
High throughput efficiency
during complete filling or emptying
of a pallet channel
Collision-free pallet storage
and retrieval
Total system flexibility due to
handling different pallet types
Optimum utilisation of building
height through low racking
compartment height
Operational with virtually any
Jungheinrich stacker
Under Pallet Carrier UPC
Compact Storage Shuttle System
The Jungheinrich Compact Storage System
with UPC (Under Pallet Carrier) – consisting
of carrier, carrier truck and channel racking – facilitates optimum utilisation of
storage space. UPC racking provides room
in height and width for several pallet channels. The low height utilisation per channel
level also allows effective use of the available storage height. Any Jungheinrich
stacker with sufficient residual capacity
can be used as carrier truck.
The UPC is particularly effective during repeated storage and retrieval in the same
pallet channel – e.g. when buffering a
large quantity of the same pallets. The
UPC is put on the forks of the carrier truck
and used in the pallet channel where it
travels independently under the stored
pallets without being connected to the
carrier truck. After putting down the first
pallet on the UPC rail in the racking channel and pressing the start button on the
operating console, the process control carries out all necessary travel and lift move-
ments independently. Sensors recognise
the position of stored pallets. Storage and
retrieval of new pallets then takes place
with no danger of collision.
Operating terminal and process control
communicate via bi-directional radio link
run on the registration-free ISM band
(433 MHz). The operator picks up another
pallet while the carrier is travelling, puts it
down at the channel start and a new work
cycle can begin. Retrieval is carried out
accordingly.

Technical data in line with VDI 2198 as at: 07/2010
1.1 Manufacturer (abbreviation) Jungheinrich Jungheinrich Jungheinrich Jungheinrich 1.1
1.2 Manufacturer’s type designation UPC P1 UPC P2 UPC P5 UPC P6 1.2
1.3 Drive electric electric electric electric 1.3
1.4 Operator type hand
1.5 Load capacity / rated load Q (t) 1.5 1.5 1.5 1.5 1.5
Identification
1.6 Load centre distance c (mm) 400 500 500
1.9 Wheelbase y (mm) 667 845 845 984 1.9
2.1 Service weight incl. battery (see line 6.5) kg 190 212 212 225 2.1
2.2 Axle loading, laden front / rear kg 845 / 845 856 / 856 856 / 856 863 / 863 2.2
2.3 Axle loading, unladen front / rear kg 95 / 95 106 / 106 106 / 106 113 / 113 2.3
Weights
3.1 Tyres Polyurethan Polyurethan Polyurethan Polyurethan 3.1
3.2 Tyre size, front mm
3.3 Tyre size, rear mm
3.5 Wheels, number front rear (x = driven wheels) 2x / 2x 2x / 2x 2x / 2x 2x / 2x 3.5
3.6 Track width, front b10 (mm) 952 952 952 842 3.6
Wheels, Chassis
3.7 Track width, rear b11 (mm) 952 952 952 842 3.7
4.4 Lift h3 (mm) 27 27 27 27 4.1
4.15 Height, lowered h13 (mm) 150 150 150 150 4.15
4.16 Length of loading surface l
4.18 Width of loading surface b
4.19 Overall length (without load) l
4.21 Overall width b
4.26 Distance between wheel arms / loading surfaces b
Basic Dimensions
4.27 Width across guide rolls b
4.42 Pallet width b
4.43 Pallet length l
(mm) 800 1000 1000 1140 4.16
3
(mm) 1010 1010 1010 900 4.18
9
(mm) 864 1064 1064 1204 4.19
1
/ b2 (mm) 880 / 1034 880 / 1034 880 / 1034 770 / 924 4.21
1
(mm) 651 651 651 468 4.26
4
(mm) 1038 1038 1038 928 4.27
6
(mm) 1200 1200 1200 1140 4.42
12
(mm) 800 1000 1000 2) 1140 4.43
6
5.1 Travel speed, laden / unladen km / h 3.4 / 3.8 3) 3.4 / 3.8 3) 3.4 / 3.8 3) 3.4 / 3.8 3) 5.1
5.2 Lift speed, laden / unladen m / s 0.012 / 0.013 0.012 / 0.013 0.012 / 0.013 0.012 / 0.013 5.2
5.3 Lowering speed, laden / unladen m / s 0.014 / 0.013 0.014 / 0.013 0.014 / 0.013 0.014 / 0.013 5.3
1
) hand 1) hand 1) hand 1) 1.4
2
) 570 1.6
100 x 40 100 x 40 100 x 40 100 x 40
100 x 40 100 x 40 100 x 40 100 x 40
3.2
3.3
Performance Data
6.1 Drive motor rating S2 60 min kW 0.23 0.23 0.23 0.23 6.1
6.2 Lift motor rating at S3 15% kW 2 x 0.15 2 x 0.15 2 x 0.15 2 x 0.15 6.2
6.4 Battery voltage, nominal capacity K
E-Motor
6.5 Battery weight kg 46 46 46 46 6.5
5
V / Ah 2 x 12 / 58 2 x 12 / 58 2 x 12 / 58 2 x 12 / 58 6.4
8.1 Type of drive control impulse impulse impulse impulse 8.1
8.4 Sound level at the driver‘s ear according to EN 12 053 dB (A) 62 62 62 62 8.4
Others
1) Rail guided in pallet channel
2) Type P5 switchable, Euro pallet: c = 400 mm, l
3) Travel speed with load with Q = 1000 kg
= 800 mm
6
This specification sheet according to VDI regulation 2198 only provides technical values for the standard truck. Non-standard tyres, different masts, additional equipment, etc. could produce
other values. Right reserved for technical changes and improvements.
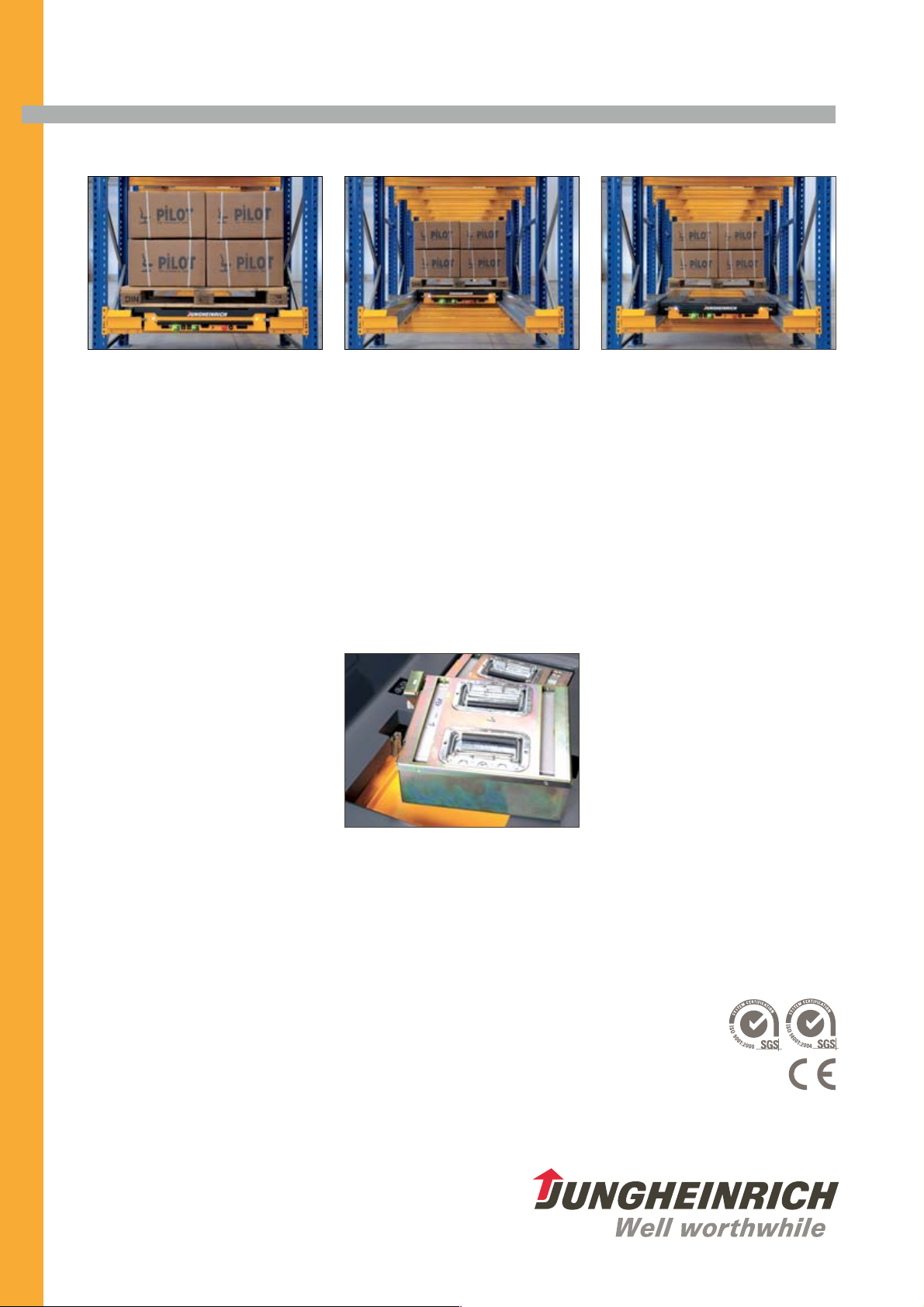
Make use of the advantages
Start of storage UPC returns to the beginning of the channel
Flexibility through handling different
pallet types
Different UPC variants facilitate the handling of different load carriers:
쐍
Euro pallets.
쐍
Industrial pallets.
쐍
Euro and industrial pallets in the same
racking system: Kombi carriers with sen-
for recognising the pallet size.
sors
쐍
Chemistry pallets.
쐍
Other variants are available on request.
Special functionalities
쐍
Stacking and retrieval according to LiFo
(Last-in-First-out) and FiFo (First-in-Firstout) is made easy.
쐍
When channel is to be emptied com-
pletely, e.g. for a supply order, the UPC
automatically takes each pallet in the
channel to the retrieval side from where
Storage
Easy battery change for 2- and 3-shift
operation
The battery charger of the carrier ensures
easy charging at any 230 V mains socket.
Dependent on the intensity of the application, the carrier with a fully charged
battery set is operational for eight to ten
hours. An additional second battery – in
combination with a battery changing station (optional) – significantly increases the
application time in 2- and 3-shift operations. Battery change is carried out in seconds due to the battery container.
UPC Compact Storage System in
cold store
Excellent space utilisation is of particular
importance for the efficient operation in a
cold store. UPC in cold store design (optional) allows application in temperatures
up to –30°C. A second battery set with
charging station noticeably increases operational availability.
User-friendly hand-held
radio terminal
쐍
Ergonomic mounting within the opera-
tor’s field of vision.
쐍
Simple operation and clear information
display.
쐍
Well-arranged function keys.
쐍
Numerous diagnostic functions for
Jungheinrich Service.
쐍
Mobile use is also possible.
it is picked up by a stacker and taken to
Goods-out.
쐍
This function is also possible if not all
but only a defined number of pallets are
to be retrieved.
쐍
Compressing: If there is no stacking or
retrieval (e.g. at shift end), all pallets
can automatically be brought to the retrieval side.
Easy battery change
Larger racking installations with
several carriers
Up to 69 different carriers can be dialled
up with a hand-held radio terminal for
larger racking installations. The operator
only needs to change the identification on
the hand-held terminal to contact the next
carrier.
Jungheinrich UK Ltd.
Head Office:
Sherbourne House · Sherbourne Drive
Tilbrook · Milton Keynes MK7 8HX
Phone 01908 363100
Fax 01908 363180
info@jungheinrich.co.uk
www.jungheinrich.co.uk
Jungheinrich
Plants, Sales and
Services Europe
ISO 9001/ ISO 14001
conform to the European
Safety Requirements.
Jungheinrich trucks
1404.GB.07.2010.r.s.