
INSTALLATION AND MAINTENANCE INSTRUCTIONS
I56-3432-006
SK-Duct
12 Clintonville Road, Northford, CT 06472-1610
Phone: 203-484-7161 Fax: 203-484-7118
Air Duct Smoke Detector
SPECIFICATIONS
Operating Temperature: –4° to 158°F (–20° to 70°C)
32° to 120°F (0° to 49°C) with module installed in the SK-Duct
Storage Temperature: –22° to 158°F (–30° to 70°C)
Humidity: 0% to 93% Relative Humidity Non-condensing
Air Velocity: 100 to 4000 ft./min. (0.5 to 20.3 m/sec.)
Rectangular Footprint Dimensions: 14.38 in L×5 in W×2.5 in D (37 cm L×12.7 cm W×6.36 cm D)
Square Footprint Dimensions: 7.75 in L×9 in W×2.5 in D (19.7 cm L×22.9 cm W×6.35 cm D)
Weight: 1.8 pounds; 0.82 kg
Operating Voltage Range: 15 to 32 VDC
Standby Current: 300 µA @ 24 VDC (one communication every 5 seconds with LED blink enabled)
Max. Alarm Current (LED on): 6.5 mA @ 24 VDC
NOTE: The SK-Duct comes with the sensor head factory installed, part number SK-PHOTOR.
Table of Contents Page
[1] Limitations of Duct Smoke Detectors .........................1
[2] General Description .....................................1
[3] Contents of the Duct Smoke Detector Kit ......................1
[4] Detector Installation .....................................1
[5] Sampling Tube Installation ................................2
[6] Measurement Tests ......................................3
[7] Field Wiring ...........................................3
[8] Verification of Operation ..................................4
[9] Detector Cleaning Procedures ..............................4
[10] Sensor Replacement ....................................5
[11] Optional Accessories ....................................5
Warranty .............................................6
BEFORE INSTALLING
Read System Sensor's Applications Guide: Duct Smoke Detectors (HVAG53),
which provides detailed information on detector spacing, placement, zoning,
wiring, and special applications. Copies of this manual are available online
at www.systemsensor.com. NFPA Standards 72 and 90A should also be referenced for detailed information.
NOTICE: This manual shall be left with the owner/user of this equipment.
IMPORTANT: This detector must be tested and maintained regularly following
NFPA 72 requirements. The detector must be tested an maintained regularly following NFPA 72 requirements. According to NFPA, the detector should be visually inspected semiannually and functionally tested at least once a year. This
may need to be more frequent depending on the air quality of the duct supply air.
[1] LIMITATIONS OF DUCT SMOKE DETECTORS
The National Fire Protection Association has established that DUCT DETECTORS MUST NOT BE USED AS A SUBSTITUTE FOR OPEN AREA DETECTOR
PROTECTION as a means of providing life safety. Nor are they a substitute for
early warning in a building’s regular fire detection system.
System Sensor supports this position and strongly recommends that the user
read NFPA Standards 90A, 72, and 101. The SK-Duct Air Duct Smoke Detectors
are listed per UL 268A.
This device will not operate without electrical power. Fire situations may
cause an interruption of power. The system safeguards should be discussed
with your local fire protection specialist.
This device will not sense smoke unless the ventilation system is operating
and the cover is installed.
For this detector to function properly, it MUST be installed according to the
instructions in this manual. Furthermore, the detector MUST be operated within
ALL electrical and environmental specifications listed in this manual and the
sensor head installation manual. Failure to comply with these requirements may
prevent the detector from activating when smoke is present in the air duct.
[2] GENERAL DESCRIPTION
Smoke introduced into this air duct system will be distributed throughout the
entire building. Smoke detectors designed for use in air duct systems are used
to sense the presence of smoke in the duct.
Model SK-Duct Air Duct Smoke Detector utilizes photoelectric technology for
the detection of smoke. This detection method, when combined with an efficient housing design, samples air passing through the duct and allows detection of a developing hazardous condition. When sufficient smoke is sensed,
an alarm signal is initiated at the fire control panel monitoring the detector,
and appropriate action can be taken to shut off fans, blowers, change over air
handling systems, etc. These actions can facilitate the management of toxic
smoke and fire gases throughout the areas served by the duct system.
The SK-Duct incorporates a sensor cover tamper feature that provides a trouble signal at the panel immediately if the cover is removed or improperly installed. Proper installation of the sensor cover removes the trouble condition.
If programmed with the system control panel, two LEDs on each duct smoke
detector light to provide local visible indication.
The SK-Duct provides a remote alarm output for use with auxiliary devices,
such as the RA400Z/RA100Z remote LED annunciator, as well as remote test
capability with the RTS451/RTS151 or RTS451KEY/RTS151KEY Remote Test
Stations.
[2.1] DETECTOR FEATURE SET
– Utilizes plug-in head, part number SK-PHOTOR
– Sampling tubes install from front and rear
– Compatible with existing accessories
– Able to address detector per code switches on sensor head.
[3] CONTENTS OF THE DUCT SMOKE DETECTOR KIT
1. Sensor/power board assembly and covers sensor head is factory installed
2. Three #10 sheet metal screws for mounting
3. Drilling template
4. One sampling tube end cap
5. One plastic exhaust tube
NOTE: A sampling tube must be ordered to complete the installation. It must
be the correct length for the width of the duct where it will be installed. See
Table 1 on page 3 to determine the inlet tube required for different duct widths.
[4] DETECTOR INSTALLATION
[4.1] VERIFY DUCT AIR FLOW DIRECTION AND VELOCITY
Model SK-Duct detectors are designed to be used in air handling systems having air velocities of 100 to 4000 feet per minute. Duct widths from 6 inches to
12 feet can be accommodated. Be sure to check engineering specifications to
ensure that the air velocity in the duct falls within these parameters. If necessary, use a velocity meter (anemometer) to check the air velocity in the duct.
ACCESSORY CURRENT LOADS AT 24 VDC
DEVICE STANDBY ALARM
RA400Z/RA100Z 0 mA 12 mA Max.
RTS451/RTS151 0 mA 12 mA Max.
RTS451KEY/
RTS151KEY
www.silentknight.com
12 mA 12 mA Max.
1 I56-3432-006
04-12
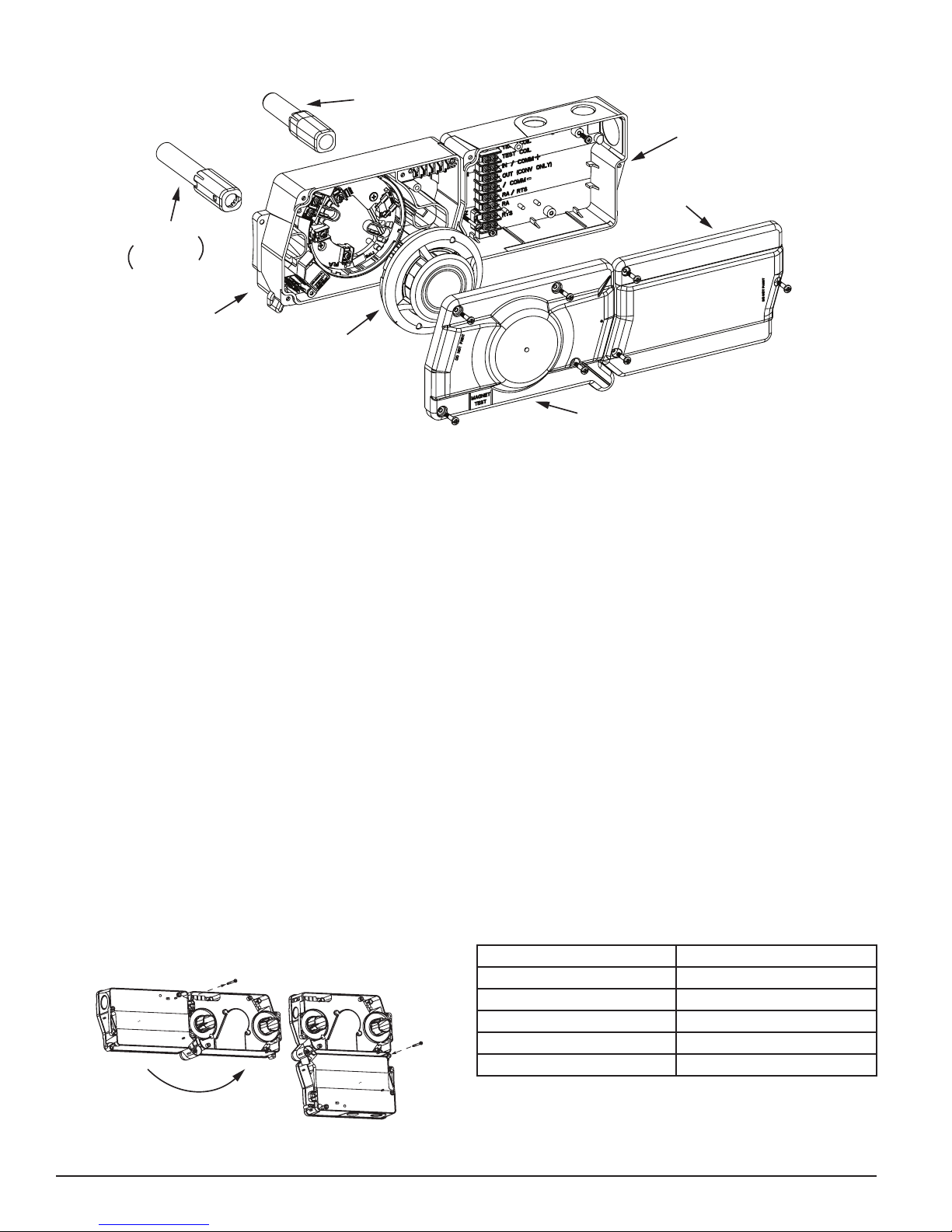
FIGURE 1. EXPLODED VIEW OF DUCT SMOKE DETECTOR COMPONENTS:
SAMPLING
TUBE
SOLD
SEPERATELY
SENSOR MODULE
SENSOR HEAD
NOTE: SENSOR HEAD IS ONLY
INCLUDED ON SPECIFIED MODELS.
WIRING COMPARTMENT
WIRING COMPARTMENT COVER
SENSOR MODULE COVER
H0569-06
[4.2] ] DETERMINE MOUNTING LOCATION AND CONFIGURATION
On ducts wider than 18 inches it is recommended that the detector be
mounted downstream of a bend, obstruction in the duct, or the supply or
return air inlet.
Exception: Installation of duct detectors can be on or within a commercial
packaged rooftop heating and air-conditioning system, fire/smoke dampers
and economizers. They may be mounted in either the supply and/or return air
section as determined by local code.
Once a suitable location is selected, determine if the detector is to be mounted
in a side-by-side “rectangular” configuration or a top-over-bottom “square”
configuration as shown in Figure 2. If mounting in the square configuration,
remove the rear attachment screw, rotate the unit at hinge, and replace the
screw into the new attachment hole as shown in Figure 2. Do NOT remove
the hinge screw during this process. Final installation approval shall be based
upon passing differential pressure and smoke entry tests described in the Measurement Tests section.
[4.3] DRILL THE MOUNTING HOLES
Remove the paper backing from the mounting template supplied. Affix the
template to the duct at the desired mounting location. Make sure the template
lies flat and smooth on the duct.
[4.3.1] FOR RECTANGULAR SIDE-BY-SIDE MOUNTING CONFIGURATION:
Center punch at (4) target centers: (2) “A” for sampling tubes and (2) “B” for
the rectangular configuration mounting tabs as shown on mounting template.
Drill pilot holes at target “A” centers and cut two 1.375-inch diameter holes
using a 13⁄8-inch hole saw or punch. Drill .156-inch diameter holes using a 5⁄32inch drill at target “B” centers.
FIGURE 2:
DETECTOR AS SHOWN BELOW.
TO SECURE DETECTOR
IN PLACE.
[4.3.2] FOR SQUARE TOP-OVER-BOTTOM MOUNTING CONFIGURATION:
Center punch at (4) target centers: (2) “A” for sampling tubes and (2) “C” for
the square configuration mounting tabs as shown on mounting template. Drill
pilot holes at target “A” centers and cut two 1.375-inch diameter holes using
a 13⁄8-inch hole saw or punch. Drill .156-inch diameter holes using a 5⁄32-inch
drill at target “C” centers. If desired, drill an additional .156-inch hole at the
location of one of the mounting tabs on the lower housing.
[4.4] SECURE THE DUCT DETECTOR TO THE DUCT
Use two (rectangular configuration) or three (square configuration) of the provided sheet metal screws to screw the duct detector to the duct.
CAUTION: Do not overtighten the screws.
[5] SAMPLING TUBE INSTALLATION
[5.1] SAMPLING TUBE SELECTION
The sampling tube must be purchased separately. Order the correct length,
as specified in Table 1, for width of the duct where it will be installed. The
sampling tube length must extend at least 2⁄3 across the duct width for optimal
performance.
The sampling tube is always installed with the air inlet holes facing into the
air flow. To assist proper installation, the tube’s connector is marked with an
arrow. Make sure the sampling tube is mounted so that the arrow points into
the airflow as shown in Figure 3. Mounting the detector housing in a vertical
orientation is acceptable provided that the air flows directly into the sampling tube holes as indicated in Figure 3. The sampling tube and exhaust tube
can be mounted in either housing connection as long as the exhaust tube is
mounted downstream from the sampling tube.
TABLE 1. SAMPLING TUBES RECOMMENDED FOR
DIFFERENT DUCT WIDTHS:
Outside Duct Width Sampling Tube Recommended*
Up to 1 ft. DST1
1 to 2 ft. DST1.5
2 to 4 ft. DST3
4 to 8 ft. DST5
8 to 12 ft. DST10 (2-piece)
*Must extend a minimum of 2⁄3 the duct width.
2 I56-3432-006
04-12
H0550-00