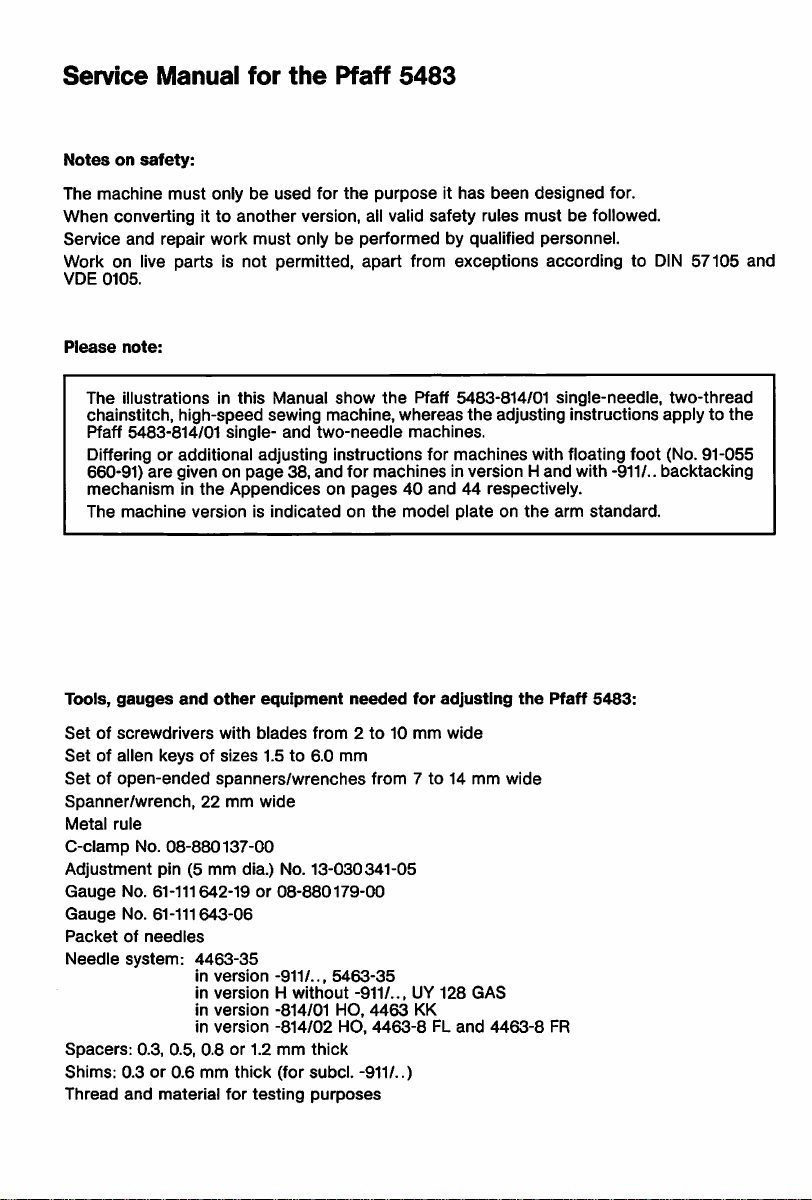
Service
Notesonsafety:
The
When
Service
Work on live
VDE
Please
The
chainstitch,
Pfaff
Manual
machine
0105.
must
converting
and
repair
partsisnot
note:
illustrationsinthis
high-speed
5483-814/01
Differing or additional
660-91)
are
givenonpage
mechanisminthe
The
machine
for
the
onlybeused
it to
another
work
must
sewing
single-
adjusting
Pfaff
for
version, ali valid
onlybeperformedbyqualified
permitted,
Manual
and
38,
show
machine,
two-needle
instructions
and
5483
the
purposeithas
safety
rules
apart
from
exceptions
the
Pfaff
5483-814/01
whereas
for
machinesinversionHand
machines.
for
machines
the
Appendicesonpages40and44respectively.
versionisindicatedonthe
model
plateonthe
been
designed
mustbefollowed.
personnel.
according
single-needle,
adjusting
instructions
with floating
with -911/..
arm
for.
to DIN
foot
standard.
57105
two-thread
applytothe
(No. 91-055
backtacking
and
Tools,
gauges
Setofscrewdrivers
Setofalien
Setofopen-ended
Spanner/wrench,
Metal
rule
C-clamp
Adjustment
Gauge
Gauge
Packetofneedles
Needle
Spacers;
Shims:
Thread
and
keysofsizes
No.
08-880137-00
pin(5mm
No.
61-111642-19or08-880179-00
No.
61-111643-06
system:
0.3, 0.5,
0.3or0.6
and
material
other
equipment
with
blades
1.5to6.0
spanners/wrenches
22
mm
wide
dia.) No.
4463-35
in
version
in
versionHwithout
in
version
in
version
0.8
mm
or 1.2
thick
for
-911/..,
-814/01
-814/02
mm
(for
testing
needed
from2to10mm
mm
13-030341-05
5463-35
HO,
HO,
thick
subcl.
for
from7to14mm
-911/..,UY128
4463
4463-8FLand
-911/..)
purposes
KK
adjusting
wide
GAS
the
wide
4463-8
Pfaff
FR
5483:
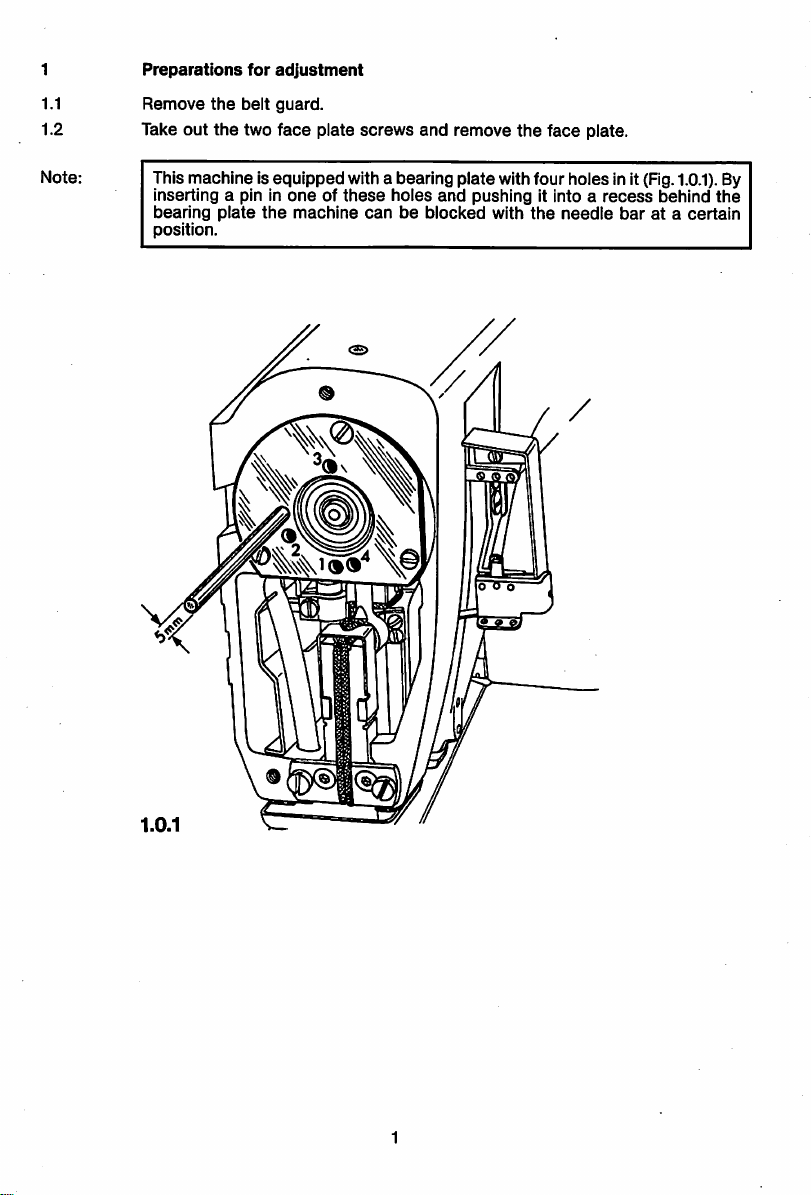
1
Preparations
for
adjustment
1.1
Remove
1.2 Take
Note:
This machineIs
Inserting a pin In
bearing
position.
out
the
the
plate
belt
two
equipped
the
guard.
face
plate
oneofthese
machine
screws
and
remove
the
face
plate.
with a bearingplatewithfour holes InIt (Fig.
holes
and
canbeblocked
pushing It Into a
with
the
needle
recess
barata
behind
1.0.1).
certain
By
the
1.0.1
P
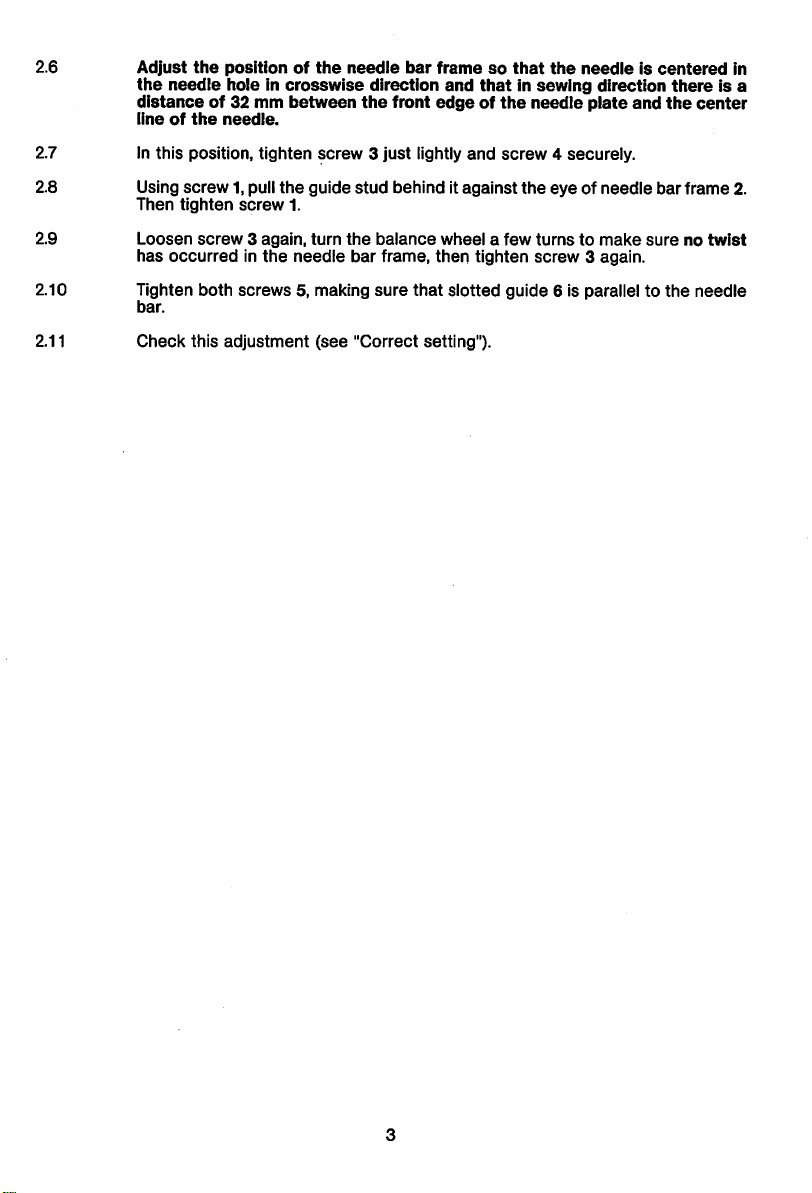
2.6
Adjust
the
the
positionofthe
needle
holeIncrosswise
distanceof32
lineofthe
needle.
mm
between
2.7 In this position, tighten
screw
1,pull
2.8 Using
Then
2.9
Loosen
has
occurredinthe
2.10 Tighten
bar.
tighten
screw3again,
both
screw
screws
the
1.
needle
needle
screw
guide
stud
turn
the
bar
5, making
bar
direction
the
front
3 Just lightly
behind it
balance
frame,
sure
that
framesothat
and
thatInsewing
edgeofthe
and
screw
against
the
wheel
a few
then
tighten
slotted
guide
the
needleIscentered
direction
needle
plate
4 securely.
eyeofneedle
turnstomake
screw
3 again.
6 is parallel to
there
and
the
center
bar
frame
surenotwist
the
needle
In
Is a
2.
2.11
Check
this
adjustment
(see
"Correct
setting").
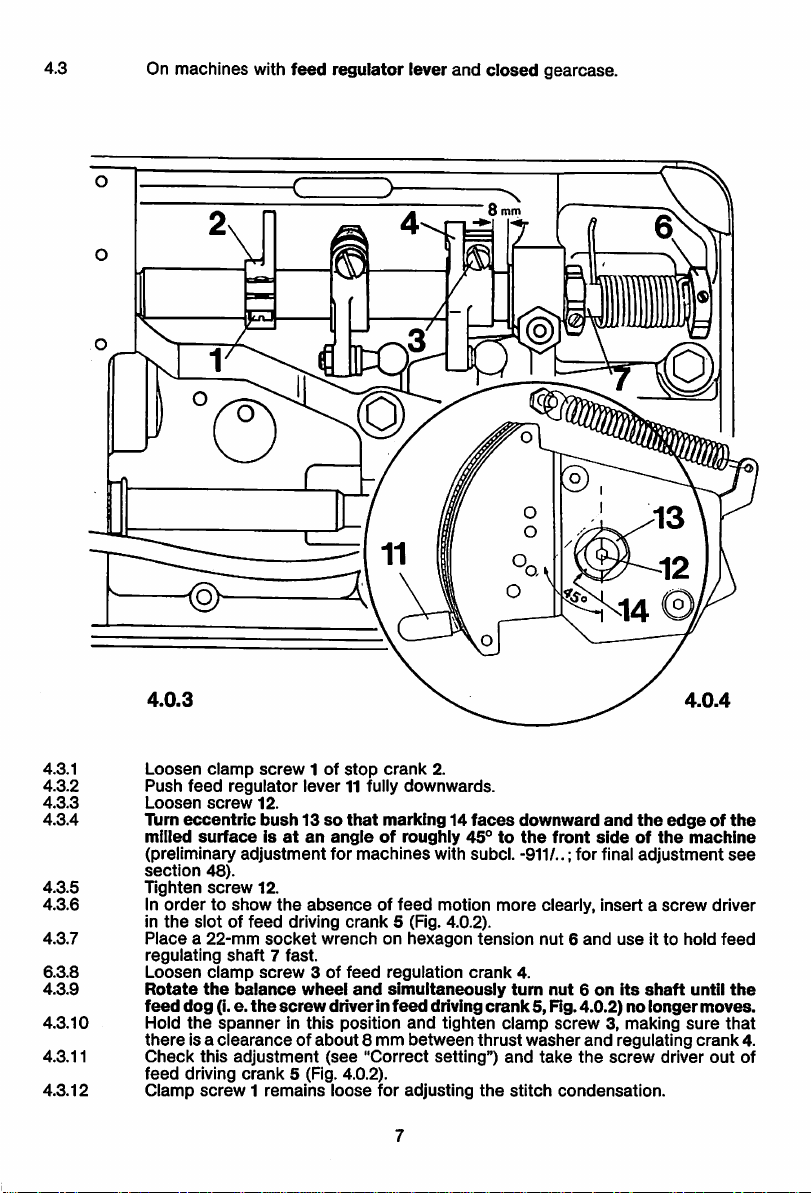
4.3
On
machines
with
feed
regulator
lever
and
closed
gearcase.
©
4.3.1
4.3.2
4.3.3
4.3.4
4.3.5
4.3.6
4.3.7
6.3.8
4.3.9
4.3.10
4.3.11
4.3.12
Loosen
Push
Loosen
Turn
milled
(preliminary
section
Tighten
In
In
Placea22-mm
regulating
Loosen
Rotate
feed
Hold
there
Check
feed
Clamp
clamp
screw
feed
regulator
screw
eccentric
surfaceisatanangleofroughly
adjustment
48).
screw
ordertoshow
the
slotoffeed
shaft7fast.
clamp
the
balance
dog
(i.e.
the
spannerInthis
Isa
clearanceofabout
this
adjustment
driving
crank
screw1remains
12.
bush13so
12.
the
driving
socket
screw
the
screw
5 (Fig. 4.0.2).
1 of
lever
for
absenceoffeed
wrenchonhexagon
3 of
wheel
driver in
(see
loose
stop
crank
11 fully
downwards.
that
marking14faces
machines
crank
5 (Fig. 4.0.2).
feed
regulation
and
simultaneously
feed
position
8 mm
"Correct
for
adjusting
2.
with
motion
driving
and
tighten
between
setting")
downward
45°tothe
subcl.
-911/..; for final
more
tension
crank
4.
turn
crank
clamp
thrust
washer
and
the
stitch
and
front
sideofthe
clearly,
Insertascrew
nut6and
nut6on
use
its
5, Fig.4.0.2)no
screw3,making
and
take
regulating
the
screw
condensation.
the
edgeofthe
machine
adjustment
It to
hold
shaft
until
longer
moves.
sure
crank
driver
see
driver
feed
the
that
out
4.
of
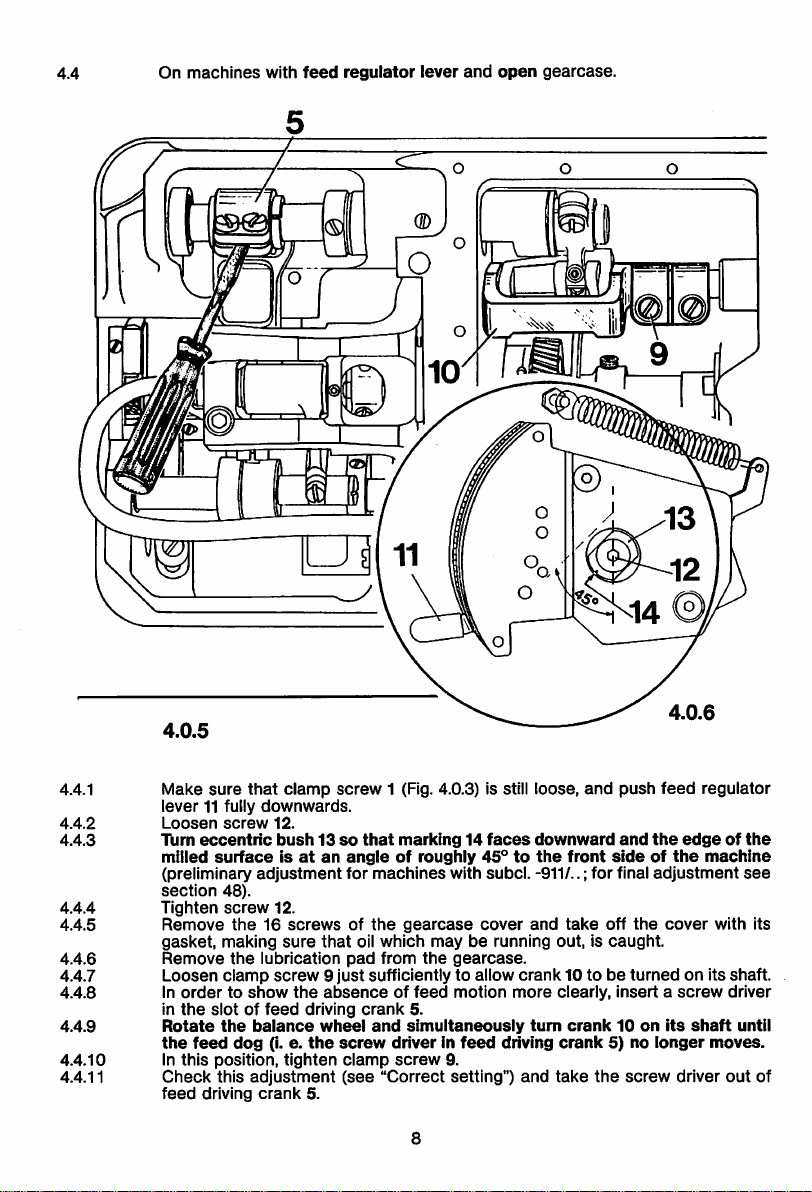
4.4
On
machines
with
feed
regulator
lever
and
open
gearcase.
4.4.1
4.4.2
4.4.3
4.4.4
4.4.5
4.4.6
4.4.7
4.4.8
4.4.9
4.4.10
4.4.11
4.0.5
Make
sure
that
clamp
lever
11 fully
Loosen
Turn
eccentric
milled
(preliminary
section
Tighten
Remove
gasket,
Remove
Loosen
In
ordertoshow
in
the
Rotate
the
feed
In
this
Check
feed
downwards.
screw
12.
surfaceisatanangleofroughly
adjustment
48).
screw
12.
the16screwsofthe
making
the
lubrication
clamp
screw9just
slotoffeed
the
balance
dog
(i. e.
position,
this
adjustment
driving
crank
screw
bush13so
sure
that
the
absenceoffeed
driving
wheel
the
screw
tighten
5.
for
pad
clamp
(see
1 (Fig. 4.0.3) is still loose,
that
marking14faces
machines
gearcase
oil
which
from
45°tothe
with
subcl.
cover
mayberunning out, is
the
gearcase.
sufficiently to allow
motion
crank
5.
and
simultaneously
driverinfeed
screw
"Correct
8
driving
9.
setting")
and
downward
front
-911/..; for final
and
take
off
crank
10 tobeturnedonits
more
clearly,
turn
crank10on
crank
and
take
the
push
feed
and
the
adjustment
the
cover
edgeofthe
sideofthe
caught.
insertascrew
its
5) no
longer
screw
driver
regulator
machine
with its
shaft.
driver
shaft
moves.
out
see
until
of
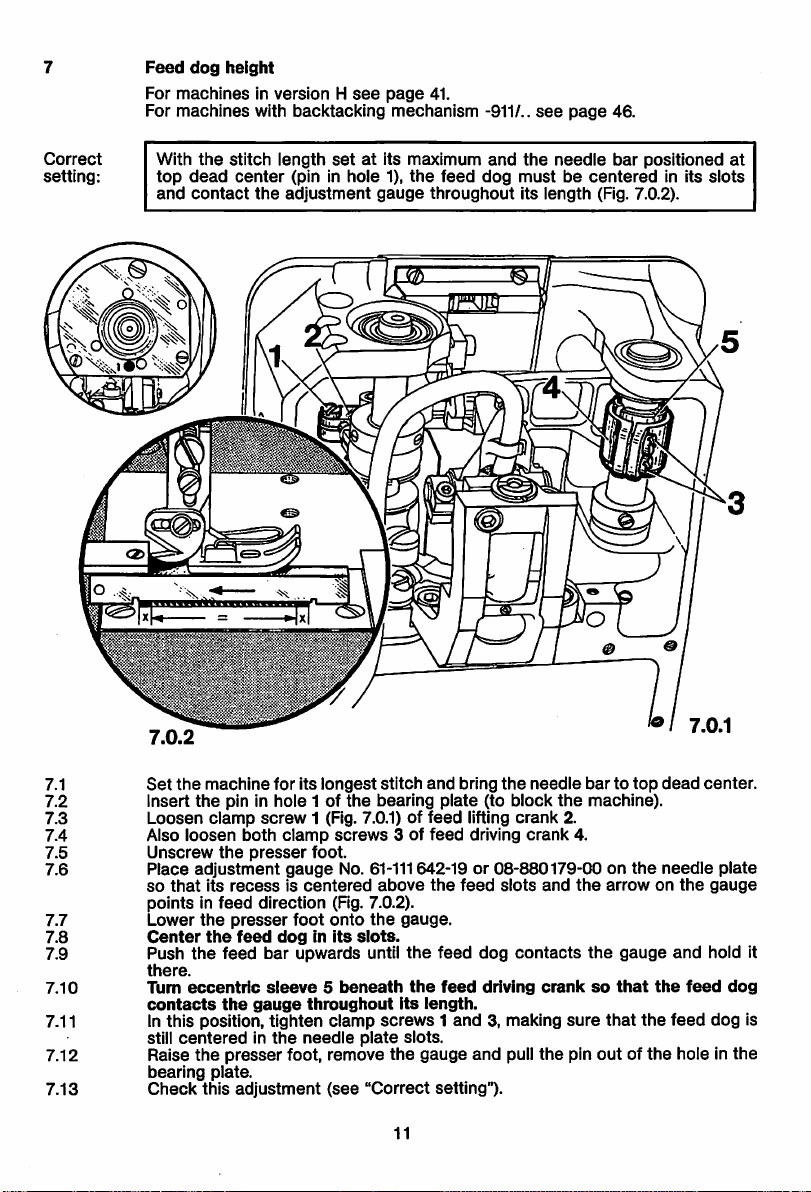
7
Feed
dog
height
For
machinesinversionHsee
For
machines
with
backtacking
page
41.
mechanism
-911/..
see
page
46.
Correct
setting:
With
top
and
7.0.2
the
dead
contact
stitch
center
the
length
setatits maximum
(pin in
adjustment
hole
1),
gauge
the
feed
throughout
and
the
dog
needle
mustbecentered
its
length
bar
positioned
(Fig. 7.0.2).
f
in its
at
slots
7.0.1
7.1
7.2 Insert
7.3
7.4 Also
7.5
7.6
7.7
7.8
7.9 Push
7.10
Set
the
machine
the
Loosen
pin in hole 1 of
clamp
loosen
Unscrew
Place
so
adjustment
that
its
the
recessiscentered
pointsinfeed
Lower
the
Center
there.
Turn
contacts
presser
the
the
feed
eccentric
the
for its
screw
both
clamp
presser
gauge
direction (Fig. 7.0.2).
foot
feed
doginits
bar upwards until
sleeve5beneath
gauge
7.11 In this position, tighten
still
7.12 Raise
7.13
bearing
Check
centeredinthe
the
presser
plate.
this
adjustment
needle
foot, remove
longest
1 (Fig. 7.0.1) of
foot.
the
screws
stitch
bearing
3 of
and
plate
feed
feed
bring
(to block
lifting
driving
the
needle
crank
crank
No. 61-111642-19 or 08-880179-00 on
above
the
feed
slots
and
onto
the
gauge.
siots.
the
feed
dog
contacts
the
feed
driving
throughout
clamp
plate
(see
"Correct
its
length.
screws1and
slots.
the
gauge
setting").
11
and
cranksothat
3, making
pull
the
bartotop
the
2.
4.
the
the
sure
pin
machine).
the
arrowonthe
gauge
that
the
outofthe
dead
needle
and
the
feed
hole in
feed
center.
plate
gauge
hold it
dog
dog
the
is
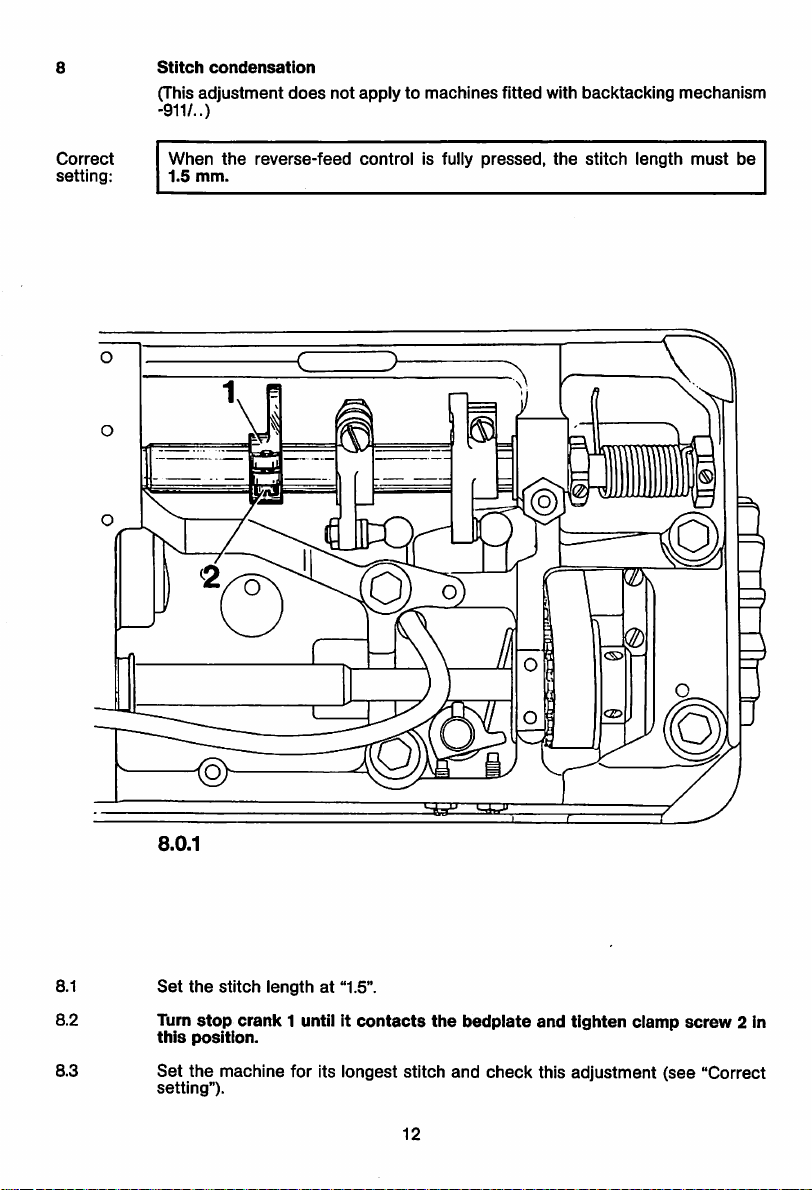
stitch
(This
-911/..)
condensation
adjustment
does
not
applytomachines
fitted
with
backtacking
mechanism
Correct
setting:
When
1.5
mm.
the
reverse-feed
control
is fully
pressed,
©
the
stitch
'VW
length
mum
Q)
must
be
8.0.1
8.1
Set
8.2 Turn
this
8.3
Set
setting").
the
stitch
lengthat"1.5".
stop
crank
position.
1 until it
the
machine for Its longest stitch
contacts
the
bedplate
and
12
check
and
tighten
clamp
this adjustment
(see
screw
"Correct
2 in

11
Looper
For
heightonmachines
machines
in version H
without
see
page
subcl.
43.
-900/..
For machines with backtacking mechanism -911/..
see
page
48.
Correct
setting:
When
the
looper
holder
of 0.7 mm
needle
On
front
between
plate on single-needle machines (Fig.
two-needle
looper
machines,
and
is in its vertical position,
the
highest
the
there
needle
pointofthe
mustbea
plate.
there
and
mustbea
the
looper
11.0.2).
clearanceof1.0
clearance
undersideofthe
mm
between
the
11.1
11.2
11.3
11.4
11.5
11.6
Remove
Place
the
Turn
Loosen
Turn
highest
of
In
Continuedonnext
the
presser
balance
eccentric
1.0
this
bed
slide,
needle
foot
wheel
clamp
pointofthe
mm
between
position,
screw1and
bearing
tighten
cover
plate
onto
Inposition
the
until
stud3until
looper
front
clamp
page.
plate,
needle
the
screw
and
looper
looper
needle
plate
again
and
plate.
holderisvertical.
2 of
eccentric
there
the
undersideofthe
and
needle
screw1and
15
and
feed
dog.
operate
is a
the
bearing
clearanceof0.7
needle
plateontwo-needle
screw
2.
presser
stud
plate
bar
lifter to lower
3.
mm
between
(or a
clearance
machines).
the

11.7 Ifa
proceedasfollows;
clearance
of 0.7 mm (or 1.0mm on
two-needle
machines)
cannotbeobtained,
10.7.1 Raise
11.7.2
11.7.3 Fitanappropriate
11.7.4
11.7.5
11.7.6
11.8
11.9
Loosen
spacer).
the
looper
Set
the
liminary
Replace
foot
onto
Check
between
when
If
necessary,
Check
the
presser
clamp
into
looper
adjustment)
the
needle
the
that
there
the
the
looper
this
adjustment
screw
needle
highest
repeat
foot
and
remove
4 in
looper
spacer
looper
blade
(see
holder5againasfarasit will go.
roughly parallel to
and
tighten
plate
and
the
holder5and
inside
clamp
operate
needle
front
the
plate.
is a
clearance
pointofthe
holder
is in its vertical position.
steps
(see
11.3
"Correct
of 0.7
looper
through
mm
11.6.
setting").
plate.
take
off
the
cover)onthe
the
front
screw
4.
presser
(or 1.0 mmontwo-needle
and
the
looper
edgeofthe
bar
liftertolower
undersideofthe
looper
(do
neck
and
bedplate
the
machines)
needie
not
push
(pre
presser
plate
lose
16