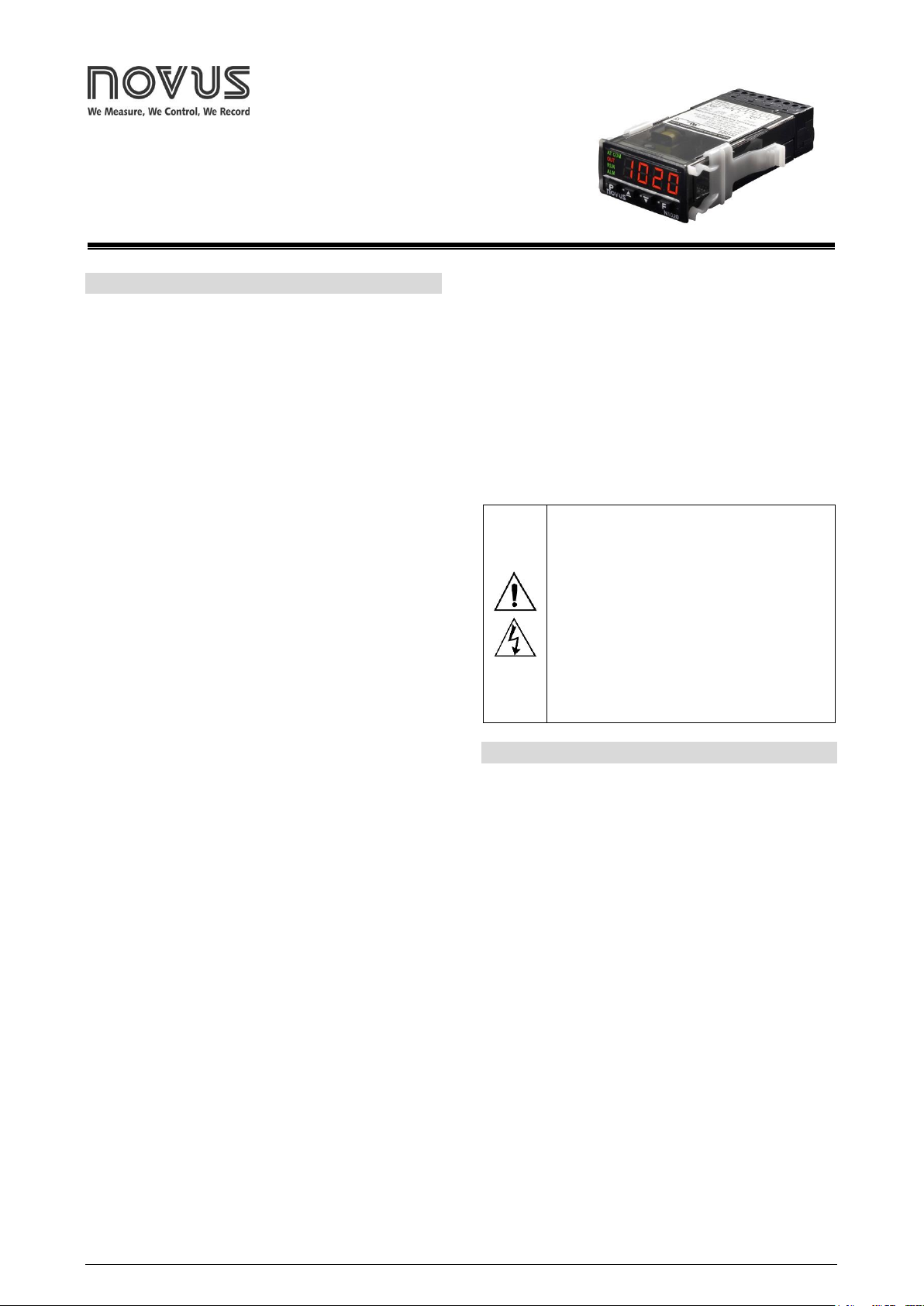
N1020 Temperature Controller
INSTRUCTIONS MANUAL – V1.1x B
The USB interface IS NOT SEPARATE from the
signal input (PV) or the controller’s digital inputs and
outputs. It is intended for temporary use during
CONFIGURATION and MONITORING periods. For
the safety of people and equipment, it must only be
used when the piece of equipment is completely
disconnected from the input/output signals. Using the
USB in any other type of connection is possible but
requires a careful analysis by the person responsible
for installing it. When MONITORING for long periods
of time and with connected inputs and outputs, we
recommend using the RS485 interface, which is
available or optional in most of our products.
INTRODUCTION
The N1020 is a small and yet powerful temperature controller. It
accepts most of the temperature sensors used in industry and its 2
outputs can be configured independently as control or alarm output.
It also embeds an auto-adaptative PID control algorithm for best
system performance.
The configuration can be performed directly on the controller or through
the USB interface. The NConfig software (free) is the configuration
management tool. Connected to the USB of a Windows computer, the
controller is recognized as a serial communications port (COM) running
with a Modbus RTU protocol.
Through the USB interface, even if disconnected from the power
supply, the configuration performed in a piece of equipment can be can
be saved in a file and repeated in other pieces of equipment that
require the same configuration.
It is important that the users read carefully this manual before using
the controller. Verify if the release of this manual matches the
instrument version (the firmware version is shown when the controller
is energized). The N1020 main characteristics are:
Multi-sensor universal input;
Self-tuning PID parameters;
2 outputs: 1 relay and 1 logical pulse for SSR;
Output functions: Control, Alarm1 and Alarm 2;
8 distinct alarm functions;
Programmable timer;
Function key for enabling/disabling outputs, resetting the timer or
turning the timer ON/OFF;
Programmable soft-start;
Rate function
Password for parameters protection;
Capability of restoring factory calibration;
Universal power supply.
USB INTERFACE
The USB interface is used for CONFIGURING or MONITORING the
controller. The NConfig software must be used for the configuration.
It makes it possible to create, view, save and open configurations
from the equipment or files in your computer. The tool for saving and
opening configurations in files makes it possible to transfer
configurations between pieces of equipment and to make backup
copies. For specific models, the NConfig software also makes it
possible to update the firmware (internal software) of the controller
through the USB.
For MONITORING purposes you can use any supervisory software
(SCADA) or laboratory software that supports the MODBUS RTU
communication on a serial communications port. When connected to
the USB of a computer, the controller is recognized as a conventional
serial port (COM x). Use the NConfig software or consult the
DEVICE MANAGER in the Windows CONTROL PANEL to identify
the COM port that was assigned to the controller. Consult the
mapping of the MODBUS memory in the controller’s communications
manual and the documentation of your supervisory software to
conduct the MONITORING process.
NOVUS AUTOMATION 1/8
Follow the procedure below to use the USB communication of the
equipment:
1. Download the NConfig software from our website and install it on
your computer. The USB drivers necessary for operating the
communication will be installed together with the software.
2. Connect the USB cable between the equipment and the
computer. The controller does not have to be connected to a
power supply. The USB will provide enough power to operate the
communication (other equipment functions cannot operate).
3. Open the NConfig software, configure the communication and
start recognition of the device.
4. Consult the NConfig help desk for detailed instructions about
how to use it and solve problems.
INSTALLATION / CONNECTIONS
The controller must be fastened on a panel, following the sequence
of steps described below:
Prepare a panel cut-out 23 x 46 mm;
Remove the mounting clamps from the controller;
Insert the controller into the panel cut-out;
Slide the mounting clamp from the rear to a firm grip at the panel.
RECOMMENDATIONS FOR THE INSTALLATION
All electrical connections are made to the screw terminals at the
rear of the controller. They accept wire sizes from 0.5 to 1.5 mm2
(16 to 22 AWG). The terminals should be tightened to a torque of
0.4 Nm (3.5 lb in).
To minimize the pick-up of electrical noise, the low voltage DC
connections and the sensor input wiring should be routed away
from high-current power conductors. If this is impractical, use
shielded cables. In general, keep cable lengths to a minimum.
All electronic instruments must be powered by a clean mains
supply, proper for instrumentation.
It is strongly recommended to apply RC'S FILTERS (noise
suppressor) to contactor coils, solenoids, etc.
In any application it is essential to consider what can happen when
any part of the system fails. The controller features by themselves
can not assure total protection.
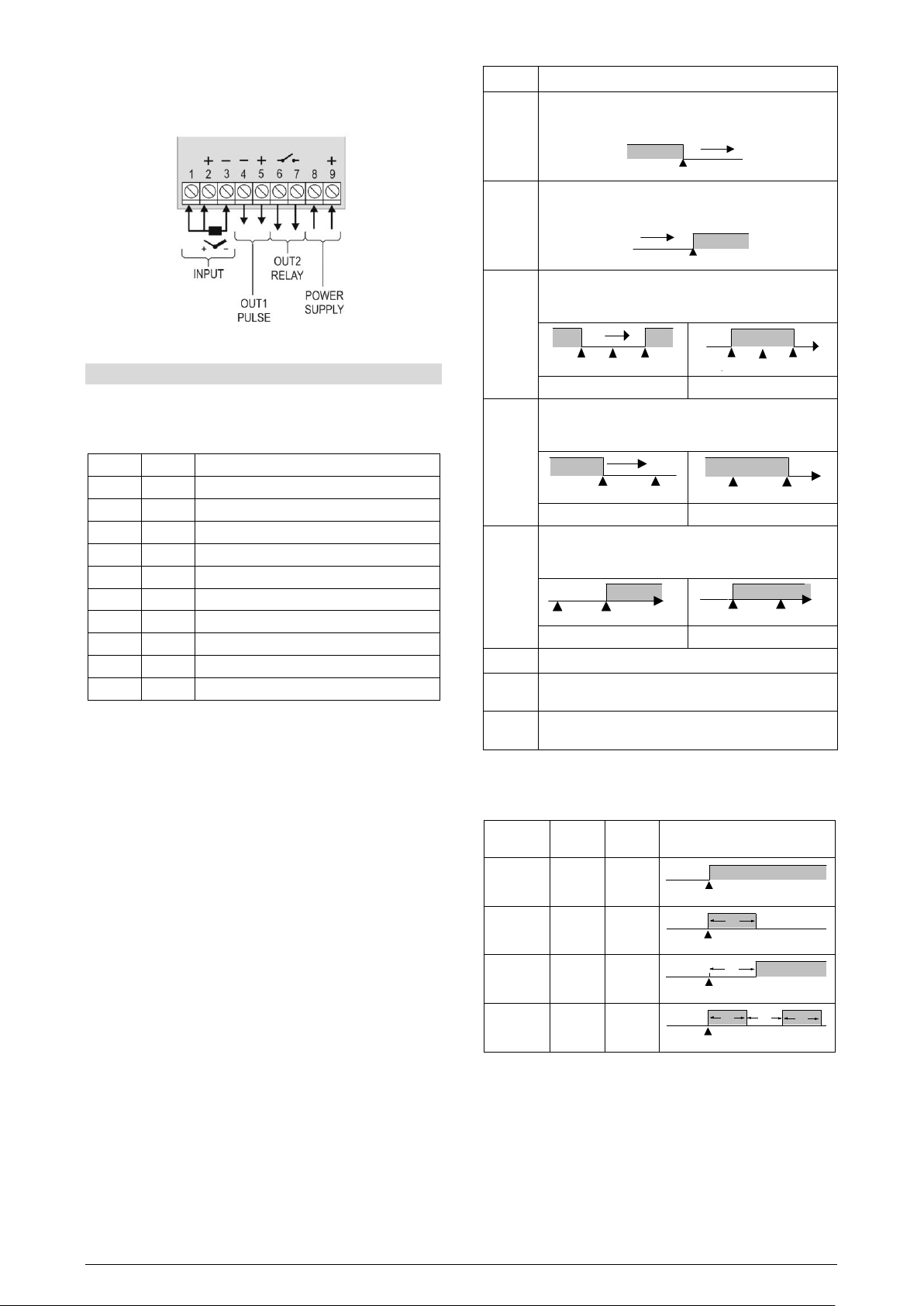
ELECTRICAL CONNECTIONS
Range: -110 to 950 ºC (-166 to 1742 ºF)
Range: -150 to 1370 ºC (-238 to 2498 ºF)
Range: -160 to 400 ºC (-256 to 752 ºF)
Range: -270 to 1300 ºC (-454 to 2372 ºF)
Range: -50 to 1760 ºC (-58 to 3200 ºF)
Range: -50 to 1760 ºC (-58 to 3200 ºF)
Range: 400 to 1800 ºC (752 to 3272 ºF)
Range:-90 to 730 ºC (-130 to 1346 ºF)
Range: -200 to 850 ºC (-328 to 1562 ºF)
Linear. Programmable indication -1999 to 9999
Alarm of Absolute Minimum Value. Triggers when the value of
measured PV is below the value defined for alarm Setpoint
(SPA1 or SPA2).
Alarm of Valor Absolute Maximum Value. Triggers when the
value of measured PV is above the value defined for alarm
Setpoint.
Alarm of Differential Value. In this function the parameters
SPA1 and SPA2 represent the deviation of PV in relation to
the SP of CONTROL.
Alarm of Minimum Differential Value. It triggers when the value
of PV is below the defined point by (using the Alarm 1 as
example):
Alarm of Valor Maximum Differential Value. Triggers when the
value of PV is above the defined point by (using Alarm 1 as
example):
Timer ON alarm. Sets alarm output ON when timer is runing.
Timer end. Configures the alarm to actuate when the timer
expires.
Sensor Break Alarm. Activated when the input signal of PV is
interrupted, out of the range or when Pt100 in short-circuit.
Activation for
a defined time
The controller complete set of features is drawn in Fig. 01. The
features loaded in a particular unit are shown on its label:
Fig. 01 - Connections of the back panel
FEATURES
INPUT TYPE SELECTION
Select the input type (in parameter “tYPE”) from Table 01 below.
N1020 Temperature Controller
Table 01 - Input Types
OUTPUTS
The N1020 offers two output channels, user configurable as Control
output, Alarm 1 output or Alarm 2 output.
OUT1 - Logical pulse, 5 Vdc / 25 mA, available at terminals 4 and 5.
OUT2 - Relay SPST-NA, 1.5 A / 240 Vac, available at terminals 6
and 7.
Note: The outputs can be configured independently from each other,
for example, both can be control outputs at the same time.
CONTROL OUTPUT
The control strategy can be configured as ON / OFF or PID.
ALARM OUTPUT
There two alarms available in the N1020. The alarms can be
assigned to either output, logical or relay. The alarm functions are
described below.
ALARM FUNCTIONS
The alarms can be configured to operate with nine different functions,
as shown in Table 02.
NOVUS AUTOMATION 2/8
Table 02 – Alarm functions
Alarms Timer Modes (Temporization)
The controller alarms can be configured to perform 4 timer modes:
Table 03 - Temporization Functions for the Alarms
The signs associated to the alarms will light when the alarm condition
is recognized, not following the actual state of the output, which may
be temporarily OFF because of the temporization.
Initial Blocking of Alarm
The initial blocking option inhibits the alarm from being recognized if
an alarm condition is present when the controller is first energized (or
after a transition from run YES NO). The alarm will be enabled
only after the occurrence of a non alarm condition followed by a new
occurrence for the alarm.
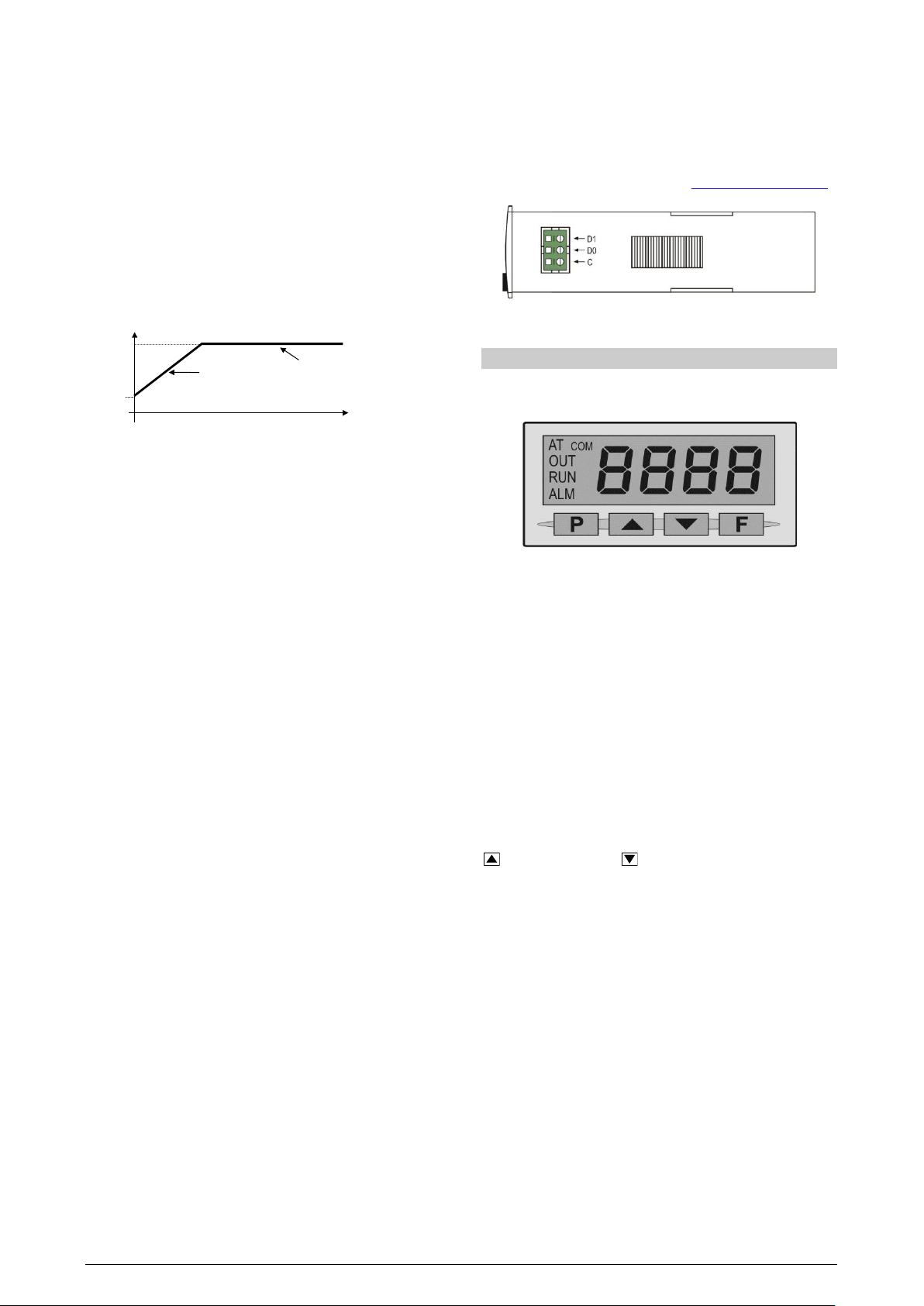
N1020 Temperature Controller
The initial blocking is useful, for instance, when one of the alarms is
configured as a minimum value alarm, causing the activation of the
alarm soon upon the process start-up, an occurrence that may be
undesirable.
The initial blocking is disabled for the sensor break alarm function.
RAMP AND SOAK FUNCTION
When the parameter Rate is configured, the N1020 performs a
gradual SV increase from the current PV value to the temperature
value set in SV. The user defines the rate of rise in degrees per
minute at the Rate prompt. When SV is reached, the temperature
is leveled at this point for 1 to 9999 minutes as programmed in the
T1me prompt. Setting 0 (zero) at T1me defines an infinite length soak
profile.
Fig. 02 - Ramp to Soak Function
The Ramp function will work whenever the controller is powered on,
the rvn parameter is set to YES or the SP variable is changed.
To disable the ramp function, set Rate = 0.0
After a power failure the controller will resume ramp generation at the
current value of PV.
OFFSET
Allows fine trimming the PV indication to compensate for sensor
errors. Default value: zero.
SERIAL COMMUNICATION
For full documentation download the Registers Table N1020 for
Serial Communication on our web site – www.novusautomation.com.
Fig. 02-a – Serial Communications Conections
OPERATION
The controller’s front panel, with its parts, can be seen in the Fig. 03:
TIMER FUNCTION
The N1020 embeds a timer function (decreasing) for applications that
require particular process duration.
Once defined the time interval in the T1me parameter, the timer will
START when:
When PV reaches the temperature programmed in the SP
parameter.
When enabling the control (RUN = YES).
By pressing the F key when configured to Timer reset mode (the
timer is reloaded with the T1me parameter and restarts counting).
By pressing the F key in ON/OFF mode stops the timer counting;
pressing it again, resumes the counting.
When the timer expires, the two possible actions can be:
Disables de control (RUN→ NO) or
Activate the alarm.
FUNCTIONS FOR THE F KEY
The F key on the frontal keypad is meant for special commands, as
follows:
Enable outputs (identically to the RUN parameter).
Timer reset: - reloads the timer and initiates a new time
counting.
Timer ON/OFF. Timer holds or resumes counting each time
the F key is pressed.
Keeping the F key pressed for 3 seconds resets the timer
(reloads the timer to the value set in T1me), initiating a new
time counting.
Note: when the F key is configured as RUN = YES/NO (RUN =
f.key), the controller outputs are born disabled after powers up.
SOFT-START
The Soft-start function is generally used in processes that require
slow start-up, where the instantaneous application of 100% of the
available power to the load may cause damages to parts of the
system.
In order to disable this function, the soft-start parameter must be
configured with 0 (zero).
NOVUS AUTOMATION 3/8
Fig. 03 - Identification of the parts referring to the front panel
Display: Displays the current value of PV. When configuring a
parameter, the display alternates between the parameter prompt and
its value (the parameter value is shown with a light blinking to
differentiate it from the parameter prompt).
The display contains also the signs AT, OUT, RUN ALM and COM:
AT Indicator: Stays ON while the controller is in tuning process.
OUT Indicator: For relay or pulse control output; it reflects the
actual state of the output.
RUN Indicator: Indicates that the controller is active, with the
control output and alarms enabled. (RUN=YES).
ALM Indicator: Signalize the occurrence of alarm condition. It
lights when either alarm is active.
COM Indicator: Flashes when there is RS485 activity.
P Key: Used to walk through the menu parameters.
Increment key and Decrement key: allow altering the
values of the parameters.
F Key: accesses special functions: RUN (toggles YES/NO) and the
two modes of timer control.
STARTUP
When the controller is powered up, it displays its firmware version for
3 seconds, after which the controller starts normal operation. The
value of PV is then displayed and the outputs are enabled.
In order for the controller to operate properly in a process, its
parameters need to be configured first, such that it can perform
accordingly to the system requirements. The user must be aware of
the importance of each parameter and for each one determine a valid
condition.
The parameters are grouped in levels according to their functionality
and operation easiness. The 5 levels of parameters are:
1 – Operation
2 – Tuning
3 – Alarms
4 – Configuration
5 – Calibration
The P key is used for accessing the parameters within a level.