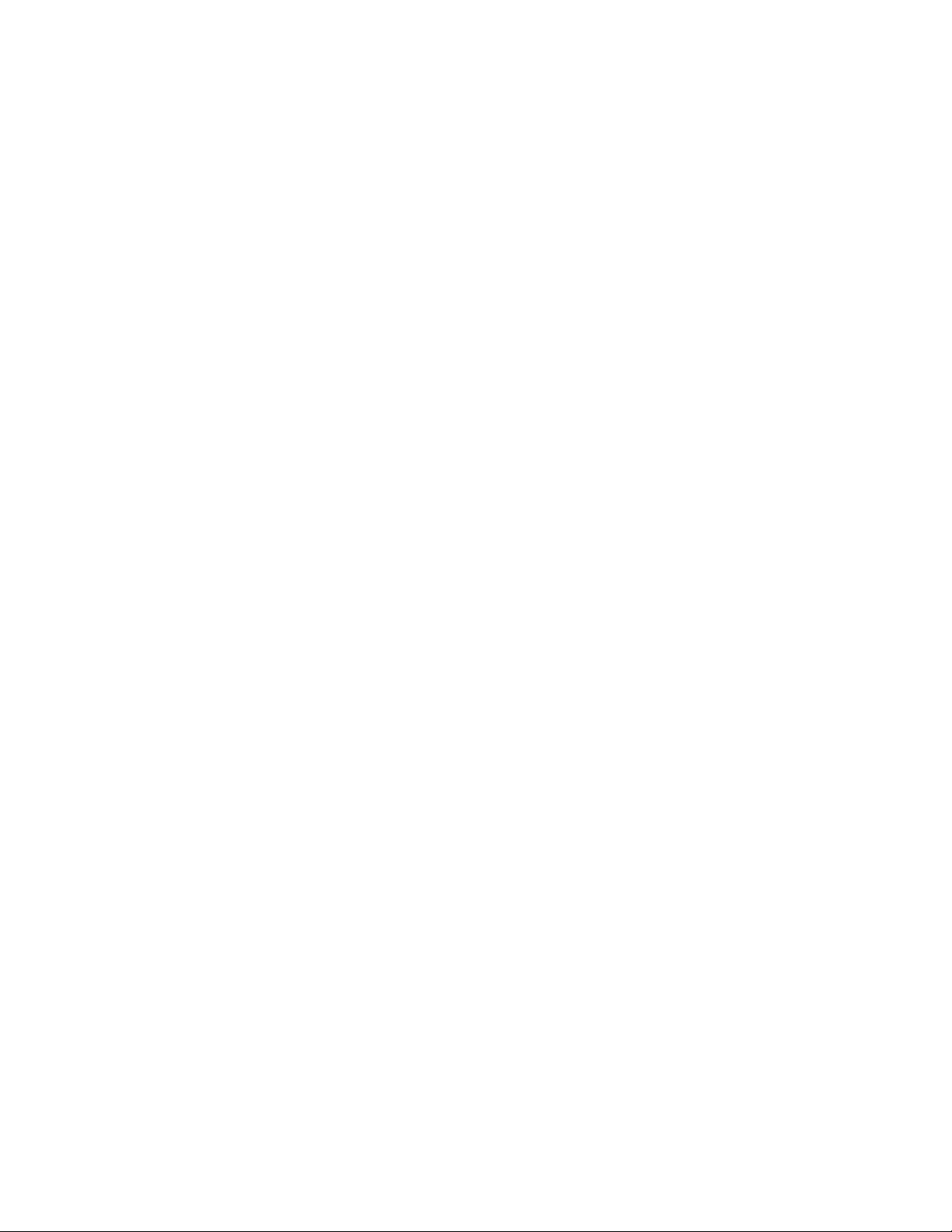
TABLE OF CONTENTS
GENERAL INFORMATION 1. . . . . . . . . . . . . . . . .
GENERAL DESCRIPTION 1. . . . . . . . . . . . . . .
UNIT DESCRIPTION 1. . . . . . . . . . . . . . . . . . . .
THEORY OF OPERA TION 2. . . . . . . . . . . . . .
INSTALLA TION 5. . . . . . . . . . . . . . . . . . . . . . . . . . .
UNP ACKING AND INSPECTION 5. . . . . . . . .
IDENTIFICA TION OF LOOSE--SHIPPED
P ARTS 5. . . . . . . . . . . . . . . . . . . . . . . . . . . . . . . .
SELECTING LOCATION 5. . . . . . . . . . . . . . . . .
INSTALLING UNIT 5. . . . . . . . . . . . . . . . . . . . . .
LOCA TING UNIT 5. . . . . . . . . . . . . . . . . . . . .
DRAIN CONNECTIONS 6. . . . . . . . . . . . . . .
ROUTING UNIT PRODUCT INLET LINES AND
DRIP TRAY DRAIN HOSE OUT OF UNIT CAB-
INET 6. . . . . . . . . . . . . . . . . . . . . . . . . . . . . . . .
CONNECTING UNIT PRODUCT INLET
LINES 6. . . . . . . . . . . . . . . . . . . . . . . . . . . . . . .
INSTALLING DISPENSING VALVES
KNOBS 6. . . . . . . . . . . . . . . . . . . . . . . . . . . . . .
FILL EVAPORATOR TANK AND STAR T REFRIG-
ERA TION SYSTEM 6.. . . . . . . . . . . . . . . . . . . .
PREP ARING UNIT FOR OPERATION 7. . . . .
UNIT OPERATION 7. . . . . . . . . . . . . . . . . . . . . .
OPERA TORS INSTRUCTIONS 9. . . . . . . . . . . . .
OPERA TING CONTROLS 9. . . . . . . . . . . . . . .
DISPENSING VALVE LEVER 9. . . . . . . . . . .
UNIT POWER SWITCH 9. . . . . . . . . . . . . . .
DAIL Y PRE OPERATION CHECK 9. . . . . . . . .
UNIT OPERATION 9. . . . . . . . . . . . . . . . . . . . . .
ADJUSTMENTS 9. . . . . . . . . . . . . . . . . . . . . . . .
ADJUSTING PRODUCT TANKS CO2 REG-
ULA TORS 9. . . . . . . . . . . . . . . . . . . . . . . . . . .
ADJUSTING DISPENSED PRODUCT FLOW
RA TE 9. . . . . . . . . . . . . . . . . . . . . . . . . . . . . . . .
REPLENISHING CO2 SUPPLY 9. . . . . . . . . . .
REPLENISHING PRODUCT SUPPLY 9. . . . .
CLEANING AND SANITIZING 9. . . . . . . . . . . .
DAIL Y CLEANING OF UNIT 9. . . . . . . . . . . .
WEEKL Y CLEANING OF DISPENSING
V ALVES 9. . . . . . . . . . . . . . . . . . . . . . . . . . . . .
SANITIZING UNIT 9. . . . . . . . . . . . . . . . . . . .
CHECKING CONDENSER COIL FOR RESTRIC-
TIONS 9. . . . . . . . . . . . . . . . . . . . . . . . . . . . . . . . .
CHECKING ICE WATER BATH 9. . . . . . . . . . .
SERVICE AND MAINTENANCE 11.. . . . . . . . . . .
PREP ARING UNIT FOR SHIPPING, RELOCAT-
ING, OR STORING 1 1.. . . . . . . . . . . . . . . . . . . .
PAGE
TOP COVER, ACCESS GRILLES, AND DRIP
TRA Y REMOVAL ) 1 1.. . . . . . . . . . . . . . . . . . . . .
TOP COVER REMOV AL 1 1.. . . . . . . . . . . . . .
ACCESS GRILLES REMOVAL 1 1.. . . . . . . .
DRIP TRAY REMOVAL 11. . . . . . . . . . . . . . . .
PERIODIC INSPECTION 11.. . . . . . . . . . . . . . .
ADJUSTMENTS 1 1.. . . . . . . . . . . . . . . . . . . . . . .
ADJUSTING PRODUCT TANKS CO2 REG-
ULA TORS 11.. . . . . . . . . . . . . . . . . . . . . . . . . .
ADJUSTING DISPENSED PRODUCT FLOW
RA TE 1 1.. . . . . . . . . . . . . . . . . . . . . . . . . . . . . . .
REPLENISHING CO2 SUPPLY 1 1.. . . . . . . . . .
REPLENISHING PRODUCT SUPPLY 12. . . . .
PRODUCT FLAVOR CHANGE 12. . . . . . . . . . .
CLEANING CONDENSER COIL 12. . . . . . . . . .
CHECKING ICE WATER BATH ) 12.. . . . . . . . .
CLEANING EVAPORATOR TANK ) 14. . . . .
CLEANING AND SANITIZING 15. . . . . . . . . . . .
DAIL Y CLEANING OF UNIT 15. . . . . . . . . . . .
WEEKL Y CLEANING OF DISPENSING
V ALVES ) 16. . . . . . . . . . . . . . . . . . . . . . . . . . . .
SANITIZING UNIT 16. . . . . . . . . . . . . . . . . . . .
TROUBLESHOOTING 21. . . . . . . . . . . . . . . . . . . . .
NO PRODUCT DISPENSED. 21.. . . . . . . . . . . .
DISPENSED PRODUCT COMES OUT OF DISPENSING VALVE CLEAR BUT FOAMS IN CUP
OR GLASS 21. . . . . . . . . . . . . . . . . . . . . . . . . . . . .
DISPENSED PRODUCT FOAMS AS IT LEAVES
DISPENSING VALVE. 21. . . . . . . . . . . . . . . . . . .
REFRIGERA TION SYSTEM 22. . . . . . . . . . . . . .
COMPRESSOR DOES NOT OPERA TE. 22.
COMPRESSOR WILL NOT STOP AFTER
SUFFICIENT ICE BANK IS FORMED. 22. .
COMPRESSOR OPERATES CONTINUOUSLY
BUT DOES NOT FORM SUFFICIENT ICE
BANK. 22.. . . . . . . . . . . . . . . . . . . . . . . . . . . . . .
CONDENSER FAN MOTOR NOT
OPERA TING. 23. . . . . . . . . . . . . . . . . . . . . . . .
AGITA TOR MOTOR NOT OPERATING. 23.
COMMERCIAL WARRANTY 25. . . . . . . . . . . . . . .
LIST OF FIGURES
FIGURE 1. UNIVERSAL 750 PRE-MIX DISPENS-
ER 1. . . . . . . . . . . . . . . . . . . . . . . . . . . . . . . . . . . .
FIGURE 2. FLOW DIAGRAM 3. . . . . . . . . . . . .
FIGURE 3. PAR TS IDENTIFICATION 13. . . . . .
FIGURE 4. EVAPORATOR TANK (STANDARD
UNIT SHOWN) 14. . . . . . . . . . . . . . . . . . . . . . . . .
FIGURE 5. CLEANING DISPENSING VALVE 15
FIGURE 6. WIRING DIAGRAM 18. . . . . . . . . . .
i
PAGE
189159000
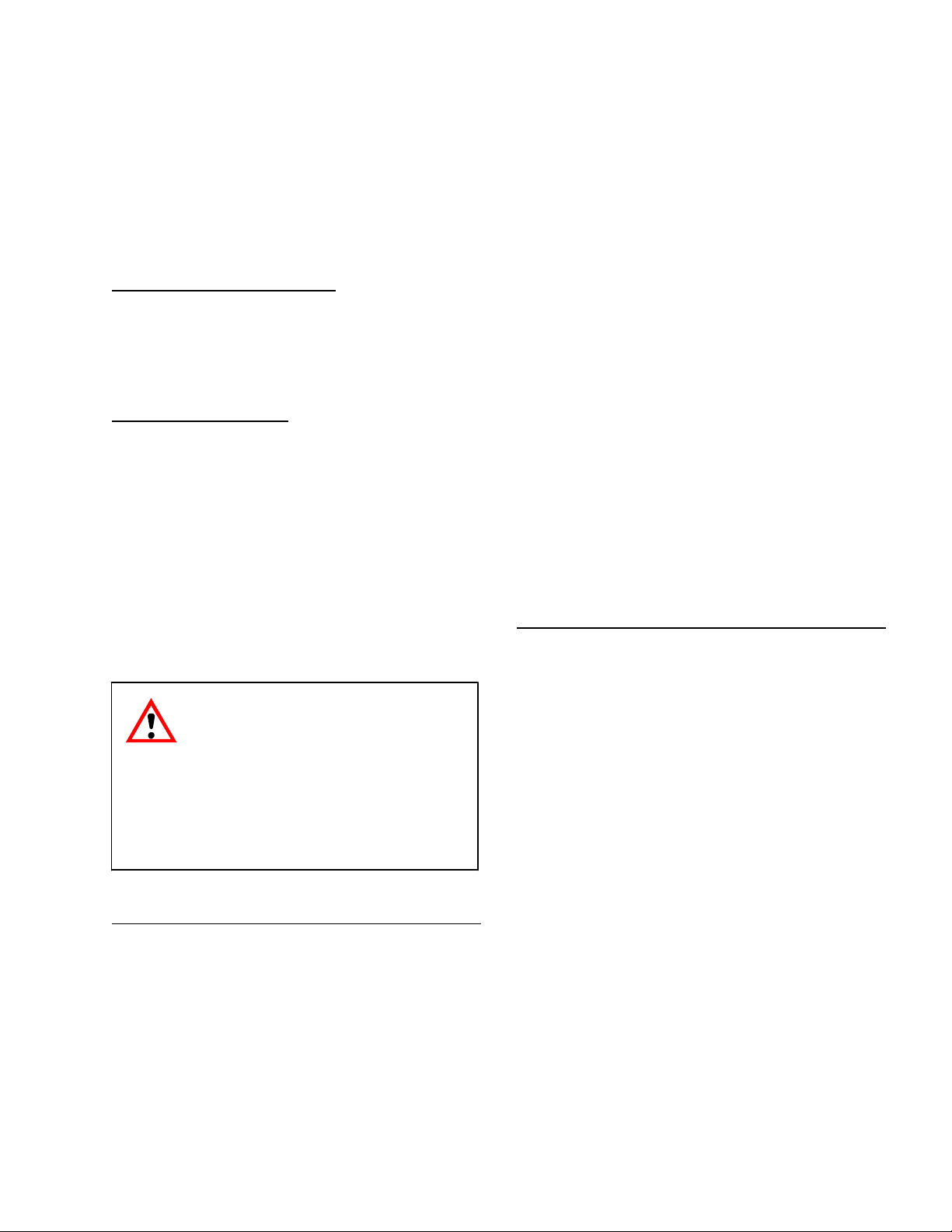
GENERAL INFORMATION
IMPORTANT: To the user of this manual -- This
manual is a guide for installing, operating, and
maintaining this equipment. Refer to Table of
Contents for page location of detailed
information pertaining to questions that arise
during installation, operation, service and
maintenance, or troubleshooting this equipment.
GENERAL DESCRIPTION
This section gives the unit description, installation
requirements, theory of operation, design data, and
flow diagram for the Universal 750 Four-- Flavor Pre-Mix Dispenser (hereafter referred to as a unit).
UNIT DESCRIPTION
The dispenser (see Figure 1) is a compact unit that
may be installed free standing or under a
counter or bar.
Installation of the LOOSE-- SHIPPED PARTS, (see
Table 2-- 1), connection to a grounded electrical outlet
with proper electrical requirements, filling evaporator
tank with water, and connection to product tanks with
regulated CO2pressure are all that is required to set
unit up for operation. A 6--inch leg kit (P/N
187416-- 000) is available. Also available is a four
caster kit (P/N 316290-- 000) to make unit mobile.
CAUTION: Before shipping, storing,
or relocating this Unit, the syrup
systems must be sanitized and all
sanitizing solution must be purged from the
syrup systems. All water must also be
purged from the plain and carbonated water
systems. A freezing ambient environment
will cause residual water in the Unit to freeze
resulting in damage to internal components.
Table 1. Design Data
Model Numbers:
Universal 750 (domestic) 284729-- 000
Standard Unit
Universal 750 (domestic) with 284780-- 000
Sealed Evaporator Tank
Universal 750 (export) 494729-- 000
Overall Dimensions:
Height 37--1/4 inches
Width 16 inches
Depth (with drip tray) 22 inches
FIGURE 1. UNIVERSAL 750 PRE-MIX DISPENSER
Table 1. Design Data (cont’d)
Weights:
Shipping (1Carton) 159 pounds
Dry Weight 140 pounds
With Evaporator Tank full 225 pounds
of Water
Ice Bank Weight 46 pounds
Capacities:
Unit Water Bath (no ice bank)
approx.
Dispensing Rate:
6-- oz. drinks @ 4/minute *763
6-- oz. drinks @ 6/minute *507
Recovery Rate 3 drinks/minute
NOTE: *Number of 6-- oz. drinks that can be dispensed at 40° F or below with 75° F product inlet
temperature and 75° F ambient.
Ambient Operating Temperature 40°F to 100°F
Electrical Requirements:
Operating Voltage (domestic) 1 15 VAC, 60
Current Draw (domestic) 8.1 amps
Operating Voltage (export) 230 VAC, 50
Current Draw (export) 3 amps
1 189159000
10 gallons
Hz
Hz
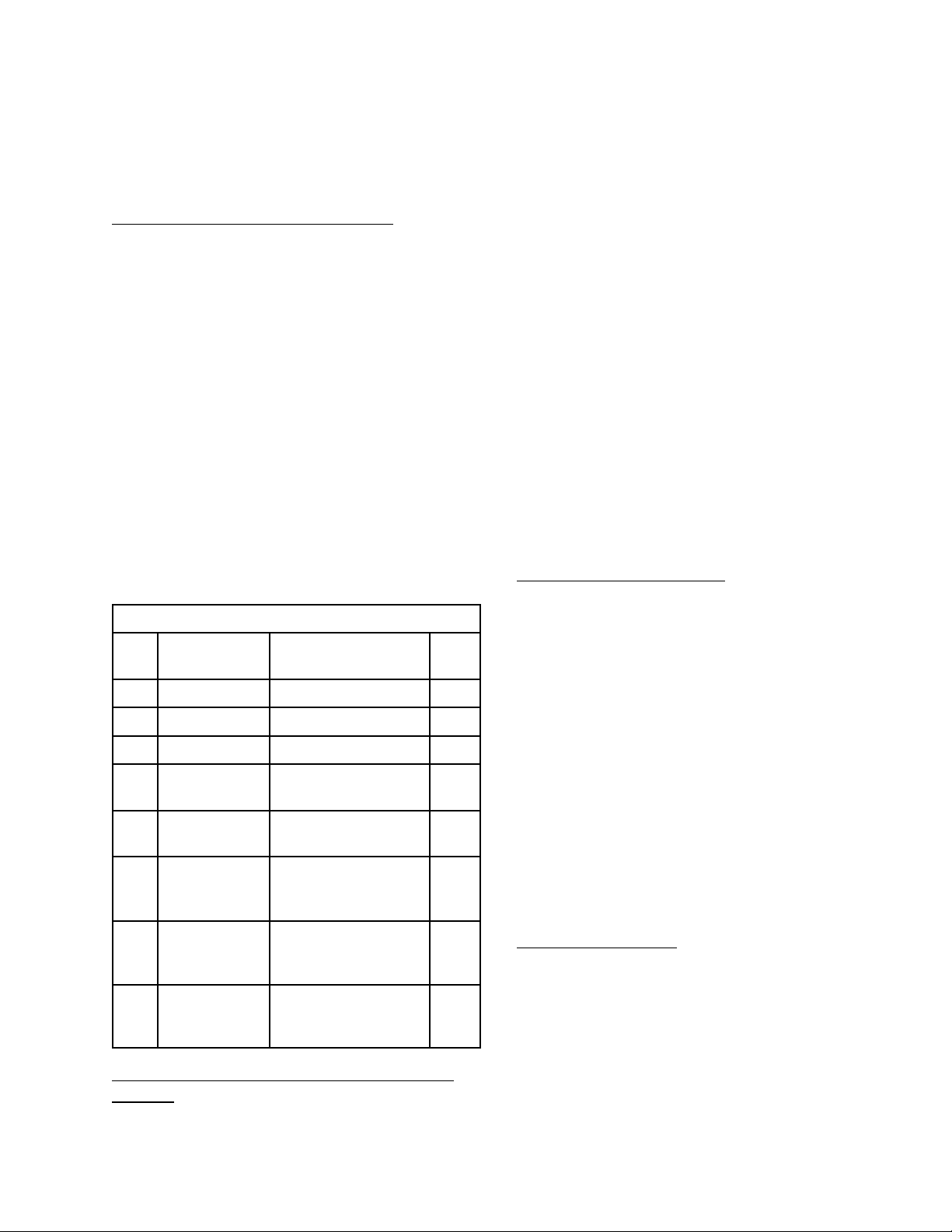
INSTALLATION
This section covers unpacking and inspection, identification of LOOSE--SHIPPED PARTS, selecting location, installing unit, preparing unit for operation, and
unit operation.
UNPACKING AND INSPECTION (see Figure
3)
NOTE: The unit was thoroughly inspected before
leaving factory and carrier has accepted and
signed for it. Any damage or irregularities
should be noted at time of delivery and immediately reported to delivering carrier. Request a
written inspection report from Claims Inspector
to substantiate any necessary claim. File claim
with delivering carrier, not with IMI Cornelius Inc.
1. After unit has been removed from shipping carton, remove shipping tape and other packing
material. Inspect for shipping damage and follow
procedure in preceding NOTE if damage is evident.
2. Unpack item listed in LOOSE--SHIPPED
P ARTS. Make sure all items are present and in
good condition.
2. CUP REST (item 2) to be installed in DRIP
TRA Y
(item 3).
3. DRIP TRAY (item 3) to be installed on unit by
inserting rear edge of tray under lip of valve trim
panel and lifting up until bottom tray supports
are inserted in square holes provided in front
panel. Lock drip tray in place by slight downward pressure.
4. DECALS, DISPENSING VALVES KNOBS (item
7) to be installed on DISPENSING V ALVES
KNOBS (item 4)
5. DISPENSING VALVES KNOBS (item 4) to be
installed on dispensing valves by pushing knobs
down into place on valves levers.
6. Applicable ADAPTERS (item 5) to be used to
connect product inlet lines from product tanks to
unit product inlet lines. REDUCERS (item 6)
may be used to connect unit product inlet lines
directly to product tanks quick disconnects provided disconnects have 1/4-- inch flare (7/16--20)
male fittings.
SELECTING LOCATION
Table 2. Loose-Shipped Parts
Item
No. Part No. Name Qty.
1 188090 Leveling Legs 4
2 186642 Cup Rest 1
3 186573-- 039 Drip Tray 1
4 151741-- 039 Dispensing Valve
Knob
5 150807-- 100 Adapter, 7/16-- 20
Male by 1/2--16 Male
150807-- 200 Adapter, 1/2-- 16
Male by 1/2--16 Male
(domestic unit only)
6 31 1245 Reducer, 7/16--20
Female by 1/2--16
Male
7 317904-- 999 Decal, Dispensing
V alve Knob (as
ordered)
IDENTIFICATION OF LOOSE--SHIPPED
PARTS (see Figure 3)
1. LEVELING LEGS (item 1) to be installed in
threaded holes provided on unit base (only units
installed outside the United States).
NOTE: For identification purposes, side of unit
dispensing valves are on is designated ‘‘front’’ of
unit. This unit may be installed free standing or
under counter or bar. Locate unit so following
requirements are satisfied.
1. Near a properly grounded electrical outlet with
proper electrical requirements. No other electrical appliance should be connected to this circuit.
ALL ELECTRICAL WIRING MUST CONFORM
4
4
4
4
TO NATIONAL AND LOCAL ELECTRICAL
CODES.
2. Air circulation through condenser coil, required
for cooling coil, is drawn in through air intake
grille on front of unit and is exhausted out
through grilles on sides and back of unit. When
locating unit, make sure grilles are not restricted
to insure proper air circulation through unit.
INSTALLING UNIT
LOCATING UNIT
4
Areas Outside United States (Canada, Europe, etc.)
Install LEVELING LEGS (item 1) in threaded holes
on each corner of unit base. Adjust each leveling leg
until unit sits level and stands solid. Make sure all
leveling legs are in contact with floor.
Areas Within United States -- To comply with National
Sanitation Foundation (NSF) requirements, unit must
be sealed to floor and LEVELING LEGS (item 1)
may not be used. Perform following procedure to
install unit.
5 189159000