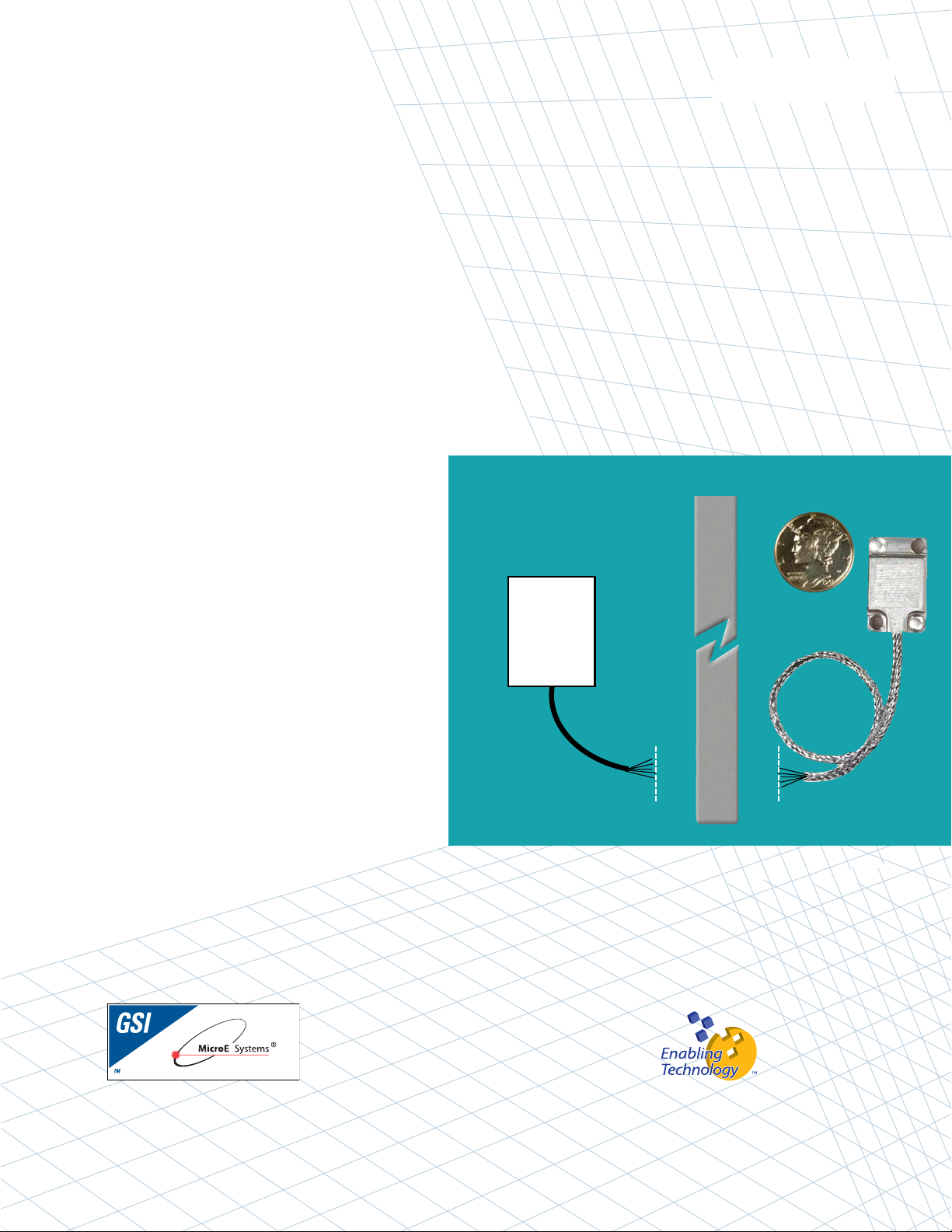
Mercury™1500V - Vacuum Rated
DDiiggiittaall OOuuttppuutt EEnnccooddeerr SSyysstteemm
IInnssttaallllaattiioonn MMaannuuaall
aanndd RReeffeerreennccee GGuuiiddee
Vacuum Wall
Customer
Controller
Preliminary 8/20/2008
Manual No. IM-M1500V Rev S7
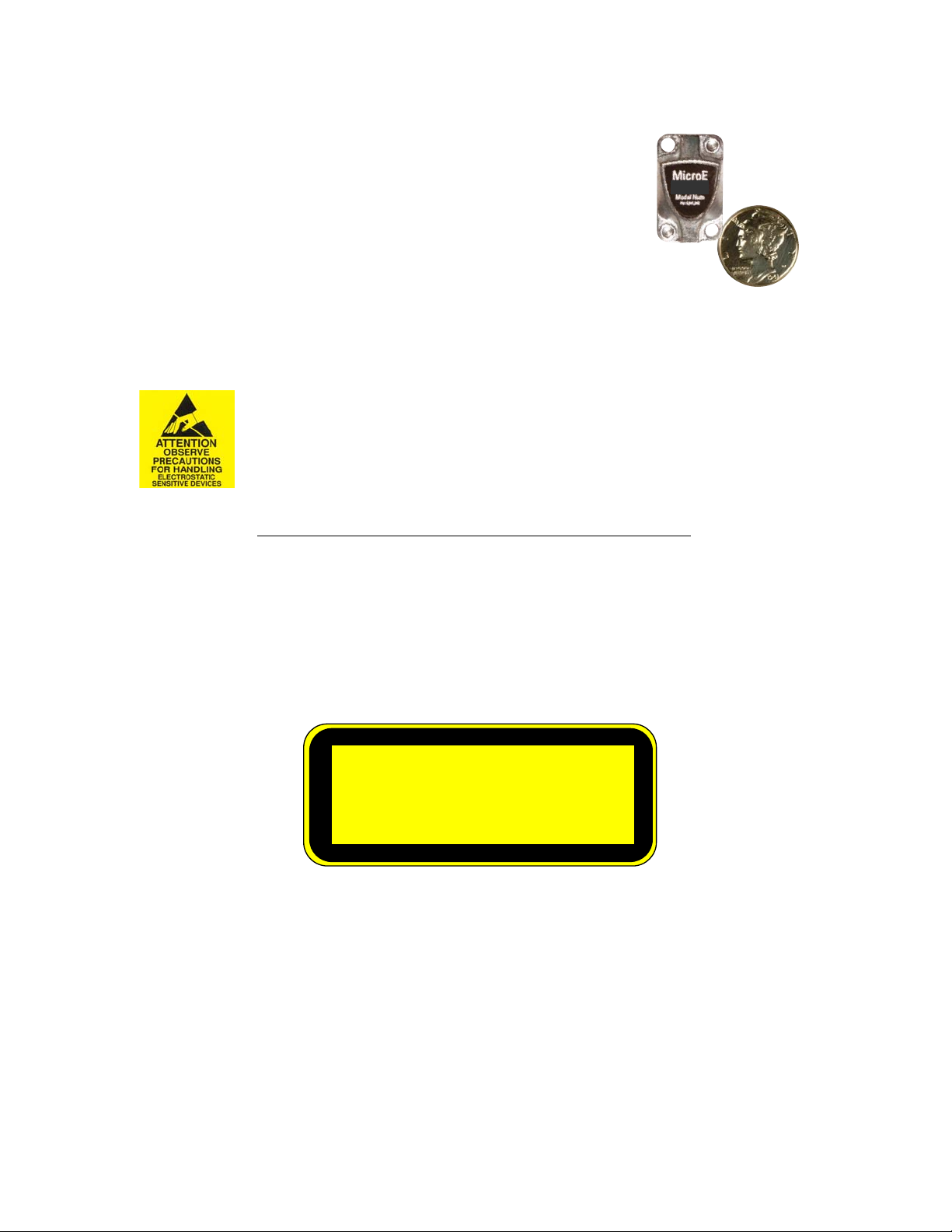
IInnttrroodduuccttiioonn
MicroE Systems was founded to advance encoder technology to
a level never before achieved. Our objective was to design encoder
systems that would be small enough to fit into densely packed OEM
equipment designs, affordable enough for cost-sensitive applications
and easy enough to enable installation, setup and alignment by
assemblers with little training. We are pleased to say that all of
these goals have been realized with the introduction of the Mercury
family of encoders.
Sensor shown
actual size
M10
PPaatteennttss
Covered by the following patents: US 5,991,249; EP 895,239; JP 3,025,237; US
6,897,435; and EP 1,451,933. Additional patents and patents pending may apply.
PPrreeccaauuttiioonnss
Follow standard ESD precautions. Turn power off before connecting the sensor.
Do not touch the electrical pins without static protection such as a grounded
wrist strap.
Do not touch the glass scale unless you are wearing talc-free gloves or finger
cots. Please read this installation manual for full instructions.
LLAASSEERR SSAAFFEETTYY IINNFFOORRMMAATTIIOONN::
MMeerrccuurryy && CChhiippEEnnccooddeerr
1
2
This product is sold solely for use as a component (or replacement) in an electronic product; therefore it is not
required to, and does not comply with, 21 CFR 1040.10 and 1040.11 which pertain to complete laser
products. The manufacturer of the complete system-level electronic product is responsible for complying with 21
CFR 1040.10 and 1040.11 and for providing the user with all necessary safety warnings and information.
MicroE encoders contain an infrared laser diode or diodes. Emitted invisible laser radiation levels have been
measured to be within the CDRH Class 1 range, which is not considered hazardous; however, to minimize
exposure to the diverging beam, the encoder sensor should be installed in its operational configuration in close
proximity to the encoder scale before power is applied.
• Invisible laser radiation; wavelength: 850 nm
• Max power 2.4 mW CW (4.8 mW CW for Mercury II™)
• CAUTION – The use of optical instruments with this product will increase eye hazard. DO NOT VIEW
DIRECTLY WITH OPTICAL INSTRUMENTS (MICROSCOPES, EYE LOUPES OR MAGNIFIERS).
• All maintenance procedures such as cleaning must be performed with the MicroE encoder turned off.
• Do not insert any reflective surface into the beam path when the encoder is powered.
• Do not attempt to service the MicroE encoder.
INVISIBLE LASER RADIATION
DO NOT VIEW DIRECTLY WITH OPTICAL
INSTRUMENTS
(MICROSCOPES, EYE LOUPES OR
MAGNIFIERS)
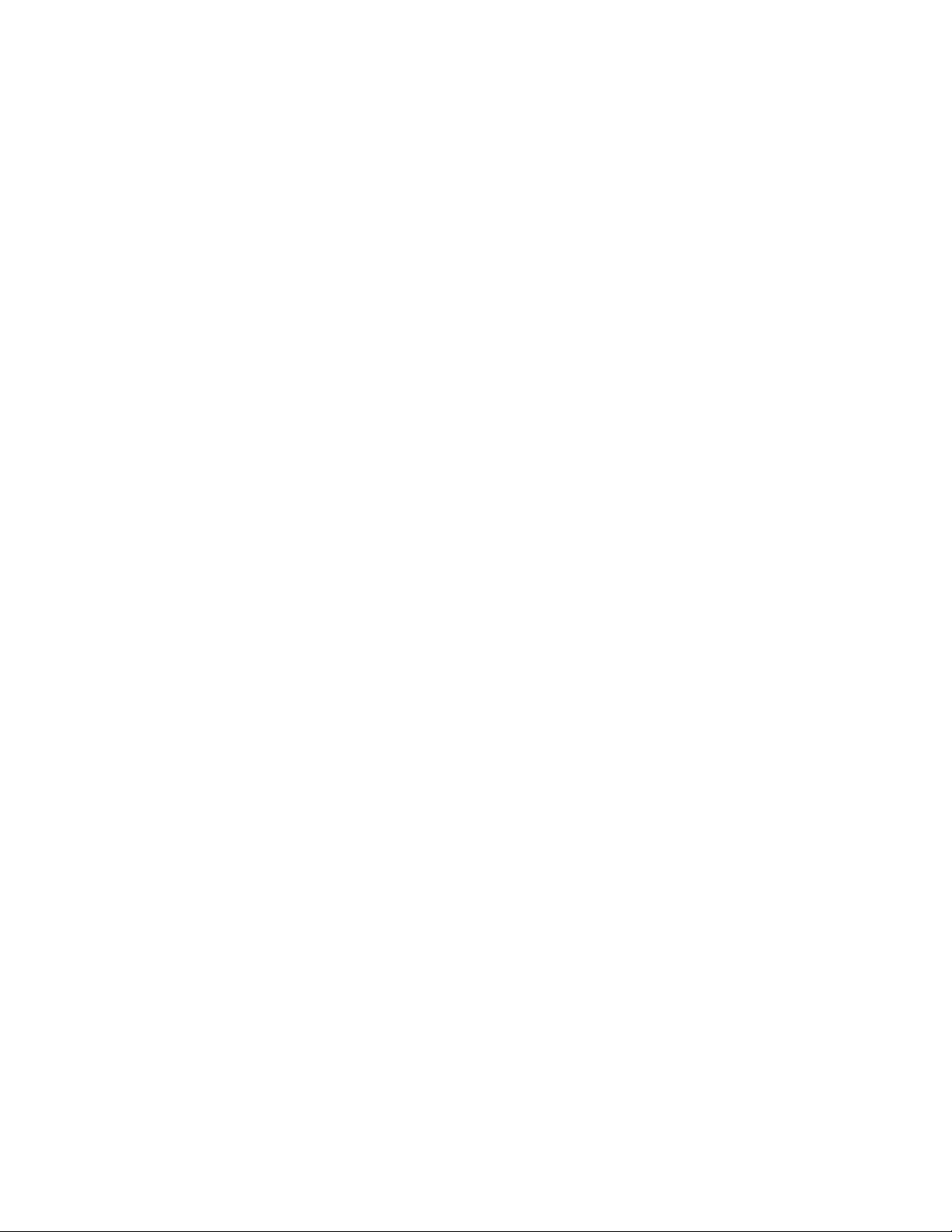
Page 1
TTaabbllee ooff CCoonntteennttss
SYSTEM ILLUSTRATION PAGE
Encoder with Linear scale 2
Encoder with Rotary scale 3
INSTALLATION INSTRUCTIONS
Using SmartPrecision Alignment Tool - Linear Scales
Mounting Encoder System 4
Alignment of Encoder System 5
Using SIN/COS Signals - Linear Scales
Mounting Encoder System 6
Alignment of Encoder System 7
Establishing an Index 7
Using SmartPrecision Alignment Tool - Rotary Scales
Mounting Encoder System 8
Alignment of Encoder System 9
Using SIN/COS Signals - Rotary Scales
Mounting Encoder System 10
Alignment of Encoder System 11
Establishing an Index 11
REFERENCE SECTION
Installation of Linear Scales 12
Grounding Instructions 13
Recommendations for Power 13
Customer Interface Cable Requirements 14
Output Signal description 15
ENCODER TROUBLESHOOTING
Selected Topics 16
Cleaning Scales 16
Contact MicroE Systems Back Cover
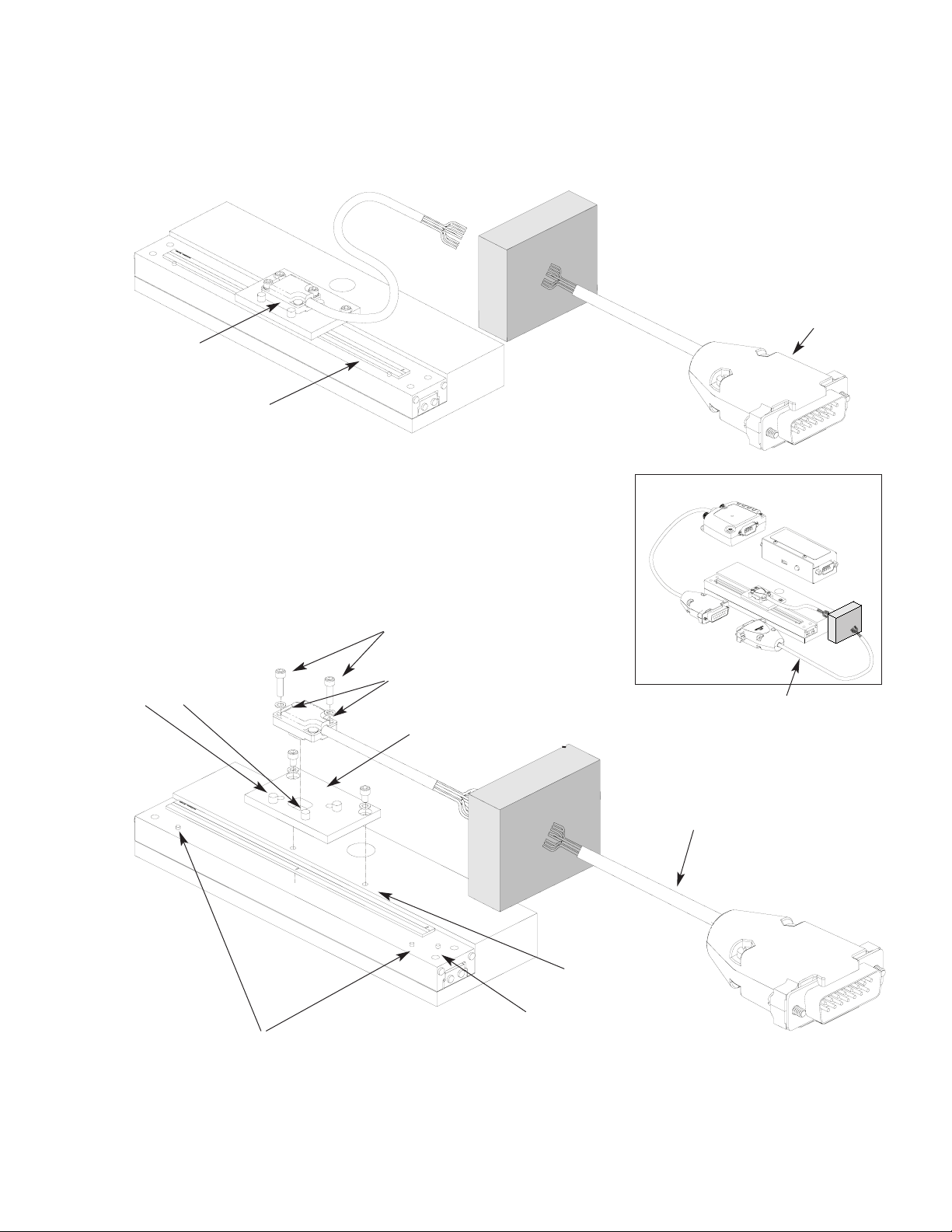
15 pin standard D-sub connector
MercuryTM1500V Encoder System
with Linear scale
EExxppaannddeedd VViieeww
End locator pin
Mounting screws & flat washers (2
needed per screw)
Bracket mounting holes (2)
Optional sensor benching pins (3)
Typical user-supplied
sensor mounting bracket
SSyysstteemm VViieeww
Shown with linear scale
Page 2
Scale reference datum;
example shown with benching pins
SmartPrecision Alignment Tool SSAT1500-V
Sensor mounting holes (2)
Sensor
Linear glass scale
(shown mounted on a linear slide)
Vacuum wall
Vacuum wall
Double shielded cable
Atmospheric Cable
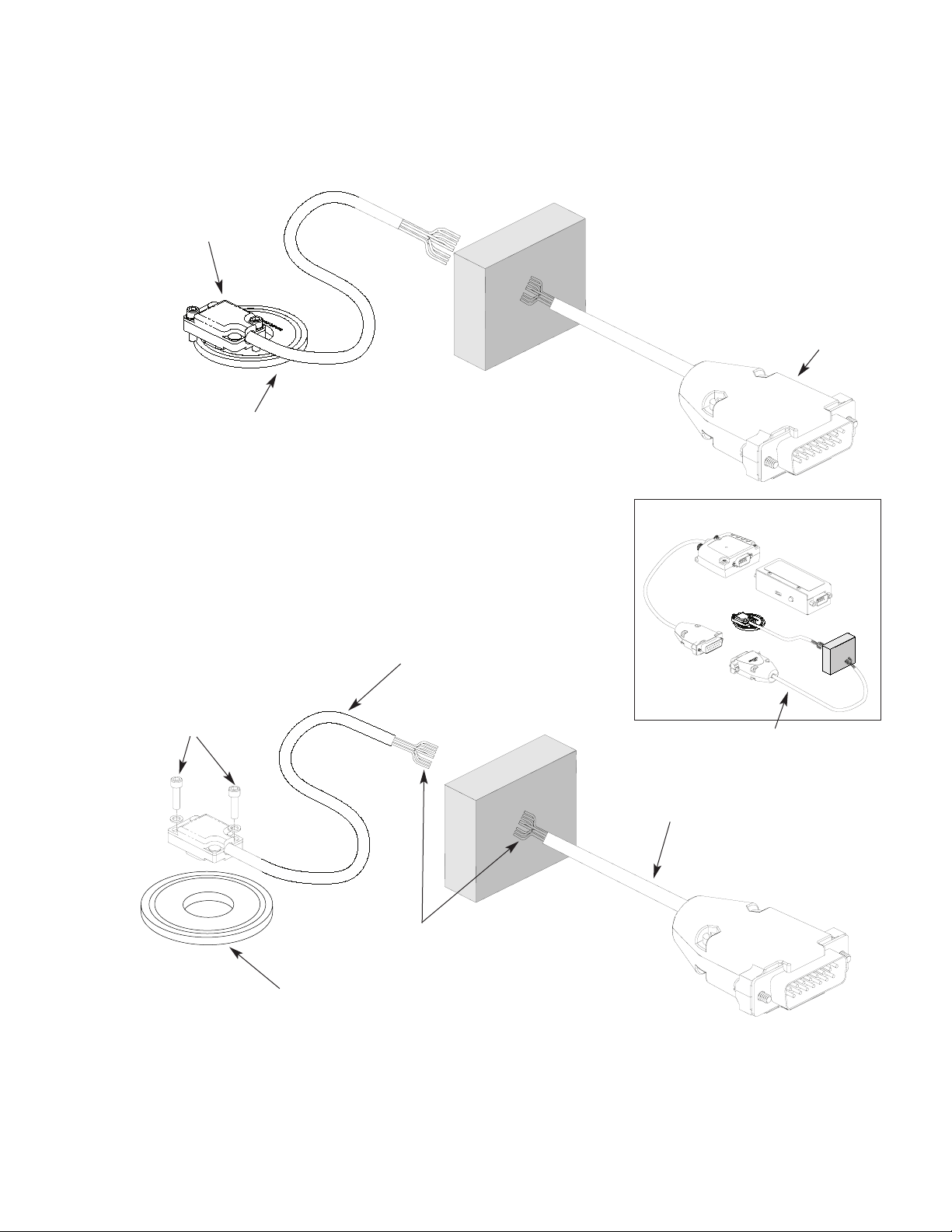
sensor
Mercury 1500V Encoder System
with Rotary scale
EExxppaannddeedd VViieeww
Top reflective rotary scale
Rotary glass scale
Page 3
Mounting screws & flat
washers (2 needed per screw)
SSyysstteemm VViieeww
Shown with rotary scale
Vacuum compatable cable
Flying leads
Vacuum wall
SmartPrecision Alignment Tool SSAT1500-V
Vacuum wall
15 pin standard D-sub connector
Atmospheric Cable
Double shielded cable
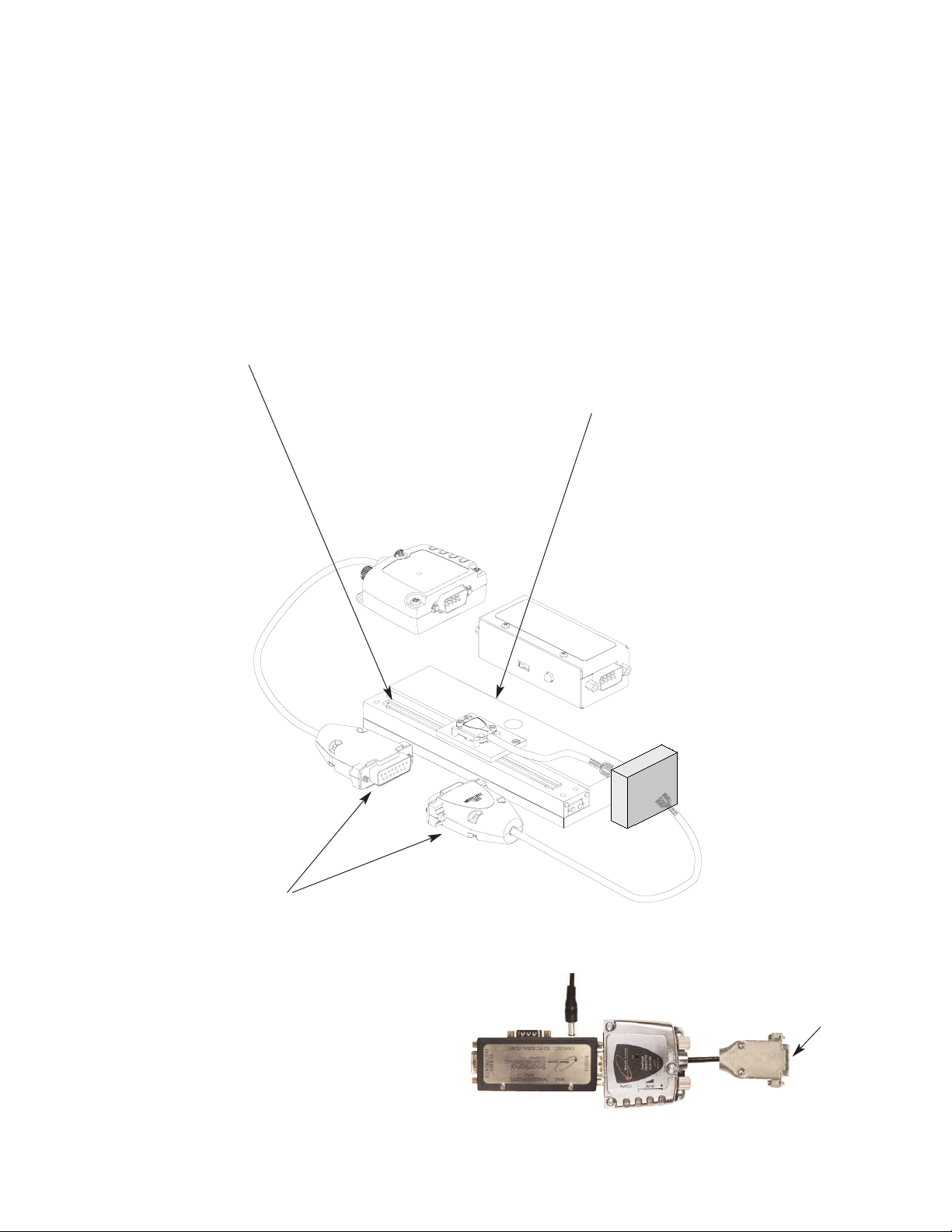
Installation Instructions
Linear Encoders - Using Alignment Tool - Mounting
1
2
Attach the scale to the base slide. Reference the preferred
datum on the interface drawing for either end or center
index orientation.
Depending on the mounting method, attach the scale
to the slide with adhesive. Refer to pg. 12 for details.
Be sure the grating surface of the scale faces the sensor.
Insure that there is no contact between these surfaces or
damage may result.
Be sure the source power is off before
connecting the SmartPrecisionTMII Alignment Tool.
Connect the M1500V to the SmartPrecision II
Alignment Tool. (The M1500V-AC Atmospheric
Cable shown in the illustration above is optional.
A customer-supplied cable may be used.)
3
Page 4
To M1500V encoder
To Power Supply
4
Connect the Alignment Tool to the
Computer Interface Adapter. Turn on
the power.
Install the sensor on your mounting surface
referencing the appropriate datum surface as
shown on the interface drawing. Use 2 washers
per mounting screw.
Benching pins may be used to locate the sensor
if the system mechanical tolerances are adequate.
See data sheet for alignment tolerances, or keep
mounting screws loose for sensor alignment if
benching pins are not used.