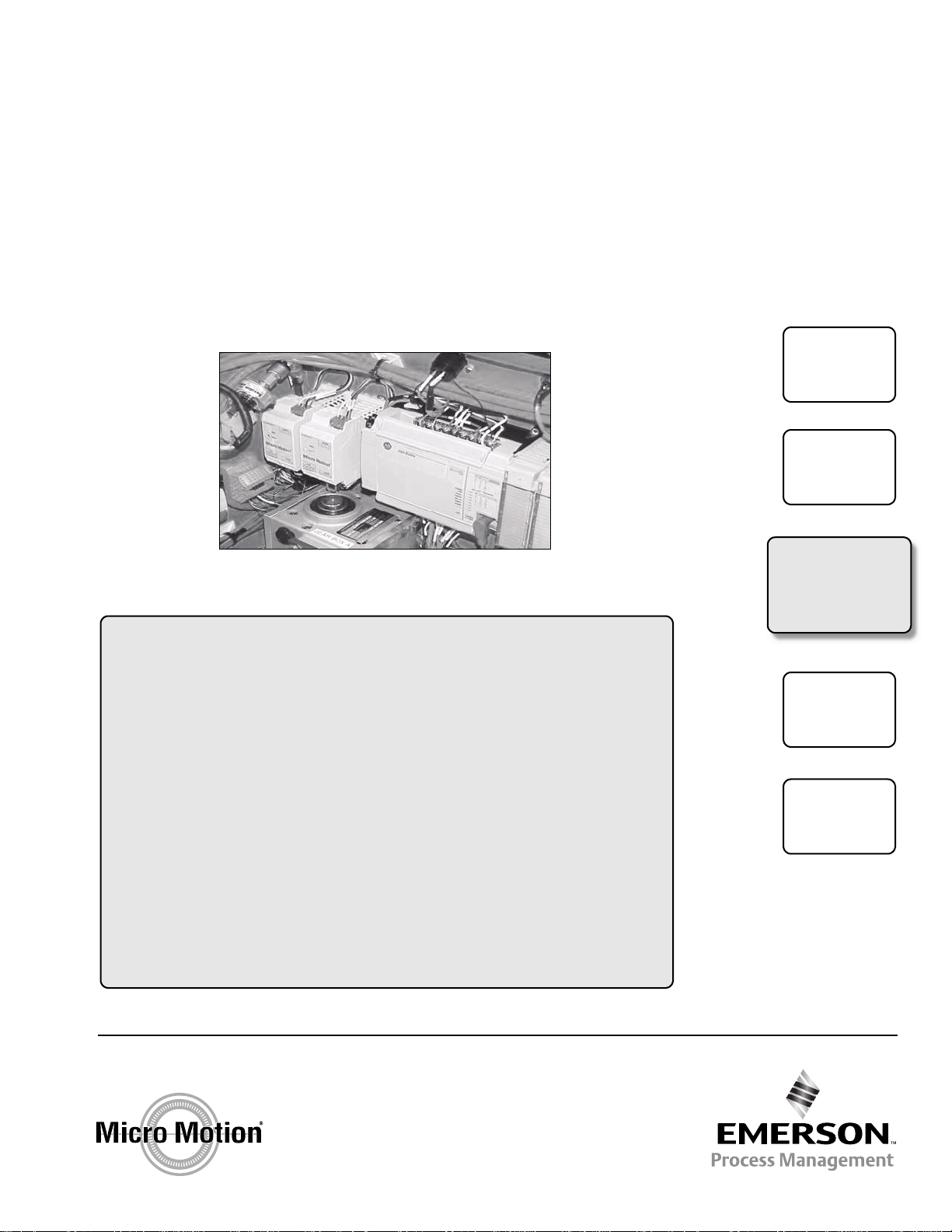
Product Data Sheet
Integrated architecture optimized for filling performance
• Discrete valve control for best repeatability
• Real-time density and temperature measurement for quality control
• Automatic overshoot compensation for on-set-point fills every time
• Compatible with CIP, SIP, and EHEDG requirements
Flexibility for simplified system design
• Compact size to maximize heads for rotary and linear filling systems
• Integral valve control for easy integration with control system
• Faster product turn-over due to cleanable sensor design
• Scalability to handle a wide range of container sizes and fillers with
a
single platf
orm
-00717, Rev. D
PS
April 2013
Micro Motion® Model 1500 Transmitter
with the Filling and Dosing Application
Micro Motion's Model 1500 transmitter with the filling and dosing application
offers all the benefits of MVD
™
technology, in a package specifically
designed for filling, dosing, and bottling processes.
1500
2500
2400S
1700
2700
3300
3350
Compact integral
transmitter
Versatile fieldmount transmitter
Compact controlroom transmitter
Frequency-input
discrete
controller
3500
3700
Integrated control
and measurement
platform
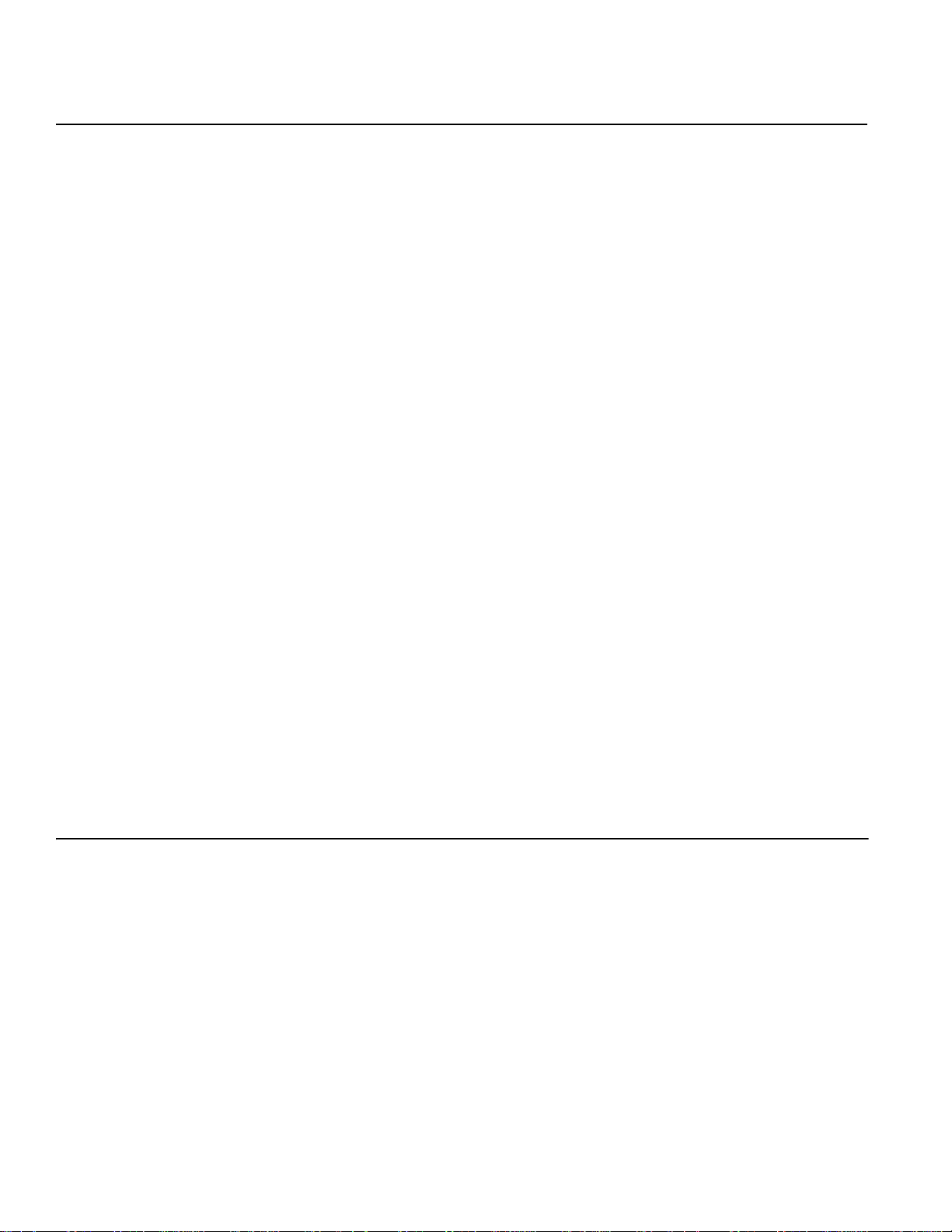
Micro Motion Model 1500 transmitter with the filling
Contents
Model 1500 platform . . . . . . . . . . . . . . . . . . . . . . . 3
Application architecture and process. . . . . . . . . . . 4
Accuracy, reliability, and repeatability . . . . . . . . . . 5
User interface . . . . . . . . . . . . . . . . . . . . . . . . . . . . 6
Electrical connections . . . . . . . . . . . . . . . . . . . . . . 7
Input/output signals . . . . . . . . . . . . . . . . . . . . . . . . 7
Digital communications . . . . . . . . . . . . . . . . . . . . . 8
Power supply. . . . . . . . . . . . . . . . . . . . . . . . . . . . . 8
Environmental limits . . . . . . . . . . . . . . . . . . . . . . . 8
Environmental effects . . . . . . . . . . . . . . . . . . . . . . 8
Hazardous area classifications . . . . . . . . . . . . . . . 9
Physical specifications . . . . . . . . . . . . . . . . . . . . . 9
Transmitter dimensions . . . . . . . . . . . . . . . . . . . . 10
Remote core processor dimensions . . . . . . . . . . 11
Ordering information . . . . . . . . . . . . . . . . . . . . . . 12
and dosing application
Micro Motion's Model 1500 transmitter with the filling and dosing application combines the benefits of
Micro Motion MVD
processes, and compatibility with a wide range of sensors, including hygienic models for CIP, SIP, and
EHEDG certification.
Filling and dosing application. Micro Motion’s new
patented filling and dosing application is packed
with features for precise control and delivery of
small quantities of fluids over broad ranges of
process conditions.
• Measure by mass or volume, with sensor
accuracies up to 0.05%, independent of
changes in temperature, density, or viscosity.
• Measure a wide range of both liquids and gases ,
including liquids with entrained air and
suspended solids. We have experience with
high-viscosity pastes, creams, emulsions, and
slurries.
• Instantly validate product quality using the
secondary density or temperature
measurement, eliminating the need for
expensive lab checks.
™
technology, a software package specially designed for filling, dosing, and bottling
• Overshoot compensation (OC) automatically
adjusts the valve closure signal to
accommodate changing process conditions
• User-selectable OC algorithms: never overfill,
never underfill, fixed, rolling average
• Select from a variety of standard measurement
units, or define your own
• Set up one-stage or two-stage filling, using
standard discrete (ON/OFF) valv es, or configure
the transmitter to control a three-position analog
valve
• Automatic or manual purge cycle
• Sensors suitable for both CIP and SIP cleaning,
enabling rapid product changeover
• Special update rate between transmitter and
sensor enables near-instantaneous response
2 Model 1500 Transmitter with the Filling and Dosing Appli ca tion
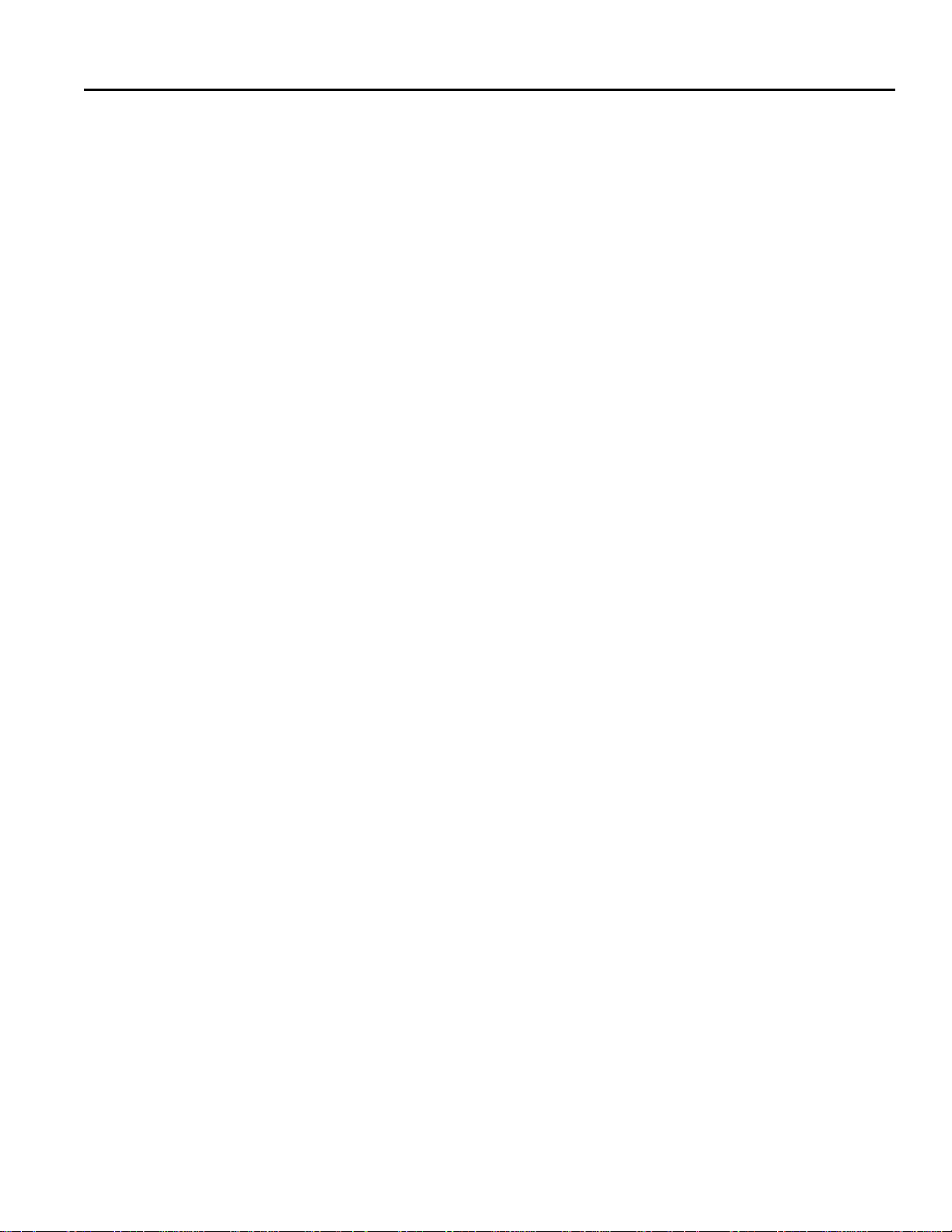
Model 1500 platform
Micro Motion’s popular Model 1500 transmitter
provides the platform for the filling and dosing
application.
The Model 1500 delivers a big transmitter in a small
package. Designed for DIN rail mounting, it
measures a tiny 4” × 4.5” × 1.8” — perfect for
carousels or skids.
Embedded MVD technology provides front-end
digital processing, for dramatically reduced signal
noise, faster response time, and expanded
diagnostics.
The Model 1500 connects to a wide range of
Micro Motion sensors, using standard 4-wire cable
for significantly reduced installation costs. And
because the sensor is powered by the transmitter,
there’s no need to run separate power to the sensor.
Three input/output channels can be configured for
mA output, discrete output, discrete input, or threeposition analog valve control.
Meter verification. Meter verification is an
application available in conjunction with
Micro Motion ELITE
core processor. Initiated by a user command, the
method measures mechanical characteristics of the
meter to a very high accuracy. When a change in
the structural stiffness of the sensor tubes is
detected, the device indicates the meter may no
longer meet factory specifications. The structural
integrity test verifies complete meter performance
from tube structure to electronics to signal
processing for complete performance certainty.
®
meters utilizing the enhanced
A status LED on the transmitter face indicates
transmitter health at a glance.
Model 1500 Transmitter with the Filling and Dosing Application 3
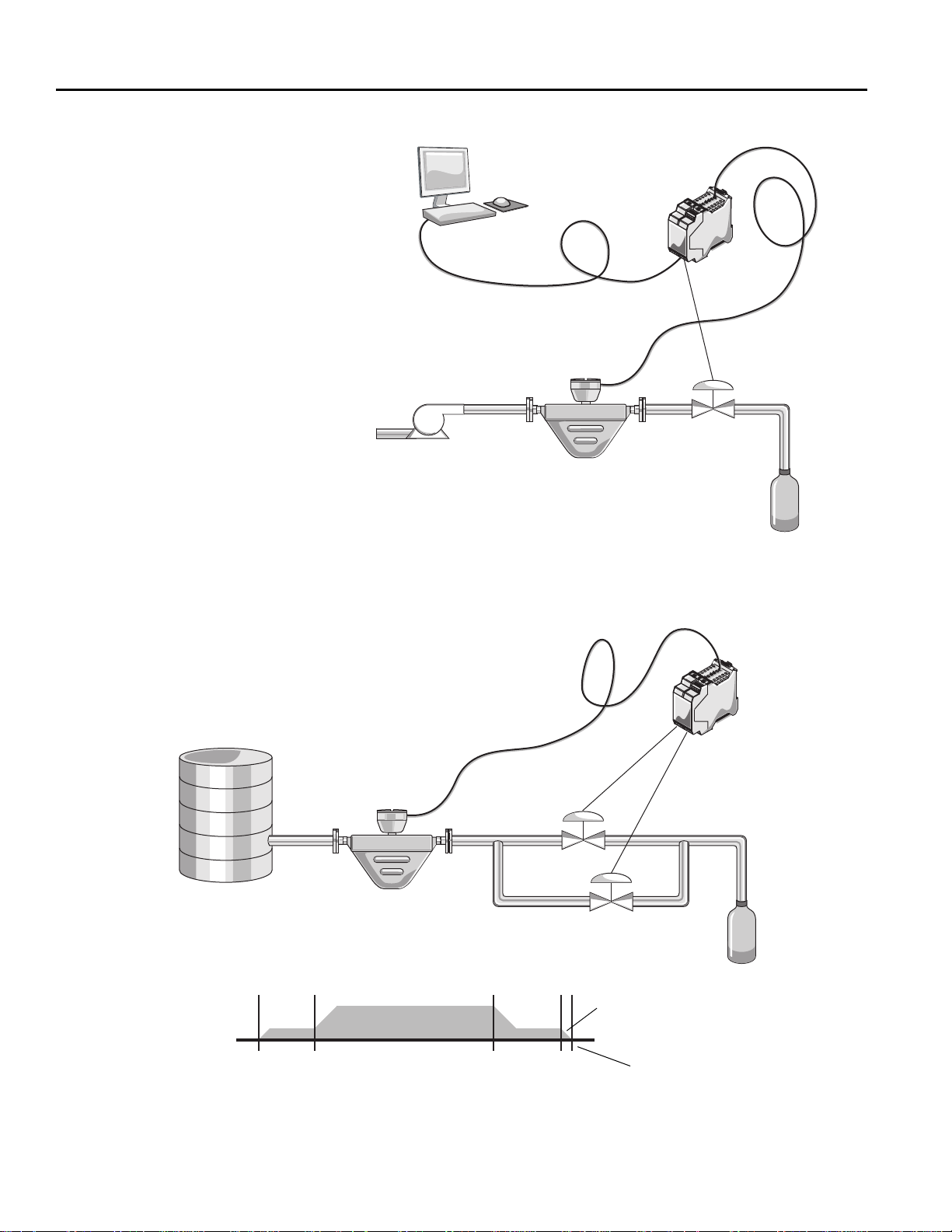
Application architecture and process
Discrete output
controlling primary valve
Discrete output controlling
secondary valve
Process data from sensor
Open
secondary
Close
primary
Compensation
TARGET
Close
secondary
FLOW
Open
primary
Overshoot Compensation
Modbus connection to host
Discrete output
controlling valve
Process data from sensor
Simple one-stage fill process
The host downloads the target to the
Model 1500, which opens the controlling
valve. When the target is reached, the
Model 1500 closes the controlling valve
and reports the totals to the host system.
Two-stage control
One of several two-stage control schemes is illustrated here. The
secondary valve opens to start the fill. The primary valve opens
and closes at user-configured points during the fill. The secondary
valve closes slightly before the target is reached, at a point
determined by the Overshoot Compensation feature.
4 Model 1500 Transmitter with the Filling and Dosing Appli ca tion
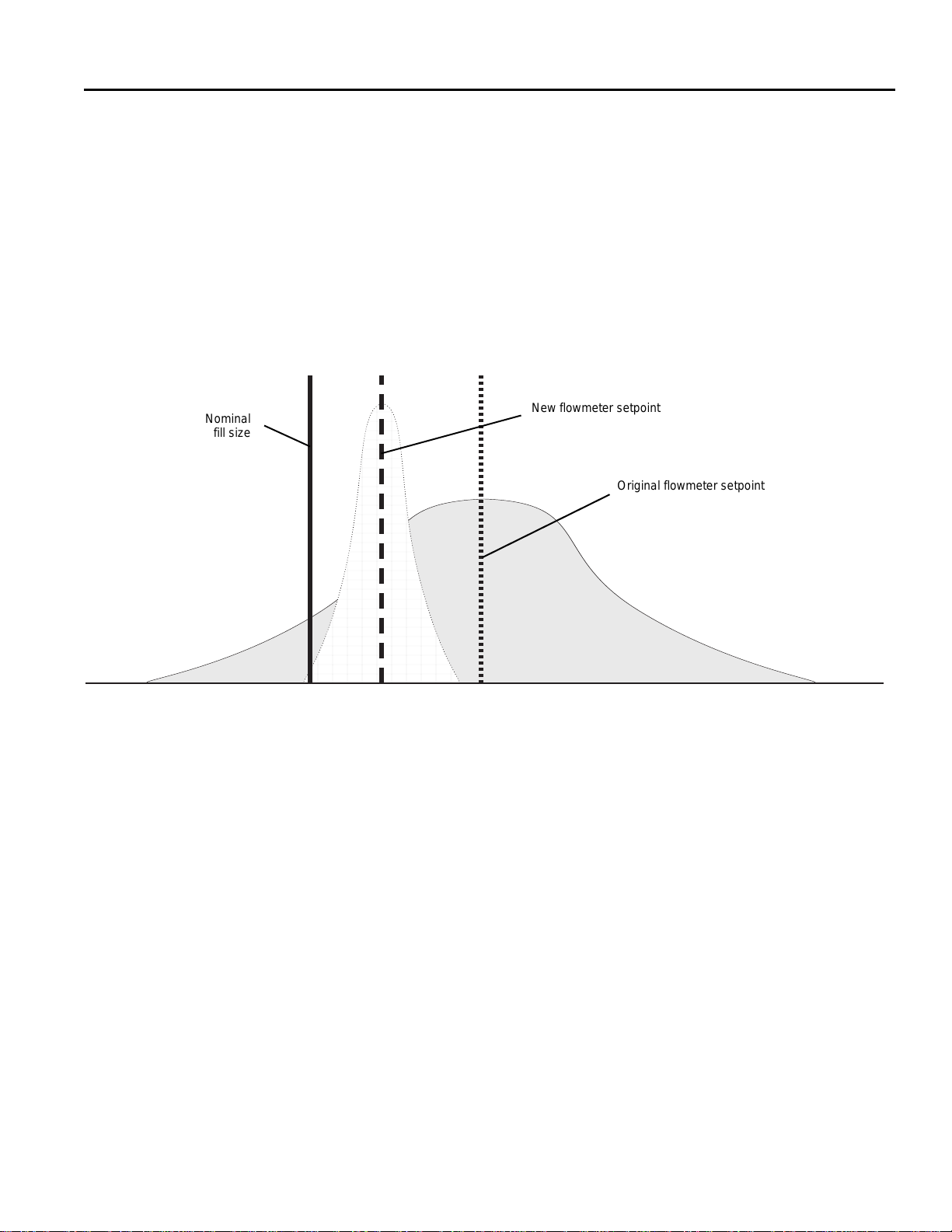
Accuracy, reliability, and repeatability
aaaaaaaaaaa
aaaaaaaaaaa
aaaaaaaaaaa
aaaaaaaaaaa
aaaaaaaaaaa
aaaaaaaaaaa
aaaaaaaaaaa
aaaaaaaaaaa
aaaaaaaaaaa
aaaaaaaaaaa
aaaaaaaaaaa
aaaaaaaaaaa
aaaaaaaaaaa
aaaaaaaaaaa
aaaaaaaaaaa
aaaaaaaaaaa
aaaaaaaaaaa
aaaaaaaaaaa
aaaaaaaaaaa
aaaaaaaaaaa
aaaaaaaaaaa
aaaaaaaaaaa
aaaaaaaaaaa
aaaaaaaaaaa
aaaaaaaaaaa
aaaaaaaaaaa
aaaaaaaaaaa
aaaaaaaaaaa
aaaaaaaaaaa
aaaaaaaaaaa
aaaaaaaaaaa
Nominal
fill size
Original flowmeter setpoint
New flowmeter setpoint
The Model 1500 transmitter with the filling and dosing application can be paired with any 4-wire or 9-wire
Micro Motion sensor to provide highly accurate and repeatable mass flow, volume flow, density, and
temperature measurements, all in real time.
Underfilling a container puts the producer at risk with customers and regulatory agencies, yet overfilling can
create significant cost issues, as well as possible problems with spills, safety, and cleanup. Reducing the
variation in product fills can have a significant impact on a manufacturer’s bottom line. Typical system
accuracies provide standard deviation of fills below 0.2.
A program that combines a Micro Motion measurement system with statistical quality control (SQC) analysis
can allow you to lower the fill target—“squeeze and shift”—and reduce overfill while still meeting regulatory
requirements.
Model 1500 Transmitter with the Filling and Dosing Application 5