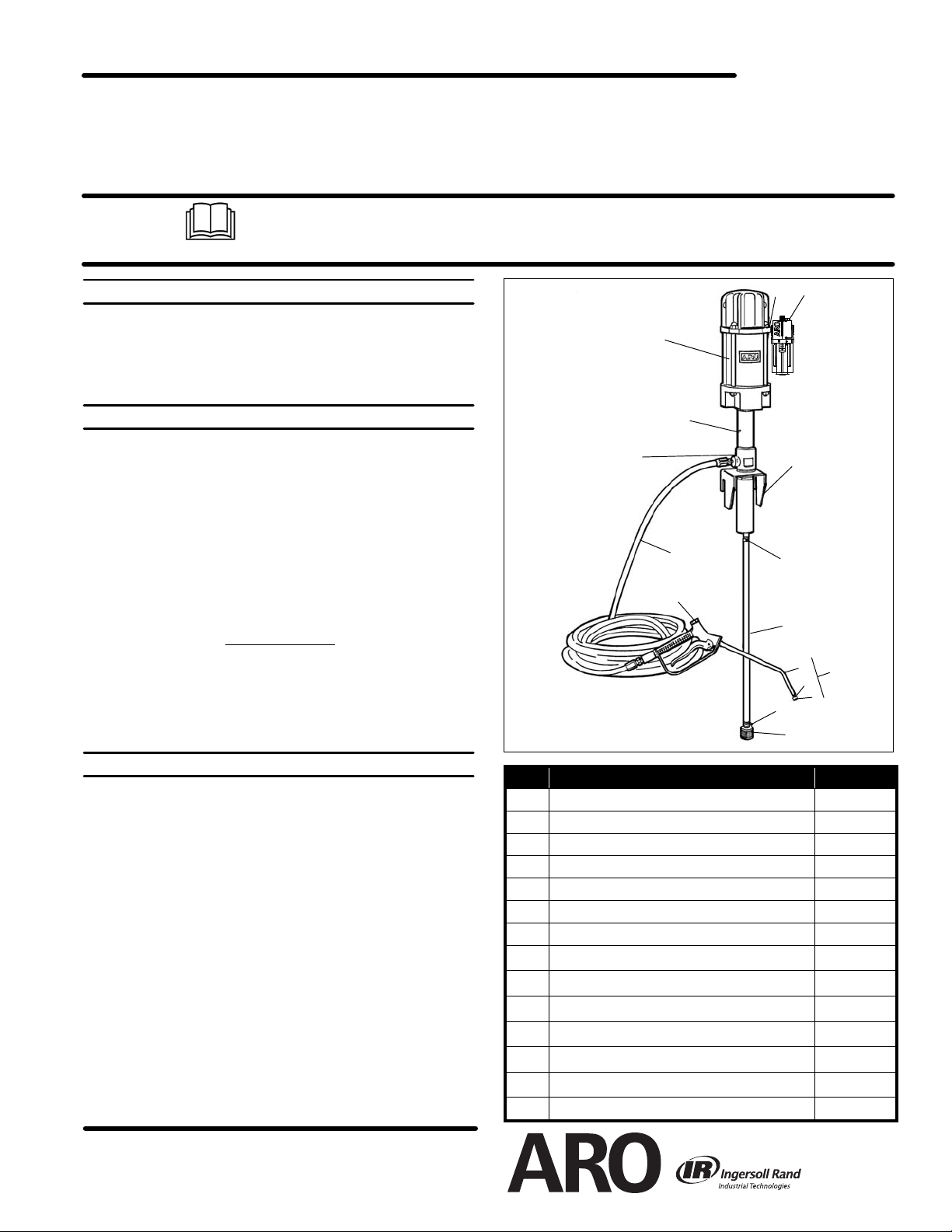
OPERATOR’S MANUAL
INCLUDING: OPERATION, INSTALLATION & MAINTENANCE
ALSO INCLUDE MANUALS: 6544X-X AIR MOTOR (97999 -64), 641523 CONTROL HANDLE (97999-230),
S-633 GENERAL INFORMATION MANUAL (PN 97999-625)
4-1/4” AIR MOTOR
10:1 RATIO
4” STROKE
It is the responsibility of the employer to place this information in the hands of the operator. Keep for future reference.
SERVICE KITS
613100 -1
WASH PUMP
DETERGENT PUMP ASSEMBLY
READ THIS MANUAL CAREFULLY BEFORE INSTALLING,
OPERATING OR SERVICING THIS EQUIPMENT.
613104
613100-1
613104
RELEASED: 4-10-67
REVISED: 8-26-10
N)
(REV.
A
B
• Use only genuine AROR replacement parts to assure compatible
pressure rating and longest service life.
• 637001 for repair of 61371-1 Lower Pump end.
• 61268 for repair of 65444-B Air Motor section.
• 637033 for repair of 641523 Control Handle.
SPECIFICATIONS
Model 613100-1...................
Type Air Operated, Wash Pump....................
Ratio 10:1....................
Air Motor Diameter 4-1/4” (10.795 cm).........
Stroke (Double Acting) 4” (10.16 cm).....
Air Inlet 1/2 - 14 NPTF - 1 (f).................
Air Exhaust 1-1/4 - 11-1/2 NPTF - 1 (f)..............
Material Outlet 3/8 - 18 NPTF - 1 (f)
.............
Material Inlet Barbed..............
Pump Construction Series 425 Stainless Steel.......
Dimensional Data SeeFigure1..........
PERFORMANCE
Air Inlet Pressure Range 0 - 150 p.s.i. (0 - 10.3 bar).....
Fluid Pressure Range 0 - 1500 p.s.i. (0 - 103 bar).......
Displacement In
Cycles Per Gallon 21 (5.5 L)..........
Maximum Delivery / Min. 3.9 Gallons (14.8 L).....
Accessories Available: 61113 Wall Mount Bracket......
3
Per Cycle 11.0 (.18 L)...
GENERAL DESCRIPTION
The Aro model 613100-1 and 613104 wash pump has been designed for
heavy duty cleaning with detergents, caustics, and dilute acid type cleaners. (The model 613100-1 basic pumps come without accessories).
The 10:1 ratio double acting pump section is separated from the air motor to prevent any cleaning solution from coming in contact with and
damaging the air motor.
All metal parts in the pumping section are manufactured from 316 stainless steel or “K” monel, the packing and “O”rings are manufactured from
Nitrile, and the packing back-ups and portions of the material piston are
manufactured from acetal resins.
Packings, “O” rings, and material pistons of virgin PTFE and packing
back-ups of glass filled PTFE are available on special request.
The 4-1/4 inch air motor is of the double acting reciprocating type. The
valving in the air motor uses “D” type valves and is mechanical with a
pneumatic assist.
The 613104wash pump may be directly mounted in the twoinch bung of
a standard 55 gal. drum or,when using the 61113 mounting bracket, the
pump can be mounted on the wall or in a 55 gal. open head drum. (The
61139 suction tube comes with a 100 mesh screen).
65444-B AIR MOTOR
See Operators Manual
Oil Daily
GEAR OIL
WITH SAE 90W
61371-1LOWER
PUMP END
F
G
FIGURE 1
E
J
H
K
P
N
Q
R
L
M
ITEM DESCRIPTION PART NO.
A Nipple Y27-4-N
B Airline Lubricator L36341-110
E Pump Bracket Assembly (2” Bung) 61113
F Hose Assembly (3/8 I.D. 2 Fabric) 622427-40
G Control Handle Assembly 641523
H Suction Tube Assembly (Includes J, K, L & M) 61139-1
J Hose Clamp 61204-1
K Tube 92249-26
L Hose Clamp 76315
M Screen Assembly 61138
N Bent Pipe Assembly (Includes P, Q & R) 61133
P Bent Pipe 76821
Q Nozzle Cover 76330
R Spray Tip TP6250-18
INGERSOLL RAND COMPANY
209 NORTH MAIN STREET -- BRYAN, OHIO 43506
(800) 495--0276 D FAX (800) 892--6276
www.ingersollrandproducts.com
E2010
CCN 99711491
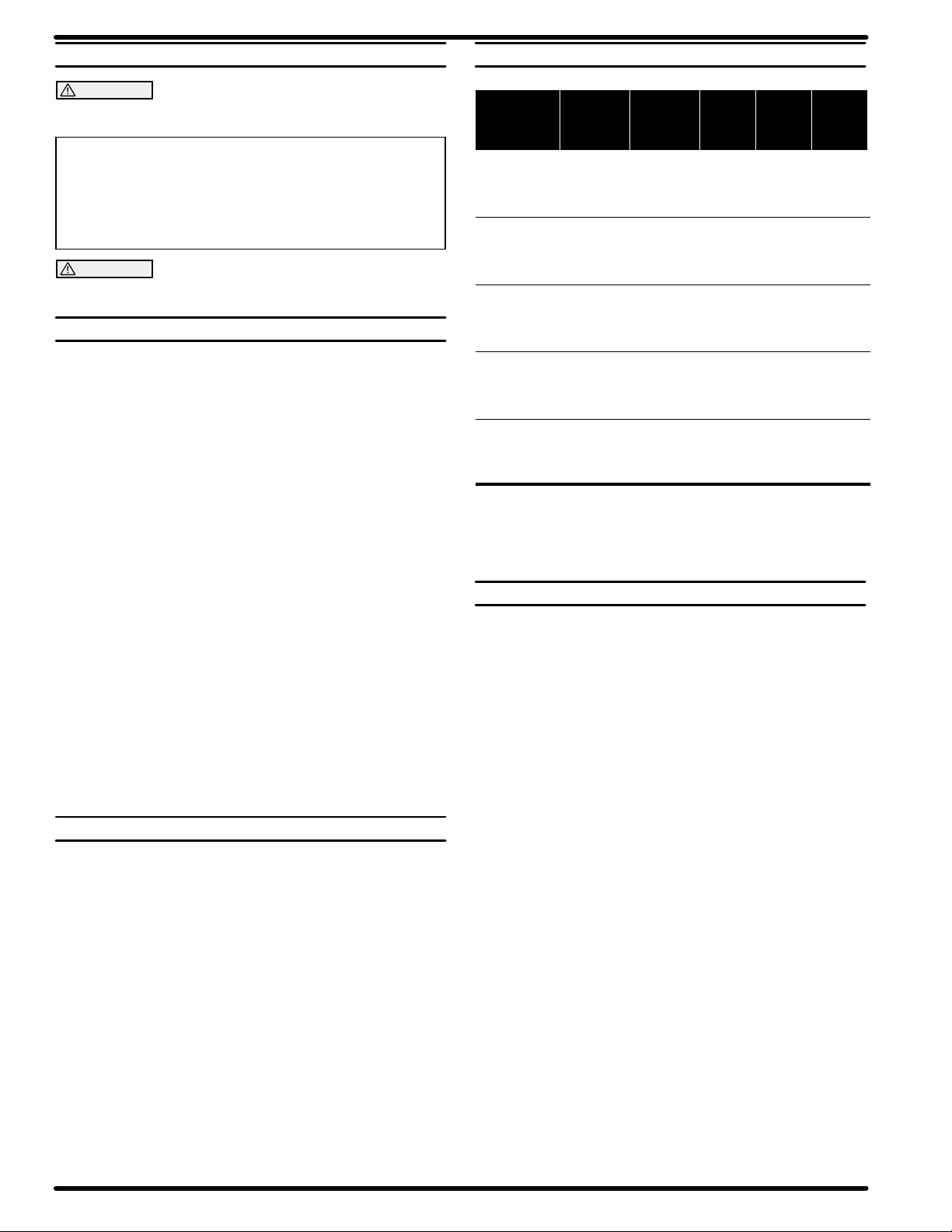
OPERATING PRECAUTIONS
PUMP PERFORMANCE CHART
WARNING
HAZARDOUS PRESSURE. Do not exceed maxi-
mum operating pressure of 1500 p.s.i. (103 bar) at 150 p.s.i.
(10.3 bar) inlet air pressure.
INLET PRESSURE TO PUMP MOTOR
Pump ratio is an expression of the relationship between the pump motor area and the
lower pump end area. EXAMPLE: When 150 p.s.i. (10.3 bar) inlet pressure is supplied
to the motor of a 10:1 ratio pump it will develop a maximum of 1500 p.s.i. (103 bar) fluid
pressure (at no flow) - as the fluid control is opened, the flow rate will increase as the
motor cycle rate increases to keep up with the demand.
WARNING
PUMP RATIO X
Refer to general information sheet for additional
MAXIMUM PUMP
=
FLUID PRESSURE
safety precautions and important information.
OPERATING INSTRUCTIONS
1. Fill air line lubricator bowl with SAE 90 gear oil.
2. Oil the lower pump assembly section by squirting SAE 90 Gear Oil
into the two holes marked “Oil Daily”.
3. Fill the cleaning solution container with clear water.
4. Connect the air supply line to the air line lubricator.
5. Openthe (G) control handle assembly by squeezing the trigger until
water sprays out the spray tip.
6. Adjust air line oiler to approximately 1 drop every 2 minutes by turning adjusting screw clockwise for less flow.
7. Close control handle.
8. Addthe proper amount of cleaning solution to cleaning solution container. Insert the (N) bent pipe assembly into the cleaning solution
and open the control handle assembly. Continue holding the control
handle open until spray from the (N) bent pipe assembly has thoroughly mixed the cleaning solution.
NOTE:
• Mostcleaning solutionswill performmore efficientlyin warm wa-
ter.
• Powdereddetergents willbe easier to mix ifthey are dissolved in
a container of hot water first.
• Consult chemical manufacturer’s recommendations for proper
mixing and concentration
9. Theair supply line should be disconnected when the wash pumpassembly is not in operation.
CAUTION: DO NOT ALLOW THE AIR MOTOR TO RUN AFTER THE
SOLUTION CONTAINER IS EMPTIED.
CLEANING INSTRUCTIONS
Use the cleaning instructions supplied by the cleaning chemical supplier.
General cleaning instructions for detergents and caustics: (In the event
cleaning instructions are not supplied by chemical supplier).
1. Lightly and rapidly cleaning solution to object being cleaned.
2. Let cleaning solution stand on the object for two or three minutes.
3. Starting from the bottom up, clean the object with cleaning solution
holding the spray tip 6 to 8 inches away from object and at approximately 45_. The 45_ angle will produce a chiseling effect for better
cleaning.
4. Rinse the object thoroughly with clean water from the top down.
General cleaning instructions for aluminum brightening: (If not supplied
by chemical supplier).
1. Apply aluminum brightener to an area of approximately 100 square
feet (approximately 3 semi-trailer panels) from the bottom up.
2. Let the brightening solution soak until light foaming occurs on the
aluminum.
3. Rinse thoroughly with clear clean water from the top down.
CAUTION: Brightening solution will etch glass and will burnaluminum if permitted to soak after the light foaming occurs.
Operating
Air Pressure
(PSIG)
Spray Tip
Orifice
Pump Back
Pressure
(PSIG)
Air
Usage
(CFM)
Pump
Speed
(CPM)
Flow
Rate
(GPM)
.042 410 5.66 20 .94
50 .052 370 6.62 24 1.16
.062 330 10.35 35 1.72
.042 640 8.75 23 1.09
75 .052 600 12.96 32 1.53
.062 500 19.85 47 2.25
.042 880 13.34 27 1.25
100 .052 800 19.78 37 1.81
.062 720 28.80 56 2.68
.042 1080 20.00 31 1.44
125 .052 1000 26.50 42 2.00
.062 920 40.00 63 3.00
.042 1300 25.50 34 1.59
150 .052 1200 34.32 47 2.19
.062 1100 50.60 68 3.25
PSIG = Pound per square inch gage CPM = Cycles per minute
CFM = Cubic Feet per minute GPM = Gallons per minute
NOTE: Pump should not be operated continuously at speeds in excess
of 60 cycles per minute.
MAINTENANCE
The basic pump consists of two major components: 1. Air Motor, 2. Lower Pump End. The air motor is connected to the lower pump end by a
spacer tube - this allows access for lubricating the upper packing gland
in the lower pump end, and to prevent air motor contamination because
of normal wear and eventual leakage through material packing gland.
The air motor is removable and is to be serviced separately.Refer to air
motor manual for service and parts.
• Periodically flush entire pump system with a solvent that is compatible with the material being pump.
• Periodicallyinspect and replace if necessary the (M) screen assembly on the bottom of the (H) suction tube assembly.
• Refer to Disassembly Procedures of air motor and lower pump end
(see Page 3 and 4) for correct breakdown.
• Disassembly should be done on a clean work bench with clean
cloths to keep parts clean.
• If replacement parts are necessary, consult drawing containing
parts for identification.
• Before assembling, lubricate parts where required. When assembling “O” rings or parts adjacent to “O” rings, care must be exercised
to prevent damage to “O” rings and “O” ring groove surfaces.
Daily Maintenance
1. The airline lubricator should be filled with SAE 90 weight gear oil.
2. Maintain the oil level on the packings in the lower pump assembly.
Use SAE 90 weight gear oil.
3. The air line should be disconnected from the air motor if the pump
sits idle for long periods.
PAGE 2 OF 6 613100-X