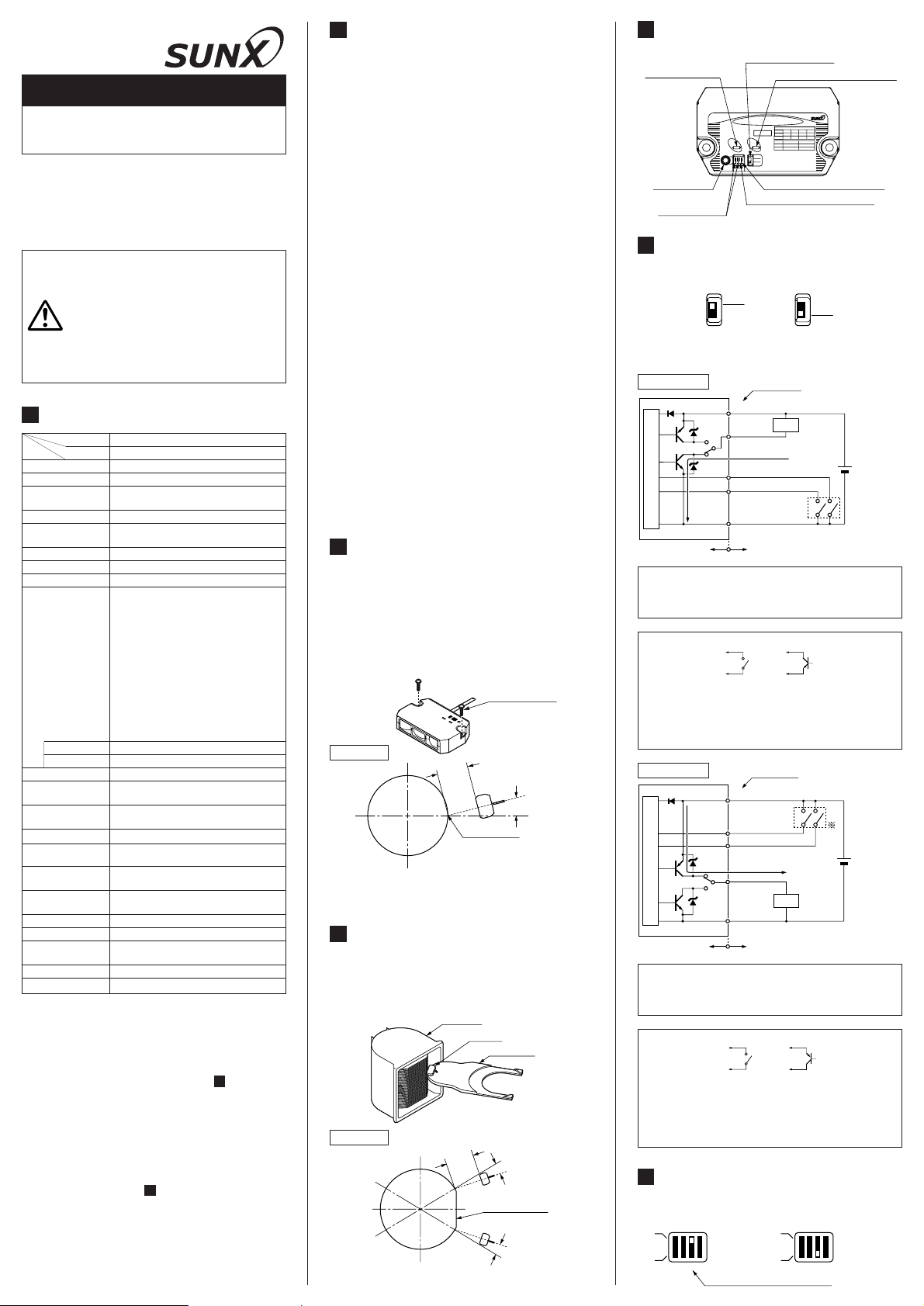
INSTRUCTION MANUAL
LED Beam Reflective Type Wafer Mapping Sensor
M-DW1
Thank you very much for using SUNX sensors.
Please read this Instruction Manual carefully
and thoroughly for the correct and optimum use
of this sensor. Kindly keep this manual in a
convenient place for quick reference.
䢇 Make sure to carry out the wiring in the power
supply off condition.
䢇
Take care that wrong wiring will damage the sensor.
䢇
Verify that the supply voltage variation is within the rating.
䢇
If power is supplied from a commercial switching
regulator, ensure that the frame ground (F.G.) terminal
of the power supply is connected to an actual ground.
䢇 In case noise generating equipment (switching
regulator, inverter motor, etc.) is used in the vicinity
of this product, connect the frame ground (F.G.)
terminal of the equipment to an actual ground.
䢇 Do not use during the initial transient time (0.5 sec.)
after the power supply is switched on.
䢇 Extension up to total 10m is possible with 0.15mm
2
,
or more, cable. However, in order to reduce noise,
make the wiring as short as possible.
䢇
Do not run the wires together with high-voltage lines
or power lines or put them in the same raceway.
This can cause malfunction due to induction.
䢇 Take care that the sensor is not directly exposed to
fluorescent light from a rapid-starter lamp or a high
frequency lighting device, as it may affect the
sensing performance.
䢇 Avoid dust, dirt, and steam.
䢇 Take care that the sensor does not come in direct
contact with water, oil, grease, or organic solvents,
such as, thinner, etc.
䢇 Take care that dust, etc., does not collect on the
sensing surfaces, as it may result in malfunction.
Should it collect, clean the sensing surfaces by
blowing air or wiping them gently with a soft cloth.
䢇 Make sure to use an isolation transformer for the
DC power supply. If an auto-transformer (single
winding transformer) is used, this product or the
power supply may get damaged.
䢇 In case a surge is generated in the used power
supply, connect a surge absorber to the supply and
absorb the surge.
䢇
Set the distance between the sensor detection surface
and the wafer edge to be 45mm and mount the sensor
so that sensing is done at an angle of 12.5˚ with
respect to the wafer.
Mount using M4 (length 16mm) screws. The tightening
torque should be 1.2N•m or less. Further, although the
sensing distance may change due to variation in the
wafer position (wafer protrusion, orientation flat position,
etc.), if it is within
5
mm, stable sensing is possible.
䢇
This product is not a safety sensor. Its
use is not intended or designed to
protect life and prevent body injury or
property damage from dangerous
parts of machinery. It is a normal
object detection sensor.
䢇
In case the product may be subjected
to electrostatic discharge, make sure
to ground the stainless case.
3
MOUNTING
5
PART DESCRIPTION
1
SPECIFICATIONS
2
CAUTIONS
Notes: 1) In case of 8 inch or less wafers, the wafer pitch,
orientation flat or the surface condition may affect the
sensing.
Notes: 2) Polished wafers, etc., which have a sharp edge
cannot be detected since they do not reflect the light
in the light receiving direction.
Notes: 3) Since the position of the orientation flat may vary by
Ⳳ20˚ due to its rotation, refer to DETECTING
WAFER HAVING ORIENTATION FLAT for detection
of a wafer having an orientation flat.
Notes: 4) This is the pitch of an 8 inch wafer near its center
region when it is inserted in an inclined fashion. When
detecting a wafer having an orientation flat, the wafer
pitch becomes still smaller when sensing at positions
which avoid the orientation flat. In this case, the
sensing signal cannot be resolved and it becomes a
continuous, broad signal.
For details, refer to SENSING SIGNAL.
13
4
Cassette
Sensor
Robot arm
45mm
Mounting angle
12.5˚
Sensor axis
Spot position
Wafer
center axis
Orientation flat
Detection
2
Detection
1
4
5
m
m
12.5
ⴗ
12.5
ⴗ
Note: If the wafer center axis and the sensor axis lie along a
straight line, detection is not possible. Always mount the
sensor at an angle to the wafer.
䢇
When detecting a wafer having an orientation flat,
mount the sensor so that a portion other than the
orientation flat is detected. Further, arrange to detect
the wafer from two different angles by moving the
robot arm, etc., and OR the signal so obtained.
6
I/O CIRCUIT DIAGRAMS
Brown : 12 to 24V DC
Blue : 0V
Black : Out
Pink : Light emission control
Violet : Ext. sensitivity selection
LowMidHighMaxSW
LLLLHHH
H
SW
PNP
NPN
OFDNON
D-ONL-ON
Sensitivity SW
LH
4
3
2
1
M-DW1
Wafer Mapping Sensor
STB OUT
SET 1 2 3 4
L
H
MADE IN JAPAN
Timer operation mode switch
Output operation mode switch
Output setting switch
Operation indicator (Orange)
Sensitivity
selection switch
Sensitivity
setting button
Stability indicator
(Green)
Users' circuitInternal circuit
Color code
(Brown)
ⳭV
(Black) Output
100mA max.
12 to 24V DC
Ⳳ10%
(Pink) Ext. light
emission control input
(Violet) Ext. sensitivity selection input
(Blue) 0V
ZD2
D
Tr2
ZD1
Tr1
Sensor circuit
Load
1
Ⳮ
ⳮ
Symbols...D: Reverse supply polarity protection diode
Z
D1, ZD2: Surge absorption zener diode
Tr
1: NPN output transistor
Tr
2: PNP output transistor
Non-voltage contact or PNP open-collector transistor
• External emission control input
0 to 3V, or 9V to
ⳭV (26.4V max.): Emission halted
Open, or 4 to 8V: Emission
• External sensitivity selection input
0 to 3V, or 9V to
ⳭV (26.4V max.): Input ON
Open, or 4 to 8V: Input OFF
Non-voltage contact or NPN open-collector transistor
• External emission control input
0 to 3V, or 9V to
ⳭV (26.4V max.): Emission halted
Open, or 4 to 8V: Emission
• External sensitivity selection input
0 to 3V, or 9V to
ⳭV (26.4V max.): Input ON
Open, or 4 to 8V: Input OFF
Symbols...D: Reverse supply polarity protection diode
Z
D1, ZD2: Surge absorption zener diode
Tr
1: NPN output transistor
Tr
2: PNP output transistor
䢇 The output can be selected as NPN output or PNP
output by the output setting switch.
4
DETECTING WAFER HAVING ORIENTATION FLAT
m1
m1
Top-view
Top-view
NPN output
PNP output
7
OUTPUT OPERATION
䢇 The output operation can be set either Light-ON or
Dark-ON by the output operation mode switch.
: Light-ON : Dark-ON
Output operation mode switch
L
H
L
H
1 2 3 4 1 2 3 4
Designation
Item
Model No.
Center measuring distance
Sensing object
Detectable surface
Sensing angle
Wafer pitch
Suitable cassette
Supply voltage
Current consumption
Output
Output operation
Short-circuit protection
Response time
External light
emission control input
External sensitivity
selection input
Operation indicator
Stability indicator
Timer function
Ambient
temperature
Ambient humidity
Emitting element
Material
Cable
Weight
LED beam reflective type wafer mapping sensor
M-DW1
45mm
3 inch or larger semiconductor wafer (Note 1)
Surface having a side edge which reflects
light in the light receiving direction (Note 2)
12.5˚Ⳳ5˚ (Note 3)
Separate sensing is possible at normal
sensitivity for 3mm pitch or more (Note 4)
SEMI standard FOUP cassette / open cassette
12 to 24V DCⳲ10% Ripple P-P 10% or less
65mA or less
NPN output / PNP output, selectable with
output selection switch
<NPN output>
NPN open-collector transistor
• Maximum sink current: 100mA
•
Applied voltage: 30V DC or less (between output and 0V)
•
Residual voltage: 1V or less (at 100mA sink current)
0.4V or less (at 16mA sink current)
<PNP output>
PNP open-collector transistor
• Maximum source current: 100mA
•
Applied voltage: 30V DC or less (between output and +V)
•
Residual voltage: 1V or less (at 100mA source current)
0.4V or less (at 16mA source current)
Light-ON / Dark-ON, selectable by switch
Incorporated (restored automatically)
500!s or less
0 to 3V, or 9V toⳭV (26.4V max.): Emission halted
Open, or 4 to 8V: Emission
0 to 3V, or 9V toⳭV (26.4V max.): Input ON
Open, or 4 to 8V: Input OFF
Orange LED (lights up when the output is ON)
Green LED (lights up under stable light
received condition or stable dark condition)
Approx. 2ms fixed OFF-delay timer,
switchable either effective or ineffective
0 to
Ⳮ55˚C (No dew condensation)
Storage:
ⳮ10 toⳭ70˚C
35 to 85% RH, Storage: 35 to 85% RH
LED (modulated)
Enclosure: ABS / SUS301
Lens: Acrylic
0.15 mm25-core cabtyre cable, 300mm long
75g approx.
Note: Make sure to operate the output setting switch in the
power supply off condition. If it is operated with power on,
it may get damaged.
D
ZD2
Tr2
ZD1
Tr1
Sensor circuit
Color code
(Brown)ⳭV
Load
(Black) Output
100mA max.
(Pink) Ext. light emission control input
(Violet) Ext. sensitivity selection input
(Blue) 0V
Users' circuitInternal circuit
or
Ⳮ
ⳮ
m1
12 to 24V DC
Ⳳ10%
or
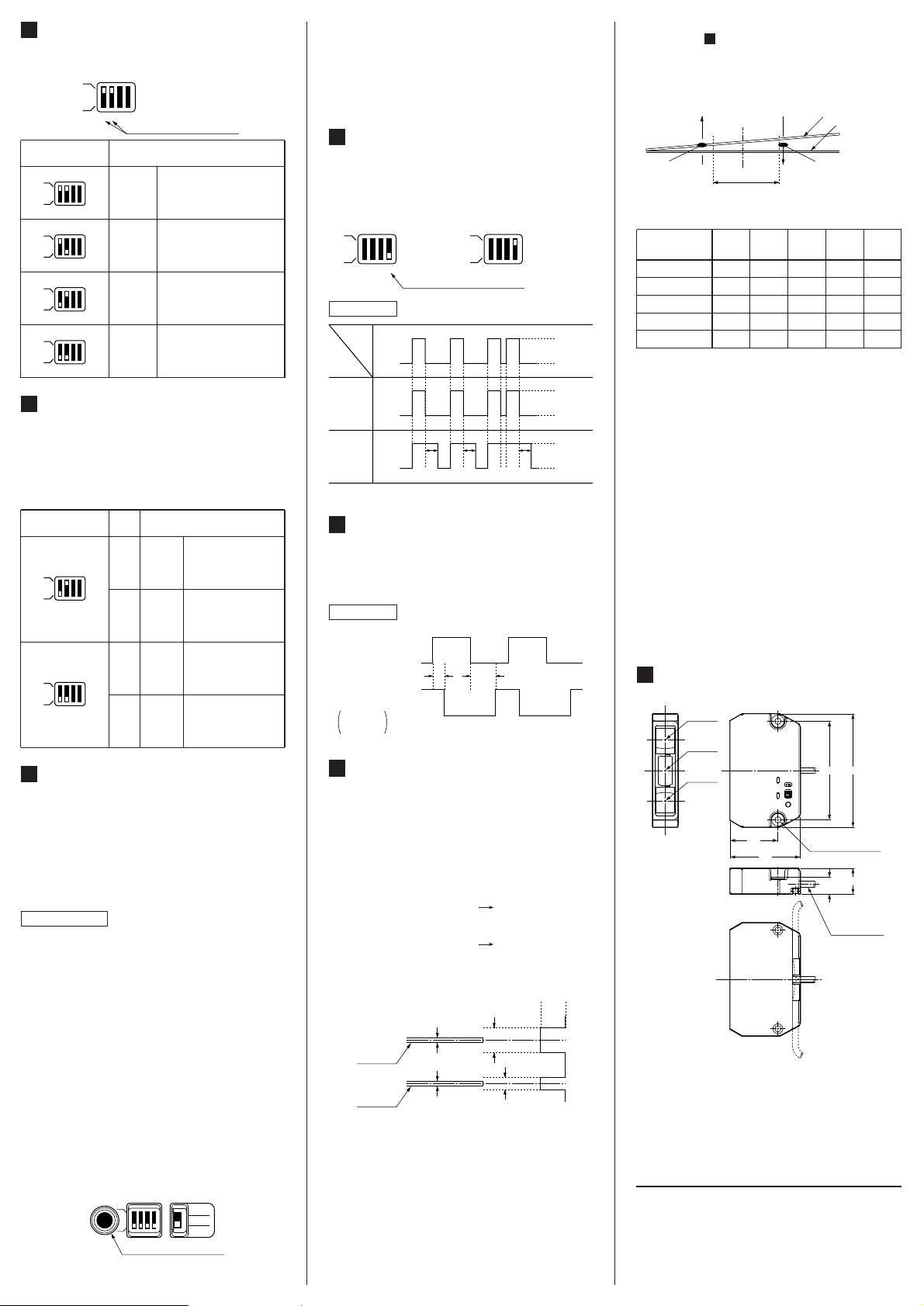
䢇 Sensing signal width
• The sensing signal which is output from the sensor
is as follows
1
The sensing signal has a width larger than the
thickness of the wafer.
2
The signal width also varies with the reflectivity of
the sensing edge.
High reflectivity (polish, aluminum film, etc.): Large signal width
Example:
Low reflectivity (nitride or oxide film processed): Small signal width
Example:
3
The signal width also changes with the sensing
distance or the sensing angle.
Maximum
sensitivity
(MAX)
Medium
sensitivity
(MID)
High
sensitivity
(HIGH)
Low
sensitivity
(LOW)
ON
OFF
ON
OFF
14
DIMENSIONS (Unit: mm)
13
SENSING SIGNAL
12
LIGHT EMISSION CONTROL FUNCTION
11
TIMER FUNCTION
9
External sensitivity selection input
8
SENSITIVITY SELECTION SETTING
10
SENSITIVITY SETTING
䢇
Although this sensor has an optical system whitch makes
it difficult for the background to affect the detection, the
background may have an effect when detecting small
diameter wafers. Hence, if the background gets detected,
or the stability indicator (green) lights off when the
cassette has no wafers, sensitivity setting should be
done so that the background does not have an effect.
However, the sensitivity reduces when sensitivity
setting is done.
䢇 Sensitivity setting is done when the background
affects the detection.
Press the sensitivity setting button in the actual
environment where the sensor is to be used (place
at which the background has an effect), but without
any wafers being present.
䢇
The sensitivity is set at the time the sensitivity setting
button is released. After the sensitivity setting, the
output once turns into the detection state. If the
sensitivity setting has been successfully done, the
output turns to the non-detection state after 25ms
approx. and the sensitivity is set so that the
background does not have an effect.
In case the output remains in the detection state,
since this is a condition in which detection cannot be
done, readjust the sensitivity selection switch. In this
case, set the sensitivity selection switch to one level
higher sensitivity than the present sensitivity level.
However, if the sensitivity selection switch is already
at maximum sensitivity (MAX), move the background
further away.
䢇
If sensitivity setting is done with nothing in the
background, the sensitivity returns to the initial value.
䢇
Since the sensitivity is stored in an EEPROM when the
sensitivity setting button is pressed, the setting need
not be repeated when the power is switched on again.
However, note that the EEPROM has a lifetime and its
guaranteed life is 100,000 write operation cycles.
䢇
Sensitivity can be selected from four levels by appropriate setting of the sensitivity selection switch (2 bit).
䢇 The external sensitivity selection input (violet)
becomes ON when it is connected to 0 to 3V, or 9V
to
ⳭV (26.4V max.), and becomes OFF when it is
kept open or connected to 4 to 8V.
䢇 If the sensitivity is selected with the external
sensitivity selection input, set the sensitivity
selection switch as shown in the table below.
䢇 Using the timer operation mode switch, it is possi-
ble to select an approx. 2ms fixed OFF-delay timer.
Since the output is extended by a fixed period, it is
useful when the connected device has a slow
response time.
䢇 Light emission is halted when the external light
emission control input (pink) is connected to 0 to
3V, or 9V to
ⳭV (26.4V max.).
In this case, the output turns to the dark state.
Setting method
• From the above, for determining the position of the
wafer from the sensing signal, calculate the center
position of the signal's ON region, while taking into
consideration the response time.
1st cross pitch
(small)
Orientation flat length
Normal sensing
position
2nd cross pitch
(large)
Cross-condition
wafer
Normal wafer
• The calculated pitch based on the wafer size is
given in the table below.
• From the above, it is seen that, since the pitch of
the cross-condition wafer reduces, the pitch
resolution required for high reflectivity wafers
becomes more stringent than the specified
resolution of 3mm. Hence, the sensing signal from
two wafers may not be resolved and may become a
continuous signal.
Further, the sensing signal may also change due to
the sensitivity setting, the reflectivity of the wafer,
and the sensing conditions (sensing distance or
sensing angle).
For the above reasons, in case of wafers which
have been cross-inserted, since the small crosspitch side is similar to overlapping wafers, the
sensing signal of two wafers may become a
continuous signal or may get resolved.
• If the orientation flat happens to get in the position
of sensing, sensing is not possible in one of the two
sensing positions. Therefore, if the wafer is crossinserted, a resolved signal may not be output, and
in this case, the information on the wafer position
calculated from the sensing signal will be
erroneous.
"4.2 cable,
300mm long
2-"4.5 mounting
holes
Beamreceiving
part
Beamreceiving
part
Beam
emitting
part
18.3
12
50
34
80.670
PRINTED IN JAPAN
http://www.sunx.co.jp/
Head Office
SUNX Limited
Phone: ⴐ81-(0)568-33-7861 FAX: ⴐ81-(0)568-33-8591
Overseas Sales Dept.
2431-1 Ushiyama-cho, Kasugai-shi, Aichi, 486-0901, Japan
Phone: ⴐ81-(0)568-33-7211 FAX: ⴐ81-(0)568-33-2631
Sensitivity selection
switch
Sensitivity
Maximum
sensitivity
(MAX)
High
sensitivity
(HIGH)
Medium
sensitivity
(MID)
Low
sensitivity
(LOW)
Used for low reflectivity
wafers with nitride or oxide
film processing, or for thin
wafers (0.3 to 0.4mm)
Sensitivity between maximum
sensitivity and medium
sensitivity
Used for high reflectivity
polished wafers, etc., or for
3mm wafer pitch
Lowest possible sensitivity
setting
3 inch (75mm)
4 inch (100mm)
5 inch (125mm)
6 inch (150mm)
8 inch (200mm)
4.75mm
4.75mm
4.75mm
4.75mm
6.35mm
22.2mm
32.5mm
42.5mm
57.5mm
59.3mm
0.380mm
0.625mm
0.625mm
0.675mm
0.725mm
1.58mm
1.54mm
1.52mm
1.43mm
2.19mm
3.17mm
3.21mm
3.23mm
3.33mm
4.16mm
Wafer size
Normal
pitch
Orientation
flat length
Wafer
thickness
Cross pitch
(small)
Cross pitch
(large)
Sensitivity selection
switch
Ext.sensitivity
selection input
Sensitivity
Used for low reflectivity
wafers with nitride or oxide
film processing, or for thin
wafers (0.3 to 0.4mm)
Used for high reflectivity polished wafers,
etc., or for 3mm wafer
pitch
Sensitivity between
maximum sensitivity
and medium sensitivity
Lowest possible sensitivity setting
m The cable
direction can be
changed.
Wafer thickness
t=0.6mm
Signal width
1.5mm approx.
Wafer thickness
t=0.6mm
Signal width
1.1mm approx.
䢇 Narrow pitch sensing signal width
• In case of
4
DETECTING WAFER HAVING ORI-
ENTATION FLAT, when the sensor is mounted at
positions which avoid the wafer orientation flat, the
pitch of a cross-condition wafer changes as shown
in the figure below.
H
L
1 2 3 4
Sensitivity selection switch
H
L
: Approx. 2ms
OFF-delay
timer
1 2 3 4 1 2 3 4
Timer operation mode switch
H
L
: Without
timer
Sensing
condition
Operation
Normal
With
timer
T T T
Timer period: T= 2ms approx.
Sensing
Not
sensing
ON
OFF
ON
OFF
External light
emission
control input
Output
In case of
Light-ON
ON
OFF
T1 T2
ON
OFF
T1=5ms, T2=20ms max.
H
L
Sensitivity setting button
NPN
PNP
High
reflectivity
wafer
Low
reflectivity
wafer
Wafer
thickness
t=0.6mm
Wafer
thickness
t=0.6mm
Sensing signal
width 1.5mm
approx. (Example)
Sensing signal
width 1.1mm
approx. (Example)
ON OFF