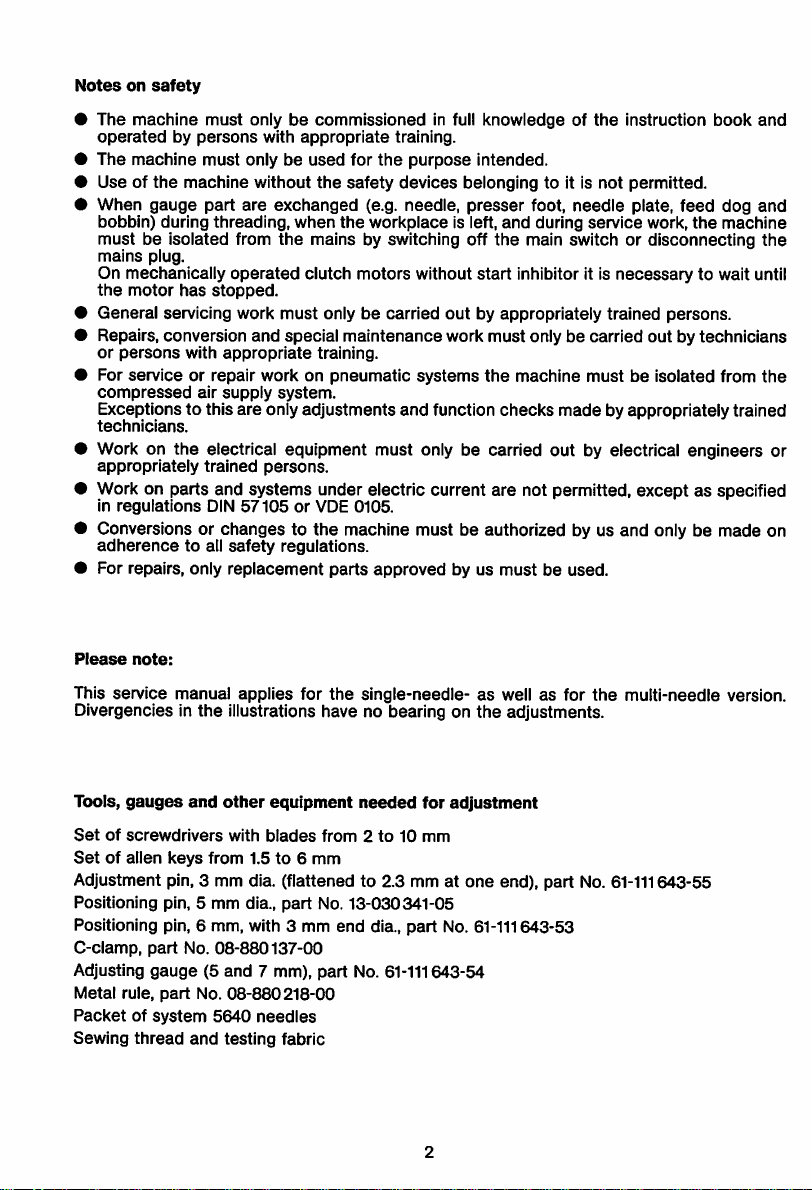
Notesonsafety
•
The
machine
operatedbypersons
•
The
machine
•
Useofthe
•
When
bobbin)
must
be isolated from
mains
On
mechanically
the
motor
• General servicing work
• Repairs, conversion
or
persons
• For
service
compressed
Exceptionstothis
technicians.
• Work on
appropriately
must
must
machine
gauge
part
during
threading,
plug.
has
stopped.
with
appropriate
or repair work on
air
supply
the
electrical
trained
onlybecommissioned
with
appropriate
onlybeused
without
are
exchanged
the
operated
must
and
special
for
the
safety
when
the
mains by switching off
clutch
motors
onlybecarried
maintenance
training.
pneumatic
system.
are
only
adjustments
equipment
persons.
in full
training.
the
purpose
devices
(e.g.
needle,
workplace
knowledgeofthe
intended.
belonging
presser
is left,
and
the
without
systems
and
start
out
by appropriately trained
work
must
the
function
checks
must only be carried
to it is
foot,
during
not
needle
service
instruction
permitted.
plate,
work,
book
feed
the
main switch or disconnecting
inhibitor it is
necessary
to wait until
persons.
only be carried
machine
made
out
by electrical
outbytechnicians
mustbeisolated
by appropriatelytrained
engineers
and
dog
and
machine
the
from
the
• Work on parts and systems under electric current are not permitted, except as specified
in
regulations
• Conversions or
adherencetoall
• For repairs, only
Please
note:
This service manual
Divergencies in
DIN
57105orVDE 0105.
changestothe
safety
regulations.
replacement
applies
the
illustrations have no bearing on
machine must be authorized by us and only be made on
parts
approved
for
the
single-needle-aswell as for
by us
the
must
be used.
adjustments.
the
multi-needle version.
or
Tools,
gauges
Setofscrewdrivers
Set
of alien
and
other
with
keys
from 1.5to6 mm
equipment
blades
from2to10mm
needed
for
Adjustment pin, 3 mm dia. (flattened to 2.3 mm at
Positioning pin, 5 mm dia.,
Positioning pin, 6 mm, with 3 mm end dia.,
C-clamp,
Adjusting
Metal
Packetofsystem
Sewing
part
gauge(5and
rule,
part
thread
No.
08-880137-00
No.
5640
and
part
7 mm),
08-880218-00
needles
testing
fabric
No.
13-030341-05
part
No. 61-111643-54
part
adjustment
one
end), part No. 61-111643-55
No. 61-111643-53
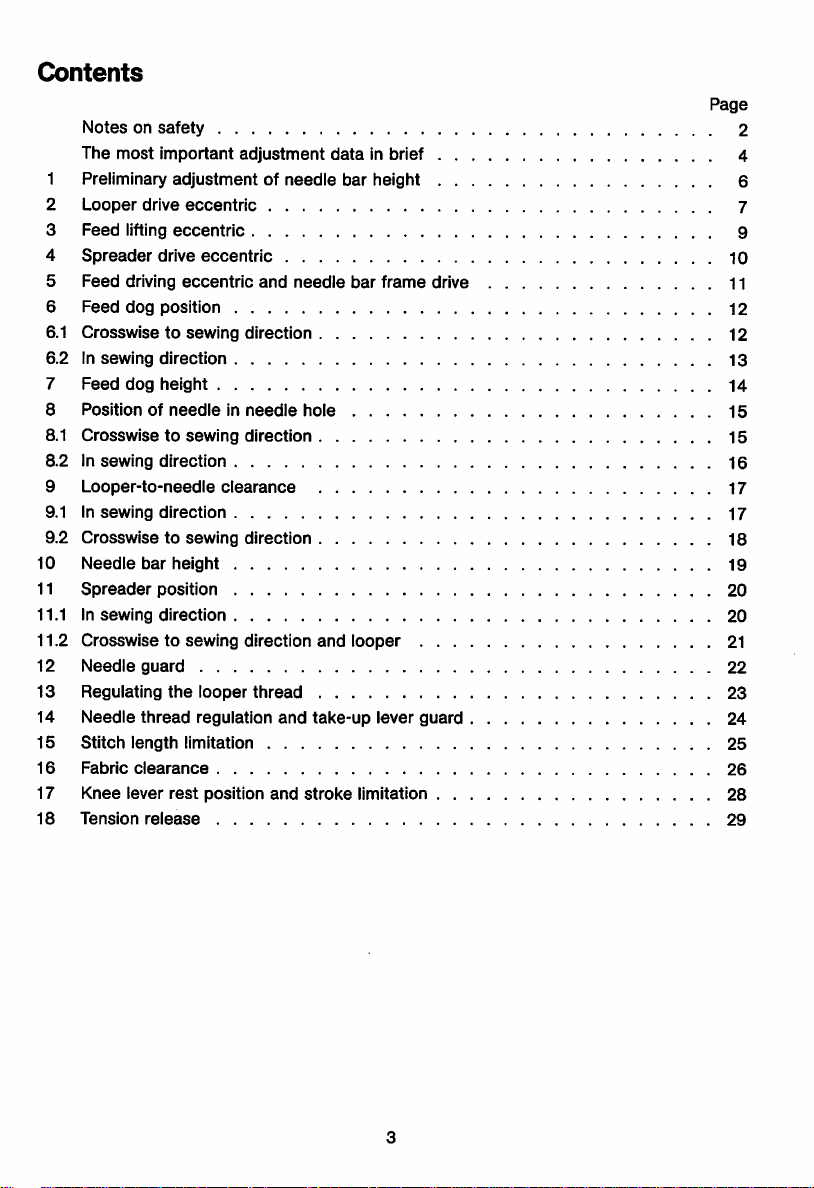
Contents
Notesonsafety
The
most
important
1 Preliminary
2
Looper
3
Feed
Spreader
4
5
Feed
6
Feed
6.1
Crosswisetosewing
6.2Insewing
7
Feed
8
Positionofneedleinneedle
8.1
Crosswisetosewing
8.2Insewing
9
Looper-to-needle
sewing
9.1 In
9.2
Crosswisetosewing
10
Needle
11
Spreader
11.1 In
sewing
adjustmentofneedle
drive
lifting
eccentric
drive
driving
dog
position
direction
dog
height
direction
direction
bar
height
position
direction
11.2 Crosswise to sewing direction
12
Needle
guard
13
14
15
16
17
18
Regulating
Needle
Stitch
Fabric
Knee
Tension
thread
length
clearance
lever
release
the
rest
eccentric
eccentric
eccentric
clearance
looper
regulation
limitation
position
adjustment
and
needle
direction
direction
direction
thread
and
and
data
hole
and
take-up
stroke
In brief 4
bar
height
bar
frame
drive
looper
lever
guard
limitation
Page
2
6
7
9
10
11
12
12
13
14
15
15
16
17
17
18
19
20
20
21
22
23
24
25
26
28
29
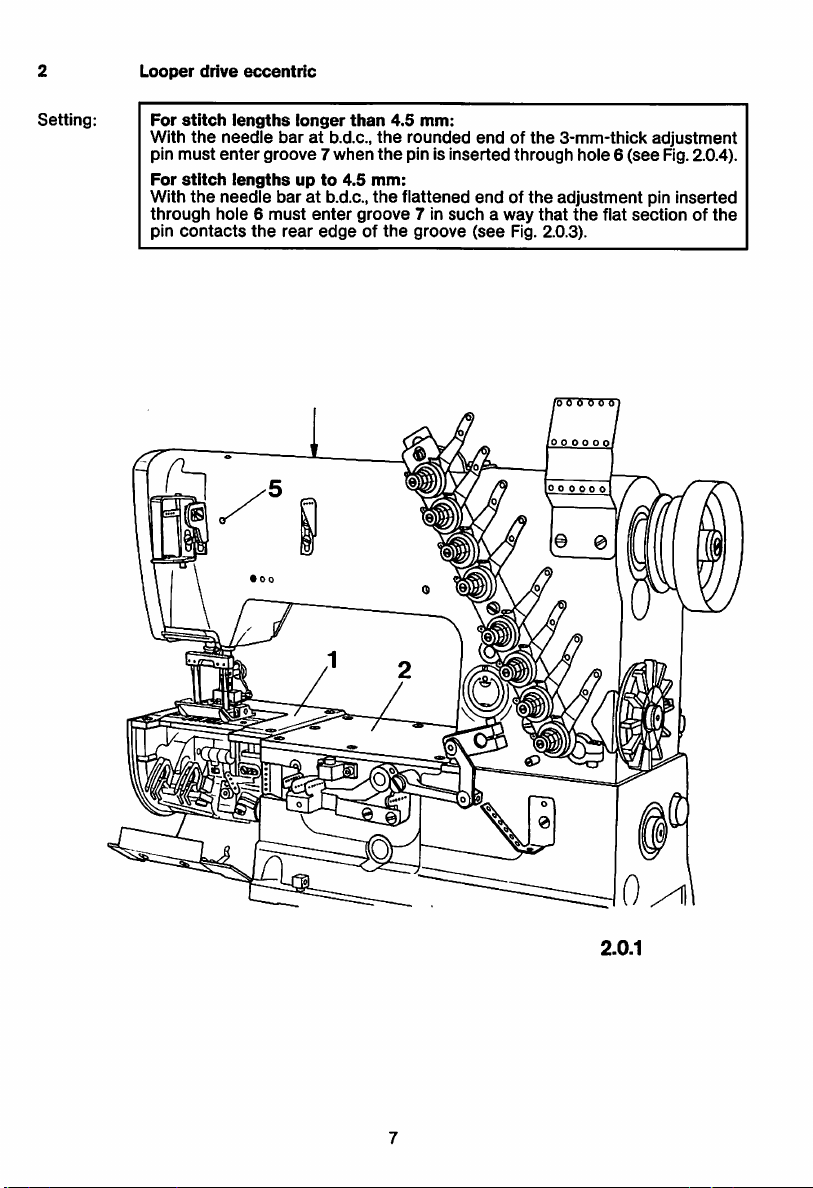
2
Looper
drive
eccentric
Setting:
For
stitch
With
pin
must
For
stitch
With
the
through
pin
contacts
lengths
the
needle
enter
lengthsupto
needle
hole6must
longer
baratb.d.c.,
groove
baratb.d.c.,
the
rear
than
7 when
4.5
mm:
the
enter
groove
edgeofthe
4.5
mm:
the
rounded
the
pin is insertedthrough hole6
flattened
groove
7 in
suchaway
endofthe
endofthe
(see
Fig. 2.0.3).
that
3-mm-thlck
(see
adjustment
the
flat
o o O O O O
adjustment
Rg. 2.0.4).
pin
inserted
sectionofthe
2.0.1
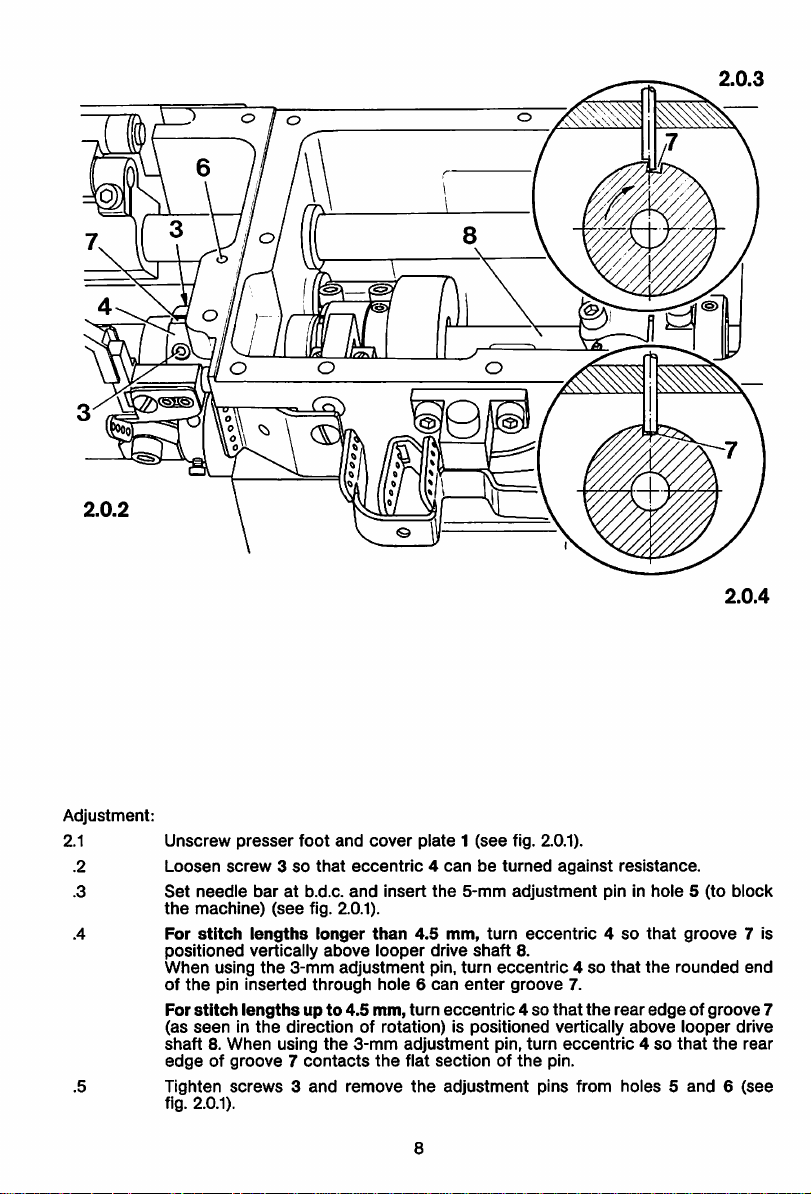
2.0.3
2.0.4
Adjustment:
2.1
.2
.3
Unscrew
Loosen
Set
the
For
positioned
When
of
For
(as
shaft8.When
edgeofgroove7contacts
Tighten
fig. 2.0.1).
presser
screw3so
needle
machine)
stitch
using
the
pin
inserted
stitch
lengthsupto
seeninthe
screws3and
foot
and
that
baratb.d.c.
(see
fig. 2.0.1).
lengths
vertically
the
longer
3-mm
above
adjustment
through
directionofrotation)ispositioned
using
the
cover
plate1(see
eccentric4canbeturned
and
insert
the
than
4.5
looper
mm,
drive
pin,
hole6can
4.5
mm,
turn
eccentric4so
3-mm
adjustment
the
flat
sectionofthe
remove
the
8
adjustment
fig. 2.0.1).
5-mm
adjustment
turn
shaft
turn
eccentric4so
enter
groove
pin,
8.
against
eccentric4so
resistance.
pin in
that
7.
that
the
rear
vertically
turn
eccentric4so
pin.
pins
from
hole5(to
that
the
groove
rounded
block
7 is
end
edgeofgroove
above
looper
drive
that
the
rear
holes5and6(see
7