
Important
note:
ThisServiceManual applies also to the Raff 441-0 and 442-0. Deviations in the illustrations do not
affect
the
adjustment of the machines.
The
Sen/ice
Manual is
based
on a two-needle machine.
When adjusting a single-needle machine,
simply
ignore the adjustment procedure for the left
needle and the left sewing hook. A separate Service
Manual
is available for adjusting the
Pfaff
441-R
(0)-705/03: -755/03.
Tools,
gauges
and
other
items required for adjusting
Raff
machines
442-R, 441-0
and
442-0
1
setofscrewdrivers
with
blades
from2to10mm
wide
1
set
ofwrencheswithopeningsfrom 7 to 14 mm wide
1
set
of alien keysfrom 2 to 6 mm
1 feed dog
gauge,
part No.
91-129995-05
1 adjusting
gauge,
part No. 91
-129573-91
1 C-clamp,
part
No.
880137/00
1
metal
rule
1 wrapper of needles: system 134 (for7 mm fabric clearance)
system
134-35
(for 9 mm fabric clearance)
2 strips of white
paper
Sewing thread and testing material
Technical
data
Maximumsewing
speed:
5000 s.p.m.
Balance
wheel:
65
mm
eff.
dia.
Drive:
clutchmotor0,550 kW(% HP)
lever-operated Stop motor 0,550 kW(% HP)
electronic-stop-motor 0,550 kW(%HP)
Needle system: 134 (for7 mm fabric clearance)
134-35
(for 9 mm fabric
clearance)
Fabric
clearance:7or9mm
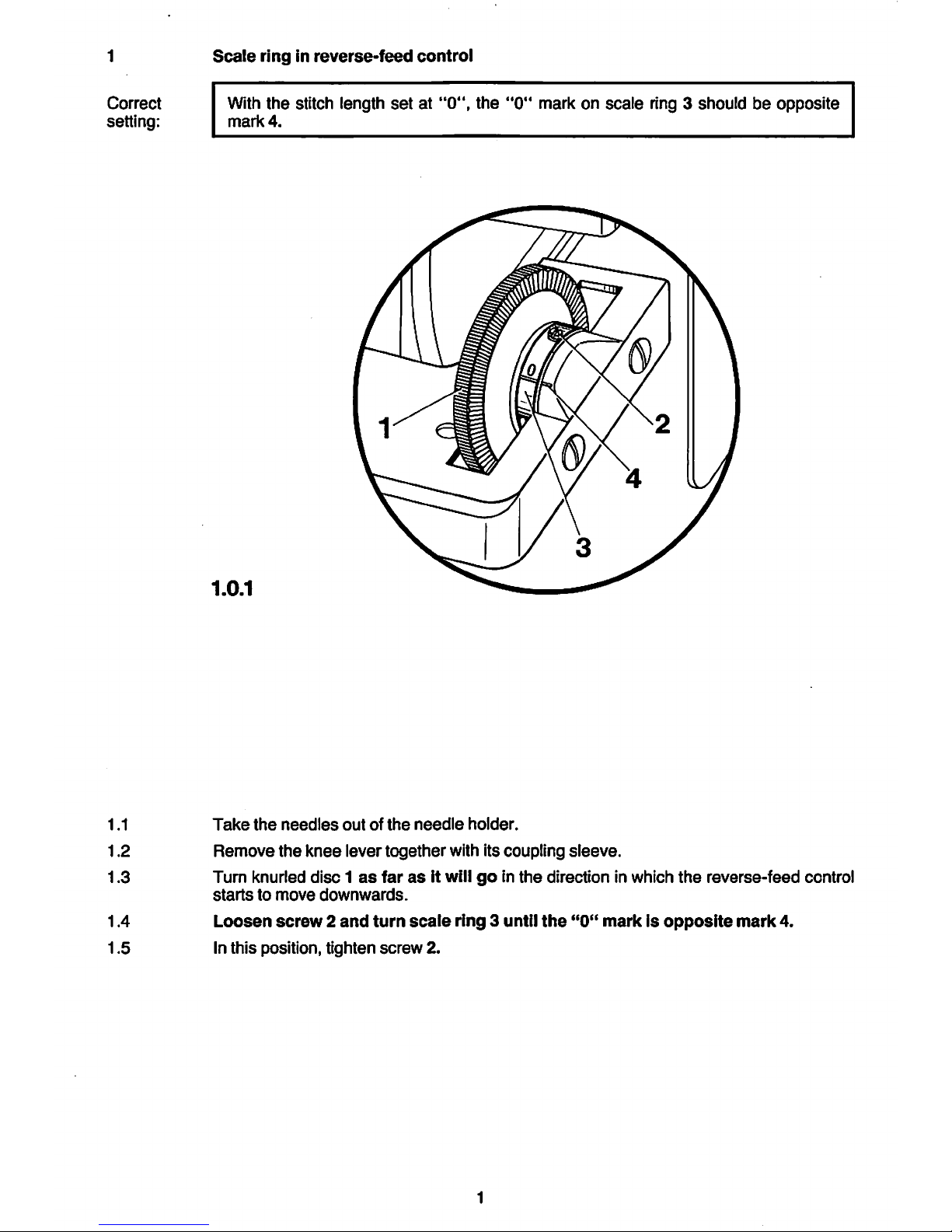
Correct
setting:
Scale
ringinreverse-feed
control
With the stitch length
setat"0",
the
"0"
mark on scale ring 3 should be opposite
mark
4.
1.0.1
1.1
Take
the
needles
outofthe
needle
holder.
1.2
Remove
the
knee
levertogether with its coupling
sleeve.
1.3
Tum
knurled
disc1as
farasit willgoin
the
direction in which
the
reverse-feed
control
starts
to
move
downwards.
1.4
Loosen
screw2and
turn
scale
ring
3 until
the
"0"
markIsopposite
mark
4.
1.5
Inthis position, tighten
screw
2.
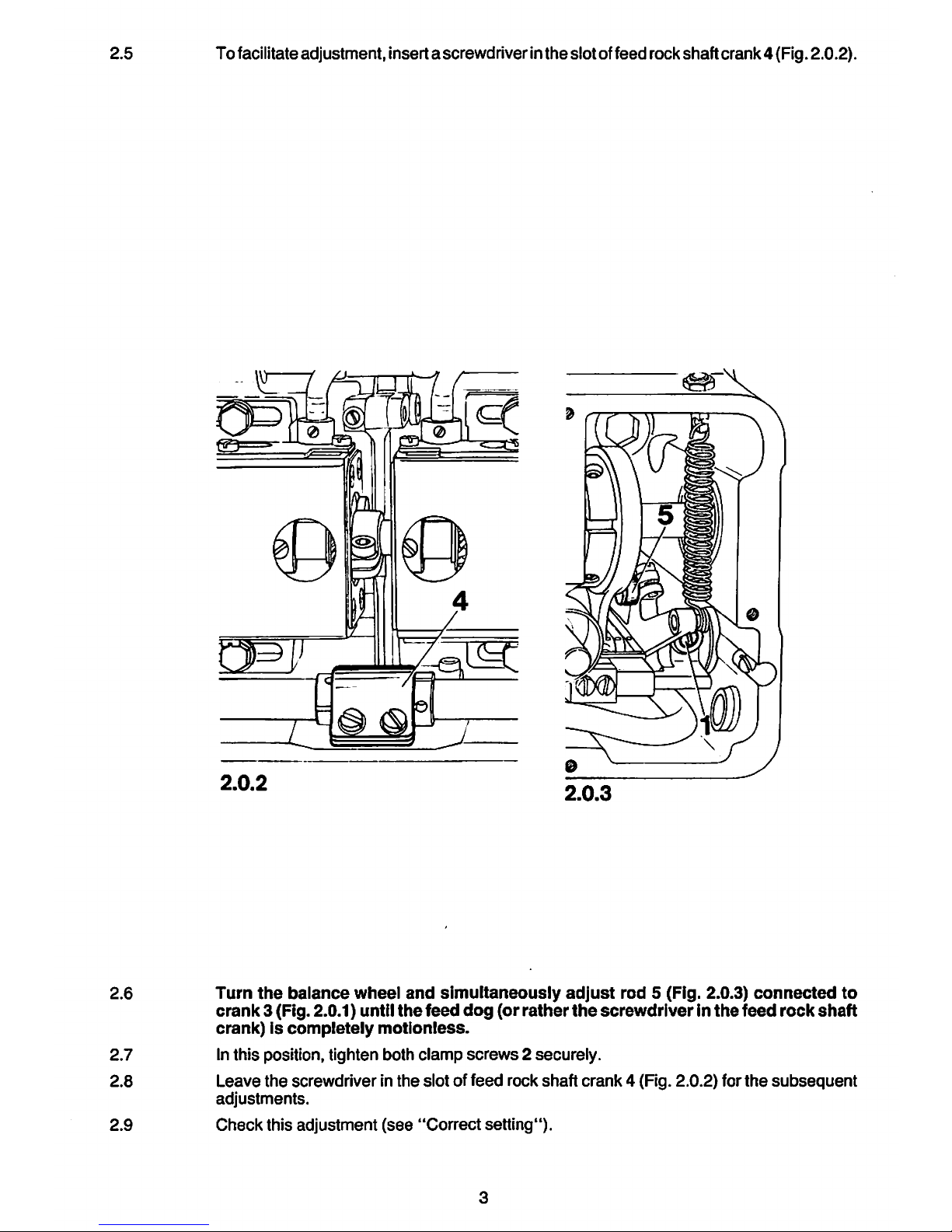
2.5
Tofacilitateadjustment, inserta screwdriverinthe slot offeedrockshaftcrank4 (Fig. 2.0.2).
2.0.2
2.0.3
2.6
Turn
the
balance
wheel
and
simultaneously
adjust
rod
5 (Fig. 2.0.3)
connected
to
crank
3 (Fig. 2.0.1) until
the
feed
dog
(or
rather
the
screwdriverinthe
feed
rock
shaft
crank)Iscompletely
motionless.
2.7
Inthis position, tighten both
clamp
screws2securely.
2.8 Leave the screwdriver in the slot of
feed
rock shaftcrank 4 (Fig. 2.0.2) for
the
subsequent
adjustments.
2.9
Check
this
adjustment
(see
"Correct
setting").
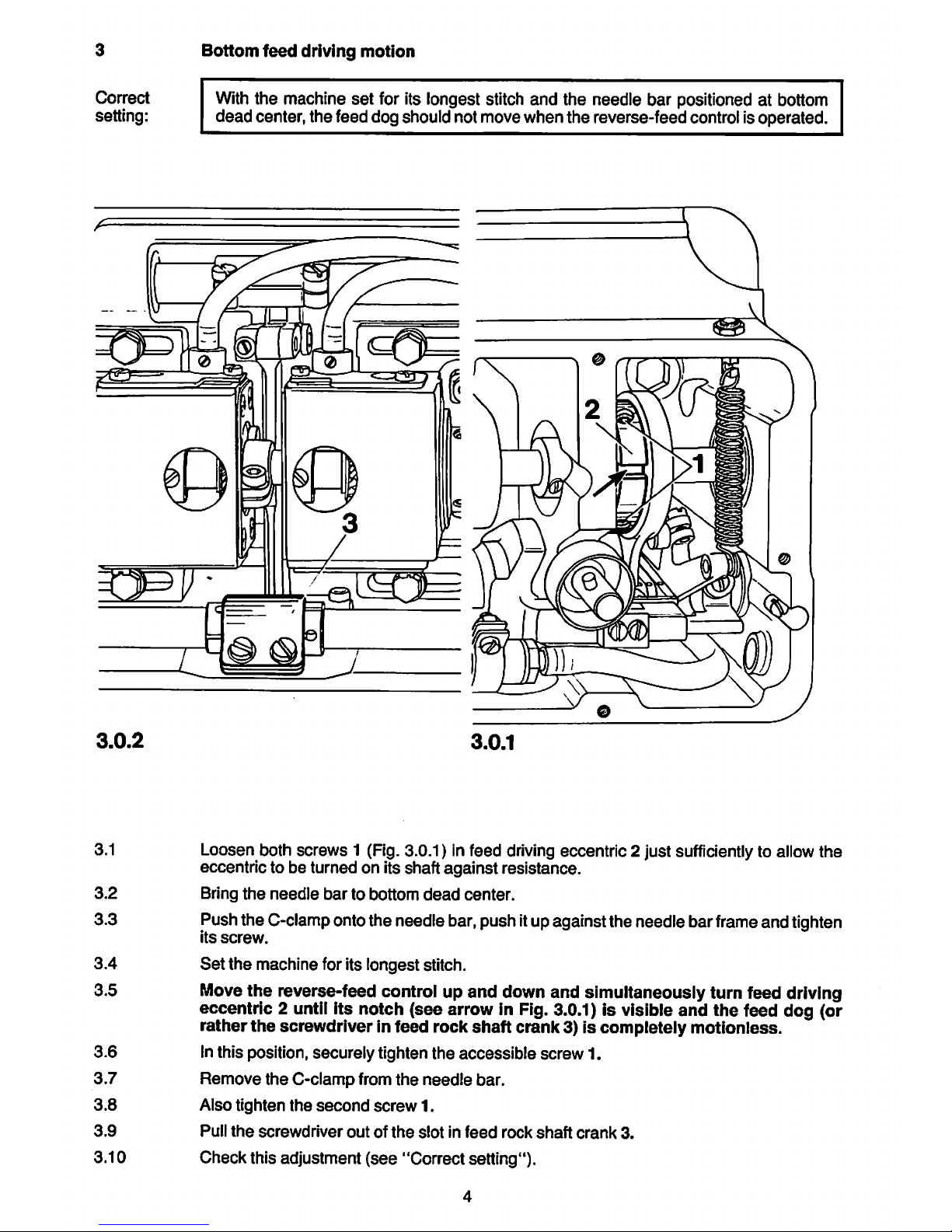
Correct
setting:
3.0.2
Bottom
feed
driving
motion
With the machine
set
for its longest stitch and the needle bar positioned at bottom
deadcenter, the feed dog should not move when the reverse-feedcontrol is operated.
J
3.0.1
3.1 Loosen both screws 1 (Fig. 3.0.1) In feed drivingeccentric 2 just sufficientlyto allow the
eccentric to be turned on its shaft against resistance.
3.2
Bring
the
needle
bar
to bottom
dead
center.
3.3 Pushthe C-clampontotheneedlebar,push itupagainsttheneedlebarframeandtighten
its
screw.
3.4
Set
the
machine for its longest stitch.
3.5 Movethe reverse-feed control up and down and simultaneously turn feed driving
eccentric 2 until its notch (see arrow in Fig.3.0.1) is visible and the feed dog (or
rather
the
screwdriverin feed rock
shaft
crank3) is completely motionless.
3.6 Inthis position, securely tighten the accessible screw 1.
3.7
Remove
the
C-clamp
from
the
needle
bar.
3.8
Also tighten
the
second
screw
1.
3.9
Pull
the
screwdriver
outofthe
slotinfeed
rock
shaft
crank
3.
3.10 Check this adjustment (see "Correct setting").
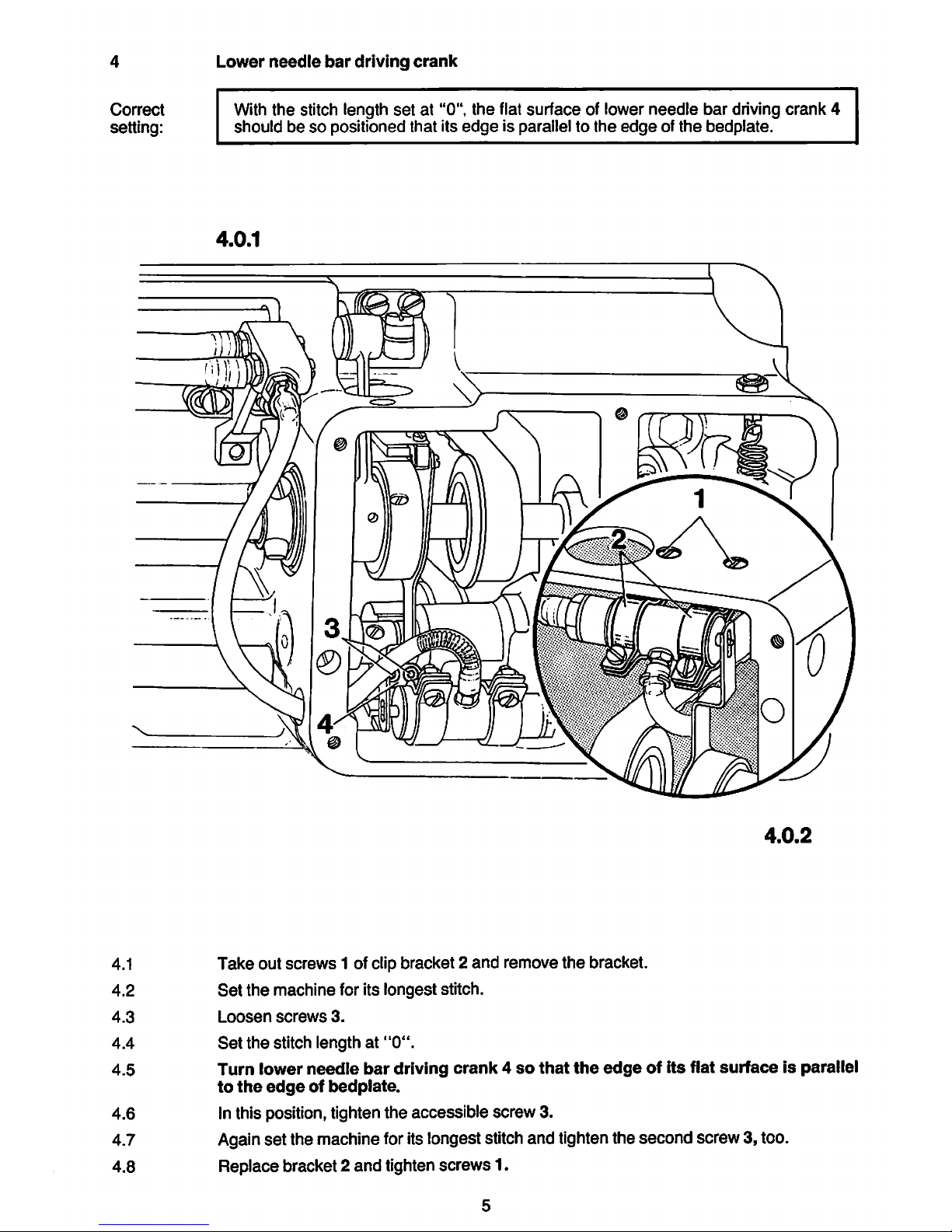
Correct
setting:
Lower
needle
bar
driving
crank
With the stitch length
set
at "0", the flat surface of lower needle bar driving crank 4
shouldbeso
positioned that its
edge
is parallel to
the
edgeofthe
bedplate.
4.0.1
4.0.2
4.1
Take
out
screws
1 of clip bracket 2
and
remove
the
bracket.
4.2
Set
the
machine for its longeststitch.
4.3
Loosen
screws
3.
4.4
Set
the
stitch length at
"0".
4.5 Turn lower
needle
bar
driving
crank4so
that
the
edge
of its flat
surface
is parallel
to
the
edgeofbedplate.
4.6 Inthis position,tightenthe accessible screw 3.
4.7 Againset the machineforitslongeststitchand tightenthe second screw3, too.
4.8 Replace bracket 2
and
tighten
screws
1.

Correct
setting:
5.1
5.2
5.3
5.4
Counter-balance
With
the machine set for its longest stitch, counter-balance 2 should move freely
when
the reverse-feed control is operated.
5.0.1
Set
the
machine for its longest stitch.
Makesure screw 1 ofcounter-balance 2 is loose (Fig.5.0.1), move the latteras faras it
will
go, turning it inthe direction indicated by an arrow.
Turnthe counter-balancebackbyabt.1 mmagain,and inthis
position
tighten
screw1.
Check this adjustment
(see
"Correct setting").
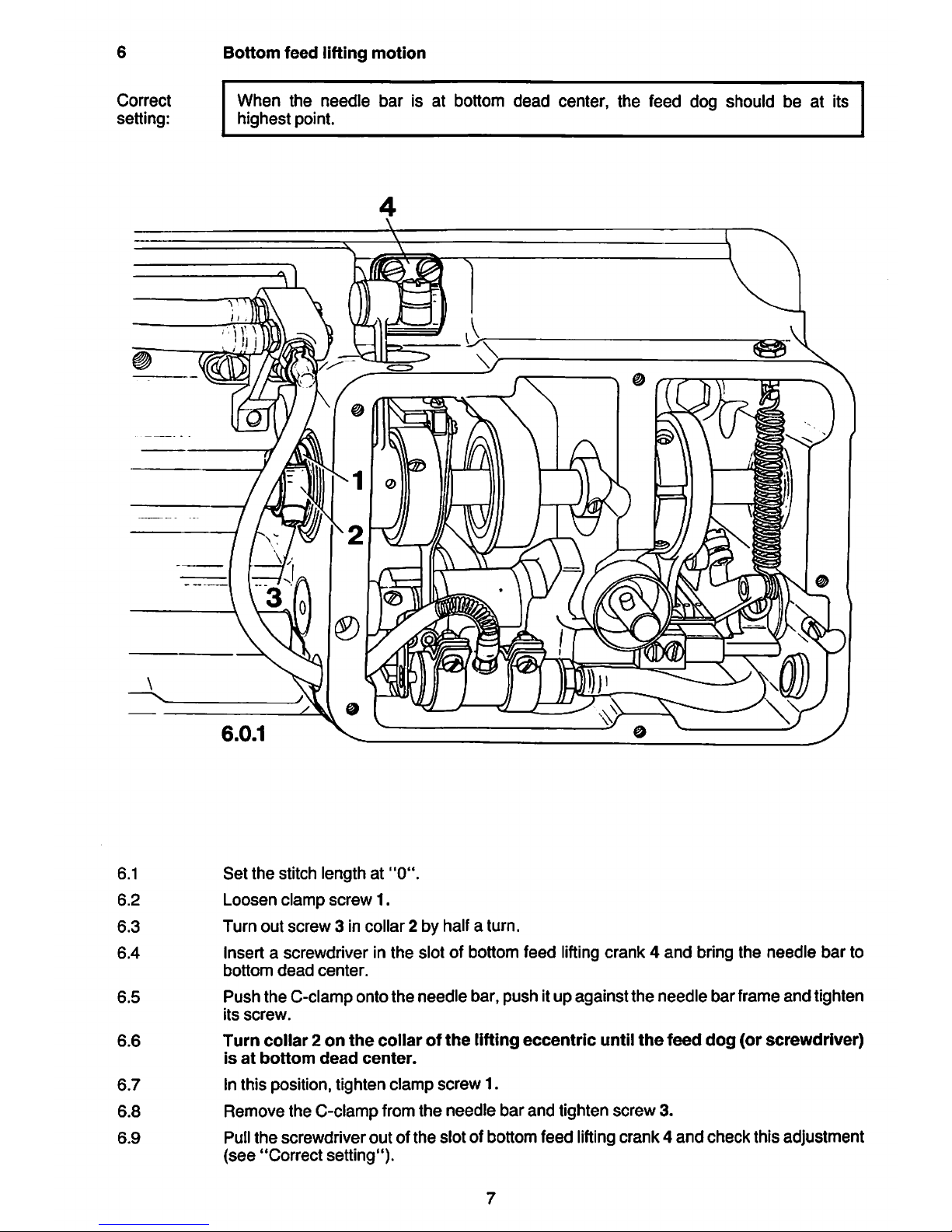
Correct
setting:
6.1
6.2
6.3
6.4
6.5
6.6
6.7
6.8
6.9
Bottom
feed
lifting
motion
When the needle bar is at bottom
dead
center, the feed dog should be at its
highest
point.
n
W
Set
the
stitch length at
"0".
Loosen
clamp
screw
1.
Turn out
screw
3 incollar 2 by half a turn.
Insert a screwdriver in
the
slot of bottom
feed
lifting
crank4and
bring
the
needle
bar
to
bottom
dead
center.
Push
the C-clamponto
the
needle
bar, push itup
against
the
needle
bar
frame
and
tighten
its
screw.
Turn
coiiar2on
the
collarofthe
lifting
eccentric
until
the
feed
dog
(or
screwdriver)
isatbottom
dead
center.
Inthis position, tighten clamp
screw
1.
Remove the C-clamp from
the
needle
bar
and
tighten
screw
3.
Pull
the
screwdriver
outofthe
slot
of bottom
feed
lifting
crank4and
check
this
adjustment
(see
"Correct
setting").

Correct
setting:
7.1
7.2
7.3
7.4
7.5
7.6
7.7
Note:
Clearance
between
presser
foot
and
needle
plate
Withpresser bar lifter1 raised, there shouid be a ciearance of7.0 mm (needie system
134) or 9.0 mm (needle system 134-35) between presserfootand needle plate.
7mm(9mm)
f
Take
out
the
two
screwsofthe
face
cover
and
remove
the
latter.
Unscrew
the
cover
on
the
backofthe
machine
arm.
Raise
presser
bar lifter1 and screw on the
presser
foot.
Loosen both
screws
2 in the
presser
bar collar.
Push the 7-mm (or9-mm) thickpart ofthe gauge under the presserfootso that itsrecess
faces downwards (Fig. 7.0.1).
Push the presser foot downonto the gauge and adjustItlaterallysothat its
sides
are
parallel to
the
edgesofthe
needle
plate
slot.
Inthis position, tighten both screws 2.
Adjust
the presser footpressure by
turning
regulating
screw4
(Fig.
9.0.1)inoroutwhen
you
make
a sewing test.
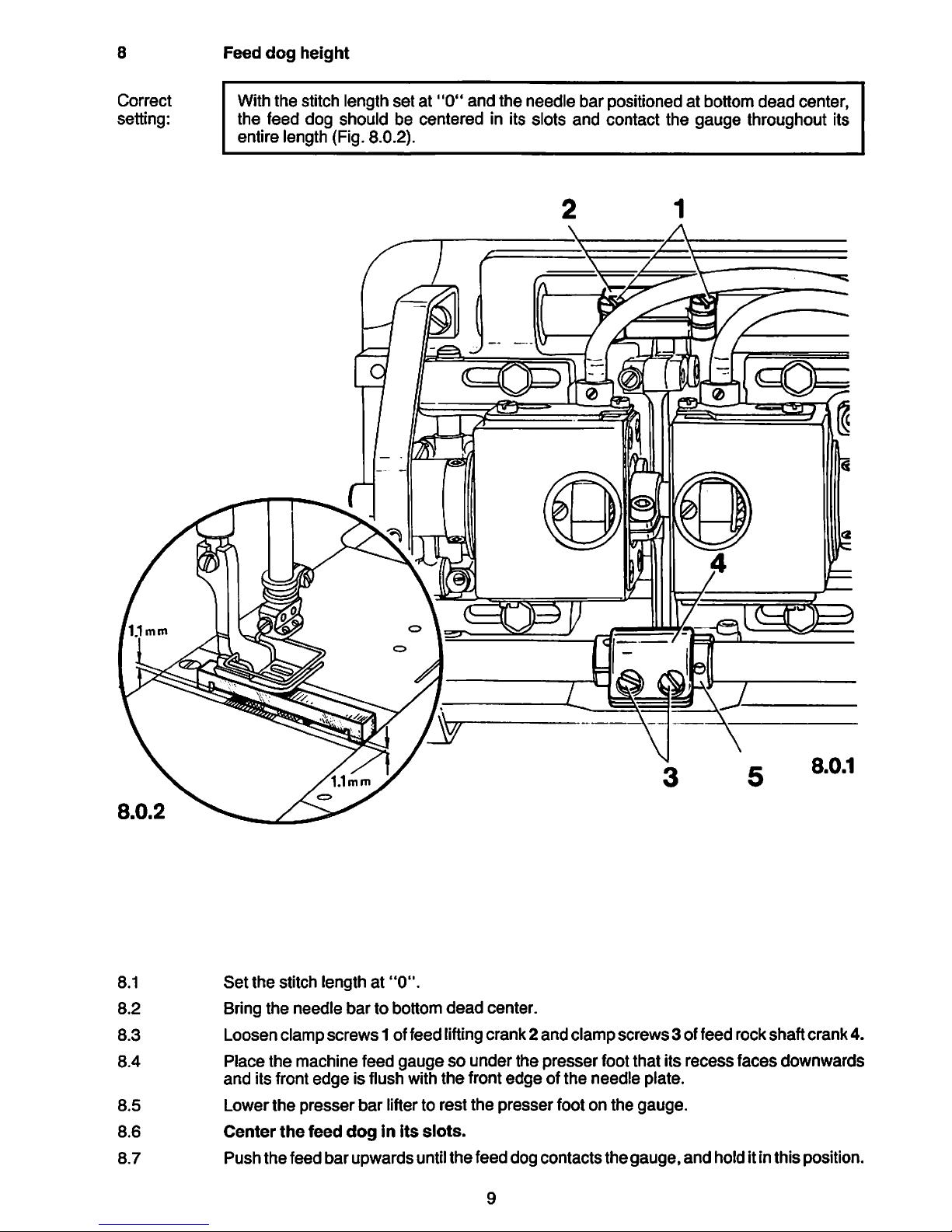
Correct
setting:
Feed
dog
height
Withthe stitch length
setat"0"
and
the
needle
bar
positioned at bottom
dead
center,
the feed dog should be centered in its slots and contact the gauge throughout its
entire length (Fig. 8.0.2).
2
8.1
Set
the
stitch length at
"0".
8.2
Bring
the
needle
bar
to bottom
dead
center.
8.3 Loosenclamp
screws
1 offeed liftingcrank2
and
clamp
screws
3 offeed rock shaftcrank4.
8.4
Place
the
machine feed
gaugesounder
the
presser
foot that its
recess
faces
downwards
and
its front
edge
is flush with
the
front
edgeofthe
needle
plate.
8.5
Lower
the
presser
bar
lifterto
rest
the
presser
foot on
the
gauge.
8.6
Center
the
feed
doginits
slots.
8.7
Push
the
feed
bar
upwardsuntil
the
feed dog
contacts
the
gauge,
and
hold itinthis position.