
OPERATOR’S MANUAL 6544X-X
INCLUDING: SERVICE KITS, TROUBLESHOOTING, PARTS LIST,
6546X-X
DISASSEMBLY & REASSEMBLY.
4-1/4” AIR MOTORS
6544X-X (4” STROKE) and 6546X-X (6” STROKE)
Also covers 61268 service kits
READ THIS MANUAL CAREFULLY BEFORE INSTALLING,
OPERATING OR SERVICING THIS EQUIPMENT.
It is the responsibility of the employer to place this information in the hands of the operator. Keep for future reference.
THIS MANUAL COVERS THE FOLLOWING MODELS
MODEL
65440 65442-B 65444-2-B 65462
65441-B 65444-B 65445-B 65465-B
Also covers obsolete and cancelled models: 61777, 65420-1, 65443-B, 65443-2-B, 65444-1B, 65465-1-B and 65466.
SERVICE KITS
Use only genuine ARO® replacement parts to assure com-
patible pressure rating and longest service life.
61268 for general repair of all 4-1/4” air motors.
RELEASED: 2-26-82
REVISED: 11-28-07
(REV. U)
GENERAL DESCRIPTION
WARNING
PRESSURE AS INDICATED ON PUMP MODEL PLATE.
WARNING
FOR ADDITIONAL SAFETY PRECAUTIONS AND IMPORTANT INFORMATION.
This manual only covers the air motor section. It is one of
four documents which support an ARO pump. Replacement copies of these forms are available upon request.
650XXX-X Pump Model Operator’s Manual.
General Information for Air Operated or Hydraulically
Lower Pump End Operator’s Manual.
Air or Hydraulic Motor Operator’s Manual.
The 4-1/4” air motor is a general purpose power unit and
is used with many 2-ball, 4-ball and chop check pumps. It
utilizes tie rod type construction for easy breakdown and
it connects to the various lower ends via tie rods for easy
operation. Consult pump model operator’s manual for
speci c instructions. It is recommended that a mu er be
connected to the exhaust port to reduce noise to acceptable OSHA standards.
Filtered and oiled air will allow the air motor to operate
more e ciently and yield a longer life to operating parts
and mechanisms. A filter capable of filtering particles
larger than 50 microns should be used with an oiler. Keep
the oiler supplied with a good grade of S.A.E. no. 90W
non-detergent gear oil, set at a rate not to exceed 1 or 2
drops per minute.
NOTICE: Do not operate the air motor above the recommended air pressure of 150 p.s.i. (10.3 bar) or 75 cycles
per minute. The air motor may be rated di erently in the
next assembly. Check the pump model plate.
DO NOT EXCEED MAXIMUM OPERATING
REFER TO GENERAL INFORMATION SHEET
Operated Pumps.
Figure 1
MAINTENANCE
The air / hydraulic motor is completely separate from the
lower pump end. This helps to keep the motor from being
contaminated by the material being pumped. Periodically,
ush entire pump system with a solvent that is compatible
with the material being pumped.
Keep solvent cup lled with this compatible solvent. This will
keep material from drying on the piston rod, which would
drag thru the packings, ruin them and eventually scour the
piston rod.
Provide a clean work surface to protect sensitive internal
moving parts from contamination from dirt and foreign matter during disassembly and reassembly.
Before reassembling, lubricate parts as required. When assembling “O” rings, or parts adjacent to “O” rings, exercise
care to prevent damage to “O” rings and “O” ring groove surface.
INGERSOLL RAND COMPANY LTD
P.O. BOX 151 ONE ARO CENTER BRYAN, OHIO 43506-0151
(800) 276-4658 FAX (800) 266-7016
© 2007 CCN 81582769
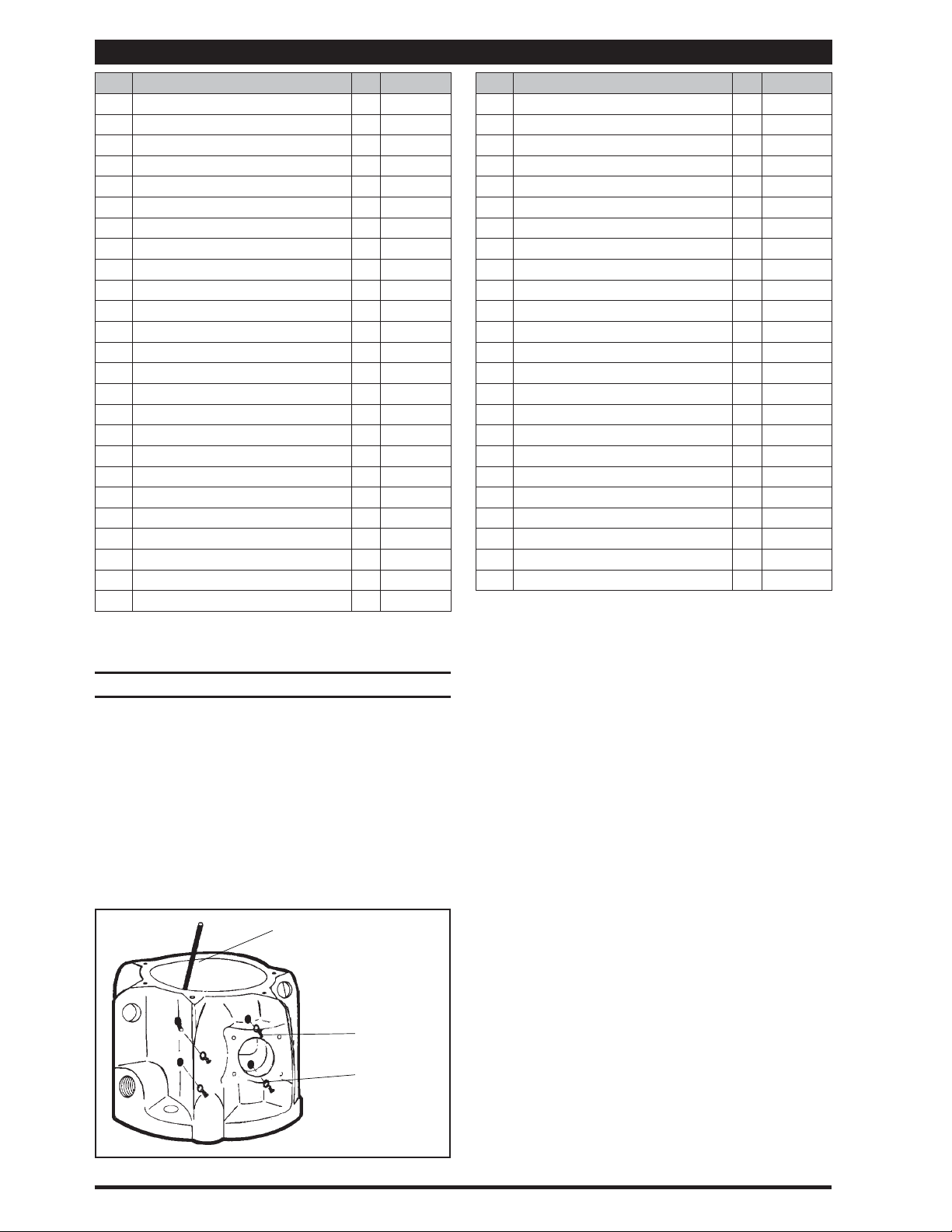
PARTS LIST / 6544X-X & 6546X-X
Item Description
1 Screw
2 De ector
3 Screw
4 Screw
5 Washer (4) 90084
6 Screw
7 Washer
8 Air Motor Cap (1) 90078
9 Valve Guide (1) 90093
10 Gasket (1) 90083-1
11 Insert (1) 90097
12 Valve Plate and Pin Assembly (1) 65028
12a Roll Pin
13 Insert Spring Assembly (1) 65032
14 Valve Insert (1) 90796
15 Gasket (1) 90091
16 “O” Ring
17 Washer (1) 91344
18 “O” Ring
19 Head Assembly (1) 65889
20 “U” Cup
21 “O” Ring
22 Screw
24 Piston Assembly (1) 61851
27 Rod Assembly
“Smart Parts”, keep these items on hand in addition to the service kits
for fast repair and reduction of downtime.
Includes item (12a) roll pin (qty 2).
(size)
(#8 - 32 x 7/8”) (not shown)
(not shown)
(#10 - 24 x 1/2”)
(#8 - 32 x 3/4”)
(1/4” - 28 x 3/4”)
(1/4” i.d.)
(3/32” o.d. x 3/4” long)
(1/16” x 1-3/8” o.d.)
(1/16” x 3/4” o.d.)
(3/16” x 1-3/8” o.d.)
(1/8” x 4-1/4” o.d.)
(#8 - 32 x 3/8”)
(see chart, page 4)
(Qty) Part No.
(4) Y136-90-S
(1) 90409
(6) 95956827
(4) Y19-89-S
(2) Y119-49-C
(2) Y14-416
(2) Y178-26-S
(2) Y325-26
(2) Y325-16
(1) Y186-51
(2) Y325-242
(4) Y136-85-S
(1) - - - - -
DISASSEMBLY OF AIR MOTOR
NOTE: All threads are right hand.
Place motor in up stroke position. This can be accom-
1.
plished by pushing (48) rod toward the top of the air
motor.
Remove four (1) screws from (2) de ector.
2.
Remove (2) de ector.
3.
Remove six (3) screws from (8) air motor cap.
4.
Remove (8) air motor cap and (10) gasket.
5.
Loosen four (4) screws (which hold (12) valve plate and
6.
(9) valve guide) until (9) valve guide can be removed by
pulling upward (see gure 9, page 6).
Allen Wrench
(Use an Allen wrench to
push out screws and
washers as shown.)
Item Description
28 Cylinder
29 Tube
30 Base and Bearing Ass’y
31 Valve Piston (1) 92394
32 Washer (1) 90105
33 Gland (1) 91006
34 Seal (1) 91007
35 “O” Ring
36 Extension Rod (1) 90080
38 Adapter (1) 92393
39 Gland (1) 90114
40 Washer (1) 91345
41 “O” Ring
42 Bolt
43 Snap Ring
44 Washer
45 “U” Cup
46 Washer
47 Nut
48 Piston Rod
49 “O” Ring
50 Ground Lug (1) 93006
51 Ground Label
Items included in Service Kit 61268
Remove four (4) screws and four (5) washers from (19)
7.
head assembly by pressing outward with a small allen
wrench, as illustrated in gure 2.
With the aid of a screwdriver, unhook the legs of (13) in-
8.
sert spring assembly from the bottom of (12) valve plate.
Remove (12) valve plate and (13) insert spring assembly
9.
from (19) head by pulling upward. If (12) valve plate is
stuck, tap the top edge lightly with a soft face mallet. Do
not tap with anything metallic.
Remove both (11 and 14) inserts and (13) insert spring
10.
assembly from (12) valve plate.
Remove (15) gasket from (19) head assembly.
11.
Remove two (6) screws and two (7) lock washers from
12.
(33) gland in (19) head assembly.
With fingers, pull (31) valve piston upward until (33)
13.
gland has pulled out of its chamber.
Remove (33) gland by sliding it up over (31) valve piston.
14.
Remove (34) seal and (35) “O” ring from (33) gland (see
15.
gure 8, page 6).
Disassemble (31) valve piston from (38) adapter as
16.
shown in gure 4, page 3.
Pull (38) adapter upward until assembly is taut and
17.
grasp (36) extension rod with ngers, as shown in gure
(size)
(see chart, page 4)
(see chart, page 4)
(0.103” x 1.255” o.d.)
(1/16” x 7/16” o.d.)
(see chart, page 4)
(see chart, page 4)
(see chart, page 4)
(see chart, page 4)
(see chart, page 4)
(see chart, page 4)
(see chart, page 4)
(see chart, page 4)
(not shown)
(see chart, page 4)
(Qty) Part No.
(1) - - - - -
(1) - - - - -
(1) - - - - -
(1) 91207
(1) Y325-11
(4) - - - - -
(1) - - - - -
(1) - - - - -
(1) - - - - -
(1) - - - - -
(4) - - - - -
(1) - - - - -
(1) - - - - -
(1) 93007
9, page 6. Grasp (36) extension rod below (38) adapter.
4 Screws (4)
5 Washers (4)
Figure 2
Page 2 of 8 6544X-X (en)
Now push (38) adapter down on (36) extension rod and
remove (32) washer from (36) extension rod. Now remove (38) adapter.
Remove (17) washer and (20) “U” cup from (38) adapter.
18.
Remove four (47) nuts from four (42) bolts.
19.
Remove four (42) bolts.
20.
Remove (19) head assembly and place on the work-
21.
bench with (8) cap side down. This action will allow (40)
washer to fall out of its cavity.
(continued on page 5)
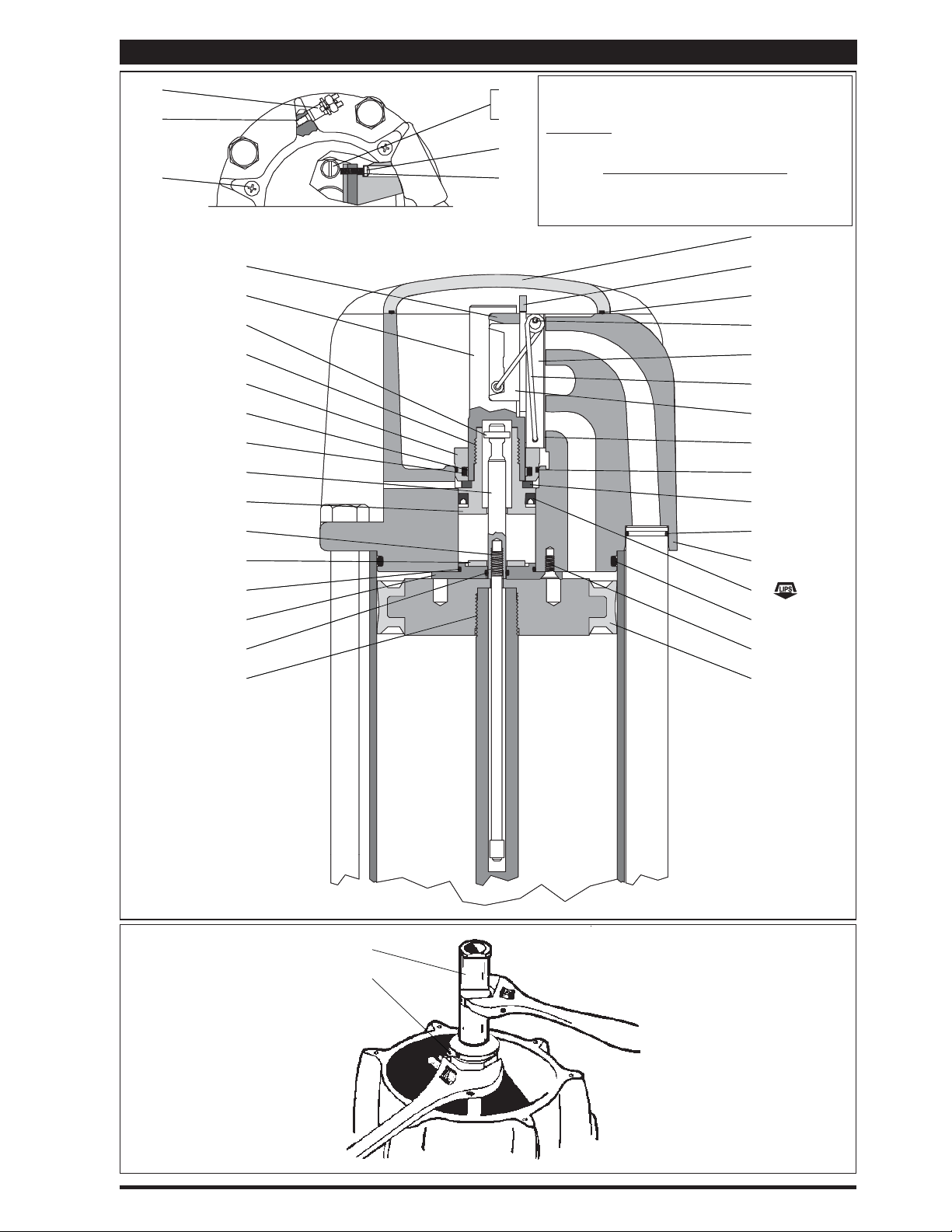
PARTS LIST / 6544X-X & 6546X-X - (AIR MOTOR HEAD)
50
50
Part numbers listed below and on parts list (opposite
6
6
7
7
4
4
5
3
3
11
11
31
31
32
32
33
33
34
34
35
35
36
36
38
38
5
page) are typical.
NOT SHOWN
93897-1 Pipe Plug (models 65440 only)
LUBRICATION / SEALANTS
NOTE: Lubricate with Parker “O” ring lube (ARO p/n
36460).
Apply Loctite® 271 to threads.
8
8
9
9
10
10
12a
12a
12
12
13
13
14
14
15
15
16
16
17
17
18
18
40
40
16
16
39
39
41
41
271™ is a trademark of Henkel Loctite Corporation
ARO® is a registered trademark of Ingersoll Rand Company
Loctite®is a registered trademark of Henkel Loctite Corporation
31
38
19
19
20
20
21
21
22
22
24
24
Figure 3
Figure 4
6544X-X (en) Page 3 of 8