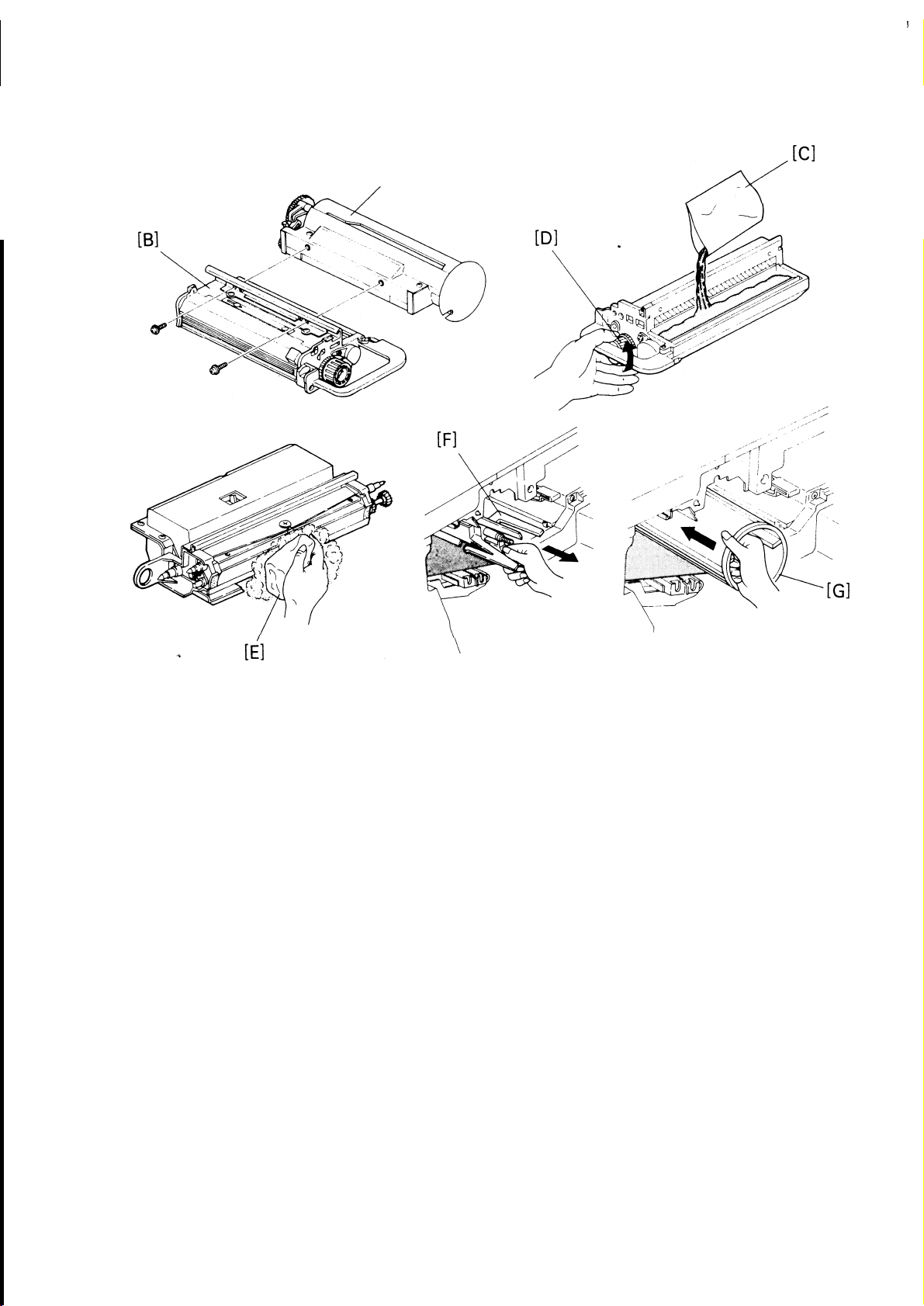
[A]
I
1 Nov. ’87
.
21
Separate the toner tank [A] from the development unit [B] (2 screws).
.
22
Pour one pack of developer (Developer Type 3300) [C] into the development unit while turning the knob [D] counterclockwise to distribute the
developer.
.
Remount the toner tank on the development unit.
23
.
24
Dust the drum, the cleaning blade, and the cleaning brush with setting
powder [E].
25
●
Pull out the drum guide [F] and insert the drum [G].
Push in the drum guide and set the drum flange.
26
1-9
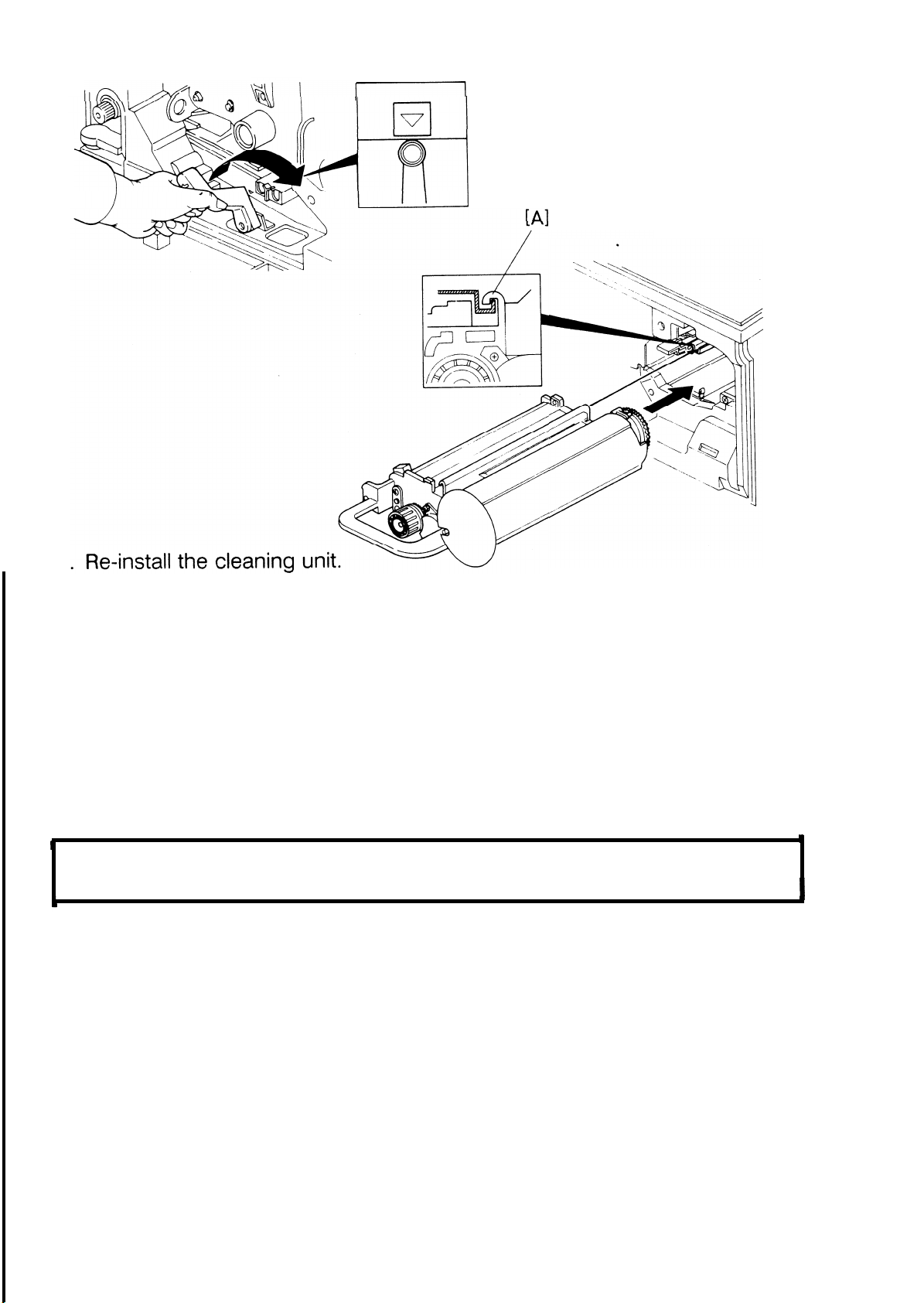
1 Nov. ’87
27
NOTE: When inserting
face.
+
28. Set the drum stay
the cleaning unit, keep it away from the drum sur-
and the charge corona unit complete
with the wire
cleaner.
29. Remove the paper
over the T/S corona unit and return
the transport
release lever until the roller is positioned under the arrow.
To prevent the drum from being damaged, do not raise the transport
unit without setting the drum stay.
30. Re-install the development unit and secure it using the development
retainer plate.
NOTE: When installing the development unit, be sure that the development
unit rail [A] is properly engaged with the unit guide rail on the
copier, but keep it away from the drum surface.
1“10
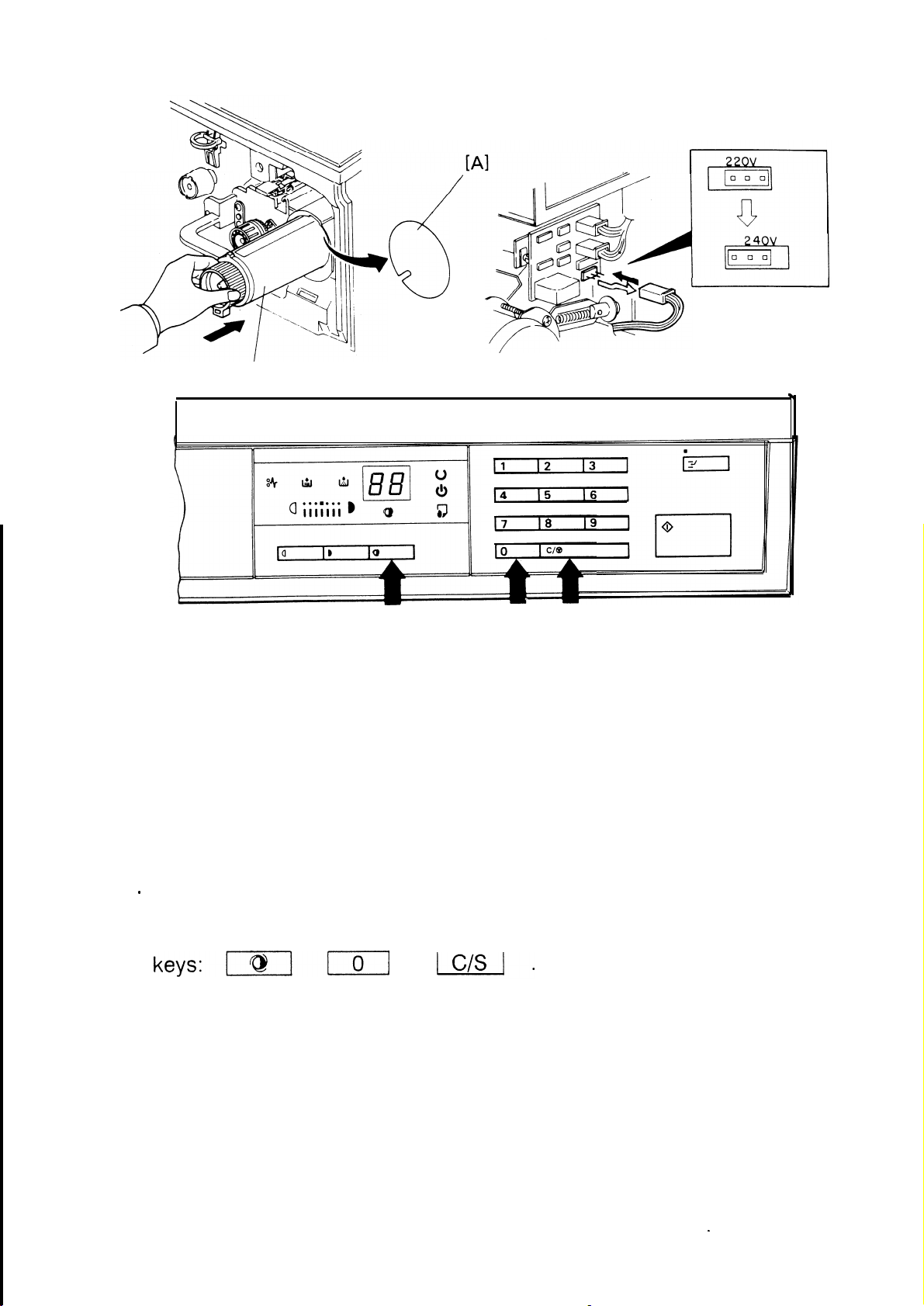
[B]
.
1 Nov. ’87
31. Remove the toner hopper seaI [A], then install one toner cartridge [B].
NOTE: Refer to the decal on the machine or the Operating Instructions for
the toner supply procedure.
32
.
For 240-volt areas, remove the rear cover (2 screws) and reposition the
220/240 -voIt connector on the ac drive board.
Load paper in the cassette, then set the cassette and the copy tray.
9
33.
.
Plug in the copier and turn on the main switch while pressing the
34
This causes the toner agitator to
rotate, filling the toner hopper with toner.
●
Check the machine operation and the copy quality,
35
●
Fill out the New Equipment Condition Report.
36
1-11
.
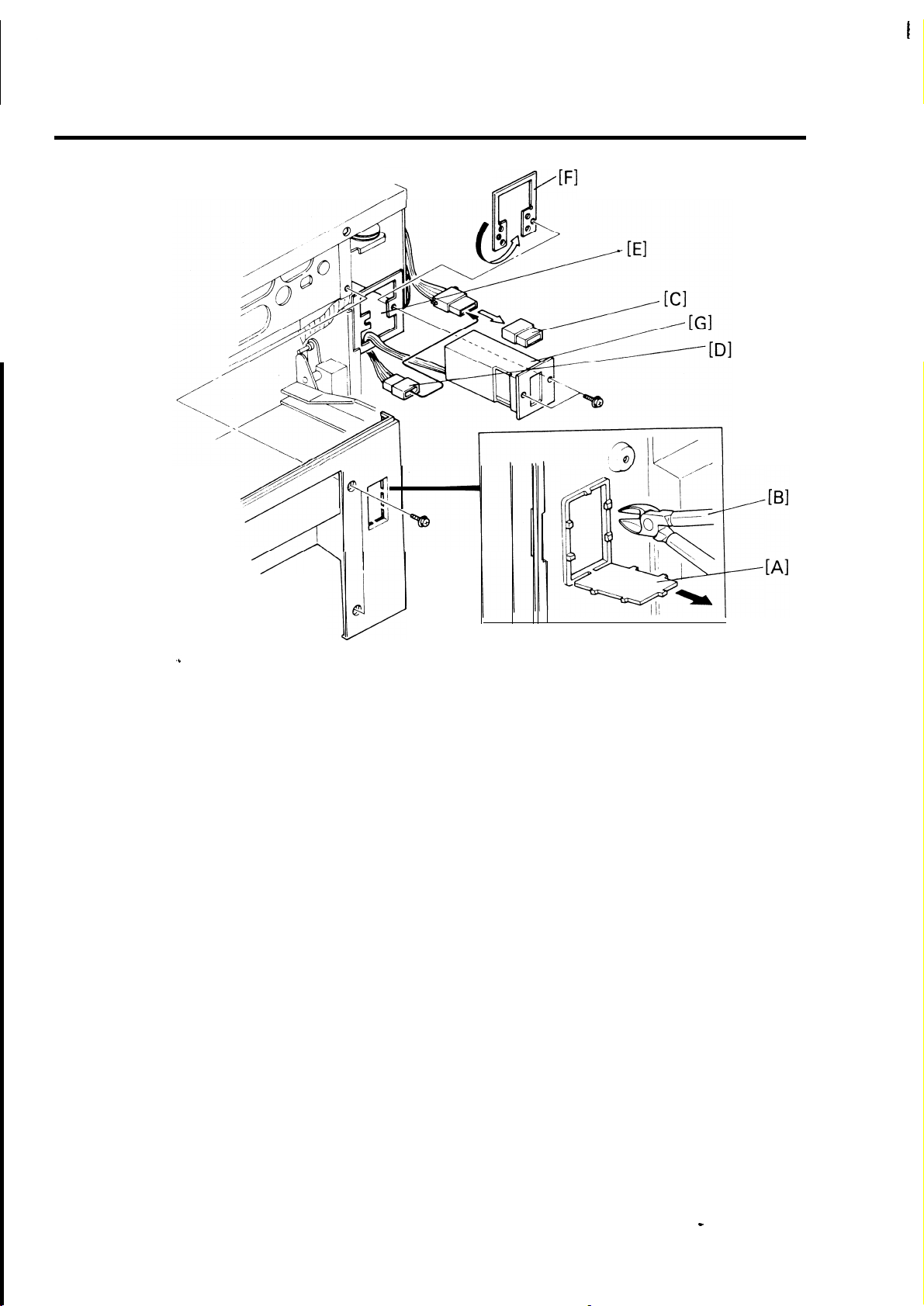
.
1 Nov. ’87
3. KEY COUNTER HOLDER INSTALLATION
[
●
Remove the rear and right covers.
1
s
●
Cut out the key counter access hole section [A] with nippers [B].
2
●
Remove the shorting plug [C] from the key counter connector (4p).
3
4
.
Connect the connector [D] (4p) of the key counter holder to the key
counter harness through the access hole [E].
.
Hold the fixing plate [F] on the inside of the key counter bracket and in-
5
sert the key counter holder [G].
.
Align the holes on the fixing plate with the mounting holes of the key
6
counter holder and secure the holder.
NOTE: The fixing plate has three sets of holes. When installing, make sure
to use the correct holes that match the type of counter.
7. Re-install the covers.
0
1-12
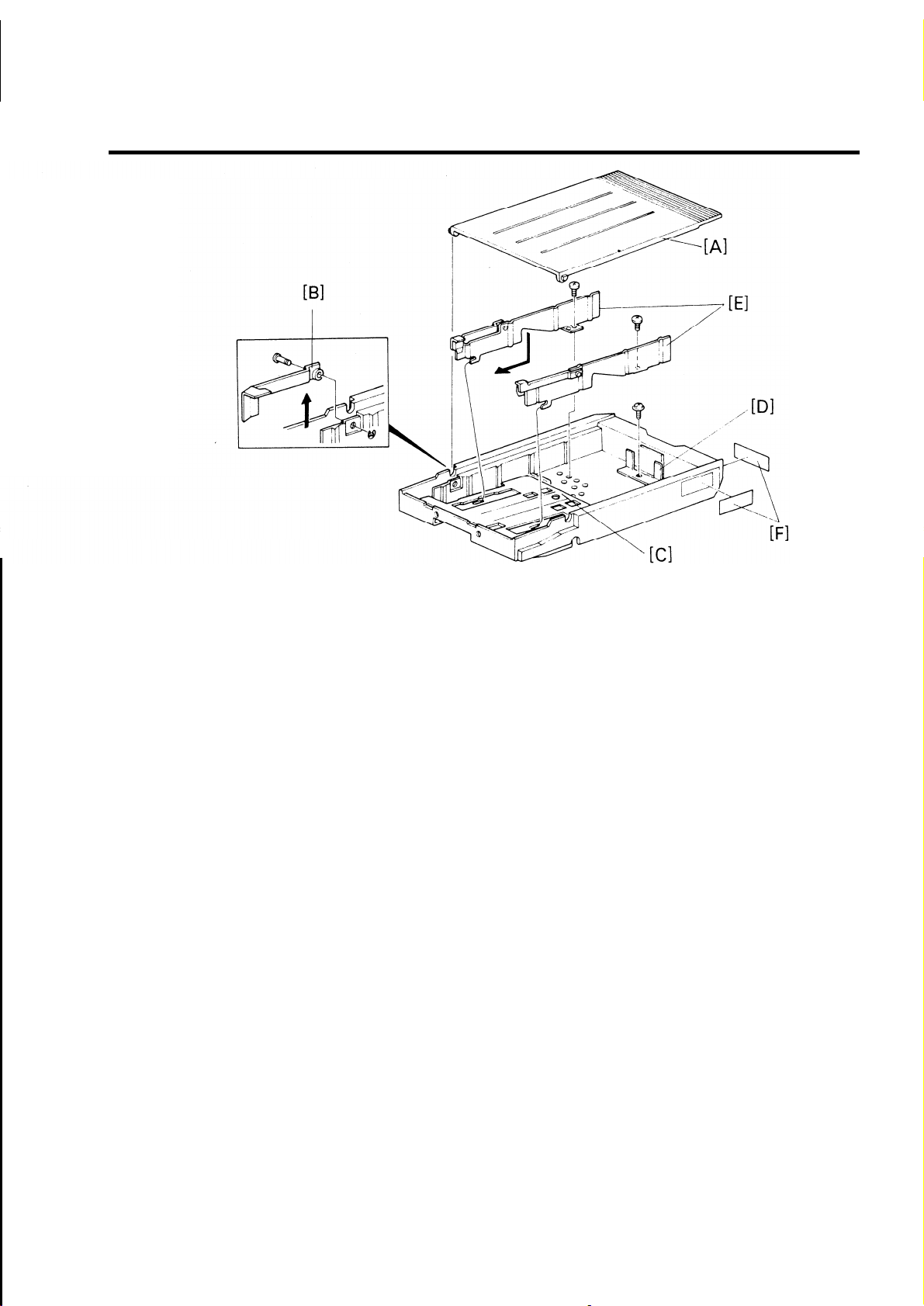
4. CASSETTE MODIFICATION
I
1 Nov. ’87
1
●
Remove the cassette cover [A].
2. Remove the arm pins (1 “E” ring each) and lift out the side fence arms
[B]
..
NOTE: Keep these parts for future use.
3. Remove the bottom plate [C].
4. Fit the rear fence [D] (1 screw), side fences [E] (1 screw each), and re-
install the bottom plate.
NOTE: The paper size positions are shown on the inside of the cassette.
5. Attach the appropriate paper size decals [F] to the cassette as shown.
The part numbers for the above parts are as follows:
ITEM
Rear fence
Right side fence
Left side fence
Screws (3 pcs.)
PART NUMBER
54472941
A0082727
52152716
09644010W
-
1-13
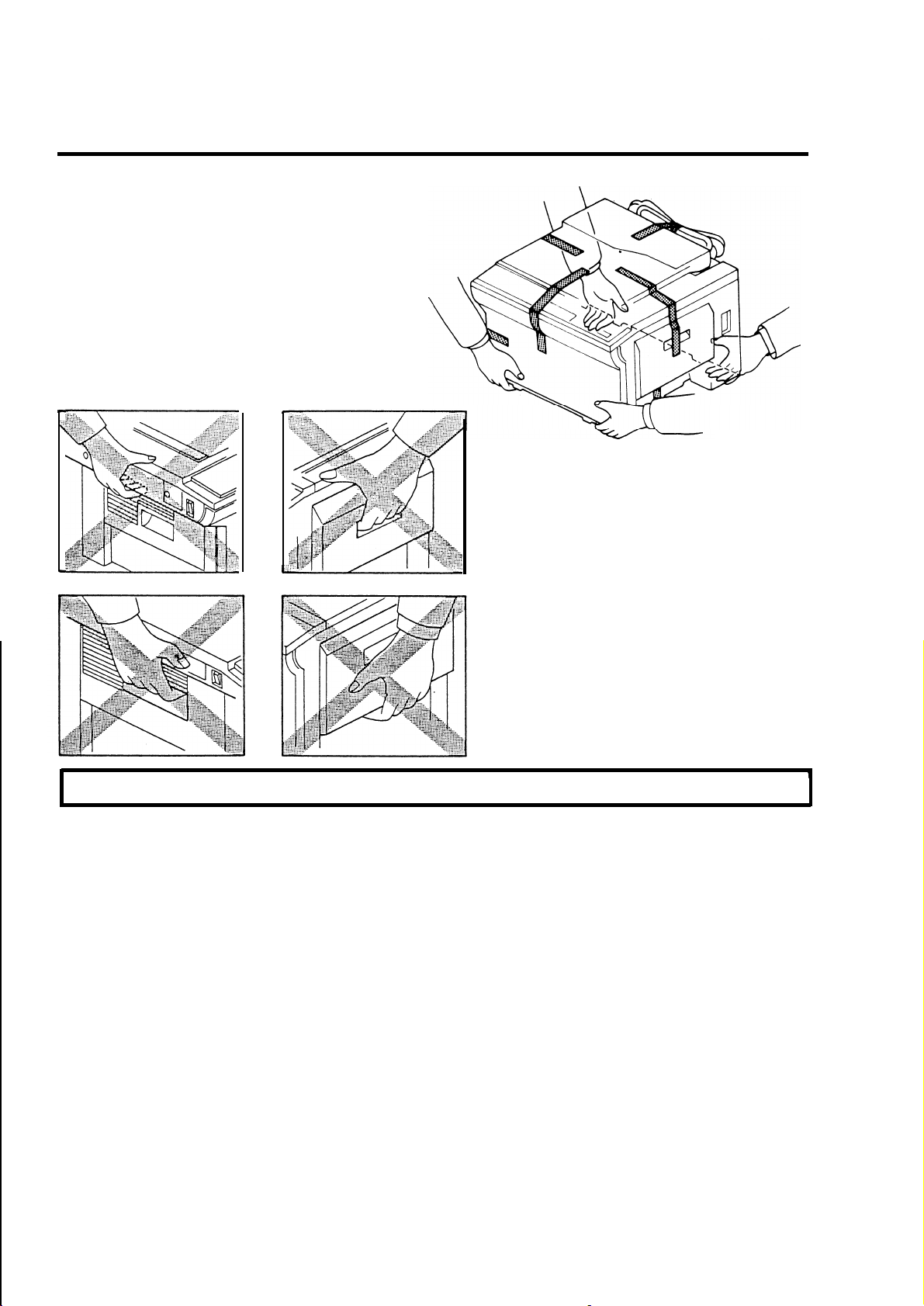
1 Nov. ’87
5. TRANSPORTING THE COPIER
Always hold the copier at the correct places (see illustration).
The copier may be seriously damaged
if it is moved without the following
preparation:
5-1 SHORT HAUL TRANSPORTATION
1.
Remove the copy tray and the cassette.
2. Secure the following items with tape:
manual
a)
platen cover
b)
front cover
c)
d)
exit cover
e)
power supply cord (roll
feed table
up first).
1-14
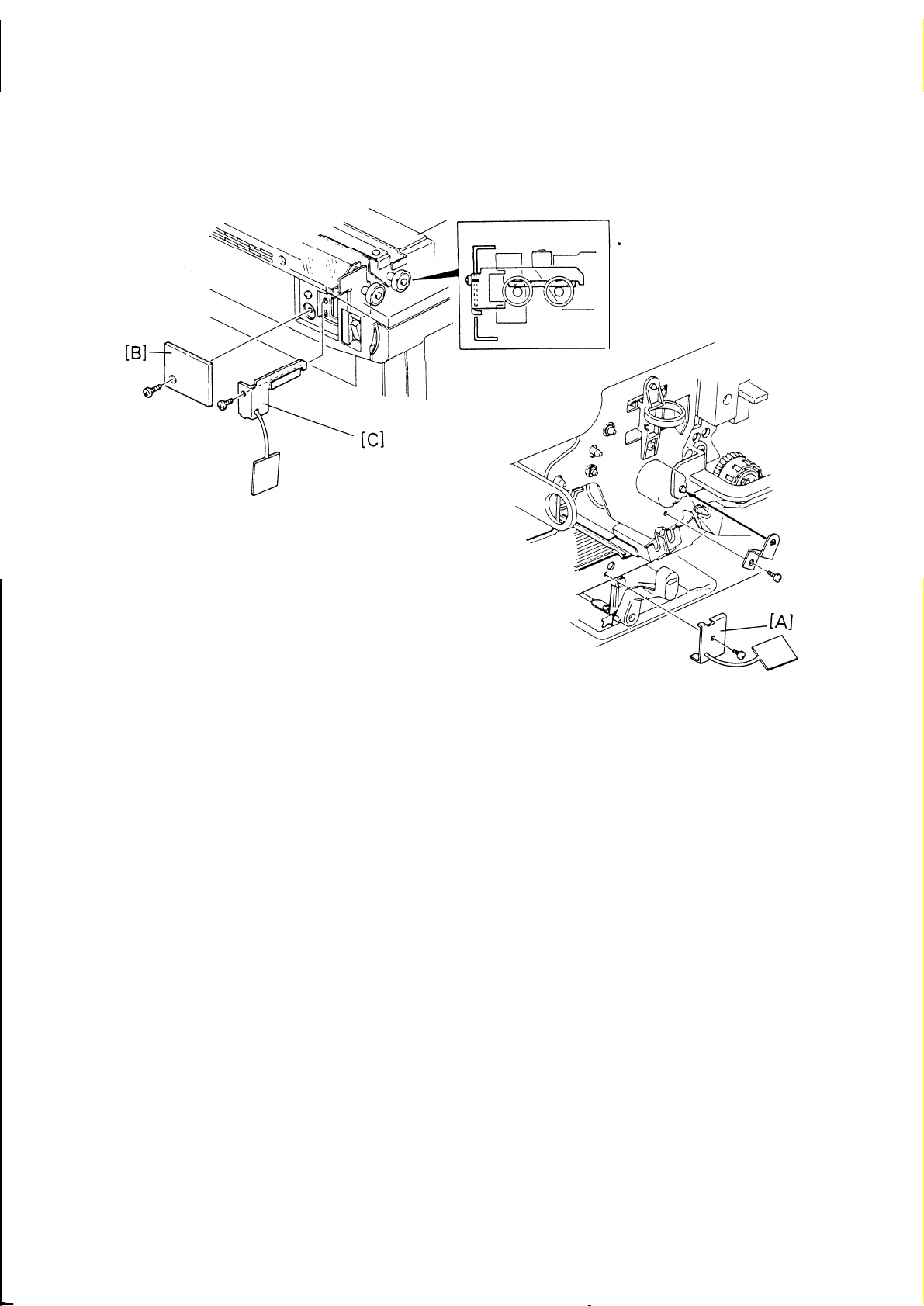
5-2 LONG HAUL TRANSPORTATION BY VEHICLE
9
1 Nov. ’87
1. Remove the developer (see 2-1 Developer Replacement).
2. Install the transport lock plate [A] (1 screw).
3. Temporarily remove the lock plate cover [B] (1 screw) and fit the scanner lock plate [C] (1 screw), and re-install the lock plate cover.
NOTE: The scanner should be in the home
position before this
procedure
is made.
4. Perform procedures 1. and 2. of the Short
Haul Transportation
1-15
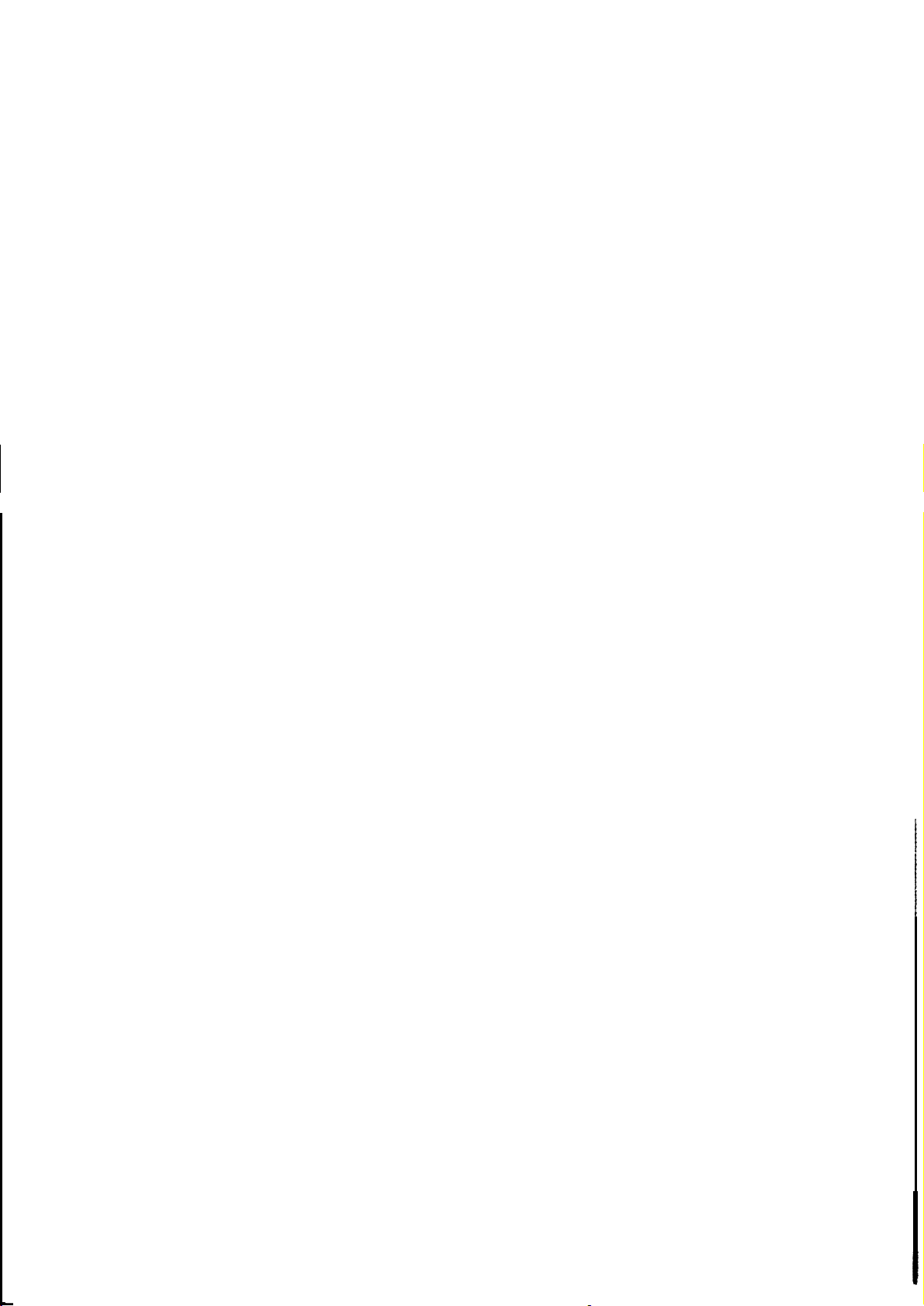
SECTION 2
SERVICE TABLES
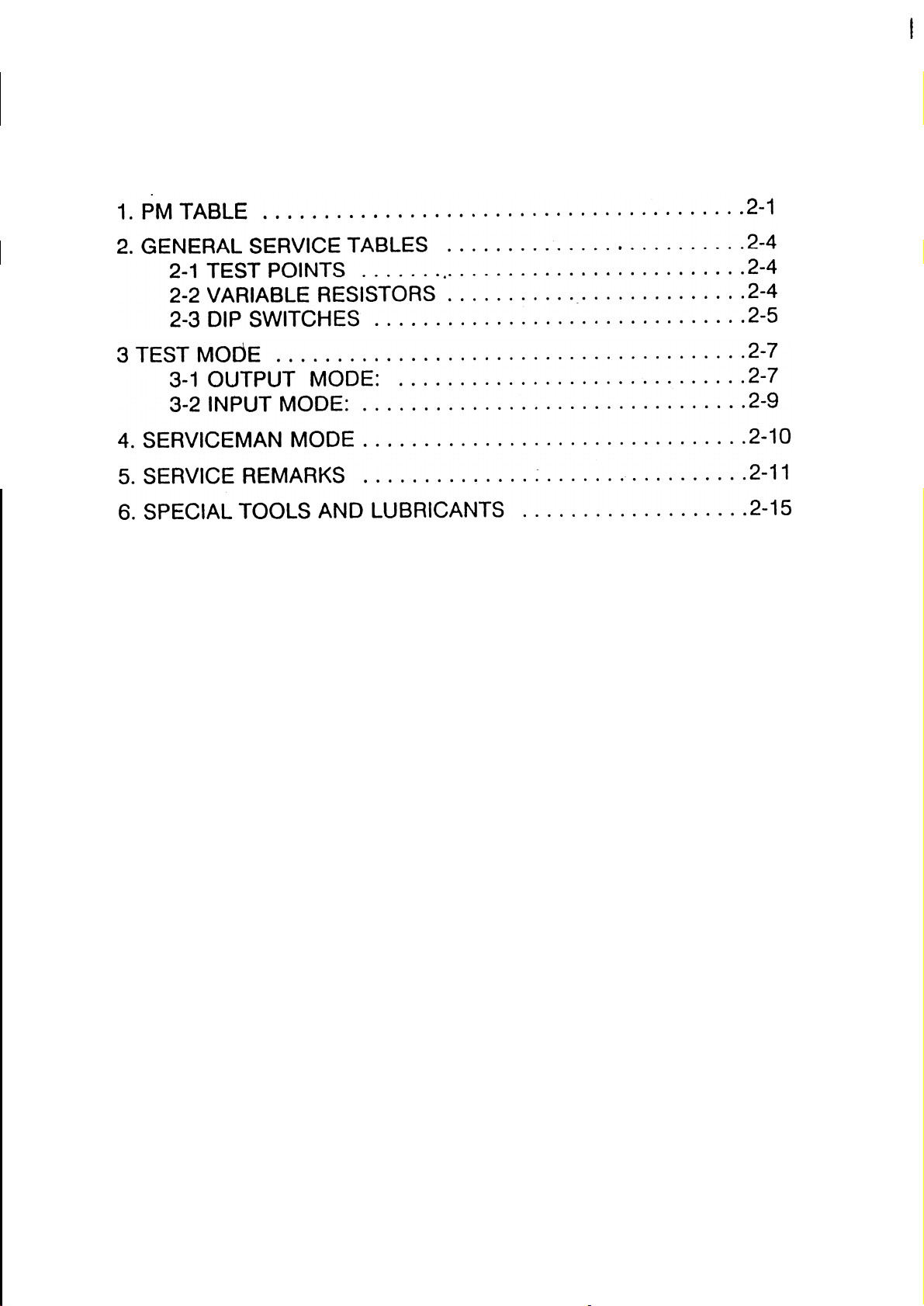
SERVICE
TABLES
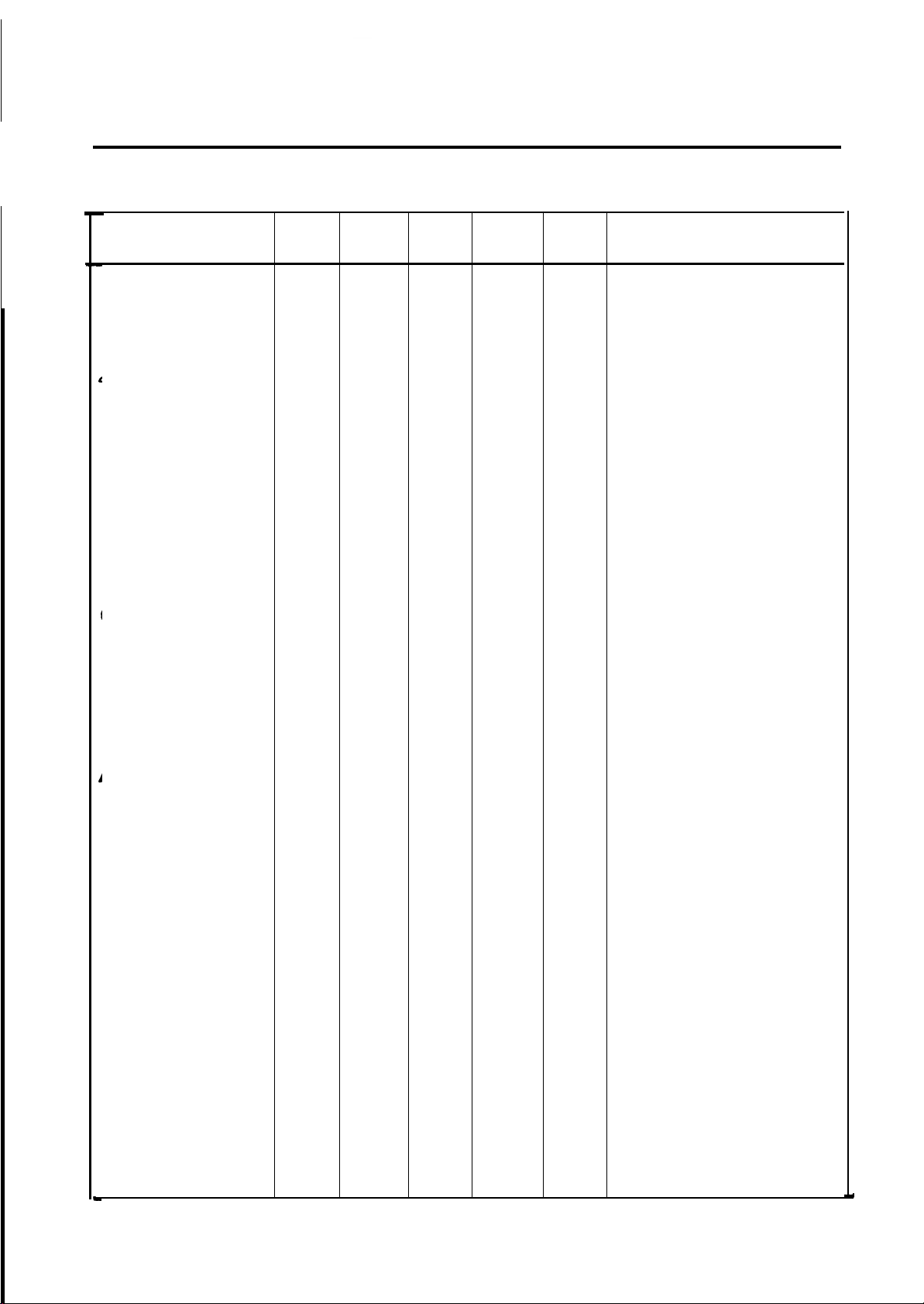
1. PM TABLE
1 Nov. ’87
1: Inspect L: Lubricate
ITEM
OPTICS
1.
Platen cover
sheet
2. Exposure
glass
3.
Lens, mirrors,
reflector,
toner shield
glass
4. Original ID
sensor
5. Exposure lamp
6. Reverse
clutch damper
7 Guide rod and
EM 40K
c c c c c
c
c
c
R: Replace A: Adjust C: Clean
80K 120K
c c
c c
c
c c
160K
c
c
I
I
c
Water (replace if
necessary)
Water or alcohol
Silicone cloth or
blower brush
Blower brush
Replace if necessary
Check for damage.
Replace if necessary
Alcohol
NOTES
guide plate
8. Guide rod felt
AROUND DRUM
1.
Corona wires
2. End blocks
and casings
3. Corona paper
guide
4. Transfer
entrance mylar
5. Quenching
Lamp
6. Pre-Transfer
Lamp
7. ID sensor,
L
I
c c
c
c
c
c
c c
c c c
c c
c c
c c c
c c
I
R
c
I
c
c
c
c
c
c
I
R
c
c
c
c
c
c
Launa oil
Blower brush or dry
cloth
Blower brush or dry
cloth
Blower brush or
cloth (alcohol)
Blower brush or
cloth (alcohol)
Blower brush or dry
cloth
Blower brush or dry
cloth
Blower brush
Drum thermis-
tor
2-1
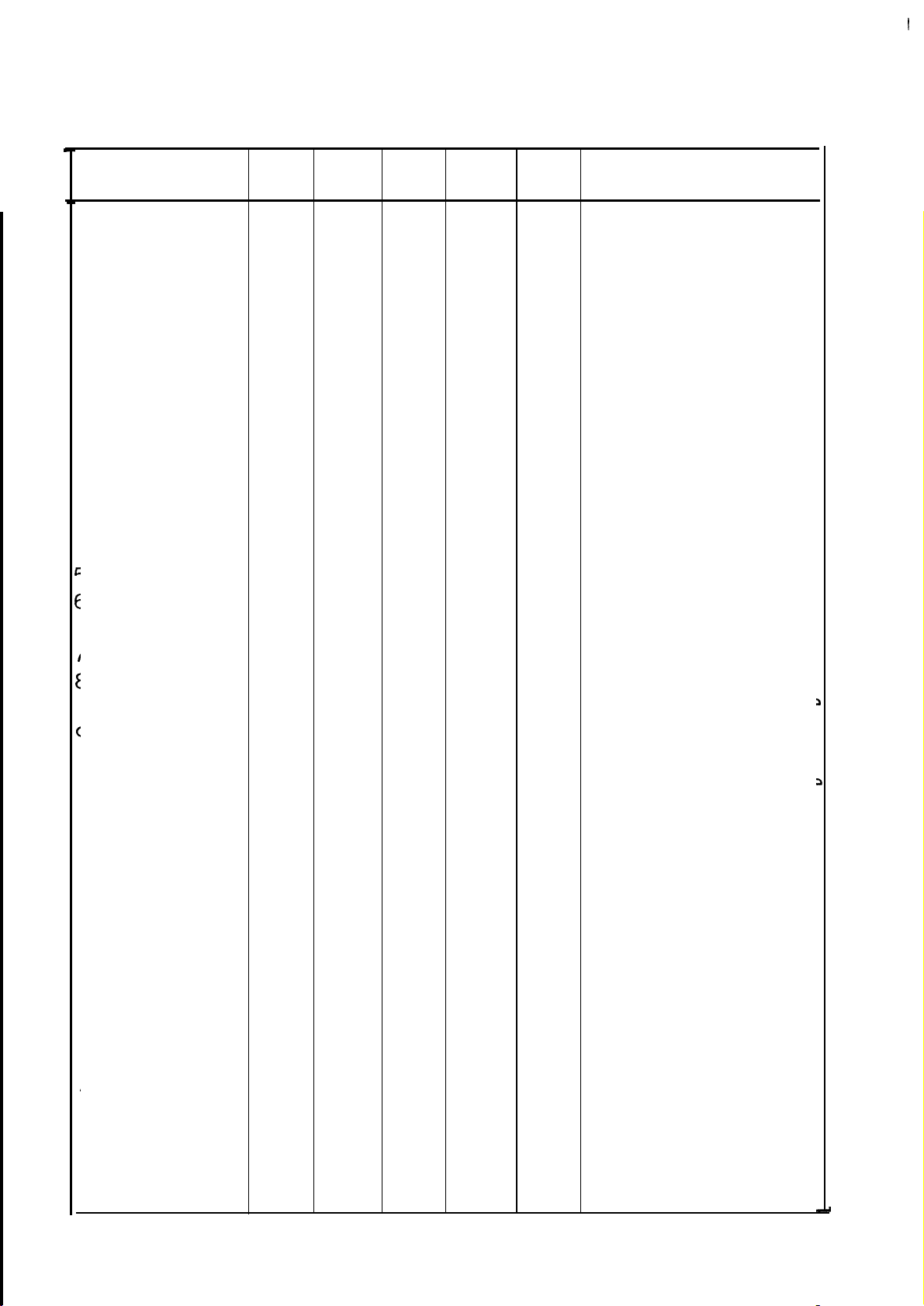
1 Nov. ’87
I
I: Inspect L: Lubricate
ITEM
PAPER FEED
1.
Pickup roller
2. Registration
rollers
3. Cassette Bottom Plate Pad
4. Paper feed
guide plates,
transport
guide plates,
and other
guide plates
5. Transport belt
6. Feed and
reverse rollers
7. Pick-off pawls
8. Torque limiter
EM
c
R: Replace A: Adjust C: Clean
40K
I
80K
I
120K
I I
c
C
c
c
c
c
c
R
c
c
160K
c
c
c
c
R
c
L
L
NOTES
Cloth (water),
replace if necessary
Cloth (water)
Cloth (water)
Cloth (water)
Cloth (water)
Replace if necessary
Mobil Temp 78,
clean before lubricate
9. Exit rollers
10. Paper feed
clutch
‘FUSING UNIT
1.
Hot roller
2. Pressure roller
3. Fusing ther-
mister/ thermoswitch
4. Hot roller
strippers
5. Oil supply pad
6. Fusing
entrance and
exit guides
7. Silicone oil
tank
c
c
c
L
R
C
R
c
I“
I
I
I
I
c
L
R
c
R
R
c
I
Alcohol or water
Mobil Temp 78,
clean before lubricate
Dry cloth
Refill if less than half
full
2“2
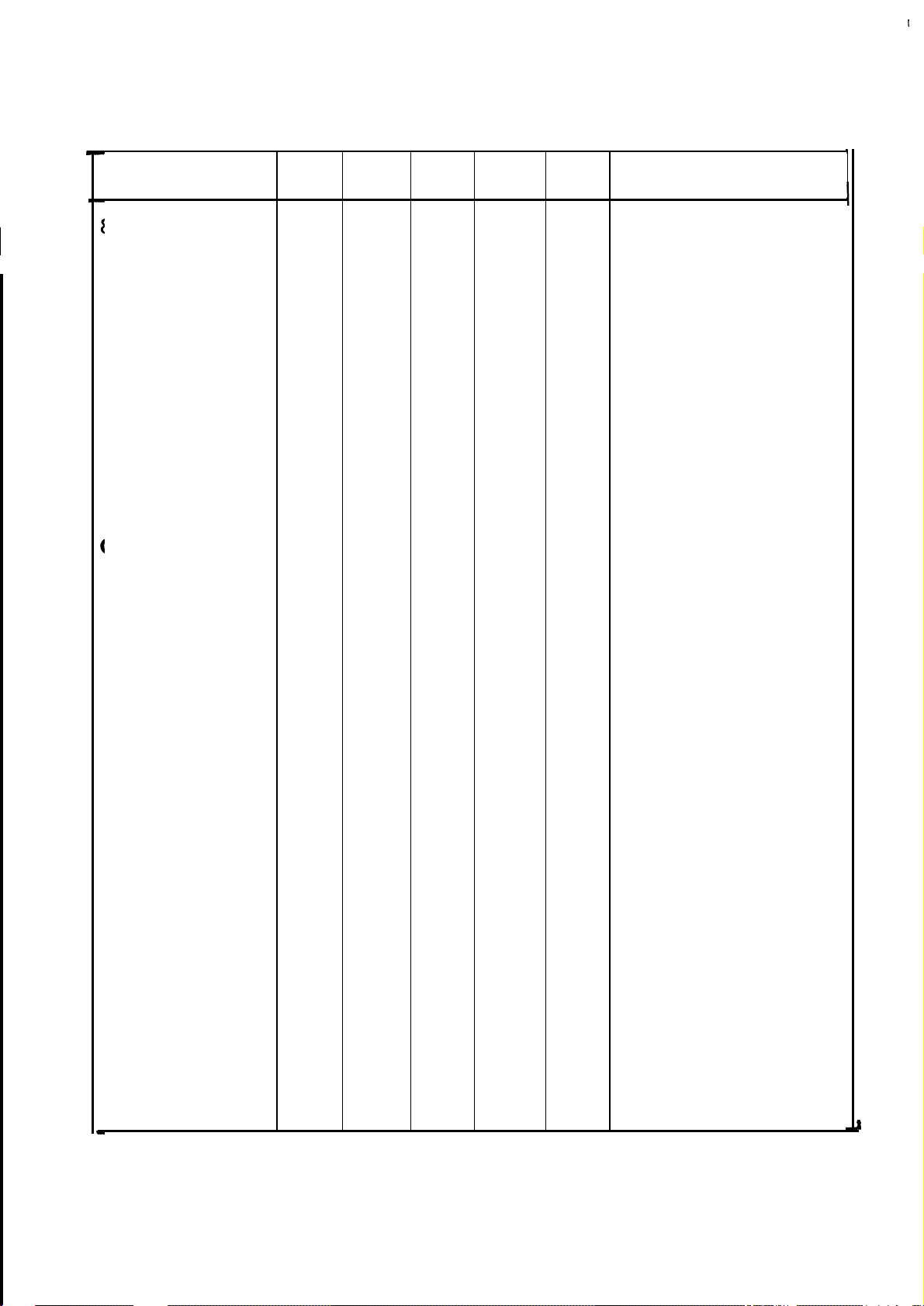
1 Nov. ’87
I
I: Inspect L: Lubricate
ITEM
8.
Oil Blade
DEVELOPMENT
1.
Developer
2. Toner scattering prevention
seal
3. Side seals
4.
Development
unit guide
CLEANING
1.
Cleaning blade
2. Cleaning brush
EM 40K
C
R: Replace A: Adjust C: Clean
80K 120K
I
I I
c
R
I
R
R
I
I
c c
R
R
I I
R R
I
160K
R
R
I
c
R
If necessary
Clean off paper dust
and other dirt
Clean with soft cloth
when replacing
developer
Dust with setting
powder
When replacing,
clean inside the unit
and dust the brush
with setting powder
I
T
NOTES
3. Cleaning seal
4. Cleaning unit
5. Used toner
tank
OTHERS
1.
Exit sensor
2. Rear cover filter
3. Drive belt
4. Bearings
5. Drive gears
6. Antistatic
brush
I
I
c
I
c
I
I
I
c
I I
I
1
I
I
I
I I
I
c c
I
I
I
I
I
I
I
I
Replace if dirty
Replace if toner over”
flow is detected
Check the feeler ac-
tion
Clean or replace if
necessary
Adjust if deformed
2-3
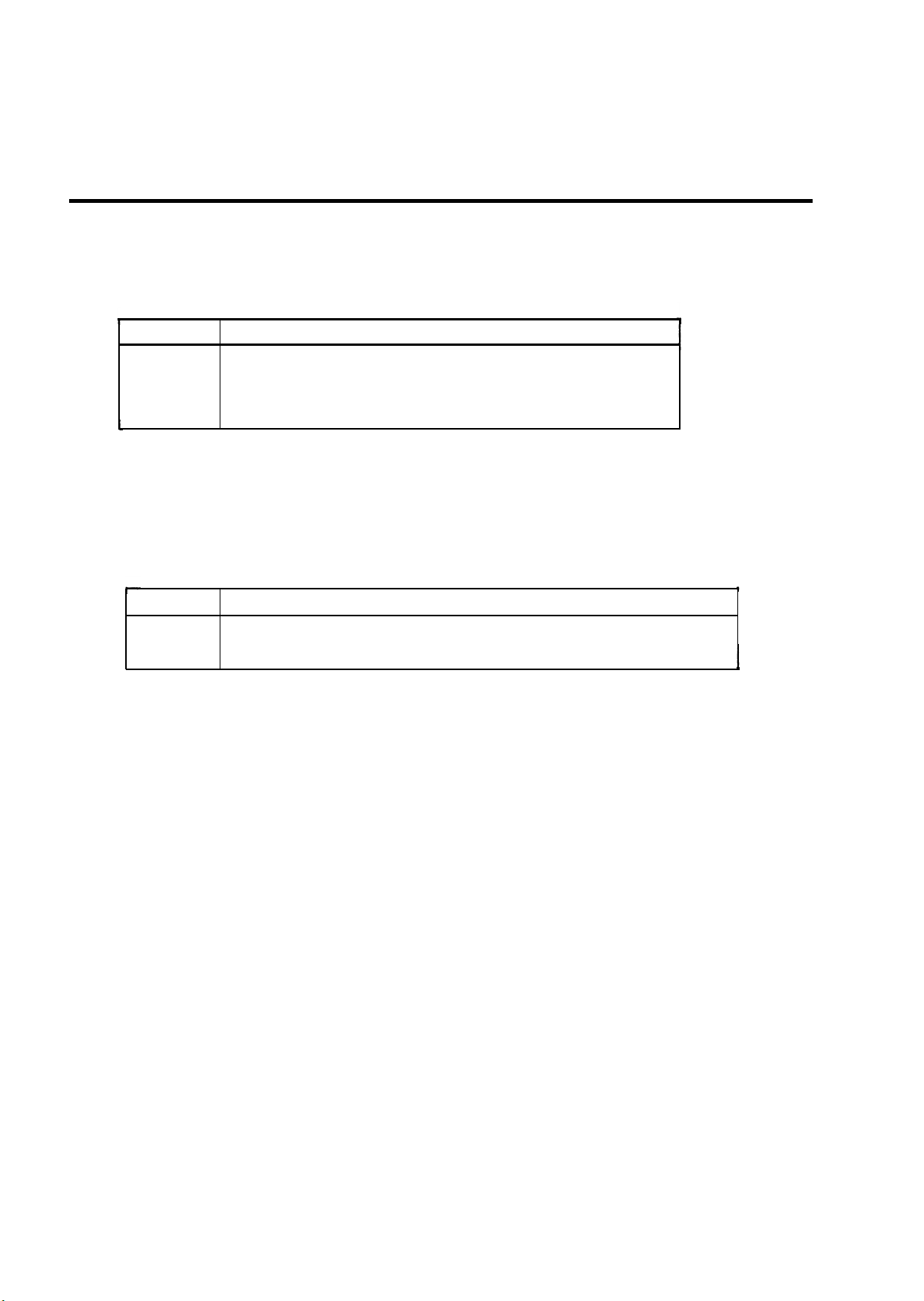
1 Nov. ’87
2. GENERAL SERVICE TABLES
Test Points
2-1
Number
TPI02
TPI03
TPI04
-
22
Variable Resistors
Number Function
VR101
VR102
Function
Original ID sensor voltage
GND
image density sensor voltage
Adjusts the original ID sensor voltage
Adjusts the image density sensor voltage
2-4
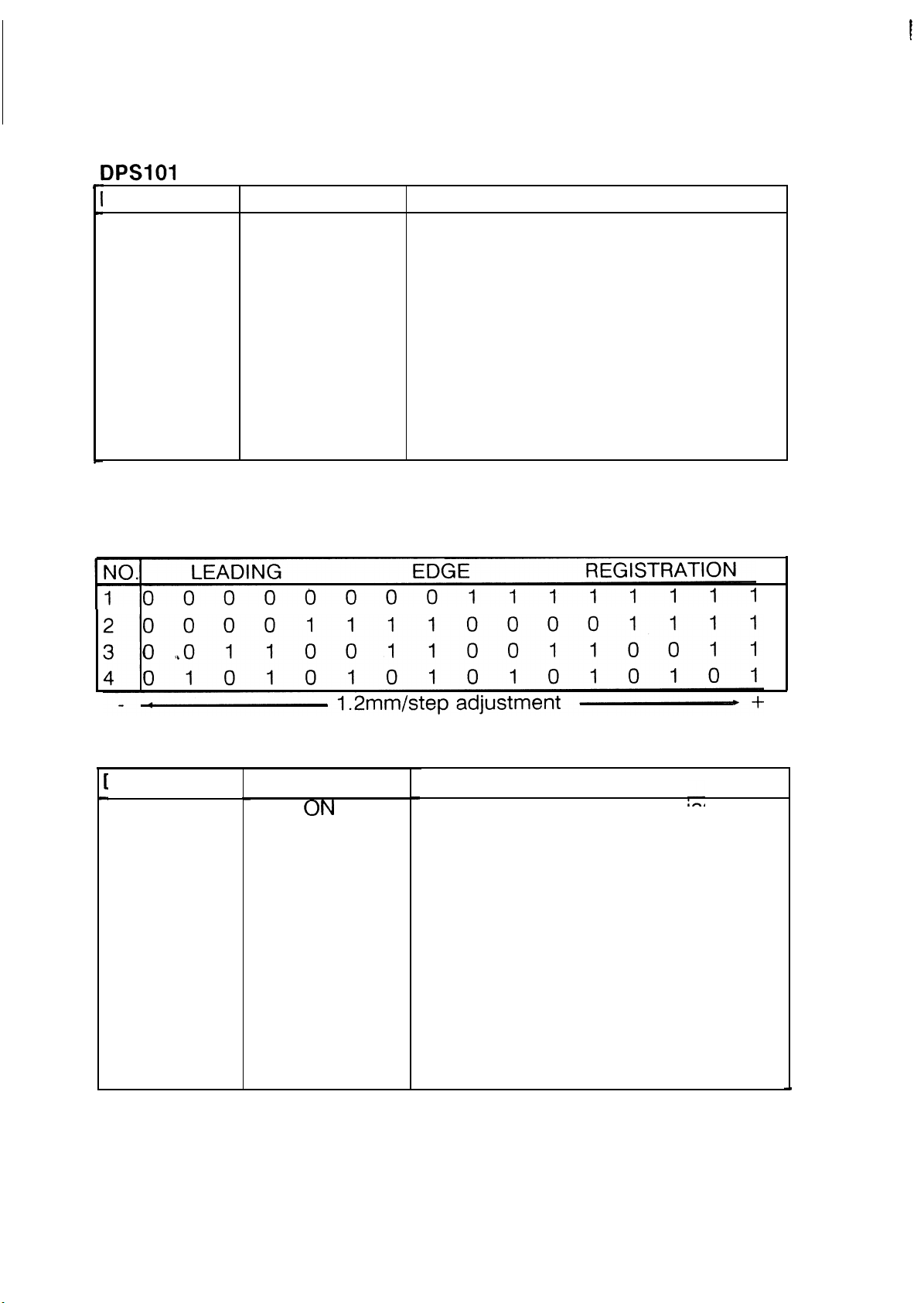
2-3 DIP Switches
I
1 Nov. ’87
DIP Switch
101-1
101-2
101-3
101-4 Lead edge registration adjustment 4
101-5
101-6
Normal
OFF
OFF
Lead edge registration adjustment 1
Lead edge registration adjustment 2
Lead edge registration adjustment 3
Test Mode
Free Run. (When in Free Run Mode,
Function
the paper feed solenoid, total
counter, and paper lift clutch do
not work. )
NOTE: The lead edge registration adjustment interval is 1.2 mm per step,
See the following table:
DPSI02
DIP Switch
102-1
102-2
102-3
102-4
Normal
OFF
OFF
OFF
Function
Selects ID sensor pattern bias level.
(See the following table.)
Selects ID sensor pattern bias level.
(See the following table.)
Selects the fusing temperature level.
(OFF = 185°C, ON = 175°C)
Warm-up idle. If ON the machine
idles for 8 minutes after warm-up.
(During warm-up idle, the cleaning
solenoid is energized and the development bias is fixed at 250 volts.)
2-5
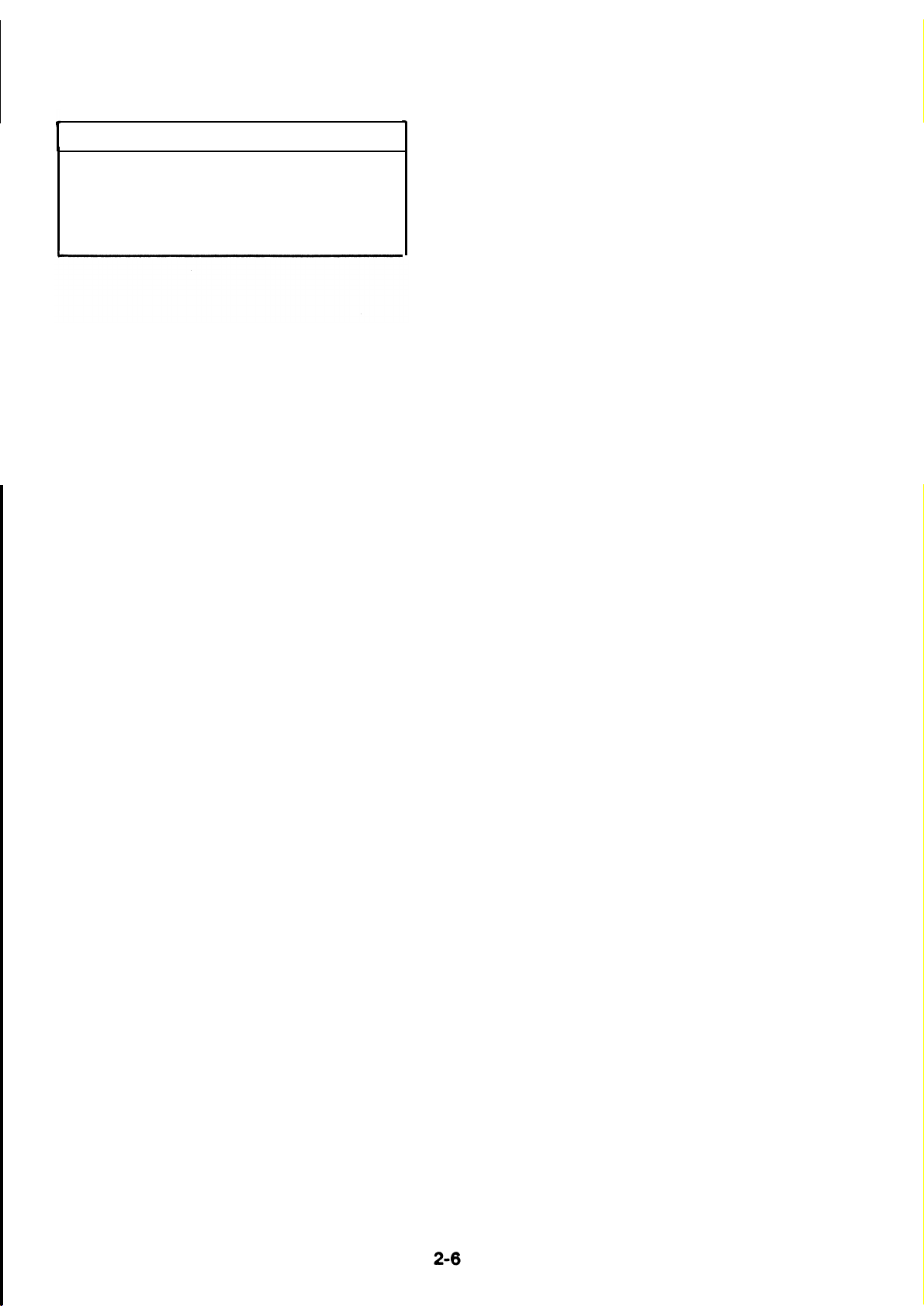
1 Nov. ’87
ID Sensor
DPSI02-I
OFF
ON
OFF
ON
Bias
DPS102-2 ID Bias
OFF
OFF
ON
ON
420 V
470 V
520 V
550 V