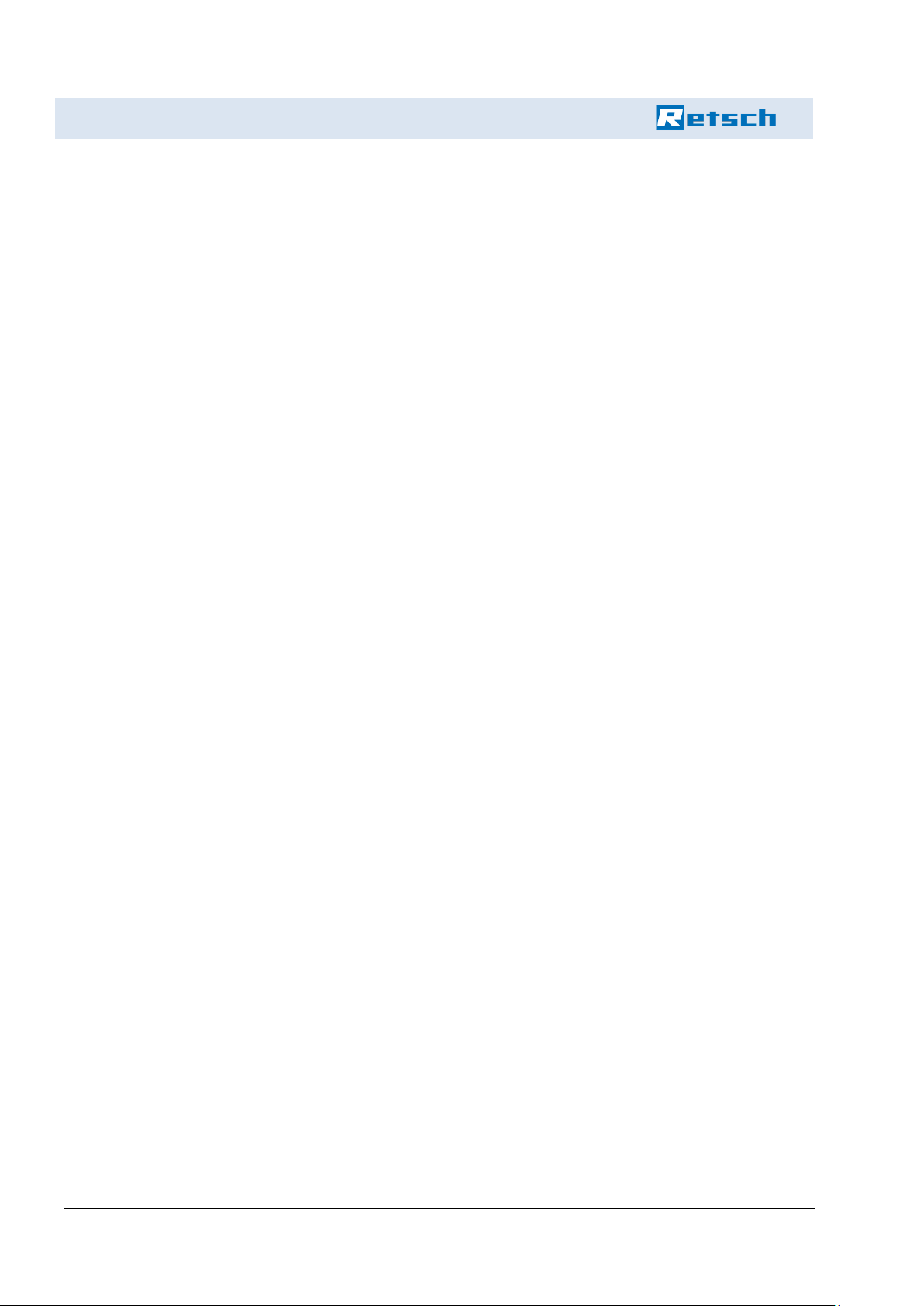
1 Basic construction .................................................................................................................................. 7
2 Safety instructions and use ................................................................................................................... 9
2.1 Requirements for the user ................................................................................................................ 9
2.2 Intended use ................................................................................................................................... 10
2.2.1 Operating principle ..................................................................................................................... 10
2.3 Duties of the operating company.................................................................................................... 10
2.4 Hazard warnings and symbols used .............................................................................................. 11
2.5 Device safety instructions ............................................................................................................... 15
2.6 Safety equipment ........................................................................................................................... 17
2.7 Danger areas .................................................................................................................................. 18
2.8 Electrical safety .............................................................................................................................. 18
2.8.1 General information.................................................................................................................... 18
2.8.2 Protection against restarting ...................................................................................................... 19
3 Technical data ....................................................................................................................................... 21
3.1 Dimensions ..................................................................................................................................... 21
3.2 Weight ............................................................................................................................................ 21
3.3 Operating noise .............................................................................................................................. 21
3.4 Voltage, power consumption, power input ..................................................................................... 21
3.5 Fuse ................................................................................................................................................ 21
3.6 Material ........................................................................................................................................... 22
3.7 Final fineness ................................................................................................................................. 22
4 Installation ............................................................................................................................................. 23
4.1 Transport ........................................................................................................................................ 23
4.2 Unpacking ....................................................................................................................................... 23
4.3 Positioning ...................................................................................................................................... 24
4.4 Ambient conditions ......................................................................................................................... 25
4.5 Electrical connection ...................................................................................................................... 26
4.5.1 Adjusting the disc mill to the mains network .............................................................................. 26
4.6 Putting into service ......................................................................................................................... 26
4.7 Switching on for the first time / function test ................................................................................... 27
4.7.1 Switching on ............................................................................................................................... 27
4.7.2 Switching off ............................................................................................................................... 27
5 Working with the disc mill .................................................................................................................... 29
5.1 Display and control panel ............................................................................................................... 30
5.2 Menu navigation ............................................................................................................................. 30
5.3 Specifying the zero point ................................................................................................................ 31
5.4 Adjusting the gap width .................................................................................................................. 32
5.5 Reverse operation .......................................................................................................................... 33
5.6 Adjusting the grinding time ............................................................................................................. 34
5.7 Changing the language .................................................................................................................. 35
5.8 Grinding with zirconium oxide grinding discs ................................................................................. 35
5.9 Material feed ................................................................................................................................... 36
5.10 Sample removal.............................................................................................................................. 38
5.11 Final fineness ................................................................................................................................. 38
6 Cleaning ................................................................................................................................................. 39
6.1 Extracting dust after grinding .......................................................................................................... 39
6.2 Grinding chamber ........................................................................................................................... 39
6.3 Housing .......................................................................................................................................... 40
6.4 Cleaning the hopper ....................................................................................................................... 40
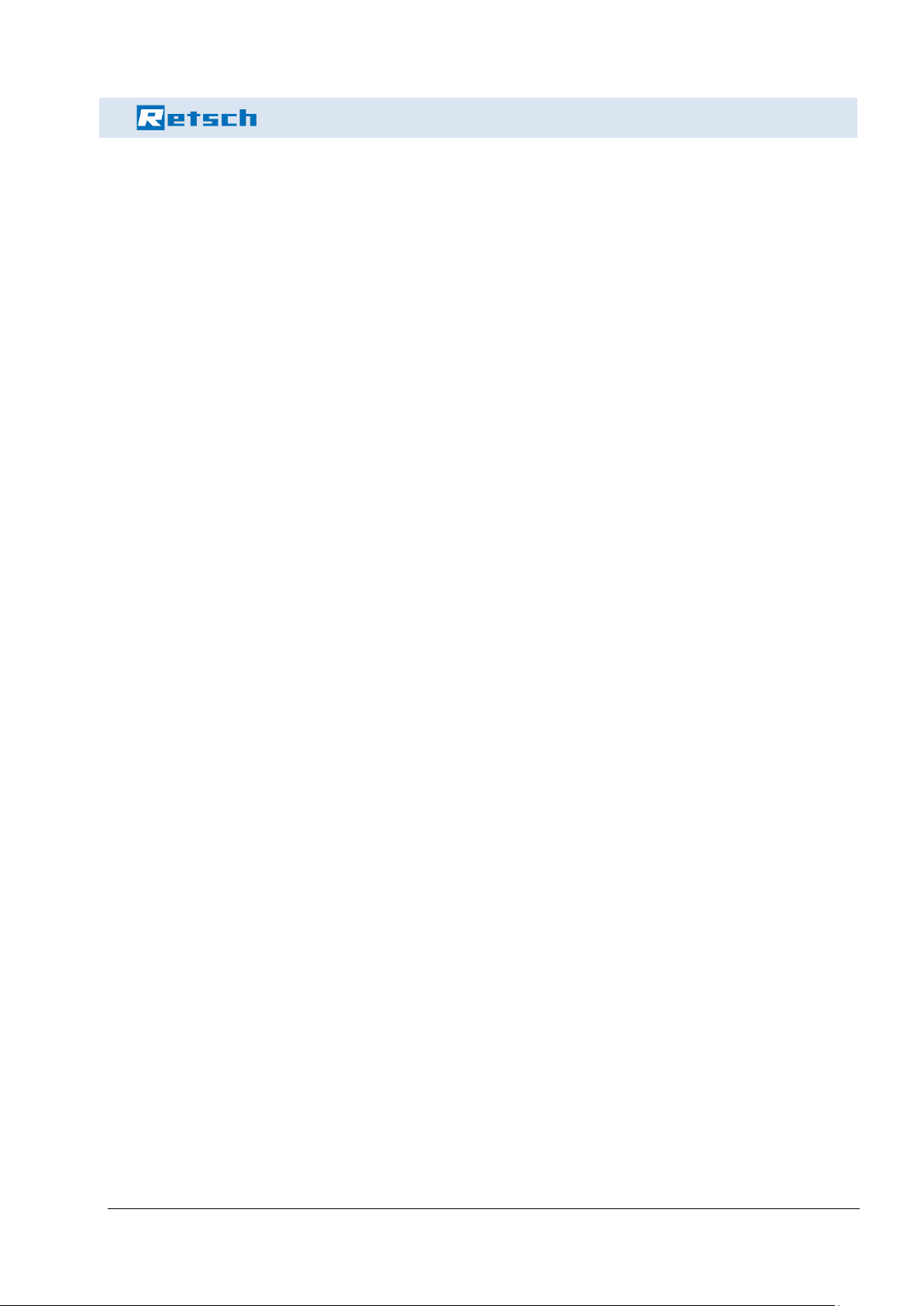
7 Servicing ................................................................................................................................................. 41
7.1 Grinding discs ................................................................................................................................. 42
7.2 Replacing the grinding discs (5 + 6)................................................................................................ 42
7.3 Replacing the gear oil ..................................................................................................................... 49
7.3.1 Conducting the gear oil change .................................................................................................. 49
8 Repair ...................................................................................................................................................... 51
8.1 Checklist for troubleshooting ........................................................................................................... 52
9 Disposal .................................................................................................................................................. 54
10 EC Declaration of Conformity ............................................................................................................... 55
11 Index ........................................................................................................................................................ 57
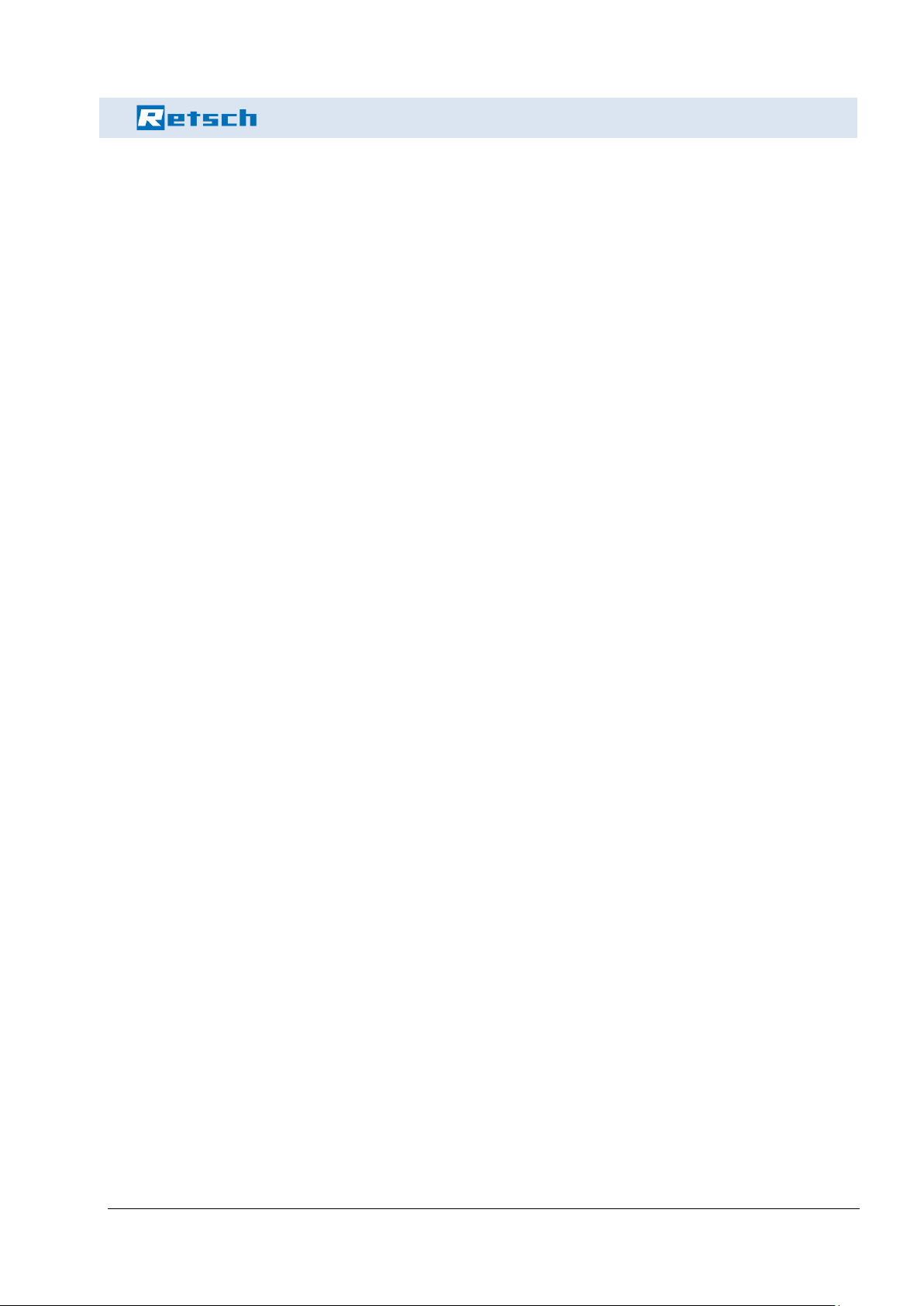
Safety instructions and use
This Operating Manual is intended for persons commissioned with
the operation and monitoring of the DM400. The Operating Manual,
and in particular the safety instructions, should be heeded by all persons working on or with the equipment. Furthermore the regulations
and provisions on accident prevention applicable at the application
site must be observed. The Operating Manual must always be kept
where the DM400 is used.
Persons with health disorders or who are under the influence of medication, drugs, alcohol or extreme tiredness must not operate the device.
The DM400 may only be operated by authorised persons and serviced and repaired by trained specialists. Technically qualified personnel must conduct all maintenance, servicing and repair work!
Qualified personnel are people who have been authorised by persons
responsible for the safety of the system to execute the required activities and are able to recognise potential dangers and avoid them
based on their training, experience and instruction, as well as their
knowledge of relevant standards, regulations, accident prevention
regulations and operating conditions (definition of skilled personnel
according to IEC 364).
The instructions in this Manual should be followed in order to prevent
danger to the user.
Faults which can impair the safety of persons, the DM400 or other
material assets should be rectified immediately. The following instructions serve both personal safety of operating staff and the safety of
the described products as well as connected equipment: all servicing
and repair work may only be carried out by technically qualified personnel!
This Operating Manual is not a full technical description. It only describes information required for safe operation and maintenance of
serviceability.
Retsch has prepared and checked this Operating Manual very carefully. However no liability can be assumed regarding completeness and
accuracy.
Subject to technical amendments.
2 Safety instructions and use
2.1 Requirements for the user
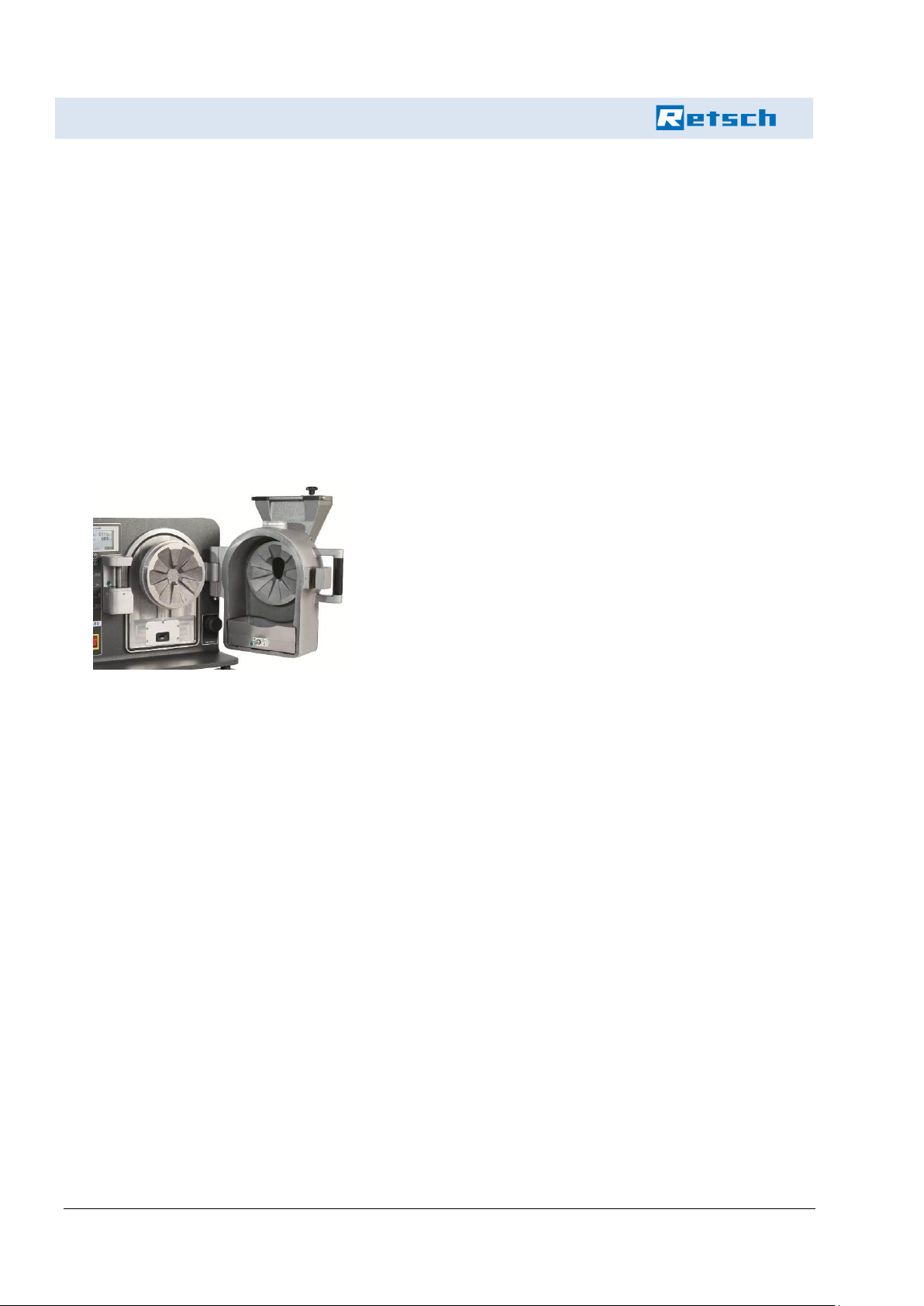
Safety instructions and use
2.2 Intended use
The DM400 is a disc mill for batch or continuous fine grinding of hard
brittle to medium hard solids from the areas of mining and metallurgy,
geology and mineralogy and the glass and ceramics industry.
The maximum feed size is 20 mm edge length; the achievable final
fineness level depending on the gap width set is approx. 12 mm (largest gap width) and 0.05 mm (smallest gap width).
The material throughput of the disc mill lies in the range of 20 to 150
kg/h. This depends on the setting of the outlet gap and the bulk
weight and grinding conduct of the sample.
The grinding of the material sample takes place in a grinding
chamber which is dustproof to the outside and in which two
coarsely toothed grinding discs operate against each other.
The moving grinding disc is driven by a powerful, slow running
gear motor.
The sample material is filled through a lockable hopper into the
centre of the upright grinding disc and, after being ground by
compression and shear stress, escapes through the gap between the two discs. The gap width determines the mean particle size of the sample material. The grinding gap can be set to
an accuracy of 0.05 mm using the plus/minus buttons on the
control panel. The gap width can be read off the display (1).
When grinding batches, the sample material is collected in a
sample material container placed in the device (volume: 2l).
The closed design prevents dust escaping. A dust extraction
device may additionally be connected. To clean, the front housing is opened sideways - the grinding chamber is then freely
accessible.
This Manual should be read and understood before using the DM400.
Use of the DM400 demands expert knowledge and should be limited
to commercial users.
Operating personnel must be familiar with the contents of the Operating Manual. It is therefore very important for this Operating Manual to
be actually handed to these persons. It must be ensured that the
Operating Manual always remains with the device.
The DM400 may be used exclusively within the possible uses set out
in this Manual and within the specified regulations in this Manual. In
the event of contravention or incorrect use, the customer assumes full
2.2.1 Operating principle
2.3 Duties of the operating company
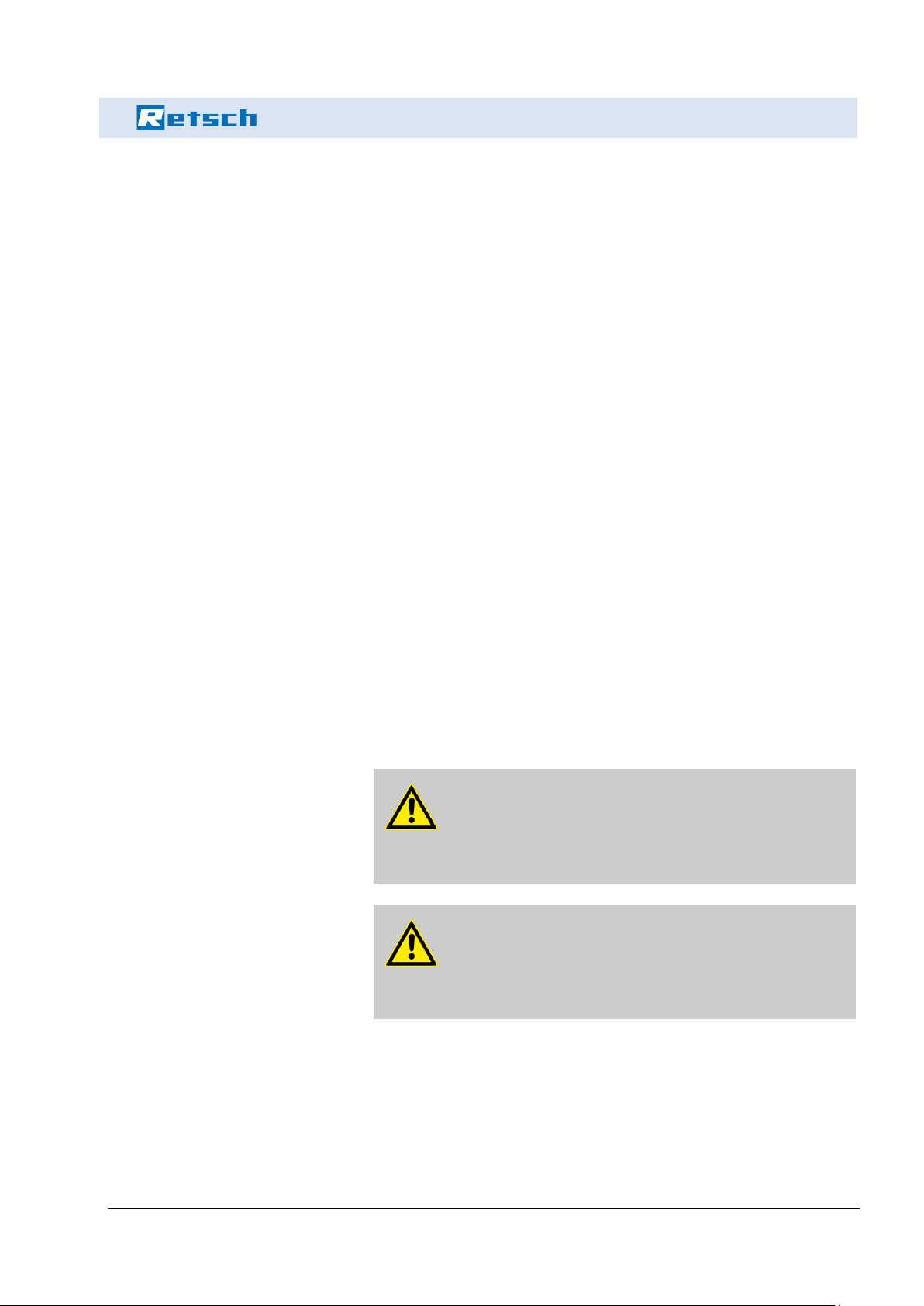
Safety instructions and use
liability for the functionality of the DM400 or for damage arising from
an infringement of this duty.
Through use of the DM400 the customer agrees and recognises that
defects, faults or errors cannot be entirely ruled out. In order to avoid
the risk of personal injury or damage to property arising from this or
otherwise or of other indirect or direct damage, customers must take
adequate and comprehensive safety measures when working with the
device.
It is not possible for Retsch GmbH to monitor compliance with this
Manual or the conditions and methods used in the installation, operation, use and servicing of the DM400. Damage to property leading to
danger to persons may result from incorrect installation. We therefore
assume no responsibility and liability at all for loss, damage or costs
arising from or in any way associated with faulty installation, incorrect
operation or from incorrect use and servicing.
The applicable accident prevention regulations must be complied with.
Generally accepted statutory and other binding regulations on envi-
ronmental protection must be observed.
Safety instructions are indicated in this Manual by symbols. The safety instructions are introduced by signal words which express the degree of danger.
DANGER!
This combination of symbol and signal word indicates a
direct hazardous situation leading to death or serious
injuries if it is not avoided.
WARNING!
This combination of symbol and signal word indicates a
potentially hazardous situation which can lead to death
or serious injuries if it is not avoided.
2.4 Hazard warnings and symbols used
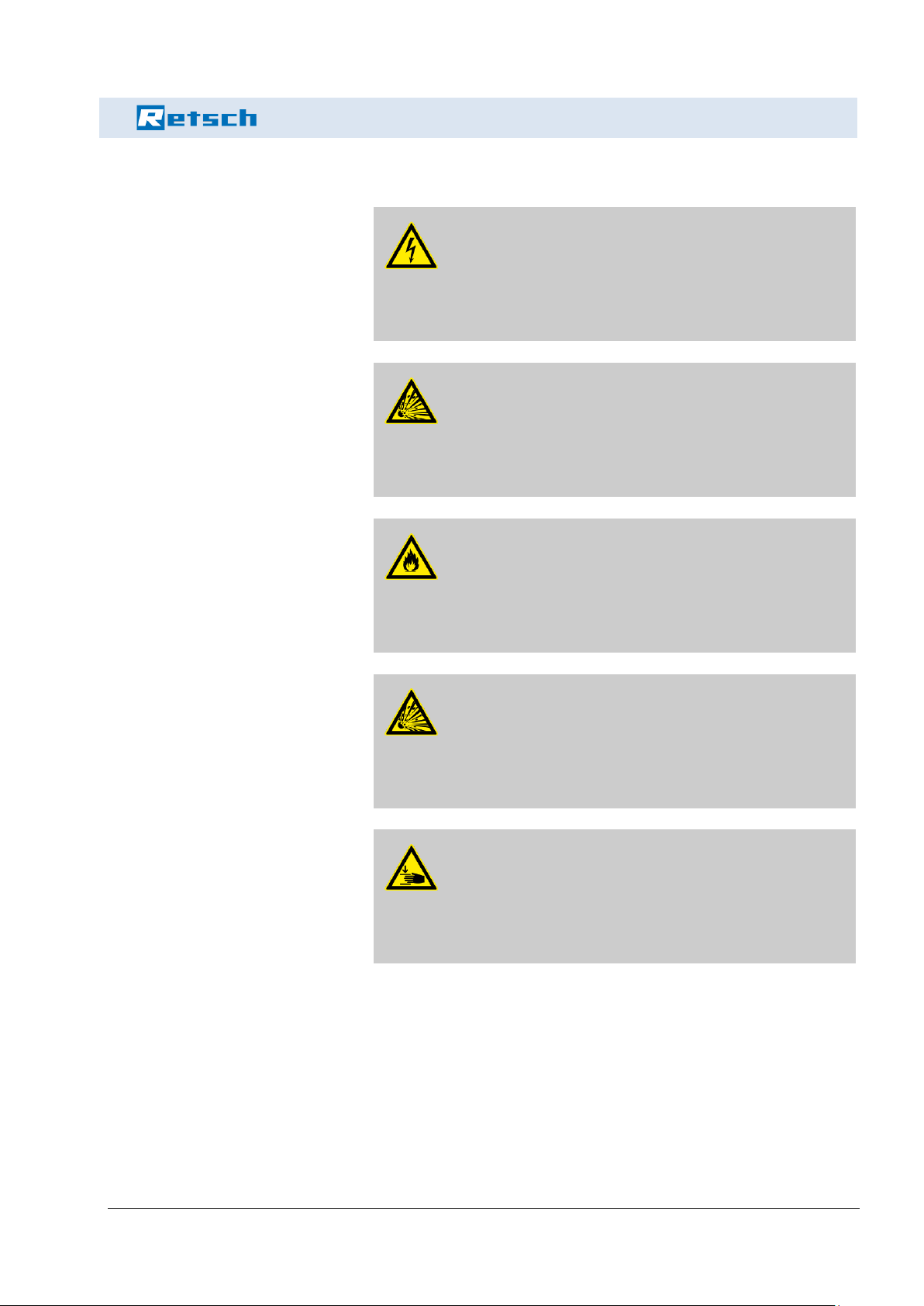
Safety instructions and use
Special safety instructions
The following symbols are used in safety instructions to alert to specific hazards:
DANGER!
This combination of symbol and signal word indicates a
direct hazardous situation through electric current. If a
sign with this symbol is not heeded, serious or fatal
injuries will result.
DANGER!
This combination of symbol and signal word designates
content and instructions for intended use of the machine
in potentially explosive areas. If a sign with this symbol
is not heeded, serious or fatal injuries will result.
DANGER!
This combination of symbol and signal word designates
content and instructions for intended use of the machine
with flammable materials. If a sign with this symbol is
not heeded, serious or fatal injuries will result.
DANGER!
This combination of symbol and signal word designates
content and instructions for intended use of the machine
with potentially explosive substances. If a sign with this
symbol is not heeded, serious or fatal injuries will result.
WARNING!
This combination of symbol and signal word indicates a
direct hazardous situation due to moving parts. If a sign
with this symbol is not heeded, injuries to hands may
result.
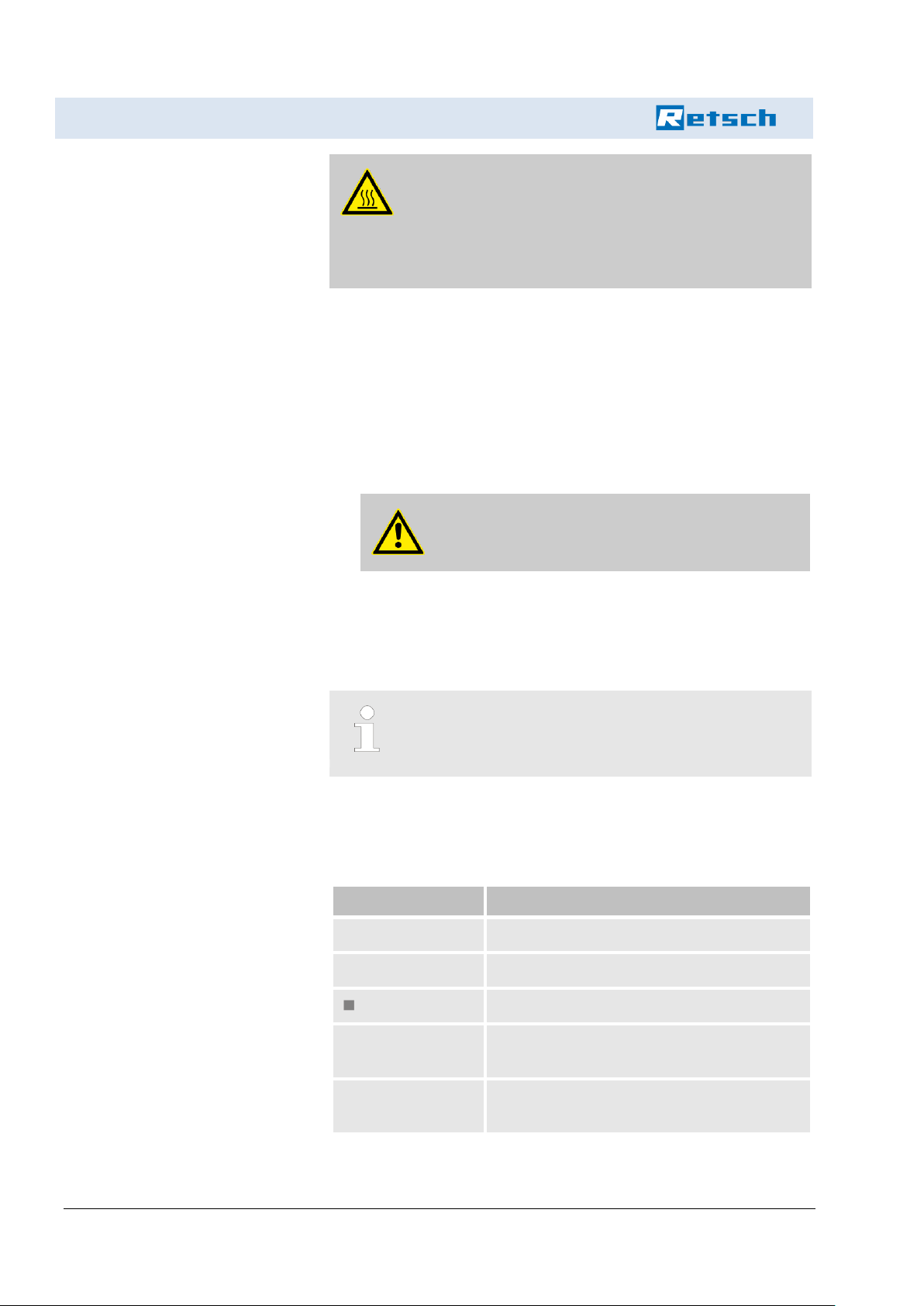
Safety instructions and use
WARNING!
This combination of symbol and signal word indicates a
direct hazardous situation due to hot surfaces. If a sign
with this symbol is not heeded, skin contact with hot
surfaces may cause serious burns to skin.
Safety instructions in
operating instructions
Safety instructions may refer to a specific, individual operating instruction. Such safety instructions are embedded in this operating instruction in order not to interrupt the flow of reading when performing the
action concerned. The signal words described above are used.
Example:
CAUTION!
Risk of pinching on the lid.
This symbol highlights useful tips and recommendations
as well as information for efficient and fault-free
operation.
The following labels are used to emphasise operating instructions,
results, lists, references and other elements in this Manual:
Step-by-step operating instructions
Results of operating steps
Lists without specified order
Control elements (e.g. button, switch), indicators (e.g. signalling lamps)
Screen elements (e.g. buttons, assignment
of function buttons)
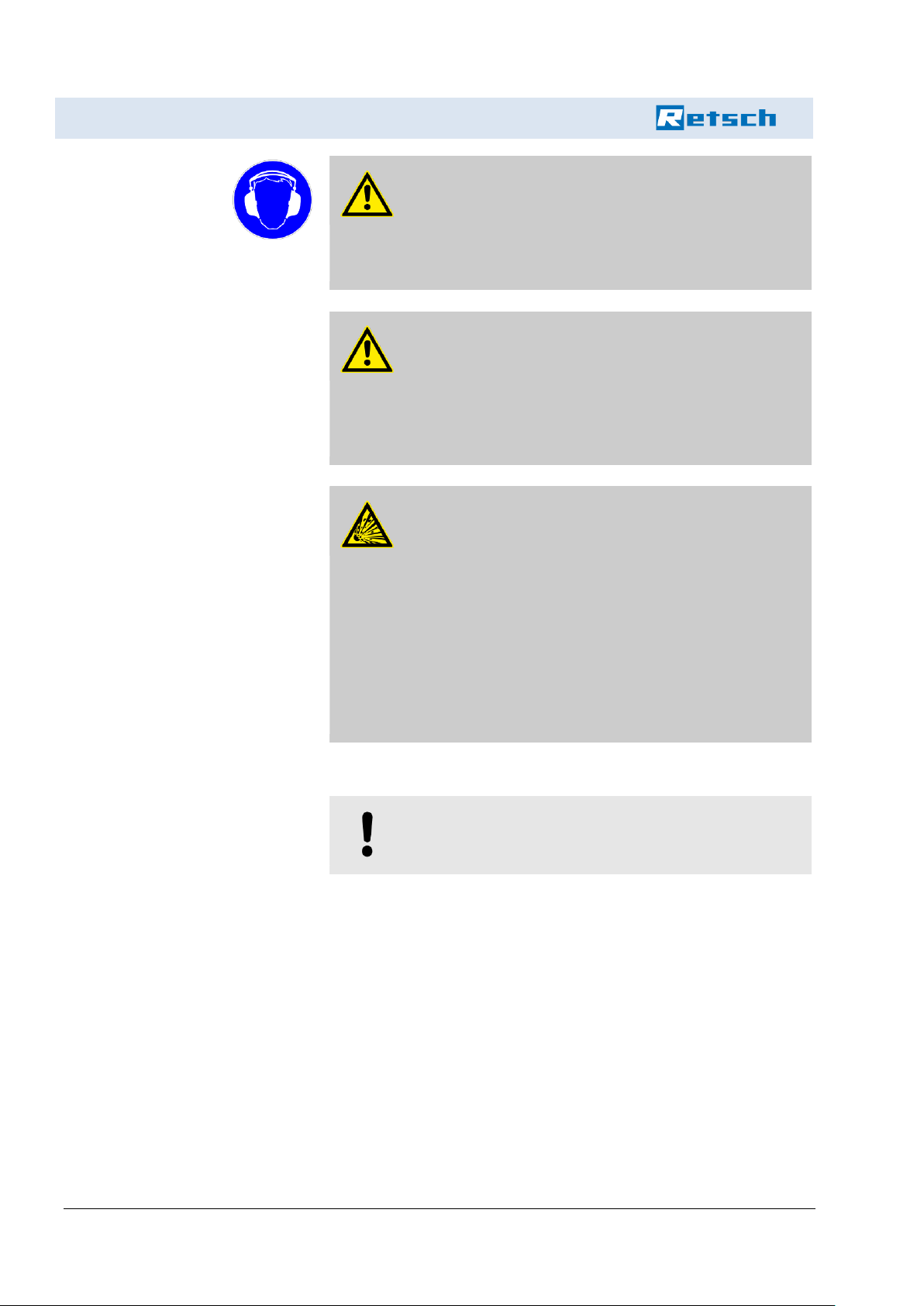
Safety instructions and use
CAUTION!
Wear hearing protection!
Hearing protection should be worn when a noise level of
85dB (A) is reached or exceeded in order to prevent
damage to hearing.
WARNING!
The maximum workplace concentrations (threshold limit
values - TLV) in valid safety regulations must be
observed, and ventilation must be provided where
necessary or the machine operated under an extractor
hood.
DANGER!
Risk of explosion!
- When grinding oxidable substances (e.g. metals or
coal) there is a risk of spontaneous ignition (dust
explosion) if the fine fraction exceeds a certain
percentage. For this reason special safety measures
must be taken when grinding such substances and
the work must be supervised by a specialist.
- The device is not designed for use in potentially
explosive areas and is not suitable for grinding
explosive materials.
NOTICE!
Replace damaged or illegible signs without delay.
Unauthorised modifications to the device lead to loss of the
conformity to European directives declared by Retsch and to loss
of the warranty claim.
Only use the DM400 in a technically perfect state and as intended,
with an awareness of safety and dangers as specified in the
Operating Manual. In particular have faults which might impair
safety rectified immediately!
If you have any questions or problems after reading the Operating
Manual, please contact our technical staff.
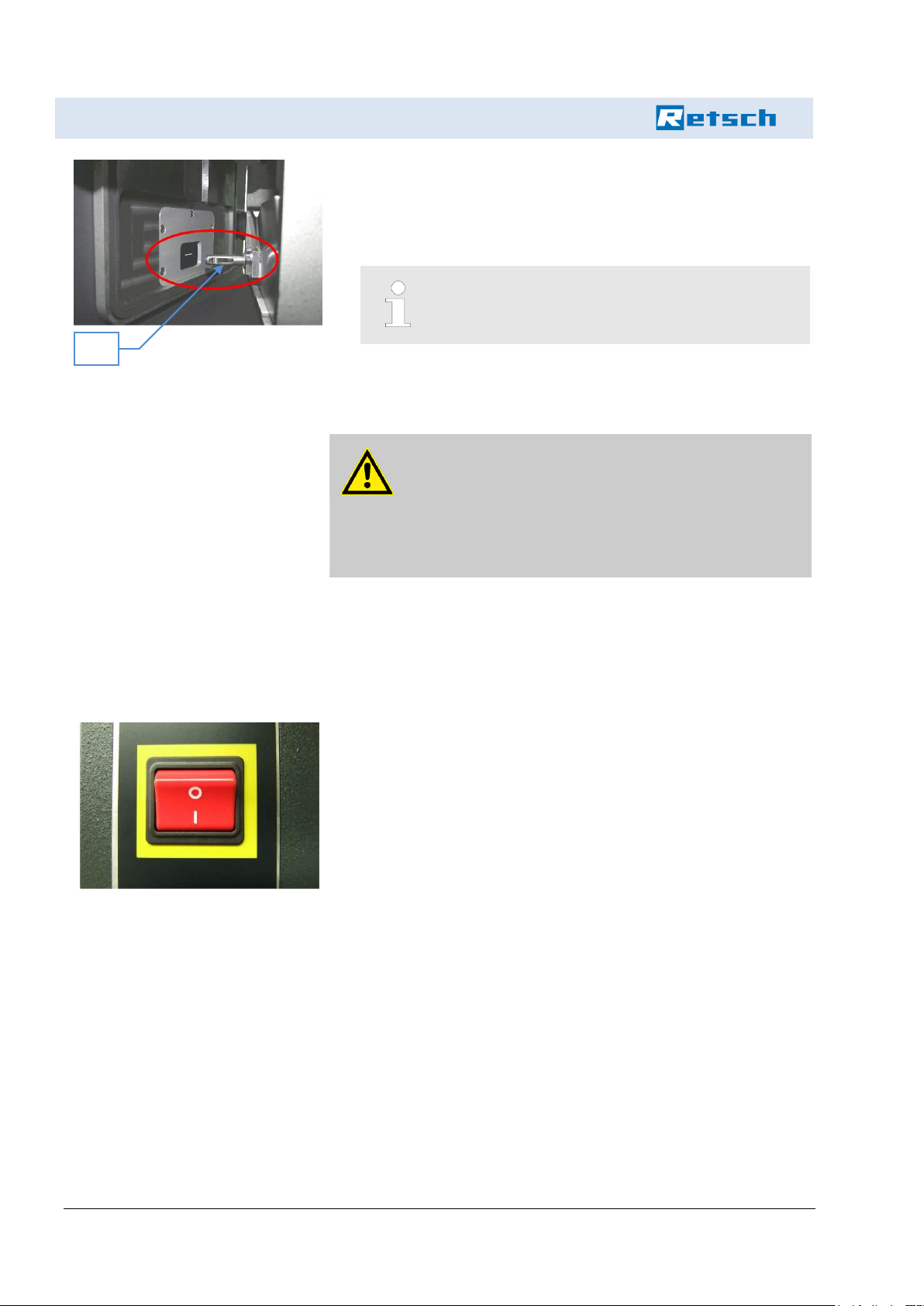
Safety instructions and use
The interlock switch (13) pulls in the sample material container
after the start of grinding and locks it using the locking bolt (9) on
the container. During operation the interlock switch monitors
whether the device is closed correctly. It likewise prevents the
disc mill starting up after it has been opened.
The disc mill does not start if the grinding chamber
is open or the sample material container is missing.
CAUTION!
- Risk of crushing on hopper cover
- Risk of crushing when closing the grinding chamber
- Risk of crushing when cover of dust extraction is
removed during operation!
The disc mill is switched on and off with a main switch (3).
By pressing the switch to I (On):
Disc mill is activated and can be started using the start button (e)
as long as the grinding chamber is closed and the sample material
container is inserted!
By pressing the switch to O (off) during grinding:
The disc mill comes to a halt and is completely deactivated!
Grinding chamber and sample material container remain locked
when switched “off” and cannot be opened.
2.7 Danger areas
2.8 Electrical safety
2.8.1 General information