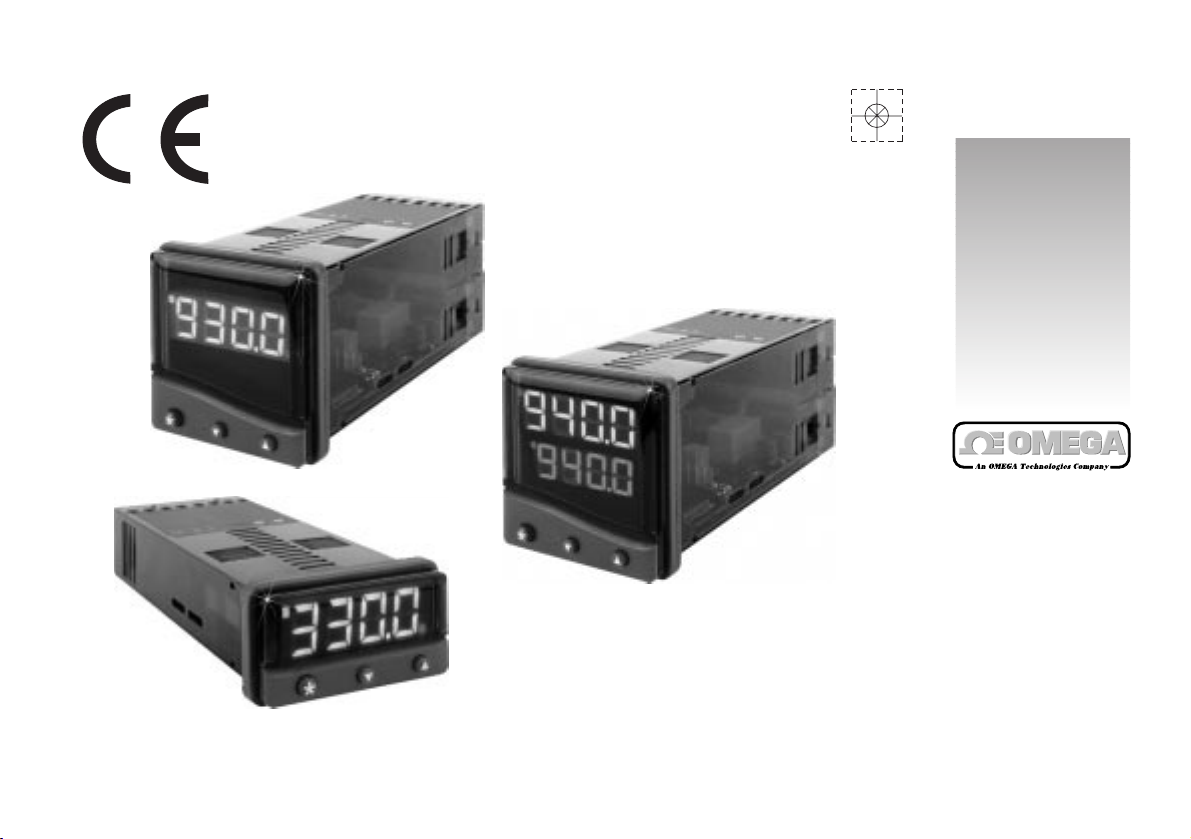
User ’s Guide
http://www.omega.com
e-mail: info@omega.com
CN9-SW-95
CN9-SW-NT
Software Communications Manual
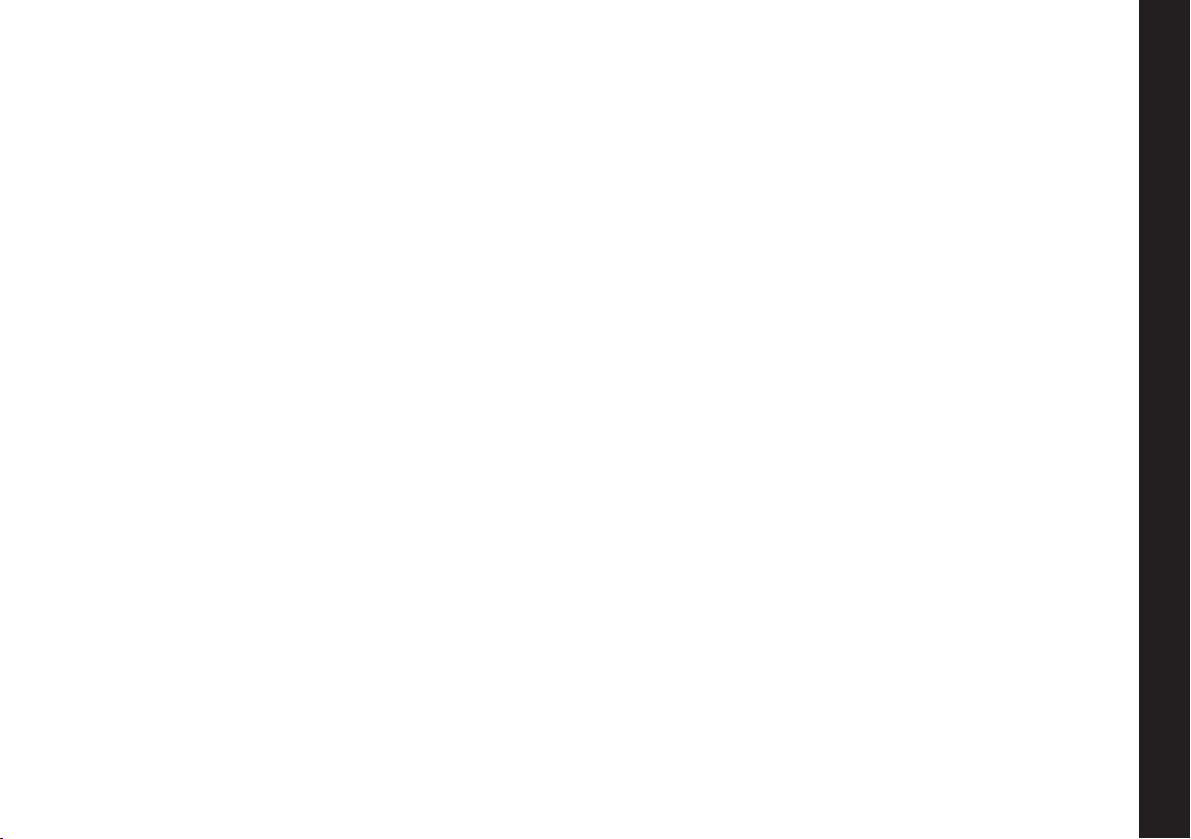
INDEX
KEY TO PROGRAM ICONS
OVERVIEW (inside front cover)
INSTALLATION/CABLING
RS232 1
RS485 2
Termination resistors 3
Bias resistors 4
RS232/RS485 features 5
INSTRUMENT COMMS SETTINGS 6
CONFIGURING INSTRUMENT COMMS SETTINGS 7-8
INSTALLING CN9-SW SOFTWARE 9-10
GETTING STARTED 11
CN9-SWINSTRUMENT SCREENS 12
PC COM PORT SETTINGS 13-14
INSTRUMENT PARAMETER CONFIGURATION
SOFTWARE ALARMS 15
SETPOINT ADJUSTMENT 16
INSTRUMENT CLONING 17
SAVING SETTINGS TO FILE 18
SECURITY LOCKOUTS 19-20
LOGGING AND CHARTING 21-24
LOG ON CHANGE 25-26
EXPORTING LOG FILES 27
TROUBLE SHOOTING 28
GLOSSARY OF TERMS 29-30
WARRANTY 31
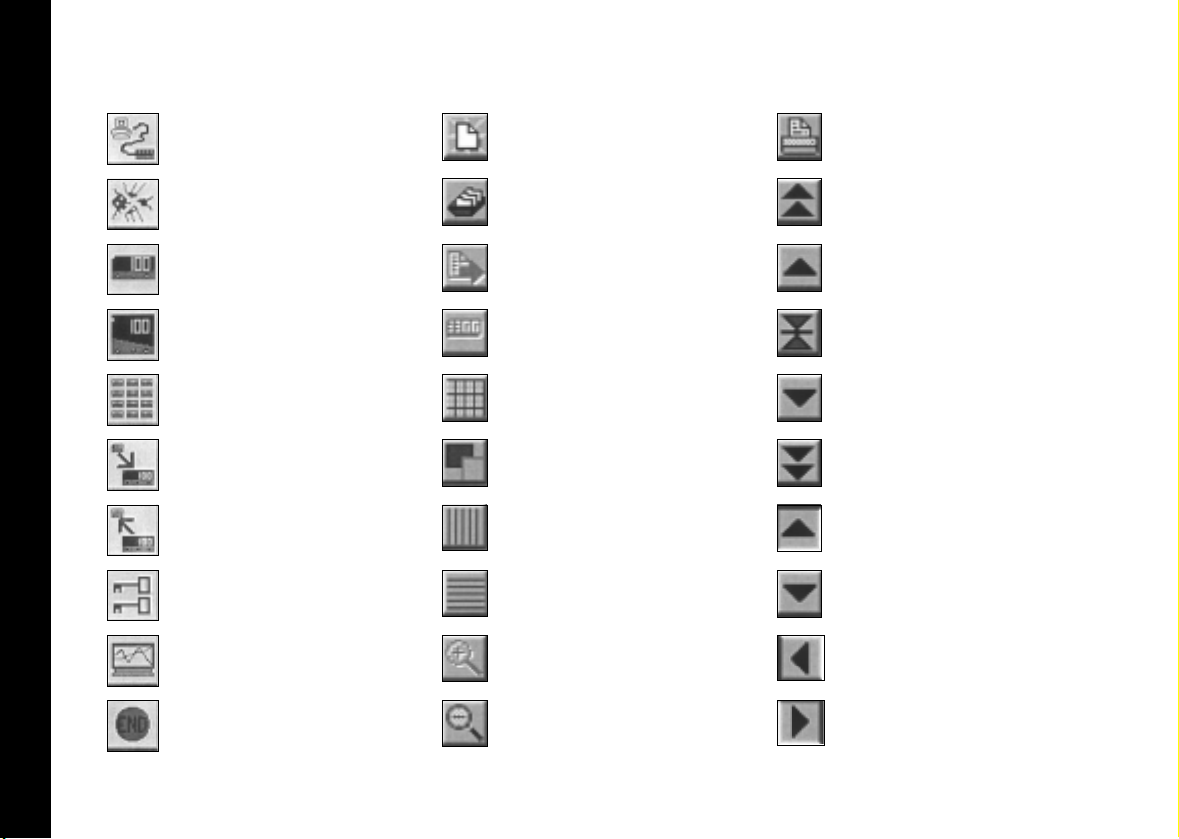
Change comms settings &
start monitoring
Create new file
Print chart recorder
Toggle Modbus comms
de-bug window
Add new instrument CN 9500
Add new instrument CN 9300
Arrange instruments in grid
Make instruments larger
Make instruments smaller
Set security locks
Add new chart recorder
Open existing file
Export file in text format
Select units to record
Toggle grid density
Select background colour
Select primary grid colour
Select grid colour
Make chart bigger
Key to Program Icons
Close program
Make chart smaller
Scroll chart up 100%
Scroll chart up 10%
Find chart zero
Scroll chart down 10%
Scroll chart down 100%
Expand verticle scaling range
Decrease verticle scaling range
Increase time/division
Decrease time/division
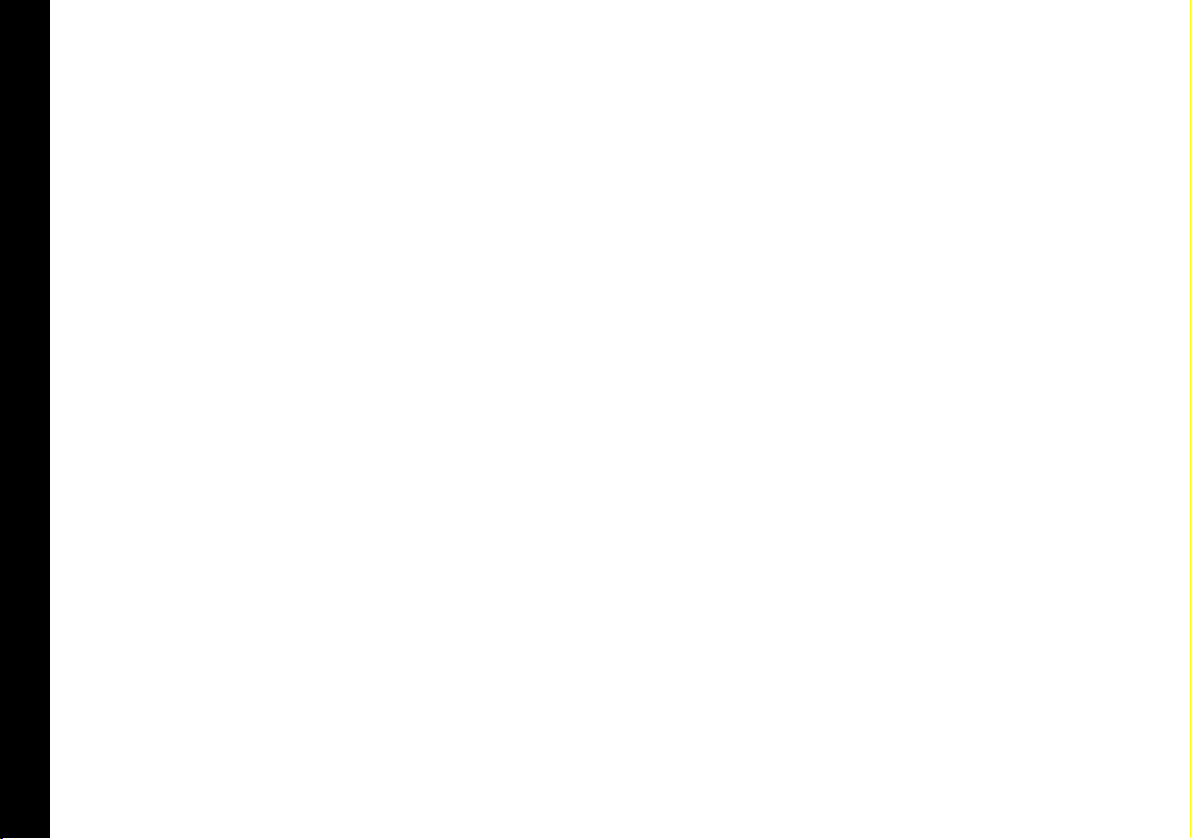
OVERVIEWKey to Program Icons
CN9-SW is a graphic WINDOWSTMbased software
package designed for PC supervision of Omega Model
CN9500 / CN9400 and Model CN9300 controllers. It offers
the capability of remote adjustment, instrument
configuration, cloning, saving and retrieving instrument
settings to files together with logging and charting in real
time.
Communication uses the MODBUS
fully isolated RS232 or RS485 link depending on the number
of instruments and the transmission distances involved in the
®
protocol via either a
Overview
application.
PC Requirements
To gain the full benefit of CN9-SW software, it is recommend
that the PC is fitted with a Pentium processor and is running
WINDOWS 95 or Windows NT programs. A minimum of 16
Mb RAM is recommended to run the program, together with
enough free hard disc space to meet logging requirements.
This manual assumes that a mouse or other pointing device
will be employed, but alternatively or in an emergency the
standard WINDOWS key convention can be used to operate
or close the program.
Because the controllers are “stand alone” they do not need
PC supervision for their normal function, and will continue to
control the process unaffected by failure of any part of the
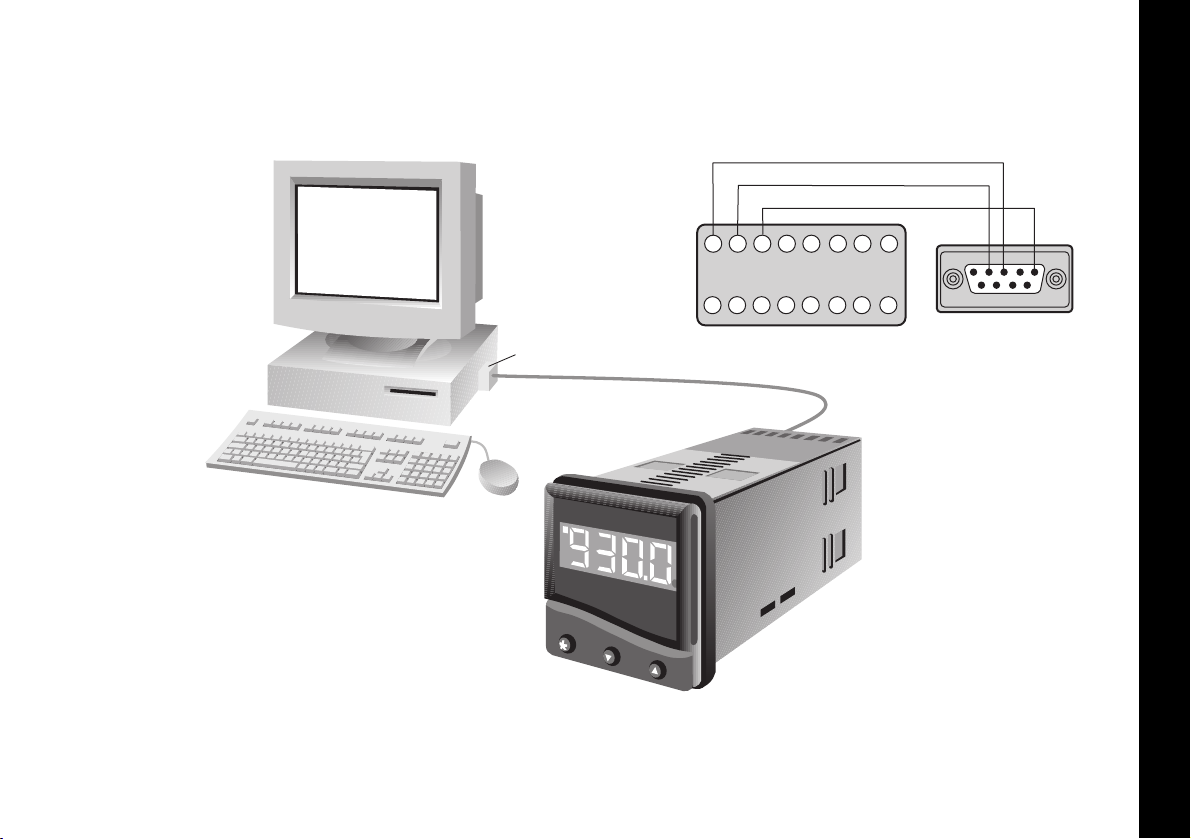
1 2 3 4 5 6 7 8
9 10 11 12 13 14 15 16
CN 9500 / CN 9300
rear terminal
1
5
69
PC Com 1
DB-9 Pin
Tx
Rx
Gnd
COM port
Installation/Cabling
Installation/Cabling
1
RS-232 Is the standard most widely used for interfacing
peripherals to PC's and is designed for serial
communications with single instrument up to a distances
of 15 metres, in a low electrical noise environment.
Connection is via a screened two core cable where the
voltage signal on each line is referenced to the screen
which is grounded. Most PC's have one or two RS-232
compatible ports fitted as standard.
RS232 Connections
PortCN9500 / CN9400 / CN9300
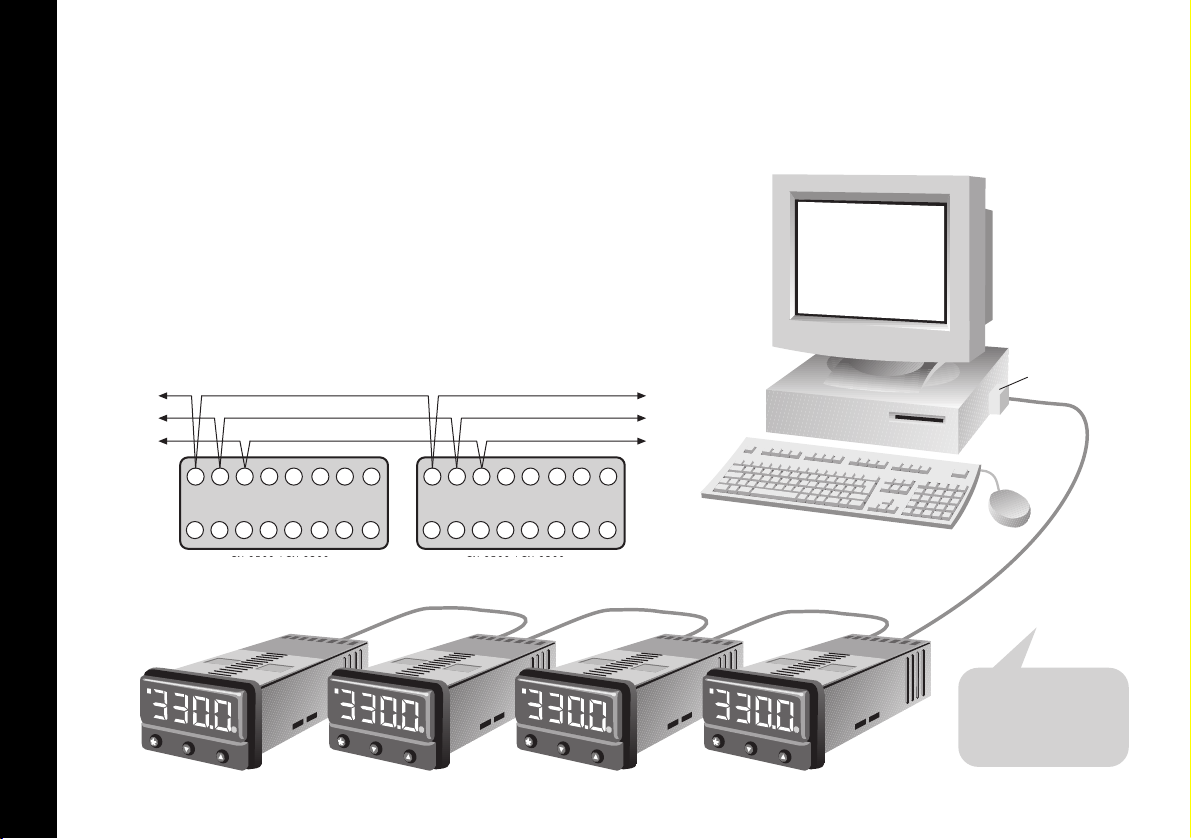
Installation/Cabling
Installation/Cabling
2
Tx Rx (+)
1 2 3 4 5 6 7 8
9 10 11 12 13 14 15 16
To
additional
units
1 2 3 4 5 6 7 8
9 10 11 12 13 14 15 16
CN 9500 / CN 9300
unit 2
Tx Rx (-)
CN 9500 / CN 9300
unit 1
Gnd
Tx Rx (+)
Tx Rx (-)
Gnd
Daisy chained connections
Connections if PC 485 card used
To RS 485 Interface
Either plug in board or
separate converter
Note:
Where separate RS 485
interface is used, refer to
manufacturers instructions for
connection details
To
RS 485
interface
COM port
RS485 Connections
RS-485 Is a half duplex serial communications link and is the
standard most commonly used for industrial applications due
to it's high noise immunity and multi-drop capability. It
enables a PC to communicate with up to 32 instruments
over distances up to 1200 metres, and requires the addition
of an RS-485 interface card, or a separate RS-232/485
converter.
CN9500 / CN9400 / CN9300
unit 2
CN9500 / CN9400 / CN9300
unit 1
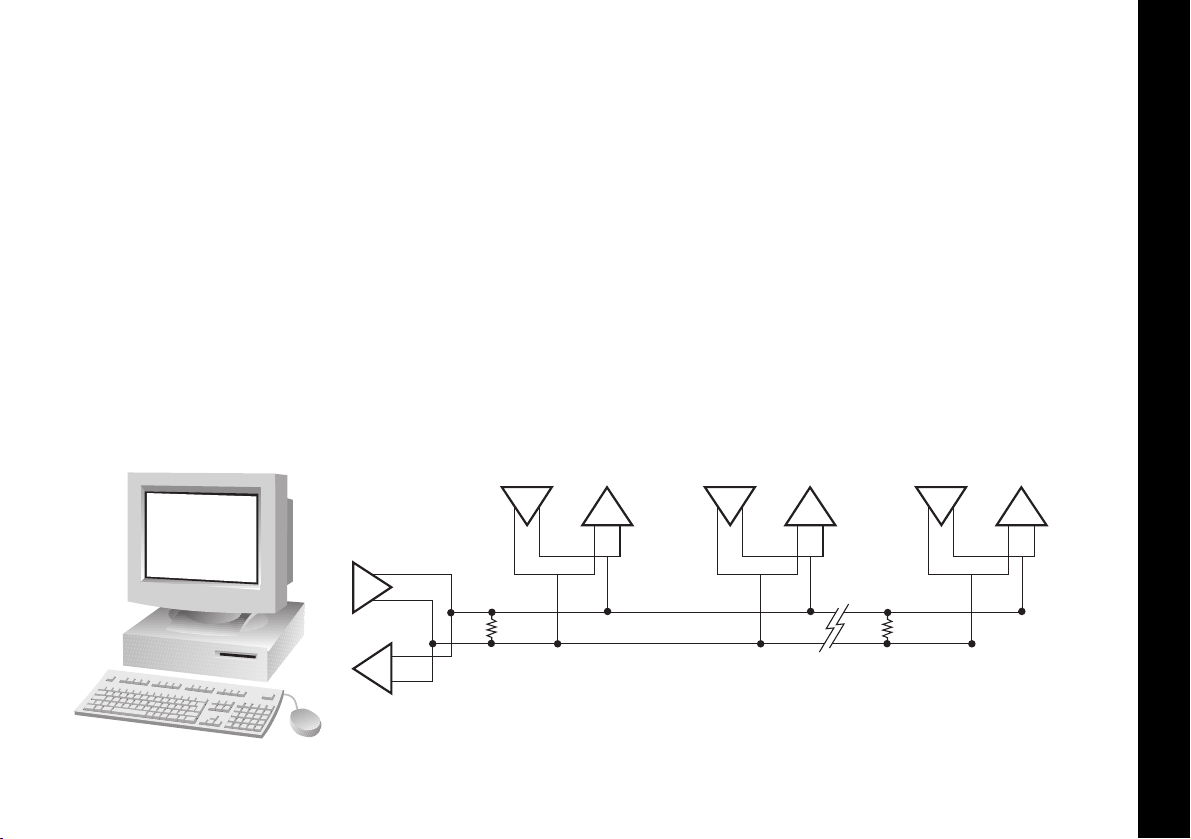
Installation/Cabling
Installation/Cabling
3
Termination resistors
–
120Ω
Tx
Rx
+
+
–
+
–
+
–
Tx
Rx
+
–
+
–
Tx
Rx
+
–
+
–
Tx
Rx
120Ω
Instrument 1 Instrument 2 Instrument ‘N’
Each RS485 interface has specific connection and
termination biasing requirements which will be detailed in
their installation instructions. The general principles are as
follows.
Terminations Because each wire is a transmission line, it
must be properly terminated to prevent reflections. Where
multiple instruments are daisy-chained together, a 120 ohm
terminating resistor should be fitted at the connection to
the PC and to the last instrument in the chain.

Installation/Cabling
Installation/Cabling
4
Bias resistors
–
Tx
Rx
+
+
–
+
–
+
–
Tx
Rx
+
–
+
–
Tx
Rx
+
–
+
–
Tx
Rx
Instrument 1 Instrument 2 Instrument ‘N’
+5V
620Ω
-5V
620Ω
Bias resistors When transmission lines are not transmitting,
they remain in an indeterminate state which can allow
receivers to receive invalid data bits due to electrical noise
on the cable. To prevent this, the the lines should be forced
into a known state by fitting two 620 ohm bias resistors to
one point (node).
If an RS-485 interface card is being fitted to the PC,
separate bias resistors may not be needed because they
may already be fitted to the card. Check the manufacturers
specification.
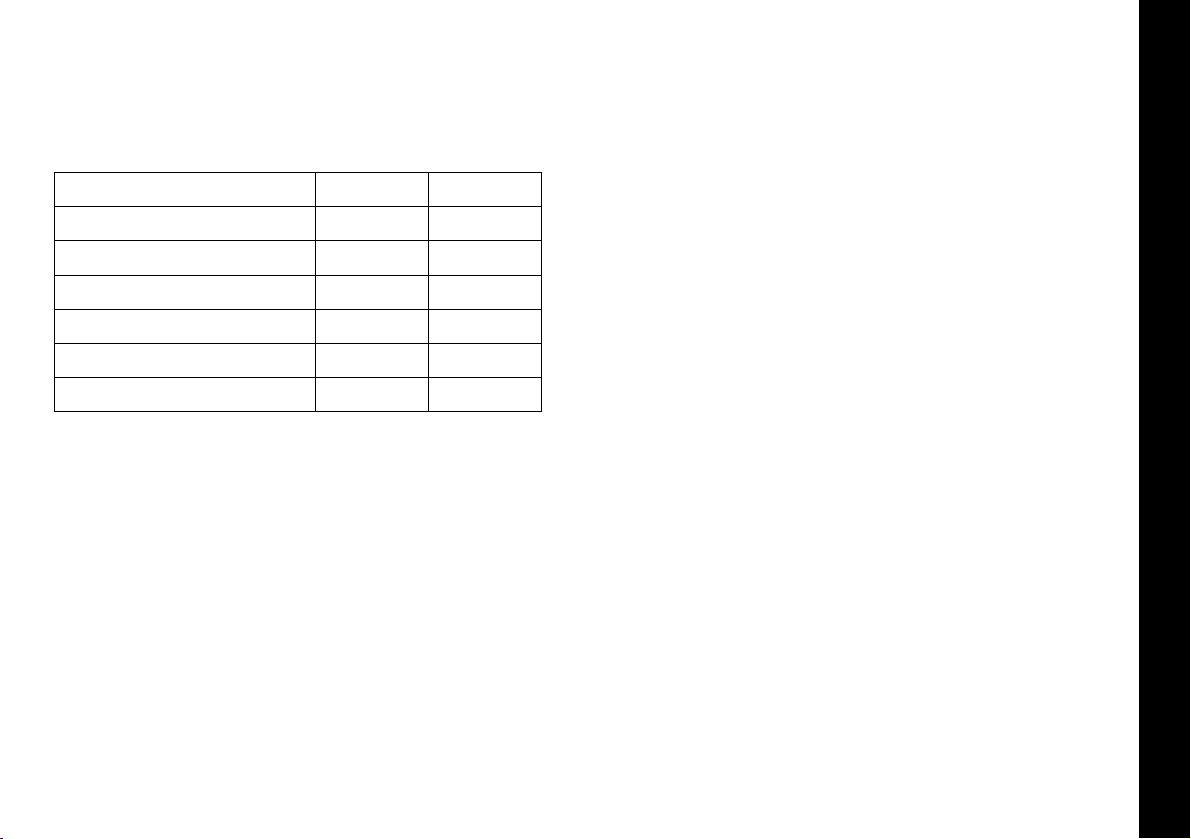
Installation/Cabling
Installation/Cabling
5
For a continually updated list of recommended RS-485
interface cards, contact Omega.
Feature
Type of transmission lines Unbalanced
132
321
15M
19.2Kb/sec 19.2Kb/sec
+/- 25V + 12 to - 7V
1200M
Differential
Maximum number of drivers
Maximum number of receivers
Maximum cable length
Maximum data rate
Maximum CMV
RS232 RS485
Table lists the features of both RS-232 and RS-485
standards.
Cable To ensure data integrity over long transmission
distances, it is recommended that good quality RS-485 cable
is used.
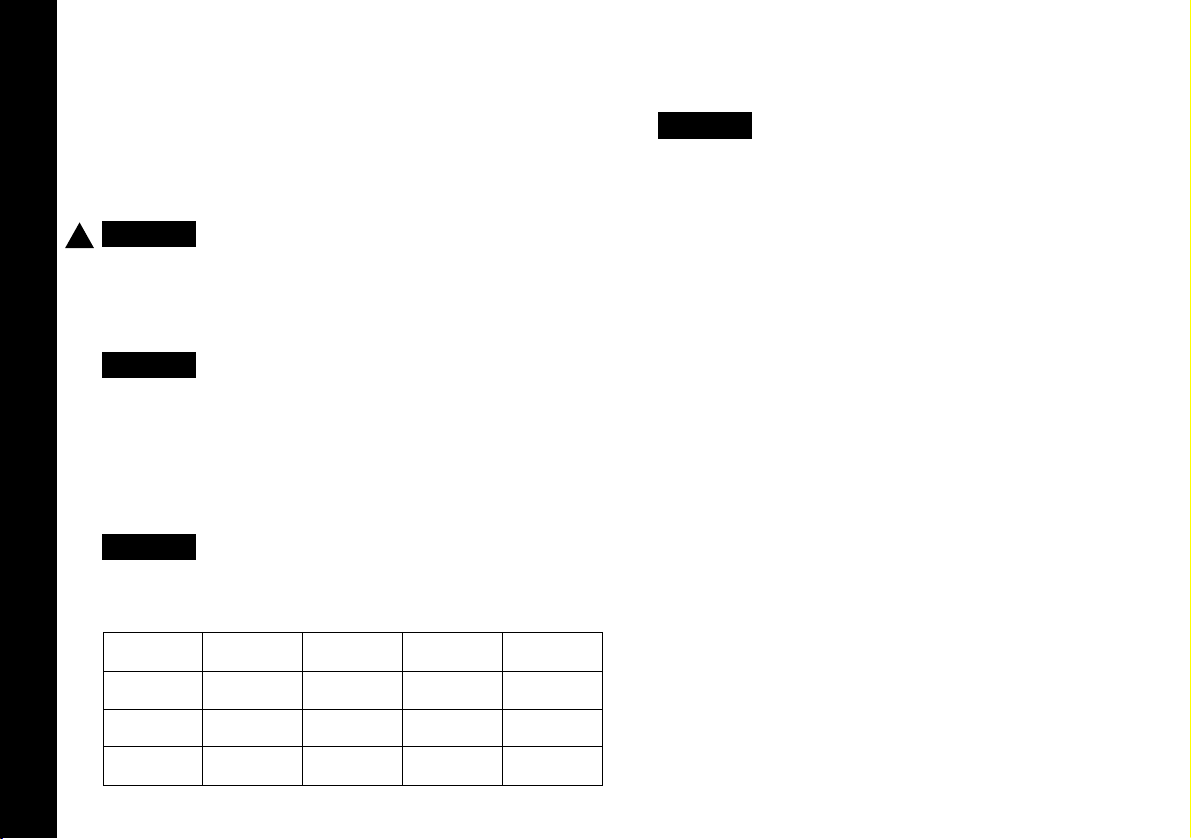
Instrument Comms Settings
Instrument Comms Settings
6
Immediately after power-up, both instrument, and PC comms
settings need to be made compatible before communication
between them is possible. Instrument defaults are shown
below together with the available options.
ADDR (Address) This is a unique
identification number that must be
allocated to each instrument
connected to the network.
Default =0. Options;
1 to 247
BAUD (Baud rate) The setting determines
the serial communication data
transmission rate in bits/sec, and must
match the PC settings
Default =
9600
.
Options;
1200;2400;4800;9600 and 19200
DATA (Data) Sets the transmission format, and
must match the PC settings.
Data Format Table
Settings Start bits
1
1
1
Data bits
8
8
8
Parity
n (none)
e (even)
o (odd)
Stop bits
1
1
1
Default
Option 1
Option 2
DBUG (Debug). Commissioning and
troubleshooting aid. Display shows
when the instrument is transmitting or
receiving data by rapidly flashing the
three horizontal segments of the first
and last digit of the display.
First digit = Tx; last digit = Rx
Default = Off. Options
off; on
Only use dbuG during commissioning or trouble-shooting
because it shares display segments and therefore
corrupts the normal display.
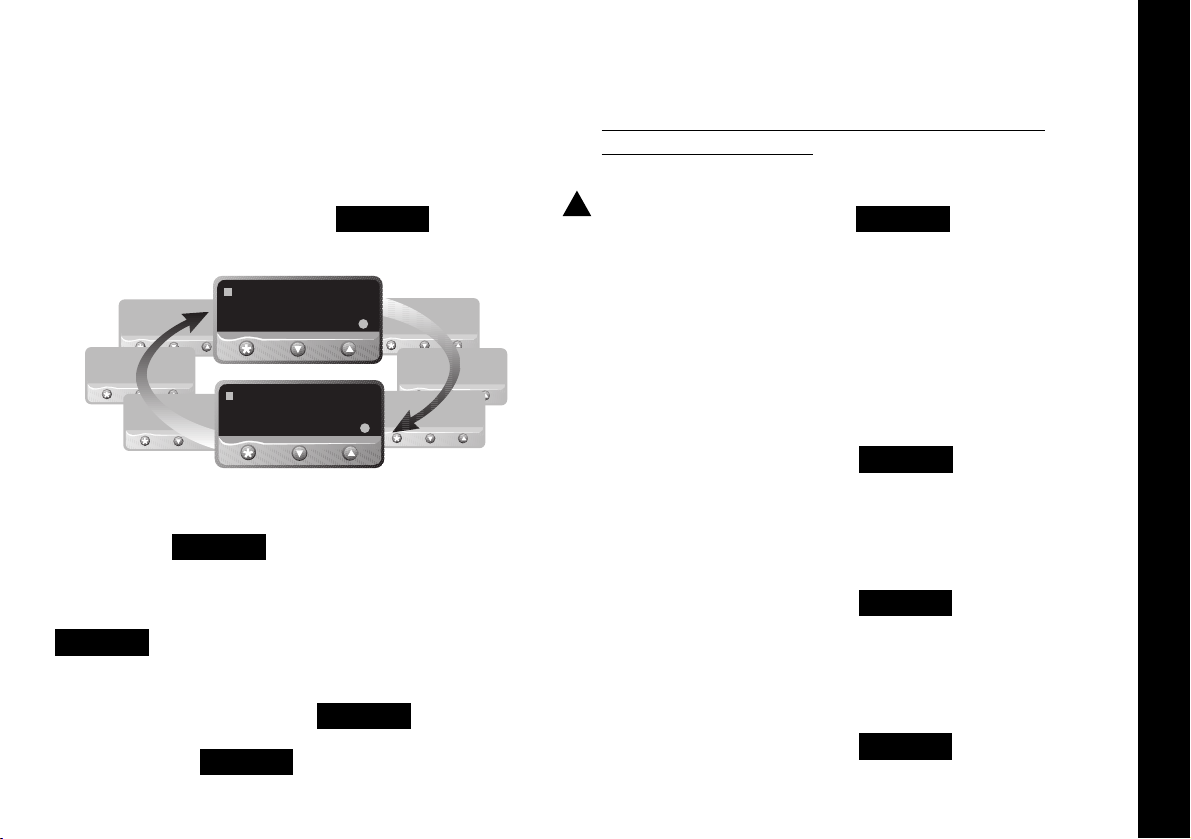
Instrument Comms Address
Configuring Instrument Comms Settings
7
This should also be done immediately after power-up, and
is only possible from the instrument front panel.
On power-up the controller will display the self test
sequence followed by Alternating INPT and
nonE
INPT
INPT
INPT
NONE
NONE
NONE
CAL 3300
INPT
NONE
Note: During the following procedure the display will revert
to alternating INPT and
nonE
after 60 seconds of
keying inactivity, but will retain any settings already
completed. Should this occur, or in the event of becoming
"lost" in the program, please start again from the alternating
INPT and
nonE
display
To select Level C (communications settings)
Press ▼ once display alternates LEVL and
5
Press and hold ✱ and press ▼ five times to reach level C
display alternates LEVL and
C
Note: Level C is only visible when the comms interface
board is fitted to the unit
To set up Instrument comms address
Press ▲ once display alternates ADDR and
0
Press and hold ✱ and press ▲ to index to chosen address
number
(1 to 247)
Note: In the absence of any conflicting information the
following comms settings should be left as the default
values. (see details on page 6).
To read or adjust comms settings
Baud rate
Press ▲ once display alternates BAUD and
9600
(Default setting)
Press and hold ✱ and use ▲ or ▼ keys to select preferred
value
Data format
Press ▲ once display alternates DATA and
18n1
(Default setting)
Press and hold ✱ and use ▲ or ▼ keys to select preferred
setting (see table page 6)
Debug setting
Press ▲ once display alternates DBUG and
oFF
(Default setting)
Press and hold ✱ and use ▲ key to select
on