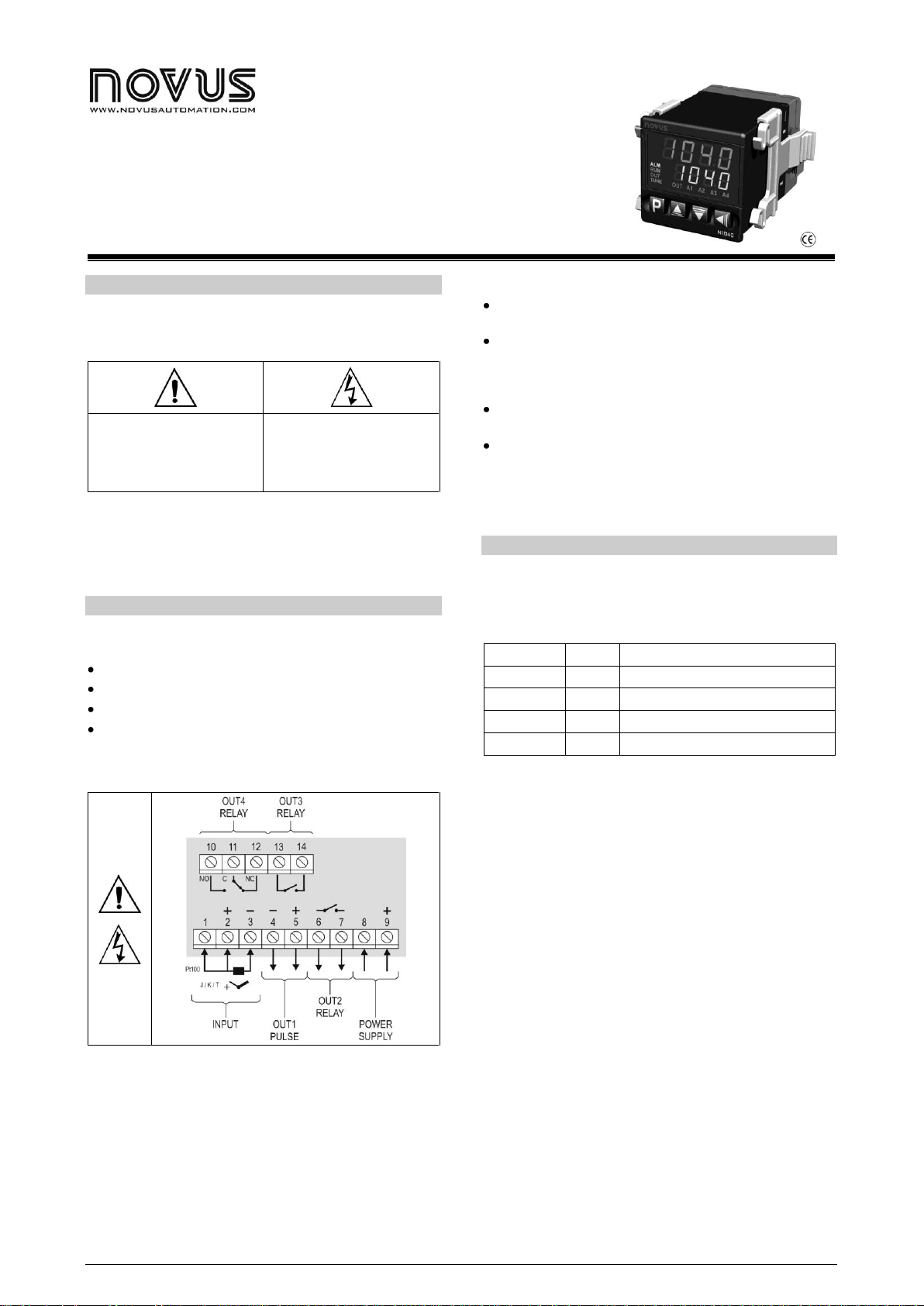
N1040 Controller
TEMPERATURE CONTROLLER – INSTRUCTIONS MANUAL – V1.1x D
SAFETY ALERTS
CAUTION:
Read the manual thoroughly
before installing and operating
the equipment.
CAUTION OR DANGER:
Electrical shock hazard
Range: -110 to 950 ºC (-166 to 1742 ºF)
Range: -150 to 1370 ºC (-238 to 2498 ºF)
Range: -160 to 400 ºC (-256 to 752 ºF)
Range: -200 to 850 ºC (-328 to 1562 ºF)
The symbols below are used on the equipment and throughout this
document to draw the user’s attention to important operational and
safety information.
All safety related instructions that appear in the manual must be
observed to ensure personal safety and to prevent damage to either
the instrument or the system. If the instrument is used in a manner not
specified by the manufacturer, the protection provided by the
equipment may be impaired.
INSTALLATION / CONECTIONS
The controller must be fastened on a panel, following the sequence
of steps described below:
Prepare a panel cut-out of 46 x 46 mm;
Remove the mounting clamps from the controller;
Insert the controller into the panel cut-out;
Slide the mounting clamp from the rear to a firm grip at the panel.
ELECTRICAL CONNECTIONS
Fig. 01 below shows the electrical terminals of the controller:
Fig. 01 - Connections of the back panel
NOVUS AUTOMATION 1/5
RECOMMENDATIONS FOR THE INSTALLATION
All electrical connections are made to the screw terminals at the
rear of the controller.
To minimize the pick-up of electrical noise, the low voltage DC
connections and the sensor input wiring should be routed away
from high-current power conductors. If this is impractical, use
shielded cables. In general, keep cable lengths to a minimum.
All electronic instruments must be powered by a clean mains
supply, proper for instrumentation.
It is strongly recommended to apply RC'S FILTERS (noise
suppressor) to contactor coils, solenoids, etc. In any application it
is essential to consider what can happen when any part of the
system fails. The controller features by themselves can not assure
total protection.
FEATURES
INPUT TYPE SELECTION
Table 01 shows the sensor types accepted and their respective
codes and ranges. Access the parameter TYPE in the INPUT cycle
to select the appropriate sensor.
Table 01 – Input types
OUTPUTS
The controller offers two, three or four output channels, depending on
the loaded optional features. The output channels are user
configurable as Control Output, Alarm 1 Output, Alarm 2 Output,
Alarm 1 OR Alarm 2 Output and LBD (Loop Break Detect)
Output.
OUT1 - Logical pulse, 5 Vdc / 25 mA, available at terminals 4 and 5.
OUT2 - Relay SPST-NA, 1.5 A / 240 Vac, available at terminals 6 and
7.
OUT3 - Relay SPST-NA, 1.5 A / 240 Vac, available at terminals 13
and 14.
OUT4 - Relay SPDT, available at terminals 10, 11 and 12.
CONTROL OUTPUT
The control strategy can be ON/OFF (when PB = 0.0) or PID. The
PID parameters can be automatically determined enabling the autotuning function (ATvN).
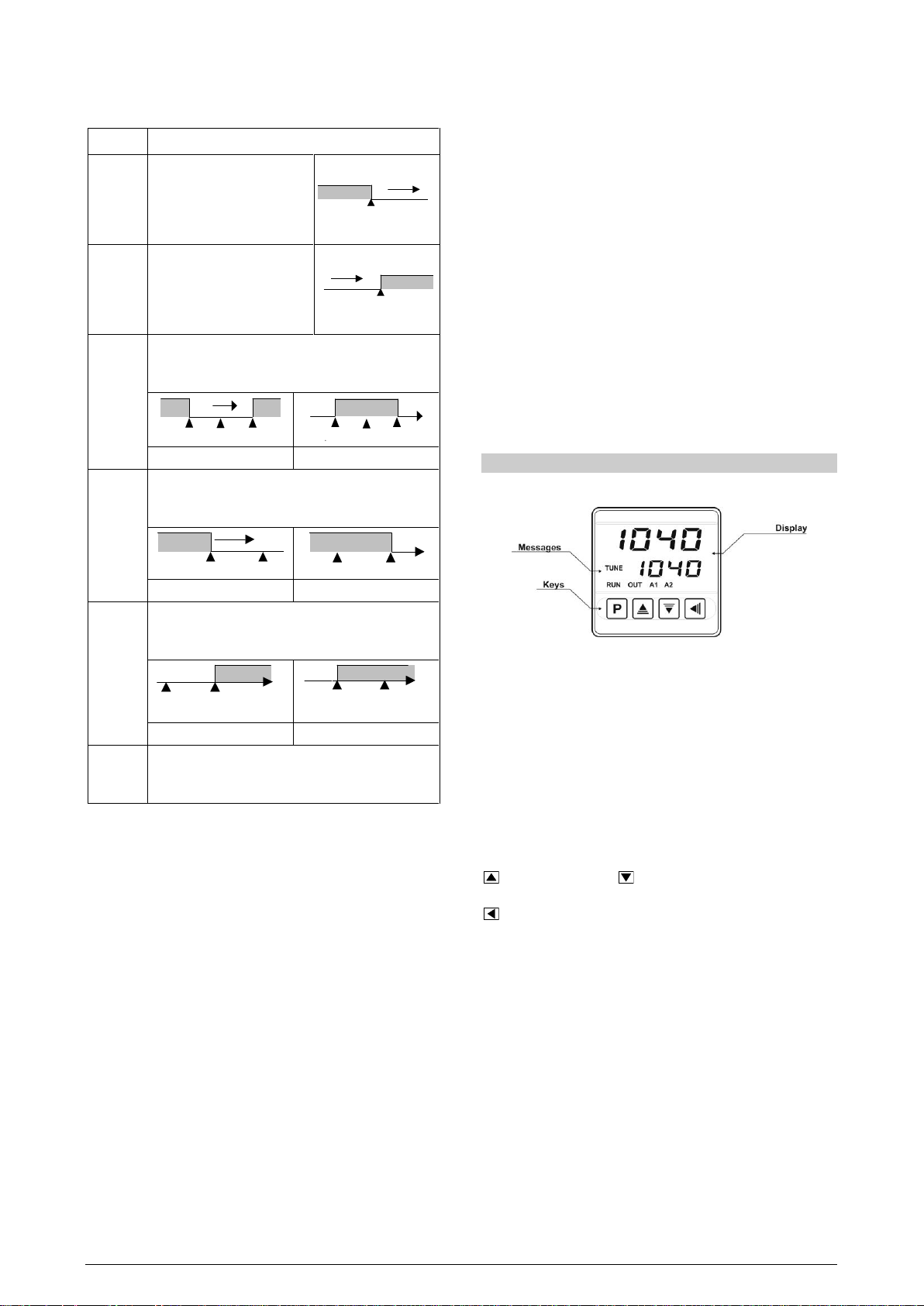
N1040 Controller
Output is not used as alarm.
Alarm of Absolute Minimum
Value. Triggers when the
value of measured PV is
below the value defined for
alarm Setpoint.
Alarm of Absolute Maximum
Value. Triggers when the
value of measured PV is
above the value defined for
alarm Setpoint.
Alarm of Differential Value. In this function the
parameters SPA1 and SPA2 represent the deviation
of PV in relation to the SP of CONTROL.
Alarm of Minimum Differential Value. It triggers when
the value of PV is below the defined point by (using
the Alarm 1 as example).
Alarm of Valor Maximum Differential Value. Triggers
when the value of PV is above the defined point by
(using Alarm 1 as example):
Sensor Break Alarm. Activated when the input signal
of PV is interrupted, out of the range limits or Pt100 in
short-circuit.
ALARM OUTPUT
The controller contains 2 alarms that can be directed (assigned) to any
output channel. The alarm functions are described in Table 02.
selected output will be activated when a LDB condition is detected.
When the Lbd.t parameter is programmed with 0 (zero), the LDB
function is disabled.
The LBD is useful in detecting system failures, such us defective
sensors or actuators, loads and power supply, among others.
SAFE OUTPUT VALUE WITH SENSOR FAILURE
This function defines an output value (user defined) to be assigned to
the control output in the event of a sensor failure.
When the input sensor is identified as broken, the controller switches
the control mode to MANUAL while forcing MV to assume the user
configured value in the 1E.ov parameter. This function requires that
one of the alarms be configured as 1Err and the 1E.ov parameter
(control output percentage) programmed with a value other then 0
(zero).
Once this function is triggered, the controller remains in SAFE mode
(MANUAL control output) even after the sensor failure appears to be
fixed. The operator intervention is required for switching back to
AUTO mode.
1E.ov values are only 0 and 100 % when in ON/OFF control mode.
For PID control mode any value in the range from 0 to 100 % is
accepted.
OPERATION
The controller’s front panel, with its parts, can be seen in the Fig. 02:
Table 02 – Alarm functions
Note: Alarm functions on Table 02 are also valid for Alarm 2 (SPA2).
INITIAL BLOCKING OF ALARM
The initial blocking option inhibits the alarm from being recognized
if an alarm condition is present when the controller is first energized
(or after a transition from run YES NO). The alarm will be enabled
only after the occurrence of a non alarm condition followed by a new
occurrence for the alarm.
The initial blocking is useful, for instance, when one of the alarms is
configured as a minimum value alarm, causing the activation of the
alarm soon upon the process start-up, an occurrence that may be
undesirable.
The initial blocking is disabled for the sensor break alarm function.
OFFSET
Allows fine adjustments to the PV reading for compensation of
sensor error.
FUNÇÃO LBD – LOOP BREAK DETECTION
The parameter defines a time interval, in minutes, within which the
PV is expect to react to a control output signal. If the PV does not
react properly within the time interval configured in lbd.t, the
controller interprets this as a control loop break and signals this
occurrence in the display.
A LBD event may be sent to any output channel. Simply configure
the LDB function to the desired output channel (OUT1 or OUT2): the
NOVUS AUTOMATION 2/5
Fig. 02 - Identification of the parts referring to the front panel
Display of PV / Programming (top display, red color): Displays the
current value of PV (Process Variable). When in configuration mode,
it shows the parameters names.
Display of SP / Parameters (bottom display, green color): Displays
the value of SP (Setpoint). When in configuration mode, it shows the
parameters values.
TUNE Indicator: Stays ON while the controller is in tuning process.
OUT Indicator: For relay or pulse control output; it reflects the actual
state of the output.
A1 and A2 Indicators: signalize the occurrence of alarm situation.
P Key: used to walk through the menu parameters.
Increment key and - Decrement key: allow altering the
values of the parameters.
Back key: used to retrocede parameters.
OPERATION
When the controller is powered up, it displays its firmware version for
3 seconds, after which the controller starts normal operation. The
value of PV and SP is then displayed and the outputs are enabled.
In order for the controller to operate properly in a process, its
parameters need to be configured first, such that it can perform
accordingly to the system requirements. The user must be aware of
the importance of each parameter and for each one determine a valid
condition.
The parameters are grouped in levels according to their functionality
and operation easiness. The 5 levels of parameters are:
1 – Operation / 2 – Tuning / 3 – Alarms / 4 – Input / 5 – Calibration
The “P” key is used for accessing the parameters within a level.
Keeping the “P” key pressed, at every 2 seconds the controller jumps
to the next level of parameters, showing the first parameter of each
level:
PV >> atvn >> fva1 >> type >> pass >> PV …